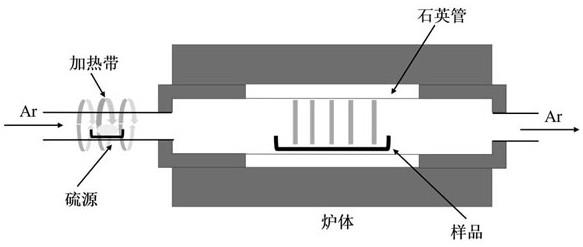
1.本发明属于金属材料领域,具体涉及一种镍基硫化材料的制备方法。
背景技术:
2.电解水制氢技术呈现出绿色环保、工艺简便、无副反应、无副产物、产物高纯等特性,被认为是工业化制氢的理想方法之一。但是,现有阴极电极材料成本昂贵、催化活性较低、能耗较高,严重地降低了电解水制氢的效率,因此,寻找低成本、高活性、低能耗电极材料成为亟待解决的问题。过渡金属硫化物及其相关催化剂含量丰富、价格便宜且催化效率较高,在现有材料的基础上进一步优化材料结构、改善催化性能,增大比表面积、改善机械性能及延长材料使用寿命从而替代现有贵金属等其他催化剂。现有用作电极的镍基硫化材料制备工艺通常采用电镀、电沉积、水热等化学法或直接将硫化物粉体粘接于基底等物理法,该类方法存在成本高、电解水反应时析氢过电位过高、气体难以排除等缺陷。
技术实现要素:
3.针对上述已有技术存在的不足,本发明提供一种镍基硫化材料的制备方法。
4.本发明是通过以下技术方案实现的。
5.一种镍基硫化材料的制备方法,其特征在于,所述制备方法包括:基底材料预处理、基底材料原位硫化、后处理。
6.进一步地,所述基底材料为ni基底材料,所述ni基底材料为泡沫ni、ni纤维毡或ni-mo纤维毡。
7.进一步地,所述基底材料预处理工艺包括:采用酸溶液、去离子水及无水乙醇对基底材料依次洗涤3~10次,然后于50℃~80℃烘干。
8.进一步地,所述酸溶液为盐酸、硝酸、硫酸中的一种或几种混合酸溶液,所述酸溶液中酸的质量分数为10~100%。
9.进一步地,所述基底材料原位硫化工艺包括如下步骤:(1)将硫源、基底材料分别置于管式炉上游和恒温区,管式炉内抽真空至0.1~5.0 kpa;(2)对管式炉恒温区的基底材料以2~30℃/min的升温速率升至200~1200℃进行加热;(3)通过管式炉上游均匀缠绕的加热带,以2~30℃/min的升温速率升至100℃~1000℃对硫源进行加热;(4)通入ar气,控制流速为5~800 ml/min,保温10~600 min;(5)保温完成后,待加热带温度降至50~600℃时,停止通入ar气。
10.进一步地,所述硫源为硫粉或硫脲。
11.进一步地,所述硫源用量与基底材料暴露在管式炉恒温区域中的表面积的比例为0.1~10g/cm2。
12.进一步地,所述步骤(1)中,盛放基底材料的瓷舟位于距离盛放硫源的瓷舟1~100cm的下游处,先将管式炉内真空度降至0.1~10.0 kpa,再抽真空至0.1~5.0 kpa。
13.进一步地,所述后处理工艺包括:保温完成后,管式炉自然冷却至室温,待管式炉内真空度恢复到大气压时,取出制备的镍基硫化材料。
14.进一步地,制备的镍基硫化材料在500~800 ma/cm2电流密度下,析氢过电位为595~776 mv。
15.本发明的有益技术效果:与现有技术相比,本发明采用原位硫化技术,即在镍基体材料表层原位生长出硫化物,以达到强化的目的,该制备工艺简便、易操作、成本低,且无需胶黏剂等其他辅助物质。制备的材料颗粒尺寸均匀、细小,热力学性能稳定,界面无污染、结合强度高,可直接用作电极材料。材料具有凹凸不平的表面,以提高材料比表面积,为电解水反应提供更多的催化活性位点,从而降低析氢过电位。此外,颗粒间较大的空隙也易于气体逃逸,解决气体难以排出的难题。
