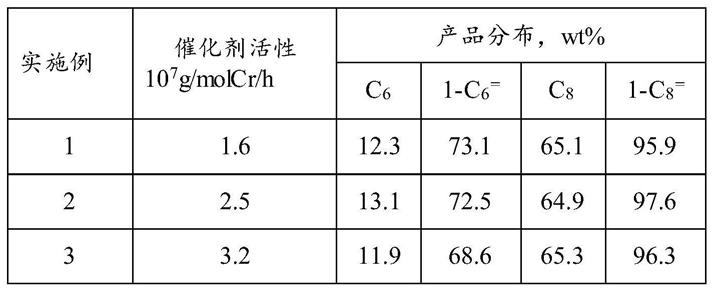
一种合成1
‑
辛烯的催化剂及其应用
技术领域
1.本发明属于催化剂技术领域,尤其涉及一种合成1
‑
辛烯的催化剂及其应用。
背景技术:
[0002]1‑
辛烯是无色液态烯烃化合物,是一种重要的有机化工原料和化学中间体。主要用作聚乙烯(pe)的共聚单体,如作为线型低密度聚乙烯(lldpe)、高密度聚乙烯(hdpe)和乙烯/1
‑
辛烯共弹性体(poe)的共聚单体。此外还可用作增塑剂、表面活性剂等有机化工产品的原料,在日常生活中有着广泛的应用,市场前景乐观。随着pe工业的迅速发展,对1
‑
辛烯的需求也越来越大,加快我国1
‑
辛烯的合成催化剂的开发,对于提高我国聚乙烯行业的整体水平具有重要意义。
[0003]
目前,1
‑
辛烯的生产方法有正辛醇脱水法、正构烷烃脱氢法、蜡裂解法、萃取分离法、丁二烯调聚法、乙烯选择性齐聚法等。正辛醇脱水制备1
‑
辛烯是最古老的方法,这种方法已被淘汰。正构烷烃脱氢法最薄弱的环节就是脱氢烯烃的转化率低(11%~13%),导致产品成本偏高。蜡裂解法是20世纪70年代α
‑
烯烃的主要生产方法,但其很难分离出共聚用高纯度1
‑
辛烯,国外已经停止使用。萃取分离法是唯一从煤基合成气生产的烃类中提取蒸馏得到α
‑
烯烃的方法,仅sasol公司独家采用,国内其他研究院均处于小试阶段。丁二烯调聚的原料成本太高,推行的可能性不大。
[0004]
乙烯选择性齐聚生产1
‑
辛烯技术是近年来新兴的一种专门生产1
‑
辛烯的技术,催化剂是乙烯选择性齐聚生产1
‑
辛烯技术的关键。
技术实现要素:
[0005]
有鉴于此,本发明的目的在于提供一种合成1
‑
辛烯的催化剂及其应用,本发明提供的合成1
‑
辛烯的催化剂催化活性高、产品选择性高、收率高、纯度高,可用于生产聚合1
‑
辛烯。
[0006]
本发明提供了一种合成1
‑
辛烯的催化剂,包括:
[0007]
主催化剂;
[0008]
助催化剂;
[0009]
促进剂;
[0010]
所述主催化剂由活性组分和配体组成;
[0011]
所述活性组分为含铬化合物;
[0012]
所述配体为含p和c的化合物;
[0013]
所述助催化剂为有机铝化合物。
[0014]
优选的,所述促进剂选自氯代烷烃和氯代芳烃中的一种或几种。
[0015]
优选的,所述含铬化合物选自四氢呋喃氯化铬、氯化铬、丙酸铬和乙酰丙酮铬中的至少一种。
[0016]
优选的,所述含p和c的化合物的通式为:
[0017]
p(r1r2)c(r3)c(r4)p(r5r6)式i;
[0018]
式i中,r1、r2、r5和r6独立的选自取代或未取代的烷烃基、环烷烃基和芳香族烷基中的至少一种;
[0019]
r3和r4独立的选自烷烃基、环烷基和芳香族烷基中的至少一种。
[0020]
优选的,所述有机铝化合物选自甲基铝氧烷、乙基铝氧烷、三甲基铝、改性三甲基铝、三乙基铝、三异丁基铝、三正辛基铝、三正己基铝和一氯二乙基铝中的至少一种。
[0021]
优选的,所述促进剂选自二氯甲烷、二氯乙烷、氯苯、2,4
‑
二氯甲苯、1,1,2
‑
三氯乙烷、1,1,2,2
‑
四氯乙烷、五氯乙烷和六氯乙烷中的至少一种。
[0022]
优选的,所述配体的制备方法包括:
