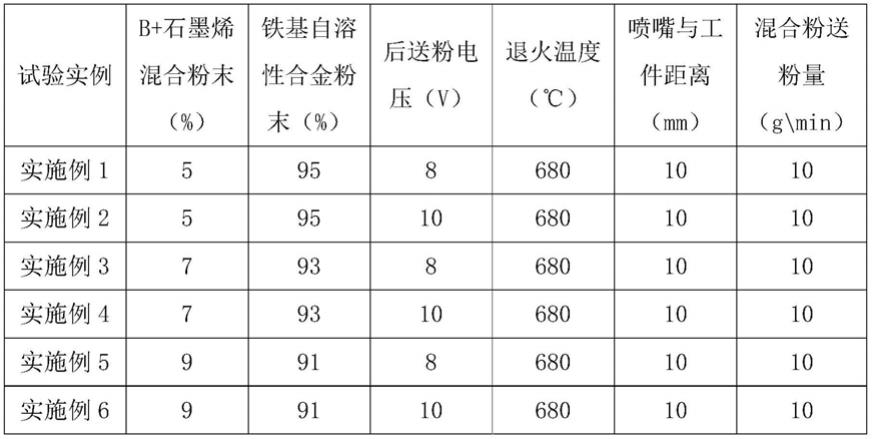
1.本发明涉及材料熔覆涂层技术领域,具体提供了提高直升机桨叶金属衬套耐蚀性的熔覆方法。
背景技术:
2.直升机桨叶一般为双销构型,桨根处通过两个突出桨叶本体的金属衬套与直升机桨榖相连。当直升机在海洋环境中长时间服役时,由于水汽和盐份同时存在,极易对衬套进行腐蚀,而暴露在空气中的衬套端面锈蚀最为严重。一旦金属衬套发生锈蚀,脱落的锈斑易积累在衬套和桨榖的连接处,造成卡涩,直升机的安全飞行存在巨大隐患。
3.熔覆材料体系的研究主要是加入不同类型粉末来提高熔覆涂层的性能。采用等离子熔覆所制备的金属基复合材料,一般选用陶瓷颗粒(wc)与金属粉末混合,制备各种高体积分数的颗粒增强钴基,铁基和镍基复合涂层,次涂层一般具有优良的耐磨性,而直升机桨叶金属衬套表面更需要良好的抗蚀性。石墨烯诸多优异的力学性能可以应用在熔覆材料体系中,能有效细化涂层组织;b原子质量小,可以有效降低体系熔点,提高熔池流动性和润湿性,减少气孔裂纹缺陷的产生。欲通过石墨烯和b粉的同时添加来改善涂层中的晶体组织,提高基体与涂层的冶金结合,提升涂层的抗腐蚀性能。
技术实现要素:
4.本发明的目的:本发明旨在提供一种提高直升机桨叶金属衬套耐蚀性的熔覆方法,以提高直升机桨叶金属衬套的耐腐蚀性能。本发明提供的桨叶金属衬套耐蚀性的熔覆方法,其涂层具有优异的耐蚀性,成本也低。
5.本发明的技术方案:提高直升机桨叶金属衬套耐蚀性的熔覆方法,在金属衬套表面熔覆耐腐蚀混合粉末,形成3mm~5mm厚度的耐腐蚀熔覆涂层;
6.所述混合粉末由b粉末、石墨烯和铁基自熔性合金粉末组成,b粉末和石墨烯的质量比为(2~3):(3~2);b粉末和石墨烯在混合粉末中的质量分数为5%~9%wt;
7.对金属衬套表面进行铣切加工,使得所述耐腐蚀熔覆涂蚀层的厚度为1mm~2mm。
8.进一步的,所述b粉的粒径为50~200目,石墨烯的粒径为50~300目,铁基自熔性合金粉末粒径为50~150目;
9.进一步的,所述金属衬套的材质为0cr17ni4cu4nb马氏体沉淀硬化不锈钢;
10.进一步的,所述混合粉末为增强相,所述自熔性合金粉为涂层粘接材料;
11.进一步的,所述混合粉末和铁基自熔性合金粉末分别通过送粉器同时送粉,在惰性气体保护下熔覆出具有复合增强相的耐腐蚀熔覆涂层。
12.进一步的,b粉和石墨烯还经过预处理,步骤为:将b粉末和石墨烯在混料机中混合4~8h,混合均匀,然后进行干燥处理以除去水分,干燥温度为100~120℃,直至质量不在发生变化,干燥时间为10~12h。
13.进一步的,对所述金属衬套进行打磨处理,去除表面的锈迹和污渍,打磨后用酒精
进行超声波清洗,最后在60~120℃温度下干燥5~10h,去除溶剂。
14.进一步的,所述熔覆为等离子熔覆。更具体的等离子熔覆参数为:熔覆所使用气体为氩气,工作气压为0.2
‑
0.3mpa,冷却水压力为0.1
‑
0.2mpa,熔覆电流为100
‑
130a,混合粉料送粉量为8
‑
14g\min,后送粉电压为6
‑
12v,熔覆扫描速度为50
‑
150mm\min,离子气流为300
‑
800l\h,保护气流为800
‑
1000l\h,送粉气流为300
‑
800l\h,熔覆喷嘴与铁基表面距离为8
‑
14mm。
15.进一步的,熔覆后进行退火处理,用铸铁铁硝覆盖金属衬套,密封加热到680
‑
780℃,之后保温2
‑
4h,然后自然冷却;
16.与现有技术相比,本发明的有益效果体现在:
17.1、本发明所制备的复合材料中,采用热喷涂或热喷焊或等离子熔覆等表面熔覆方法涂覆于基材表面,使其与基材结合,工艺简单,成本低。
18.2、本发明所制备的涂层中主要是添加了石墨烯和b粉,b原子的加入,能有效降低合金粉末体系的自身熔点,提高熔池的流动性和润湿性,此举大大减少裂纹和气孔的缺陷产生,提高了复合材料的抗蚀性能。此外,石墨烯的加入,可以均匀细化涂层组织,与合金基体呈现较为良好的冶金结合,进一步提高复合材料的抗腐蚀性能。
19.3、本发明所制备的熔覆层相较于一般电镀涂层,具备足够的加工余量。而桨根衬套的最终成型一般需要对端面进行铣切,普通的电镀膜厚度较薄,经过铣刀打磨后,膜层几乎消失不见,表面防腐效果差。而本发明可以制备厚度为5
‑
8mm的涂层,具备足够的加工余量,即使经过铣刀打磨后,防腐效果依旧优良。
附图说明
20.图1为金属衬套在桨叶上的示意图;
21.图2为金属衬套与熔覆层的示意图;
22.其中:1
‑
金属衬套、2
‑
熔覆层。
具体实施方式
23.下面结合具体的实施例对本发明的技术方案作详细说明。以下实施例是说明性的,而不是限定性的,不能以下述实施例来限定本发明的保护范围。
24.选取0cr17ni4cu4nb马氏体沉淀硬化不锈钢作为涂层基材,fe313自溶性粉末为涂层粘接材料。其中铁基合金粉末成分如下:
25.表1 fe313合金粉末成分
26.fe313csicrnifewt(%)0.11150bal.
