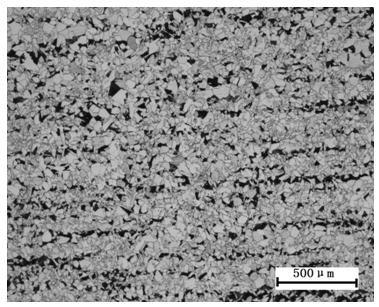
1.本发明涉及工程机械领域,具体涉及一种高低温韧性液压缸缸头缸尾用钢及其制造方法。
背景技术:
2.由于液压缸结构简单、工作稳定性好,它可以实现往复运动时,无需额外的减速装置,且无传动间隙,将液压能直接转化为机械能,运动平稳,广泛应用于工程机械、石油化工等行业。缸头和缸尾作为液压缸中非常重要的零部件,目前加工缸头与缸尾的材料常见为45钢,由于45钢调质后低温韧性较差,使得其装配的液压缸使用环境受到了很大限制,即只能使用在常温环境下,而无法正常使用在低温环境下。为了改善低温条件下的使用性能,常常需要向钢内添加镍元素,而镍元素成本相对较高。
3.从已报道的专利来看,目前关于液压缸方面的专利主要为一些设计和加工领域,而专门针对液压缸的缸头缸尾用钢的专利未见报道,因此开发出一种高低温韧性液压缸缸头缸尾用钢及其制造方法成为一种市场诉求。
技术实现要素:
4.本发明的目的在于:针对在低温环境下使用的液压缸缸头缸尾,提供一种经济可行的高低温韧性液压缸缸头缸尾用钢及其制造方法,克服现有技术存在的缺陷。
5.本发明在化学成分设计时,对于恶化低温韧性的化学元素加以严格控制,而对于既可以提高强度,又可改善或不至于恶化低温韧性的元素的比列给予提高;考虑到非金属夹杂物对低温韧性和疲劳性能的不利影响,在生产工艺路线制定时,该钢种必须经过真空处理,且真空处理选用rh炉;在冶炼时,控制转炉下渣、真空处理、渣面扩散脱氧和喂入丝线变性处理,合理控制软吹时间,促进非金属夹杂物上浮;在轧制工艺方面,为了控制终轧温度,适当降低加热温度。该专利发明钢种具有高纯净度、高低温韧性,用本发明钢种加工的液压缸缸头缸尾低温韧性良好,
‑
40℃的v型冲击功高达190j以上,其生产工艺操作简单,生产成本低,适应性强,可在本行业推广使用。
6.本发明所采取的技术方案是:一种高低温韧性液压缸缸头缸尾用钢,其特征在于:由以下元素按质量百分比组成:c 0.08~0.11 %、si 0.30~0.40%、mn 1.70~1.80%、cr≤0.10%、cu≤0.10%、ni≤0.10%、mo≤0.0080%、v 0.050~0.065%、nb≤0.010%、as≤0.0050%、al 0.020~0.035%、p≤0.013%、s≤0.0050%、b≤0.0008%、ti≤0.0030%、n0.0055~0.0090%,余量为fe和不可避免的杂质元素。
7.本发明进一步改进方案是,所述缸头缸尾用钢,由以下元素按质量百分比组成:c 0.08~0.10%、si 0.35~0.40%、mn 1.70~1.76%、cr≤0.10%、cu≤0.10%、ni≤0.10%、mo≤0.0080%、v 0.055~0.065%、nb≤0.010%、as≤0.0050%、al 0.025~0.035%、p≤0.010%、s≤0.0050%、b≤0.0008%、ti≤0.0030%、n 0.0070~0.0090%,余量为fe和不可避免的杂质元素,其中v/n必须控制在6.11~9.29。
8.下面具体说明本发明对缸头缸尾用钢化学成分的限定理由:c:碳可以提高钢种的强度、硬度,但是碳含量过高会给材料的冲击韧性带来不利影响,所以考虑到碳元素对强韧性相互影响, c含量取0.08~0.11%。
