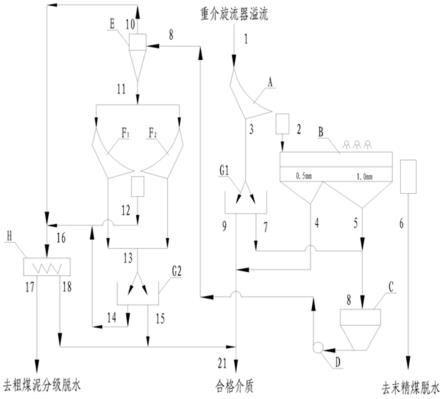
1.本发明属于末煤重介回收工艺技术领域,具体涉及一种浓缩-磁选联合的选煤厂介质回收工艺。
背景技术:
2.重介选煤因其分选精度高、自动化程度高、密度便于控制等诸多优势在各大选煤厂被广泛应用。介质回收作为重介分选工艺的重要环节,不仅影响着分选介质稳定性,也关系着介质损耗大小,是决定分选精度和生产成本的关键因素,在末煤重介洗选工艺中表现尤为突出。现有末煤分选介质系统一般采用直接磁选回收方式,精煤稀介(合介分流和脱介筛稀介)和重产物稀介(中矸脱介筛稀介)分别去磁选机回收处理,磁选后精矿去合介桶,精煤磁尾脱水后作为粗精煤泥,中矸磁尾脱水后作为粗中煤泥。
3.现有直接磁选工艺中,磁选承担着脱泥、介质净化回收的多重任务,但实际生产中磁选效果往往不理想,主要原因有:(1)磁选入料波动大。精煤磁选的入料由合介分流和筛下稀介组成,合介分流作为介质系统中调节悬浮液性质、分选密度、桶位等参数的关键变量,往往不稳定。因此,在生产过程中磁选机入料因分流量而波动,经常出现负荷高、介质损失严重的情况;(2)磁选机最佳工况条件苛刻。磁选效率与其最佳工况条件密切相关,要求入料量≤100m3/(h
·
m),磁性物含量≤18.5t/(h
·
m),15%≤入料浓度≤25%,否则磁选效率难以得到保证。由于波动的入料性质和磁选机苛刻的工况条件,现有直接磁选中磁选效率低、介耗大、重介成本高,成为困扰造成众多选煤厂的难题。
技术实现要素:
4.本发明的目的在于提供一种浓缩-磁选联合的选煤厂介质回收工艺,解决了现有直接磁选回收介质工艺存在入料波动大、磁选效率低、介耗高的问题。本发明以浓缩 磁选联合回收代替单一磁选方式,减少合介分流,稳定了磁选入料性质,降低了磁选负荷,因此提高了磁选效率,降低了介质损耗。
5.本发明所采用的技术方案是,一种浓缩-磁选联合的选煤厂介质回收工艺,具体包括以下步骤:
6.(a)精煤脱介;重介旋流器分选后的末精煤溢流经过一次脱介弧形筛和脱介筛脱水脱介,得到弧形筛合介、脱介筛合介、脱介筛稀介和筛上物;
7.(b)一次分流;弧形筛合介通过分流器分成固定的两部分,一部分合介返回合介桶作为合格介质;另一部分作为合介分流和步骤a中的脱介筛稀介去稀介桶中;
8.(c)稀介分级;步骤a中脱介筛稀介和步骤中合介分流经稀介桶缓冲后经泵送至分级旋流器分级浓缩,得到溢流和底流;
9.(d)底流脱介;步骤c中底流给入二次弧形筛脱介,得到筛上物及筛下合介;筛上物去磁选机磁选回收,筛下合介去二次分流;
10.(e)二次分流;步骤d中筛下合介通过分流器分成两部分,一部分介质返回合介桶
作为合格介质;另一部分作为二次合介分流去磁选磁选回收;根据煤质情况、分选密度、悬浮液特性等动态调节筛下合介去合介桶或磁选机的比例。
11.(f)磁选回收:步骤c中溢流、步骤d中筛上物、步骤e中二次合介分流去磁选机磁选处理,得到磁选精矿和尾矿;精矿与步骤a中脱介筛合介、步骤b中合格介质、步骤e中合格介质一并作为最终合格介质循环使用,尾矿去粗煤泥分级脱水。
12.本发明的特点还在于,
13.步骤b中,去稀介桶合介分流量为固定分流,取25%~35%间的定值。
