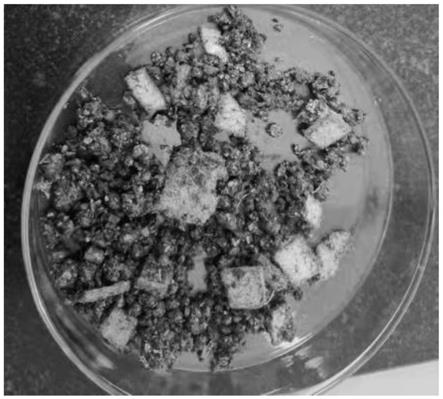
1.本发明涉及过滤材料技术领域,更具体地说,关于一种可降解低温除尘过滤材料的制备方法及制得的过滤材料。
背景技术:
2.2020年,国家就明确提出支持可降解材料推广使用,鼓励推广应用可循环、易回收、可降解的替代产品。可降解材料未来容量巨大,目前国内产能还未释放,预计到2025年,全国可降解塑料的需求量将超过140万吨。
3.目前的除尘滤料为不可降解材料,废旧滤料的处理极为困难,易造成“二次污染”。如专利cn110947243a公开一种除尘滤袋用滤料,包括纤维面层、基布;所述滤料主体采用上、下层纤维面和基布经过针刺法组成,其中纤维都为帝人 conex芳纶纤维。因此,亟需研发可降解除尘滤料,做到工业除尘滤料“纺丝
‑ꢀ
加工-服役-回收处理”整个生命周期的全方位循环。但是可降解材料大多应用于一次性餐盒、塑料购物袋、餐具等生活领域,对于工业除尘滤料领域鲜有报道。
4.由于除尘滤袋在工况中运行温度较高,对于一些熔点较低的可降解材料,无法适用长期的使用要求。因此,亟需开发出生物可降解的除尘过滤材料。
技术实现要素:
5.发明所要解决的技术问题在于如何解决现有的除尘滤料为不可降解材料,废旧滤料的处理极为困难,易造成“二次污染”的问题。
6.本发明通过以下技术手段实现解决上述技术问题的:
7.一种可降解低温除尘过滤材料的制备方法,包括以下步骤:
8.(1)将pbat树脂切片置入真空烘箱中真空干燥,使树脂切片充分干燥,然后将经真空干燥的pbat树脂切片置入纺丝机的料斗中,添加质量分数为 0.8-1.2%的纳米蒙脱土(mmt);再经过螺杆挤出装置的四个加热区加热熔融后挤出,进入纺丝箱体,经计量泵计量后由喷丝板喷吹,再经侧吹风冷却固化,由一对牵伸辊进行牵伸,再经过集束、上油、加卷,最后经短切制成生物可降解pbat纤维;
9.(2)将步骤(1)制备的可降解pbat纤维分别经两套开松-混合-精开松
‑ꢀ
梳理-铺网工艺设备,制作成过滤材料纤维面层和底层;在铺网和针刺环节中间,将聚四氟乙烯基布放入面层和底层之间,组合成“底层-基布-面层”的结构;再经预刺、主刺1、主刺2后制备成可降解pbat纤维滤料半成品;
10.(3)将步骤(2)制作的可降解pbat滤料半成品经过烧毛处理,速度为 20-25m/min,烧去滤料表面的绒毛;
11.(4)将聚四氟乙烯乳液、去离子水按照质量比1:8-10的比例,配制成后处理浸渍乳液,再向其中加入浓度为0.8-1%的十二烷基苯磺酸钠,经电动搅拌器中搅拌3-4h,充分混匀;
12.(5)将步骤(3)中经烧毛后的可降解pbat滤料通过浸渍乳液浸渍后,进入热定型机,热定型共分6个温区,1区、2区起烘干作用,3-6区起热定型作用,消除滤料中纤维之间的内应力,使尺寸稳定,最终制成生物可降解pbat 纤维低温除尘过滤材料。
13.本发明利用pbat材料具有完成生物可降解的特性,并利用蒙脱土插层法改性pbat材料,得到具有一定温度、强力性能的可降解材料,可以满足常温滤料的使用工况,且可以在土壤中生物降解,最终分解成水和二氧化碳。
14.优选地,所述步骤(1)中真空烘箱温度为105-115℃,真空干燥时间为 40-50h。
15.优选地,所述步骤(1)中的四个加热区的温度设置为:一区温度为 220-225℃,二区温度为225-230℃,三区温度为230-235℃,四区温度为 230-235℃。