[0023]
将含p化合物、溶剂和三乙胺混合后加入含c化合物混合,得到混合溶液;
[0024]
将所述混合溶液进行反应,得到配体;
[0025]
所述含c化合物和含p化合物的摩尔比为1:(1.1~3);
[0026]
所述溶剂选自正己烷、环己烷、四氢呋喃、二氯甲烷和甲苯中的至少一种。
[0027]
优选的,所述含p化合物选自氯代二苯基膦、苯基二氯化膦、二对甲苯基氯化膦、二环己基氯化膦和三烷基膦中的至少一种;
[0028]
所述含c化合物选自乙烷、丙烷、正丁烷、异丁烷、环戊烷、环己烷和苯基烷烃中的至少一种。
[0029]
优选的,所述铬化合物和配体的摩尔比为1:(1~3)。
[0030]
本发明提供了一种1
‑
辛烯的制备方法,包括:
[0031]
采用上述技术方案所述的合成1
‑
辛烯的催化剂制备1
‑
辛烯。
[0032]
本发明提供的合成1
‑
辛烯的催化剂,不仅能够生产1
‑
辛烯,同时还能够生产高附加值的1
‑
己烯。本发明中的催化剂以含铬化合物为活性组分,以含p和c化合物为配体,以有机铝化合物为助催化剂,以氯代烷烃或氯代芳烃为促进剂。本发明提供的催化剂可用于乙烯选择性齐聚合成1
‑
辛烯的反应中。和现有技术相比,采用本发明中的催化剂合成1
‑
辛烯,具有催化剂活性高、产品选择性好,收率高和产品纯度高的特点,可用于生产聚合级1
‑
辛烯;解决了现有技术生产工艺中合成1
‑
辛烯工艺落后繁琐和分离困难的问题。
具体实施方式
[0033]
下面将对本发明实施例中的技术方案进行清楚、完整地描述,显然,所描述的实施例仅仅是本发明一部分实施例,而不是全部的实施例。基于本发明中的实施例,本领域普通技术人员经改进或润饰的所有其它实例,都属于本发明保护的范围。应理解,本发明实施例仅用于说明本发明的技术效果,而非用于限制本发明的保护范围。实施例中,所用方法如无特别说明,均为常规方法。
[0034]
本发明提供了一种合成1
‑
辛烯的催化剂,包括:
[0035]
主催化剂;
[0036]
助催化剂;
[0037]
促进剂;
[0038]
所述主催化剂由活性组分和配体组成;
[0039]
所述活性组分为含铬化合物;
[0040]
所述配体为含p和c的化合物;
[0041]
所述助催化剂为有机铝化合物。
[0042]
在本发明中,所述含铬化合物可以为单一的化合物,也可以为含铬化合物的混合物,可以为有机铬化合物也可以为无机铬化合物,所述含铬化合物中铬的价态优选为1~6价,更优选为2~5价,最优选为3~4价。
[0043]
在本发明中,所述含铬化合物优选选自四氢呋喃氯化铬、氯化铬、丙酸铬和乙酰丙酮铬中的至少一种。
[0044]
在本发明中,所述含p和c的化合物的通式具有式i结构:
[0045]
p(r1r2)c(r3)c(r4)p(r5r6)式i;
[0046]
式i中,r1、r2、r5和r6独立的选自取代或未取代的烷烃基、环烷烃基和芳香族烷基中的一种或几种;所述取代的基团优选选自卤素、硫或氧;
[0047]
r3和r4独立的选自烷烃基、环烷基和芳香族烷基中的至少一种。
[0048]
在本发明中,所述含p和c的化合物的结构式优选为:
[0049][0050]
其中,r1、r2、r5和r6选自芳香族烷基中的一种。
[0051]
