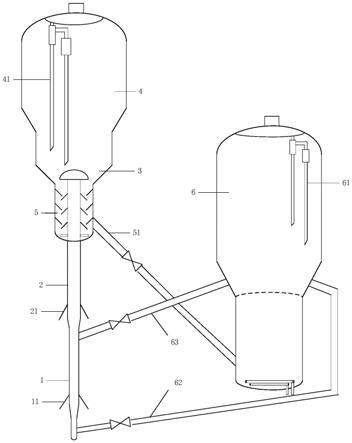
1.本发明涉及石油化工领域,具体地,涉及一种催化裂解的方法和用于实施该方法的设备。
背景技术:
2.催化裂解是生产乙烯和丙烯等低碳烯烃的主要工艺之一。例如cn1102431a就公开了一种制取低碳烯烃兼产高辛烷值汽油的石油烃催化转化方法,具体包括:经预热的石油烃在提升管或下行式输送线反应器或流化床反应器内与热的含磷和稀土的五元环高硅沸石催化剂接触,在温度为480~680℃、压力为1.2~4.0
×
105帕、催化剂与原料油的重量比为4~20∶1、水蒸汽与原料油的重量比为0.01~0.5∶1的条件下反应0.1~6秒,产物物流经分离得到低碳烯烃和液体产品,待生催化剂经汽提进入再生器,在含氧气体存在下于600~800℃再生,再生催化剂经汽提后循环使用。
3.现有的催化裂解方法存在着产品分布不佳的缺陷,具体地是甲烷和焦炭产率过高和/或乙烯和丙烯产率较低的缺陷。
技术实现要素:
4.本发明的目的是提供一种催化裂解的方法,该方法能够显著地改善催化裂解产品的分布,具体地是能够降低甲烷和焦炭产率,并且同时能够提高乙烯和丙烯产率。
5.本发明的发明人出乎意料地发现:将富含低碳烷烃的轻烃原料进行第一段催化裂解后再与重油原料一起进行第二段催化裂解和第三段催化裂解后,能够显著地改善催化裂解产品的分布,由此得到了本发明。
6.为了实现上述目的,本发明提供一种催化裂解的方法,该方法包括:(1)将富含低碳烷烃的轻烃原料与第一再生催化剂送入第一管状反应器,进行第一催化裂解反应,得到第一催化裂解后的油剂物料;(2)将所述第一催化裂解后的油剂物料、重油原料和第二再生催化剂送入第二管状反应器,进行第二催化裂解反应,得到第二催化裂解后的油剂物料;(3)将所述第二催化裂解后的油剂物料送入流化床反应器进行第三催化裂解,得到第三催化裂解后的油剂物料;(4)将所述第三催化裂解后的油剂物料进行油剂分离,得到油气产物和待生催化剂,将所述待生催化剂进行再生,得到再生催化剂。
7.本公开还提供了一种用于实施如上所述的催化裂解的方法的设备,该设备包括:依次流体连通的第一管状反应器、第二管状反应器、流化床反应器和沉降器;该设备还包括流体连通地设置在所述流化床反应器下方的汽提器和与所述汽提器通过待生催化剂通道连通的再生器;其中,所述第一管状反应器的进料端设置有轻烃原料入口和第一再生催化剂入口,所述第二管状反应器的进料端设置有重油原料入口和第二再生催化剂入口。
8.通过上述技术方案,甲烷和焦炭产率得到了显著地降低,并且同时乙烯和丙烯的产率得到了显著的提高。
9.本发明的其他特征和优点将在随后的具体实施方式部分予以详细说明。
40:1,反应压力为0.15-0.32mpa,反应时间为0.5-2秒。
30.优选地,所述第三催化裂解的条件包括:温度为550-620℃,反应压力为0.15-0.30mpa,重时空速为5-20h-1
。
31.优选地,所述第一催化裂解的出口温度比所述第二催化裂解的出口温度高75-125℃。
32.优选地,所述第一催化裂解的剂油比是所述第二催化裂解的剂油比的1.3-3倍。
33.在所述第一催化裂解优选具有更高的出口温度和更高的剂油比的情况下,更适合富含低碳烷烃的轻烃原料的催化转化,并且第一催化裂解转化后的物料还能够促进重油原料在第二催化裂解和第三催化裂解中转化的产物结构,避免产生更多的甲烷和焦炭。
