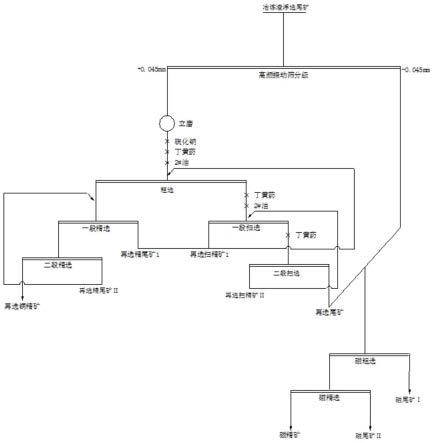
1.本发明涉及渣选矿领域,具体涉及一种铜冶炼渣浮选尾矿的处理方法。
背景技术:
2.铜冶炼渣浮选尾矿是指铜冶炼渣经过浮选工艺回收铜后产出的废弃矿料,其中的铜含量不高,且很难再分离回收,因此一般都是将浮选尾矿废弃处理,或者外售给水泥厂做辅料。
3.然而,随着社会经济的发展,我国铜金属消费量迅猛增长,铜冶炼渣以及浮选尾矿的数量也逐年提高,据统计,平均年产铜冶炼渣浮选尾矿产量约2000万吨,浮选尾矿中含金属铜约6万吨,含铁约700万吨,可见,回收废弃尾矿中的有价金属具有较高的资源价值和经济价值。
4.现有技术中,提高铜回收率的方法主要是不断优化冶炼渣的浮选工艺,以期能够降低浮选尾矿的铜品位,减少资源的浪费。不同的冶炼渣浮选难度不同,铜冶炼渣包括熔炼渣、转炉渣、电炉渣等,其中熔炼渣相对较为常见,其浮选难度也较大,调查研究表明,我国大多数铜熔炼渣浮选尾矿铜品位高达0.30%~0.35%,这甚至与国内部分铜矿山生产原矿品位相当,资源浪费严重,即使是技术和管理较为成熟的渣选厂,其渣选尾矿铜品位也在0.25%左右。而转炉渣和电炉渣的浮选难度相对较小,其尾矿含铜可降低至约0.22%。
5.还有少数情况是浮选工艺结束后,对浮选尾矿进行再磨处理,然后进入磁选产出部分磁精矿,磁精矿外售可以获得一些经济效益,然而,浮选尾矿本身粒径较小,且产量极大,再磨处理对设备要求较高,能耗和钢耗大,得到的磁精矿品位也很难提高到售卖标准(磁精矿中铁品位能够达到50%的话,价格会大幅度提高),投入和产出不成正比,因此限制了冶炼渣浮选尾矿中的资源回收。
技术实现要素:
6.本发明的目的在于提供一种铜冶炼渣浮选尾矿的处理方法,大大降低了浮选尾矿回收铜和铁的投入,不仅减少了资源浪费,且能够为企业带来经济效益。
7.为实现上述目的,本发明采用的技术方案为:一种铜冶炼渣浮选尾矿的处理方法,将浮选尾矿按照粒径大小分成粗料和细料两部分,细料部分进行磁选,粗料部分先进行磨矿和浮选作业得到铜精矿后,再送至磁选作业,得到磁精矿。
8.上述方案,将浮选尾矿中粒径较大、铜品位相对较高的部分分离出来单独磨矿和浮选,这部分物料相对较少,磨矿和浮选的压力大大降低;细料和浮选后的尾矿再进行磁选,既能减少铜铁资源的浪费,又给企业带来了经济效益,该方法适用范围广,可用于熔炼渣、转炉渣和电炉渣等不同类型冶炼渣的浮选尾矿处理。
9.所述方法包括如下步骤:
10.a)浮选尾矿分级:将铜冶炼渣浮选所得尾矿过筛得到粗料和细料,所述筛的孔径为0.074~0.038mm;
11.b)再磨再选:将步骤a)所得粗料进行磨矿作业,磨矿细度为-0.045mm占90%以上;磨矿后的物料进行浮选作业,得到再选铜精矿和再选尾矿,再选铜精矿送至铜冶炼系统处理;
12.c)磁选:将步骤a)所得细料和步骤b)所得再选尾矿进行磁粗选,得到磁粗精矿和磁尾矿ⅰ,磁粗精矿进行磁精选得到磁精矿和磁尾矿ⅱ,磁尾矿ⅰ和磁尾矿ⅱ作为最终尾矿废弃或外售。
13.具体地,步骤a)中,所述筛的孔径为0.045mm。
14.步骤b)中,所述浮选作业是将磨矿后的物料进行粗选得到再选粗精矿和再选粗尾矿,再选粗精矿进行两段精选作业,再选粗尾矿进行两段扫选作业。其中,浮选作业时加入调整剂、捕收剂和起泡剂;所述调整剂为硫化钠、捕收剂为丁黄药、起泡剂为2#油;加入量为硫化钠30g/t、丁黄药50g/t、2#油15g/t,即每吨绝干物料加入硫化钠30g、丁黄药50g、2#油(松醇油)15g。
