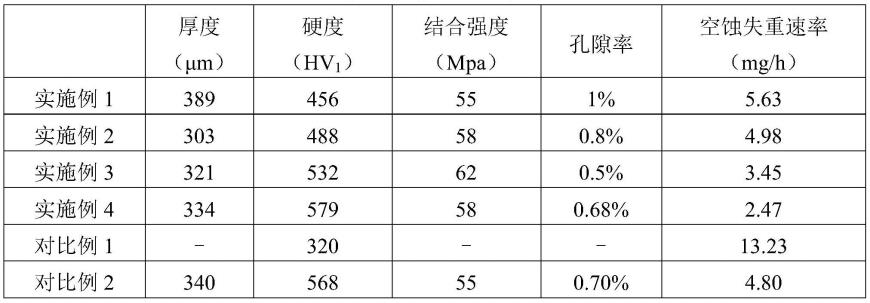
1.本发明属于合金涂层技术领域,具体地,本发明涉及一种抗空蚀钴基涂层及其制备方法。
背景技术:
2.空蚀是发生在水利机械运行过程中一种常见的破坏现象,是由于液体内部压力急剧降低引起了液体局部气化形成大量微小气泡,气泡急速溃灭后对过流部件造成局部变形和质量损失,导致水力机械的工作效率降低,从而严重影响了设备的使用性能、服役寿命,甚至设备的安全运行,产生巨大的经济损失。
3.由于空蚀仅发生在设备的表面,而涂层防护技术是保护材料表面不受破坏并提高其表面性能的一个重要手段,因此,使用抗空蚀涂层材料涂覆在过流部件的表面,以提高其抗空蚀能力、延长寿命是目前技术比较成熟且经济效益高的方式。目前,常见的抗空蚀涂层主要包括合金涂层,陶瓷涂层和有机涂层。然而,不同类型的防护涂层仍然存在着各自的优缺点,例如,铁基合金涂层成本较低,但其抗空蚀性能一般;陶瓷涂层(包括氧化物和碳化物陶瓷涂层)硬度高,抗空蚀性能较好,但其塑性差,且易受孔隙率和硬质相脆性失效影响;有机涂层(包括低表面能防污涂层、结构仿生防污涂层等)韧性好,但是其制备工艺较为复杂,且硬度相对较低,导致抗空蚀性能较差,而且还存在着与基体结合力不强、容易发生脱落等问题。总之,目前已有的抗空蚀涂层的制备方法较为复杂繁琐,所制得的抗空蚀涂层存在硬度低、结合强度低,易脱落失效等问题,因此,亟需开发一种综合性能更加优越的抗空蚀涂层。
技术实现要素:
4.本发明旨在至少在一定程度上解决相关技术中的技术问题之一。为此,本发明实施例提出一种抗空蚀钴基涂层及其制备方法。
5.本发明实施例一方面提出一种抗空蚀钴基涂层,该抗空蚀钴基涂层由包括质量百分比分别为55~75wt%co、25~35wt%cr、0~3wt%mo、1~5wt%fe、0~5wt%b、1~3wt%ni、0.5~2wt%c、2~10wt%w、0~2wt%si、0~1wt%nb组成的合金粉末经超音速火焰喷涂制备而成。
6.本发明实施例通过优化抗空蚀涂层的组成成分及其含量,设计一种以金属co为主要元素,cr为次要元素,同时还添加有b、c等非金属元素的钴基合金涂层,该涂层具有良好的抗空蚀性能;且本发明实施例中抗空蚀钴基涂层的原料粉均为常规金属粉末或非金属粉末,无需控制粉末为非晶粉末或或纳米晶,原料易得。
7.本发明实施例抗空蚀钴基涂层中的金属co具备低的堆垛层错能,在受到外力冲击的情况下更容易产生相变从而吸收更多能量,有效增长空蚀孕育周期,减小空蚀腐蚀破坏;还可以通过应力诱发相变强化,可抑制裂纹延展,进一步降低空蚀损伤;此外,金属co还具备良好的润湿性,可以很好的结合涂层中的硬质相,有效防止涂层被高速水流冲刷剥落。其
次,高含量的金属cr可以结合碳元素形成cr7c3、cr
23
c7等硬度很高的硬质相,起到弥散强化作用;且金属cr还可与ni、co等元素形成固溶强化,进一步提高涂层的强度。其它元素如金属w为硬质颗粒,可以增加涂层的硬度;金属mo可以提高涂层的抗酸腐蚀性能,且其塑性范围宽,能够喷厚涂层,且不易开裂,特别适合不规则形状部位喷熔;si、b及c元素也可以形成共晶化合物分布在固溶体间,起到第二相强化效果。
8.在本发明的一些实施例中,所述抗空蚀钴基涂层的组成包括:55~70wt%co、26~32wt%cr、0~2.5wt%mo、1.5~4wt%fe、0~3wt%b、1~3wt%ni、0.5~2wt%c、3~8wt%w、0~2wt%si、0~0.5wt%nb;其中,各单质元素的纯度不低于99.99%。