9.si:硅能够提高钢材强度,特别是屈服强度;改善高钢材淬透性、回火稳定性和抗氧化,但硅含量过高时,易导致加热过程中钢中碳的石墨化,促进钢表面脱碳,硅易使钢呈带状组成,硅还会使钢的脆性转变温度升高。综合考虑硅元素对钢材性能的影响,在成分设计时,将si含量确定为0.30~0.40%。
10.mn:考虑到锰元素对强度和韧性的影响,即当mn含量低于1.8%时,随着其含量增加,钢材强度不断增加,而对韧性不会有显著危害。在本钢种的成分设计中,将锰元素作为一种主要的合金元素添加,它可以消除或减弱钢因硫所引起的热塑性,从而改善钢的热加工性能,但锰含量较高时会使钢的晶粒粗化,因此将mn含量确定为1.70~1.80%。
11.v:钒元素在非调质钢已广泛使用,钒元素可以细化组织和晶粒,借鉴与钒元素在细化晶粒和强化组织方面的作用,在该发明钢种中适当添加钒元素,但钒含量不易过高,否则由于v4c3在晶内的弥散析出将导致钢韧性的降低,同时考虑到该元素在成本方面的影响,因此将v含量确定为0.050~0.065%。
12.n:氮可以与钢中钒有较强的亲和力,一般与之化合形成极稳定的氮化物,以不同的形态存在于钢中,这些氮化物若以高度弥散状态分布在钢中,这些弥散分布的氮化物可以限制铁素体晶粒度的长大,从而细化铁素体晶粒,改善钢的低温韧性,但氮含量较高又会恶化钢的韧性,对此在成分设计中,将氮作为一种微量元素添加,n含量确定为0.0055
‑
0.0090%。al:铝作为一种最常用的廉价脱氧剂,用于本钢中在冶炼过程中的脱氧,同时铝的存在可以平衡钢的氧,但铝含量超过0.060%以后,钢中的氧含量变化较小;铝在钢中要发挥其细化晶粒的作用,铝的含量必须大于0.020%;铝含量较高也会带来很多不利的影响。综合考虑上述因素,本发明设计al含量为0.020~0.035%。
13.mo:钼增加钢材淬透性的作用较铬强,钼元素提高强度,且钼的价格较贵,为了发挥本钢种在韧性方面的潜力,在成分设计中,我们将钼元素作为残余元素加以控制。确定mo含量为≤0.0080%。
14.ti:考虑到发明钢中设计了一定量的氮元素,如果向钢中再添加钛元素,将会使得钛与氮之间形成带有棱角的硬质夹杂物,从而降低钢在低温状态下的韧性。综合考虑,将钛元素作为一种有害的残余元素加以控制。确定ti含量为≤0.0030%。
15.p:一般认为磷对钢的抗拉强度有显著作用,但会增加钢的脆性,特别是低温脆性,同时磷会造成严重的偏析和回火脆性。综合考虑,将磷元素作为一种有害的残余元素加以控制。确定p含量为≤0.013%。
16.s:硫对钢的强度影响不大,但由于硫化物夹杂物的存在,却使其延展性及韧性降低,特别是冲击韧性;硫与铁结合形成的硫化铁易在晶界上形成连续的网状组织,在轧制加热容易过热和过烧。综合考虑,将硫元素作为一种有害的残余元素加以控制。确定s含量为≤0.0050%。
17.为了保障强度和韧性的稳定,同时控制生产成本,将cr、ni、cu、b、as作为残余元素加以严格控制。因此cr≤0.10%、cu≤0.10%、ni≤0.10%、b≤0.0008%、as0~0.0050%。
18.生产如上述的缸头缸尾用钢,包括下列步骤:1)铁水脱硫处理:铁水经过kr深度脱硫处理,铁水中硫含量控制在0.008%以内,同时将脱硫渣扒干净,以防止在转炉回硫;2)转炉冶炼:以预脱硫铁水和废钢为原料在顶底复吹式转炉中进行冶炼,采用合适的拉碳0.03~0.07%范围进行操作,出钢温度1630~1670℃,出钢磷和硫分别≤0.009%和≤0.003%,出钢的时候加入350~450kg/炉预熔精炼渣,400~500kg/炉石灰、低钛金属锰,100~150kg/炉低钛铝饼;钢水在吊包之前,钢包底吹氩气搅拌2~4分钟,以便于加入的合金和渣料全部熔化;3)lf精炼:根据到站渣况,可以向钢水中添加50