在本发明中,所述配体即含p和c的化合物的制备方法优选包括:
[0052]
将含p化合物、溶剂和三乙胺混合后加入含c化合物混合,得到混合溶液;
[0053]
将所述混合溶液进行反应,得到配体;
[0054]
所述含c化合物和含p化合物的摩尔比为1:(1.1~3);
[0055]
所述溶剂选自正己烷、环己烷、四氢呋喃、二氯甲烷和甲苯中的至少一种。
[0056]
在本发明中,所述含p化合物优选选自氯代二苯基膦、苯基二氯化膦、二对甲苯基氯化膦、二环己基氯化膦和三烷基膦中的至少一种。
[0057]
在本发明中,所述含c化合物优选选自乙烷、丙烷、正丁烷、异丁烷、环戊烷、环己烷和苯基烷烃中的至少一种。
[0058]
在本发明中,所述含c化合物和含p化合物的摩尔比优选为1:(1.1~3),更优选为1:(1.5~2.5),更优选为1:(1.8~2.2),最优选为1:2。
[0059]
在本发明中,所述溶剂和含p化合物的摩尔比优选为(15~50):1,更优选为(15~40):1,更优选为(15~30):1,更优选为(15~20):1,最优选为20:1。
[0060]
在本发明中,所述三乙胺和含p化合物的摩尔比优选为(2~5):1,更优选为(3~4):1,最优选为3:1。
[0061]
在本发明中,所述含p化合物、溶剂和三乙胺的混合反应优选在无氧无水且惰性气体的条件下进行。
[0062]
在本发明中,所述加入含c化合物混合的温度优选为0~20℃,更优选为5~15℃,更优选为8~12℃,最优选为10℃;所述混合优选在搅拌的条件下进行,所述搅拌的时间优选为0.2~2h,更优选为0.5~1.5h,更优选为0.8~1.2h,最优选为1h。
[0063]
在本发明中,所述混合溶液进行反应的温度优选为
‑
50~80℃,更优选为
‑
30~50℃,更优选为
‑
25~30℃,最优选为
‑
20℃;所述反应优选在搅拌的条件下进行,所述搅拌的时间优选为2~10h,更优选为3~8h,更优选为4~6h,最优选为5h;所述反应的时间优选为2~10h,更优选为3~8h,更优选为4~6h,最优选为5h;所述反应的整体反应体系优选处于无氧无水的惰性气体环境中。
[0064]
在本发明中,所述混合溶液进行反应后优选还包括:
[0065]
将得到的反应产物过滤、旋蒸和重结晶,得到配体。
[0066]
在本发明中,所述过滤的方法优选为抽滤。
[0067]
在本发明中,所述过滤的温度优选为常温;所述过滤优选在真空条件下进行。
[0068]
在本发明中,所述抽滤完成后若溶液未澄清透明,优选反复进行抽滤直至溶液澄清为止。
[0069]
在本发明中,所述旋蒸优选在旋转蒸发仪中进行;所述旋蒸的温度优选为40~100℃,更优选为50~90℃,更优选为60~80℃,最优选为70℃;所述旋蒸优选在真空的条件下进行。
[0070]
在本发明中,所述旋蒸优选得到流沙状产物。
[0071]
在本发明中,所述重结晶的溶剂优选选自甲醇、乙醇、叔丁醇、和苯中的至少一种;对配体溶解度温度敏感性高,且对杂质的溶解非常大。
[0072]
在本发明中,所述配体的制备方法更优选包括:
[0073]
将含p化合物、溶剂和三乙胺放置于无氧无水且充满惰性气体的烧瓶中,在0~20℃下混合均匀,加入含c化合物、在0~20℃的环境下搅拌0.2~2h,得的混合溶液;将所述混合溶液温度调至反应温度