9.在本发明的一些实施例中,所述抗空蚀钴基涂层的厚度为250~500μm。
10.本发明实施例另一方面还提供了上述抗空蚀钴基涂层的制备方法,包括以下步骤:
11.(1)按比例称取所述抗空蚀钴基涂层的各原料组分,并进行机械球磨,然后将混合均匀的原料组分进行干燥、过筛,得到合金粉末;
12.(2)对钢基体表面进行预处理后,进行喷砂处理;
13.(3)采用超音速火焰喷涂工艺在钢基体表面制备抗空蚀钴基涂层;
14.(4)对喷涂后的抗空蚀钴基涂层进行机加工,降低其表面粗糙度至ra1.2~ra0.4;
15.其中,所述超音速火焰喷涂的工艺参数为:氧气流量为120~400l/min,丙烷流量为50~150l/min,喷涂距离为200~300mm,喷枪移动速度为900mm/s。
16.本发明实施例抗空蚀涂层的制备方法工艺简单,组成涂层的原料粉只需通过简单的机械球磨进行均匀混合和细化,无需采用真空雾化等特殊方法对原料粉进一步处理,简化了生产流程,同时降低生产难度和产品成本;且喷涂后的钴基涂层不需要额外使用封孔剂,只需通过简单的机加工来控制钴基涂层表面的粗糙度即可提高钴基涂层表面的抗空蚀性能,操作方便,成本较低。
17.涂层的抗空蚀性能不仅取决于喷涂材料的特性,还取决于涂层的喷涂方法。本发明实施例中采用超音速火焰喷涂方法对基体进行喷涂,超音速火焰喷涂是热喷涂领域继等离子喷涂之后的又一重大进步,是在普通火焰喷涂的基础上发展起来的一种新型热喷涂技术。作为热源,由于是基于燃气和氧气的燃烧,与等离子热源相比,具有温度低、速度高的特点。与其它热喷涂技术相比,超音速火焰喷涂不会给基体带去过多热量,基体不会受到高温热作用,进而可以有效抑制了基体的形变。
18.在本发明的一些实施例中,所述超音速火焰喷涂的工艺参数优选为:氧气流量为180~350l/min,丙烷流量为80~120l/min,喷涂距离为200~245mm。
19.在本发明的一些实施例中,所述机械球磨的时间为10~12h;所述干燥的温度为150~200℃,干燥时间为4~5h。
20.在本发明的一些实施例中,过筛后,所述合金粉末的粒径为20~100μm。
21.在本发明的一些实施例中,所述喷砂处理采用粒径为800~900μm的氧化铝粉末;所述喷砂处理的工艺参数为:喷砂气压为0.4mpa,喷砂距离为80~120mm。
22.在本发明的一些实施例中,对所述钢基体表面进行预处理的过程为:将钢基体的待喷涂面打磨至粗糙度为ra0.8,然后采用乙醇进行清洗。
23.在本发明的一些实施例中,所述机加工的方式为采用砂纸、平磨机、或铣床中的任
一种。
24.本发明所具有的优点和有益效果为:
25.(1)本发明通过合理优化涂层的组成成分及其含量,以金属co为主要元素,金属cr为次要元素,同时还添加有b、c等非金属元素,利用超音速火焰喷涂技术获得一种钴基合金涂层,该涂层具有良好的抗空蚀性能。
26.(2)本发明抗空蚀钴基涂层的制备方法简单,喷涂后的钴基涂层不需要额外使用封孔剂,只需通过简单的机加工来控制钴基涂层表面的粗糙度即可提高钴基涂层表面的抗空蚀性能,简单易操作,且成本较低。
27.(3)本发明采用超音速火焰喷涂制备抗空蚀钴基涂层,超音速火焰喷涂较高的喷射速度与较低的喷涂温度可以有效地抑制涂层材料烧损或者氧化,同时也不会使基体因受热而发生形变;且操作简便易控,也不受基体形状限制,适合批量化生产应用。
具体实施方式