14.步骤c中,分级旋流器e的锥角为15
°
~20
°
,安装角度为10
°
~15
°
,分级粒度在0.1mm~0.15mm之间。
15.步骤c中,分级旋流器e的入料压力为0.15-0.2mpa,入料质量浓度在20%~30%之间。
16.步骤f中,磁选机的磁场强度为1600~2000gs。
17.本发明的有益效果是:
18.(1)稀介质在分级旋流器中完成分级、浓缩,底流中经弧形筛脱出的部分合介可直接去合介桶,减少了进入磁选环节的负荷量,以浓缩 磁选联合回收代替了单一磁选方式,减少了合介分流,降低了磁选固有损失带来的介质损耗;
19.(2)稀介质分级浓缩后,煤泥富集于溢流,介质系统中煤泥平衡通过分级溢流和二次合介分流共同完成,避免了单一分流因煤泥平衡控制带来的波动。因此,由溢流和二次分流组成的磁选机入料性质更为稳定,减少了磁选机因入料不均衡带来磁选损耗;
20.(3)固定分流和二次动态分流方式,不仅保证了分级稳定性和介质系统的平衡,而且有效降低了磁选机入料量、磁性物含量和入料浓度,使其在允许负荷内运行,提高了磁选效率,减少了磁选能力不足、效率低带来的介质损耗;
21.(4)本发明工艺简单,投资少,回收效率高,经济效益显著。
附图说明
22.图1为本发明方法的设备流程图;
23.图2为现有技术中的选煤工艺流程图;
24.图3为本发明实施例选煤工艺流程图。
25.图中:a.一次脱介弧形筛;b.精煤脱介筛;c.稀介桶;d.稀介泵;e.分级旋流器;f1、f2.二次脱介弧形筛;g1、g2.分流器;h.磁选机。
具体实施方式
26.下面结合附图和具体实施方式对本发明进行详细说明。
27.如图1所示,本发明一种浓缩-磁选联合的选煤厂介质回收工艺,具体包括以下步骤:
28.(a)精煤脱介;重介旋流器分选后的末精煤溢流1经过一次脱介弧形筛a和脱介筛b脱水脱介,得到弧形筛合介3、脱介筛合介4、脱介筛稀介5和筛上物6;
29.其中,筛上物6脱水后作为精煤产品。
30.(b)一次分流;弧形筛合介3通过分流器g1分成两部分,部分合介9返回合介桶作为
合格介质;部分作为合介分流7和步骤a中的脱介筛稀介5去稀介桶c中;
31.去稀介桶c合介分流7为固定分流,一般取25%~35%的定值。
32.(c)稀介分级;步骤a中脱介筛稀介5和步骤b中合介分流7经稀介桶c缓冲后经泵d送至分级旋流器e分级浓缩,得到溢流10和底流11;
33.分级旋流器e的锥角为15
°
~20
°
,安装角度为10
°
~15
°
,分级粒度在0.1mm~0.15mm之间。
34.分级旋流器e的入料压力为0.15-0.2mpa,入料质量浓度在20%~30%之间。
35.(d)底流脱介;步骤c中底流11给入二次弧形筛f1、f2脱介,得到筛上物12及筛下合介13;筛上物12去磁选机h磁选回收,筛下合介12去二次分流;
36.(e)二次分流;步骤d中筛下合介12通过分流器g2分成两部分,部分介质15返回合介桶作为合格介质;少部分作为二次合介分流14去磁选机h磁选回收;
37.根据煤质情况、分选密度、悬浮液特性等动态调节去合介15和合介分流14的比例。