附图说明
16.图1为本发明方法中的硫化工艺过程示意图。
17.图2为本发明对比例未硫化的电极材料扫描电镜图片。
18.图3为本发明对比例硫化后的电极材料扫描电镜图片。
19.图4为本发明实施例3未经硫化的电极材料扫描电镜图片。
20.图5 为本发明实施例3硫化后的电极材料扫描电镜图片。
21.图6 为本发明实施例3 硫化前后电极的极化曲线,测试方法为线性扫描伏安法,测试条件:三电极体系,所制备电极为工作电极,ag/agcl为参比电极,铂丝为辅助电极,电解液采用浓度为1 mol/l 的koh溶液,扫描速率为10 mv/s,扫描范围为0~-1.2v(相对标准氢电极)。
22.图7 为本发明对比例及实施例1-3硫化后电极的极化曲线对比图。
具体实施方式
23.下面结合附图和具体实施方式对本发明进行详细说明。
24.一种镍基硫化材料的制备方法,包括:基底材料预处理、基底材料原位硫化、后处理。
25.基底材料为ni基底材料,具体可以为泡沫ni、ni纤维毡或ni-mo纤维毡。
26.具体步骤包括:1.基底材料预处理工艺包括:采用酸溶液、去离子水及无水乙醇对基底材料依次洗涤3~10次,然后于50℃~80℃烘干;其中,酸溶液为盐酸、硝酸、硫酸中的一种或几种混合酸溶液,具体地,酸溶液由浓盐酸、浓硝酸、浓硫酸中的一种或几种与去离子水混合而成,其中,酸的质量分数为10~100%。
27.2.基底材料原位硫化工艺包括如下步骤:(1)将1~100 g硫源、基底材料分别置于管式炉上游和恒温区,盛放基底材料的瓷舟位于距离盛放硫源的瓷舟1~100cm的下游处,其中,硫源为硫粉或硫脲,硫源用量与基底材料暴露在管式炉恒温区域中的表面积的比例为0.1~10g/cm2;
(2)将加热带均匀缠绕在管式炉上游(即管式炉石英管前端进口处);(3)将管式炉两端连接好、密封;(4)启动真空泵,缓慢打开管式炉尾端阀,至真空度降至0.1~10.0 kpa时,再缓慢打开前端进气阀,至真空度稳定至0.1~5.0 kpa;(5)打开管式炉控温阀,对管式炉恒温区的基底材料以2~30℃/min的升温速率升至200~1200℃进行加热;(6)打开加热带控温阀,以2~30℃/min的升温速率升至100℃~1000℃对硫源进行加热;(7)通入ar气,控制流速为5~800 ml/min,保温10~600 min;(8)保温完成后,关闭加热带控温阀,待加热带温度降至50~600℃时,关闭ar气阀,停止通入ar气,待流量计示数降为零时,关闭石英管前端进气阀;关闭管式炉控温阀以及管式炉尾端阀及真空泵。
28.3.后处理工艺包括:保温完成后,管式炉炉体自然冷却至室温后,打开管式炉尾端阀门,待管式炉内真空度恢复到大气压时,打开管式炉,取出制备的镍基硫化物电极材料。
29.制备的硫化物电极材料选用瑞士万通电化学工作站(公知设备)测试性能,制备的镍基硫化物电极材料在500~800 ma/cm2电流密度下,析氢过电位为595~776 mv。