28.为使本发明实施例的目的、技术方案和优点更加清楚,下面将对本发明实施例的技术方案进行清楚、完整的描述。显然,所描述的实施例是本发明的一部分实施例,而不是全部的实施例。基于所描述的本发明的实施例,本领域普通技术人员在无需创造性劳动的前提下所获得的所有其他实施例,都属于本发明的保护范围。
29.除非另作定义,本发明所使用的技术术语或者科学术语应当为本发明所属领域内有一般技能的人士所理解的通常意义。
30.本发明实施例一方面提出一种抗空蚀钴基涂层,该抗空蚀钴基涂层由包括质量百分比分别为55~75wt%co、25~35wt%cr、0~3wt%mo、1~5wt%fe、0~5wt%b、1~3wt%ni、0.5~2wt%c、2~10wt%w、0~2wt%si、0~1wt%nb组成的合金粉末经超音速火焰喷涂制备而成。
31.本发明实施例通过优化抗空蚀涂层的组成成分及其含量,设计一种以金属co为主要元素,cr为次要元素,同时还添加有b、c等非金属元素的钴基合金涂层,该涂层具有良好的抗空蚀性能;且本发明实施例中抗空蚀钴基涂层的原料粉均为常规市售金属粉末或非金属粉末,无需控制粉末为非晶粉末或或纳米晶,原料易得。
32.在本发明的一些实施例中,抗空蚀钴基涂层的组成包括:55~70wt%co、26~32wt%cr、0~2.5wt%mo、1.5~4wt%fe、0~3wt%b、1~3wt%ni、0.5~2wt%c、3~8wt%w、0~2wt%si、0~0.5wt%nb;其中,各单质元素的纯度不低于99.99%。
33.在本发明的一些实施例中,抗空蚀钴基涂层的厚度为250~500μm,例如可以为250μm、300μm、321μm、334μm、390μm、465μm、500μm等,此厚度范围既能起到较好的防护作用,又不会因为涂层过厚而导致设备部件增重,影响输出功率。
34.本发明实施例另一方面还提供了上述抗空蚀钴基涂层的制备方法,包括以下步骤:
35.(1)按比例称取所述抗空蚀钴基涂层的各原料组分,并进行机械球磨,然后将混合均匀的原料组分进行干燥、过筛,得到合金粉末;
36.(2)对钢基体表面进行预处理后,进行喷砂处理;
37.(3)采用超音速火焰喷涂工艺在钢基体表面制备抗空蚀钴基涂层;
38.(4)对喷涂后的抗空蚀钴基涂层进行机加工,降低其表面粗糙度至ra1.2~ra0.4;
39.其中,超音速火焰喷涂的工艺参数为:氧气流量为120~400l/min,丙烷流量为50~150l/min,喷涂距离为200~300mm,喷枪移动速度为900mm/s。
40.本发明实施例抗空蚀涂层的制备方法工艺简单,组成涂层的原料粉只需通过简单的机械球磨进行均匀混合和细化,无需采用真空雾化等特殊方法对原料粉进一步处理,简化了生产流程,同时降低生产难度和产品成本;且喷涂后的钴基涂层不需要额外使用封孔剂,只需通过简单的机加工来控制钴基涂层表面的粗糙度即可提高钴基涂层表面的抗空蚀性能,操作方便,成本较低。
41.在本发明的一些实施例中,超音速火焰喷涂的工艺参数为:在本发明的一些实施例中,所述超音速火焰喷涂的工艺参数优选为:氧气流量为180~350l/min,例如可以为180l/min、200l/min、260l/min、300l/min、320l/min、350l/min等;丙烷流量为80~120l/min,例如可以为80l/min、95l/min、100l/min、120l/min等;喷涂距离为200~245mm,例如可以为200mm、215mm、220mm、230mm、245mm等。
