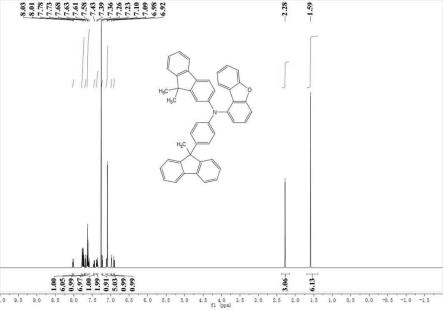
1.本发明涉及发光材料技术领域,更具体的说是涉及一种有机化合物及其制备方法及有机电致发光器件。
背景技术:
2.有机电致发光显示器(oled)是主动发光显示装置。其具有自发光、颜色鲜艳亮丽、厚度薄、质量轻、响应速度快、视角广、驱动电压低、耐受苛刻自然条件、可做成柔性面板等特点,目前中小尺寸的oled显示屏已经在多种高端智能手机上得到了大规模的应用,在低工作电压条件下获得器件的最佳发光效率是oled领域的普遍需求。
3.已经进行了许多改进以使有机el器件得到实际应用。例如,众所周知,通过进一步分配层压结构的各种作用并形成阳极,可以实现高效率和高耐久性,在基板上设置空穴注入层,空穴传输层,空穴阻挡层,发光层,电子传输层,电子注入层和阴极。
4.利用该有机el器件,从两个电极注入的电荷在发光层中重新组合以获得发光。在这种情况下,如何有效地将空穴和电子的电荷转移到发光层是重要的,并且该器件需要具有优异的载流子平衡。而且,通过增强阻挡从阴极注入的电子的空穴注入特性和电子阻挡特性以增加空穴和电子的复合概率,以及通过限制在发光层内产生的激子,发光效率得以提高。因此,发光辅助材料的作用是如此重要。
5.有机电致发光材料的研究已经在学术界和工业界广泛开展,但目前为止还未充分开发出稳定又高效的有机电气元件用的有机物层材料,而且该技术的产业化进程仍面临许多关键问题,因此,如何开发一种新的发光辅助材料,一直是本领域技术人员亟待解决的问题。
技术实现要素:
6.有鉴于此,本发明的目的之一是提供一种新型有机化合物;目的之二是提供新型有机化合物的合成方法;目的之三是提供了一种应用所述新型有机化合物的有机电致发光器件为了实现上述目的,本发明采用如下技术方案:一种有机化合物,其分子式如通式(i)所示:
式中:l选自经取代或未经取代的c6-c30的芳基、经取代或未经取代的c6-c30的杂芳基,其中杂原子选自氧、氮、硫;r
1-r4彼此相同或不同并各自独立的选自氢、氘、经取代或未经取代的c1-c15烷烃、经取代或未经取代的c1-c18环烷烃、经取代或未经取代的c6-c30的芳基、经取代或未经取代的c6-c30的杂芳基,其中杂原子选自氧、氮、硫。
7.进一步优选:l选自经取代或未经取代的苯基,且经取代时取代基选自氢、苯基、c1-c10的烷基;r
1-r4彼此相同或不同并各自独立的选自氢、氘、经取代或未经取代的c1-c10烷烃、经取代或未经取代的c1-c12环烷烃、经取代或未经取代的c6-c20的芳基、经取代或未经取代的c6-c20的杂芳基,其中杂原子选自氧、氮、硫。
8.本说明中,“取代”意指被选自以下的一个、两个或更多个取代基取代:氢、c1-c20烷基、c1-c20烷氧基、c6-c30的芳基、c6-c30的杂芳基,其中杂原子选自氧、氮、硫。
9.进一步的,上述的多环芳族系化合物中,选自下述结构式所示化合物中的任意一种:
。
10.本发明的另一个目的在于提供上述发光辅助材料的制备方法,式i的合成路线为:
式中r
1-r4、l均如上述限定;hal1选自氟、氯、溴、碘;将原料a和原料b溶于甲苯后,在n2氛围下加入pd2(dba)3、p(t-bu)3和t-buona,升温至110-120℃并搅拌反应10-12h,反应结束后使用硅藻土趁热抽滤,除去盐和催化剂,滤液冷却至室温后,将蒸馏水添加到滤液中进行洗涤,分液后保留有机相,用乙酸乙酯萃取水相,然后使用硫酸镁干燥合并后的有机层,并使用旋转式蒸发器去除溶剂,最后以二氯甲烷和石油醚的混合物作为洗脱剂,用管柱色谱法纯化剩余物质,得到通式ⅰ所示化合物。
11.一种有机电致发光器件,包括:有机物层;所述有机物层包括发光辅助层,所述发光辅助层包括上述的有机化合物。