27.实施例1
28.本实施例中一种提高直升机桨叶金属衬套耐蚀性的熔覆方法,其制备方法如下:
29.步骤1:备料
30.将b粉和石墨烯作为增强颗粒;0cr17ni4cu4nb马氏体沉淀硬化不锈钢作为基材;铁基自溶性合金粉末作为粘接材料。
31.步骤2:预处理
32.b粉和石墨烯的预处理:将b粉和石墨烯在混料机中混合4
‑
8h,得到均匀混合的混合粉,然后对混合粉料进行干燥处理以除去其中的水分,干燥温度为100
‑
120℃,直至质量不在发生变化,干燥时间为10
‑
12h;
33.基材的预处理:用打磨机对基材进行打磨处理,去除基材表面的锈迹和污渍,打磨后用酒精进行超声波清洗,最后在60
‑
120℃温度下干燥5
‑
10h,去除溶剂。
34.步骤3:等离子熔覆
35.将步骤2中处理的混合粉料和铁基自溶性粉料经两个送粉器分别同时送粉,进行等离子熔覆。等离子熔覆参数为:熔覆所使用气体为氩气,工作气压为0.2
‑
0.3mpa,冷却水压力为0.1
‑
0.2mpa,熔覆电流为100
‑
130a,混合粉料送粉量为8
‑
14g\min,后送粉电压为6
‑
12v,熔覆扫描速度为50
‑
150mm\min,离子气流为300
‑
800l\h,保护气流为800
‑
1000l\h,送粉气流为300
‑
800l\h,熔覆喷嘴与铁基表面距离为8
‑
14mm。
36.步骤4:退火处理
37.将步骤3熔覆后的铁基工件进行退火处理,将铁基工件装在铁箱中,并用铸铁铁硝覆盖密封加热到680
‑
780℃,此温度下保温2
‑
4h,然后缓慢降温;
38.步骤5:后处理
39.对退火后的铁基工件用酒精进行超声波清洗,去除表面污垢,然后于60
‑
120℃干燥处理2
‑
10h。
40.实施例2
‑
6的制备过程参见实施例1,不同的是原材料的质量百分比和主要实验参数,如表2所示:
41.表2实施例1
‑
6中原材料百分比和主要实验参数
[0042][0043]
实施例中,熔覆电流设置为120a,离子气流量为300l\h,保护气流量800l\h,送粉气流量为300l\h。
[0044]
实施例结果分析
[0045]
通过添加石墨烯和b粉所制备的含5%(b,石墨烯),7%(b,石墨烯),9%(b,石墨烯)的复合涂层,均成型良好,表面光滑连续且无气孔、裂纹等宏观缺陷。通过后送粉的技术,使得石墨烯粉末在熔池中溶解量较少,比较完整的保留石墨烯的原始形态,增强效果较好。后送粉电压的大小决定了混合粉末的送入量,随着后送粉电压的适量增大,涂层中增强
相的含量随之提升,分布也更为紧密均匀。对实施例中的1,3和5例进行抗腐蚀性能检测,将三种熔覆涂层置于3.2%的nacl溶液中进行腐蚀试验。实施例1中,所测自腐蚀电位
‑
502mv,自腐蚀电流密度为4.619μa
·
cm
‑2,通过能斯特图拟合后的膜电阻为2624ω
·
m
‑2;实施例3中,所测自腐蚀电位
‑
489mv,自腐蚀电流密度为4.522μa
·
cm
‑2,通过能斯特图拟合后的膜电阻为3132ω
·
m
‑2;实施例5中,所测自腐蚀电位
‑
477mv,自腐蚀电流密度为3.935μa
·
cm
‑2,通过能斯特图拟合后的膜电阻为3637ω
·
m
‑2。由自腐蚀电位和电流密度可知,发生腐蚀后含5%(b,石墨烯)熔覆层的腐蚀速率最快,含9%(b,石墨烯)熔覆层的腐蚀速率最慢。由阻抗谱可知,含9%(b,石墨烯)熔覆层的耐蚀性最好,含5%(b,石墨烯)熔覆层的耐蚀性能最差。即一定范围内,随着体系中石墨烯和b含量的增加,熔覆层耐腐蚀性能也依次增强。
再多了解一些
本文用于企业家、创业者技术爱好者查询,结果仅供参考。