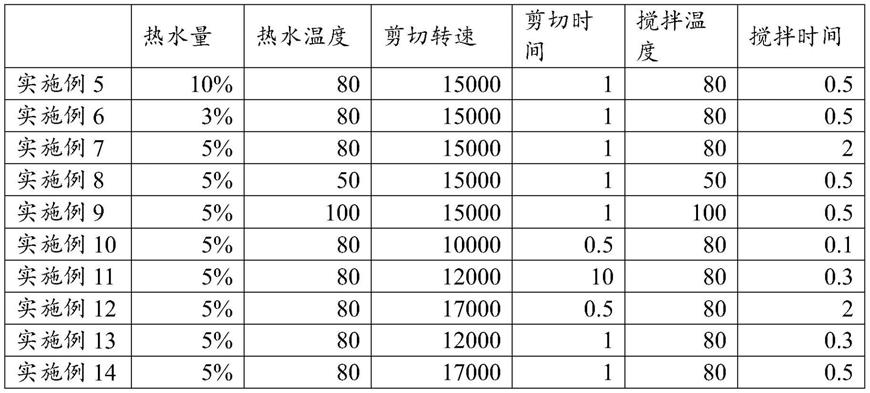
2h。
17.在一些实施方案中,在加水前先将菜籽油或菜籽毛油加热至50-80℃,优选60-70℃。
18.在一些实施方案中,在步骤1)中,水的温度为50-100℃,优选60-80℃。
19.在一些实施方案中,步骤1)中的剪切涉及以8000-18000rpm,优选10000-17000rpm剪切0.5-10分钟,优选1-8分钟。
20.在一些实施方案中,在步骤1)中,在加水前先将菜籽油或菜籽毛油加热至50-100℃,优选60-80℃。
21.在一些实施方案中,在步骤1)中,将剪切而乳化后的菜籽油或菜籽毛油在50-100℃,优选60-80℃下搅拌0.1-10小时,优选0.3-7小时。
22.在一些实施方案中,步骤2)中的离心于5000-12000g,优选7000-10000g下进行1-20分钟,优选5-15分钟。
23.在第二方面,本技术涉及一种菜籽油乳化物,其通过第一方面所述的方法制备。
24.在第三方面,本技术涉及一种制备菜籽油的方法,其包括将第二方面所述的菜籽油乳化物干燥以得到最终的菜籽油。
25.在一些实施方案中,所述干燥在真空下进行。
26.在一些实施方案中,所述干燥在50-150℃,优选70-120℃下进行。
27.在第四方面,本技术涉及一种制备菜籽油的方法,其包括在菜籽油产品中加入至少1重量%,优选3-10重量%的第二方面所述的菜籽油乳化物并干燥以得到最终的菜籽油。
28.在一些实施方案中,所述干燥在真空下进行。
29.在一些实施方案中,所述干燥在50-150℃,优选70-120℃下进行。
30.在第五方面,本技术涉及第二方面所述的菜籽油乳化物用于提高菜籽油的糖含量或粘度的用途。
31.在第六方面,本技术涉及一种菜籽油,其通过第三方面或第四方面所述的方法制备。
32.在一些实施方案中,所述菜籽油中的总糖含量为0.02-0.1重量%,优选0.04-0.07重量%。
33.在第七方面,本技术涉及一种调和油,其包含第六方面所述的菜籽油。
34.本技术可以利用初榨后的菜籽毛油或商购的菜籽油进行提取,得到了高粘度的浓香菜籽油。此外,本技术工艺过程简单,易于工业化生产,生产效率较高。
35.发明的详细描述
36.提供以下定义和方法以更好地界定本技术以及在本技术实践中指导本领域普通技术人员。除非另作说明,本技术的术语按照相关领域普通技术人员的常规用法理解。
37.定义
38.本文使用的术语“约”指所记载的数字的
±
10%,例如约1%指的0.9%至1.1%的范围。
39.本文使用的术语“菜籽油”,又称为菜油、油菜籽油、香菜油、芸苔油、香油、芥花油,是用油菜籽榨出来的一种食用油。是中国的主要食用油之一,主产于长江流域及西南、西北等地,产量居世界首位。菜籽油色泽金黄或棕黄,有一定的刺激气味。这种气味是其中含有
一定量的芥子甙所致,但特优品种的油菜籽则不含这种物质。
40.本文使用的术语“毛油”是指从植物油料中制取、没经过精炼加工的初级油。毛油由于加工工艺简单,含杂质多、易氧化变质,不宜长期储存。本文使用的术语“菜籽毛油”是指从菜籽中制取、没经过精炼加工的初级油。
41.本文使用的术语“饼粉”是指菜籽经过蒸炒后压榨出油脂之后的菜籽残余物,其中水分含量较少,同时还会剩余少量油脂。
42.本文使用的术语“糖脂”属于脂类化合物,广泛存在于各种生物体中。自然界中的糖脂可按其组分中的醇基种类而分为两大类:甘油基糖脂及鞘糖脂。糖基化的甘油醇脂类称为甘油基糖脂,存在于动物的神经组织、植物和微生物中,是植物中的主要糖脂。