34.可选地,其中,所述重油原料包括常压瓦斯油、减压瓦斯油、加氢尾油、原油、渣油、动植物油脂、煤液化油、费托合成油、油砂油和页岩油中的一种或几种。
35.可选地,所述富含低碳烷烃的轻烃原料中的低碳烷烃的含量为60-100重量%,优选为80-100重量%,更优选为90-100重量%。
36.可选地,所述低碳烷烃的分子中的碳原子数为1-5,例如1、2、3、4、5;优选3-5,例如3、4或5。
37.优选地,所述富含低碳烷烃的轻烃原料由低碳烃物料经预处理及调和得到;所述低碳烃物料包括醚后碳四、裂解碳五、重整拔头油和芳烃抽余油中的一种或多种。
38.优选地,所述富含低碳烷烃的轻烃原料中的烯烃的含量为20重量%以下,优选10重量%以下。
39.所述富含低碳烷烃的轻烃原料的馏程的初馏点可以为0-50℃之间的任意温度,终馏点可以为0-100℃之间的任意温度。
40.可选地,其中,所述第一管状反应器和所述第二管状反应器各自独立地为提升管反应器或下行管反应器。可选地,所述流化床反应器选自固定流化床反应器、散式流化床反应器、鼓泡床反应器、湍动床反应器、快速床反应器、输送床反应器和密相流化床反应器中的一种或几种。
41.优选地,所述提升管反应器为等直径提升管反应器、等线速提升管反应器和变直径提升管反应器中的一种或几种;所述下行管管反应器为等直径下行管管反应器、等线速下行管管反应器和变直径下行管反应器中的一种或几种。
42.可选地,其中,所述第一催化剂和所述第二催化剂可以为各种能够用于催化裂解的催化剂,例如所述第一催化剂和所述第二催化剂可以含有1-60重量%的沸石、5-99重量%的耐热无机氧化物和余量的粘土。优选地,所述沸石为含稀土和磷的五元环高硅沸石、含过渡金属和磷的β沸石、含或不含稀土的高硅y型沸石中的至少一种,可选地,所述耐热无机氧化物选自氧化铝和/或氧化硅。
43.可选地,其中,所述第一再生催化剂和/或所述第二再生催化剂部分或全部来自所述再生催化剂。所述再生催化剂的温度为650-750℃。
44.另一方面,参考图1,本发明还提供了一种用于实施如上所述的催化裂解的方法的设备,该设备包括:依次流体连通的第一管状反应器1、第二管状反应器2、流化床反应器3和沉降器4;该设备还包括流体连通地设置在所述流化床反应器3下方的汽提器5和与所述汽提器5通过待生催化剂通道51连通的再生器6;其中,所述第一管状反应器1的进料端设置有
轻烃原料入口11和第一再生催化剂入口,所述第二管状反应器2的进料端设置有重油原料入口21和第二再生催化剂入口。
45.可选地,其中,所述再生器6上连接有第一再生剂出料管62和第二再生剂出料管63;所述第一再生剂出料管62延伸并连接到所述第一再生催化剂入口上,所述第二再生剂出料管63延伸并连接到所述第二再生催化剂入口上。
46.可选地,其中,所述第一管状反应器1、所述第二管状反应器2、所述流化床反应器3、所述沉降器4和所述汽提器5共轴设置;所述沉降器4中设置有第一气固分离器41,所述流化床反应器3的出口与所述第一气固分离器41的入口相连;所述再生器6中设置有第二气固分离器61。
