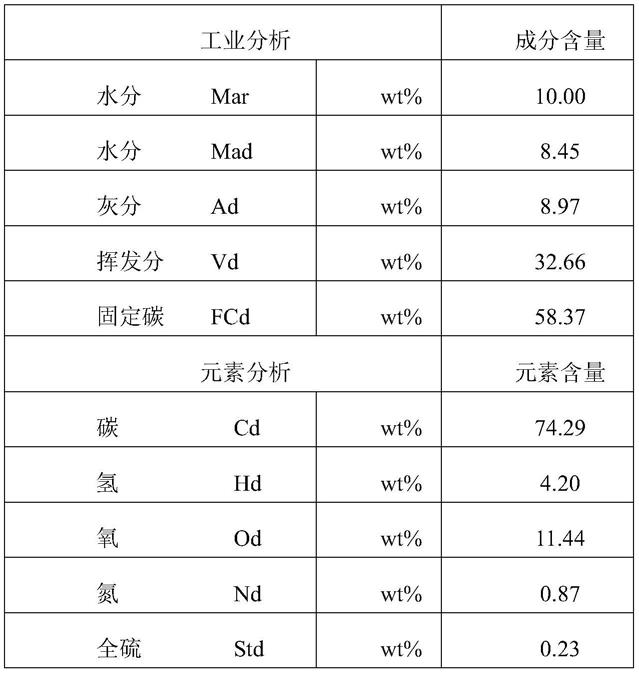
1.本实用新型涉及一种含碳物质的超细颗粒气化系统。
背景技术:
2.固体含碳物质转化成富含co、h2(或含ch4)等气态物质的过程是以氧气(空气、富氧或工业纯氧)、水蒸气作为气化剂,通过化学反应将煤或煤焦中的可燃部分转化为富含co、h2(或含ch4)等气态物质的工艺过程。
3.现有含碳物质气化工艺根据进入反应器的固体颗粒尺度可以分为固定床常压(加压)气化工艺、流化床气化工艺和气流床气化工艺。固定床常压(加压)气化工艺中固态物质以厘米级尺度进入气化炉,转化时间为几十分钟到几小时;流化床气化工艺以毫米级固体颗粒为原料,转化时间约为分钟级;气流床气化技术以百微米级颗粒为原料,转化时间为10s级。颗粒尺度变化导致颗粒的反应时间发生巨大变化,进而使气化炉结构、处理能力、工艺流程发生很大的差别。从固定床气化炉、流化床气化炉、气流床气化炉的反应性能可以看出,气流床气化炉的单位容积处理能力最大。中国专利文献cn110257105a公开了一种超细粉低温气流床气化生产合成气的工艺,其以粒径小于75μm的固体含碳颗粒为气化原料,在低于1300℃的气化温度下,与气化剂反应生成合成气。其存在的主要问题在于,气化效率难以进一步提升,气化炉的单位容积处理能力不高,且气化温度仍然高达1300℃,气化炉内衬里受到较大侵蚀,降低衬里的使用寿命,企业运行成本高。
4.虽然本领域技术人员知道,进一步细化固体颗粒粒径能提升气流床气化速率,从而可以降低气化温度、提升气化炉的单位容积处理能力,但是目前为止,气流床气化的原料粒径仍然停留在百微米级别,这其中除了超细颗粒研磨的技术难点外,超细颗粒气化本身也主要存在两大技术难点:一是超细颗粒的气力输送稳定性问题,固体颗粒越细,其流动性越差,气力输送的流量越不稳定,现有气力输送系统无法输送含碳物质的超细颗粒;二是合成气和熔渣、飞灰的分离,固体颗粒粒径进一步降低,虽然带来气化效率的提升,但同时也使飞灰的颗粒尺度进一步减小,飞灰与合成气的分离难度进一步提升,现有技术中的载气输送系统和合成气净化系统不再适用于超细颗粒的气化。
技术实现要素:
5.本实用新型要解决的技术问题是克服了现有气流床气化工艺的气化效率难以进一步提升,单位容积气化炉的处理能力不高,气化温度高、气化炉耐火衬里使用寿命短,企业运行成本高,以及现有技术的载气输送系统以及合成气净化系统不适用于超细颗粒气化的缺陷,提供了一种含碳物质的超细颗粒气化系统,通过进一步细化含碳物质的颗粒粒径,进一步提升气化效率,提高气化炉的处理能力,降低了气化温度,延长了耐火衬里的使用寿命,降低了企业的运行成本,同时提高了超细颗粒输送的稳定性和使合成气中灰含量将到较低水平。
6.本实用新型是通过下述技术方案来解决上述技术问题:
7.本实用新型提供一种含碳物质的超细颗粒气化系统,其包括原料输送单元、气化单元和合成气净化单元;所述原料输送单元的出口与所述气化单元的进口相连,所述气化单元的出口与所述合成气净化单元的进口相连;
8.所述原料输送单元包括载气控制系统和料仓,所述料仓的下端设置有2~10层环管分支,每层所述环管分支均匀设置有4~20个进气口;所述载气控制系统包括电磁阀、脉冲电源控制器和气体分配器,所述脉冲电源控制器与所述电磁阀电连接,所述电磁阀的出口与所述气体分配器的进口连接,所述气体分配器的出口与各所述进气口连接;
9.所述合成气净化单元依次包括旋风分离器、颗粒层过滤器、对流废锅和洗涤塔,所述旋风分离器的进口即为所述合成气净化单元的进口,所述旋风分离器的出口与所述颗粒层过滤器的进口相连,所述颗粒层过滤器的出口与所述对流废锅的进口相连,所述对流废锅的出口与所述洗涤塔的进口相连。
10.本实用新型中,所述环管分支的层数较佳地为4
‑
8,更佳地为6
‑
7。