16.优选地,所述步骤(1)中纺丝箱体温度为227-232℃。
17.优选地,所述步骤(1)中纺丝速度控制为800-1000m/min。
18.优选地,所述步骤(2)中聚四氟乙烯基布的克重控制在110-130g/m2。
19.优选地,所述步骤(2)中滤料半成品的克重控制在550-650g/m2。
20.优选地,所述步骤(2)中预刺针刺密度为50-55p/cm2,刺针深度为 10.5-11.0mm;主刺1针刺密度为340-360p/cm2,上、下针刺深度均为7-8mm;主刺2针刺密度为350-370p/cm2,上针刺深度为6.0-6.2mm,下针刺深度为 6.2-6.4mm。
21.优选地,所述步骤(5)中热定型机6个温区的温度分别为:100-110℃、 120-130℃、150-160℃、160-170℃、150-160℃、130-140℃,定型速度为5-6m/min。
22.本发明还提供上述一种可降解低温除尘过滤材料的制备方法制得的过滤材料。
23.本发明具有如下的有益效果:本发明利用pbat材料具有完成生物可降解的特性,并利用蒙脱土插层法改性pbat材料,得到具有一定温度、强力性能的可降解材料,可以满足常温滤料的使用工况,且可以在土壤中生物降解,最终分解成水和二氧化碳。
附图说明
24.图1为本发明实施例2制备的生物可降解pbat纤维低温除尘过滤材料经 3个月土埋后的结果图。
具体实施方式
25.为使本发明实施例的目的、技术方案和优点更加清楚,下面将结合说明书附图和本发明实施例,对本发明实施例中的技术方案进行清楚、完整地描述,显然,所描述的实施例是本发明一部分实施例,而不是全部的实施例。基于本发明中的实施例,本领域普通技术人员在没有作出创造性劳动前提下所获得的所有其他实施例,都属于本发明保护的范围。
26.下述实施例中所用的试验材料和试剂等,如无特殊说明,均可从商业途径获得。
27.实施例中未注明具体技术或条件者,均可以按照本领域内的文献所描述的技术或条件或者按照产品说明书进行。
28.实施例1
29.一种可降解低温除尘过滤材料的制备方法,包括以下步骤:
30.(1)将pbat树脂切片置入真空烘箱中真空干燥,控制真空烘箱温度为 105℃,真空干燥时间为40h使树脂切片充分干燥,然后将经真空干燥的pbat 树脂切片置入纺丝机的料
斗中,添加质量分数为0.8-%的纳米蒙脱土(mmt);再经过螺杆挤出装置的四个加热区(一区温度为220℃,二区温度为225℃,三区温度为230℃,四区温度为230℃)加热熔融后挤出,进入纺丝箱体(纺丝箱体温度为227℃),纺丝速度控制为800m/min,经计量泵计量后由喷丝板喷吹,再经侧吹风冷却固化,由一对牵伸辊进行牵伸,再经过集束、上油、加卷,最后经短切制成生物可降解pbat纤维;
31.(2)将步骤(1)制备的可降解pbat纤维分别经两套开松-混合-精开松
‑ꢀ
梳理-铺网工艺设备,制作成过滤材料纤维面层和底层;在铺网和针刺环节中间,将聚四氟乙烯基布放入面层和底层之间,组合成“底层-基布-面层”的结构;再经预刺、主刺1、主刺2后制备成可降解pbat纤维滤料半成品;其中,所用聚四氟乙烯基布克重控制在110/m2,滤料半成品克重控制在550g/m2;预刺针刺密度为50p/cm2,刺针深度为10.5mm;主刺1针刺密度为340p/cm2,上、下针刺深度均为7mm;主刺2针刺密度为350p/cm2,上针刺深度为6.0mm,下针刺深度为6.2mm;
