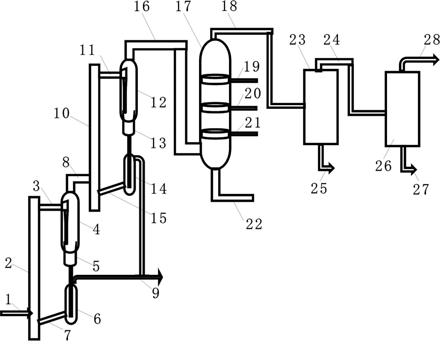
1.本发明属于石油化工领域,具体公开一种最大限度制备乙烯、丙烯及芳烃的方法。
背景技术:
2.原油催化裂解技术可以直接将原油转化为轻质烯烃和芳烃等化学品,这对化解我国炼油产能过剩、化学品供应不足矛盾具有重要意义,它不仅为原油制化学品开辟了一条新的途径,更为炼化企业转型发展增加新引擎,进一步推动企业高质量发展;催化裂化技术是炼油工业发展最迅速、极为重要的二次加工装置,催化裂化反应器形式历经固定床、移动床、流化床发展到现在的提升管反应器,配套的催化剂也由小球催化剂、微球催化剂发展到现在的分子筛催化剂,形成了反应器形式多样、催化剂种类繁多的欣欣向荣的局面,目前我国已拥有单套装置每年加工能力达350万吨的催化裂化装置,随着市场对轻质油需求的加大,可利用石油资源却趋向重质化和劣质化,作为重质油轻质化的重要转化过程之一的催化裂化技术显得尤为重要。
3.近年来,我国的原油催化裂化技术得到了快速发展,已开发出许多新的工艺,例如:洛阳石化工程公司开发一种灵活多效催化裂化工艺
‑
fdfcc工艺,由ripp开发的多产异构烷烃的催化裂化工艺
‑
mip工艺,石油大学(华东)提出的两段提升管催化裂化工艺,中国石油大学(北京)研究开发的催化裂化汽油辅助反应器改质降烯烃技术,洛阳石化工程公司开发的hcc(heavy oil contact cracking process)工艺,上述工艺方法各有优点,但是仍无法解决现有市场对轻质油大量需求与可利用石油资源却趋向重质化和劣质化的矛盾。
技术实现要素:
4.为了解决背景技术中问题,本发明公开一种最大限度制备乙烯、丙烯及芳烃的方法,利用两个串联连接提升管反应器,第一个提升管反应器以原油为原料,在催化剂的作用下进行深度催化裂化,最大化裂化原油,生产低碳烃类,第一个提升管反应后经气固分离所得到的油气是第二个提升管反应器的反应原料,第二个提升管反应器反应后经气固分离所得到的油气经分馏得到产物,两个提升管反应器分别催化反应,两种催化剂分别再生,实现利用原油最大量生产乙烯、丙烯及芳烃的目的。
5.为实现上述发明目的,本发明采用下述技术方案:
6.一种最大限度制备乙烯、丙烯及芳烃的方法,该方法包括下列步骤:
7.(1)原料油自原油罐区进入原料油罐,经原料油泵升压后,通过原料油
‑
轻燃油换热器、原料油
‑
分馏塔
‑
中段油换热器换热至150℃左右过入原料预处理系统,首先进电脱盐罐脱盐,然后经原料油
‑
分馏塔二中段油换热器加热至179℃,再经原料油
‑
循环油换热器加热至220℃左右并与从分馏塔来的回炼油混合后分多路经原料油雾化喷嘴进入低温提升管反应器,与低温催化裂化催化剂接触,进行原料的升温、汽化及反应;
8.(2)低温提升管反应器反应后的油气与待生低温催化裂化催化剂在低温提升管反应器油气出口经粗旋风分离器分离后由升气管密闭进入低温沉降器,经原油单级旋风分离
器后,再进一步除去携带的低温催化裂化催化剂细粉后离开低温沉降器,进入高温提升管反应器与高温裂解催化剂接触进行物料的升温、汽化及反应,高温提升管反应器反应后的油汽与待生高温裂解催化剂在高温提升管反应器油气出口经粗旋风分离器迅速分离后,由升气管密闭进入高温沉降器内经轻油单级旋风分离器后,再进一步除去携带的高温裂解催化剂细粉后进入分馏塔;