‑
50~80℃,继续搅拌2~10h,得的反应产物;然后将反应产物过滤、旋蒸和重结晶得到含p和c的化合物配体。
[0074]
在本发明中,所述有机铝化合物优选选自甲基铝氧烷、乙基铝氧烷、三甲基铝、改性三甲基铝、三乙基铝、三异丁基铝、三正辛基铝、三正己基铝和一氯二乙基铝中的至少一种。
[0075]
在本发明中,所述促进剂优选选自氯代烷烃和氯代芳烃中的一种或几种,更优选选自二氯甲烷、二氯乙烷、氯苯、2,4
‑
二氯甲苯、1,1,2
‑
三氯乙烷、1,1,2,2
‑
四氯乙烷、五氯乙烷和六氯乙烷中的至少一种。
[0076]
在本发明中,所述活性组分、含p和c的化合物和助催化剂的摩尔比优选为1:(1~30):(1~1000),更优选为1:(5~25):(10~800),更优选为1:(10~20):(50~600),最优选为1:15:(100~500)。
[0077]
在本发明中,所述促进剂的用量为少量添加,所述活性组分和促进剂的摩尔比优选为1:(1~5),更优选为1:(1~4),更优选为1:(1~3),最优选为1:(1~2)。
[0078]
在本发明中,在上述催化剂中各成分的摩尔比范围内,在适宜的温度和压力下,原料乙烯在催化剂的作用下进行选择性齐聚反应,反应产物主要是1
‑
辛烯,副产1
‑
己烯。
[0079]
本发明提供了一种1
‑
辛烯的制备方法,包括:
[0080]
采用上述技术方案所述的合成1
‑
辛烯的催化剂制备1
‑
辛烯。
[0081]
在本发明中,所述1
‑
辛烯的制备方法优选包括:
[0082]
在合成1
‑
辛烯的催化剂的作用下,通入乙烯进行反应,得到1
‑
辛烯。
[0083]
在本发明中,优选将所述合成1
‑
辛烯的催化剂加入到溶剂中使用;所述溶剂优选为甲苯。
[0084]
在本发明中,所述合成1
‑
辛烯的催化剂中含铬化合物中的铬和助催化剂中的铝的摩尔比优选为1:(480~520),更优选为1:(490~510),最优选为1:500。
[0085]
在本发明中,所述溶剂、主催化剂和促进剂的用量比例优选为(380~420)ml:(0.8~1.2)mol:(1~3)mol,更优选为(390~410)ml:(0.9~1.1)mol:(1.5~2.5)mol,最优选为400ml:1mol:2mol。
[0086]
在本发明中,所述通入乙烯进行反应的温度优选为35~70℃,更优选为40~60℃,最优选为55℃;反应的压力优选为4~8mpa,更优选为5~7mpa,最优选为5mpa;优选通过通入乙烯达到反应压力;反应的时间优选为0.5~1.5小时,更优选为0.8~1.2小时,最优选为1小时。
[0087]
在本发明中,所述制备1
‑
辛烯优选在高压反应釜中进行;所述高压反应釜优选为800~1200ml,更优选为900~1100ml,最优选为1000ml;优选对所述高压反应釜进行抽真空,依次用氮气和乙烯进行置换;所述抽真空的温度优选为110~130℃,更优选为115~125℃,最优选为120℃;所述置换优选为置换3次。
[0088]
在本发明中,所述通入乙烯进行反应完成后优选还包括:
[0089]
将反应体系冷却降温、卸压,并通入酸化乙醇终止反应。
[0090]