43.本文使用的术语“粘度”是指流体对流动所表现的阻力。当流体(气体或液体)流动时,一部分在另一部分上面流动时,就受到阻力,这是流体的内摩擦力。要使流体流动就需在流体流动方向上加一切线力以对抗阻力作用。根据消费者调研,发现消费者更倾向于高粘度的菜籽油,而菜籽油的粘度和其微量成分含量成正相关。
44.本文使用的术语“菜籽油产品”是指可从市场上商购获得的可食用的菜籽油,或者通过本领域内的公知方法制备的可食用的菜籽油。
具体实施方式
45.植物中含量最高的糖脂是甘油基糖脂,在菜籽油中甘油基糖脂主要是单半乳糖甘油酯和双半乳糖甘油酯。本技术通过对菜籽油或菜籽毛油进行提取,得到一定总糖含量的浓香菜籽油,提高菜籽油中糖脂含量,提高菜籽油粘度,得到具有更好烹饪特性的浓香菜籽油产品,提高浓香菜籽油的烹饪消费体验。
46.在第一方面,本技术提供了一种制备菜籽油乳化物的方法,其包括如下步骤:
47.1)在菜籽油或菜籽毛油中加入2-10重量%,优选3-7重量%,更优选4-6重量%的水并对其进行剪切而乳化;和
48.2)将剪切而乳化后的菜籽油或菜籽毛油离心,弃去上清液,从而得到菜籽油乳化物。
49.在一些实施方案中,在步骤1)之前,在菜籽油或菜籽毛油中加入0.1-10重量%,优选0.3-5重量%,更优选0.5-3重量%的饼粉。
50.在一些实施方案中,在加入了饼粉后,将菜籽油或菜籽毛油搅拌0.5-3h,优选1-2h。
51.在一些实施方案中,将搅拌后的菜籽油或菜籽毛油于1000-10000g,优选3000-7000g下离心。
52.在一些实施方案中,在加入饼粉前先在菜籽油或菜籽毛油中加入0.5-5重量%,优选1.5-3重量%的水并离心。
53.在一些实施方案中,所述离心于1000-10000g,优选3000-7000g下进行。
54.在一些实施方案中,在加水后离心前先将菜籽油或菜籽毛油搅拌0.5-3h,优选1-2h。
55.在一些实施方案中,在加水前先将菜籽油或菜籽毛油加热至50-80℃,优选60-70℃。
56.在一些实施方案中,在步骤1)中,水的温度为50-100℃,优选60-80℃。
57.在一些实施方案中,步骤1)中的剪切涉及以8000-18000rpm,优选9000-17000rpm,更优选10000-16000rpm,甚至更优选11000-15000rpm,最优选12000-14000rpm剪切0.5-10分钟,优选1-8分钟。
58.在一些实施方案中,在步骤1)中,在加水前先将菜籽油或菜籽毛油加热至50-100℃,优选60-80℃。
59.在一些实施方案中,在步骤1)中,将剪切而乳化后的菜籽油或菜籽毛油在50-100℃,优选60-80℃下搅拌0.1-10小时,优选0.3-7小时。
60.在一些实施方案中,步骤2)中的离心于5000-12000g,优选7000-10000g下进行1-20分钟,优选5-15分钟。
61.在第二方面,本技术涉及一种菜籽油乳化物,其通过第一方面所述的方法制备。
62.在第三方面,本技术涉及一种制备菜籽油的方法,其包括将第二方面所述的菜籽油乳化物干燥以得到最终的菜籽油。
63.在一些实施方案中,所述干燥在真空下进行。
64.在一些实施方案中,所述干燥在50-150℃,优选70-120℃下进行。
65.在第四方面,本技术涉及一种制备菜籽油的方法,其包括在菜籽油产品中加入至少1重量%,优选3-10重量%的第二方面所述的菜籽油乳化物并干燥以得到最终的菜籽油。
66.在一些实施方案中,所述干燥在真空下进行。
67.在一些实施方案中,所述干燥在50-150℃,优选70-120℃下进行。
