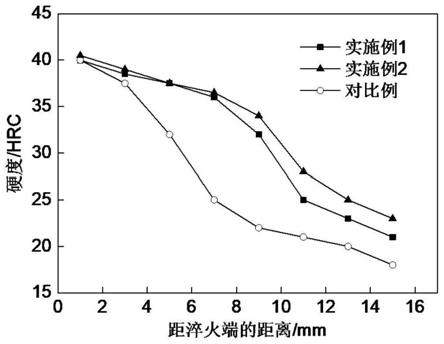
一种含nb、b冷锻齿轮钢及其制备方法
技术领域
1.本发明属于齿轮钢技术领域,特别涉及一种含nb、b冷锻齿轮钢及其制备方法。
背景技术:
2.一次冷轧罩退包装用钢是通过电镀作业获得的在两面镀覆锡层或铬层的冷轧罩退低碳钢板或钢带,主要用于饮料罐、食品罐、喷雾罐和化工罐等领域。
3.近年来,随着机械加工行业的快速发展,冷锻技术作为一种耗材少、效率高、性能优越的少/无切削加工工艺,在汽车、机床、仪表等民用工业以及国防工业系统中得到广泛应用。冷锻技术展现出的巨大技术优越性和良好经济效益,已逐渐成为齿轮等中小锻件精密化生产的发展方向。
4.齿轮常规的制备流程为:齿轮钢原料
→
下料
→
热锻
→
锻后热处理
→
齿轮加工(滚齿、插齿、铣齿、刨齿)
→
渗碳
→
淬火、回火
→
表面清洗
→
检验
→
入库。目前该齿轮产品生产工艺非常成熟,被广泛应用于齿轮制造行业,但该工艺热锻后的齿形加工将毛坯的锻造流线切断,导致齿轮的力学性能降低。此外,该工艺切削加工工时长、齿坯利用率低、生产成本高,极大程度地影响了齿轮行业的发展。
5.将冷锻技术引入齿轮加工行业,可充分解决上述问题,其具体优势如下:冷精锻齿轮因金属流线沿齿廓分布且组织致密,使得齿轮的强度、齿面的耐磨能力、热处理性能及啮合噪声都比切削加工齿轮优越。与切削加工齿轮相比,冷精锻齿轮的强度可提高20%,抗弯疲劳寿命可提高20%,热处理变形减少30%,生产成本降低20%以上。用冷精锻工艺快速生产高质量的齿轮已经成为全球趋势。
6.然而,冷精锻技术虽好,却对齿轮钢原料提出了更高的要求,现有坯料变形抗力不佳,对模具的磨损严重,使用寿命较短;二是冷锻后渗碳淬火后,出现局部粗晶,导致齿轮的性能下降。传统的解决方法是采用球化退火的方式降低原料硬度,渗碳淬火后采用二次淬火的方式解决局部粗晶问题,这样严重降低了生产效率,大幅增加了生产成本。因此,传统齿轮钢原料已难以满足冷精锻技术的要求,亟需一种新型的齿轮钢,在满足齿轮性能的基础上,具有较低的硬度,同时解决渗碳淬火后的局部粗晶问题,适用于冷锻技术。
技术实现要素:
7.鉴于上述问题,本发明提供了一种含nb、b冷锻齿轮钢及其制备方法来克服上述问题或者至少部分地解决上述问题。
8.本发明实施例提供一种含nb、b冷锻齿轮钢,所述齿轮钢的组成元素及质量百分比为:c:0.15%~0.25%,si:0.05%~0.40%,mn:0.30%~1.40%,p:0~0.03%,s:0~0.035%,cr:0.80%~1.50%,nb:0.01%~0.05%,b:0.0005%~0.0030%,ti:0~0.05%,al:0~0.045%,cu:0~0.15%,n:0~0.0150%,余量为fe及不可避免杂质。
9.可选的,所述齿轮钢的金相组织包括奥氏体,所述奥氏体的晶粒度为6级
‑
7级。
10.可选的,所述金相组织还包括铁素体和珠光体,所述铁素体比率>50%。
11.一种含nb、b冷锻齿轮钢的制备方法,所述方法包括:
12.将冶炼后钢水依次进行浇注、连铸,得到铸坯;
13.将所述铸坯进行加热,后除鳞,获得脱鳞后铸坯;
14.将所述脱鳞后铸坯依次进行轧制、冷却,获得所述齿轮钢;
15.所述轧制包括粗轧和精轧,所述粗轧的开轧温度为1050~1100℃,所述精轧的温度为850~950℃,所述精轧的机组总变形量为40%~60%。
16.可选的,所述浇注的温度为1500~1580℃,所述加热的温度为1150~1200℃,所述加热的时间为2.5~3.5h。