在本发明中,所述冷却的温度优选为0~20℃,更优选为5~15℃,更优选为8~12℃,最优选为10℃。
[0091]
在本发明中,所述酸化乙醇的制备方法优选包括:
[0092]
将浓盐酸加入到乙醇中混合,得到乙醇盐酸溶液(酸化乙醇)。
[0093]
在本发明中,所述浓盐酸的质量浓度优选为35~40%,更优选为36~39%,更优选为37~28%,最优选为37%。
[0094]
在本发明中,所述加入优选为将浓盐酸慢慢引流至乙醇中。
[0095]
在本发明中,所述混合优选在搅拌的条件下进行,优选小心搅拌。
[0096]
在本发明中,所述混合后优选还包括:静置至室温。
[0097]
本发明对所述浓硫酸和乙醇的用量没有特殊的限制,本领域技术人员根据预获得的酸化乙醇的浓度配加浓硫酸和乙醇即可。
[0098]
在本发明中,所述酸化乙醇的质量浓度优选为8~12%,更优选为9~11%,最优选为10%。
[0099]
本发明提供的催化剂,同时加入少量的促进剂,能够通过乙烯选择性齐聚合成聚合级1
‑
辛烯,同时副产高附加值的1
‑
己烯。聚合级1
‑
辛烯是重要的精细化工产品,可用作乙烯的共聚单体,作为poe的原材料,此外还可用作增塑剂、表面活性剂、润滑剂、合成羧酸、环氧化合物和橡胶加工化学品等,应用前景十分广泛。
[0100]
本发明提供的合成1
‑
辛烯的催化剂,不仅能够生产1
‑
辛烯,同时还能够生产高附加值的1
‑
己烯。本发明中的催化剂以含铬化合物为活性组分,以含p和c化合物为配体,以有机铝化合物为助催化剂,以氯代烷烃或氯代芳烃为促进剂。本发明提供的催化剂可用于乙烯选择性齐聚合成1
‑
辛烯的反应中。和现有技术相比,采用本发明中的催化剂合成1
‑
辛烯,具有催化剂活性高、产品选择性好,收率高和产品纯度高的特点,可用于生产聚合级1
‑
辛
烯;解决了现有技术生产工艺中合成1
‑
辛烯工艺落后繁琐和分离困难的问题。
[0101]
实施例1
[0102]
将6ml的二氯化苯基膦、60ml的二氯甲烷和15ml的三乙胺放置于无氧无水且充满高纯氮气的烧瓶中,在0~20℃下混合均匀,加入1.2ml的乙烷,在0~20℃的环境下搅拌0.2~2h,得的混合溶液;将混合溶液温度调至
‑
35℃,搅拌反应2h,然后将得到的反应产物在常温、真空条件下进行抽滤,如抽滤后溶液未澄清透明,应反复抽滤至澄清为止;将上述抽滤后澄清溶液在40~100℃、真空条件下使用旋转蒸发仪进行旋蒸,直至液体呈流沙状为止;将旋蒸后的产物采用甲醇进行重结晶,得到含p和c化合物配体;配体收率为75%。
[0103]
配体收率的计算方法为:
[0104]
配体合成时,按照化学反应方程式算所加入的含膦化合物相对于含c化合物的过量,依据含c化合物摩尔数计算出理论配体质量;对重结晶后得到的配体称重得到实际配体质量:
[0105]
配体收率(%)=实际配体质量(g)/理论配体质量(g)*100%。
[0106]
实施例2
[0107]
将15ml的氯化二苯基膦、60ml的二氯甲烷和15ml的三乙胺放置于无氧无水且充满高纯氮气的烧瓶中,在0~20℃下混合均匀,加入2.0ml的异丁烷,在0~20℃的环境下搅拌0.2~2h,得到混合溶液;将混合溶液温度调至
‑
