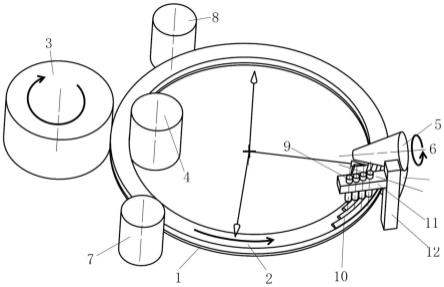
1.本发明涉及电弧熔丝增材制造和环件轧制成形领域,更具体地说,涉及一种大型环件多丝电弧增材同步制坯复合轧制成形方法。
背景技术:
2.随着我国航空航天、军工、能源等领域的不断发展,对关键构件大型化、整体化、高性能制造提出了更高需求。10米级以上超大型环件是火箭筒体、核反应堆加强圈、风电法兰、航空机匣、盾构机驱动环等大型装备的关键构件。大型环件目前主要采用热轧成形工艺生产,主要流程为:大型坯料铸造、整体加热、镦粗、冲孔、轧制成形,工艺流程较为复杂。大规格铸锭重量可超过100吨,受目前铸造技术限制,铸造难度大;大尺寸铸锭,冷却过程缓慢,芯部组织粗大,内部缺陷多,成分偏析严重;且传统的预铸造制坯-整体轧制依赖大型成套轧制设备,制坯、轧制过程工艺能耗高,严重制约了我国载人航天、能源领域关键构件的高性能、高效率生产。为了克服该问题,部分学者提出了分体制造-焊接拼装工艺和“构筑成形”工艺,但仍存在接头性能差、结合截面不良等问题。
3.电弧熔丝增材制造技术(wire and arc additive manufacturing,waam),以焊接电弧为热源,金属焊丝作为填充材料,通过逐点、逐道、逐层的材料精确受控堆积,实现金属零件的近净成形。相比于目前的激光、等离子、电子束等增材制造技术,电弧增材技术成形效率高,单丝可达6~15kg/h,设备造价低,自动化程度高,尤其适用于中大型构件的快速增材成形,已被应用于航空航天、军工、汽车、能源等领域关键构件的快速增材制造。然而,电弧增材制造工艺中材料在电弧热源作用下形成局部熔池,并随着焊枪迅速移动,熔体沿着固液界面梯度方向迅速凝固,易形成柱状晶,且局部熔池凝固、温度分布极不均匀形成了显著的残余拉应力,力学性能较差,限制了电弧增材制造技术的进一步推广应用。
技术实现要素:
4.本发明要解决的技术问题在于,提供一种大型环件多丝电弧增材同步制坯复合轧制成形方法,能够克服传统大型坯料整体铸造难、性能差的难题,且显著提高电弧增材环件的力学性能,实现大型环件的高性能、高效率、一体化成形。
5.本发明解决其技术问题所采用的技术方案是:构造一种大型环件多丝电弧增材同步制坯复合轧制成形方法,包括以下步骤:
6.s1、根据所成形环件底部壁厚度ds、内径rs,采用多块厚度hs=10~20mm厚的环形组件进行拼焊成形,制作环形支撑底板,环形支撑底板宽度与最终环件底部厚度一致;
7.s2、采用径-轴向成形轧机作为轧制设备,其包括主动辊、芯辊、上锥辊、下锥辊和两个导向辊,环形支撑底板上方并排布置多只多丝焊枪,多丝焊枪安装在横梁上,所述横梁与竖架连接;
8.s3、多丝电弧增材同步制坯复合轧制成形;将环形支撑底板置于轧环机驱动辊-芯辊、上锥辊-下锥辊之间,设置好轧环机驱动辊角速度w,环形支撑底板在各辊的驱动下旋
转;启动焊接电源,开始增材同步制坯;随着环形支撑底板的旋转,多丝焊枪在环形支撑底板上形成增材铺层;当增材铺层运动到上下锥辊之间时,受到锥辊的轴向碾压,发生一定的轴向压缩变形,且部分材料向两边流动;当增材铺层在环形支撑底板上旋转到驱动辊-芯辊位置时,受到径向碾压,发生一定的径向变形;随着轴向、径向的持续碾压,增材铺层发生连续的轴向、径向塑性变形;
9.s3、增材完成时,通过卧式车床铣削去掉环形支撑底板,制得成形的环件。
