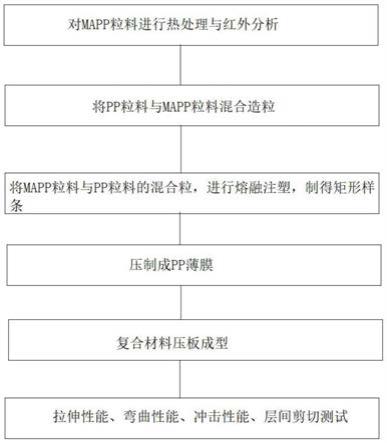
1.本发明属于复合材料的制备方法领域,尤其涉及一种碳纤维织物增强热塑性复合材料的制备方法。
背景技术:
2.复合材料是由两种或者两种以上不同性质的材料通过物理或者化学的方法在宏观上组成具有新的性能的材料,古代普通建筑用的土坯是一种由胶泥和农作物秸秆制成的复合材料,20 世纪40 年代,因航空工业的需要,发展了玻璃纤维增强塑料(俗称玻璃钢),从此出现了复合材料这一名称。50 年代以后,陆续发展了碳纤维、石墨纤维和硼纤维等高强度和高模量纤维。70 年代出现了芳纶纤维和碳化硅纤维。这些高强度、高模量纤维能与合成树脂、碳、石墨、陶瓷、橡胶等非金属基体或铝、镁、钛等金属基体复合,构成各具特色的复合材料。
3.现代高科技的发展离不开复合材料,复合材料对现代科学技术的发展,有着十分重要的作用。聚合物基复合材料是目前复合材料的主要品种,产量远远超过其他的复合材料,按照基体的不同可以分为两大类:热塑性复合材料和热固性复合材料。树脂基复合材料已经在航空航天、汽车工业、运动器材和建筑等领域得到了广泛的应用,复合材料的研究深度和应用广度及其生产发展的速度和规模,已成为衡量一个国家科学技术先进水平和居民生活水平的重要标志之一。
技术实现要素:
4.为了解决上述技术问题,本发明提供一种碳纤维织物增强热塑性复合材料的制备方法,包括碳纤维织物、pp粒料、mapp粒料、热重分析仪、微型双螺杆挤出机、平板硫化机、鼓风机,所述碳纤维织物增强热塑性复合材料的制备方法为:s1:对mapp粒料进行热处理与红外分析:采用热重分析仪,在氮气气氛下,用温控磨具在150℃和210℃条件下分别对maoo粒料进行热处理20min,并分别对纯的pp粒料、mapp粒料、在150℃处理过的mapp粒料以及在210℃处理过的mapp粒料进行红外光谱的表征;s2:将pp粒料与mapp粒料混合造粒:将mapp粒料与pp粒料按照mapp粒料/pp粒为5%-20%的重量份进行配比,并将混合配比后的粒料分别放入微型双螺杆挤出机中,将螺速首先调至40rpm,转动4min后再将螺速调至50rpm,转动3min,挤出mapp粒料与pp粒料的混合粒,进行混合造粒;s3:将mapp粒料与pp粒料的混合粒,进行熔融注塑,制得矩形样条;s4:压制成pp薄膜:将矩形样条放置在两块平板模具中,利用平板硫化机在210℃温度下压制成膜,制成pp薄膜;s5:复合材料压板成型:先将碳纤维织物与pp薄膜放进鼓风机在80℃的温度下烘干8h,再将烘干后的碳纤维织物与pp薄膜交替叠放在已经预热的平板硫化机的平板模具内,当平板模具升温至220℃采用三段式加压的方式对平板模具进行加压,制得的复合材料冷却至
室温成型;s6:对压制好的复合材料分别进行拉伸性能、弯曲性能、冲击性能、层间剪切测试。
5.优选的,所述mapp粒料是通过对pp粒料的分子链进行接枝改性,在pp粒料的大分子链上引入极性的支链来改善pp粒料分子链的刚性、亲水性、亲油性、与无机填料的相容性。
6.优选的,所述热重分析仪的型号为德国耐驰209 f1型,升温速率为10 ℃/min,最高温度为300℃。
7.优选的,所述pp薄膜压制成后长度为200mm、宽度为150mm、厚度为0.2mm。
8.优选的,所述mapp粒料/pp粒的重量份可以为mapp粒料/pp粒料=5%、mapp粒料/pp粒料=10%、mapp粒料/pp粒料=15%、mapp粒料/pp粒料=20%四种不同配比。
9.与现有技术相比,本发明的有益效果为:通过对制得的不同配比的复合材料分别进行拉伸性能、弯曲性能、冲击性能、层间剪切测试,制得的不同配比的复合材料的拉伸性能、弯曲性能、冲击性嫩以及层间剪切性能均有所提高。
附图说明
10.图1是本发明的步骤示意图;图2是本发明的mapp的热失重示意图;图3是本发明纯pp材料,未处理的mapp材料、150℃处理的mapp、200℃处理的mapp材料的红外光谱图;图4是本发明的五种不同配比的复合材料的拉伸性能、冲击性能测试中拉伸强度和拉伸模量对比图;图5是本发明的五种不同配比的复合材料的拉伸性能、冲击性能测试中冲击强度对比图;图6是本发明的五种不同配比的复合材料的弯曲性能、层间剪切测试中拉伸强度和拉伸模量对比图;图7是本发明的五种不同配比的复合材料的弯曲性能、层间剪切测试中冲击强度对比图。