11.本实用新型中,每层所述环管分支的进气口的数量优选为5
‑
15,更优选为12。
12.本实用新型中,所述料仓的结构设计,结合脉冲式载气加入方式,可以实现超细颗粒均匀且顺畅地下料。结合脉冲气体组合控制,可以实现超细颗粒顺畅且均匀下料,颗粒流量波动小于5%。采用传统的料仓结构以及现有的载气控制方式,超细颗粒在料仓内很容易发生堵塞,超细颗粒的进料流量波动也很大,影响气化炉的稳定运行。
13.本实用新型中,所述气化单元一般包括气化室和辐射废锅,所述气化室的出口即为所述辐射废锅的进口。所述气化室用于所述含碳物质的超细颗粒的气化,所述辐射废锅可用于回收出所述气化室的合成气的热量,同时在所述合成气降温后,其中的固体飞灰或液态熔渣由于重力作用发生部分沉降。
14.本实用新型中,所述气化单元的气化室可采用本领域常规的耐火衬里,例如耐火砖衬里或水冷壁衬里。
15.本实用新型中,较佳地,所述气化系统为固态排渣时,所述气化室采用耐火砖衬里;所述气化系统为液态排渣时,所述气化室采用水冷壁衬里。
16.本实用新型中,来自气化炉的高温合成气首先通过旋风除尘器进行粗颗粒的分离,然后进入颗粒床分离较细颗粒,得到含固量少的合成气再经过对流废锅冷却降温,最后通过水洗塔进行除尘。
17.虽然本实用新型中的旋风分离器、颗粒床、对流废锅以及水洗塔等均为常规的除尘装置,但是对于超细颗粒气化后所得合成气,其中的飞灰因为尺度太小很容易被合成气夹带,导致分离更加困难,所以并非是所有除尘装置的简单组合就能实现本实用新型所得合成气中飞灰的分离效果。
18.本实用新型提供一种含碳物质的超细颗粒的气化工艺,其利用上述的含碳物质的超细颗粒的气化系统,其包括如下步骤:
19.含碳物质的超细颗粒由所述原料输送单元的载气输送至所述气化单元,与气化单元的气化剂进行气化反应,得粗合成气;
20.所述粗合成气通过所述合成气净化单元,即得合成气;
21.所述超细颗粒是指平均粒径小于10μm、最大粒径不超过50μm的颗粒。
22.所述脉冲电源控制器的脉冲频率可为1~60hz,较佳地为10
‑
50hz,更佳地为25hz。
23.本实用新型中,所述含碳物质可为本领域常规,一般地包括煤、石油焦、兰炭、生物质,较佳地为煤。其中,所述煤的种类为本领域常规,较佳地为烟煤。
24.本实用新型中,所述超细颗粒一般是指颗粒平均粒径小于10μm、颗粒最大粒径不超过50μm的颗粒。
25.本实用新型中,所述超细颗粒可采用本领域常规的方法研磨而成,例如机械研磨或气流粉碎,较佳地为气流粉碎。
26.本实用新型中,所述载气可为本领域常规,一般地为n2、co2或空气中的一种或多种,较佳地为n2。
27.本实用新型中,每千克所述含碳物质的超细颗粒对应的所述载气的流量可为0.0025~0.005nm3,较佳地为0.0033nm3。
28.本实用新型中,所述气化剂可为本领域常规,较佳地为氧气、空气、co2和水蒸气中的一种或多种,更佳地为氧气和水蒸气。
29.其中,所述气化剂为氧气和水蒸气时,所述氧气和所述水蒸气的体积比可为(5~1.5):1;较佳地为3:1。
30.本实用新型中,每吨所述含碳物质的超细颗粒对应的所述气化剂的流量可为0.45
‑
0.6nm3。
31.本实用新型中,所述气化工艺为固态排渣时,所述气化剂的流量可为0.45
‑
0.52nm3/kg煤;所述气化工艺为液态排渣时,所述气化剂的流量可为0.5
‑
0.6nm3/kg煤。
32.本实用新型中,所述气化反应的温度可根据排渣方式进行调节,一般地可为800~1700℃。
33.其中,所述气化工艺采用固态排渣时,所述气化反应的温度低于所述含碳物质的灰熔融温度,较佳地,所述气化反应的温度低于所述含碳物质的灰熔融温度100
‑
400℃,更佳地为低于所述含碳物质的灰熔融温度200℃。
34.在某些较佳实施方案中,所述气化工艺为固态排渣,所述气化反应的温度为800~1000℃。
