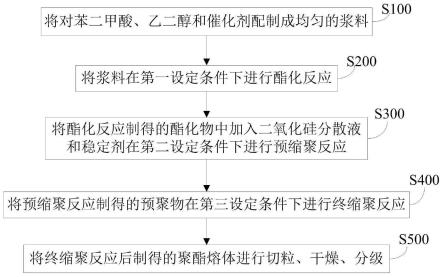
一种mlcc离型膜专用聚酯母粒及其制备方法
技术领域
1.本发明涉及离型膜技术领域,具体涉及一种mlcc离型膜专用聚酯母粒及其制备方法。
背景技术:
2.mlcc(multi-layer ceramic capacitors,片式多层陶瓷电容器的简称)离型膜,也称为印刷电路基板成型膜、剥离膜,是一种在mlcc的制备过程中使用的具有离型性的膜材料,作为流延涂布时承载陶瓷层的基材。mlcc离型膜是将有机硅离型剂涂布于pet聚酯薄膜的表层上。近几年由于智能手机等便携设备需求的扩大,以及车载的电子化,mlcc业向着小型化及高容化的发展,陶瓷介质的层数越来越多,相应的厚度在减小,对离型膜的要求也越来越高。中国正成为全球最大的电子终端产品加工制造基地,经由中国制造与市场集散的mlcc已占到全球产销量的一半,但是目前国内mlcc离型膜主要依赖进口,所以急需开发mlcc离型膜并产业化。
3.目前,多采用pet表面涂层法获得mlcc离型膜。例如:专利cn113978086a,提供了一种易剥离mlcc离型膜及其制备方法,采用在线pet涂布离型剂的技术并且在生产过程中采用等离子对薄膜表面处理使硅油与薄膜结合力更好,对陶瓷的剥离性更好,膜至少为二层:表层包含硅氧烷改性后的二硫化钼、蒙脱土或石墨烯片状无机材料和pet,基层为100%pet,发明还提出了该离型薄膜生产工艺,包括以下步骤:(1)制备至少二层结构基膜;(2)基膜加热纵向拉伸;(3)等离子体对基膜表面处理;(4)基膜的被处理表面涂覆硅油乳液;(5)将未固化乳液涂层的厚膜经加热、横向拉伸完成涂层固化、热定型和冷却。例如:专利cn114103360a,提供了一种应用于mlcc的离型基膜及其制备方法,包括离型膜和两个功能层,两个功能层分别位于离型膜的两侧,离型膜包括以下重量份的原料:pet颗粒85~96份、非水溶性碳酸盐2~5份、含氢增粘剂0.5~1份和纳米石墨0.08~0.8份;功能层包括以下重量份的原料:高密度聚乙烯32~44份、消光剂5~12份、柔性树脂39~55份和抗氧化剂0.3~0.9份,通过在离型膜的两表面粘接有功能层,功能层中采用柔性树脂和高密度聚乙烯,增加了离型基膜的柔性以及消光性。但是涂布法获得的mlcc离型膜稳定性相对较差,粉体分布均匀性一般,易出现大颗粒,从而导致表面粗糙度相对较高。
4.另外,也有采用mlcc离型膜专用母粒获得mlcc离型膜的,由于mlcc离型膜要求薄膜的表面光滑性好、粗糙度低,所以mlcc离型膜专用聚酯母粒,必须选用粒径较小、分布较窄的粉体,但是小粒径粉体易团聚、分散液稳定性差,如何获得粒径均匀、分布较窄且稳定性好的分散液是一大技术难题。
5.例如:专利cn110239185b,公开了一种mlcc离型膜基膜及其功能母料以及制备方法,在mlcc离型膜基膜的表面层的功能母料中,包括90%~99.5%的pet、0.1%~0.4%的纳米石墨以及0.1%~9.9%的无机填料,所述a层和c层的表面粗糙度ra为17.2μm~17.4μm,所述无机填料的粒径范围为0.5μm~10μm。该专利提供的mlcc离型膜的表面粗糙度只能达到微米级,且无机填料的粒径分布较宽,不能满足高端mlcc离型膜的需求。
6.因此,发明人提供了一种mlcc离型膜专用聚酯母粒及其制备方法。
技术实现要素:
7.(1)要解决的技术问题