9.(3)通过分馏塔分离气体产物和汽油、柴油、重柴油、油浆等液体产物,分馏得到的汽油、柴油进入高温提升管反应器重新裂化,分馏得到的重柴油、油浆、液体产物重新进入低温提升管反应器进行再裂化反应,以尽可能多的生成乙烯丙烯气体,分馏得到的液体产物直至其不能裂化,再外甩得到富含芳烃的汽油、柴油、油浆,进而通过抽提工艺获得芳烃,或者通过加氢反应器进行加氢饱和,生产芳烃类化工产品。
10.进一步地,步骤(2)中从低温提升管反应器出来的积炭的待生低温催化裂化催化剂自粗旋料腿出来,再经沉降器单级旋风分离器料腿出来后,进入汽提段与蒸汽逆流接触,汽提待生低温催化裂化催化剂携带的油汽,汽提后的待生低温催化裂化催化剂沿低温待生立管下流,经待生塞阀、待生催化剂分配器进入低温再生器,在低温再生器内与向上流动的主风逆流接触,完成待生低温催化裂化催化剂烧焦再生,再生后的低温催化裂化催化剂经再生立、斜管及再生滑阀进入低温提升管反应器底部,在干气的提升下,完成低温催化裂化催化剂加速、分散过程,然后与雾化原料接触,重新催化裂化原料。
11.进一步地,步骤(2)中从高温提升管反应器出来的积炭的待生高温裂解催化剂自粗旋料腿及高温沉降器单级旋风分离器料腿出来后进入汽提段,在此与蒸汽逆流接触以汽提待生高温裂解催化剂携带的油汽,汽提后的待生高温裂解催化剂沿待生立管下流,经待生塞阀、待生身催化剂分配器进入高温再生器,在高温再生器内与向上流动的主风逆流接触,完成待生高温裂解催化剂烧焦再生,再生高温裂解催化剂经再生立、斜管及再生滑阀进入高温提升管反应器底部,在由低温提升管反应器油气出口出来的大量油气提升下,完成高温裂解催化剂加速、分散过程,然后与高温提升管反应器内物料接触,重新催化裂化高温提升管反应器内原料。
12.进一步地,低温提升管反应器反应温度控制在450
‑
580℃度之间,剂油比为5
‑
15:1。
13.进一步地,低温再生器温度在600
‑
750℃之间。
14.进一步地,高温提升管反应器反应温度为580
‑
750℃,剂油比为10
‑
30:1。
16.进一步地,高温再生器的温度在750
‑
900℃之间。
17.进一步地,低温催化裂化催化剂是usy筛和zsm
‑
5混合物、reusy和zsm
‑
5混合物或者多产低碳烯烃商品催化剂。
18.进一步地,高温提升管所用的催化剂是sio2、al2o3、mgo、fe2o3、cao、zro2、mno2或tio2中的一种或者一种以上混合物经碱性或碱土金属氧化物改性得到的硅酸铝,并在其中混入沸石或经viii族、viib族或vib族金属离子交换的沸石和金属铁粉末,再经喷雾干燥、焙烧、酸碱处理制备得到的多孔高温裂解催化剂。
19.进一步地,低温再生器和高温再生器烧焦所需的主风分别由主风机提供,主风自大气进入第一主风机,经第二主风机升压、第三主风机升压后经主风管道、辅助燃烧室及主风分布管进入对应的再生器。
20.进一步地,低温再生器和高温再生器产生的烟气分别经多组两级旋风分离器分离催化剂后,进入三级旋风分离器进一步分离催化剂,再经双动滑阀及降压孔板降压后进入余热锅炉回收烟气的热能,烟气温度降到180℃以下经烟气管道排入大气。
21.与现有技术相比,本发明的有益效果是:
22.本发明最大限度制备乙烯、丙烯及芳烃的方法,采用串联连接的低温提升管反应器和高温提升管反应器,低温提升管反应器反应温度低,高温提升管反应器反应温度高,低温提升管反应器采用原油为原料,低温提升管反应器反应后得到的油气和低温催化裂化催化剂气固分离后进入高温提升管反应器进行高温裂解反应,高温提升管反应器反应后油气和高温裂解催化剂气固分离后进入分馏塔分馏,低温提升管反应器和高温提升管反应器共用一套分馏系统,低温提升管反应器和高温提升管反应器使用不同的催化剂,且低温提升管反应器和高温提升管反应器分别连接有催化剂再生器,两种催化剂不混合并分别再生,保持各自的催化性能优势大大提高乙烯、丙烯的产率,两者产率之和达30%,有效缓解现有市场对轻质油大量需求与可利用石油资源却趋向重质化和劣质化的矛盾;
23.本发明采用的低温提升管反应器和高温提升管反应器与其催化剂再生器装置采用同轴式两器布置方案,能够减少设备投资、减少占地,技术先进,操作简单,抗事故能力强,能耗低。
附图说明
24.图1是本发明中最大限度制备乙烯、丙烯及芳烃设备的简图;
25.上图中:1
‑
原油进料管;2
‑
低温提升管反应器;3
‑
低温提升管反应器油气出口;4
‑
低温沉降器;5
‑
低温汽提器;6
‑
低温再生器;7
‑
低温再生斜管;8
‑
高温提升管油气入口;9
‑
烟气管道;10
‑
高温提升管反应器;11
‑
高温油气出口;12
‑
高温沉降器;13
‑
高温汽提器;14
‑
高温再生器;15
‑
高温再生斜管;16
‑
油气管线;17
‑
分馏塔;18
‑
轻烃出口;19
‑
汽油出口;20
‑
柴油出口;21
‑
重柴油出口;22
‑
油浆出口;23
‑
丙烯分离系统;24
‑
干气管线;25
‑
丙烯产品出口;26
‑
乙烯分离系统;27
‑
乙烯产品出口;28
‑
去干气利用系统。
具体实施方式
26.下面将结合本发明实施例中的附图,对本发明实施例中的技术方案进行清楚、完整地描述,显然,所描述的实施例仅仅是本发明一部分实施例,而不是全部的实施例。基于本发明中的实施例,本领域普通技术人员在没有做出创造性劳动前提下所获得的所有其他实施例,都属于本发明保护的范围。
27.本发明一种最大限度制备乙烯、丙烯及芳烃的方法,包括反应
‑
再生、分馏和余热回收步骤,如附图1所示,其配套使用的最大限度制备乙烯、丙烯及芳烃的设备包括串联连接的低温提升管反应器2和高温提升管反应器10,低温提升管反应器2下端进料口与原油进料管1连通,低温提升管反应器2上端的低温提升管反应器油气出口3与低温沉降器4相连通,低温沉降器4下端通过低温汽提器5和再生立管与低温再生器6上端连通,低温再生器6下端通过低温再生斜管7与低温提升管反应器2的下端连通,低温再生器6的上端设置有用于排出烟气的烟气管道9,低温沉降器4上端的通过高温提升管油气入口8与高温提升管反应器10底部进料口相连通,高温提升管反应器10上端的高温油气出口11与高温沉降器12连