38.(f)磁选回收:步骤c中溢流10、步骤d中筛上物12、步骤e中二次合介分流14去磁选机h磁选处理,得到磁选精矿18和尾矿17;精矿18与步骤a中脱介筛合介4、步骤b中部分合介9、步骤e中部分介质15一并作为最终合格介质21循环使用,尾矿17去粗煤泥分级脱水;
39.磁选机h的磁场强度为1600~2000gs。
40.图2为现有技术中采用直接磁选回收介质的典型选煤工艺流程,图3为本发明的一种浓缩-磁选联合回收介质的实施例选煤工艺流程。本发明以浓缩 磁选联合回收代替了单一磁选方式,解决了现有选煤工艺中的直接磁选效率低、介耗大、重介成本高的问题。
41.实施例
42.该选煤厂为3.00mt/a炼焦煤选煤厂,-50mm原煤不脱泥直接进入三产品重介质旋流器分选,分成精煤、中煤、矸石。三个产品分别进入各自弧形筛和脱介筛,脱介筛前段为合格介质段,后段为稀介质段。其中精煤弧形筛下一部分合格介质和精煤脱介筛合介一并进入合格介质桶,另一部分弧形筛下合介分流进入稀介质桶,分流量在15%~35%间。精煤脱介筛下稀介质进入精煤稀介桶,中煤、矸石筛下稀介质合并进入中矸稀介桶。脱介筛筛上精煤、中煤脱水后成为最终产品,筛上矸石直接排出。
43.稀介桶物料经缓冲后泵送入精煤滚筒式磁选机回收介质,中煤、矸石稀介质泵送入中矸磁选机回收介质。磁选机精矿自流均返回合格介质桶,与各自脱介筛下合介一起缓冲后泵送返回重介旋流器内使用,精煤磁选尾矿脱水后作为粗精煤泥,中矸磁选尾矿脱水后作为粗中煤泥,煤泥水自流进入后续处理环节。
44.图3为本发明一种浓缩-磁选联合的选煤厂介质回收工艺流程图,在现有实施方案上新增了分级浓缩、弧形筛脱介回收、二次分流环节。
[0045]-50mm原煤不脱泥直接进入无压三产品重介质旋流器分选,分成精煤、中煤、矸石。三个产品分别进入各自弧形筛和脱介筛,脱介筛前段为合格介质段,后段为稀介质段。其中精煤弧形筛下65%合格介质和精煤脱介筛合介一并进入合格介质桶,弧形筛下35%合介分流和精煤脱介筛下稀介质进入精煤稀介桶,中煤、矸石筛下稀介质合并进入中矸稀介桶。脱介筛筛上精煤、中煤脱水后成为最终产品,筛上矸石直接排出。
[0046]
稀介桶物料经缓冲后泵送入分级旋流器进行浓缩,得到溢流和底流。底流给入弧形筛脱介,得到筛上物及筛下合介。筛下合介通过分流器分成两部分,部分返回合介桶作为
合格介质,部分作为二次合介分流去磁选机磁选回收,合介分流量为25%~45%动态调节以保证系统平衡。分级溢流、弧形筛上物、二次合介分流自流至磁选机处理,得到磁选精矿作为合格介质,磁选尾矿去粗煤泥分级脱水环节。中煤、矸石稀介质泵送入中矸磁选机回收介质。磁选精矿自流均返回合格介质桶,与各自脱介筛下合介一起缓冲后泵送返回重介旋流器内使用,精煤磁选尾矿脱水后作为粗精煤泥,中矸磁选尾矿脱水后作为粗中煤泥,煤泥水自流进入后续处理环节。
[0047]
该选煤厂现有工艺吨煤介耗在1.20kg/t左右,实施本发明工艺后可降低至0.85kg/t以下,采用本工艺可使现有介耗降低25%以上,磁选机负荷可降低30%左右。
再多了解一些
本文用于创业者技术爱好者查询,仅供学习研究,如用于商业用途,请联系技术所有人。