17.可选的,所述将冶炼后钢水进行浇注、连铸,得到铸坯,之前还包括:将含有所述化学成分的钢水进行冶炼,冶炼过程中进行真空脱气,获得冶炼后钢水;所述真空脱气的时间为4~7min。
18.可选的,所述冶炼包括炉外真空精炼,所述炉外真空精炼具体包括:在压力小于67pa的真空压力环境中保压10~12min。
19.可选的,所述炉外真空精炼包括对所述钢水进行脱氧和调铝,使精炼到站钢水,以质量分数计,铝含量为0.0450%~0.070%,所述脱氧的脱氧剂为铝合金。
20.可选的,所述冷却依次包括进冷床并盖保温罩、出冷床、进缓冷坑和出缓冷坑。
21.可选的,所述进缓冷坑的温度为550~650℃,所述出缓冷坑的温度≤300℃;所述出缓冷坑的齿轮钢组织为铁素体和珠光体。
22.本发明实施例中的一个或多个技术方案,至少具有如下技术效果或优点:
23.本发明提供的含nb、b冷锻齿轮钢,其化学成分以质量分数计为:c:0.15%~0.25%,si:0.05%~0.40%,mn:0.30%~1.40%,p:0~0.03%,s:0~0.035%,cr:0.80%~1.50%,nb:0.01%~0.05%,b:0.0005%~0.0030%,ti:0~0.05%,al:0~0.045%,cu:0~0.15%,n:0~0.0150%,余量为fe及不可避免杂质;通过降低si、mn元素含量,降低齿轮钢坯料的冷态变形抗力;通过添加nb、b元素,利用其冷锻渗碳后形成析出相的钉扎作用,阻止奥氏体晶粒的长大,从而避免局部粗晶现象,同时可弥补降低si、mn含量后淬透性的降低,以满足齿轮的淬透性要求;提高奥氏体晶粒内部变形带数量,为铁素体相变提供了大量的形核位置,促进铁素体相变,提高轧材组织中铁素体比例,降低冷态变形抗力。总结为:一,具有较高的冷态塑性,较小的变形抗力,减少坯料对模具的磨损,提高模具的使用寿命;二是冷锻后渗碳淬火后组织均匀,避免出现局部粗晶,造成齿轮的性能下降。齿轮钢硬度可达到200hbw以下,具有较低的冷态变形抗力,可供冷锻使用,抗拉强度≥835mpa,冲击韧性≥60j,淬透性j9点硬度达到30~42hrc。
24.上述说明仅是本发明技术方案的概述,为了能够更清楚了解本发明的技术手段,而可依照说明书的内容予以实施,并且为了让本发明的上述和其它目的、特征和优点能够更明显易懂,以下特举本发明的具体实施方式。
附图说明
25.为了更清楚地说明本发明实施例中的技术方案,下面将对实施例描述中所需要使用的附图作一简单地介绍,显而易见地,下面描述中的附图是本发明的一些实施例,对于本领域普通技术人员来讲,在不付出创造性劳动的前提下,还可以根据这些附图获得其它的
附图。
26.图1为本发明实施例与对比例钢的淬透性曲线对比图;
27.图2为本发明实施例与对比例钢的冷态应力
‑
应变曲线对比图;
28.图3为本发明实施例1齿轮钢930℃渗碳1h后原奥氏体晶粒形貌;
29.图4为本发明实施例2齿轮钢930℃渗碳1h后原奥氏体晶粒形貌;
30.图5为本发明对比例1钢930℃渗碳1h后原奥氏体晶粒形貌;
31.图6为本发明对比例2钢930℃渗碳1h后原奥氏体晶粒形貌;
32.图7为本发明实施例1齿轮钢930℃渗碳6h后原奥氏体晶粒形貌;
33.图8为本发明实施例2齿轮钢930℃渗碳6h后原奥氏体晶粒形貌;
34.图9为本发明对比例1钢930℃渗碳6h后原奥氏体晶粒形貌;
35.图10为本发明对比例2钢930℃渗碳6h后原奥氏体晶粒形貌。
具体实施方式
36.下文将结合具体实施方式和实施例,具体阐述本发明,本发明的优点和各种效果将由此更加清楚地呈现。本领域技术人员应理解,这些具体实施方式和实施例是用于说明本发明,而非限制本发明。