‑
100kg/炉萤石,快速造二元碱度6~8精炼渣,向渣面添加电石和碳化硅(电石与碳化硅的比例按照5:3)进行渣面脱氧,强化脱硫和去除钢水中非金属夹杂物,添加金属锰进行锰含量微调;在精炼中后期向钢水添加一定量的钒铁;精炼结束后,向钢水中喂入100~150m的纯钙线,丝线的喂入速度必须控制在3~4m/s的范围内;4)rh真空脱气:在真空度<100pa条件下对钢水进行15~20分钟的深度处理,真空处理结束后,向钢水中喂入100~150m/炉氮锰线,钢水软吹时间控制在20~30分钟;5)连铸:在弧形连铸机进行浇铸,使用中间包覆盖剂和专用结晶器保护渣,实行全程全保护浇铸;6)轧钢:采用冷装入炉,在冷床入口处放置10台风压350pa、风量24500m3/h的混流式风机对钢材进行强制冷却,钢材入坑温度控制在350~550℃。
19.本发明的优点在于:第一、本发明的一种高低温韧性液压缸缸头缸尾用钢,根据钢种用途、成本和化学元素对于强韧性的影响,在成分设计中,将碳含量设计较低,从而减少珠光体的量,同时增加铁素体的相对量,达到提高低温韧性的目的;为了补偿碳含量的降低对强度方面的负面影响,增加了钒和氮,且钒氮比必须满足5.56~11.82(最优比为6.11~9.29),通过钒氮析出强化提高强度,同时细化铁素体晶粒,进一步改善低温韧性,最终在强度满足要求的前提下,钢材具有很好的低温冲击韧性。
20.第二、本发明的一种高低温韧性液压缸缸头缸尾用钢的生产工艺,在转炉出钢特意大搅拌2~4分钟,充分利用转炉出钢后热力学上的优势,将渣料全部熔化,为精炼过程创造好动力学上条件,以便于解决非金属夹杂物lf炉精炼前期难以上浮的难题;由于在成分设计中添加了一定量的氮元素,突破氮化钛可以细化晶粒的传统思路,而有意控制钢中钛含量,在合金选择方面使用了低钛金属锰和低钛铝饼;lf炉渣面脱氧剂选取电石和碳化硅两种常见脱氧剂进行自创搭配,探寻出5:3合理配比,充分了脱氧剂的脱氧能力;在夹杂物变性处理时,选取3~4m/s的喂丝速度,可以保证夹杂物变性过程充分;在钢材上冷床前,通过风压350pa和风量24500m3/h混流式风机对钢材进行强制冷却,提高铁素体比例和细化铁素体晶粒。
21.第三、本发明的一种高低温韧性液压缸缸头缸尾用钢的生产工艺,打破传统的工艺设计思路,制定出适宜于钢种冶炼和轧制工艺路线,以合适的工艺路线来提高原材的品质,从而满足高低温韧性的要求。
22.第四、本发明的一种高低温韧性液压缸缸头缸尾用钢及其生产工艺,在轧制比≥3
的前提下使用本发明生产所得高低温韧性液压缸缸头缸尾用钢的热轧状态下
‑
40℃v型冲击功≥190j、下屈服强度≥320mpa、抗拉强度≥490mpa、延伸率≥28%、断面收缩率≥48%,非金属夹杂物(a类夹杂物≤1.0级、b类夹杂物≤1.0级、c类夹杂物≤0.5级、d类夹杂物≤1.0级),奥氏体晶粒细(奥氏体晶粒度≥6.0级)。
附图说明
23.图1为实施例1所得钢的非金属夹杂物a类细系0.5级电镜图;图2为实施例1所得钢的奥氏体晶粒度6.0级电镜图;图3为实施例1所得钢的带状组织1.5级电镜图;图4为实施例2所得钢的非金属夹杂物a类细系1.0级电镜图;图5为实施例2所得钢的奥氏体晶粒度7.0级电镜图;图6为实施例2所得钢的带状组织1.5级电镜图。