15.两段精选作业是再选粗精矿先进行一段精选得到再选铜精矿ⅰ和再选精尾矿ⅰ,再选铜精矿ⅰ进行二段精选得到再选铜精矿和再选精尾矿ⅱ,再选精尾矿ⅰ返回至粗选作业循环处理,再选精尾矿ⅱ返回至一段精选循环处理。
16.两段扫选作业是再选粗尾矿先进行一段扫选得到再选扫精矿ⅰ和再选扫尾矿ⅰ,再选扫尾矿ⅰ进行二段扫选得到再选扫精矿ⅱ和再选尾矿,再选扫精矿ⅰ返回至粗选作业循环处理,再选扫精矿ⅱ返回至一段扫选循环处理。其中,一段扫选作业时加入丁黄药10g/t、2#油10g/t;二段扫选加入丁黄药10g/t。
17.所述步骤c)中,磁粗选磁场强度为2000gs~3000gs,磁精选磁场强度为1500gs~2000gs。
18.采用本发明的技术方案对铜冶炼渣浮选尾矿进行处理,降低了金属资源的浪费,也为企业提高了经济效益。以申请人铜陵有色金属集团的金冠铜业分公司为例,按照本发明的方案,年处理冶炼渣180万吨,浮选尾矿含铜降低0.035%,即每年多回收630吨铜,铜的价格按照6万元人民币每吨计算,多回收的铜价值3780万元,而处理工艺的经济投入和维护成本每年仅需数百万元,再加上回收的磁精矿可以稳定保持在50%以上的品位标准,这一部分的经济效益也非常可观。
附图说明
19.图1为本发明浮选尾矿处理方法示意图;
20.图2为对比例中浮选尾矿处理方法示意图。
具体实施方式
21.下面结合实施例对本发明的技术方案作进一步详述。
22.实施例1:筛分试验及筛孔径的选择
23.安徽某冶炼渣选车间,冶炼渣性质为熔炼渣,经浮选流程选别铜后,得到的浮选尾矿含铜为0.264%,将浮选尾矿进行多级筛分,筛孔径分别为0.074mm、0.045mm、0.038mm,各级物料占比及铜分布如下。
24.表1浮选尾矿粒度组成及铜分布
[0025][0026]
从表1可以看出,随着粒级逐渐变粗,相应粒级含铜也逐渐升高。其中, 0.045mm(“ ”表示粒径大于0.045mm)粒级总含铜高达0.416%,较平均品位高出0.152个百分点;而-0.045mm(
“‑”
表示粒径小于0.045mm)粒级总含铜为0.205%,较平均品位低0.059个百分点。
[0027]
由此可见,粒径在0.045mm以上的物料铜品位相对较高,有回收价值,且这一部分物料仅占浮选尾矿总量的三分之一左右,磨矿和浮选的压力小。且该尺寸可更好地使得尾矿含铜得到显著降低的同时,实际操作时筛孔堵塞现象少,减少了对渣选厂日常生产能力和后期设备维护造成的影响。
[0028]
实施例2:浮选尾矿的处理
[0029]
a)采用0.045mm粒级标准筛对实施例1中的浮选尾矿进行人工筛分,筛分结果如表2所示。
[0030]
表2浮选尾矿筛分数据
[0031]
物料名称物料占比/%铜品位/%铜分布/%粗料( 0.045mm)27.80.41643.80细料(-0.045mm)72.20.20556.20合计100.00.264100.00
[0032]
b)将上述筛分得到的粗料( 0.045mm)用立磨机进行磨矿作业,磨矿细度为-0.045mm占95.5%,(相比于每吨绝干物料)加入硫化钠30g/t、丁黄药50g/t、2#油(松醇油)15g/t进行粗选作业,得到再选粗精矿和再选粗尾矿,再选粗精矿进行两段精选作业,再选粗尾矿进行两段扫选作业。