8.本发明实施例提供了一种mlcc离型膜专用聚酯母粒及其制备方法,解决了mlcc离型膜专用母粒粉体分布均匀性差、存在大颗粒、分散液稳定性差和膜的表面粗糙度高的技术问题。
9.(2)技术方案
10.本发明提供了一种mlcc离型膜专用聚酯母粒,由聚对苯二甲酸乙二醇酯、催化剂、稳定剂、二氧化硅和分散剂组成;其中,所述聚对苯二甲酸乙二醇酯的质量占比为94.1~98.7%,催化剂的质量占比为0.08~0.4%,稳定剂的质量占比为0.002~0.010%,二氧化硅的质量占比为0.2~0.5%,分散剂的质量占比为1~5%。
11.进一步地,所述聚对苯二甲酸乙二醇酯由对苯二甲酸和乙二醇在一定工艺条件和催化剂的催化作用下合成制得,所述对苯二甲酸与所述乙二醇的摩尔比为1.1~1.6。
12.本发明还提供了一种用于mlcc离型膜专用聚酯母粒的制备方法,包括以下步骤:
13.将对苯二甲酸、乙二醇和催化剂配制成均匀的浆料;
14.将所述浆料在第一设定条件下进行酯化反应;
15.将酯化反应制得的酯化物中加入二氧化硅分散液和稳定剂在第二设定条件下进行预缩聚反应;
16.将预缩聚反应制得的预聚物在第三设定条件下进行终缩聚反应;
17.将终缩聚反应后制得的聚酯熔体进行切粒、干燥、分级。
18.进一步地,所述催化剂采用钛系催化剂,其中钛的质量占比为2~10ppm。
19.进一步地,所述二氧化硅分散液的配制过程包括如下步骤:
20.在带有搅拌器的二氧化硅配制槽中,先加入乙二醇,再将二氧化硅加入乙二醇中,加入分散剂,搅拌设定时间,制备出二氧化硅的预分散液;
21.将所述预分散液送至球磨机进行球磨分散,形成所述二氧化硅分散液。
22.进一步地,所述设定时间为1~2h。
23.进一步地,所述二氧化硅配制槽中搅拌器的转速为2000~6000r/min。
24.进一步地,所述球磨机的转速为200~680r/min。
25.进一步地,球磨分散的时间为4~8h。
26.进一步地,所述二氧化硅的质量占比为2000~5000ppm。
27.进一步地,所述稳定剂为磷酸、磷酸三甲酯、磷酸三乙酯、磷酸三苯酯中的至少一种,其中磷的质量占比为3~15ppm。
28.(3)有益效果
29.综上,本发明通过采用对苯二甲酸、乙二醇聚合法,制备mlcc离型膜专用聚酯母粒,然后再将母粒用于薄膜生产,不需要涂布,操作更加简便,可以实现量化生产,膜的洁净度更高,稳定性更高。该mlcc离型膜专用聚酯母粒双向拉伸成膜后,薄膜表面粉体分布均匀、无大颗粒,聚酯薄膜表面粗糙度ra<15nm,rz<200nm,在保证低粗糙度的前提下,制备的母粒还具有良好的开口性,满足薄膜的生产和加工需要。
附图说明
30.为了更清楚地说明本发明实施例的技术方案,下面将对本发明实施例中所需要使用的附图作简单地介绍,显而易见地,下面所描述的附图仅仅是本发明的一些实施例,对于本领域普通技术人员来讲,在不付出创造性劳动的前提下,还可以根据这些附图获得其他的附图。
31.图1是本发明实施例提供的一种mlcc离型膜专用聚酯母粒的制备方法的流程示意图;
32.图2是本发明实施例提供的一种mlcc离型膜专用聚酯母粒的粒径分布示意图;
33.图3(a)是采用外购韩国的mlcc离型膜专用聚酯母粒制得的薄膜在显微镜下的表面形态示意图;
34.图3(b)为采用本发明的mlcc离型膜专用聚酯母粒制得的薄膜在显微镜下的表面形态示意图;
35.图4(a)是本发明母粒所制得的薄膜的表面粗糙度ra的测试图;
