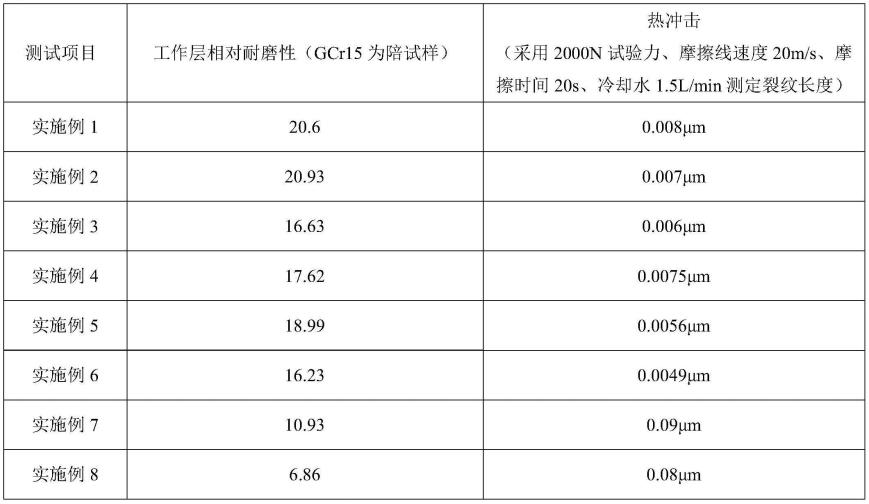
1.本发明涉及一种高速钢工作辊的制备方法,属于粉末冶金轧辊制备技术领域。
背景技术:
2.随着短流程轧制技术的发展,近终形成型技术在轧制领域及钢铁行业呈现出蓬勃发展的趋势,对轧辊的性能需求不断提高,粉末冶金轧辊组织致密,可消除常规铸造轧辊凝固过程中产生的偏析,同时,粉末冶金轧辊具有成形性好的优点,符合近终形制造的特点,同时,其细晶粒、高耐磨及组织的高度均匀性也更能满足短流程长辊役轧制用辊的需求。
3.针对后段、成品机架及短流程轧制特点研发粉末冶金高速钢,如何确定制备工艺,都是开发粉末冶金高速钢工作辊急需解决的问题。
技术实现要素:
4.本发明需要解决的技术问题是提供一种高速钢工作辊的制备方法,以满足热轧线后段尤其是成品机架使用高速钢的需求,满足短流程轧线用辊需求,提升轧辊质量。
5.为解决上述技术问题,本发明所采用的技术方案是:
6.一种高速钢工作辊的制备方法,所述高速钢工作辊的合金料配比为:c:1.0~2.30%,si:0.5~2.0%,b:0.5-1.5%,mn:0.2~1.2%,p≤0.10%,s≤0.1%,cr:1.0-8.0%,ni:0.5-1.20%,mo:2.0-10.00%,v:2.00-10.00,w:0.1-5.0,nb≤1.0%,余量为fe;
7.制备方法包括如下步骤:
8.步骤a、将按照上述配比的合金料放入球磨机进行球磨;
9.步骤b、球磨结束后在真空度≤10-3
pa的真空炉加热烘干,冷却至30-50℃,碾碎,利用≥400目的筛网进行过筛制粉备用;
10.步骤c、采用模具制备样坯,压实备用;
11.步骤d、利用真空烧结炉进行烧结,制备粉末冶金的辊套;
12.步骤e、将粉末冶金辊套加工内孔去除毛坯缺陷,在预热炉进行预热;
13.步骤f、将预热后的粉末冶金辊套放置于砂型中,浇注芯部钢水,凝固、成型;
14.步骤g、将浇注成型的毛坯件放置于热处理炉进行热处理;
15.步骤h、热处理结束后加工、检测直至成品。
16.本发明技术方案的进一步改进在于:所述步骤a中合金料粒度为2-3mm,采用行星式球磨机,球磨机液体介质为无水酒精、丙酮、航空煤油中的一种,同时加入3-5%的液体石蜡。
17.本发明技术方案的进一步改进在于:所述步骤a中采用的球磨球为硬质合金球,球:料配比为10:1,球磨时间50-100h。
18.本发明技术方案的进一步改进在于:所述步骤b中烘干温度为150-350℃,烘干时间40-80h;同时冷却在真空度≤10-3
mp的条件下进行。
19.本发明技术方案的进一步改进在于:所述步骤c中压实过程中压样机的压力≥
200mpa,压制时间3-20s,或采用冷等静压法进行压实。
20.本发明技术方案的进一步改进在于:所述步骤d中的烧结工艺为:在350-450℃保温8-20h后,以5-20℃/h的升温速率升温至烧结温度,烧结温度为1200-1300℃,烧结时间60-120min,烧结结束后以20-30℃/h速率降至室温。
21.本发明技术方案的进一步改进在于:所述步骤e中预热温度500-600℃,预热时间10-20h。
22.本发明技术方案的进一步改进在于:所述步骤f中的芯部钢水材质为低合金钢或足够强度的铁系材质。
23.本发明技术方案的进一步改进在于:所述步骤g中的热处理方式为退火,退火温度600-700℃,保温时间40-60h。
24.由于采用了上述技术方案,本发明取得的技术进步是:
25.本发明将粉末冶金技术应用到轧辊领域,通过粉末制备、样坯制取、烧结、进一步的浇注复合及热处理,获得高细晶粒度,高耐磨,高组织均匀性的粉末冶金轧辊,在球磨阶段加入液体石蜡作为粘接剂,有利于制备的粉末压实成型,在烧结过程中在350-450℃保温过程中,在烧结炉体持续抽真空的过程中,液体石蜡挥发为气体去除,同时,球磨中加入球磨介质无水酒钢、丙酮及航空煤油等,避免了粉末在球磨过程中的氧化,在烧结过程中属于半熔状态,其组织中消除了常规铸造轧辊中出现的大块状共晶碳化物,因此其较常规高速钢轧辊具有更高的抗事故性、耐磨性及组织均匀性。