24.图7 为实施例3所得钢的奥氏体晶粒度7.0级电镜图;图8 为实施例3所得钢的带状组织2.5级电镜图。
具体实施方式
25.化学成分如下表1和表2所示。
26.表1 主要化学成分(wt%)csimnvalnv/n0.080.361.730.0570.0250.00826.95表2 残余元素(wt%)pscrmotininbascub0.0100.0030.040.00400.00200.040.00600.00300.020.0005采用以下生产工艺制备:1)铁水预处理:铁水采用kr脱硫处理,铁水硫含量0.045%,脱硫剂加入量500kg,搅拌速度80r/min,搅拌时间9分钟。
27.2)转炉冶炼:在90吨的顶底复吹式转炉中冶炼,以铁水75吨与废钢20吨为原料进行初炼,出钢碳0.05%、磷0.009%、硫0.003%、出钢温度1670℃,出钢采用滑板和挡渣锥双挡渣方式防止下渣,转炉出钢加入预熔精炼渣380kg、石灰420kg、低钛金属锰17kg/t、低钛铝饼120kg进行造渣、脱氧、合金化,钢水出完后开氩气大搅拌,保证合金和渣料熔化;3)lf精炼:向钢水中添加50kg萤石,精炼渣的二元碱度为6.5,向渣面添加电石和碳化硅(电石与碳化硅的比例按照5:3)进行渣面脱氧,强化脱硫和去除钢水中非金属夹杂物,添加金属锰进行锰含量微调;在精炼中后期向钢水添加钒铁1.17kg/t;精炼结束后,向钢水中喂入130m的纯钙线,丝线的喂入速度必须控制在3.5m/s;4)rh真空脱气:在真空度<100pa条件下对钢水进行15分钟的深度处理,真空处理结束后,向钢水中喂入120m/炉氮锰线,钢水软吹时间控制在20分钟;5)连铸:在6机6流弧形连铸机进行浇铸,使用中间包覆盖剂和专用结晶器保护渣,实行全程全保护浇铸,浇铸断面为φ500mm,拉速0.32m/min,过热度31℃;6)轧钢:采用冷装入炉,加一段温度1000~1100℃、加热二段温度1160~1200℃、均
热段温度1210~1250℃,在炉时间为8.1小时,轧制钢材规格为φ280mm,在冷床入口处放置10台风压350pa、风量24500m3/h风机对钢材进行强制冷却,钢材入坑温度控制在450℃。
28.热轧状态力学性能如表3、非金属夹杂物见表4和图1。
29.奥氏体晶粒度为6.0级见图2。
30.带状组织1.5见图3。
31.表3 热轧状态力学性能表4非金属夹杂物具体实施方式2:化学成分如下表5和表6所示。
32.表5主要化学成分(wt%)csimnvalnv/n0.100.361.750.0600.0300.00787.69表6 残余元素(wt%)pscrmotininbascub0.0090.0030.030.00350.00250.020.00450.00400.030.0004采用以下生产工艺制备:1)铁水预处理:铁水采用kr脱硫处理,铁水硫含量0.030%,脱硫剂加入量350kg,搅拌速度80r/min,搅拌时间7分钟。
33.2)转炉冶炼:在90吨的顶底复吹式转炉中冶炼,以铁水72吨与废钢20吨为原料进行初炼,出钢碳0.06%、磷0.008%、硫0.002%、出钢温度1630℃,出钢采用滑板和挡渣锥双挡渣方式防止下渣,转炉出钢加入预熔精炼渣372kg、石灰400kg、低钛金属锰16kg/t、低钛铝饼110kg进行造渣、脱氧、合金化,钢水出完后开氩气大搅拌,保证合金和渣料熔化;3)lf精炼:向钢水中添加30kg萤石,精炼渣的二元碱度为6.5,向渣面添加电石和碳化硅(电石与碳化硅的比例按照5:3)进