30.实施例1 制备泡沫ni基硫化物电极材料(1)、用质量分数30%的硝酸溶液、去离子水及无水乙醇对泡沫ni依次洗涤5次,后于60℃真空烘箱中至干燥;(2)、用分析天平称量5 g硫脲(用量与表面积的比例0.5 g/cm2)于瓷舟中,并置于管式炉上游处;(3)、盛有泡沫ni的瓷舟放在恒温区,距离上游瓷舟20 cm左右的下游处;(4)、将加热带均匀的缠绕在管式炉石英管前端进口处;(5)、将管式炉两端连接好、密封;(6)、启动真空泵,缓慢打开管式炉尾端阀,至真空度降至3.0 kpa左右时,再缓慢打开前端进气阀,至真空度稳定在2.0 kpa左右;(7)、打开管式炉控温阀,以10℃/min的升温速率升至600℃对基底材料进行加热;(8)、打开管式炉前端加热带控温阀,以10℃/min升温至150℃对硫脲加热;(9)、通入ar气,控制流量计流速为20 ml/min,保温60 min;(10)、保温完成后,关闭加热带控温阀;(11)、加热带温度降至120℃时,关闭ar气阀,待流量计示数降为零时,关闭石英管前端进气阀;(12)、关闭管式炉控温阀;(13)、关闭管式炉尾端阀及真空泵;(14)、自然冷却至室温后,打开管式炉尾端阀,待真空度恢复到大气压时,打开管式炉,取出制备得到的ni硫化物电极材料样品。
31.实施例2 制备ni纤维毡基硫化物电极材料(1)、用质量分数30%的硝酸溶液、去离子水及无水乙醇对ni纤维毡依次洗涤5次,后于60℃真空烘箱中至干燥;
(2)、用分析天平称量5 g硫脲(用量与表面积的比例0.5 g/cm2)于瓷舟中,并置于管式炉上游处;(3)、盛有ni纤维毡的瓷舟放在恒温区,距离上游瓷舟50 cm左右的下游处;(4)、将加热带均匀的缠绕在管式炉石英管前端进口处;(5)、将管式炉两端连接好、密封;(6)、启动真空泵,缓慢打开管式炉尾端阀,至真空度降至5.0 kpa左右时,再缓慢打开前端阀,至真空度稳定在3.0kpa左右;(7)、打开管式炉控温阀,以25℃/min的升温速率升至300℃对基底材料进行加热;(8)、打开管式炉前端加热带控温阀,以5℃/min升温至200℃对硫脲加热;(9)、通入ar气,控制流量计流速为20 ml/min,保温60 min;(10)、保温完成后,关闭加热带控温阀;(11)、加热带温度降至180℃时,关闭ar气阀,待流量计示数降为零时,关闭石英管前端进气阀;(12)、关闭管式炉控温阀;(13)、关闭管式炉尾端阀及真空泵;(14)、自然冷却至室温后,打开管式炉尾端阀,待真空度恢复到大气压时,打开管式炉,取出制备得到的ni硫化物样品。
32.实施例3 制备ni-mo基硫化物电极材料(1)、用质量分数30%的硝酸溶液、去离子水及无水乙醇对ni-mo纤维毡依次洗涤4次,后于55℃真空烘箱中至干燥;(2)、用分析天平称量5 g硫脲(用量与表面积的比例0.5 g/cm2)于瓷舟中,并置于管式炉上游处;(3)、盛有ni-mo纤维毡的瓷舟放在恒温区,距离上游瓷舟90 cm左右的下游处;(4)、将加热带均匀的缠绕在管式炉石英管前端处;(5)、将管式炉两端连接好、密封;(6)、启动真空泵,缓慢打开管式炉尾端阀,至真空度降至3.0 kpa左右时,再缓慢打开前端阀,至真空度稳定在2.0 kpa左右;(7)、打开管式炉控温阀,以5℃/min的升温速率升至400℃对基底材料进行加热;(8)、打开管式炉前端加热带控温阀,以30℃/min升温至750℃对硫脲加热;(9)、通入ar气,控制流量计流速为100 ml/min,保温500 min;(10)、保温完成后,关闭加热带控温阀;(11)、加热带温度降至400℃时,关闭ar气阀,待流量计示数降为零时,关闭石英管前端进气阀;(12)、关闭管式炉控温阀;(13)、关闭管式炉尾端阀及真空泵;(14)、自然冷却至室温后,打开管式炉尾端阀,待真空度恢复到大气压时,打开管式炉,取出制备得到的ni-mo硫化物样品。
