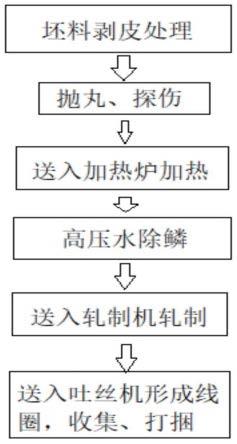
1.本发明涉及钢材轧制领域,尤其涉及一种产品表面质量高、稳定性好的超高强度弹簧钢线材轧制方法。
背景技术:
2.汽车减重成为汽车工业发展的必然趋势,悬架弹簧作为汽车的重要组件,减小其尺寸、减少缠绕圈数成为汽车减重的主要措施,而为了提高汽车安全性能,弹簧减小尺寸、减少缠绕圈数后其性能不能减甚至还要高于原来的性能,因此,提高弹簧钢的强度成为突破点,超高强度弹簧钢的生产成为必然。
3.超高强度弹簧钢是指热处理后材料的抗拉强度大于2000mpa,断面收缩率大于40%的弹簧钢材料,现有超高强度弹簧钢线材牌号有54sicr6、sae9254,超高强度弹簧钢在生产的过程中对材料表面质量、表面脱碳以及组织均匀性要求较高,如何在轧制过程中保证超高强度弹簧钢的要求,轧制出合格的超高强度弹簧钢线材,是亟需要解决的问题。
技术实现要素:
4.发明目的:本发明的目的是提供一种产品表面质量高、稳定性好的超高强度弹簧钢线材轧制方法。
5.技术方案:本发明包括以下步骤:
6.(1)使用两火成材工艺生产,对坯料进行剥皮处理之后再进行角部剥皮处理;
7.(2)对坯料抛丸、探伤,将坯料表面缺陷和表面原始脱碳层去除干净;
8.(3)送入步进式加热炉进行加热,经过预热段、加热段和均热段将坯料加热到预定的温度;
9.(4)进行高压水除鳞,将坯料在加热过程中产生的氧化铁皮去除干净;
10.(5)送入无扭轧制机进行轧制,经过粗轧、中轧、预精轧、精轧机和减定径轧制成所需规格线材;
11.(6)送入吐丝机形成一连串大直径的线圈,再落到风冷线上向前运输;
12.(7)通过收集和打捆形成成品。
13.进一步地,所述步骤(1)中坯料进行剥皮处理的剥皮深度为d,d≥0.8mm。
14.进一步地,所述步骤(2)对坯料抛丸、探伤后进行坯料整体面部修磨,采用五道次倒角,降低台车速度、提高砂轮切线速度以及降低坯料每道次修磨的平移量。
15.进一步地,所述步骤(5)中轧制用的导卫采用滚动导卫,即在空过槽和水冷槽底部加装滚动体的导卫。
16.进一步地,所述步骤(5)无扭轧制机进行轧制时对轧制速度的主导值、水箱开度和流量进行规定,1#轧机线速度为v,v≤0.23m/s,每个水冷段的两个水冷箱均匀打开,开度为40%-70%。
17.进一步地,所述步骤(6)吐丝机上线前进行动平衡测试,震动值为n,n≤6mm/s,盘
卷收集时托板下降速度调低。
18.进一步地,所述步骤(7)打捆时对打捆机过程参数进行优化,打捆机托起分两步进行,第一步托起高度设定为100mm-150mm,第二步托起高度为打捆机盘卷内圈上沿与c型钩刚好脱离,设定为320mm-380mm。
19.有益效果:本发明与现有技术相比,具有如下显著优点:可有效提高表面质量,消除弹簧钢线材表面全脱碳、降低总脱碳深度,提高线材组织均匀性,提高产品质量稳定性;用户能够稳定制作2000mpa级超高强度弹簧,订单量每月达到2000吨-3000吨,创造了良好的效益。
附图说明
20.图1为本发明的流程图。
具体实施方式
21.下面结合附图及实施方法对本发明的技术方案作进一步说明。
22.如图1所示,本发明包括以下步骤:
23.(1)使用150mm*150mm*12m的坯料,使用两火成材工艺生产,对坯料进行剥皮处理之后再进行角部剥皮处理;为消除坯料表面缺陷的影响,坯料进行剥皮处理,以往收集的缺陷最深0.6mm,因此规定剥皮深度d≥0.8mm,确保缺陷消除干净,为保证材料具有良好的性能,超高强度弹簧钢使用两火成材工艺生产,为消除开坯高温加热产生的脱碳,对坯料除剥皮处理外另外加一道角部剥皮处理,在充分消除角部脱碳,还能使角部修磨更加圆滑,杜绝尖角在加热时急剧升温产生全脱碳以及轧制过程中产生轧制缺陷。
