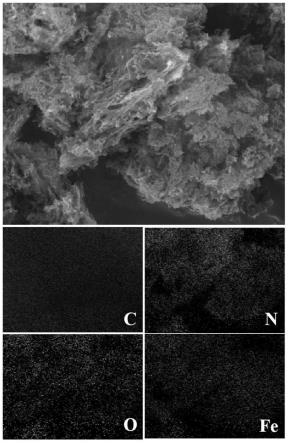
1.本发明涉及污水处理技术领域,具体为一种铁原位掺杂氮化碳非均相芬顿催化剂的制备方法,以及该催化剂在降解废水中染料、抗生素中的应用。
背景技术:
2.金属离子原位掺杂型非均相芬顿催化剂因其优秀的稳定性和催化活性受到广泛研究。研究表明,铁掺杂g-c3n4非均相芬顿催化剂中的fe-n
x
结构是其主要的活性单元,而合成过程中生成的金属氧化物则活性较低,且会降低单位催化剂质量中fe-n
x
结构的含量和导致h2o2无效分解。
3.目前,以g-c3n4为基体的金属离子掺杂型非均相芬顿催化主要通过热解金属盐和g-c3n4前体的物理混合物合成。这种物理尺度上的混合难以保证金属离子在g-c3n4前体中均匀分散,不可避免的将部分金属离子转化为金属氧化物。
4.因此,开发合理的制备方法,制备出高fe-n
x
含量的催化剂,是亟待解决非均相芬顿水处理技术难题。
技术实现要素:
5.针对上述技术问题,本发明提供一种铁原位掺杂氮化碳非均相芬顿催化剂的制备方法和应用。
6.本发明是通过如下技术手段实现的:
7.一种铁原位掺杂氮化碳非均相芬顿催化剂的制备方法,包括以下步骤:
8.(1)制备结晶前体尿素铁
9.将一定量fe(no3)3·
9h2o溶于无水乙醇,并在30℃下保持磁力搅拌,然后向溶液中匀速投加一定质量的尿素。持续搅拌30min后,将生成的淡绿色固体过滤后收集,然后再真空干燥箱中干燥6h,所得淡绿色粉末即为尿素铁。
10.(2)制备铁原位掺杂氮化碳非均相芬顿催化剂
11.称取一定质量的尿素铁与一定比例的尿素混合研磨成粉,将其装入瓷坩埚并置于马弗炉中升温煅烧。将所得产物研磨后用无水乙醇和去离子水各洗涤三次后,在烘箱中干燥6h,所得样品即为铁原位掺杂氮化碳非均相芬顿催化剂。
12.进一步的,步骤(1)所述fe(no3)3·
9h2o的用量为8.08g,无水乙醇体积为100ml。
13.进一步的,步骤(1)所述尿素投加量为8.408g,尿素投加速率为0.5min/g,磁力搅拌转速为400r/min。
14.进一步的,步骤(2)所述尿素添加量>20g,所述尿素铁与尿素的质量比为1~3:50。
15.进一步的,步骤(2)所述升温煅烧条件为:
16.以20℃/min的升温速率升至540℃,并在540℃下保持90min。
17.进一步的,步骤(2)所述烘箱干燥温度为60℃,干燥时间为6h。
18.本发明还公开了一种上述任一制备方法制得的铁原位掺杂氮化碳非均相芬顿催化剂。
19.本发明还公开了一种上述铁原位掺杂氮化碳非均相芬顿催化剂在污水治理中的应用。
20.进一步的,该应用包括:催化h2o2降解废水中的染料、抗生素等污染物。
21.本发明的有益效果在于:
22.本发明制得的材料作为非均相芬顿催化剂催化h2o2降解水中难降解有机污染物。其具体性能如下:在中性ph下能快速降解20mg/l的rhb、mb、ao7、tc等有机污染物;催化活性不受ph的显著影响,在广泛ph(3-11)范围内均具有较高活性;在较高浓度污染物环境(100mg l-1)下也能保持优秀的催化活性;催化活性不受水体中h2po4-、co32-、so42-、cl-、no3-等无机阴离子的显著影响;较低的h2o2消耗量,仅需10mm;四次循环使用后仍保持了较高的催化活性。
附图说明
23.图1为实施例2中制备的4种不同尿素铁添加比例的催化材料对rhb的催化降解活性;
24.图2为实施例3不同温度下制备的0.8c-fe/cn对rhb的催化降解活性;
25.图3为实施例4中制备的3种催化材料对rhb的催化降解活性;
26.图4为实施例5中不同浓度的0.8c-fe/cn540对rhb的催化降解活性;
27.图5为实施例5中h2o2浓度对0.8c-fe/cn540催化活性影响;
28.图6为实施例5中ph对0.8c-fe/cn540催化活性的影响;
