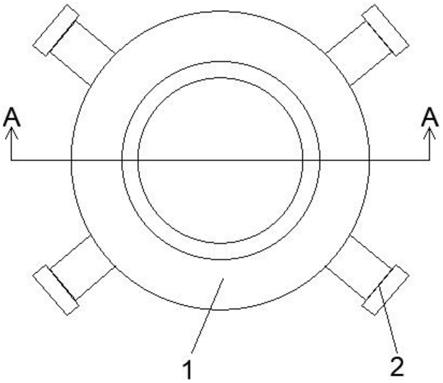
1.本实用新型涉大型自由锻液压机镦粗工装及技术领域,具体为一种高径比大型合金钢锭自由锻液压机分步镦粗组合装置。
背景技术:
2.镦粗是使毛坯高度减小、横断面积增大的锻造工序。对于高合金钢产品生产过程中,采用镦粗
‑
拔长联合锻造工艺有效破坏铸态树枝晶,可破摔碳化物,并使其均匀分布,提高塑性变形方法,为最终产品性能奠定基础。尤其是用于拔长前的镦粗,可减少锻件机械性能的异向性,提高锻件径向的机械性能。但镦粗时高径比太大或太小对镦粗工序都极为不利,所谓的高径比是指镦粗前钢锭高度与镦粗前的钢锭直径之比,一般情况钢锭镦粗前高径比最好控制在2.0~2.5之间,当圆钢锭高径比超过3时,在平砧间镦粗时会产生弯曲现象,且钢锭变形主要集中在上下两端部分,中部变形量小,镦粗后会形成双鼓肚,继而后续拔长过程中产生折叠缺陷;当高径比超过4.0时,钢锭在镦粗时会失稳,如果没有辅助工装,钢锭几乎无法镦粗。这就使得镦粗范围受到局限性。对于高合金钢大型钢锭,强烈镦粗还可能产生纵向裂纹。由于对高合金钢大型钢锭质量要求高,镦粗前钢锭的高径比大于4.0,为后续锻造成形带来严峻困难。
技术实现要素:
3.本实用新型的目的在于提供一种高径比大型合金钢锭自由锻液压机分步镦粗组合装置以解决上述背景技术中提出的问题。
4.为实现上述目的,本实用新型提供如下技术方案:一种高径比大型合金钢锭自由锻液压机分步镦粗组合装置,包括镦粗装置,所述镦粗装置设置有两套,且镦粗装置为锥体结构,所述镦粗装置的锥度为2
‑3°
,所述镦粗装置内壁上端呈圆弧状。
5.进一步地,所述镦粗装置内壁上端的圆弧半径为100
‑
200mm。
6.进一步地,所述镦粗装置的侧壁设有至少两组预留槽,且预留槽内均焊接有吊耳。
7.进一步地,所述镦粗装置的总高度为h1,原始钢锭高度为h0,则h1=k*h0,其中,系数k的取值范围为0.65~0.7。
8.进一步地,所述镦粗装置对钢锭镦粗时的每次变形率为30%~35%,且镦粗后坯料上端面距离镦粗装置上端面为100~200mm。
9.进一步地,所述镦粗装置的厚度不小于150mm。
10.与现有技术相比,本实用新型的有益效果是:本实用新型通过分步多次镦粗,较好地解决了镦粗产生的质量和高合金钢锭偏析问题,锻件力学性能和等向性显著提高。工装结构简单、制造成本低,通用性强,灵活性大,可操作性强。
附图说明
11.图1为本实用新型的结构示意图(实施例三中第一镦粗装置的结构示意图);
12.图2为本实用新型的a
‑
a的结构剖视图(实施例三中第一镦粗装置的结构剖视图);
13.图3为实施例三中第二镦粗装置的结构示意图;
14.图4为实施例三中第二镦粗装置的b
‑
b的结构剖视图;
15.图5为实施例三镦粗成型后坯料的结构示意图。
16.图中:1、镦粗装置;2、吊耳。
具体实施方式
17.下面将结合本实用新型实施例中的附图,对本实用新型实施例中的技术方案进行清楚、完整地描述,显然,所描述的实施例仅仅是本实用新型一部分实施例,而不是全部的实施例。基于本实用新型中的实施例,本领域普通技术人员在没有做出创造性劳动前提下所获得的所有其他实施例,都属于本实用新型保护的范围。
18.实施例一
19.高径比大型合金钢锭自由锻液压机分步镦粗组合装置,包括镦粗装置1,所述镦粗装置1设置有两套,且镦粗装置1为锥体结构,所述镦粗装置1的锥度均为2
°
,所述镦粗装置1内壁上端呈圆弧状。
20.在本实施例中,所述镦粗装置1内壁上端的圆弧半径为200mm。
21.在本实施例中,所述镦粗装置1的侧壁设有至少两组预留槽,且预留槽内均焊接有吊耳2。
22.在本实施例中,所述镦粗装置1的总高度为h1,原始钢锭高度为h0,则h1=k*h0,其中,系数k的取值为0.65。
23.在本实施例中,镦粗后坯料上端面距离镦粗装置1上端面为100mm。
24.在本实施例中,所述镦粗装置1的厚度为150mm。
25.使用过程:步骤一、采用镦粗装置1进行第一次镦粗;
26.步骤二、将第一步镦粗后的钢锭移入第二个镦粗装置1进行第二次镦粗,每次变形率为30%~35%。