33.实施例4 制备ni-mo基硫化物电极材料(1)、用质量分数50%的盐酸溶液、去离子水及无水乙醇对ni-mo纤维毡依次洗涤10
次,后于80℃真空烘箱中至干燥;(2)、用分析天平称量50 g硫粉(用量与表面积的比例5 g/cm2)于瓷舟中,并置于管式炉上游处;(3)、盛有ni-mo纤维毡的瓷舟放在恒温区,距离上游瓷舟70 cm左右的下游处;(4)、将加热带均匀的缠绕在管式炉石英管前端处;(5)、将管式炉两端连接好、密封;(6)、启动真空泵,缓慢打开管式炉尾端阀,至真空度降至8.0 kpa左右时,再缓慢打开前端阀,至真空度稳定在4.0 kpa左右;(7)、打开管式炉控温阀,以30℃/min的升温速率升至800℃对基底材料进行加热;(8)、打开管式炉前端加热带控温阀,以15℃/min升温至500℃对硫粉加热;(9)、通入ar气,控制流量计流速为500 ml/min,保温300 min;(10)、保温完成后,关闭加热带控温阀;(11)、加热带温度降至500℃时,关闭ar气阀,待流量计示数降为零时,关闭石英管前端进气阀;(12)、关闭管式炉控温阀;(13)、关闭管式炉尾端阀及真空泵;(14)、自然冷却至室温后,打开管式炉尾端阀,待真空度恢复到大气压时,打开管式炉,取出制备得到的ni-mo硫化物样品。
34.实施例5 制备ni-mo基硫化物电极材料(1)、用质量分数100%硫酸溶液、去离子水及无水乙醇对ni-mo纤维毡依次洗涤7次,后于60℃真空烘箱中至干燥;(2)、用分析天平称量100 g硫脲(用量与表面积的比例10 g/cm2)于瓷舟中,并置于管式炉上游处;(3)、盛有ni-mo纤维毡的瓷舟放在恒温区,距离上游瓷舟50 cm左右的下游处;(4)、将加热带均匀的缠绕在管式炉石英管前端处;(5)、将管式炉两端连接好、密封;(6)、启动真空泵,缓慢打开管式炉尾端阀,至真空度降至9.0 kpa左右时,再缓慢打开前端阀,至真空度稳定在1.0 kpa左右;(7)、打开管式炉控温阀,以20℃/min的升温速率升至1000℃对基底材料进行加热;(8)、打开管式炉前端加热套控温阀,以25℃/min升温至1000℃对硫脲加热;(9)、通入ar气,控制流量计流速为800 ml/min,保温20 min;(10)、保温完成后,关闭加热带控温阀;(11)、加热带温度降至300℃时,关闭ar气阀,待流量计示数降为零时,关闭石英管前端进气阀;(12)、关闭管式炉控温阀;(13)、关闭管式炉尾端阀及真空泵;(14)、自然冷却至室温后,打开管式炉尾端阀,待真空度恢复到大气压时,打开管式炉,取出制备得到的ni-mo硫化物样品。
