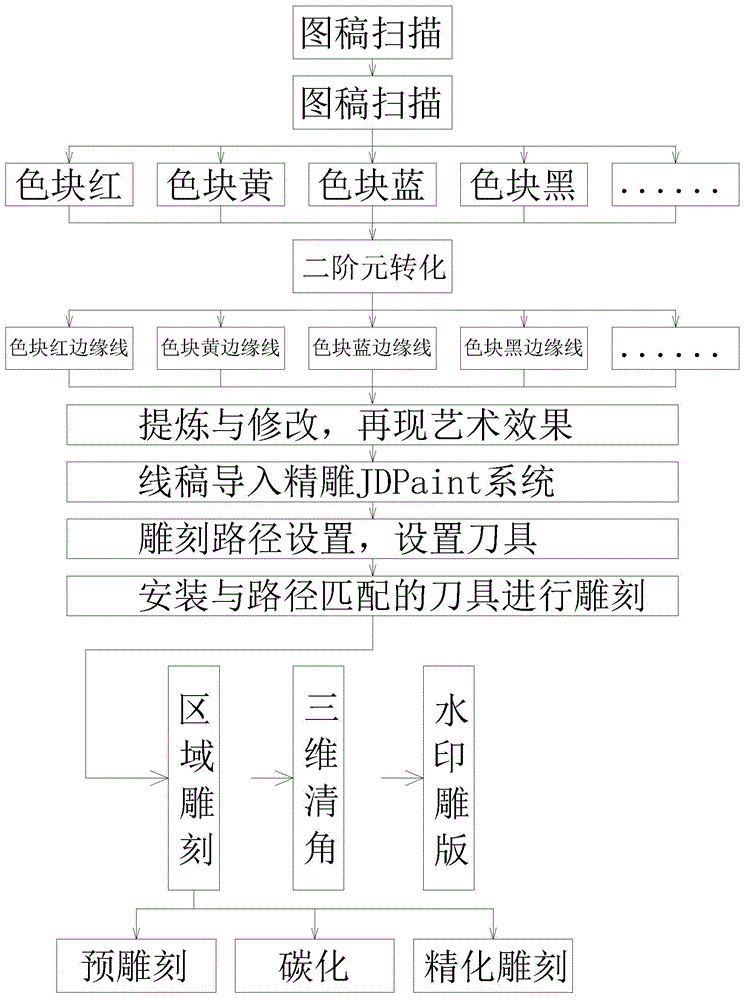
本发明属于微雕技术领域,涉及一种水印版画木刻装置。
背景技术:
传统的水印版画木刻方法是人的手工制作,以人的手工制作就会受到人的技艺的限制,速度极其慢,效率低下。利用电脑精雕技术处理,运用计算机技术替代手工作业。电脑雕刻在亚克力,pvc,铜、铁、铅等板材上目前已经非常成熟,但是在木材雕刻上却问题很大,具体有1、图形精度达不到0.2mm的精度,2、木刻版画木材以果木为材,木材密度低,雕刻精美图案会边缘毛刺,后期无法印刷;3、0.2mm以内的线条断线严重,可以说基本上雕刻实现不了。
技术实现要素:
本发明的目的是针对现有的技术存在的上述问题,提供一种水印版画木刻装置,本发明所要解决的技术问题是如何减少雕刻毛边的产生。
本发明的目的可通过下列技术方案来实现:一种水印版画木刻装置,其特征在于,包括刀头、安装头、连接臂和高压气源,所述安装头呈中空筒状,所述安装头内纵向滑动连接有固定在连接臂下端的活塞,所述活塞与安装头之间连接有一复位弹簧,所述活塞上开设有贯穿活塞下端面的安装孔,所述安装孔内具有励磁绕组,所述安装头内固定设置有一中空轴,所述中空轴上转动连接有一永磁转子,所述励磁绕组通电后能够驱使所述永磁转子旋转,所述永磁转子上固定设置有一安装板,所述安装板的中部具有一进风口,所述进风口出设置有一叶轮,所述叶轮位于中空轴的上端开口处,所述刀头杆状的本体,所述本体内具有一贯穿本体上下两端的排渣孔,所述排渣孔的上端与中空轴的下端相通,所述本体的下端具有对称分布的两个刃部,所述刃部位于排渣孔下端开口的外侧;所述活塞与安装头内腔的下端面之间形成一储气腔,所述所述安装头上设置有能够使储气腔与高压气源相连的进气接管;所述永磁转子旋转能够在叶轮的作用下驱使储气腔内的气体进入排渣孔。
进一步的,所述刃部的外壁面为平直面。
进一步的,所述刃部的外壁面与本体的轴线之间呈5~15°倾角。
进一步的,所述安装孔呈上端孔径大于下端孔径的锥形,所述永磁转子的外壁面与安装孔内壁面适配。
进一步的,所述励磁绕组的纵向长度大于永磁转子的纵向长度。
进一步的,所述永磁转子与中空轴之间通过一阻尼轴承相连。
本雕刻机利用两个片状的刃部对路径的两侧进行纵向切割,对于致密度相对较差的木材而言,毛边产生主要是因为刀具的旋转或冲压切割而使木材受到挤压形变,造成部分未能切割部位的木纤维残留,采用纵向双刃部作用在路径两侧的方式,可尽可能减少对木质纤维的“搅动”,减少对刃部之外的木质纤维的挤压,相比旋转雕刻而言具有很好的优化边缘的效果,相比楔型冲压刀具而言,传统楔型冲压刀具单侧有刃,而另一侧则对木质纤维造成较大非切割式挤压,这种挤压会造成致密度较差的木材受压形变而产生毛边;由于水印版画的雕刻槽宽度极小,冲压雕刻时,两个刃部之间的木料残料较少,且一般呈粉状或小粒状,在高压气源的作用下被吹离,如果有较宽雕刻槽则可以设置偏移的雕刻路径,使多次切割形成较宽雕刻槽。