47.参考图1,来自再生器6的热再生催化剂分为两股:一股由第一再生剂出料管62引入第一管状反应器1进料端的第一催化剂入口,富含低碳烷烃的轻烃原料预热后通入第一管状反应器1的进料端的轻烃原料入口11,在第一管状反应器1中富含低碳烷烃的轻烃原料与第一催化剂进行第一催化裂解,反应后形成包括半待生催化剂和油气产物的第一催化裂解后的油剂物料;另一股热再生催化剂离开再生器6后由第二再生剂出料管63注入第二管状反应器2进料端的第二再生催化剂入口,重油原料经预热后通入第二管状反应器2的进料端的重油原料入口21,第一催化裂解后的油剂物料进入第二段提升管反应器2,第一催化裂解后的油剂物料、重油原料和第二再生催化剂进行第二催化裂解,反应后形成包括半待生催化剂和油气产物的第二催化裂解后的油剂物料;第二催化裂解后的油剂物料进入流化床反应器3,第二催化裂解后的油剂物料在流化床反应器3的床层内进行第三催化裂解,得到第三催化裂解后的油剂物料。离开流化床反应器3后的第三催化裂解后的油剂物料进入气固分离装置41,气体产物离开反应器进行后续处理,待生催化剂进入位于下方的汽提器5。
48.本公开的技术方案所得到的产物分布优化,能够实现多产乙烯和丙烯同时抑制甲烷和焦炭的目的,同时能够对炼厂的碳四和碳五烷烃进行了高价值的利用。
49.下面的实施例将对本公开予以进一步的说明,但并不因此限制本公开的范围。实施例和对比例在小型提升管装置(ru)上实施。实施例和对比例中所使用的原料油的性质列于表1和表2。催化裂化催化剂为中国石化股份有限公司齐鲁催化剂分公司生产的商品号为mmc-2的催化剂。
50.实施例1-3
51.该实施例按照图1的装置和流程进行试验,使用表1所示的轻质原料油a作为富含低碳烷烃的轻烃原料,使用表2所示的重质原料油作为重油原料。
52.富含低碳烷烃的轻烃原料预热后通入第一管状反应器1的进料端的轻烃原料入口11,来自再生器6的热再生催化剂中的一股由第一再生剂出料管62引入第一管状反应器1进料端的第一催化剂入口,在第一管状反应器1中富含低碳烷烃的轻烃原料与第一再生催化剂进行第一催化裂解,反应后形成包括半待生催化剂和油气产物的第一催化裂解后的油剂物料;来自再生器6的热再生催化剂中的另一股热再生催化剂离开再生器6后由第二再生剂出料管63注入第二管状反应器2进料端的第二再生催化剂入口,重油原料经预热后通入第二管状反应器2的进料端的重油原料入口21,第一催化裂解后的油剂物料进入第二段提升管反应器2,第一催化裂解后的油剂物料、重油原料和第二再生催化剂进行第二催化裂解,反应后形成包括半待生催化剂和油气产物的第二催化裂解后的油剂物料;第二催化裂解后
的油剂物料进入流化床反应器3,第二催化裂解后的油剂物料在流化床反应器3的床层内进行第三催化裂解,得到第三催化裂解后的油剂物料。离开流化床反应器3后的第三催化裂解后的油剂物料进入气固分离装置41,气体产物离开反应器进行后续处理,待生催化剂进入位于下方的汽提器5。操作条件及产物分布列于表3。
53.对比例1
54.采用与实施例1相同的方法进行,不同在于,不使用富含低碳烷烃的轻烃原料。
55.具体地,来自再生器6的热再生催化剂中的一股热再生催化剂离开再生器6后由第二再生剂出料管63注入第二管状反应器2进料端的第二再生催化剂入口,重油原料经预热后通入第二管状反应器2的进料端的重油原料入口21,重油原料和第二再生催化剂进行第二催化裂解,反应后形成包括半待生催化剂和油气产物的第二催化裂解后的油剂物料;第二催化裂解后的油剂物料进入流化床反应器3,第二催化裂解后的油剂物料在流化床反应器3的床层内进行第三催化裂解,得到第三催化裂解后的油剂物料。离开流化床反应器3后的第三催化裂解后的油剂物料进入气固分离装置41,气体产物离开反应器进行后续处理,待生催化剂进入位于下方的汽提器5。操作条件及产物分布列于表3。