20℃,搅拌反应4h,然后将得到的反应产物在常温、真空条件下进行抽滤,如抽滤后溶液未澄清透明,应反复抽滤至澄清为止;将上述抽滤后澄清溶液在40~100℃、真空条件下使用旋转蒸发仪进行旋蒸,直至液体呈流沙状为止;将旋蒸后的产物采用甲醇进行重结晶,得到含p和c的化合物配体;配体收率为77%。
[0108]
实施例3
[0109]
将9ml的氯化二苯基膦、60ml的二氯甲烷和9ml的三乙胺放置于无氧无水且充满高纯氮气的烧瓶中,在0~20℃下混合均匀,加入2ml的乙苯,在0~20℃的环境下搅拌0.2~2h,得到混合溶液;将混合溶液温度调至
‑
10℃,搅拌反应2h,然后将得到的反应产物在常温、真空条件下进行抽滤,如抽滤后溶液未澄清透明,应反复抽滤至澄清为止;将上述抽滤后澄清溶液在40~100℃、真空条件下使用旋转蒸发仪进行旋蒸,直至液体呈流沙状为止;将旋蒸后的产物采用甲醇进行重结晶,得到含p和c的化合物配体;配体收率为65%。
[0110]
实施例4
[0111]
将实施例1~3制备得到的配体和催化剂的活性进行评价,评价方法为:采用1000ml高压反应釜,在120℃下对高压反应釜进行抽真空,依次用氮气和乙烯置换三次;待高压反应釜温度降至40℃时,将400ml的甲苯溶液加入反应釜中,依次以铝铬摩尔比500的量加入甲基铝氧烷(mao),并迅速加入1.0μmolcr(四氢呋喃氯化铬)和1.2μmol含p和c配体,2μmol二氯甲烷;通入乙烯达到反应压力5mpa,控制反应温度在55℃,反应1h后,进行冷却降温,卸压,通入质量浓度为10%酸化乙醇终止反应,得到产品。
[0112]
采用内标定量方法进行气相色谱分析:取10g产品溶于5g去离子水中,然后取上层有机相0.4~0.5g,并加入内标物正庚烷/正壬烷0.02~0.03g,送色谱分析;检测结果如下:
[0113][0114]
催化剂活性计算方法为:
[0115]
产物总质量(g)=反应后釜重(g)
‑
空釜重(g)
‑
溶剂质量(g);
[0116]
催化剂活性(g/molcr/h)=产物总质量(g)/铬摩尔数(mol)/反应时间(h);
[0117]
根据气相色谱分析及总产物质量可计算1
‑
辛烯、1
‑
己烯、c8(产品中所有带8个碳的烯烃和烷烃)和c6(产品中所有带6个碳的烯烃和烷烃)的质量。
[0118]
由以上结果可以得知,根据本发明提供的方法制备的催化剂具有高活性和高选择性,并且能够在生产1
‑
辛烯的同时得到高附加值的1
‑
己烯。
[0119]
本发明提供的合成1
‑
辛烯的催化剂,不仅能够生产1
‑
辛烯,同时还能够生产高附加值的1
‑
己烯。本发明中的催化剂以含铬化合物为活性组分,以含p和c化合物为配体,以有机铝化合物为助催化剂,以氯代烷烃或氯代芳烃为促进剂。本发明提供的催化剂可用于乙烯选择性齐聚合成1
‑
辛烯的反应中。和现有技术相比,采用本发明中的催化剂合成1
‑
辛烯,具有催化剂活性高、产品选择性好,收率高和产品纯度高的特点,可用于生产聚合级1
‑
辛烯;解决了现有技术生产工艺中合成1
‑
辛烯工艺落后繁琐和分离困难的问题。
[0120]
以上所述的仅是本发明的优选实施方式,应当指出,对于本技术领域的普通技术人员来说,在不脱离本发明原理的前提下,还可以做出若干改进和润饰,这些改进和润饰也应视为本发明的保护范围。
再多了解一些
本文用于企业家、创业者技术爱好者查询,结果仅供参考。