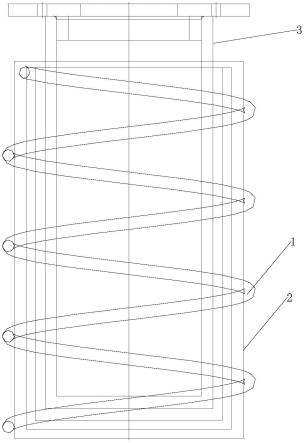
1.本发明属于中频感应炉加工技术领域,涉及一种银合金中频熔炼用石墨坩埚加工方法。
背景技术:
2.银基电接触材料制造行业中,多采用中频炉冶炼,而石墨坩埚由于不影响熔炼合金元素成分而广泛使用。银基电接触材料熔炼温度在960℃以上,石墨坩埚在这个温度下容易氧化而烧损,且石墨坩埚与中频线圈直接接触易导致线圈过热损坏。在实际生产中一般在石墨坩埚外另筑一层以石英砂、玻璃水夯实而成的炉衬,以石棉布为隔热材料保护中频线圈,并减少石墨坩埚氧化烧损,专利cn201310082503、cn102889789a等都有详细描述。此类方式在更换石墨坩埚时必须将坩埚连带夯实的高密度外衬、内衬一起敲掉,费时费力,同时石英砂-玻璃水类衬料热膨胀系数与石墨坩埚不一致易导致坩埚裂开减少寿命,且其更换过程、衬料加热烘干全程占用中频炉,极大的降低了设备的利用率,此外由于其浇口使用材料也是石英砂-玻璃水,每次更换坩埚必须敲掉,增加了更换坩埚的时间和成本。
3.专利cn103791718b提供了一种以氧化钙部分稳定氧化锆陶瓷代替石英砂-玻璃水外衬的石墨加工方式,应用于真空中频熔炼,其解决了更换坩埚时因需敲掉外衬而更换麻烦的问题,同时回收内衬打结料节约成本,氧化钙部分氧化锆陶瓷隔热材料的使用减少中频线圈烧坏的可能。但其更换坩埚时仍需敲掉打结料,外加使用中频炉烘干,其打结过程和烘干过程共需占用中频炉长达20小时以上,严重影响生产效率,且大量使用氧化钙部分稳定氧化锆陶瓷成本远高于原有石英砂-玻璃水体系。
4.根据上述情况,本发明提出新的解决方案。
技术实现要素:
5.本发明的目的是为了克服现有技术存在的缺点和不足,而提供一种银合金中频熔炼用石墨坩埚的加工方法,该方法烘干工艺易于控制、时间和成本更少、更换坩埚方便、中频炉利用率更高、各部件分体式处理灵活更换的银合金中频熔炼用石墨坩埚加工方法。
6.为实现上述目的,本发明的技术方案是包括以下步骤:
7.(1)石墨坩埚表面预处理:将乙醇溶液倒入超声波清洗机中,石墨坩埚浸入超声波清洗机中清洗,洗完毕后将所述石墨坩埚烘干;
8.(2)石墨坩埚表面涂覆涂料:经步骤(1)处理的石墨坩埚置于可加热的旋转台上,加热至80-100℃,以25-35r/min的转速匀速旋转,将耐高温抗氧化涂层材料均匀喷涂至所述石墨坩埚外表面,冷却后在所述石墨坩埚外表面包裹10-12mm厚度的含锆硅酸铝纤维布;
9.(3)烧结:将经步骤(2)处理的石墨坩埚置于电阻炉中保温烧结;
10.(4)坩埚安装:将经步骤(3)处理的石墨坩埚置于耐高温陶瓷筒内,所述耐高温陶瓷筒装入中频炉线圈内并固定在中频炉炉体上,将耐高温陶瓷筒的浇口安装于所述石墨坩埚开口端,并将所述浇口固定在中频炉炉体上。
11.进一步设置是所述的耐高温抗氧化涂层材料的骨料成分为,以质量百分比计:si粉20-30%、sic粉20-30%、zr2o3粉5-10%、b4c粉5-10%、sio2粉余量,其粘结剂为聚二苯醚树脂。
12.进一步设置是所述的耐高温抗氧化涂层材料的骨料成分为,以质量百分比计:si粉20-30%、sic粉20-30%、mosi2粉5-10%、al2o35-10%、sio2粉余量,其粘结剂为酚醛树脂。
13.进一步设置是所述的耐高温陶瓷筒由氧化铝陶瓷制成,总厚度为50-80mm,其内部有厚度占总厚度60-65%的真空层;耐高温陶瓷筒外径小于中频炉线圈内径4-8mm,耐高温陶瓷筒外高与中频炉炉体相等,内深小于石墨坩埚外高25-30mm,内径大于石墨坩埚外径18-20mm。
14.进一步设置是所述的步骤(1)中所述乙醇溶液浓度为55%-65%,超声清洗工艺为30hz清洗30-50min,烘干工艺为120-150℃烘烤2-3h。