26.采用的烧结工艺通过在粉末处于微熔状态,可完成各物相形成的同时,避免晶粒长大及成分偏析。粉末冶金高速钢轧辊可有效消除铸造高速钢的成分偏析,晶粒粗大等缺点,粉末冶金高速钢组织均匀,晶粒细小,能较好适应成品机架高速钢的工况特点,同时,粉末冶金高速钢可实现近终形制造,而铸造高速钢需去除铸造缺陷而加工余量大大高于粉末冶金高速钢,粉末冶金高速钢出材率大幅增加;同时,粉末冶金高速钢工艺生产周期较铸造高速钢大幅缩短。
附图说明
27.图1是本发明的烧结工艺图;
28.图2是烧结出来的粉末冶金高速钢。
具体实施方式
29.下面结合实施例对本发明做进一步详细说明:
30.实施例1
31.以废钢屑、锻钢料头、钼铁、钒铁、电极粉为合金原料,合金原料总成分为c 1.76,si 0.93,b 0.56,mn 0.69,cr 6.23,ni 0.62,mo 4.95,v 8.32,w 0.65,p≤0.10%,s≤0.1%,nb≤1.0%,余量为fe。加入行星式球磨机中进行球磨,加入无水酒精球磨60h,加入3.3%液体石蜡,采用滤纸过滤,后放入真空烘干炉烘干,真空度0.001pa,烘干温度156℃,烘干时间45h,冷却至25℃出炉。利用400目的网筛进行筛选粉末,利用压样机进行压样,压制成辊身直径710mm,内孔515mm的试样,在抽真空至10-4
mpa的真空炉内进行烧结,先在400℃保温10h,然后以8℃/h的升温速率升温至1280℃烧结100min,以25℃/h降温速率降温至
30℃出炉。内孔车削见光并预热至550℃后装入提前预留空间的砂型内,浇注低合金钢的芯部钢水,冷却至室温开箱,成型为轧辊。
32.实施例2
33.以废钢屑、锻钢料头、钼铁、钒铁、电极粉为合金原料,合金原料总成分为c 1.83,si 0.98,b 0.62,mn 0.72,cr 6.36,ni 0.78,mo 5.65,v 6.93,w 0.78,p≤0.10%,s≤0.1%,nb≤1.0%,余量为fe加入行星式球磨机中进行球磨,加入航空煤油球磨55h,加入液体石蜡3.69%,采用滤纸过滤,后放入真空烘干炉烘干,真空度0.00025pa,烘干温度108℃,烘干时间46h,冷却至28℃出炉。利用600目的网筛进行筛选粉末,利用压样机进行压样,压制成辊身直径715mm,内孔510mm的试样,在抽真空至10-3
mpa的真空炉内进行烧结,先在430℃保温10h,然后以7℃/h的升温速率升温至1290℃烧结105min,以26℃/h降温速率降温至25℃出炉。内孔车削见光并预热至560℃后装入提前预留空间的砂型内,浇注低合金钢的芯部钢水,冷却至室温开箱,成型为轧辊。
34.实施例3
35.以废钢屑、锻钢料头、钼铁、钒铁、电极粉为合金原料,合金原料总成分为c 1.36,si 0.99,b 0.69,mn 0.73,cr 5.36,ni 0.69,mo 7.69,v 7.93,w 0.79,p≤0.10%,s≤0.1%,nb≤1.0%,余量为fe。加入行星式球磨机中进行球磨,加入丙酮球磨58h,加入3.63%液体石蜡,采用滤纸过滤,后放入真空烘干炉烘干,真空度0.0002pa,烘干温度103℃,烘干时间43h,冷却至29℃出炉。利用600目的网筛进行筛选粉末,利用压样机进行压样,压制成辊身直径723mm,内孔515mm的试样,在抽真空至3
×
10-4
mpa的真空炉内进行烧结,先在425℃保温9h,然后以9℃/h的升温速率升温至1260℃烧结95min,以30℃/h降温速率降温至28℃出炉。内孔车削见光并预热至553℃后装入提前预留空间的砂型内,浇注低合金钢的芯部钢水,冷却至室温开箱,成型为轧辊。
36.实施例4
