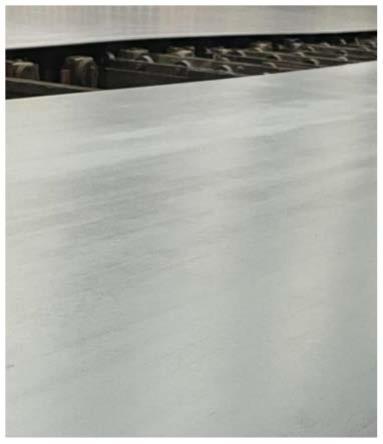
1.本发明属于船舶及海洋工程用结构钢技术领域,具体涉及一种高表面质量船板钢的生产方法。
背景技术:
2.船板钢用于制造船体结构、船坞、码头设施等,因其在制造时要涂装,所以对表面要求极其严格。在当今激烈的竞争市场中,表面质量是船板的主要质量指标之一。船厂对船板表面采取强光照射等手段,检测其表面是否有花斑、麻坑等缺陷。花斑、麻坑等缺陷的形成原因为出炉钢坯或轧制过程除鳞不彻底,在轧制中氧化铁皮呈片状或块状压入船板本体,喷丸前后表现为大小不一、形状和深浅不同花斑或麻坑,直接影响涂装后的表面质量。由于船板的出厂状态为轧态,表面覆盖氧化铁皮,而表面的检验是在船厂抛丸后进行,对涂装的高要求是各造船厂尤其是中小造船厂的装备技术瓶颈。
3.钢板在热轧的高温状态下与空气和水接触,就会生成氧化铁皮,最靠近铁层的是feo,依次向外是fe3o
4 和fe2o3, 按形成顺序分为一次氧化铁皮和二次氧化铁皮,其中一次氧化铁皮是在加热过程产生,二次氧化铁皮则是在轧制过程产生,常规手段就是通过高压水除鳞系统予以去除。当下中厚板装备发展趋势是大型化、自动化,产品趋势是高表面质量、高强度,因此在钢板轧制前与轧制中及时清除氧化铁皮就成为影响钢板表面质量的重要工序,而要获得很好的除鳞效果则除鳞水压力则有时需要高达23mpa。但是,对于一条老旧中厚板生产线,其除磷水压力一般仅有15~16mpa,若采用低温加热预防板坯生成剥离性差的fe2sio
4 则会因轧机扭矩的限制增加轧制道次。应用传统轧钢技术,难以兼顾生产过程的诸多因素,不能实现高表面质量钢板的规模化生产,如何在这样的生产线生产出高表面质量的钢板就成了一个技术难题。
4.中国专利cn103506382b(一种改善厚规格船板表面质量的生产方法),是一种通过调整加热炉气氛、除鳞压力、除鳞方式与控轧温度等轧制工艺参数生产18~50mm厚无表面粗糙等缺陷的船板轧制方法。中国专利cn109719146a(一种针对高表面质量中厚板产品的高效除鳞方法),是一种利用气雾喷淋装置的除鳞方法。
5.本发明创新思路,既然不能把轧态的钢板表面氧化铁皮去除干净,则利用老旧设备的现有能力,通过创新工艺所生产的轧态船板钢表面的氧化铁皮分布均匀、薄、无可见花斑,经抛丸可以把表面的氧化铁皮清除干净且无麻坑等缺陷,满足船板的高表面涂装质量要求。与现有技术中去除氧化铁皮的解决思路与技术手段不同。
技术实现要素:
6.为解决上述技术问题,本发明提供一种高表面质量船板钢的生产方法,其适用于厚度规格为8~20mm,牌号为a、b一般强度及a32、a36高强度船板钢的生产。本发明采用的技术方案是:一种高表面质量船板钢的生产方法包括板坯加热、粗除鳞、轧制、冷却、矫直工序;
板坯出加热炉后在除鳞箱进行一次粗除鳞,除鳞水压力15~16mpa,流量3150
±
50l/min。
7.所述轧制工序,采用单机架轧机轧制;(1)对于a、b一般强度船板钢采用两阶段轧制工艺,开轧温度1100
±
20℃,在开坯第1、第2道次与转钢后第1、第2道次进行4次精除鳞,第二轧程不除鳞,开轧温度1020
±
20℃,终轧温度920
±
20℃;(2)对于a32、a36高强度船板钢采用两阶段轧制工艺,第一轧程:开轧温度1100
±
20℃,在开坯第1、第2道次与转钢后第1、第2、第3道次中进行4次或5次精除鳞;第二轧程:不除鳞,开轧温度970
±
20℃,终轧温度870
±
30℃;所述精除鳞的水压为15~16mpa,流量3150
±
50l/min。
8.所述冷却工序,当h≤14mm时,采用空冷;当14<h≤20mm时,采用acc弱冷工艺,冷却速率5~8℃/s;所述h为成品船板钢厚度。
9.所述板坯加热工序,预热段温度≤850℃,ⅰ加热段温度1000
±
50℃,ⅱ加热段温度1250
±
30℃,均热段温度1200
±
30℃,总加热时间150~210min,加热炉内残氧含量2~5%。
10.所述轧制工序,采用3000mm单机架轧机轧制,板坯在辊道上停留不超过10s。