通,高温沉降器12下端通过高温汽提器13和再生立管与高温再生器14上端连通,高温再生器14下端通过高温再生斜管15与高温提升管反应器10的下端连通,在高温再生器14的上端还设置有用于排出烟气的烟气管道9,高温沉降器12上端通过油气管线16与分馏塔17下部连通,分馏塔17底部设有油浆出口22,分馏塔17中部设有汽油出口19、柴油出口20和重柴油出口21,分馏塔17顶部通过轻烃出口18与丙烯分离系统23连接,丙烯分离系统23底部设置有丙烯产品出口25,丙烯分离系统23顶部通过干气管线24与乙烯分离系统26连接,乙烯分离系统26顶部与去干气利用系统28连接,乙烯分离系统26底部设置有乙烯产品出口27。
28.由于原油转化为乙烯丙烯的过程不是一步就转化为小分子乙烯丙烯,而是通过多级转化,最后实现转化为乙烯丙烯的,如大庆常压渣油的分子式:c
65
h
111
s
0.04
n
0.24
,因为原油的分子大,裂化反应容易进行,可以在低反应温度下反应,随着裂化的分子逐步变小,裂化时所需的反应温度就要越来越高,较小分子的烃类要转化为更小分子的乙烯丙烯则需要在较高的温度下进行,本发明最大限度制备乙烯、丙烯及芳烃的方法具体包括下列步骤:
29.(1)原料油自原油罐区进入原料油罐,经原料油泵升压后,通过原料油
‑
轻燃油换热器、原料油
‑
分馏塔
‑
中段油换热器换热至150℃左右过入原料预处理系统,首先进电脱盐罐脱盐,然后经原料油
‑
分馏塔二中段油换热器加热至179℃,再经原料油
‑
循环油换热器加热至220℃左右并与从分馏塔17来的回炼油混合后分多路经原料油雾化喷嘴进入低温提升管反应器2中,与低温催化裂化催化剂接触,进行原料的升温、汽化及反应,低温提升管反应器2反应温度控制在450
‑
580℃度之间,控制剂油比为5
‑
15:1,让原油在低温催化裂化催化剂作用下,裂化成中小分子,比如液化气、汽油、柴油组分,同时产生大量的焦炭,得到较小分子的烃类直接全部转入高温提升管反应器10中高温裂解,其生焦量是很低的,然后待生低温催化裂化催化剂在600
‑
750℃之间进行再生;
30.(2)低温提升管反应器2反应后的油气与待生低温催化裂化催化剂在低温提升管反应器油气出口3经粗旋风分离器分离后由升气管密闭进入低温沉降器4,经原油单级旋风分离器后,再进一步除去携带的低温催化裂化催化剂细粉后离开低温沉降器4,进入高温提升管反应器10与高温裂解催化剂接触进行物料的升温、汽化及反应,反应温度为580
‑
750℃,剂油比为10
‑
30:1,高温提升管反应器10反应后的油汽与待生高温裂解催化剂在高温提升管反应器10的高温油气出口11经粗旋风分离器迅速分离后,由升气管密闭进入高温沉降器12内经轻油单级旋风分离器后,再进一步除去携带的高温裂解催化剂细粉后进入分馏塔17,然后待生高温催化裂化催化剂在750
‑
900℃之间进行再生;
31.(3)通过分馏塔17分离气体产物和汽油、柴油、重柴油、油浆等液体产物,分馏得到的汽油、柴油进入高温提升管反应器10重新裂化,分馏得到的重柴油、油浆、液体产物重新进入低温提升管反应器2进行再裂化反应,以尽可能多的生成乙烯丙烯气体,分馏得到的液体产物直至其不能裂化,再外甩得到富含芳烃的汽油、柴油、油浆,进而通过抽提工艺获得芳烃,或者通过加氢反应器进行加氢饱和,生产芳烃类化工产品,实现原油最大量生产乙烯和丙烯的目的,同时保证催化剂性能的稳定发挥。
32.作为可选设计,优选步骤(2)中从低温提升管反应器2出来的积炭的待生低温催化裂化催化剂自粗旋料腿出来及沉降器单级旋风分离器料腿出来后,进入汽提段与蒸汽逆流接触,汽提待生低温催化裂化催化剂携带的油汽,汽提后的待生低温催化裂化催化剂沿低温待生立管下流,经待生塞阀、待生催化剂分配器进入低温再生器6,在低温再生器6内与向