42.在本发明的一些实施例中,机械球磨的时间为10~12h,例如可以为10h、10.5h、11h、12h等;干燥的温度为150~200℃,例如可以为150℃、165℃、180℃、190℃、200℃等;干燥时间为4~5h,例如可以为4h、4.2h、4.5h、5h等。
43.在本发明的一些实施例中,过筛后,合金粉末的粒径为20~100μm,例如可以为20μm、25μm、30μm、40μm、50μm、60μm、80μm、100μm等。
44.在本发明的一些实施例中,喷砂处理采用粒径为800~900μm的氧化铝粉末;喷砂处理的工艺参数为:喷砂气压为0.4mpa;喷砂距离为80~120mm,例如可以为80mm、90mm、95mm、100mm、110mm、120mm等。
45.在本发明的一些实施例中,对钢基体表面进行预处理的过程为:将钢基体的待喷涂面打磨至粗糙度为ra0.8,然后采用乙醇进行清洗。
46.在本发明的一些实施例中,机加工的方式为采用砂纸、平磨机、或铣床中的任一种,通过简单的机加工,降低涂层表面的粗糙度,提高水下光滑过流性和抗空蚀冲击性能,进一步提高涂层使用寿命。
47.本发明实施例中所用的原料均可由市场中购得;本发明实施例中的钢基体均为马氏体不锈钢(牌号为zg06cr13ni4mo)。
48.以下实施例和对比例中所用测试皆参照相关标准:厚度测试按照gb/t 11374-2012《热喷涂涂层厚度的无损测量方法》进行;硬度测试按照gb/t 4340.1-1999《金属维氏硬度试验第1部分:试验方法》进行;结合强度测试按照gbt8642-2002《热喷涂-抗拉结合强度的测定》进行;孔隙率测试按照astme2109-2001(2014)《测定热喷镀涂层孔隙率面积百分比的标准试验方法》进行;空蚀失重速率测试按照gb/t 6383-2009《振动装置检测空蚀方法》进行,空蚀失重速率的测试参数设置为:温度为25℃恒温,频率为20khz,振幅为50μm,振动头距试样1mm。
49.下面结合具体实施例对本发明技术方案作进一步详细说明,实施例中未注明具体条件的实验方法为所属领域熟知的常规方法和常规条件。
50.实施例1
51.本实施例提供一种抗空蚀钴基涂层,该抗空蚀钴基涂层由以下元素组成:58wt%
co、28wt%cr、1wt%mo、3wt%fe、1wt%b、3wt%ni、1wt%c、4wt%w、1wt%nb。
52.该抗空蚀钴基涂层的制备方法,包括以下步骤:
53.(1)按比例称取上述抗空蚀钴基涂层的各原料组分,并进行机械球磨12h,然后将混合均匀的合金粉末置于真空烘箱中,于180℃下干燥5h,最后再筛选出粒径为60μm左右的合金粉末;
54.(2)在进行超音速火焰喷涂前,首先将钢基体的待喷涂面打磨至粗糙度为ra0.8,并使用乙醇进行清洗;然后再采用粒径为900μm的氧化铝粉末,在喷砂气压为0.4mpa、喷砂距离为120mm的条件下,对钢基体进行喷砂处理;
55.(3)采用超音速火焰喷涂工艺在钢基体表面制备抗空蚀钴基涂层,喷涂的工艺参数设置为:氧气压力为1.2mpa,氧气流量为180l/min,丙烷压力为0.7mpa,丙烷流量为55l/min,送粉量为40g/min,喷涂距离为200mm,喷枪移动速度为900mm/s,喷涂厚度为470μm;
56.(4)采用平磨机对喷涂后的抗空蚀钴基涂层的表面进行打磨,使其表面粗糙度降至ra1.2即可。