37.在整个说明书中,除非另有特别说明,本文使用的术语应理解为如本领域中通常所使用的含义。因此,除非另有定义,本文使用的所有技术和科学术语具有与本发明所属领域技术人员的一般理解相同的含义。若存在矛盾,本说明书优先。
38.除非另有特别说明,本发明中用到的各种原材料、试剂、仪器和设备等,均可通过市场购买得到或者可通过现有方法制备得到。
39.本技术实施例的技术方案为解决上述技术问题,总体思路如下:
40.根据本发明一种典型的实施方式,一种含nb、b冷锻齿轮钢,所述齿轮钢的组成元素及质量百分比为:c:0.15%~0.25%,si:0.05%~0.40%,mn:0.30%~1.40%,p:0~0.03%,s:0~0.035%,cr:0.80%~1.50%,nb:0.01%~0.05%,b:0.0005%~0.0030%,ti:0~0.05%,al:0~0.045%,cu:0~0.15%,n:0~0.0150%,余量为fe及不可避免杂质。
41.通过降低si、mn元素含量,降低齿轮钢坯料的冷态变形抗力;通过添加nb、b元素,利用其冷锻渗碳后形成析出相的钉扎作用,从而避免局部粗晶现象,同时可弥补降低si、mn含量后淬透性的降低,以满足齿轮的淬透性要求;通过低温大变形量精轧的方式,大幅提高奥氏体晶粒内部变形带数量,为铁素体相变提供了大量的形核位置,促进铁素体相变。
42.所述齿轮钢的硬度可达到220hbw以下,由其金相组织结构决定,与球化退火态常规齿轮钢20crmnti硬度相当,具有较低的冷态变形抗力,可供冷锻使用。
43.作为一种可选的实施方式,所述齿轮钢的金相组织包括奥氏体,所述奥氏体的晶粒度为6级
‑
7级。
44.奥氏体中,温度不大于980℃渗碳后的晶粒度为6级
‑
7级,避免了局部粗晶的出现。
45.大幅提高奥氏体晶粒内部变形带数量,为铁素体相变提供了大量的形核位置,促进铁素体相变。比例过小造成的不良后果是在冷挤压过程中变形抗力过大,无法形成很好的流变;
46.作为一种可选的实施方式,所述金相组织还包括铁素体和珠光体,所述铁素体比
率>50%。
47.确保了所述齿轮钢的力学性能,同事大幅提高奥氏体晶粒内部变形带数量,为铁素体相变提供了大量的形核位置,促进铁素体相变。
48.一种含nb、b冷锻齿轮钢的制备方法,所述方法包括:
49.将冶炼后钢水依次进行浇注、连铸,得到铸坯;
50.将所述铸坯进行加热,后除鳞,获得脱鳞后铸坯;
51.将所述脱鳞后铸坯依次进行轧制、冷却,获得所述齿轮钢;
52.所述轧制包括粗轧和精轧,所述粗轧的开轧温度为1050~1100℃,所述精轧的温度为850~950℃,所述精轧的机组总变形量为40%~60%。
53.利用其冷锻渗碳后形成析出相的钉扎作用,阻止奥氏体晶粒的长大,从而避免局部粗晶现象,同时可弥补降低si、mn含量后淬透性的降低,以满足齿轮的淬透性要求;通过低温大变形量精轧的方式,大幅提高奥氏体晶粒内部变形带数量,为铁素体相变提供了大量的形核位置,促进铁素体相变,采用轧后缓冷的方式,增加铁素体相区停留时间,可提高轧材组织中铁素体比例,降低冷态变形抗力。
54.精炼结束可直接连铸得到钢坯,也可对钢水进行真空脱气(选用vd、rh或vod中的一种或多种。
55.作为一种可选的实施方式,所述浇注的温度为1500~1580℃;所述加热的温度为1150~1200℃,所述加热的时间为2.5~3.5h。
56.作为一种可选的实施方式,所述将冶炼后钢水进行浇注、连铸,得到铸坯,之前还包括:将含有所述化学成分的钢水进行冶炼,冶炼过程中进行真空脱气,获得冶炼后钢水;所述真空脱气的时间为4~7min。作为一种可选的实施方式,所述冶炼包括炉外真空精炼,所述炉外真空精炼具体包括:在压力小于67pa的真空压力环境中保压10~12min。作为一种可选的实施方式,所述炉外真空精炼包括对所述钢水进行脱氧和调铝,使精炼到站钢水,以质量分数计,铝含量为0.0450%~0.070%,所述脱氧的脱氧剂为铝合金。