36.图4(b)是本发明母粒所制得的薄膜的表面粗糙度rz的测试图。
具体实施方式
37.下面结合附图和实施例对本发明的实施方式作进一步详细描述。以下实施例的详细描述和附图用于示例性地说明本发明的原理,但不能用来限制本发明的范围,即本发明不限于所描述的实施例,在不脱离本发明的精神的前提下覆盖了零件、部件和连接方式的任何修改、替换和改进。
38.需要说明的是,在不冲突的情况下,本技术中的实施例及实施例中的特征可以相互组合。下面将参照附图并结合实施例来详细说明本技术。
39.在本发明的描述中,需要理解的是,术语“上”、“下”、“前”、“后”等指示的方位或位置关系为基于附图所示的方位或位置关系,或者是本发明产品使用时惯常摆放的方位或位置关系,或者是本领域技术人员惯常理解的方位或位置关系,仅是为了便于描述本发明和简化描述,而不是指示或暗示所指的设备或元件必须具有特定的方位、以特定的方位构造和操作,因此不能理解为对本发明的限制。
40.在本发明的描述中,还需要说明的是,除非另有明确的规定和限定,术语“设置”、“安装”应做广义理解,例如,可以是固定连接,也可以是可拆卸连接,或一体地连接;可以是直接相连,也可以通过中间媒介间接相连。对于本领域的普通技术人员而言,可以具体情况理解上述术语在本发明中的具体含义。
41.本发明实施例提供了一种mlcc离型膜专用聚酯母粒,由聚对苯二甲酸乙二醇酯、催化剂、稳定剂、二氧化硅和分散剂组成;其中,所述聚对苯二甲酸乙二醇酯的质量占比为94.1~98.7%,催化剂的质量占比为0.08~0.4%,稳定剂的质量占比为0.002~0.010%,二氧化硅的质量占比为0.2~0.5%,分散剂的质量占比为1~5%。
42.在上述实施方式中,由于受到生产条件、催化剂、添加粉体粒径大小、分散均匀性以及聚酯加工流动性等因素的影响,聚酯母粒的l值一般都在84~86。mlcc离型膜专用聚酯母粒,l值可以达到89以上,切片更亮;用其制得的mlcc离型膜的雾度可以控制在1.0%以内,透光率可以达到90.0%以上。
43.作为一种可选的实施方式,聚对苯二甲酸乙二醇酯由对苯二甲酸和乙二醇在一定工艺条件和催化剂的催化作用下合成制得,对苯二甲酸与乙二醇的摩尔比为1.1~1.6。
44.其中,本文中所提到的质量占比均表示其添加量在理论聚酯熔体产量中的质量占比,下文中不再赘述。
45.图1是本发明实施例提供的一种用于上述的mlcc离型膜专用聚酯母粒的制备方法的流程示意图,该方法可以包括以下步骤:
46.s100、将对苯二甲酸、乙二醇和催化剂配制成均匀的浆料;
47.s200、将浆料在第一设定条件下进行酯化反应;
48.s300、将酯化反应制得的酯化物中加入二氧化硅分散液和稳定剂在第二设定条件下进行预缩聚反应;
49.s400、将预缩聚反应制得的预聚物在第三设定条件下进行终缩聚反应;
50.s500、将终缩聚反应后制得的聚酯熔体进行切粒、干燥、分级。
51.在上述实施方式中,将亚微米级二氧化硅粉体与乙二醇先配制成预分散液,然后采用球磨机球磨球磨分散,获得粒径更小、更集中的二氧化硅分散液。将对苯二甲酸(pta,terephthalic acid)、乙二醇(eg,ethylene glycol)和催化剂配制成均匀的浆料后,通过螺杆泵送至酯化釜,于230~260℃、常压条件下进行酯化反应,180~260min后,然后采用氮气压送至预缩聚釜,从预缩聚釜加入一定量的二氧化硅分散液和稳定剂,于220~250℃、20~80kpa条件下进行预缩聚反应,20~60min后,然后采用氮气经过过滤器之后压送至终缩聚釜,于260~290℃、10~50pa条件下进行终缩聚反应,160~260min后,聚酯熔体利用立式水下切粒机系统进行切粒、干燥、分级,最后包装入库。