12.经由上述的技术方案可知,与现有技术相比,本发明具有如下有益效果:本发明提供一种以芴类为母核以及三芳胺类官能团的化合物可以作为绿光和红光有机电致发光器件的发光辅助层,该类化合物可减少空穴传输层和发光层之间的势垒,降低有机电致发光器件的驱动电压,进一步提高空穴传输速率,以及电子阻挡能力,空穴和电子在发光层内的电荷均衡增加,从而不在空穴输送层表面,而是在发光层内部很好的的形成光,从而极大的提高器件的寿命和发光效率。
附图说明
13.为了更清楚地说明本发明实施例或现有技术中的技术方案,下面将对实施例或现有技术描述中所需要使用的附图作简单地介绍,显而易见地,下面描述中的附图仅仅是本发明的实施例,对于本领域普通技术人员来讲,在不付出创造性劳动的前提下,还可以根据提供的附图获得其他的附图。
14.图1为本发明实施例1的核磁共振氢谱图。
具体实施方式
15.下面将结合本发明实施例中的附图,对本发明实施例中的技术方案进行清楚、完整地描述,显然,所描述的实施例仅仅是本发明一部分实施例,而不是全部的实施例。基于本发明中的实施例,本领域普通技术人员在没有做出创造性劳动前提下所获得的所有其他实施例,都属于本发明保护的范围。
16.实施例1将原料a(20.00mmol)和原料b(20.00mmol)溶于甲苯后,在n2氛围下加入pd2(dba)3(0.4mmol)、p(t-bu)3(1.0mmol)和t-buona(40.00mmol),升温至120℃并搅拌反应10h,反应结束后使用硅藻土趁热抽滤,除去盐和催化剂,滤液冷却至室温后,将蒸馏水添加到滤液中进行洗涤,分液后保留有机相,用乙酸乙酯萃取水相,然后使用硫酸镁干燥合并后的有机层,并使用旋转式蒸发器去除溶剂,最后以二氯甲烷和石油醚(v:v=1:10)的混合物作为洗
脱剂,用管柱色谱法纯化剩余物质,得到化合物11所示化合物;(10.85g,产率:86.25%,mw:629.80);质谱测试:理论值为629.80;测试值为629.65。
17.元素分析:计算值为:c,89.63; h, 5.60; n, 2.72; o, 2.54。
18.测试值为:c,88.86; h, 5.76; n, 2.94; o, 2.78。
19.实施例2实施例2中原料b需要根据以下反应进行合成。
20.将原料1(1.0eq)和原料2(1.0eq)溶于甲苯后,在n2氛围下加入pd2(dba)3(0.02eq)、p(t-bu)3(0.05eq)和t-buona(2.0eq),升温至120℃ 并搅拌反应10h,制备得到原料b。
21.将原料a(20.00mmol)和原料b(20.00mmol)溶于甲苯后,在n2氛围下加入pd2(dba)3(0.4mmol)、p(t-bu)3(1.0mmol)和t-buona(40.00mmol),升温至120℃并搅拌反应10h,反应结束后使用硅藻土趁热抽滤,除去盐和催化剂,滤液冷却至室温后,将蒸馏水添加到滤液中进行洗涤,分液后保留有机相,用乙酸乙酯萃取水相,然后使用硫酸镁干燥合并后的有机层,并使用旋转式蒸发器去除溶剂,最后以二氯甲烷和石油醚(v:v=1:10)的混合物作为洗脱剂,用管柱色谱法纯化剩余物质,得到化合物83所示化合物;(11.29g,产率:80.05%,mw:705.90);质谱测试:理论值为705.90;测试值为705.67。
22.元素分析:计算值为:c, 90.18; h, 5.57; n, 1.98; o, 2.27。
23.测试值为:c, 89.68; h, 5.79; n, 2.22; o, 2.39。
24.实施例3实施例3中原料b需要根据以下反应进行合成。
25.将原料1(1.0eq)和原料2(1.0eq)溶于甲苯后,在n2氛围下加入pd2(dba)3(0.02eq)、p(t-bu)3(0.05eq)和t-buona(2.0eq),升温至120℃ 并搅拌反应10h,制备得到原料b。