10.按上述方案,多丝焊枪采用多个焊接电源、送丝机分别驱动,在锥辊轴向成形前合适的位置架设竖架,竖架安装位置及锥辊位置到圆心夹角为α;在竖架上安装横梁,横梁与环件径向方向夹角为β,在横梁上并排安装多只焊枪;单条焊道厚度为hw,单条焊道宽度dw,焊枪数量为nw,相邻焊道搭接间距为η,各焊枪由内到外送丝速度分别为{f1,f2,
…
,fn};焊枪间距dg根据焊道宽度和搭接间距要求适当调整,保证dg
×
cos(β)=dw/2。
11.按上述方案,横梁在竖架上的安装方式为齿轮齿条驱动,并通过伺服电机、pcl控制器驱动,增材开始第一圈时,设置横梁向上匀速运动速度为vh=(hw/2)/(2π/w);后续保持横梁向上运动速度为vh=hw/(2π/w)。
12.按上述方案,在所述步骤s2中,由于环件外圈线速度快,内圈线速度慢,为了保证不同半径上增材焊道宽度的一致性,从而保证焊层较小的表面波纹度,设置各只焊枪的送丝速度不同;环件半径上由内到外的焊枪送丝速度比例应满足,f1:f2:f3:
…
:fn=(rr dw/2):(rr dw):(rr dw
×
3/2):
…
:(rr dw
×
n/2)。
13.按上述方案,在所述步骤s3中,驱动辊和芯辊的距离保持与环件最终尺寸相等,仅做旋转运动,不做径向运动,下锥辊高度保持不变,仅做旋转运动;上锥辊做旋转运动的同时,还做向上的轴向运动,环件每运动一圈,上锥辊向上匀速运动hw,焊枪横梁同步向上匀速运动hw;保证上锥辊与焊枪同步向上运动,从而实现连续的同步增材复合轧制,直到达到环件高度要求。增材层受到上锥辊的轴向碾压作用,局部高温区发生一定的压缩变形,且部分材料向两边流动。
14.按上述方案,在所述步骤s3中,在驱动辊-锥辊位置,已受到锥辊轴向碾压变形的部分在此处宽度大于驱动辊-锥辊间距,从而受到径向碾压作用,发生径向压缩变形,变形后的环件厚度与最终厚度保持一致。
15.按上述方案,在所述步骤s3中,顶部的多丝电弧增材层温度较高,约为400~700℃,塑性提高,在轴向、径向碾压作用下易发生变形,而底部温度降低至100~200℃,塑性降低,在连续成形过程中几乎不发生变形。
16.实施本发明的大型环件多丝电弧增材同步制坯复合轧制成形方法,具有以下有益效果:
17.1、本发明在径-轴向环件轧制成形机上安装多丝电弧增材焊枪,通过多丝电弧熔丝增材逐层制坯,通过轧机同步逐层碾压,逐层同步增材-径轴向碾压累积成形,克服传统大型坯料整体铸造难、性能差的难题,且电弧增材初始性能优于铸坯性能;
18.2、本发明通过径-轴向同步轧制,使增材层发生一定程度的塑形变形,细化晶粒,消除残余拉应力,显著提高电弧增材环件的力学性能,实现大型环件的高性能、高效率、一体化成形。
19.3、本发明通过多丝电弧增材同步制坯复合轧制连续成形,克服大型铸坯制备难问
题,多丝电弧增材同步制坯,省去传统镦粗、冲孔工艺,高效短流程;分层轧制碾压,而非传统整体轧制,减小变形抗力,降低设备要求;利用焊接余热进行轧制变形处理,省去传统加热工序,降低能耗。
附图说明
20.下面将结合附图及实施例对本发明作进一步说明,附图中:
21.图1是本发明大型环件多丝电弧增材同步制坯复合轧制成形方法的原理图;
22.图2是本发明的实施例所构建的环形支撑底板及分块拼焊示意图;
23.图3是本发明的实施例所构建的多丝增材焊枪安装位置与锥辊相对位置示意图;