32.(3)将步骤(2)制作的可降解pbat滤料半成品经过烧毛处理,速度为 20m/min,烧去滤料表面的绒毛;
33.(4)将聚四氟乙烯乳液、去离子水按照质量比1:8的比例,配制成后处理浸渍乳液,再向其中加入浓度为0.8%的十二烷基苯磺酸钠,经电动搅拌器中搅拌3h,充分混匀;
34.(5)将步骤(3)中经烧毛后的可降解pbat滤料通过浸渍乳液浸渍后,进入热定型机,热定型共分6个温区,1区、2区起烘干作用,3-6区起热定型作用,消除滤料中纤维之间的内应力,使尺寸稳定,热定型机6个温区的温度分别为:100℃、120℃、150℃、160℃、150℃、130℃,定型速度为5m/min,最终制成生物可降解pbat纤维低温除尘过滤材料。
35.将本实施例制得的生物可降解pbat纤维低温过滤材料采用yg026mg-500 电子织物强力机(温州方圆仪器有限公司)对可降解pbat低温除尘过滤材料进行拉伸强力测试,测试结果见表1;采用yg461e全自动织物透气量仪(温州方圆仪器有限公司)对可降解pbat低温除尘过滤材料进行透气性能测试,测试结果见表2;采用土埋法将可降解pbat低温除尘滤料埋于含有微生物的富营养土质中,观测形态变化,测试结果见表3。
36.实施例2
37.一种可降解低温除尘过滤材料的制备方法,包括以下步骤:
38.(1)将pbat树脂切片置入真空烘箱中真空干燥,控制真空烘箱温度为 110℃,真空干燥时间为45h使树脂切片充分干燥,然后将经真空干燥的pbat 树脂切片置入纺丝机的料斗中,添加质量分数为1.0%的纳米蒙脱土(mmt);再经过螺杆挤出装置的四个加热区(一区温度为223℃,二区温度为227℃,三区温度为233℃,四区温度为233℃)加热熔融后挤出,进入纺丝箱体(纺丝箱体温度为230℃),纺丝速度控制为900m/min,经计量泵计量后由喷丝板喷吹,再经侧吹风冷却固化,由一对牵伸辊进行牵伸,再经过集束、上油、加卷,最后经短切制成生物可降解pbat纤维;
39.(2)将步骤(1)制备的可降解pbat纤维分别经两套开松-混合-精开松
‑ꢀ
梳理-铺网工艺设备,制作成过滤材料纤维面层和底层;在铺网和针刺环节中间,将聚四氟乙烯基布放入面层和底层之间,组合成“底层-基布-面层”的结构;再经预刺、主刺1、主刺2后制备成可降解pbat纤维滤料半成品;其中,所用聚四氟乙烯基布克重控制在120g/m2,滤料半成品克重控制在600g/m2;预刺针刺密度为53p/cm2,刺针深度为10.7mm;主刺1针刺密度为350p/
cm2,上、下针刺深度均为7.5mm;主刺2针刺密度为360p/cm2,上针刺深度为6.1mm,下针刺深度为6.3mm;
40.(3)将步骤(2)制作的可降解pbat滤料半成品经过烧毛处理,速度为 23m/min,烧去滤料表面的绒毛;
41.(4)将聚四氟乙烯乳液、去离子水按照质量比1:9的比例,配制成后处理浸渍乳液,再向其中加入浓度为0.9%的十二烷基苯磺酸钠,经电动搅拌器中搅拌3.5h,充分混匀;
42.(5)将步骤(3)中经烧毛后的可降解pbat滤料通过浸渍乳液浸渍后,进入热定型机,热定型共分6个温区,1区、2区起烘干作用,3-6区起热定型作用,消除滤料中纤维之间的内应力,使尺寸稳定,热定型机6个温区的温度分别为:105℃、125℃、155℃、165℃、155℃、135℃,定型速度为5.5m/min,最终制成生物可降解pbat纤维低温除尘过滤材料。