35.其中,所述气化工艺采用液态排渣时,所述气化反应的温度高于所述含碳物质的灰熔融温度,较佳地,所述气化反应的温度高于所述含碳物质的灰熔融温度50
‑
300℃,更佳地为高于所述含碳物质的灰熔融温度150℃。
36.本实用新型中,所述气化反应的停留时间可根据所述超细颗粒的平均粒径进行控制。
37.其中,所述超细颗粒平均粒径为10um时,所述气化反应停留时间可为0.05s~5s,较佳地为1s。
38.其中,所述超细颗粒平均粒径为5um时,所述气化反应停留时间可为0.03s~2s,较佳地为0.5s。
39.本实用新型中,所述气化单元的气化反应停留时间一般是指所述超细颗粒的停留时间。
40.本实用新型中,所述粗合成气一般地包括co(40
‑
60%)、h2(20
‑
30%)、co2(5~10%)、载气(2
‑
5%)、h2o(2
‑
10%)以及随气体一同流出的未气化的含碳固体颗粒、固体飞灰和液态熔渣。
41.在符合本领域常识的基础上,上述各优选条件,可任意组合,即得本实用新型各较佳实例。
42.本实用新型的积极进步效果在于:
43.(1)进一步提高了气化效率,气化炉单位容积处理能力大幅提升,相同处理能力下,气化炉体积仅为现有技术的近四分之一;
44.(2)固态排渣时气化温度可由1400℃降至1000℃以下,比煤耗较现有技术降低可达5.9%,提升了煤炭利用率,比氧耗较现有技术降低可达15%,节约了运行成本,同时也大大降低了气化炉衬里的侵蚀,延长了衬里使用寿命。
45.(3)本实用新型可以实现超细颗粒均匀且顺畅下料,颗粒流量波动性小于5%。
46.(4)经过本实用新型的合成气净化单元所得的合成气中灰含量可降至1mg/nm3以下,达到与传统百微米级别颗粒气化同等水平。
附图说明
47.图1为实施例1的含碳物质的超细颗粒气化系统示意图;
48.图2为实施例1的环管分支结构示意图。
49.11
‑
载气进口;12
‑
电磁阀;121
‑
脉冲电源控制器;13
‑
气体分配器;14
‑
进气口;15
‑
料仓;16
‑
第一煤粉进口;2
‑
气化炉;21
‑
第二煤粉进口;22
‑
气化剂进口;23
‑
辐射废锅;24
‑
粗渣出口;31
‑
旋风分离器;311
‑
含尘合成气进口;312
‑
粗灰出口;32
‑
颗粒层过滤器;321
‑
第一细灰出口;33
‑
对流废锅;331
‑
第二细灰出口;332
‑
循环压缩机;333
‑
循环合成气进口;34
‑
洗涤塔;341
‑
清洁合成气出口;342
‑
循环洗涤水管线;343
‑
外排废水出口。
具体实施方式
50.下面通过实施例的方式进一步说明本实用新型,但并不因此将本实用新型限制在所述的实施例范围之中。
51.实施例1
52.如图1和2所示,料仓15下部设置6层环管分支,每层环管分支的进气口14数量为12个。合成气净化单元包括1个旋风分离器31、2个颗粒层过滤器32、1个对流废锅和1个洗涤塔,2个颗粒层过滤器32之间并联,出对流废锅的部分合成气经回流管线由压缩机输送到旋风分离器中进行二次净化。
53.再参照图1所示的含碳物质的超细颗粒气化系统,输送载气从载气进口11由电磁阀12控制进入气体分配器13;电磁阀12由脉冲电源控制器121进行控制,使得输送载气呈脉冲式分布。输送载气在气体分配器13中被分配成多股气流分别从各个进气口14进入料仓15,料仓15中有自第一粉煤进口16进入的超细煤粉,超细煤粉在脉冲式载气输送下由第二煤粉进口21进入气化炉2,气化剂由气化剂进口22进入气化炉2,超细煤粉和气化剂在气化炉2的气化室内进行气化反应,生成的合成气中在辐射废锅23内进行冷却降温,同时其中的熔渣或大颗粒灰渣因重力作用沉降,从粗渣出口24排出,经降温后的合成气从含尘合成气进口311进入旋风分离器31,其中的粗灰被分离出来,合成气继续进入颗粒层过滤器32中,将细灰分离出来,细灰从第一细灰出口321排出;进一步净化后的合成气进入对流废锅33,对合成气中的细灰进一步分离,细灰从第二细灰出口331排出,部分合成气经循环压缩机