52.其中,eg:pta的摩尔比为1.1~1.6:1。若摩尔比太低,则浆料中eg含量不足,会导致酯化反应不充分,酯化率偏低,酯化物料中pta反应不完全使得端羧基含量偏高,导致缩聚反应不充分甚至缩聚终止,切片中的端羧基含量偏高,粘度偏低;若摩尔比太高,则酯化率太高,体系中的端羧基含量偏低,会导致缩聚反应缓慢,反应周期变长,在缩聚反应的同时发生热降解和热氧降解,使得切片的粘度偏低。所以,我们需要选择合适的摩尔比,不能太高,也不能太低,在确保酯化率的前提下尽可能地降低摩尔比。
53.作为一种可选的实施方式,催化剂采用钛系催化剂,其中钛的质量占比为2~10ppm。
54.具体地,钛系催化剂为钛酸正丁酯、钛酸异丙酯、钛的醇盐或者络合物中的一种或者多种,其中钛系催化剂的质量占比为0.08~0.4%,其中钛的质量占比为2~10ppm。采用直接酯化法合成pet聚酯时,缩聚反应需要使用催化剂,目前广泛使用的是锑系催化剂,但是由于锑是一种重金属,对环境影响较大,因此近年来全球对锑的使用已经开始逐步控制,有些国家已经限量甚至禁止使用;与锑系催化剂相比,使用钛系催化剂时切片的l值更高;锑系催化剂的活性也远远不如钛系催化剂,一般聚酯生产时,催化剂锑的质量占比需要达到100~250ppm,比钛的添加量要高出几十倍。钛系催化剂添加量过高时,多余的钛系催化剂会加快热降解和热氧降解等副反应,形成羟基化和醌型结构等,从而导致切片的b值升高,切片偏黄,所以我们需要在保证催化效果的前提下,尽可能降低钛的添加量。
55.采用钛系催化剂,活性高,添加量小,缩聚反应周期短,生产效率高,产品性能优异,而且无重金属、更加环保。
56.作为一种可选的实施方式,步骤s300中,二氧化硅分散液的配制过程包括如下步骤:
57.s301、在带有搅拌器的二氧化硅配制槽中,先加入乙二醇,再将二氧化硅加入乙二醇中,加入分散剂,搅拌设定时间,制备出二氧化硅的预分散液;
58.s302、将预分散液送至球磨机进行球磨分散,形成二氧化硅分散液。
59.在上述实施方式中,步骤s301中,在带有搅拌器的二氧化硅配制槽中,先加入一定质量的乙二醇,再将二氧化硅加入乙二醇中,加入分散剂,搅拌1~2h,至粉体充分溶解在乙二醇中,预分散液中二氧化硅的质量百分数为1~6%,二氧化硅配制槽搅拌器的转速为2000~6000r/min。若搅拌时间过短或者搅拌器转速过低则二氧化硅溶解不充分,会直接影响其分散效果;若搅拌时间过长则配制效率过低,而搅拌器转速过高,则对设备要求将大幅度提高,设备成本也会很高,所以需要我们选择合适的搅拌时间及搅拌器转速。
60.步骤s302中,将二氧化硅与乙二醇的预分散液通过泵送至球磨机进行球磨分散,球磨机的转速和球磨分散时间,直接影响二氧化硅粉体的球磨效果,若转速过低则需要更长的球磨分散时间,球磨效果差、效率低;若转速过高,则容易将粒子磨碎,分散液反而更不稳定,更易团聚,且开口效果大大降低,粒子在薄膜表面的粗糙度也会变大,膜的性能降低,所以在保证球磨分散效果的前提下,我们需要选择合适的转速和时间。球磨机的转速为200~680r/min,球磨分散4~8h后,即可获得分散均匀、粒径分布狭窄的分散液,d(50)可以达到0.1~0.2um,d(98)可以达到0.2~0.3um。所以,我们制得的母粒中粉体分布均匀,粒子大小相近,无大颗粒,拉伸成膜后,膜的表面粗糙度低。