57.保证钢中低氧含量的基础上,提高冷态变形能力。
58.作为一种可选的实施方式,所述钢水采用电炉或转炉冶炼的方式,控制精炼到站一次成分j1的铝含量为0.0450%~0.070%。
59.出钢终点碳含量(质量分数)控制在0.08%~0.12%;随后进入lf炉进行炉外精炼,座包后喂铝线4~5m/t,控制精炼到站一次成分j1目标铝含量达到0.050%~0.070%,根据渣况及出钢时硫含量情况补加石灰和萤石的量,确保渣流动性良好,为获得良好的冷锻性能,
60.铝线可以有效地加入钢水中,并获得高而稳定的铝收得率,通过控制炼钢过程中的铝含量,保证钢中低氧含量的基础上,采用铝固氮,提高冷态变形能力;钢水质量得到改善,可大幅降低脱氧合金化成本,经济效益明显。控制铝含量的原因是:保证钢中低氧含量的基础上,采用铝固氮,提高冷态变形能力。
61.作为一种可选的实施方式,所述冷床上的冷却速度为0~2℃/s。优选的,冷速区间为0~0.5℃/s。
62.作为一种可选的实施方式,所述冷却依次包括进冷床并盖保温罩、出冷床、进缓冷坑和出缓冷坑。
63.作为一种可选的实施方式,所述进缓冷坑的温度为550~650℃,所述出缓冷坑的温度≤300℃;所述出缓冷坑的齿轮钢组织为铁素体和珠光体。
64.进冷床并盖保温罩的原因是减少冷床附近的空气对流尽量减缓轧材冷速;是采用轧后缓冷的方式,增加铁素体相区停留时间,可提高轧材组织中铁素体比例,降低冷态变形抗力。
65.所述进缓冷坑的温度为550~650℃,出缓冷坑的温度≤300℃,出缓冷坑的组织为铁素体和珠光体。控制进缓冷坑和出缓冷坑的温度,同时避免出现异常组织作为一种可选的实施方式,连铸坯为尺寸范围(120~350)mm
×
(120~350)mm的矩形坯或直径为φ100mm~φ350mm的圆坯。
66.作为一种可选的实施方式,所述冷锻齿轮钢的成品规格范围为φ8mm~φ250mm。
67.下面将结合实施例、对照例及实验数据对本技术的一种含nb、b冷锻齿轮钢的制备方法进行详细说明。
68.实施例1
69.本实施例中,齿轮钢采用的组成元素及质量百分比为:c 0.18%,si 0.07%,mn 0.50%,p 0.011%,s 0.005%,cr 1.15%,nb 0.02%,b 0.0015%,cu 0.11%,n 0.0040%,余量为fe及不可避免杂质。
70.生产规格为φ60mm新型冷锻齿轮钢具体控制参数为:
71.(1)采用电炉冶炼,出钢终点碳含量(质量分数)控制在0.12%;随后进入lf炉进行炉外精炼,座包后喂铝线5m/t,控制精炼到站一次成分j1目标铝含量达到0.060%,根据渣况及出钢时硫含量情况补加石灰和萤石的量,确保渣流动性良好;随后对钢水进行vd真空脱气,进泵时间为4min,小于67pa真空保压时间达到12min。
72.(2)钢水全程进行保护浇注,浇注温度为1520℃,过热度为25℃,凝固得到连铸坯。
73.(3)连铸坯常温入加热炉,加热温度为1150℃,加热时间为2.5h;出加热炉进行高压水除鳞;除鳞后进热连轧机组,开轧温度为1050℃,精轧温度为900℃,精轧机组总变形量控制在40%;精轧后采用0.4℃/s的冷速冷却;精轧后上冷床加盖保温罩,出冷床进缓冷坑,入缓冷坑温度为530℃,出缓冷坑温度为270℃。
74.实施例2
75.本实施例中,齿轮钢采用的组成元素及质量百分比为:c 0.18%,si 0.07%,mn 0.50%,p 0.011%,s 0.005%,cr 1.15%,nb 0.02%,b 0.0015%,ti 0.05%,al 0.025%,cu 0.11%,n 0.0045%,余量为fe及不可避免杂质。