29.图7为实施例5中rhb浓度对0.8c-fe/cn540催化活性的影响;
30.图8为实施例5中无机阴离子对0.8c-fe/cn540催化活性的影响;
31.图9为实施例5中0.8c-fe/cn540对不同污染物的催化降解活性;
32.图10为实施例6中0.8c-fe/cn540的可循环利用性测试;
33.图11为实施例7中0.8c-fe/cn540、m-fe/cn、g-c3n4的xrd图谱;
34.图12为实施例8中0.8c-fe/cn540的扫描电子显微镜图像;
35.图13为实施例8中0.8c-fe/cn540的元素映射图。
具体实施方式
36.以下结合实施例和附图对本发明进行详细描述,但需要理解的是,所述实施例和附图仅用于对本发明进行示例性的描述,而并不能对本发明的保护范围构成任何限制。所有包含在本发明的发明宗旨范围内的合理的变换和组合均落入本发明的保护范围。
37.除图中描述的条件变量外,其他催化降解条件默认为:
38.催化剂为0.8c-fe/cn540;
39.污染物溶液为100ml初始浓度20mg l-1的rhb溶液;
40.初始ph值为7;
41.催化剂投加量为0.5g l-1;
42.h2o2浓度为10mm。
43.实施例1
44.金属含量核算案例:
45.分别称取0.01g尿素铁和fe(no3)3
·
9h2o,用10ml 5%的硝酸溶解后定容至100ml,通过icp-oes测量二者铁的质量浓度。如表1所示,其浓度分别为1.122mg l-1和0.47mg l-1,即单位质量尿素铁和fe(no3)3
·
9h2o中的含铁量之比为2.38。
46.表1尿素铁与fe(no3)3
·
9h2o含铁量比较
[0047][0048]
实施例2
[0049]
尿素铁添加量对比案例:
[0050]
称取0、0.4、0.8、1.2g的尿素铁,分别与20g尿素混合后研磨成粉。将上述粉末后装入带盖瓷坩埚中,然后在马弗炉中以20℃/min的升温速率升至540℃并保持90min,所得产物研磨成粉并用无水乙醇和去离子水各洗涤三次,然后在60℃烘箱中干燥6h,所得产物分别命名为0.0c-fe/cn、0.4c-fe/cn、0.8c-fe/cn、1.2c-fe/cn。
[0051]
如图1所示,以未添加尿素铁制备的材料为参照,对比了四种材料对rhb的催化降解活性,其中0.8c-fe/cn的催化催化降解活性最高,故尿素铁的最佳添加量为0.8g,相对应的实施例4中fe(no3)3
·
9h2o添加量则为1.904g。
[0052]
实施例3
[0053]
合成温度对比案例:
[0054]
称取三份0.8g尿素铁,均与20g尿素混合研磨成粉。将上述粉末后装入带盖瓷坩埚中,然后在马弗炉中以20℃/min的升温速率将温度分别升至500℃、540℃、580℃并保持90min,所得产物研磨成粉并用无水乙醇和去离子水各洗涤三次,然后在60℃烘箱中干燥6h,所得产物分别命名为0.8c-fe/cn500、0.8c-fe/cn540、0.8c-fe/cn580。
[0055]
如图2所示,对比了三种温度下制备的c-fe/cn对rhb的催化降解活性,其中c-fe/cn540的催化催化降解活性最高,故选择540℃作为最佳合成温度。
[0056]
实施例4
[0057]
合成方法对比案例:
[0058]
首先准备3种煅烧前体,其分别为0.8g尿素铁和20g尿素混合研磨所得粉末、1.904g fe(no3)3
·
9h2o和20g尿素混合研磨所得粉末、20g尿素研磨所得粉末。将上述粉末后装入带盖瓷坩埚中,然后在马弗炉中以20℃/min的升温速率升至540℃并保持90min,所得产物研磨成粉并用无水乙醇和去离子水各洗涤三次,然后在60℃烘箱中干燥6h,所得产物分别命名为0.8c-fe/cn540、m-fe/cn、g-c3n4。
[0059]