68.在第五方面,本技术涉及第二方面所述的菜籽油乳化物用于提高菜籽油的糖含量或粘度的用途。
69.在第六方面,本技术涉及一种菜籽油,其通过第三方面或第四方面所述的方法制备。
70.在一些实施方案中,所述菜籽油中的总糖含量为0.02-0.1重量%,优选0.04-0.07重量%。
71.在第七方面,本技术涉及一种调和油,其包含第六方面所述的菜籽油。
72.本说明书和权利要求书中,词语“包括”、“包含”和“含有”意指“包括但不限于”,且并非意图排除其他部分、添加物、组分、或步骤。
73.应该理解,在本发明的特定方面、实施方案或实施例中描述的特征、特性、组分或步骤,可适用于本文所描述的任何其他的方面、实施方案或实施例,除非与之矛盾。
74.上述公开内容总体上描述了本技术,通过下面的实施例进一步示例本技术。描述这些实施例仅为说明本技术,而不是限制本技术的范围。尽管本文中使用了特殊的术语和值,这些术语和值同样被理解为示例性的,并不限定本技术的范围。除非特别指明,本说明书中的实验方法和技术为本领域常规的方法和技术。对于其它没有特别注明厂家的材料和设备等,其通常是可通过商业途径常规获得的。
75.实施例
76.在本技术的实施例和对比例中,如没有特别指明,所用原料皆为常规原料,可通过市购获得。
77.除非另有说明,本技术中的各种比例均为重量比。
78.以下实施例和对比例中使用的测定方法简述如下:
79.油脂总糖含量使用bmg labtech品牌fluostar omega全自动多功能酶标仪进行测量,具体步骤如下:
80.取1g菜籽油试样于磨口圆底烧瓶中,移取25ml 1mol/lkoh乙醇溶液(无醛乙醇),于40℃的水浴中放置20min,滴加2ml盐酸(质量分数为36%),水浴加热15min,加7ml 1mol/lkoh溶液,定容至25ml),离心分离。精密移取上清液2ml于10ml离心管,80℃以下蒸干,加蒸馏水2ml溶解。
81.向离心管中加2ml菲林试剂,沸水浴加热10min,离心5min,弃去上层清液,加2ml硫酸-钼酸铵溶液(钼酸铵-硫酸溶液:钼酸铵2.5g,加浓硫酸15ml,加水溶解至100ml)显色剂,稀释,定容至100ml,静置30min,用紫外分光光度计测定吸光度,并在半乳糖标准曲线上查出半乳糖含量。总糖含量计算如下:x=ρ
×
v
×
100%/m,其中x为总糖含量;ρ为根据标准曲线查出的半乳糖质量浓度,g/l;v为定容体积,ml;m为菜籽油重量,g。
82.油脂粘度利用anton paar公司svm3000型运动粘度计进行测量,测量方法如下:
83.用注射器吸取6ml油样,将油样连接到进样口,缓慢而均匀注入2ml液体,按“start”进行润洗,润洗15s后按“start”停止转动,进样1ml进行测定,记录数据后可再进样1ml重复测定。
84.实施例1
85.通过如下步骤来制备菜籽油:
86.1.清理菜籽,去除其中的秸秆、石头等杂质;
87.2.炒籽至170℃后出料,进榨油机(香格榨油机,型号px7)榨油,得到菜籽毛油;
88.3.将菜籽毛油加热至60℃,加入1.5%的水后搅拌1h,3000g离心后加入0.5%饼粉(即第2步榨油后所剩的菜饼残渣,其中含有少量水分和少量油脂)搅拌1h,3000g离心后得到菜籽油;
89.4.将菜籽油加热至80℃,加入5%的80℃热水,15000rpm剪切(fluko fa25-digital数显高剪切乳化机)1min,80℃继续加热搅拌0.5h;
90.5.取加水剪切而乳化后的菜籽油于8000g下离心10min;
91.6.取离心后的下层乳化层,100℃真空干燥得到高粘度菜籽油。