61.作为一种可选的实施方式,二氧化硅的质量占比为2000~5000ppm。其中,二氧化硅若添加量过低则不能满足薄膜开口性及离型膜的生产需要;若添加量过高,则粉体不好分散、易团聚,所以需要综合考虑两者,选择合适的添加量。
62.由于二氧化硅粉体的粒径较小,易团聚,所以分散液的稳定性不好,需要添加一定量的分散剂,分散剂的量不宜太多,不仅增加成本,而且也会降低聚酯的洁净度。分散剂为硅烷偶联剂、聚乙烯蜡、聚乙二醇200或聚乙二醇400中的一种或多种,分散剂的质量占比为1~5%。
63.作为一种可选的实施方式,稳定剂为磷酸、磷酸三甲酯、磷酸三乙酯、磷酸三苯酯中的至少一种,其中磷的质量占比为3~15ppm。其中,磷系稳定剂可以与体系中的水分子作用,从而降低因为水解引起的降解反应,还可以与催化剂的金属作用,从而抑制催化剂金属催化降解反应、封闭端基,达到抑制热降解和热氧降解反应、提高熔体热稳定性的作用。但是磷的添加量不宜过高,由于磷与催化剂的金属作用会导致催化剂失活,缩聚反应变慢甚至停止。
64.性能及测试:
65.a.本发明所制备的高透亮聚酯母粒的物性指标为:特性粘度为0.630~0.680dl/g,端羧基含量为13~20mol/t,l值为89~90,二甘醇含量为0.8~1.2%。
66.b.分散液的粒径均匀、粒径分布很窄,d(50)为0.1~0.2um,d(98)为0.2~0.3um,粒径分布图如下:
67.c.切片的热稳定性好,热失重测试结果如下表1:
68.表1
[0069][0070]
d.本发明所制备的mlcc离型膜专用聚酯母粒,双向拉伸成膜后,薄膜雾度可以控制在1.0%以内,透光率可以达到90.0%以上;薄膜表面粉体分布均匀、无大颗粒,聚酯薄膜表面粗糙度ra<15nm,rz<200nm,在保证低粗糙度的前提下,本母粒还具有良好的开口性,满足薄膜的生产和加工需要。
[0071]
图3(a)为采用外购韩国的mlcc离型膜专用聚酯母粒制得的薄膜在显微镜下的表面形态,图3(b)为采用本发明的mlcc离型膜专用聚酯母粒制得的薄膜在显微镜下的表面形态,从显微镜图片中可以很清晰地看出本发明的mlcc离型膜专用聚酯母粒制得的薄膜表面粒子分布更均匀,粒子更小,表面粗糙度大幅度降低。
[0072]
图4(c)和图4(d)分别为本发明母粒所制得的薄膜的表面粗糙度测试图,ra=10nm,rz=70nm。进一步说明膜表面平滑性很好,粒子很小、分布也很均匀,优于市面上的多数厂家的产品。
[0073]
需要明确的是,本说明书中的各个实施例均采用递进的方式描述,各个实施例之间相同或相似的部分互相参见即可,每个实施例重点说明的都是与其他实施例的不同之处。本发明并不局限于上文所描述并在图中示出的特定步骤和结构。并且,为了简明起见,这里省略对已知方法技术的详细描述。
[0074]
以上仅为本技术的实施例而已,并不限制于本技术。在不脱离本发明的范围的情况下对于本领域技术人员来说,本技术可以有各种更改和变化。凡在本技术的精神和原理之内所作的任何修改、等同替换、改进等,均应包含在本技术的权利要求范围内。
再多了解一些
本文用于创业者技术爱好者查询,仅供学习研究,如用于商业用途,请联系技术所有人。