24.图4是本发明的实施例所构建的焊枪安装横梁、竖架安装示意图;
25.图5是本发明的实施例所构建的上、下锥辊间增材层轴向变形示意图;
26.图6是本发明的实施例所构建的驱动辊、芯锥辊间增材层径向向变形示意图。
具体实施方式
27.为了对本发明的技术特征、目的和效果有更加清楚的理解,现对照附图详细说明本发明的具体实施方式。
28.本发明大型环件多丝电弧增材同步制坯复合轧制成形方法,包括以下步骤:
29.s1、增材支撑底板的制作。根据所成形环件底部壁厚度ds、内径rs,分多块采用激光、等离子或火焰切割厚度hs=10~20mm厚的环形组件,并进行拼焊成形,作为后续增材支撑基板,保证环形基板宽度与最终环件底部厚度一致。
30.s2、多丝增材焊枪的安装与布置。选用径-轴向成形轧机作为轧制设备,其主要成形构件包括主动辊、芯辊、上锥辊、下锥辊以及两个导向辊。采用多只熔化极气保焊枪并排布置,同时增材形成增材层,单条焊道厚度为hw,单条焊道宽度dw,焊枪数量为nw,相邻焊道搭接间距为η,各焊枪由内到外送丝速度分别为{f1,f2,
…
,fn},保证形成连续的铺层,覆盖基板或之前增材层,宽度不小于最终环件壁厚。
31.s3、多丝电弧增材同步制坯复合轧制成形。将环件支撑底板置于轧环机驱动辊-芯辊、上锥辊-下锥辊之间,设置好轧环机驱动辊角速度w,支撑底板能在各辊的驱动下旋转。设置好多丝增材焊接电源、送丝机参数,启动焊接电源,开始增材同步制坯。随着支撑底板的旋转,多丝焊枪在支撑底板上形成增材铺层。当增材铺层运动到上下锥辊之间时,受到锥辊的轴向碾压,发生一定的轴向压缩变形,且部分材料向两边流动。当增材层在支撑底板上旋转到驱动辊-芯辊位置时,受到径向碾压,发生一定的径向变形。随着轴向、径向的持续碾压,增材铺层发生连续的轴向、径向塑性变形,增材层的形貌和性能得到改善。环件增材旋转过程中,焊枪横梁及上锥辊连续向上移动,环件逐渐同步增材-碾压长高,直至达到预定高度。
32.步骤s2中,多丝焊枪采用多个焊接电源、送丝机分别驱动。在环件锥辊轴向成形前合适的位置架设焊枪焊装竖架,安装位置及锥辊位置到圆心夹角为α;在竖架上安装焊枪安装横梁,横梁与环件径向方向夹角为β,在横梁上并排安装多只焊枪,焊枪间距dg根据焊道宽度和搭接间距要求适当调整,保证dg
×
cos(β)=dw/2。
33.步骤s2中,横梁在竖架上的安装方式为齿轮齿条驱动,并通过伺服电机、pcl控制
器驱动。增材开始第一圈时,设置横梁向上匀速运动速度为vh=(hw/2)/(2π/w);后续保持横梁向上运动速度为vh=hw/(2π/w)。
34.步骤s2中,由于环件外圈线速度快,内圈线速度慢,为了保证不同半径上增材焊道宽度的一致性,从而保证焊层较小的表面波纹度,设置各只焊枪的送丝速度不同。环件半径上由内到外的焊枪送丝速度比例应满足,f1:f2:f3:
…
:fn=(rr dw/2):(rr dw):(rr dw
×
3/2):
…
:(rr dw
×
n/2)。
35.步骤s3中,驱动辊和芯辊的距离保持与环件最终尺寸相等,仅做旋转运动,不做径向运动。下锥辊高度保持不变,仅做旋转运动。上锥辊做旋转运动的同时,还做向上的轴向运动,环件每运动一圈,上锥辊向上匀速运动hw,焊枪横梁同步向上匀速运动hw。保证上锥辊与焊枪同步向上运动,从而实现连续的同步增材复合轧制,直到达到环件高度要求。增材层受到上锥辊的轴向碾压作用,局部高温区发生一定的压缩变形,且部分材料向两边流动。