11.所述轧制工序,两阶段轧制工艺中的待温厚度为成品船板钢厚度的2~3倍,轧制力矩m
max =1150knm、轧制速度v
max =4.2m/s。
12.所述成品船板钢厚度为8~20mm。
13.本发明针对除磷水压力仅有15~16mpa的老旧中厚板生产线,通过创新轧制和冷却工序,在成品道次或第二轧程不除鳞,预防二次氧化铁皮除不净产生氧压;高温控轧下保证氧化铁皮有较好的塑性;快速轧制减小氧化铁皮的厚度;根据船板钢厚度采用不同的冷却制度,以弥补高温终轧产生的强度损失。通过上述工艺参数设定,所生产的轧态船板钢表面无肉眼可见花斑,生成的氧化铁皮分布均匀、致密且薄,可通过抛丸工艺清除干净、无麻坑、无皱皮等缺陷。
附图说明
14.图1为实施例2-1轧态船板钢的表面图;图2为实施例4-2轧态船板钢的表面图;图3为实施例4-3轧态船板钢的表面图;图4为实施例2-1轧态船板钢经过抛丸处理后的表面图;图5为实施例4-2轧态船板钢经过抛丸处理后的表面图。
15.图6为实施例4-3轧态船板钢经过抛丸处理后的表面图;图7为实施例5-1轧态船板钢的表面图;图8为实施例7-3轧态船板钢的表面图;图9为实施例8-1轧态船板钢的表面图;图10为实施例5-1轧态船板钢经过抛丸处理后的表面图;图11为实施例7-3轧态船板钢经过抛丸处理后的表面图;图12为实施例8-1轧态船板钢经过抛丸处理后的表面图。
具体实施方式
16.一种高表面质量船板钢的生产方法,其适用于厚度规格为8~20mm,牌号为a、b一般强度及a32、a36高强度船板钢的生产。其生产方法包括板坯加热、粗除鳞、轧制、冷却、矫直工序。各工序步骤如下所述:1、板坯加热工序:预热段温度≤850℃,ⅰ加热段温度1000
±
50℃,ⅱ加热段温度1250
±
30℃,均热段温度1200
±
30℃,总加热时间150~210min,加热炉内残氧含量2~5%。
17.2、粗除鳞工序:在板坯出加热炉后进行一次粗除鳞,除鳞水压力15~16mpa,流量3150
±
50l/min。
18.3、轧制工序:采用3000mm单机架轧机轧制,板坯在辊道上停留不超过10s;(1)对于a、b一般强度船板钢采用两阶段轧制工艺,待温厚度为成品船板钢厚度的2~3倍。开轧温度1100
±
20℃,在开坯第1、第2道次与转钢后第1、第2道次进行4次精除鳞,第二轧程不除鳞,开轧温度1020
±
20℃,终轧温度920
±
20℃;(2)对于a32、a36高强度船板钢采用两阶段轧制工艺,待温厚度为成品船板钢厚度的2~3倍。第一轧程:开轧温度1100
±
20℃,在开坯第1、第2道次与转钢后第1、第2、第3道次中进行4次或5次精除鳞;第二轧程:不除鳞,开轧温度970
±
20℃,终轧温度870
±
30℃;所述精除鳞的水压为15~16mpa,流量3150
±
50l/min;轧制力矩m
max =1150knm、轧制速度v
max =4.2m/s。
19.4、冷却工序:当h≤14mm时不采用acc冷却,自然空冷;当14<h≤20mm时采用acc弱冷工艺,冷却速率5~8℃/s;所述h为成品船板厚度。
20.5、钢板经矫直、剪切后入库。
21.采用上述方法生产的船板钢的化学成分组成及质量百分含量见表1、表2,各实施例工艺参数设置见表3、4、5、6,船板钢的力学性能见表7、8。
22.表1、各实施例船板钢的化学成分组成及质量百分含量(%)表2、各实施例船板钢的化学成分组成及质量百分含量(%)
表3、实施例1-4板坯加热、粗除鳞工序参数表4、实施例5-8板坯加热、粗除鳞工序参数
表5、实施例1-4轧制、冷却工序参数表6、实施例5-8轧制、冷却工序参数
表7、实施例1-4船板钢的力学性能表8、实施例5-8船板钢的力学性能
由图1、2、3、7、8、9可知,本发明所生产的船板钢表面无肉眼可见花斑,生成的氧化铁皮分布均匀、致密且薄。
23.由图4、5、6、10、11、12可知,本发明所生产的船板钢经过抛丸处理之后表面清除干净、无麻坑、无皱皮等缺陷。
再多了解一些
本文用于创业者技术爱好者查询,仅供学习研究,如用于商业用途,请联系技术所有人。