26.将原料a(20.00mmol)和原料b(20.00mmol)溶于甲苯后,在n2氛围下加入pd2(dba)3(0.4mmol)、p(t-bu)3(1.0mmol)和t-buona(40.00mmol),升温至120℃并搅拌反应10h,反应结束后使用硅藻土趁热抽滤,除去盐和催化剂,滤液冷却至室温后,将蒸馏水添加到滤液中进行洗涤,分液后保留有机相,用乙酸乙酯萃取水相,然后使用硫酸镁干燥合并后的有机层,并使用旋转式蒸发器去除溶剂,最后以二氯甲烷和石油醚(v:v=1:10)的混合物作为洗脱剂,用管柱色谱法纯化剩余物质,得到化合物83所示化合物;(11.04g,产率:78.26%,mw:705.90);质谱测试:理论值为705.90;测试值为706.11。
27.元素分析:计算值为:c, 90.18; h, 5.57; n, 1.98; o, 2.27。
28.测试值为:c, 89.61; h, 5.77; n, 2.18; o, 2.45。
29.实施例4实施例4中原料a需要以下三步进行合成:将原料a-1(1.0eq)溶于thf中,接着换气3次,降温至-78℃,缓慢加入n-buli(2.0eq),反应4h,氮气保护下加入原料a-2(1.0eq),缓慢升温至25℃,搅拌12h,制备得到中间体a-3。
30.将原料a-3(1.0eq)溶于thf与甲苯混合溶剂(v:v=1:1),将msa(10.0eq)缓慢加入前述混合物中,在室温下搅拌8h,制备得到原料a-4。
31.将原料a-4(1.0eq)溶于thf溶液中,加入碘甲烷(5.0eq),叔丁醇钾(5.0eq),在室温下搅拌10h,制备得到原料a。
32.将原料1(1.0eq)和原料2(1.0eq)溶于甲苯后,在n2氛围下加入pd2(dba)3(0.02eq)、p(t-bu)3(0.05eq)和t-buona(2.0eq),升温至120℃ 并搅拌反应10h,制备得到原料b。
33.将原料a(20.00mmol)和原料b(20.00mmol)溶于甲苯后,在n2氛围下加入pd2(dba)3(0.4mmol)、p(t-bu)3(1.0mmol)和t-buona(40.00mmol),升温至120℃并搅拌反应10h,反应结束后使用硅藻土趁热抽滤,除去盐和催化剂,滤液冷却至室温后,将蒸馏水添加到滤液中进行洗涤,分液后保留有机相,用乙酸乙酯萃取水相,然后使用硫酸镁干燥合并后的有机层,并使用旋转式蒸发器去除溶剂,最后以二氯甲烷和石油醚(v:v=1:10)的混合物作为洗脱剂,用管柱色谱法纯化剩余物质,得到化合物122所示化合物;(10.84g,产率:75.34%,mw:719.93);质谱测试:理论值为719.93;测试值为719.75。
34.元素分析:计算值为:c, 90.09; h, 5.74 n, 1.95; o, 2.22。
35.测试值为:c, 89.57; h, 5.94; n, 2.18; o, 2.46。
36.因结构通式为发明内容中的式1,其他化合物的合成路线和原理均与上述所列举的实施例相同,所以在此不再穷举。按照上述制备方法可得到如下表1所示的发光辅助材料:表1:
采用上述实施例提供的发光辅助材料制备得到的有机电致发光器件,当有机物层包括发光辅助层时,所述发光辅助层包括上述实施例提供的发光辅助材料(有机化合物)。
37.器件实施例1(绿光器件)(1)ito阳极:将涂层厚度为150nm的ito(氧化铟锡)-ag-ito(氧化铟锡)玻璃基板
在蒸馏水中清洗2次,超声波洗涤30min,再用蒸馏水反复清洗2次,超声波洗涤10min,洗涤结束后,然后转移至等甩干机内进行甩干,最后用真空烘箱220℃烘烤2小时,烘烤结束后降温即可使用。以该基板为阳极,使用蒸镀机进行蒸镀器件工艺,在其上依次蒸镀其它功能层。