36.步骤s3中,环件连同底部支撑板被驱动辊带动旋转,焊枪水平方向保持位置不变。
37.步骤s3中,同步增材轧制起始时刻,上下锥辊间的距离h0=hs。在后续连续成形过程中,增材层逐渐长高,上锥辊也连续向上运动,但上锥辊底部高度始终比增材层上表面低hw/2,即第1圈结束时,上锥辊高度为h1=hs 1*hw/2=22.0mm;第i圈结束时,上锥辊高度为hi=hs i*hw/2mm,从而保证上锥辊对增次层充分的碾压变形作用。
38.步骤s3中,在驱动辊-锥辊位置,已受到锥辊轴向碾压变形的部分在此处宽度大于驱动辊-锥辊间距,从而受到径向碾压作用,发生径向压缩变形,变形后的环件厚度与最终厚度保持一致。
39.步骤s3中,当前多丝电弧增材层温度较高,约为400~700℃,塑性提高,在轴向、径向碾压作用下易发生变形,而底部温度降低至100~200℃,塑性降低,在连续成形过程中几乎不发生变形,因此本发明中材料只发生连续的逐层塑性变形。
40.步骤s3中,环件底部支撑板宽度与环件宽度一致,起着支撑增材材料的作用,在连续同步增材轧制过程中与环件一起转动,当增材完成时,通过卧式车床铣削去掉。
41.实施例
42.本发明大型环件多丝电弧增材同步制坯复合轧制成形方法采用的设备,如图1所示,包括:环形增材支撑底板1、逐层成形环件2、驱动辊3、芯辊4、上锥辊5、下锥辊6、导向辊一7、导向辊二8、多丝增材焊枪9、增材层10、焊枪安装横梁11、焊枪安装竖架12。环件内径为5m,外径为5.06m,高度为0.03m,材料为316l不锈钢。
43.s1、增材支撑底板的制作。如图2所示,根据所成形环件底部壁厚度ds=0.06m、内径rs=2.5m,分8块采用激光、等离子或火焰切割厚度hs=20mm厚的环形组件,其材料为q235钢并进行拼焊成形,作为后续增材支撑基板,保证环形基板宽度与最终环件底部厚度一致。
44.s2、多丝增材焊枪的安装与布置。选用径-轴向成形轧机作为轧制设备,成形能力满足直径6m以上环件成形,其主要成形构件包括主动辊、芯辊、上锥辊、下锥辊以及两个导向辊。如图3所示,采用5支熔化极气保焊枪并排布置,同时增材形成增材层,单条焊道厚度为hw=4.0mm,单条焊道宽度dw=20.0mm,焊枪数量为nw=5,相邻焊道搭接间距为η=50%,各焊枪由内到外送丝速度分别为{f1=10.0m/min,f2=10.02m/min,f3=10.04m/min,f4=10.06m/min,f5=10.08m/min,},各枪送丝速度关系满足f1:f2:f3:
…
:fn=(rr dw/2):(rr
dw):(rr dw
×
3/2):
…
:(rr dw
×
n/2)。多丝增材保证形成连续的铺层,覆盖基板或之前增材层,宽度不小于最终环件壁厚。图3中α为焊枪安装位置与锥辊位置到圆心夹角,β为焊枪安装横梁与环件径向的夹角。
45.s3、多丝电弧增材同步制坯复合轧制成形。如图将环件支撑底板置于轧环机驱动辊-芯辊、上锥辊-下锥辊之间,设置好轧环机运动参数,驱动辊角速度w=0.002rad/s,驱动辊和芯辊间距drs=ds=60mm,支撑底板能在各辊的驱动下旋转,锥辊角度γ=35
°