[0033]
两段精选作业是再选粗精矿先进行一段精选得到再选铜精矿ⅰ和再选精尾矿ⅰ,再选铜精矿ⅰ进行二段精选得到再选铜精矿和再选精尾矿ⅱ,再选精尾矿ⅰ返回至粗选作业循环处理,再选精尾矿ⅱ返回至一段精选循环处理,再选铜精矿送至铜冶炼系统,产出铜产品,实现了物料的循环处理。
[0034]
两段精选作业是再选粗精矿先进行一段精选得到再选铜精矿ⅰ和再选精尾矿ⅰ,再选铜精矿ⅰ进行二段精选得到再选铜精矿和再选精尾矿ⅱ,再选精尾矿ⅰ返回至粗选作业循环处理,再选精尾矿ⅱ返回至一段精选循环处理。具体如图1所示。
[0035]
表3再选作业所得铜精矿和尾矿数据
[0036]
[0037][0038]
将再选铜尾矿和浮选尾矿分级后的细料作为再选总铜尾矿,与筛分前的浮选尾矿进行铜品位比较,具体参见表4。
[0039]
表4不同尾矿分析结果
[0040][0041]
由上表数据可知,浮选尾矿中的粗料经再磨再选后,最终可使得总尾含铜由之前的0.264%降为0.228%,共计降低0.036个百分点,降低效果显著。要知道,对于浮选尾矿来讲,哪怕降低0.01个百分点都是相当不容易的,都需要付出相当大的代价,仅仅靠浮选工艺是行不通的,由此也可以见得,本技术的技术方案为废弃尾矿中铜的回收提供了新的方向。
[0042]
c)磁选:将步骤a)所得细料和步骤b)所得再选尾矿进行磁粗选,磁场强度为3000gs,得到磁粗精矿和磁尾矿ⅰ,磁粗精矿进行磁精选(磁场强度为2000gs)得到磁精矿和磁尾矿ⅱ,磁尾矿ⅰ和磁尾矿ⅱ作为最终尾矿废弃或外售给水泥厂做辅料。磁选结果如表5所示。
[0043]
表5磁选试验结果
[0044][0045][0046]
试验结果表明,采用本发明的技术方案最终得到了铁品位为53.32%的磁铁矿,并且经过多次试验后,铁品位均能够保持在高于51%的水平,达到了50%的磁铁矿铁品位标准,外售后给企业带来稳定的经济效益。
[0047]
对比例1
[0048]
考虑到没有针对本发明所述的渣选尾矿回收铜的流程的类似对比,因此采用将浮选尾矿直接全部磨细后进行磁选的工艺进行对比试验(见图2)。即磨矿细度为-0.045mm占90%以上,磁场强度与实施例1相同。试验得到的磁选指标如表6所示。
[0049]
表6对比例1磁选试验结果
[0050]
产品名称物料占比/%铁品位/%铁分布/%磁铁矿33.2249.8738.92磁精尾矿3.3643.213.41磁粗尾矿63.4238.7157.67合计100.0042.57100.00
[0051]
对比例1试验结果表明,采用直接全部磨细 磁选的工艺流程,在电耗和钢耗明显增大的同时,磨矿细度相对降低,得到的磁铁矿的铁品位为49.87%,低于50%的磁铁矿铁品位标准,也低于实施例2中磁铁矿铁品位3.45个百分点,使得磁铁矿产品价值下降,经济效益降低。
[0052]
因申请人是铜冶炼企业,得到的铁精矿是外售的,而外售过程中,根据磁铁矿铁品位不同,售卖价格也区别很大,其中,磁铁矿的铁品位能够达到50%以上,与50%以下的售卖价格是不一样的,即使品位在49%,价格也相差较大,因此看似铁品位提高幅度不大,然而对于企业经济效益来讲却具有非常大的现实意义。
[0053]
实施例3:不同冶炼渣浮选尾矿的处理
[0054]