24.(2)对坯料抛丸、探伤,将坯料表面缺陷和表面原始脱碳层去除干净;抛丸、探伤之后为提高坯料修磨质量,我们采用20-24目细砂轮修磨,坯料表面较深的缺陷先进行局部清理,待缺陷清理干净后,对坯料再进行整体面部修磨,倒角方式采用五道次倒角,适当降低台车速度至55-65m/min和提高砂轮切线速度至65-75m/s,降低坯料每道次修磨的平移量至16-20mm,使修磨后的坯料表面更加平整。
25.(3)送入步进式加热炉进行加热,经过预热段、加热段和均热段将坯料加热到预定的温度;
26.(4)进行高压水除鳞,将坯料在加热过程中产生的氧化铁皮去除干净;
27.(5)送入无扭轧制机进行轧制,经过粗轧6道次,中轧6道次,预精轧4道次,精轧机10道次,减定径4道次,轧制成所需规格线材;为保证轧制过程中的表面质量,轧线导卫使用滚动导卫,空过槽和水冷槽底部加装滚动体,防止轧件在过槽中滑动摩擦产生擦伤,为使盘条原材料组织均匀,提高后续淬火回火等热处理过程中的稳定性,超高强度弹簧钢盘条生产过程中对轧制速度的主导值、水箱开度和流量进行规定,1#轧机线速度v≤0.23m/s,每个水冷段的两个水冷箱均匀打开,避免单独打开一个水箱造成激冷产生不良组织,开度均匀打开,为40%-70%,避免激冷产生表面激冷层,在热处理时容易产生应力而断裂。
28.(6)送入吐丝机形成一连串大直径的线圈,再落到风冷线上向前运输;为使卷型保持整齐,吐丝机上线前进行动平衡测试,震动值n≤6mm/s,使吐丝机运行稳定,盘卷收集时托板下降速度调低,设定2500-3000,以防止托板下降速度过快造成盘卷收集时卷型不稳
定,出现参差不齐的现象。
29.(7)通过收集和打捆形成成品;对打捆机过程参数进行优化,将打捆机托起分两步进行,为防止打捆过程中破坏卷型,第一次托起高度不可过高,托起高度设定值为100mm-150mm,能够使压盘压紧之前卷型整体保持稳定,第二次托起高度为盘卷内圈上沿与c型钩刚好脱离,以免产生擦伤,第二次托起高度设定值为320mm-380mm。
30.超高强度汽车钢生产后,货场摆放时,只允许单层摆放,防止在码堆过程中造成压伤,超高强度汽车钢,物流运输时,执行精品物流方式,根据盘卷外圈尺寸大小进行定制木架,将盘卷摆放在木架上单层装车运输。
31.本发明的高强度弹簧钢采用54sicr6,54sicr6为德标弹簧钢牌号,产品主要用于汽车悬架簧等关键零部件,用户使用此牌号的弹簧钢制作2000mpa级弹簧,正常强度弹簧,缠绕圈数为9圈,超高强度弹簧,缠绕圈数为7圈,用于合资汽车品牌。
32.弹簧钢54sicr6的具体生产控制方法包括如下步骤:
33.(1)坯料修磨使用24目砂轮,台车速度60m/min,砂轮线速度68m/s,道次平移量16mm,整体修磨深度测量为1.0mm。
34.(2)坯料先进行一遍角部修磨,再进行总体修磨一遍,保证角部和总体的原始脱碳层去除干净,同时角部比较圆润,杜绝后续加热时局部尖角产生的急升温而产生脱碳。
35.(3)轧线与红钢接触部位全部进行滚动体化改造。
36.(4)上线送入吐丝盘进行震动值测量,震动值n调为4,集卷托板下降数值设置为2500。
37.(5)在打捆时,先使用5吨-8吨压力进行预压紧,使盘卷聚拢;正常打捆时,压力由原先正常26吨打捆压力降低为12吨-18吨。
38.(6)生产出的订单在货场摆放时,为防止低压力打捆的材料承重变形,只允许单层摆放,不能堆压;且卷与卷之前相隔30cm,不得相互接触,防止相互接触擦伤。
39.(7)物流运输时,执行精品物流方式,汽车底板摆放上根据盘卷外圈直径大小定制的木架,将盘卷摆放在木架上单层装车运输。
40.按照上述方法生产的54sicr6弹簧钢发往用户处进行制作2000mpa级超高强度弹簧钢丝,使用情况良好,达到用户要求。
再多了解一些
本文用于创业者技术爱好者查询,仅供学习研究,如用于商业用途,请联系技术所有人。