35.实施例6 制备ni-mo基硫化物电极材料(1)、用质量分数30%的混酸溶液(盐酸10%,硝酸10%,硫酸10%)、去离子水及无水乙醇对ni-mo纤维毡依次洗涤5次,后于60℃真空烘箱中至干燥;(2)、用分析天平称量5 g硫脲(用量与表面积的比例0.5 g/cm2)于瓷舟中,并置于管式炉上游处;(3)、盛有ni-mo纤维毡的瓷舟放在恒温区,距离上游瓷舟100 cm左右的下游处;(4)、将加热带均匀的缠绕在管式炉石英管前端进口处;(5)、将管式炉两端连接好、密封;(6)、启动真空泵,缓慢打开管式炉尾端阀,至真空度降至10.0 kpa左右时,再缓慢打开前端进气阀,至真空度稳定在5.0 kpa左右;(7)、打开管式炉控温阀,以10℃/min的升温速率升至600℃对基底材料进行加热;(8)、打开管式炉前端加热带控温阀,以10℃/min升温至150℃对硫脲加热;(9)、通入ar气,控制流量计流速为800 ml/min,保温600 min;(10)、保温完成后,关闭加热带控温阀;(11)、加热带温度降至120℃时,关闭ar气阀,待流量计示数降为零时,关闭石英管前端进气阀;(12)、关闭管式炉控温阀;(13)、关闭管式炉尾端阀及真空泵;(14)、自然冷却至室温后,打开管式炉尾端阀,待真空度恢复到大气压时,打开管式炉,取出制备得到的ni-mo硫化物电极材料样品。
36.对比例制备ni网硫化物电极材料(1)、用30%的硝酸溶液、去离子水及无水乙醇对ni网依次洗涤5次,后于60℃真空烘箱中至干燥;(2)、用分析天平称量5 g硫脲(用量与表面积的比例0.5 g/cm2)于瓷舟中,并置于管式炉上游处;(3)、盛有ni网的瓷舟放在距离上游瓷舟20 cm左右的下游处;(4)、将加热带均匀的缠绕在管式炉石英管前端处;(5)、将管式炉两端连接好、密封;(6)、启动真空泵,缓慢打开管式炉尾端阀,至真空度降至3.0 kpa左右时,再缓慢打开前端阀,至真空度稳定在2.0 kpa左右;(7)、打开管式炉控温阀,以10℃/min的升温速率升至600℃;(8)、打开管式炉前端加热套控温阀,以10℃/min升温至150℃;(9)、通入ar气,控制流量计流速为20 ml/min,保温60 min;(10)、保温完成后,关闭加热带控温阀;(11)、加热带温度降至120℃时,关闭ar气阀,待流量计示数降为零时,关闭石英管前端进气阀;(12)、关闭管式炉控温阀;(13)、关闭管式炉尾端阀及真空泵;(14)、自然冷却至室温后,打开管式炉尾端阀,待真空度恢复到大气压时,打开管
式炉,取出制备得到的ni硫化物样品。
37.如图7所示为本发明对比例及实施例1-3电极的极化曲线,测试方法为线性扫描伏安法,测试条件:三电极体系,所制备电极为工作电极,ag/agcl为参比电极,铂丝为辅助电极,电解液采用浓度为1 mol/l 的koh溶液,扫描速率为10 mv/s,扫描范围为0~-1.2v(相对标准氢电极)。在500ma/cm2电流密度下,对比例、实施例1、实施例2、实施例3四类电极材料在相同测试环境中的析氢过电位分别为826、775、712、596mv。与对比例相比,实施例1-3分别降低了51、114、230mv,这表明硫化后的泡沫ni、ni纤维毡及ni-mo纤维毡电极材料的析氢性能均得到了不同程度的提高,提高程度为泡沫ni<ni纤维毡<ni-mo纤维毡。
38.以上所述的仅是本发明的较佳实施例,并不局限发明。应当指出对于本领域的普通技术人员来说,在本发明所提供的技术启示下,还可以做出其它等同改进,均可以实现本发明的目的,都应视为本发明的保护范围。
再多了解一些
本文用于创业者技术爱好者查询,仅供学习研究,如用于商业用途,请联系技术所有人。