332由循环合成气进口333与气化炉2来的含尘合成气混合进入旋风分离器31,剩余合成气进入洗涤塔34进行洗涤净化,合成气由清洁合成气出口341排出,塔底排出的洗涤水中的一部分经循环洗涤水管线342进入洗涤塔34循环利用,其余部分经外排废水出口343排出。
54.实施例2
55.采用实施例1的气化系统,气化炉压力为4.0mpa,对以表1所示的原料煤进行气化,单个气化系统的处理能力大约2000吨(干基煤)/天。原料煤在传统机械研磨和高速气流研磨的作用下,制备出平均粒径约为8um的颗粒。通过程序控制脉冲加入载气,脉冲频率约为50hz,将超细颗粒连续输送到管道中,颗粒浓度为350kg/m3。在载气的作用下,煤粉与氧气、蒸汽连续送入气化炉。气化温度控制在1400℃,采用液态排渣方式,颗粒在气化炉内停留0.5s后流出,后进入合成气净化单元,进行分离。经过2级旋风、1级颗粒床和1级水洗,含尘量小于1mg/nm3。在该实施例中,反应器的金属外壳直径为1.8m,中心有效空间为1.0m,反应器高度为5m,炉内为平推流快速反应流场。
56.实施例3
57.单个气化系统的处理能力大约1500吨(干基煤)/天,原料煤在传统机械研磨和高速气流研磨的作用下,脉冲频率约为25hz,超细颗粒浓度为300kg/m3,气化温度控制在1050℃
‑
1100℃,采用固态排渣的方式,颗粒在气化炉内停留2s后流出,在该实施例中,反应器的金属外壳直径为2.2m,中心有效空间为1.4m,其他条件与操作均与实施例2相同。
58.对比例1
59.采用表1所示的煤为气化原料,采用传统的气流床粉煤气化炉,气化炉压力为4.0mpa,单个气化系统的处理能力大约1500吨(干基煤)/天。原料煤在传统机械研磨制备出平均粒径约为70um的颗粒;在输送单元以n2为载气,在载气的作用下,煤粉与氧气、水蒸汽连续送入气化炉。气化温度控制在1400℃,颗粒在气化炉内停留8s后流出,后进入合成气净化单元,进行分离。经过1级旋风分离器和1级水洗塔进行除尘,含尘量小于1mg/nm3。在该案例中,反应器的金属外壳直径为3.6m,中心有效空间为2.6m,反应器高度为8m,炉内为近似全混流反应器。
60.表1原料煤的性质
[0061][0062][0063]
表2气化工艺指标和出口气体组成表
[0064]
参数对比例1实施例2实施例3气化炉直径/m3.41.82.2炉膛有效直径/m2.41.01.4表观气速/(m/s)0.8103.2气化室直段高度/m1056气化温度/℃140014001050排渣方式液态排渣液态排渣固态排渣碳转化率/%999999比煤耗/(kg/knm3(co h2 3.12ch4))540540508比氧耗/(nm3/knm3(co h2 3.12ch4))305305262冷煤气效率/%80.180.185.1灰含量/(mg/nm3)<1<1<1
[0065]
各实施例及对比例所用气化炉的尺寸、气化工艺及效果数据见表2。实施例2和实施例3均为超细颗粒粉煤气化,对比例1采用粒径为60
‑
80μm的粉煤进行气化,实施例2和对比例1的气化温度均为1400℃、液态排渣,实施例3采用1050℃、固态排渣的方式,相同处理能力下,本实用新型的超细颗粒气化系统的气化炉体积仅为传统粉煤气化炉的体积的约四
分之一,固态排渣下,气化温度由1400℃可降至1050℃甚至1000度以下,节约了能源、降低了能耗,并且比氧耗下降15%。合成气经本实用新型的合成气净化单元除尘后,含灰量可降至1mg/nm3以下,达到与传统粉煤颗粒气化的同等水平。
再多了解一些
本文用于企业家、创业者技术爱好者查询,结果仅供参考。