15.进一步设置是所述步骤(3)的烧结工艺为:在0.2-0.4mpa氮气中烧结,烧结工艺为先升温至500-700℃,电阻炉升温速率为10℃/min,保温时间1-1.5h,随后升温至1400-1500℃,电阻炉升温速率为5℃/min,保温时间2-3h,随炉冷却至60℃以下出炉。
16.进一步设置是所述浇口由氧化铝陶瓷制成,形状为固定在一起的两个同轴空心圆柱,上空心圆柱内径等于石墨坩埚内径,厚度60-80mm,高度为15-20mm,空心圆柱上有有两个关于轴心中心对称的孔;下空心圆柱内径等于耐高温陶瓷筒内径,厚度为10-20mm,高度25-30mm。
17.本发明的有益效果是:
18.1.本发明石墨坩埚打结直接涂覆耐高温抗氧化涂料后包裹含锆硅酸铝纤维布即可,节约了坩埚打结的时间;
19.2.本发明使用电阻炉烧结,现有技术使用中频炉烘干,避免了烧结过程长时间占用中频炉无法生产的问题,提高了中频炉的利用率;
20.3.本发明浇口、耐高温陶瓷筒底座均可自由拆卸,在每次更换坩埚时不用敲除,节约了成本;
21.4.本发明将石墨坩埚加工过程移出中频炉进行,独立于其他步骤,可随时处理好备用,更换坩埚时可在将旧烧损坩埚取出后将预先烧结好的坩埚直接替换,大大提高了生产效率。
22.5.本发明涂覆前清洗、喷雾式喷涂涂料、阶段式烧结工艺更有利于涂料与坩埚的紧密贴合,在使用中不易因受热而与坩埚剥离,使用寿命更长。
23.6.本发明使用抽真空隔层氧化铝陶瓷而非使用部分稳定氧化锆陶瓷,所需成本更低廉。
附图说明
24.图1本发明的石墨钢锅装配示意图。
具体实施方式
25.为使本发明的目的、技术方案和优点更加清楚,下面将结合实施例对本发明作进
一步地详细描述。
26.实施例一:如图1所示
27.1)选用50mm厚、占总厚60%的中间抽真空层的瓷筒2放入中频炉线圈1内,其外径小于线圈内径4mm,外高与中频炉炉体相等,内深小于石墨坩埚3外高25mm,内径大于石墨坩埚外径18mm,使用铁丝将瓷筒固定在线圈上;
28.2)按质量百分比其骨料成分为质量200g si粉、200g sic粉、50g zr2o3粉、50g b4c粉、500g sio2粉配好骨粉,与粘结剂聚二苯醚树脂混合;
29.3)将55%的乙醇溶液倒入超声波清洗机中,把石墨坩埚浸入超声波清洗机中按30hz清洗30分钟;洗完毕后,将石墨坩埚置于空气烘箱中120℃烘烤2小时;
30.4)把烘干的的石墨坩埚置于会加热的旋转台上加热至80℃,以25r/min旋转,将制好的耐高温抗氧化涂料加入到喷壶中,使配好的溶液向石墨坩埚喷30秒,待风干冷却在石墨坩埚表面裹上一层10mm含锆硅酸铝纤维布;
31.5)经坩埚涂覆涂料步骤处理的石墨坩埚放入电阻炉中,在0.2mpa氮气中烧结,烧结工艺为先升温至500℃,电阻炉升温速率为10℃每分钟,保温时间1小时,随后升温至1400℃,电阻炉升温速率为5℃每分钟,保温时间2小时,随炉冷却至60℃以下出炉;
32.6)将经坩埚涂层烧结步骤处理的石墨坩埚放入底座耐高温陶瓷筒内,选用同轴空心圆柱氧化铝陶瓷浇口,其上空心圆柱厚度为60mm,高度为15mm,下空心圆柱厚度为10mm,高度25mm,将耐高温陶瓷浇口套在石墨坩埚上,使用螺栓将浇口固定在预先打好螺孔的中频炉炉体上。
33.实施例二:
34.1)选用80mm厚、占总厚65%的中间抽真空层的瓷筒放入中频炉线圈内,其外径小于线圈内径8mm,外高与中频炉炉体相等,内深小于石墨坩埚外高30mm,内径大于石墨坩埚外径20mm,使用铁丝将瓷筒固定在线圈上;
35.2)按质量百分比其骨料成分为质量百分比300g si粉、300g sic粉、100g zr2o3粉、100g b4c粉、200g sio2粉配好骨粉,与粘结剂聚二苯醚树脂混合;
36.3)将65%的乙醇溶液倒入超声波清洗机中,把石墨坩埚浸入超声波清洗机中按30hz清洗50分钟;洗完毕后,将石墨坩埚置于空气烘箱中150℃烘烤3小时;