56.对比例2
57.采用与实施例2相同的方法进行,不同在于,不进行第三催化裂解,第二催化裂解后的油剂物料进入气固分离装置41。
58.具体地,富含低碳烷烃的轻烃原料预热后通入第一管状反应器1的进料端的轻烃原料入口11,来自再生器6的热再生催化剂中的一股由第一再生剂出料管62引入第一管状反应器1进料端的第一再生催化剂入口,在第一管状反应器1中富含低碳烷烃的轻烃原料与第一催化剂进行第一催化裂解,反应后形成包括半待生催化剂和油气产物的第一催化裂解后的油剂物料;来自再生器6的热再生催化剂中的另一股热再生催化剂离开再生器6后由第二再生剂出料管63注入第二管状反应器2进料端的第二再生催化剂入口,重油原料经预热后通入第二管状反应器2的进料端的重油原料入口21,第一催化裂解后的油剂物料进入第二段提升管反应器2,第一催化裂解后的油剂物料、重油原料和第二再生催化剂进行第二催化裂解,反应后形成包括半待生催化剂和油气产物的第二催化裂解后的油剂物料;第二催化裂解后的油剂物料进入气固分离装置41,气体产物离开反应器进行后续处理,待生催化剂进入位于下方的汽提器5。操作条件及产物分布列于表3。
59.表1轻烃原料质量组成
[0060][0061]
表2重质原料油性质
[0062][0063]
表3操作条件及产物分布
[0064] 实施例1实施例2实施例3对比例1对比例2轻烃原料进料量,kg/h11101重油原料进料量,kg/h52132第一催化剂进料量,kg/h303030030第二催化剂进料量,kg/h603015 30总催化剂进料量,kg/h9060456060第一催化裂解剂油比303030 30第二催化裂解剂油比152022.52020一反出口温度,℃650650650 650
再生催化剂温度,℃720720720720720混合催化剂温度,℃696.67685673.33720685第二催化裂解出口温度,℃570570570570570产物分布,w%
ꢀꢀꢀꢀꢀ
干气14.313.813.11512.9液化气37.738.239.234.232.4汽油17.217.818.617.124.5柴油12.813.214.114.214.3重油7.77.15.98.67.2焦炭10.39.99.110.98.7总计100100100100100甲烷产率,w%4.84.54.45.54.3乙烯产率,w%7.17.57.26.74.2丙烯产率,w%21.522.623.320.617.5
[0065]
根据表3的数据可见,本公开的技术方案中,甲烷和/或焦炭产率得到了显著地降低,并且同时乙烯和丙烯的产率得到了显著的提高。
[0066]
以上结合附图详细描述了本发明的优选实施方式,但是,本发明并不限于上述实施方式中的具体细节,在本发明的技术构思范围内,可以对本发明的技术方案进行多种简单变型,这些简单变型均属于本发明的保护范围。
[0067]
另外需要说明的是,在上述具体实施方式中所描述的各个具体技术特征,在不矛盾的情况下,可以通过任何合适的方式进行组合,为了避免不必要的重复,本发明对各种可能的组合方式不再另行说明。
[0068]
此外,本发明的各种不同的实施方式之间也可以进行任意组合,只要其不违背本发明的思想,其同样应当视为本发明所公开的内容。
再多了解一些
本文用于企业家、创业者技术爱好者查询,结果仅供参考。