92.实施例2
93.通过如下步骤来制备菜籽油:
94.1.清理菜籽,去除其中的秸秆、石头等杂质;
95.2.炒籽至170℃后出料,进榨油机(香格榨油机,型号px7)榨油,得到菜籽毛油;
96.3.将菜籽毛油加热至60℃,加入1.5%的水后搅拌1h,3000g离心后加入0.5%饼粉(即第2步榨油后所剩的菜饼残渣,其中含有少量水分和少量油脂)搅拌1h,3000g离心后得到菜籽油;
97.4.将菜籽油加热至80℃,加入5%的80℃热水,15000rpm剪切(fluko fa25-digital数显高剪切乳化机)1min,80℃继续加热搅拌0.5h;
98.5.取加水剪切而乳化后的菜籽油于8000g下离心10min;
99.6.取离心后的下层乳化层,取乳化层5g,加入100g商购可获得的菜籽油产品中,100℃真空干燥得到高粘度菜籽油。
100.实施例3
101.通过如下步骤来制备菜籽油:
102.1.清理菜籽,去除其中的秸秆、石头等杂质;
103.2.炒籽至170℃后出料,进榨油机(香格榨油机,型号px7)榨油,得到菜籽毛油;
104.3.将菜籽毛油加热至60℃,加入1.5%的水后搅拌1h,3000g离心后加入0.5%饼粉(即第2步榨油后所剩的菜饼残渣,其中含有少量水分和少量油脂)搅拌1h,3000g离心后得到菜籽油;
105.4.将菜籽油加热至80℃,加入5%的80℃热水,15000rpm剪切(fluko fa25-digital数显高剪切乳化机)1min,80℃继续加热搅拌0.5h;
106.5.取加水剪切而乳化后的菜籽油于8000g下离心10min;
107.6.取离心后的下层乳化层,取乳化层8g,加入100g商购可获得的菜籽油产品中,100℃真空干燥得到高粘度菜籽油。
108.实施例4
109.通过如下步骤来制备菜籽油:
110.1.清理菜籽,去除其中的秸秆、石头等杂质;
111.2.炒籽至170℃后出料,进榨油机(香格榨油机,型号px7)榨油,得到菜籽毛油;
112.3.将菜籽毛油加热至60℃,加入1.5%的水后搅拌1h,3000g离心后加入0.5%饼粉(即第2步榨油后所剩的菜饼残渣,其中含有少量水分和少量油脂)搅拌1h,3000g离心后得到菜籽油;
113.4.将菜籽油加热至80℃,加入5%的80℃热水,15000rpm剪切(fluko fa25-digital数显高剪切乳化机)1min,80℃继续加热搅拌0.5h;
114.5.取加水剪切而乳化后的菜籽油于8000g下离心10min;
115.6.取离心后的下层乳化层,取乳化层10g,加入100g商购可获得的菜籽油产品中,100℃真空干燥得到高粘度菜籽油。
116.实施例5-实施例14
117.实施例5-14制备乳化层的操作步骤与实施例2基本上相同,除了第4步的操作步骤略有不同。现在以下表格中列出实施例5-14的第4步中与实施例2不同的操作。
[0118][0119]
对比例1
[0120]
通过如下步骤来制备菜籽油:
[0121]
1.清理菜籽,去除其中的秸秆、石头等杂质;
[0122]
2.炒籽至170℃后出料,进榨油机(香格榨油机,型号px7)榨油,得到菜籽毛油;
[0123]
3.将菜籽毛油加热至60℃,加入1.5%的水后搅拌1h,3000g离心后加入0.5%饼粉(即第2步榨油后所剩的菜饼残渣,其中含有少量水分和少量油脂)搅拌1h,3000g离心后得到菜籽油。
[0124]
对比例2
[0125]
通过如下步骤来制备菜籽油:
[0126]
1.清理菜籽,去除其中的秸秆、石头等杂质;
[0127]