本雕刻机的工作原理是:高压气源进入储气腔,储气腔气压增大,驱使活塞上移,并压缩复位弹簧,活塞上移的过程中,励磁线圈与永磁转子之间的间距组件减小,使永磁转子的转速逐渐增大,叶轮的转速增大,驱使更多的气流进入排渣孔,此时叶轮上方形成负压,且叶轮转速的加快会造成储气腔内气压的降低,迫使活塞下移,活塞下移后,由于励磁线圈与永磁转子之间的间距增大,叶轮降速,如此反复,可使连接有刀头的安装头纵向往复运动,以进行雕刻;由于微雕的雕刻深度并不大,安装头的纵向往复行程也较小,永磁转子的旋转需要阻尼以确保高频率速度变化的实现,即永磁转子与中空轴之间通过阻尼轴承相连,确保叶轮转速的高频率变化。
附图说明
图1是本水印雕板的生产工艺框图。
图2是木刻装置的结构示意图。
图中,1、刀头;2、安装头;3、连接臂;4、活塞;5、复位弹簧;6、励磁绕组;7、中空轴;8、永磁转子;9、叶轮;10、排渣孔;11、刃部;12、储气腔;13、进气接管。
具体实施方式
以下是本发明的具体实施例并结合附图,对本发明的技术方案作进一步的描述,但本发明并不限于这些实施例。
如图1所示,水印版画木刻方法包括如下步骤:
步骤一:将图稿扫描电脑,分辨率不低于600dpi;
步骤二:电脑分色,将同一颜色图稿分开,对于模糊边缘的图稿要进行修边处理;
步骤三:将分色稿进行计算机二阶元转化,转化过程根据不同的图像进1~5次不同梯度转化;
步骤四:运用计算机cdr技术,对二阶元图像进行跟踪描摹,轮廓描摹,高质量图像;
步骤五:对描摹线稿进行手工艺术效果提炼与修改;
步骤六:将线稿导入精雕jdpaint5.21系统;
步骤七:精雕系统对线稿进行雕刻路径设置,安装去毛边刀具,并设置刀具角度;
然后进行区域雕刻;区域雕刻完成后进行三维清角即完成雕刻路径设计,形成水印雕板。
步骤七的具体做法为:先进行预雕刻,预雕刻的雕槽宽度略小于设计宽度,然后进行雕槽碳化,最后进行精化雕刻,精化雕刻的雕槽宽度与设计宽度一致。
预雕刻和精化雕刻采用相同雕刻机,采用如下的雕刻机,仅需要调整两者的刀具往复行程即可,即:预雕刻时纵向冲压的行程略小于精化雕刻的纵向冲压行程,使预雕刻的雕刻槽的宽度略小于精化雕刻的雕刻槽宽度;碳化采用激光加热碳化或微波碳化的方式,对预雕刻行程的雕刻槽沿路径加热,对雕刻槽凹面进行表层碳化,在精化雕刻时去除碳化层即可。
在完成水印雕板上涂色,一般对凸部涂色即制成水印版画。
如图2所示,安装有去毛边刀具的雕刻机包括刀头1、安装头2、连接臂3和高压气源,安装头2呈中空筒状,安装头2内纵向滑动连接有固定在连接臂3下端的活塞4,活塞4与安装头2之间连接有一复位弹簧5,活塞4上开设有贯穿活塞4下端面的安装孔,安装孔内具有励磁绕组6,安装头2内固定设置有一中空轴7,中空轴7上转动连接有一永磁转子8,励磁绕组6通电后能够驱使永磁转子8旋转,永磁转子8上固定设置有一安装板,安装板的中部具有一进风口,进风口出设置有一叶轮9,叶轮9位于中空轴7的上端开口处,刀头1杆状的本体,本体内具有一贯穿本体上下两端的排渣孔10,排渣孔10的上端与中空轴7的下端相通,本体的下端具有对称分布的两个刃部11,刃部11位于排渣孔10下端开口的外侧;活塞4与安装头2内腔的下端面之间形成一储气腔12,安装头2上设置有能够使储气腔12与高压气源相连的进气接管13;永磁转子8旋转能够在叶轮9的作用下驱使储气腔12内的气体进入排渣孔10。