76.生产规格为φ120mm新型冷锻齿轮钢具体控制参数为:
77.(1)采用转炉冶炼,出钢终点碳含量(质量分数)控制在0.08%;随后进入lf炉进行炉外精炼,座包后喂铝线4m/t,控制精炼到站一次成分j1目标铝含量达到0.045%,根据渣况及出钢时硫含量情况补加石灰和萤石的量,确保渣流动性良好;随后对钢水进行vod真空脱气,进泵时间为7min,小于67pa真空保压时间达到10min。
78.(2)钢水全程进行保护浇注,浇注温度为1540℃,过热度为25℃,凝固得到连铸坯。
79.(3)连铸坯常温入加热炉,加热温度为1200℃,加热时间为3.5h;出加热炉进行高压水除鳞;除鳞后进热连轧机组,开轧温度为1100℃,精轧温度为950℃,精轧机组总变形量控制在60%;精轧后采用0.5℃/s的冷速冷却;精轧后上冷床加盖保温罩,出冷床进缓冷坑,
入缓冷坑温度为540℃,出缓冷坑温度为280℃。
80.实施例3
81.本实施例中,含nb、b冷锻齿轮钢的组成元素及质量百分比为:c:0.15%,si:0.05%,mn:0.30%,cr:0.80%,nb:0.01%,b:0.0005%,ti:0~0.05%,余量为fe及不可避免杂质。
82.一种含nb、b冷锻齿轮钢的制备方法,所述方法依次包括连铸、轧制、冷却,具体工艺参数如下:
83.将所述钢水进行浇注,温度为1500℃,得到连铸坯;
84.将所述连铸坯进行加热,温度为1150℃,时间为2.5h,后进行除鳞;
85.所述轧制中开轧温度为1050℃,所述轧制中精轧的温度为850℃。
86.实施例4
87.本实施例中,含nb、b冷锻齿轮钢的组成元素及质量百分比为:c:0.25%,si:0.40%,mn:1.40%,p:0.03%,s:0.01%,cr:1.50%,nb:0.05%,b:0.0030%,ti:0.05%,al:0.045%,cu:0.15%,n:0.0150%,余量为fe及不可避免杂质。
88.一种含nb、b冷锻齿轮钢的制备方法,所述方法依次包括连铸、轧制、冷却,具体工艺参数如下:
89.将所述钢水进行浇注,温度为1580℃,得到连铸坯;
90.将所述连铸坯进行加热,温度为1200℃,时间为3.5h,后进行除鳞;
91.所述轧制中开轧温度为1080℃,所述轧制中精轧的温度为900℃。
92.实施例5
93.本实施例中,含nb、b冷锻齿轮钢的组成元素及质量百分比为:c:0.20%,si:0.30%,mn:1.20%,p:0.01%,s:0.008%,cr:1.10%,nb:0.03%,b:0.00120%,ti:0.02%,al:0.032%,cu:0.11%,n:0.0120%,余量为fe及不可避免杂质。
94.对比例1
95.采用常规热轧态,齿轮钢20cr作为对比例,其组成元素及质量百分比为:c 0.20%,si 0.25%,mn 0.70%,p 0.015%,s 0.013%,cr 0.91%,n 0.0065%,余量为fe及不可避免杂质。
96.对比例2
97.采用常规退火态齿轮钢20cr作为对比例,其组成元素及质量百分比为:c 0.20%,si 0.25%,mn 0.70%,p 0.015%,s 0.013%,cr 0.91%,n 0.0065%,余量为fe及不可避免杂质。球化退火工艺:790℃保温1.5h,随炉冷却至690℃保温3h,炉冷至600℃,出炉缓冷。
98.相关实验:
99.将实施例1
‑
2和对比例1
‑
2制得的钢进行性能检测,测试结果如下。