27.步骤三、将第二步镦粗后的锭坯经加热,上下端调转180
°
,在平台上进行自由镦粗,镦粗至形成单鼓状坯料,既消除钢锭产生弯曲、失稳的问题,又可提高钢锭总的变形量。完成了高径比大于4.0钢锭的镦粗。
28.实施例二
29.实施例二与实施三不同之处在于:
30.在本实施例中,所述镦粗装置1内壁上端的圆弧半径为100mm。
31.在本实施例中,所述镦粗装置1的锥度均为3
°
。
32.在本实施例中,镦粗后坯料上端面距离镦粗装置1上端面为200mm。
33.其他如同实施例一。
34.实施三
35.以镦粗高合金钢圆钢锭原始直径d0=600mm,高度h0=2500mm,高径比n=2500/600=4.16为例,镦粗装置1设计成两套,且分别为第一镦粗装置和第二镦粗装置,第一镦粗装置和第二镦粗装置的内壁上部均设计成圆弧状,圆弧状的半径均为100mm,装置外坯料受力后发生自由镦粗变形,圆弧状结构避免了装置外端坯料形成台尖角,进而形成折叠,第一镦
粗装置的内壁锥度为2.5
°
,第二镦粗装置的内壁锥度α2设计为2.65
°
,装置内坯料受力后在筒内发生变形,受内壁锥体结构的限制,避免了坯料的侧弯,又便于钢锭镦粗后出模。
36.镦粗装置1总高度h1,h1=(0.65~0.7)d0,镦粗后坯料距离装置上端面约100mm~200mm。
37.第一镦粗装置的总高度h
11
=2500*0.65%=1625mm,圆整后h
11
高度为1600mm。
38.第二镦粗装置的总高度h
12
=(1600 100)*0.65%=1105mm,圆整后h
12
高度为1100mm。
39.第一镦粗装置内壁直径d
11
,按照经验公式计算得出,d
11
=钢锭原始直径d0*[1 热膨胀率(1.5%~2%)] 氧化皮厚度(5mm~8mm) 钢锭与镦粗筒的间隙2*(8mm~10mm)=600mm*(1 2%) 8mm 2*10mm=640mm。
[0040]
第二镦粗装置内壁直径d
12
按照体积不变理论计算得出,钢锭原始体积
[0041]
第二镦粗装置体积
[0042]
由于v0=v2,则
[0043]
(d12 2*1100*tg2.65)2*1100=6002*2500
[0044]
即d
12
=802mm,圆整后d
12
=800mm
[0045]
进一步:第一镦粗装置最大外径尺寸d
01
,d
01
=(d
11
2*h
11
*tg2.5) 2*200
[0046]
=(640 2*1600*tg2.5) 400=1180mm,
[0047]
即d
01
直径约为1200mm,保证镦粗工装的强度。
[0048]
第二镦粗装置最大外径尺寸d
02
,d
02
=(d
12
2*h
12
*tg2.65) 2*200
[0049]
=(800 2*1100*tg2.65) 400=1300mm,
[0050]
即d
02
直径约为1300mm,保证镦粗工装的强度。
[0051]
使用过程:步骤一、将加热后的钢锭放入第一镦粗装置后,进行第一步镦粗,钢锭镦粗后高度为1700mm,镦粗变形量为2500
‑
1700=800mm,变形率为800/2500*100%=32%,满足要求。
[0052]
步骤二、将第一步镦粗后的钢锭移入第一镦粗装置中进行第二步镦粗,镦粗后高度为1200mm,镦粗变形量为1700
‑
1200=500mm,变形率为500/1700*100%=30%,满足要求。
[0053]
步骤三、将镦粗后的锭坯经加热,上下端调转180
°
,在平台上进行自由镦粗,镦粗至形成单鼓状坯料,既消除钢锭产生弯曲、失稳的问题,又可提高钢锭总的变形量。完成高径比大于4.0钢锭的镦粗,镦粗成型后坯料见图5。
[0054]
其他如同实施一。
[0055]
尽管参照前述实施例对本实用新型进行了详细的说明,对于本领域的技术人员来说,其依然可以对前述各实施例所记载的技术方案进行修改,或者对其中部分技术特征进行等同替换,凡在本实用新型的精神和原则之内,所作的任何修改、等同替换、改进等,均应包含在本实用新型的保护范围之内。
再多了解一些
本文用于企业家、创业者技术爱好者查询,结果仅供参考。