如图3所示,以纯的g-c3n4为参照,对比了两种方法合成的催化剂对20mg l-1的rhb的催化降解活性。可见在制备的催化剂中,0.8c-fe/cn540催化活性最强。
[0060]
实施例5
[0061]
实施案例4中所制备的复合材料0.8c-fe/cn540在不同条件下的催化降解活性。
[0062]
除各图自身描述变量外,其他反应条件均为默认反应条件。催化材料浓度实验中,
0.8c-fe/cn540的浓度设置为0、0.1、0.3、0.5、0.7、1.0g l-1。在h2o2浓度实验中,h2o2浓度设置为0、5、8、10、12mm。ph适应性实验中,将rhb溶液的ph调节为3、5、7、9、11。污染物浓度适应实验中,将rhb溶液的浓度分别设置为20、30、50、100mg l-1。共存阴离子实验中,在rhb溶液中分别加入10mm的h2po4-、co32-、so42-、cl-、no3-。污染物适应性实验中,将污染物溶液更换为20mg l-1的mb、ao7、tc。
[0063]
如图4所示,仅使用0.5g l-1的催化剂,30min内rhb的去除率高于98%,当催化剂浓度超过0.5g l-1后,去除效率不随催化剂浓度增加是由于过量催化剂团聚在一起导致活性位点减少。如图5所示,即便h2o2浓度仅为5mm,30min内rhb的去除率仍高于90%,当h2o2浓度高于5mm后,降解效率不随h2o2浓度增加而增加是由于过量h2o2对
·
oh的猝灭。如图6所示,在ph 3-11范围内均保持了较高的rhb去除效率,催化活性不受ph的显著影响。如图7所示,即便rhb初始浓度上升到100mg l-1,在1h内也能被去除90%。如图8所示,材料的催化活性不受h2po4-、co32-、so42-、cl-、no3-等无机阴离子的显著影响。如图9所示,催化材料能高效降解mb、ao7、tc等多种污染物,具有良好的污染物适应性。
[0064]
实施例6
[0065]
实施案例3中所制备的复合材料0.8c-fe/cn540的可循环利用性和稳定性。
[0066]
在循环利用实验中,除rhb溶液体积外,其余均采用默认的催化降解参数。上一轮催化降解试验完成后,将催化剂过滤、洗涤、烘干后进行下一循环,所有的循环实验均保持催化剂浓度为0.5g l-1。通过每轮循环后fe的浸出量评价催化剂的稳定性,具体而言,每轮循环后将部分处理液过孔径为0.45μm的微孔滤膜,通过icp-oes测量其铁的浓度。
[0067]
如图10所示,材料具有优秀的可重复利用性,4次循环后60min内rhb的去除率保持在90以上。如表2所示,材料具有高度的稳定性,几乎不存在fe的浸出。
[0068]
表2 4次循环的fe浸出量
[0069][0070]
实施例7
[0071]
实施例4中所制备的3种材料的物相和晶形通过x射线衍射光谱(xrd)表征。
[0072]
如图11所示,0.8c-fe/cn540的xrd图谱中未观察到明显的铁氧化物特征衍射峰,而m-fe/cn的xrd图谱中检测到了铁氧化物的特征衍射峰,表明我们开发的合成方法能更有效的将铁转化为fe-nx。
[0073]
实施例8
[0074]
实施例3中所制备的0.8c-fe/cn540的微观形貌和表面元素分布通过扫描电子显微镜(sem)测定。
[0075]
如图12所示,0.8c-fe/cn540的sem图像显示为表面多孔的g-c3n4薄片,未见明显的铁氧化物颗粒堆积。edax结果如图13所示,fe与n的分散轨迹高度重合,表明铁是以形成fe-nx结构的方式原位掺入g-c3n4骨架。
[0076]
以上实施例仅是本发明的优选实施方式,本发明的保护范围并不仅局限于上述实施例。凡属于本发明思路下的技术方案均属于本发明的保护范围。应该指出,对于本技术领域的普通技术人员来说,在不脱离本发明原理的前提下的改进和润饰,这些改进和润饰也应视为本发明的保护范围。
再多了解一些
本文用于创业者技术爱好者查询,仅供学习研究,如用于商业用途,请联系技术所有人。