57.本实施例制得的抗空蚀钴基涂层的厚度为389μm,硬度为456hv1,涂层与基体的结合强度为55mpa,孔隙率为1%,空蚀失重速率为5.63mg/h。
58.实施例2
59.本实施例提供一种抗空蚀钴基涂层,该抗空蚀钴基涂层由以下元素组成:63wt%co、26wt%cr、1wt%mo、1wt%fe、3wt%ni、1wt%c、4wt%w、1wt%nb。
60.该抗空蚀钴基涂层的制备方法,包括以下步骤:
61.(1)按比例称取上述抗空蚀钴基涂层的各原料组分,并进行机械球磨12h,然后将混合均匀的合金粉末置于真空烘箱中,于200℃下干燥5h,最后再筛选出粒径为40μm左右的合金粉末;
62.(2)在进行超音速火焰喷涂前,首先将钢基体的待喷涂面打磨至粗糙度为ra0.8,并使用乙醇进行清洗;然后再采用粒径为900μm的氧化铝粉末,在喷砂气压为0.4mpa、喷砂距离为120mm的条件下,对钢基体进行喷砂处理;
63.(3)采用超音速火焰喷涂工艺在钢基体表面制备抗空蚀钴基涂层,喷涂的工艺参数设置为:氧气压力为1.2mpa,氧气流量为260l/min,丙烷压力为0.7mpa,丙烷流量为80l/min,送粉量为40g/min,喷涂距离为200mm,喷枪移动速度为900mm/s,喷涂厚度为400μm;
64.(4)采用平磨机对喷涂后的抗空蚀钴基涂层的表面进行打磨,使其表面粗糙度降至ra0.8即可。
65.本实施例制得的抗空蚀钴基涂层的厚度为303μm,硬度为488hv1,涂层与基体的结合强度为58mpa,孔隙率为0.8%,空蚀失重速率为4.98mg/h。
66.实施例3
67.本实施例提供一种抗空蚀钴基涂层,该抗空蚀钴基涂层由以下元素组成:59wt%co、28wt%cr、1wt%mo、3wt%fe、3wt%ni、1wt%c、4wt%w、1wt%nb。
68.该抗空蚀钴基涂层的制备方法,包括以下步骤:
69.(1)按比例称取上述抗空蚀钴基涂层的各原料组分,并进行机械球磨12h,然后将混合均匀的合金粉末置于真空烘箱中,于150℃下干燥5h,最后再筛选出粒径为20μm左右的合金粉末;
70.(2)在进行超音速火焰喷涂前,首先将钢基体的待喷涂面打磨至粗糙度为ra0.8,并使用乙醇进行清洗;然后再采用粒径为900μm的氧化铝粉末,在喷砂气压为0.4mpa、喷砂距离为120mm的条件下,对钢基体进行喷砂处理;
71.(3)采用超音速火焰喷涂工艺在钢基体表面制备抗空蚀钴基涂层,喷涂的工艺参数设置为:氧气压力为1.2mpa,氧气流量为300l/min,丙烷压力为0.7mpa,丙烷流量为80l/min,送粉量为40g/min,喷涂距离为200mm,喷枪移动速度为900mm/s,喷涂厚度为450μm;
72.(4)采用平磨机对喷涂后的抗空蚀钴基涂层的表面进行打磨,使其表面粗糙度降至ra0.4即可。
73.本实施例制得的抗空蚀钴基涂层的厚度为321μm,硬度为532hv1,涂层与基体的结合强度为62mpa,孔隙率为0.5%,空蚀失重速率为3.45mg/h。
74.实施例4
75.本实施例提供一种抗空蚀钴基涂层,该抗空蚀钴基涂层由以下元素组成:59wt%co、28wt%cr、1wt%mo、2.5wt%fe、3wt%ni、1wt%c、4wt%w、0.5wt%si、1wt%nb。
76.该抗空蚀钴基涂层的制备方法,包括以下步骤:
77.(1)按比例称取上述抗空蚀钴基涂层的各原料组分,并进行机械球磨12h,然后将混合均匀的合金粉末置于真空烘箱中,于150℃下干燥5h,最后再筛选出粒径为20μm左右的合金粉末;