具体实施方式
11.下面将结合本发明实施例的附图,对本发明实施例中的技术方案进行清楚、完整地描述,显然,所描述的实施例仅仅是本发明一部分实施例,而不是全部的实施例。基于本发明中的实施例,本领域普通技术人员在没有做出创造性劳动前提下所获得的所有其他实施例,都属于本发明保护的范围。
12.以下对本发明做进一步描述:实施例:如附图1所示,一种碳纤维织物增强热塑性复合材料的制备方法,包括碳纤维织物、pp粒料、mapp粒料、热重分析仪、微型双螺杆挤出机、平板硫化机、鼓风机,所述pp材料基体中加入马来酸酐接枝共聚的mapp材料作为一种偶联剂,所述mapp粒料通过对pp粒料的分子链进行接枝改性,在pp粒料的大分子链上引入极性的支链来改善pp粒料分子链的刚性、亲水
性、亲油性、与无机填料的相容性。
13.具体的,所述碳纤维织物增强热塑性复合材料的制备方法为:(1)对mapp粒料进行热处理与红外分析:采用德国耐驰209 f1型热重分析仪,其升温速率为10 ℃/min,最高温度为300℃,在氮气气氛下,用温控磨具在150℃和210℃条件下分别对maoo粒料进行热处理20min,分别对纯的pp粒料、mapp粒料、在150℃处理过的mapp粒料以及在210℃处理过的mapp粒料进行红外光谱的表征,通过热失重实验、热处理和红外光谱测试来探索并分析热处理对mapp性能的影响,尤其是对mapp极性的影响,如附图2所示,在150℃和200℃之间观察到了很明显的热失重现象。如附图3所示,其中a表示纯pp材料,b表示未处理的mapp材料,c表示经过150℃处理的mapp材料,d表示经过200℃处理的mapp材料,经过图中对比可以发现相对纯的pp材料、未处理的mapp材料、150℃处理的mapp材料、200℃处理的mapp材料的在1780和1710cm-1
处出现两个新的吸收峰,这两个吸收峰分别对应的是羰基c=o和羧基cooh,在mapp材料制备的过程中,mapp的粒料中会残存部分马来酸酐(ma)单体,这些游离于pp分子链之外的ma单体在受热的状态下很容易挥发出去,同时pp分子链上接枝的部分酸酐基团在受热部分发生水解,产生更多的羧基官能团。故从图中发现b、c、d三条曲线上在1780(c=o)和1710cm-1
(cooh)两处的吸收峰依次变弱,尤其是在1780的吸收峰位置处更为明显。从图2-7中的曲线d,可以得出经过210℃处理20min的mapp依然有足够的极性作为pp和cff间的偶联剂;(2)将pp粒料与mapp粒料混合造粒:将mapp粒料与pp粒料分别按照mapp粒料/pp粒料=5%、mapp粒料/pp粒料=10%、mapp粒料/pp粒料=15%、mapp粒料/pp粒料=20%的重量份进行配比,并将混合配比后的粒料分别放入微型双螺杆挤出机中,将螺速首先调至40rpm,转动4min后再将螺速调至50rpm,转动3min,分别挤出不同配比的mapp粒料与pp粒料的混合粒,进行混合造粒,根据配比的大小依次命名m-pp-5、m-pp-10、m-pp-15、m-pp-20;(3)分别将m-pp-5、m-pp-10、m-pp-15、m-pp-20四种不同配比的混合粒,进行熔融注塑,制得不同配比的矩形样条;(4)压制成pp薄膜:将四种不同配比的矩形样条分别放置再两块平板模具中,利用平板硫化机在210℃温度下压制成膜,制成m-pp-5、m-pp-10、m-pp-15、m-pp-20不同配比的长度为200mm、宽度为150mm、厚度为0.2mm的pp薄膜;(5)复合材料压板成型:先将碳纤维织物与m-pp-5、m-pp-10、m-pp-15、m-pp-20四种不同配比的pp薄膜放进鼓风机在80℃的温度下烘干8h,再将烘干后的碳纤维织物分别与五种不同配比的pp薄膜,其中还包括不添加mapp材料的pp薄膜,将五种不同配比的复合材料交替叠放在已经预热的平板硫化机的平板模具内,采用三段式加压的方式进行加压,当平板模具温度升到220℃时,预热5min 之后,开始施加0.5mpa的压力使纤维与树脂进行初步接触,保压时间5min;然后进行第一次泄压排气,施加1.0mpa的压力使树脂渗入纤维束中与单丝接触发生界面上的相互作用,从而尽量赶走平板模具内部的空气,减少最终制品的空隙率,保温10min;进行第二次泄压排气后施加1.5mpa的压力使纤维与树脂结合更加牢固,并且在压力作用下,复合材料的孔隙率也可以进一步得到有效的控制,保温5min 后自然冷却至室温;采用自然冷却可以保证树脂有充分的结晶时间冷却成型,制得的复合材料板材编号为:cff/pp、cff/m-pp-5、cff/m-pp-10、cff/m-pp-15、cff/m-pp-20;(6)对压制好的cff/pp、cff/m-pp-5、cff/m-pp-10、cff/m-pp-15、cff/m-pp-20复合材