上流动的主风逆流接触,完成待生低温催化裂化催化剂烧焦再生,再生后的低温催化裂化催化剂经再生立、斜管及再生滑阀进入低温提升管反应器2底部,在干气的提升下,完成低温催化裂化催化剂加速、分散过程,然后与雾化原料接触,重新催化裂化原料。
33.作为可选设计,优选步骤(2)中从高温提升管反应器10出来的积炭的待生高温裂解催化剂自粗旋料腿及高温沉降器12单级旋风分离器料腿进入汽提段,在此与蒸汽逆流接触以汽提待生高温裂解催化剂携带的油汽,汽提后的待生高温裂解催化剂沿待生立管下流,经待生塞阀、待生身催化剂分配器进入高温再生器14,高温再生器14的温度在750
‑
900℃之间,在高温再生器14内与向上流动的主风逆流接触,完成待生高温裂解催化剂烧焦再生,再生高温裂解催化剂经再生立、斜管及再生滑阀进入高温提升管反应器10底部,在由低温提升管反应器油气出口3出来的大量油气提升下,完成高温裂解催化剂加速、分散过程,然后与高温提升管反应器10内物料接触,重新催化裂化高温提升管反应器10内原料,高温裂解催化剂具有产生自由基的作用和高温热稳定性,保证催化剂具有较多的孔容和适当的比表面积,可以携带反应生成的焦炭进入再生器进行烧焦碳,再生催化剂,同时给反应系统提供部分热量,对于高温反应所需热量不足的问题,可以通过向高温再生器14,采用小型加料系统补入适量的、廉价的、合适粒度的、低含硫的炭粉实现。
34.作为可选设计,优选低温催化裂化催化剂是usy筛和zsm
‑
5混合物、reusy和zsm
‑
5混合物或者多产低碳烯烃商品催化剂,高温提升管所用的催化剂是sio2、al2o3、mgo、fe2o3、cao、zro2、mno2或tio2中的一种或者一种以上混合物经碱性或碱土金属氧化物改性得到的硅酸铝,并在其中混入沸石或经viii族、viib族或vib族金属离子交换的沸石和金属铁粉末,再经喷雾干燥、焙烧、酸碱处理制备得到的多孔高温裂解催化剂。
35.作为可选设计,优选低温再生器6和高温再生器14烧焦所需的主风分别由主风机提供,主风自大气进入第一主风机,经第二主风机升压、第三主风机升压后经主风管道、辅助燃烧室及主风分布管进入对应的再生器。
36.作为可选设计,优选低温再生器6和高温再生器14产生的烟气分别经多组两级旋风分离器分离催化剂后,进入三级旋风分离器进一步分离催化剂,再经双动滑阀及降压孔板降压后进入余热锅炉回收烟气的热能,烟气温度降到180℃以下经烟气管道9排入大气。
37.本发明以原油为原料,采用较高的反应温度、较深的反应深度,较低的油气分压、较高的剂油比,并在添加了择型分子筛的催化裂解催化剂作用下进行热裂解和催化裂解反应,粗轻油、碳四馏分进高温提升管反应器10,以增产乙烯,生产较多的乙烯,丙烯及高辛烷值轻油。
38.此外,应当理解,虽然本说明书按照实施方式加以描述,但并非每个实施方式仅包含一个独立的技术方案,说明书的这种叙述方式仅仅是为清楚起见,本领域技术人员应当将说明书作为一个整体,各实施例中的技术方案也可以经适当组合,形成本领域技术人员可以理解的其他实施方式。
再多了解一些
本文用于企业家、创业者技术爱好者查询,结果仅供参考。