38.(2)hil(空穴注入层):以1
å
/s的蒸镀速率,真空蒸镀空穴注入层材料ht和p-dopant,其化学式如下所示。所述ht和p-dopant的蒸镀速率比为97:3,厚度为10nm;(3)htl(空穴传输层):以1.0
å
/s的蒸镀速率,在空穴注入层上面真空蒸镀120nm的ht作为空穴传输层;(4)发光辅助层:以1.0
å
/s的蒸镀速率,在空穴传输层上面真空蒸镀45nm的上述实施例提供的化合物11作为发光辅助层;(5)eml(发光层):然后在上述发光辅助层上,以1
å
/s的蒸镀速率,真空蒸镀厚度为400nm的主体材料(host-1和host-2)和掺杂材料(dopant)作为发光层,其中host-1和host-2作为双主体材料同掺杂材料进行共蒸,host-1和host-2比例为50%:50%,其host-1和host-2和dopant的化学式如下所示。其中主体材料和dopant的蒸镀速率比为88:12。
39.(6)hbl(空穴阻挡层):以0.5
å
/s的蒸镀速率,真空蒸镀厚度为5.0nm的空穴阻挡层hbl。
40.(7)etl(电子传输层):以1
å
/s的蒸镀速率,真空蒸镀厚度为30nm的et和liq作为电子传输层。其中et和liq的蒸镀速率比为50:50。
41.(8)eil(电子注入层):以0.5
å
/s的蒸镀速率,蒸镀yb膜层1.0nm,形成电子注入层。
42.(9)阴极:以1
å
/s的蒸镀速率比,蒸镀镁和银18nm,其蒸镀速率比为1:9,形成阴极。
43.(10)光取出层:以1
å
/s的蒸镀速率,在阴极上真空蒸镀厚度为70nm的cpl,作为光取出层。
44.(11)将蒸镀完成的基板进行封装。首先采用涂胶设备将清洗后盖板用uv胶进行涂覆工艺,然后将涂覆完成的盖板移至压合工段,将蒸镀完成的基板置于盖板上端,最后将基板和盖板在贴合设备作用下进行贴合,同时完成对uv胶光照固化。
45.各层所采用的化合物如下:
器件对比例1:该对比例提供了一种有机电致发光器件,该有机电致发光器件的制备方法与器件实施例1的唯一区别在于,该有机电致发光器件是分别采用现有的对比化合物a、b、c、d、e、f、g、h、i、j替代上述器件实施例1中的发光辅助材料(化合物11)进行蒸镀,制备器件对比例1-10。其中,对比化合物a、b、c、d、e、f、g、h、i、j的化学结构式为:
测试应用例和对比例中制备得到有机电致发光器件的性能,在15000(nits)亮度下对上述器件实施例1-25以及器件对比例1-10得到的有机电致发光器件发光效率、以及寿命进行表征,测试结果如下表2:表2发光特性测试结果(亮度值为15000nits)
器件应用例26(红光器件)所制备oled器件的结构为:ito阳极/hil/htl/发光辅助层/eml/hbl/etl /eil/阴极/光取出层a、ito阳极:将涂层厚度为1500
å
的ito(氧化铟锡)-ag-ito(氧化铟锡)玻璃基板在蒸馏水中清洗2次,超声波洗涤30min,再用蒸馏水反复清洗2次,超声波洗涤10min,洗涤结束后,用甲醇、丙酮、异丙醇依次超声波洗涤(每次洗涤5 min),干燥,然后转移至等离子体清洗机内洗涤5min,再送至蒸镀机中,以该基板为阳极,在其上依次蒸镀其它功能层。
46.b、hil(空穴注入层):以1
å
/s的蒸镀速率,真空蒸镀空穴注入层材料ht-1和p-dopant,其化学式如下所示。所述ht-1和p-dopant的蒸镀速率比为97:3,厚度为10nm;c、htl(空穴传输层):以1.5
å
/s的蒸镀速率,在空穴注入层上面真空蒸镀130nm的ht-1作为空穴传输层;d、发光辅助层:以0.5
å