43.将本实施例制得的生物可降解pbat纤维低温过滤材料采用yg026mg-500 电子织物强力机(温州方圆仪器有限公司)对可降解pbat低温除尘过滤材料进行拉伸强力测试,测试结果见表1;采用yg461e全自动织物透气量仪(温州方圆仪器有限公司)对可降解pbat低温除尘过滤材料进行透气性能测试,测试结果见表2;采用土埋法将可降解pbat低温除尘滤料埋于含有微生物的富营养土质中,观测形态变化,测试结果见表3。
44.图1为本实施例制得的生物可降解pbat纤维低温过滤材料经3个月土埋后的状态图,可以看出,本实施例制备的可降解低温除尘滤料,可以满足常温滤料的使用工况,且可以在土壤中生物降解,最终分解成水和二氧化碳。
45.实施例3
46.一种可降解低温除尘过滤材料的制备方法,包括以下步骤:
47.(1)将pbat树脂切片置入真空烘箱中真空干燥,控制真空烘箱温度为115℃,真空干燥时间为50h使树脂切片充分干燥,然后将经真空干燥的pbat 树脂切片置入纺丝机的料斗中,添加质量分数为1.2%的纳米蒙脱土(mmt);再经过螺杆挤出装置的四个加热区(一区温度为225℃,二区温度为230℃,三区温度为235℃,四区温度为235℃)加热熔融后挤出,进入纺丝箱体(纺丝箱体温度为232℃),纺丝速度控制为1000m/min,经计量泵计量后由喷丝板喷吹,再经侧吹风冷却固化,由一对牵伸辊进行牵伸,再经过集束、上油、加卷,最后经短切制成生物可降解pbat纤维;
48.(2)将步骤(1)制备的可降解pbat纤维分别经两套开松-混合-精开松
‑ꢀ
梳理-铺网工艺设备,制作成过滤材料纤维面层和底层;在铺网和针刺环节中间,将聚四氟乙烯基布放入面层和底层之间,组合成“底层-基布-面层”的结构;再经预刺、主刺1、主刺2后制备成可降解pbat纤维滤料半成品;其中,所用聚四氟乙烯基布克重控制在130g/m2,滤料半成品克重控制在650g/m2;预刺针刺密度为55p/cm2,刺针深度为11.0mm;主刺1针刺密度为360p/cm2,上、下针刺深度均为8mm;主刺2针刺密度为370p/cm2,上针刺深度为6.2mm,下针刺深度为6.4mm;
49.(3)将步骤(2)制作的可降解pbat滤料半成品经过烧毛处理,速度为 25m/min,烧去滤料表面的绒毛;
50.(4)将聚四氟乙烯乳液、去离子水按照质量比1:10的比例,配制成后处理浸渍乳液,再向其中加入浓度为1%的十二烷基苯磺酸钠,经电动搅拌器中搅拌 4h,充分混匀;
51.(5)将步骤(3)中经烧毛后的可降解pbat滤料通过浸渍乳液浸渍后,进入热定型
机,热定型共分6个温区,1区、2区起烘干作用,3-6区起热定型作用,消除滤料中纤维之间的内应力,使尺寸稳定,热定型机6个温区的温度分别为:110℃、130℃、160℃、170℃、160℃、140℃,定型速度为6m/min,最终制成生物可降解pbat纤维低温除尘过滤材料。
52.将本实施例制得的生物可降解pbat纤维低温过滤材料采用yg026mg-500 电子织物强力机(温州方圆仪器有限公司)对可降解pbat低温除尘过滤材料进行拉伸强力测试,测试结果见表1;采用yg461e全自动织物透气量仪(温州方圆仪器有限公司)对可降解pbat低温除尘过滤材料进行透气性能测试,测试结果见表2;采用土埋法将可降解pbat低温除尘滤料埋于含有微生物的富营养土质中,观测形态变化,测试结果见表3。
53.对比例(未添加pbat)
54.1.常规pps纤维的制作
