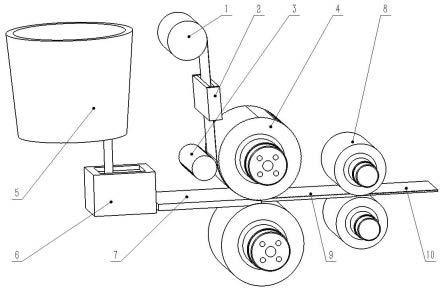
1.本发明属于双金属复合板带成形技术领域,具体涉及双金属复合板带深冷辅助波平固-液铸轧复合设备及方法。
背景技术:
2.双金属复合板带是由两种组元金属通过机械或冶金的方式实现界面结合的新型功能结构一体化复合材料,兼具两种材料的性能优势,同时可以降低材料成本,有望广泛应用于国防军工、海洋工程、石油化工等重要领域;轧制复合法由于工艺稳定、连续成形、生产效率高等优点,成为最具前景的层状金属复合板制备技术;但是,由于组元金属物理、化学、力学等性能差异显著,传统轧制复合过程存在显著的变形不协调现象,因此制备的双金属复合板依然存在结合强度低、板形质量差、残余应力大等关键技术瓶颈亟待解决。
3.针对传统轧制复合工艺存在的结合强度低、板形差、残余应力大等瓶颈问题,zl201410028776.4和zl201410028975.5提出一种波纹型轧辊的两道次波平轧制复合工艺,第1道次为粗轧,采用“波纹辊 平辊”的轧制方案,其中上辊为波纹辊,对应难变形金属,下辊为平辊,对应易变形金属,第2道次为精轧,采用“平辊 平辊”的轧制方案,将复合板表面波纹轧平,该方法可在较小的压下率下实现两种金属的高强度结合,并将复合板的结合界面形状由传统的二维提升至三维空间,大幅提高抗拉、抗剪、抗冲击等多种性能,有效改善板形质量,然而,波纹辊侧的难变形固态基体板带在局部强应力作用下极易出现撕裂现象;此外,由于轧制复合过程延伸比较大且波纹高度受限,仅仅依靠波纹成形过程的难变形固态基体板带体积预存进行组元协调变形调控效果有限,限制了该技术进一步推广。
4.固-液铸轧复合工艺集铸造复合工艺和轧制复合工艺为一体,可以实现双金属复合板带高效连续近终成形,但是复合界面氧化、重熔等问题十分显著,并且高温下复合界面处生成的金属间化合物以及铸轧态覆层金属中心偏析等现象显著降低复合板带综合性能;202210153034.9提出一种双层金属复合板波-平铸轧装置及方法,但是该方法将固态基体板带布置于平辊侧,液体覆层金属布置于波纹辊侧,虽然利用波纹辊的微幅搅拌作用可以起到抑制偏析作用,但是难变形的固态基体板带温度低,易变形的覆层金属温度高,以翘曲和撕裂为代表的变形不协调、残余应力大等问题十分突出,并且不能促进复合界面晶粒细化和形成三维空间界面。
5.面对巨大的市场需求,现有双金属复合板带的产品种类、尺寸规格、生产效率等亟待提高,在获得高强界面冶金结合效果、良好板形质量、较低残余应力的同时,兼顾高效率、短流程、低能耗的连续近终成形工艺已成为加快其工业应用进程的重点研究方向。
技术实现要素:
6.本发明针对上述问题提供了一种双金属复合板带深冷辅助波平固-液铸轧复合设备及方法。
7.为达到上述目的本发明采用了以下技术方案:
一种双金属复合板带深冷辅助波平固-液铸轧复合设备,包括开卷机、深冷处理装置、波纹辅助辊、固-液铸轧复合装置、熔炼炉、前箱、布流器和热轧复合装置,所述开卷机用于持续送出固态基体板带,所述固态基体板带依次经过深冷处理装置和波纹辅助辊进入固-液铸轧复合装置,所述熔炼炉用于持续浇注液态覆层金属,所述液态覆层金属依次经过前箱和布流器进入固-液铸轧复合装置,所述液态覆层金属和固态基体板带经过固-液铸轧复合装置和热轧复合装置的轧制复合后变为所需要的成品复合板带。
8.进一步,所述固-液铸轧复合装置包括上下相对设置的波纹铸轧辊和平铸轧辊,且所述波纹铸轧辊与波纹辅助辊相咬合,用于对固态基体板带进行波纹预制成形。
9.再进一步,所述热轧复合装置包括两个上下相对设置的平轧辊。
10.更进一步,所述波纹辅助辊和波纹铸轧辊上的波纹类型相同,且波纹曲线为正弦曲线、圆弧、三角形、梯形或样条曲线中的任意一种,所述波纹铸轧辊上波纹的高度小于覆层金属厚度的1/3。