刃部11的外壁面为平直面。
刃部11的外壁面与本体的轴线之间呈5~15°倾角。
安装孔呈上端孔径大于下端孔径的锥形,永磁转子8的外壁面与安装孔内壁面适配。
励磁绕组6的纵向长度大于永磁转子8的纵向长度。
永磁转子8与中空轴7之间通过一阻尼轴承相连。
本雕刻机利用两个片状的刃部11对路径的两侧进行纵向切割,对于致密度相对较差的木材而言,毛边产生主要是因为刀具的旋转或冲压切割而使木材受到挤压形变,造成部分未能切割部位的木纤维残留,采用纵向双刃部11作用在路径两侧的方式,可尽可能减少对木质纤维的“搅动”,减少对刃部11之外的木质纤维的挤压,相比旋转雕刻而言具有很好的优化边缘的效果,相比楔型冲压刀具而言,传统楔型冲压刀具单侧有刃,而另一侧则对木质纤维造成较大非切割式挤压,这种挤压会造成致密度较差的木材受压形变而产生毛边;由于水印版画的雕刻槽宽度极小,冲压雕刻时,两个刃部11之间的木料残料较少,且一般呈粉状或小粒状,在高压气源的作用下被吹离,如果有较宽雕刻槽则可以设置偏移的雕刻路径,使多次切割形成较宽雕刻槽。
本雕刻机的工作原理是:高压气源进入储气腔12,储气腔12气压增大,驱使活塞4上移,并压缩复位弹簧5,活塞4上移的过程中,励磁线圈与永磁转子8之间的间距组件减小,使永磁转子8的转速逐渐增大,叶轮9的转速增大,驱使更多的气流进入排渣孔10,此时叶轮9上方形成负压,且叶轮9转速的加快会造成储气腔12内气压的降低,迫使活塞4下移,活塞4下移后,由于励磁线圈与永磁转子8之间的间距增大,叶轮9降速,如此反复,可使连接有刀头1的安装头2纵向往复运动,以进行雕刻;由于微雕的雕刻深度并不大,安装头2的纵向往复行程也较小,永磁转子8的旋转需要阻尼以确保高频率速度变化的实现,即永磁转子8与中空轴7之间通过阻尼轴承相连,确保叶轮9转速的高频率变化。
与现有技术相比,本发明的优势有:1、传统手工雕刻需要勾描、裱贴、雕刻三个环节,勾描与雕刻速度都非常慢。计算机扫描图像进行描摹,速度非常快。计算机编程路径雕刻速度也远远高于传统手工,而且计算机雕刻可以24小时不间断雕刻,一个路径设计好也可以雕刻多块,甚至成千上万快;2、在雕刻成本上,计算机提高了速度,时间成本减低,另外计算机雕刻用工容易找,传统手工工艺基本上很难找到合适的从业人员,即使找到也都是工艺美术大师,工资成本巨大;3、性价比上,计算机雕刻能够保证雕刻质量,弥补传统手工艺技师计算缺陷;4、计算机雕刻就是将木板用胶粘住,雕刻方便,生产方便;4、采用无毛边雕刻机,可省略路径边缘整平和去毛边步骤,使路径一次性形成,轮廓感更强、更贴合设计稿,效率也得到提升。
本文中所描述的具体实施例仅仅是对本发明精神作举例说明。本发明所属技术领域的技术人员可以对所描述的具体实施例做各种各样的修改或补充或采用类似的方式替代,但并不会偏离本发明的精神或者超越所附权利要求书所定义的范围。
本文用于企业家、创业者技术爱好者查询,结果仅供参考。