行渣面脱氧,强化脱硫和去除钢水中非金属夹杂物,添加金属锰进行锰含量微调;在精炼中后期向钢水添加钒铁1.10kg/t;精炼结束后,向钢水中喂入120m的纯钙线,丝线的喂入速度必须控制在3.5m/s;4)rh真空脱气:在真空度<100pa条件下对钢水进行15分钟的深度处理,真空处理结束后,向钢水中喂入110m/炉氮锰线,钢水软吹时间控制在20分钟;5)连铸:在6机6流弧形连铸机进行浇铸,使用中间包覆盖剂和专用结晶器保护渣,实行全程全保护浇铸,浇铸断面为φ500mm,拉速0.32m/min,过热度30℃;6)轧钢:采用冷装入炉,加一段温度1000~1100℃、加热二段温度1170~1200℃、均
热段温度1210~1240℃,在炉时间为8.0小时,轧制钢材规格为φ150mm,在冷床入口处放置10台风压350pa、风量24500m3/h风机对钢材进行强制冷却,钢材入坑温度控制在380℃。
34.热轧状态力学性能如表7、非金属夹杂物见表8和图4。
35.奥氏体晶粒度为6.0级见图5。
36.带状组织1.5见图6。
37.表7热轧状态力学性能表8 非金属夹杂物具体实施方式3:化学成分如下表9和表10所示。
38.表9主要化学成分(wt%)csimnvalnv/n0.080.351.720.0580.0290.00807.25表10 残余元素(wt%)pscrmotininbascub0.00100.0050.020.00400.00220.020.00400.00350.040.0005采用以下生产工艺制备:1)铁水预处理:铁水采用kr脱硫处理,铁水硫含量0.028%,脱硫剂加入量340kg,搅拌速度80r/min,搅拌时间8分钟。
39.2)转炉冶炼:在90吨的顶底复吹式转炉中冶炼,以铁水70吨与废钢20吨为原料进行初炼,出钢碳0.05%、磷0.009%、硫0.003%、出钢温度1650℃,出钢采用滑板和挡渣锥双挡渣方式防止下渣,转炉出钢加入预熔精炼渣368kg、石灰390kg、低钛金属锰15.5kg/t、低钛铝饼107kg进行造渣、脱氧、合金化,钢水出完后开氩气大搅拌,保证合金和渣料熔化;3)lf精炼:向钢水中添加29kg萤石,精炼渣的二元碱度为6.4,向渣面添加电石和碳化硅(电石与碳化硅的比例按照5:3)进行渣面脱氧,强化脱硫和去除钢水中非金属夹杂物,添加金属锰进行锰含量微调;在精炼中后期向钢水添加钒铁1.08kg/t;精炼结束后,向钢水中喂入120m的纯钙线,丝线的喂入速度必须控制在3.5m/s;4)rh真空脱气:在真空度<100pa条件下对钢水进行15分钟的深度处理,真空处理结束后,向钢水中喂入115m/炉氮锰线,钢水软吹时间控制在20分钟;5)连铸:在6机6流弧形连铸机进行浇铸,使用中间包覆盖剂和专用结晶器保护渣,实行全程全保护浇铸,浇铸断面为φ500mm,拉速0.32m/min,过热度28℃;6)轧钢:采用冷装入炉,加一段温度1000~1100℃、加热二段温度1165~1190℃、均热段温度1200~1230℃,在炉时间为8.0小时,轧制钢材规格为φ90mm,在冷床入口处放置10
台风压350pa、风量24500m3/h风机对钢材进行强制冷却,钢材入坑温度控制在350℃。
40.热轧状态力学性能如表11、非金属夹杂物见表12。
41.奥氏体晶粒度为7级见图7。
42.带状组织2.5见图8。
43.表11热轧状态力学性能表12 非金属夹杂物
再多了解一些
本文用于企业家、创业者技术爱好者查询,结果仅供参考。