55.将pps树脂切片置入真空烘箱中真空干燥,真空烘箱温度为130℃,真空干燥时间为60h;将经真空干燥的pps树脂切片置入纺丝机的料斗中;经过螺杆挤出装置的四个加热区(一区温度为290℃,二区温度为305℃,三区温度为315℃,四区温度为315℃)加热熔融后挤出,进入纺丝箱体(纺丝箱体温度为320℃),经计量泵计量后由喷丝板喷吹,再经侧吹风冷却固化,由一对牵伸辊进行牵伸,再经过集束、上油、加卷,最后经短切制成pps纤维,丝速度控制为800m/min。
56.2、常规pps纤维除尘过滤材料的制作
57.将步骤1制备的常规pps纤维分别经两套开松-混合-精开松-梳理-铺网工艺设备,制作成过滤材料纤维面层和底层,在铺网和针刺环节中间,将聚四氟乙烯基布放入面层和底层之间,组合成“底层-基布-面层”的结构;再经预刺、主刺 1、主刺2后制备成常规pps纤维滤料半成品;所用聚四氟乙烯基布克重控制在 110g/m2,滤料半成品克重控制在550g/m2;预刺针刺密度为50p/cm2,针刺深度为10.5mm;主刺1针刺密度为440p/cm2,上、下针刺深度均为8.0mm;主刺2 针刺密度为500p/cm2,上针刺深度为6.2mm,下针刺深度为6.5mm。
58.3、常规pps纤维除尘过滤材料的后处理
59.将步骤2制作的常规pps滤料半成品经过烧毛处理,速度为20m/min,烧去滤料表面的绒毛。
60.4、将聚四氟乙烯乳液、去离子水按照质量比1:10的比例,配制成后处理浸渍乳液,再向其中加入助剂十二烷基苯磺酸钠(浓度控制在1.0%),经电动搅拌器中搅拌3h,充分混匀。
61.5、将经烧毛后的常规pps纤维滤料通过浸渍乳液浸渍后,进入热定型机,热定型机6个温区的温度分别为:190℃、220℃、220℃、230℃、200℃、190℃,定型速度为7m/min,最终制成常规pps纤维除尘过滤材料。
62.将本对比例制得的常规pps纤维过滤材料采用yg026mg-500电子织物强力机(温州方圆仪器有限公司)对其进行拉伸强力测试,测试结果见表1;采用 yg461e全自动织物透气量仪(温州方圆仪器有限公司)对其进行透气性能测试,测试结果见表2;采用土埋法将其埋于含有微生物的富营养土质中,观测形态变化,测试结果见表3。
63.表1为滤料拉伸强力测试结果
[0064][0065]
表2为滤料透气率测试结果
[0066][0067][0068]
表3为制备的中孔tio2比表面积测试结果
[0069]
组别形态变化及天数实施例1有腐蚀破损现象实施例2有腐蚀破损现象实施例3有腐蚀破损现象对比例1无变化
[0070]
根据表1的结果可知,本发明利用pbat材料具有完成生物可降解的特性,并利用蒙脱土插层法改性pbat材料,得到具有一定温度、强力性能的可降解材料,可以满足常温滤料的使用工况,且可以在土壤中生物降解,最终分解成水和二氧化碳,如表3的结果,用土埋法将可降解pbat低温除尘滤料埋于含有微生物的富营养土质中,观测形态,经3个月土埋后,可降解pbat低温除尘滤料发生破损、残缺,说明其具有生物可降解性。
[0071]
以上实施例仅用以说明本发明的技术方案,而非对其限制;尽管参照前述实施例对本发明进行了详细的说明,本领域的普通技术人员应当理解:其依然可以对前述各实施例所记载的技术方案进行修改,或者对其中部分技术特征进行等同替换;而这些修改或者替换,并不使相应技术方案的本质脱离本发明各实施例技术方案的精神和范围。
再多了解一些
本文用于企业家、创业者技术爱好者查询,结果仅供参考。