2.炒籽至170℃后出料,进榨油机(香格榨油机,型号px7)榨油,得到菜籽毛油;
[0128]
3.将菜籽毛油加热至60℃,加入1%的水后搅拌1h,3000g离心后加入0.5%饼粉(即第2步榨油后所剩的菜饼残渣,其中含有少量水分和少量油脂)搅拌1h,3000g离心后得到菜籽油;
[0129]
4.将菜籽油加热至80℃,加入1%的80℃热水,15000rpm剪切(fluko fa25-digital数显高剪切乳化机)1min,80℃继续加热搅拌0.5h;
[0130]
5.取加水剪切而乳化后的菜籽油于8000g下离心10min。
[0131]
对比例3
[0132]
通过如下步骤来制备菜籽油:
[0133]
1.清理菜籽,去除其中的秸秆、石头等杂质;
[0134]
2.炒籽至170℃后出料,进榨油机(香格榨油机,型号px7)榨油,得到菜籽毛油;
[0135]
3.将菜籽毛油加热至60℃,加入5%的水后搅拌1h,3000g离心后加入0.5%饼粉(即第2步榨油后所剩的菜饼残渣,其中含有少量水分和少量油脂)搅拌1h,3000g离心后得到菜籽油;
[0136]
4.将菜籽油加热至80℃,加入5%的80℃热水,20000rpm剪切(fluko fa25-digital数显高剪切乳化机)1min,80℃继续加热搅拌0.5h;
[0137]
5.取加水剪切而乳化后的菜籽油于8000g下离心10min。
[0138]
对比例4
[0139]
通过如下步骤来制备菜籽油:
[0140]
1.清理菜籽,去除其中的秸秆、石头等杂质;
[0141]
2.炒籽至170℃后出料,进榨油机(香格榨油机,型号px7)榨油,得到菜籽毛油;
[0142]
3.将菜籽毛油加热至60℃,加入5%的水后搅拌1h,3000g离心后加入0.5%饼粉(即第2步榨油后所剩的菜饼残渣,其中含有少量水分和少量油脂)搅拌1h,3000g离心后得到菜籽油;
[0143]
4.将菜籽油加热至80℃,加入5%的80℃热水,5000rpm剪切(fluko fa25-digital数显高剪切乳化机)1min,80℃继续加热搅拌0.5h;
[0144]
5.取加水剪切而乳化后的菜籽油于8000g下离心10min。
[0145]
对比例2-4无法像实施例1-14那样通过第5步的离心而获得乳化层。
[0146]
实施例1-14和对比例1制备的菜籽油中的总糖含量和菜籽油粘度结果如下:
[0147] 菜籽油中的总糖含量(%)菜籽油粘度(mpa
·
s)
实施例10.246%83.659实施例20.041%66.564实施例30.06%68.235实施例40.09%70.892实施例50.050%67.462实施例60.040%66.607实施例70.038%66.483实施例80.048%67.334实施例90.051%67.551实施例100.050%67.510实施例110.051%67.552实施例120.056%68.015实施例130.031%65.894实施例140.043%66.920对比例10.024%65.296
[0148]
从上述结果可以看出,实施例1-14中的菜籽油的总糖含量和粘度均优于对比例1。可见,实施例1-14中的剪切乳化步骤对获得高糖含量和高粘度的菜籽油至关重要。
[0149]
可以理解,尽管本技术以某种形式被说明,但本技术并不局限于本说明书中所显示和描述的内容。对本领域的技术人员显而易见的是,在不偏离本技术的范围的前提下还可做出各种变化。这些变化都在本技术要求保护的范围内。
再多了解一些
本文用于企业家、创业者技术爱好者查询,结果仅供参考。