37.以废钢屑、锻钢料头、钼铁、钒铁、电极粉为合金原料,合金原料总成分为c 1.66,si 0.65,b 0.62,mn 0.33,cr 3.36,ni 0.32,mo 6.93,v 7.13,w 0.25,p≤0.10%,s≤0.1%,nb≤1.0%,余量为fe。加入行星式球磨机中进行球磨,加入无水酒精球磨60h,加入液体石蜡4.01%,采用滤纸过滤,后放入真空烘干炉烘干,真空度0.0002pa,烘干温度103℃,烘干时间43h,冷却至29℃出炉。利用400目的网筛进行筛选粉末,利用压样机进行压样,压制成辊身直径718mm,内孔521mm的试样,在抽真空至2
×
10-4
mpa的真空炉内进行烧结,先在426℃保温9.5h,然后以9.5℃/h的升温速率升温至1290℃烧结103min,以30℃/h降温速率降温至31℃出炉。内孔车削见光并预热至552℃后装入提前预留空间的砂型内,浇注低合金钢的芯部钢水,冷却至室温开箱,成型为轧辊。
38.实施例5
39.以废钢屑、锻钢料头、钼铁、钒铁、电极粉为合金原料,合金原料总成分为c 1.73,si 0.69,b 0.65,mn 0.39,cr 3.16,ni 0.52,mo 6.33,v 6.13,w 0.45,p≤0.10%,s≤0.1%,nb≤1.0%,余量为fe。加入行星式球磨机中进行球磨,加入航空煤油球磨55h,加入液体石蜡3.65%,采用滤纸过滤,后放入真空烘干炉烘干,真空度0.0001pa,烘干温度108℃,烘干时间41h,冷却至23℃出炉。利用500目的网筛进行筛选粉末,利用压样机进行压样,压制成辊身直径790mm,内孔523mm的试样,在抽真空至5
×
10-4
mpa的真空炉内进行烧结,先
在423℃保温8.5h,然后以9.5℃/h的升温速率升温至1296℃烧结116min,以28℃/h降温速率降温至36℃出炉。内孔车削见光并预热至556℃后装入提前预留空间的砂型内,浇注低合金钢的芯部钢水,冷却至室温开箱,成型为轧辊。
40.实施例6
41.以废钢屑、锻钢料头、钼铁、钒铁、电极粉为合金原料,合金原料总成分为c 1.31,si 0.80,b 0.61,mn 0.53,cr 4.1,ni 0.32,mo 4.33,v 5.13,w 0.35,p≤0.10%,s≤0.1%,nb≤1.0%,余量为fe。加入行星式球磨机中进行球磨,加入无水酒精球磨55h,加入液体石蜡3.51%,采用滤纸过滤,后放入真空烘干炉烘干,真空度0.0001pa,烘干温度161℃,烘干时间43h,冷却至26℃出炉。利用600目的网筛进行筛选粉末,利用压样机进行压样,压制成辊身直径640mm,内孔460mm的试样,在抽真空至6
×
10-4
mpa的真空炉内进行烧结,先在395℃保温9.5h,然后以9.8℃/h的升温速率升温至1291℃烧结113min,以26℃/h降温速率降温至32℃出炉。内孔车削见光并预热至551℃后装入提前预留空间的砂型内,浇注低合金钢的芯部钢水,冷却至室温开箱,成型为轧辊。
42.实施例7
43.实施例7为对照例,成分与实施例6相同,为铸造方式生产的高速钢轧辊。
44.实施例8
45.实施例8为对照例,为常规高速钢轧辊。
46.取实施例1~实施例8产品进行试样拉伸力学性能检测,性能检测执行国家标准gb/t228.检测结果见表1。
47.表1实施例产品性能检测结果
[0048][0049]
通过对研制的粉末冶金轧辊进行性能测试,粉末冶金轧辊耐磨性高于常规高速钢,抗事故性明显高于常规高速钢工作辊。
[0050]
根据性能检测结果,研制的粉末冶金轧辊具有良好的耐磨性及抗事故性,在实际使用过程中,能较好适应后段尤其是成品机架甩钢的工况特点,适用于短流程轧线长辊役轧制特点,在机周期达到常规高镍铬工作辊的3倍以上,达到常规高速钢的1.6倍以上。
再多了解一些
本文用于企业家、创业者技术爱好者查询,结果仅供参考。