。设置好多丝增材焊接电源、送丝机参数,启动焊接电源,焊丝材料牌号为er316l,焊接保护气采用82%ar 18%co2混合气,流量20l/min,开始增材同步制坯。随着支撑底板的旋转,多丝焊枪在支撑底板上形成增材铺层。当增材铺层运动到上下锥辊之间时,受到锥辊的轴向碾压,发生一定的轴向压缩变形,且部分材料向两边流动。当增材层在支撑底板上旋转到驱动辊-芯辊位置时,受到径向碾压,发生一定的径向变形。随着轴向、径向的持续碾压,增材铺层发生连续的轴向、径向塑性变形,增材层的形貌和性能得到改善。
46.步骤s2中,多丝焊枪采用多个焊接电源、送丝机分别驱动。如图4所示,在环件锥辊轴向成形前合适的位置架设焊枪焊装竖架,安装位置及锥辊位置到圆心夹角为α=25
°
;在竖架上安装焊枪安装横梁,横梁与环件径向方向夹角为β=50
°
,在横梁上并排安装多只焊枪,焊枪间距根据焊道宽度和搭接间距要求适当调整,保证dg
×
cos(β)=dw/2,dg=16mm。
47.步骤s2中,横梁在竖架上的安装方式为齿轮齿条驱动,并通过伺服电机、pcl控制器驱动。增材开始第一圈时,设置横梁向上匀速运动速度为vh=(hw/2)/(2π/w)=0.00065mm/s,后续设置横梁向上匀速运动速度为vh=hw/(2π/w)=0.0013mm/s。
48.步骤s3中,驱动辊和芯辊的距离保持与环件最终尺寸相等,仅做旋转运动,不做径向运动。下锥辊高度保持不变,仅做旋转运动。上锥辊做旋转运动的同时,还做向上的轴向运动,环件每运动一圈,上锥辊向上匀速运动hw,向上运动速度vz=vh=0.0013mm/s。保证上锥辊与焊枪同步向上运动,从而实现连续的同步增材复合轧制,直到达到环件高度要求。如图5所示,增材层受到上锥辊的轴向碾压作用,局部高温区发生一定的压缩变形,且部分材料向两边流动。图5中图中hi为上下锥辊间距离。
49.步骤s3中,环件连同底部支撑板被驱动辊带动旋转,焊枪水平方向保持位置不变。
50.步骤s3中,同步增材轧制起始时刻,上下锥辊间的距离h0=hs=20.0mm。在后续连续成形过程中,增材层逐渐长高,上锥辊也连续向上运动,但上锥辊底部高度始终比增材层上表面低hw/2,即第i圈结束时,上锥辊高度为hi=hs i*hw/2mm,从而保证上锥辊对增次层充分的碾压变形作用。
51.步骤s3中,在驱动辊-锥辊位置,如图6所示,已受到锥辊轴向碾压变形的部分在此处宽度大于驱动辊-锥辊间距,从而受到径向碾压作用,发生径向压缩变形,变形后的环件厚度与最终厚度保持一致。图中drs为驱动辊、芯辊间距离。
52.步骤s3中,当前多丝电弧增材层温度较高,约为400~700℃,塑性提高,在轴向、径向碾压作用下易发生变形,而底部温度降低至100~200℃,塑性降低,在连续成形过程中几乎不发生变形,因此本发明中材料只发生连续的逐层塑性变形。
53.步骤s3中,环件底部支撑板宽度与环件宽度一致,起着支撑增材材料的作用,在连续同步增材轧制过程中与环件一起转动,当增材完成时,通过卧式车床铣削去掉。
54.上面结合附图对本发明的实施例进行了描述,但是本发明并不局限于上述的具体
实施方式,上述的具体实施方式仅仅是示意性的,而不是限制性的,本领域的普通技术人员在本发明的启示下,在不脱离本发明宗旨和权利要求所保护的范围情况下,还可做出很多形式,这些均属于本发明的保护之内。
再多了解一些
本文用于企业家、创业者技术爱好者查询,结果仅供参考。