100.对上述实施例、对比例齿轮钢坯料进行硬度、淬透性、冷态变形抗力、渗碳后晶粒度、热处理后力学性能的对比,结果如下:
101.(1)硬度:实施例1的硬度为151hbw;实施例2的硬度为156hbw;对比例1的硬度为163hbw;对比例2的硬度为149hbw。实施例和对比例的硬度均达到齿轮钢坯料的要求;实施例的硬度良好,优于对比例。
102.(2)淬透性:按照gb/t 5216
‑
2014《保证淬透性结构钢》和gb/t 225
‑
2006《钢淬透
性的末端淬火试验方法(jominy试验)》进行淬透性试验,结果如图1所示,其中实施例1淬透性j9点硬度达到30hrc,实施例2淬透性j9点硬度达到28hrc。实施例的淬透性良好,优于对比例。
103.(3)冷态变形抗力:按照yb/t 5293
‑
2014《金属材料顶锻试验方法》进行冷顶锻试验,将实施例、对比例齿轮钢坯料压缩至1/3位置,观察试样冷态变形抗力,得到应力
‑
应变曲线,结果如图2所示。
104.(4)渗碳后晶粒度:按照gb/t 28694
‑
2012《深层渗碳技术要求》进行渗碳,渗碳温度选用930℃,渗碳时间分别为1h和6h,观察原奥氏体晶粒形貌,如图3
‑
10所示。
105.(5)热处理力学性能:渗碳后油冷 180℃回火2h,实施例1抗拉强度达到845mpa,冲击功达到69j,实施例2抗拉强度达到854mpa,冲击功达到66j;对比例1抗拉强度达到835mpa,冲击功达到60j。实施例和对比例的抗拉强度和冲击功均达到齿轮钢坯料的要求,实施例的热处理力学性能优于对比例。
106.可见,本发明新型齿轮钢硬度、冷态变形抗力低于热轧态常规齿轮钢20cr,与其退火态接近,可供冷锻使用;同时其淬透性满足国家标准,并优于常规齿轮钢20cr;本发明实施例保温1h和6h后均可保持较细的奥氏体晶粒尺寸,晶粒度级别小于7.0级,未出现局部混晶现象;同时热处理后力学性能优于常规齿轮钢20cr。
107.附图1
‑
10的详细说明:
108.如图1所示,其中实施例1淬透性j9点硬度达到30hrc,实施例2淬透性j9点硬度达到28hrc,实施例淬透性良好,淬透性j9点硬度达到28
‑
42hrc。对比例1的实施例的淬透性j9点硬度不到18hrc,对比例1淬透性低,冷锻后渗碳淬火后易出现局部粗晶。
109.如图2所示,应变在0.5以上时,对比例真实应力分别大于实施例的真实应力,真实应力过大,易造成钢后续加工时易变形。
110.如图3
‑
10所示,为实施例和对比例在930℃渗碳1h和6h后原奥氏体晶粒形貌;本发明实施例保温渗碳1h和6h后均可保持较细的奥氏体晶粒尺寸,晶粒度级别大于等于6级同时小于7级,同时小于7.0级,未出现局部混晶现象,解决局部粗晶问题;而对比例1和对比例2保温渗碳1h和6h后出现局部混晶现象,出现局部粗晶问题。
111.最后,还需要说明的是,术语“包括”、“包含”或者其任何其他变体意在涵盖非排他性的包含,从而使得包括一系列要素的过程、方法、物品或者设备不仅包括那些要素,而且还包括没有明确列出的其他要素,或者是还包括为这种过程、方法、物品或者设备所固有的要素。
112.尽管已描述了本发明的优选实施例,但本领域内的技术人员一旦得知了基本创造性概念,则可对这些实施例作出另外的变更和修改。所以,所附权利要求意欲解释为包括优选实施例以及落入本发明范围的所有变更和修改。
113.显然,本领域的技术人员可以对本发明进行各种改动和变型而不脱离本发明的精神和范围。这样,倘若本发明的这些修改和变型属于本发明权利要求及其等同技术的范围之内,则本发明也意图包含这些改动和变型在内。
再多了解一些
本文用于企业家、创业者技术爱好者查询,结果仅供参考。