内蒙古某冶炼渣选车间,冶炼渣性质为电炉渣和转炉渣混合,经现场流程选别后,得到的尾矿含铜为0.205%,将现场尾矿进行粒度组成分析,具体指标如表7所示。
[0055]
表7实施例3浮选尾矿粒度组成结果
[0056][0057]
从表5可以看出,随着粒级逐渐变粗,相应粒级含铜也逐渐升高。其中, 0.045mm粒级总含铜高达0.317%,较平均品位高出0.112个百分点;而-0.045mm粒级总含铜为0.172%,较平均品位降低0.033个百分点。可见,采用0.045mm粒级标准筛具有普适性,经过多次不同浮选尾矿的处理后,也证实这一点,0.045mm粒级标准筛是最后选择。上述筛分结果如表8所示。
[0058]
表8实施例3现场尾矿0.045mm粒级筛分试验结果
[0059]
产品名称物料占比/%铜品位/%铜分布/%粗料23.70.32637.75细料76.30.16762.25合计100.00.205100.00
[0060]
再将该电炉渣和转炉渣的混合渣浮选尾矿的粗料采用与实施例2相同的方法进行处理,试验结果如表9所示。
[0061]
表9实施例3再选结果
[0062]
产品名称物料占比/%铜品位/%铜分布/%再选铜精矿1.788.2345.18再选尾矿98.220.18154.82合计100.000.324100.00
[0063]
将再选铜尾矿和浮选尾矿分级后的细料作为再选总铜尾矿,与混合渣浮选尾矿进行比较,具体结果参见表10。
[0064]
表10实施例3再选后不同尾矿分析结果
[0065][0066]
可见再磨再选后,最终可使得总尾含铜由之前的0.205%降为0.170%,共计降低0.035个百分点,降低效果显著。
[0067]
将再选总铜尾矿进入两段磁选作业,磁粗选的磁场强度为2500gs,磁精选的磁场强度为1500gs,磁选结果如表11所示。
[0068]
表11实施例3磁选试验结果
[0069]
产品名称物料占比/%铁品位/%铁分布/%磁精矿28.4551.8335.50磁尾矿ⅰ4.0041.904.03磁尾矿ⅱ67.5537.1860.47合计100.0041.54100.00
[0070]
试验结果表明,采用本发明的流程最终得到了铁品位为51.83%的磁铁矿,达到了50%的磁铁矿铁品位标准。
[0071]
对比例2
[0072]
将实施例3中的混合渣浮选尾矿采用全部磨细后进行磁选的工艺进行对比试验。即磨矿细度为-0.045mm占90%以上,磁场强度与实施例3相同。试验得到的磁选指标如表12所示。
[0073]
表12对比例2磁选试验结果
[0074]
产品名称物料占比/%铁品位/%铁分布/%磁精矿30.8748.9236.37磁精尾矿4.5642.544.67磁粗尾矿64.5737.9258.96合计100.0041.53100.00
[0075]
对比例2试验结果表明,采用直接全部磨细 磁选的工艺流程,在电耗和钢耗明显
增大的同时,磨矿细度相对降低,得到的磁铁矿的铁品位为48.92%,低于50%的磁铁矿铁品位标准,也低于实施例3中磁铁矿铁品位2.91个百分点,使得磁铁矿产品价值下降,经济效益降低。也证明了采用本技术的技术方案确实可以回收浮选尾矿中的铜和铁,降低金属资源浪费且为企业带来了经济效益。
再多了解一些
本文用于创业者技术爱好者查询,仅供学习研究,如用于商业用途,请联系技术所有人。