78.(2)在进行超音速火焰喷涂前,首先将钢基体的待喷涂面打磨至粗糙度为ra0.8,并使用乙醇进行清洗;然后再采用粒径为900μm的氧化铝粉末,在喷砂气压为0.4mpa、喷砂距离为120mm的条件下,对钢基体进行喷砂处理;
79.(3)采用超音速火焰喷涂工艺在钢基体表面制备抗空蚀钴基涂层,喷涂的工艺参数设置为:氧气压力为1.2mpa,氧气流量为350l/min,丙烷压力为0.7mpa,丙烷流量为100l/min,送粉量为40g/min,喷涂距离为220mm,喷枪移动速度为900mm/s,喷涂厚度为489μm;
80.(4)采用平磨机对喷涂后的抗空蚀钴基涂层的表面进行打磨,使其表面粗糙度降至ra0.4即可。
81.本实施例制得的抗空蚀钴基涂层的厚度为334μm,硬度为579hv1,涂层与基体的结合强度为58mpa,孔隙率为0.68%,空蚀失重速率为2.47mg/h。
82.对比例1
83.本对比例提供一种钢基体,该钢基体为一种常用的水电基材马氏体不锈钢(牌号为zg06cr13ni4mo),将其清洗干净后进行打磨,直至其表面粗糙度降至ra0.8即可。
84.本对比例中打磨处理后的钢基体的硬度为320hv1,空蚀失重速率为13.23mg/h。
85.对比例2
86.本对比例提供一种抗空蚀钴基涂层,该抗空蚀钴基涂层的组成成分及其含量、以及喷涂过程均与实施例4相同,不同之处在于,本对比例中的涂层的喷涂厚度为340μm;且本对比例中的涂层的制备过程不包括实施例4中的步骤(4),即本对比例中的涂层在喷涂完成后,不再利用机加工对涂层表面进行打磨处理。
87.本对比例最终制得的抗空蚀钴基涂层的厚度为340μm,硬度为568hv1,涂层与基体的结合强度为55mpa,孔隙率为0.70%,空蚀失重速率为4.80mg/h。
88.与对比例2相比较可知,实施例4在涂层喷涂完成后,通过简单的机加工对涂层进
行打磨处理,以降低涂层表面的粗糙度,从而可以降低其空蚀失重速率,提高了涂层的抗空蚀冲击性能,进一步提高涂层的使用寿命。
89.分别对上述实施例1~4制备的抗空蚀钴基涂层、对比例1中打磨处理后的钢基体以及对比例2中的抗空蚀钴基涂层的厚度、硬度、结合强度、孔隙率、和空蚀失重速率进行检测,其检测结果如表1所示(其中,空蚀失重速率测试进行了12小时)。
90.表1性能测试结果
[0091][0092]
从表1可以看出,本发明实施例所制得的抗空蚀钴基涂层其结合强度较高,均在55mpa以上;且其空蚀失重速率较低,表现出良好的耐空蚀性能。
[0093]
在本发明中,术语“一个实施例”、“一些实施例”、“示例”、“具体示例”、或“一些示例”等意指结合该实施例或示例描述的具体特征、结构、材料或者特点包含于本发明的至少一个实施例或示例中。在本说明书中,对上述术语的示意性表述不必须针对的是相同的实施例或示例。而且,描述的具体特征、结构、材料或者特点可以在任一个或多个实施例或示例中以合适的方式结合。此外,在不相互矛盾的情况下,本领域的技术人员可以将本说明书中描述的不同实施例或示例以及不同实施例或示例的特征进行结合和组合。
[0094]
尽管上面已经示出和描述了本发明的实施例,可以理解的是,上述实施例是示例性的,不能理解为对本发明的限制,本领域的普通技术人员在本发明的范围内可以对上述实施例进行变化、修改、替换和变型。
再多了解一些
本文用于创业者技术爱好者查询,仅供学习研究,如用于商业用途,请联系技术所有人。