11.一种双金属复合板带深冷辅助波平固-液铸轧复合方法,包括以下步骤:s1,固态基体板带由开卷机开卷,穿过深冷处理装置降温到目标温度t1,经过波纹辅助辊与波纹铸轧辊预制为波纹状,随后进入固-液铸轧复合装置,并与波纹铸轧辊紧密贴合;s2,液态覆层金属由熔炼炉熔炼以目标温度t2浇注,依次流经前箱和布流器,进入固-液铸轧复合装置,与波纹状的固态基体板带进行固-液铸轧复合,制备得到波纹态复合板带;s3,波纹态复合板带进入热轧复合装置进行平整轧制复合,波纹态复合板带的表面波纹被轧平,制备得到具有宏观或微观波纹复合界面的成品复合板带。
12.进一步,所述波纹态复合板带在热轧复合装置中的压下量大于波纹态复合板带上波纹的高度。
13.再进一步,所述步骤s1中,目标温度t1为-196~0℃。
14.与现有技术相比本发明具有以下优点:本发明利用超低温深冷处理提高固态基体板带塑性,使之能够通过波纹辅助辊与波纹铸轧辊预制成形为波纹状,在提高塑性的同时实现预存体积,促进固-液铸轧复合过程和热轧复合过程组元金属协调变形;本发明通过波纹辅助辊与波纹铸轧辊将深冷处理后的固态基体板带预制成形为波纹状,并使固态基体板带与波纹铸轧辊紧密贴合,可以通过固态基体板带的波纹界面对熔池进行微幅搅拌,改善覆层金属中心偏析现象;本发明的固-液铸轧复合过程中,通过深冷处理后的固态基体板带温度处于-196~0℃范围内,与液态覆层金属之间存在显著温度梯度,可以在复合界面处形成超细晶粒尺寸和优质凝固组织,促进复合界面形成高强冶金结合;本发明将预成形为波纹状的基体金属和液态覆层金属进行复合,固-液铸轧复合过程中波纹铸轧辊在波纹态复合板带的波谷处形成局部强应力,而热轧复合过程中平轧辊在波纹态复合板带的波峰处形成局部强应力,既可以促进异质金属轧制复合,减小残余应力,又可以进行具有空间特征的宏观或微观复合界面精准调控,显著提高界面结合强度,实现高强冶金结合;
本发明采用深冷处理固态基体板带,能够改善其强度、韧性和耐磨性,有利于固态基体板带预制成为波纹状,协调组元金属变形和提高凝固形核过冷度,通过控制降温速率,降低热冲击作用,操作简便、无污染、成本低,具有可观的经济效益和市场前景。
附图说明
15.图1为本发明的结构示意图;图2为本发明的钛/铝复合板带低温拉伸应力应变曲线;图中,开卷机—1、深冷处理装置—2、波纹辅助辊—3、固-液铸轧复合装置—4、熔炼炉—5、前箱—6、布流器—7、热轧复合装置—8、波纹态复合板带—9、成品复合板带—10。
具体实施方式
16.为了进一步阐述本发明的技术方案,下面通过实施例对本发明进行进一步说明。
17.实施例1如图1所示,一种双金属复合板带深冷辅助波平固-液铸轧复合设备,包括开卷机1、深冷处理装置2、波纹辅助辊3、固-液铸轧复合装置4、熔炼炉5、前箱6、布流器7和热轧复合装置8,所述开卷机1用于持续送出固态基体板带,所述固态基体板带依次经过深冷处理装置2和波纹辅助辊3进入固-液铸轧复合装置4,所述熔炼炉5用于持续浇注液态覆层金属,所述液态覆层金属依次经过前箱6和布流器7进入固-液铸轧复合装置4,所述液态覆层金属和固态基体板带经过固-液铸轧复合装置4和热轧复合装置8的轧制复合后变为所需要的成品复合板带10;所述固-液铸轧复合装置4包括上下相对设置的波纹铸轧辊和平铸轧辊,且所述波纹铸轧辊与波纹辅助辊3相咬合,用于对固态基体板带进行波纹预制成形,所述波纹辅助辊3和波纹铸轧辊上的波纹类型相同,且波纹曲线为正弦曲线、圆弧、三角形、梯形或样条曲线中的任意一种,所述波纹铸轧辊上波纹的高度小于覆层金属厚度的1/3;所述热轧复合装置8包括两个上下相对设置的平轧辊。
18.一种双金属复合板带深冷辅助波平固-液铸轧复合方法,包括以下步骤:s1,固态基体板带由开卷机1开卷,穿过深冷处理装置2降温到目标温度t1,目标温度t1为-196~0℃,经过波纹辅助辊3与波纹铸轧辊预制为波纹状,随后进入固-液铸轧复合装置4,并与波纹铸轧辊紧密贴合;s2,液态覆层金属由熔炼炉5熔炼以目标温度t2浇注,依次流经前箱6和布流器7,进入固-液铸轧复合装置4,与波纹状的固态基体板带进行固-液铸轧复合,制备得到波纹态复合板带9;s3,波纹态复合板带9进入热轧复合装置8进行平整轧制复合,所述波纹态复合板带9在热轧复合装置8中的压下量大于波纹态复合板带9上波纹的高度,波纹态复合板带9的表面波纹被轧平,制备得到具有宏观或微观波纹复合界面的成品复合板带10。