37.4)把烘干的的石墨坩埚置于会加热的旋转台上加热至100℃,以35r/min旋转,将制好的耐高温抗氧化涂料加入到喷壶中,使配好的溶液向石墨坩埚喷40秒,待风干冷却在石墨坩埚表面裹上一层12mm含锆硅酸铝纤维布;
38.5)经坩埚涂覆涂料步骤处理的石墨坩埚放入电阻炉中,在0.4mpa氮气中烧结,烧结工艺为先升温至700℃,电阻炉升温速率为10℃每分钟,保温时间1.5小时,随后升温至1500℃,电阻炉升温速率为5℃每分钟,保温时间3小时,随炉冷却至60℃以下出炉;
39.6)将经坩埚涂层烧结步骤处理的石墨坩埚放入底座耐高温陶瓷筒内,选用同轴空心圆柱氧化铝陶瓷浇口,其上空心圆柱厚度为80mm,高度为20mm,下空心圆柱厚度为20mm,高度30mm,将耐高温陶瓷浇口套在石墨坩埚上,使用螺栓将浇口固定在预先打好螺孔的中频炉炉体上。
40.实施例三:
41.1)选用65mm厚、占总厚62%的中间抽真空层的瓷筒放入中频炉线圈内,其外径小
al2o3粉、200g sio2粉配好骨粉,与粘结剂酚醛树脂混合;
57.3)将65%的乙醇溶液倒入超声波清洗机中,把石墨坩埚浸入超声波清洗机中按30hz清洗50分钟;洗完毕后,将石墨坩埚置于空气烘箱中150℃烘烤3小时;
58.4)把烘干的的石墨坩埚置于会加热的旋转台上加热至100℃,以35r/min旋转,将制好的耐高温抗氧化涂料加入到喷壶中,使配好的溶液向石墨坩埚喷40秒,待风干冷却在石墨坩埚表面裹上一层12mm含锆硅酸铝纤维布;
59.5)经坩埚涂覆涂料步骤处理的石墨坩埚放入电阻炉中,在0.4mpa氮气中烧结,烧结工艺为先升温至700℃,电阻炉升温速率为10℃每分钟,保温时间1.5小时,随后升温至1500℃,电阻炉升温速率为5℃每分钟,保温时间3小时,随炉冷却至60℃以下出炉;
60.6)将经坩埚涂层烧结步骤处理的石墨坩埚放入底座耐高温陶瓷筒内,选用同轴空心圆柱氧化铝陶瓷浇口,其上空心圆柱厚度为80mm,高度为20mm,下空心圆柱厚度为20mm,高度30mm,将耐高温陶瓷浇口套在石墨坩埚上,使用螺栓将浇口固定在预先打好螺孔的中频炉炉体上。
61.实施例六:
62.1)选用65mm厚、占总厚62%的中间抽真空层的瓷筒放入中频炉线圈内,其外径小于线圈内径6mm,外高与中频炉炉体相等,内深小于石墨坩埚外高27mm,内径大于石墨坩埚外径19mm,使用铁丝将瓷筒固定在线圈上;
63.2)按质量百分比其骨料成分为质量250g si粉、250g sic粉、75g mosi2粉、75g al2o3粉、350g sio2粉配好骨粉,与粘结剂酚醛树脂混合;
64.3)将60%的乙醇溶液倒入超声波清洗机中,把石墨坩埚浸入超声波清洗机中按30hz清洗40分钟;洗完毕后,将石墨坩埚置于空气烘箱中135℃烘烤2.5小时;
65.4)把烘干的的石墨坩埚置于会加热的旋转台上加热至90℃,以30r/min旋转,将制好的耐高温抗氧化涂料加入到喷壶中,使配好的溶液向石墨坩埚喷35秒,待风干冷却在石墨坩埚表面裹上一层11mm含锆硅酸铝纤维布;
66.5)经坩埚涂覆涂料步骤处理的石墨坩埚放入电阻炉中,在0.3mpa中烧结,烧结工艺为先升温至600℃,电阻炉升温速率为10℃每分钟,保温时间1.25小时,随后升温至1450℃,电阻炉升温速率为5℃每分钟,保温时间2.5小时,随炉冷却至60℃以下出炉;
67.6)将经坩埚涂层烧结步骤处理的石墨坩埚放入底座耐高温陶瓷筒内,选用同轴空心圆柱氧化铝陶瓷浇口,其上空心圆柱厚度为70mm,高度为17.5mm,下空心圆柱厚度为15mm,高度27.5mm,将耐高温陶瓷浇口套在石墨坩埚上,使用螺栓将浇口固定在预先打好螺孔的中频炉炉体上。
68.以上所揭露的仅为本发明较佳实施例而已,当然不能以此来限定本发明之权利范围,因此依本发明权利要求所作的等同变化,仍属本发明所涵盖的范围。
再多了解一些
本文用于创业者技术爱好者查询,仅供学习研究,如用于商业用途,请联系技术所有人。