/s的蒸镀速率,在空穴传输层上面真空蒸镀10nm的上述实
施例提供的化合物11作为发光辅助层;e、eml(发光层):然后在上述发光辅助层上,以1
å
/s的蒸镀速率,真空蒸镀厚度为20nm的主体材料(host-1)和掺杂材料(dopant-1)作为发光层,其host-1和dopant-1的化学式如下所示。其中双host-1和dopant-1的蒸镀速率比为98:2。
47.f、hbl(空穴阻挡层):以0.5
å
/s的蒸镀速率,真空蒸镀厚度为5.0nm的空穴阻挡层hb。
48.g、etl(电子传输层):以1
å
/s的蒸镀速率,真空蒸镀厚度为35nm的et-1和liq作为电子传输层,其et-1的化学式如下所示。其中et-1和liq的蒸镀速率比为50:50。
49.h、eil(电子注入层):以0.5
å
/s的蒸镀速率,蒸镀yb膜层1.0nm,形成电子注入层。
50.i、阴极:以1
å
/s的蒸镀速率比,蒸镀镁和银 18nm,其蒸镀速率比为1:9,得到oled器件。
51.j、光取出层:以1
å
/s的蒸镀速率,在阴极上真空蒸镀厚度为70nm的cpl-1,作为光取出层。
52.k、随后将蒸镀完成的基板进行封装。首先采用涂胶设备将清洗后盖板用uv胶进行涂覆工艺,然后将涂覆完成的盖板移至压合工段,将蒸镀完成的基板置于盖板上端,最后将基板和盖板在贴合设备作用下进行贴合,同时完成对uv胶光照固化。
53.器件对比例11:该对比例提供了一种有机电致发光器件,该有机电致发光器件的制备方法与器件
实施例26的唯一区别在于,该有机电致发光器件是分别采用现有的对比化合物a、b、c、d、e、f、g、h、i、j替代上述器件实施例26中的发光辅助材料(化合物11)进行蒸镀,制备器件对比例11-20。其中,对比化合物a、b、c、d、e、f、g、h、i、j的化学结构式为:
在6000(nits)亮度下对上述器件实施例26~50以及器件对比例11~20得到的有机电致发光器件的驱动电压、发光效率以及寿命进行表征,测试结果如下表3:表3:
根据表2结果,在绿光器件结构中对比化合物a与化合物17、b和化合物24是平行对比,表明在母核为苯基芴可以提高器件性能。对比化合物c与本发明结构相近,表明l桥联基团为苯基,甲苯基以及联苯基更能提升器件性能。对比化合物d与化合物95、对比化合物h与化合物89、对比化合物e与化合物27是平行对比均表明侧链为二苯并呋喃和二苯并芴基相比其他基团在绿光器件结构中更能提升器件性能。
54.根据表3结果,在红光器件结构中对比化合物h与化合物89是平行对比证明在红光器件结构中侧链取代基未进行稠合时可以提高器件性能。
55.综上,与对比例1~20所制备的有机电致发光器件相比,实施例1~50以本发明所述有机电致发光化合物作为发光辅助层用于有机电致发光器件中,其驱动电压,发光效率、寿命均得到提高,能够同时应用于和绿光有机电致发光器件和红光有机电致发光器件。在本发明所用的红光和绿光器件中,发光效率提高了4~7%,取得了显著提高。
56.本说明书中各个实施例采用递进的方式描述,每个实施例重点说明的都是与其他实施例的不同之处,各个实施例之间相同相似部分互相参见即可。对于实施例公开的装置而言,由于其与实施例公开的方法相对应,所以描述的比较简单,相关之处参见方法部分说明即可。
57.对所公开的实施例的上述说明,使本领域专业技术人员能够实现或使用本发明。对这些实施例的多种修改对本领域的专业技术人员来说将是显而易见的,本文中所定义的
一般原理可以在不脱离本发明的精神或范围的情况下,在其它实施例中实现。因此,本发明将不会被限制于本文所示的这些实施例,而是要符合与本文所公开的原理和新颖特点相一致的最宽的范围。
再多了解一些
本文用于创业者技术爱好者查询,仅供学习研究,如用于商业用途,请联系技术所有人。