料分别进行拉伸性能、弯曲性能、冲击性能、层间剪切测试:1.拉伸性能测试:采用instron5985 万能材料试验机测试样品的拉伸性能,拉伸性能的测试标准按astmd3039 标准,拉伸速度为2mm/min。拉伸测试试样大小为180
×
10
×
2 mm3,平行测试4~5 个样品;2.弯曲性能测试:采用instron5985 万能材料试验机测试矩形样条的抗弯曲性能。弯曲性能测试标准按astmd7264 标准,试样的跨厚比为32:1,试样厚度为2mm,宽度为13mm,试样的长度比跨度长20%,长度为78mm,平行4~5 个试样从所制板材上用水切割制备得到,测试速度为1.0mm/min;3.冲击性能测试:用zky-1 型冲击缺口制样机对复合材料矩形样品进行精确机械缺口制样,缺口冲击试验在ceast resil impactor摆锤式冲击仪上完成,采用悬臂梁测试方式,摆锤重5j,平行测试4~5 个样品;4.层间剪切测试:采用短梁剪切来表征复合材料层压板的层间剪切强度,测试标准按astmd2344 标准,试样的跨厚比为4:1,试样的长度是厚度的6 倍,试样的宽度是厚度的2 倍,试样的厚度为2mm,平行试样5 个,试样从所压制的层合板上用切割机切下后,先采用粗砂纸打磨后再采用细砂纸打磨至标准尺寸,测试速度为1.0 mm/min,利用τ
o
=3p/4b公式进行剪切强度计算,其中τ
o 为层间剪切强度,p为试样破坏时的最大载荷值,b为试样的宽度,h为试样的厚度。
14.如附图4、5所示,随着mapp材料在pp材料基体中比重的增加,拉伸强度和冲击强度呈现先增大后减小的趋势。其中cff/m-pp-10复合材料的拉伸强度和冲击强度达到了最佳值,与cff/pp相比抗拉强度提高23%,而冲击强度提高108%,cff/m-pp-10的拉伸模量与cff/pp相比提高32%,其拉伸模量的提高要归功于在pp材料基体中添加了刚性的mapp材料,一个良好的界面能有效的将聚合物表面的压力传递至增强体纤维,从而使复合材料具有更好的机械性能。
15.如附图6、7所示,与拉伸检测和冲击检测中的拉伸强度和冲击强度对比图不同,复合材料cff/m-pp-15的弯曲强度和层间剪切强度达到了最佳值,弯曲强度的最佳值相对于cff/pp提高了449%,层间剪切强度提高了332%,cff与基体间的界面粘结强度的提高使复合材料在性能上得到了大幅度的提高,与拉伸性能测试不同,弯曲测试中复合材料的受力方向没有与之平行的纤维丝束,一个良好的界面可以有效地抑制层间开裂和cf与基体界面脱粘的发生,界面性能的改善是促进复合材料机械性能的一个关键点,mapp材料少量的添加就可以明显的改善复合材料的层间剪切和弯曲性能,图中cff/pp-5复合材料界面的改善为其弯曲性能提高了120%、层间剪切强度提高了50%。
16.具体的,当mapp/pp为10%时得到的复合材料cff/m-pp-10拉伸强度和冲击强度达到了最佳值,当mapp/pp为15%时得到的复合材料cff/m-pp-15弯曲强度和层间剪切强度达到了最佳。
17.需要说明的是,在本文中,而且,术语“包括”、“包含”或者其任何其他变体意在涵盖非排他性的包含,从而使得包括一系列要素的过程、方法、物品或者设备不仅包括那些要素,而且还包括没有明确列出的其他要素,或者是还包括为这种过程、方法、物品或者设备所固有的要素。
18.尽管已经示出和描述了本发明的实施例,对于本领域的普通技术人员而言,可以
理解在不脱离本发明的原理和精神的情况下可以对这些实施例进行多种变化、修改、替换和变型,本发明的范围由所附权利要求及其等同物限定。
再多了解一些
本文用于企业家、创业者技术爱好者查询,结果仅供参考。