19.实施例2采用深冷辅助波平固-液铸轧复合设备及方法制备钛/铝复合板带;固态基体板带为纯钛ta2,宽度1000 mm,厚度0.5 mm,液态覆层金属为铝合金6061,目标宽度为1000mm,厚度为7mm;波纹辅助辊3与波纹铸轧辊的波纹类型为正弦曲线,
固-液铸轧复合装置4的波纹铸轧辊和平铸轧辊的直径为400mm,波纹铸轧辊周向均匀分布波高为2mm的正弦波纹,热轧复合装置8的平轧辊直径为200mm,深冷处理装置2采用气体法,利用氮气的汽化潜热对固态基体板带进行精准深冷处理。
20.制备步骤如下:s1,固态基体板带由开卷机1开卷,穿过深冷处理装置2降温到目标温度t1=-100℃,经过波纹辅助辊3与波纹铸轧辊预制为波纹状,随后进入固-液铸轧复合装置4,并与波纹铸轧辊紧密贴合;s2,液态覆层金属由熔炼炉5熔炼以目标温度t2=700℃浇注,依次流经前箱6和布流器7,进入固-液铸轧复合装置4,与波纹状的固态基体板带进行固-液铸轧复合,制备得到波纹态复合板带9;s3,波纹态复合板带9进入热轧复合装置8进行平整轧制复合,压下量为3mm,波纹态复合板带9的表面波纹被轧平,制备得到具有微观波纹复合界面的成品复合板带10。
21.对成品复合板带10进行剥离实验,结果表明,钛/铝复合板带剥离断裂位置位于铝基体侧,剥离强度达到50n/mm,即界面结合强度大于铝基体强度,远大于传统固-液铸轧复合工艺制备钛/铝复合板带的剥离强度20n/mm,复合界面晶粒细化,实现了复合界面高强冶金结合。
22.此外,钛/铝复合板带低温拉伸应力应变曲线如图2所示,随着拉伸温度降低,钛/铝复合板带的拉伸应力和延伸率均会提高,即深冷处理可以提高组元金属塑性以及二者协调变形能力。
23.实施例3采用深冷辅助波平固-液铸轧复合设备及方法制备钢/铜复合板带;固态基体板带为不锈钢316l,宽度1500 mm,厚度0.8 mm,液态覆层金属为纯铜t2,目标宽度为1500mm,厚度为8mm;波纹辅助辊3与波纹铸轧辊的波纹类型为样条曲线,固-液铸轧复合装置4的波纹铸轧辊和平铸轧辊的直径为500mm,波纹铸轧辊周向均匀分布波高为2mm的样条曲线,热轧复合装置8的平轧辊直径为250mm,深冷处理装置2采用气体法,利用氮气的汽化潜热对固态基体板带进行精准深冷处理。
24.制备步骤如下:s1,固态基体板带由开卷机1开卷,穿过深冷处理装置2降温到目标温度t1=-140℃,经过波纹辅助辊3与波纹铸轧辊预制为波纹状,随后进入固-液铸轧复合装置4,并与波纹铸轧辊紧密贴合;s2,液态覆层金属由熔炼炉5熔炼以目标温度t2=1100℃浇注,依次流经前箱6和布流器7,进入固-液铸轧复合装置4,与波纹状的固态基体板带进行固-液铸轧复合,制备得到波纹态复合板带9;s3,波纹态复合板带9进入热轧复合装置8进行平整轧制复合,压下量为2.5mm,波纹态复合板带9的表面波纹被轧平,制备得到具有宏观波纹复合界面的成品复合板带10。
25.对成品复合板带10进行剥离实验,结果表明,钢/铜复合板带剥离断裂位置位于铜基体侧,剥离强度达到90n/mm,即界面结合强度大于铜基体强度,远大于传统固-液铸轧复合工艺制备钢/铜复合板带的剥离强度40n/mm,复合界面晶粒细化,实现了复合界面高强冶金结合。
26.以上显示和描述了本发明的主要特征和优点,对于本领域技术人员而言,显然本发明不限于上述示范性实施例的细节,而且在不背离本发明的精神或基本特征的情况下,能够以其他的具体形式实现本发明。因此,无论从哪一点来看,均应将实施例看作是示范性的,而且是非限制性的,本发明的范围由所附权利要求而不是上述说明限定,因此旨在将落在权利要求的等同要件的含义和范围内的所有变化囊括在本发明内。
27.此外,应当理解,虽然本说明书按照实施方式加以描述,但并非每个实施方式仅包含一个独立的技术方案,说明书的这种叙述方式仅仅是为清楚起见,本领域技术人员应当将说明书作为一个整体,各实施例中的技术方案也可以经适当组合,形成本领域技术人员可以理解的其他实施方式。
再多了解一些
本文用于创业者技术爱好者查询,仅供学习研究,如用于商业用途,请联系技术所有人。