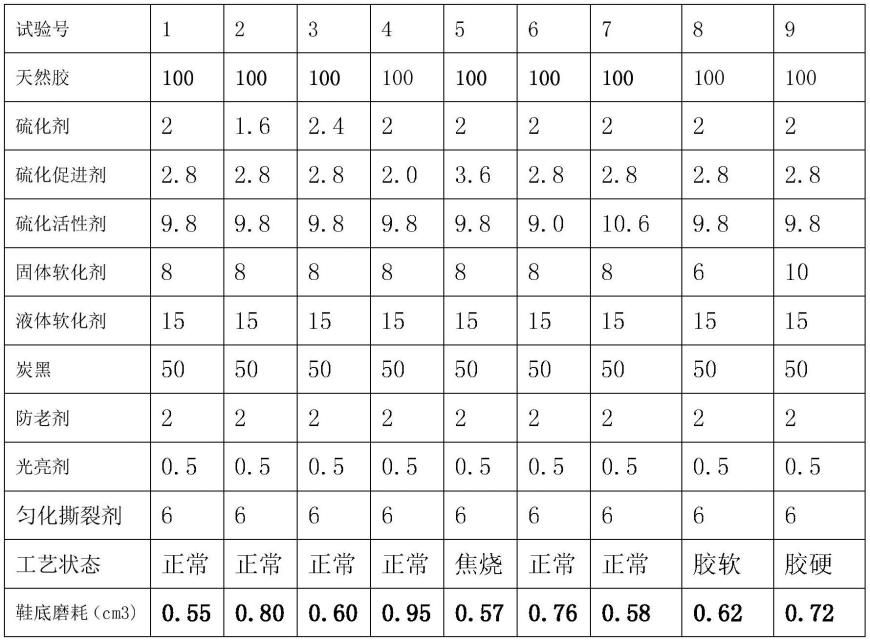
1.本发明涉及制鞋技术领域,特别是涉及一种模压鞋底边共用黑色橡胶及其制备方法与应用。
背景技术:
2.一般情况下,模压鞋外层胶部件由围条胶和大底胶两个部件组成。根据各部件性能需要,胶部件的特点也会有的不同。除一般橡胶特点外,围条橡胶的性能重点体现粘合牢度好、粘合强度高、耐屈折;而鞋底橡胶的突出性能则体现在高拉伸性能和耐磨耐折性能。
3.对于不同的部件性能侧重点,实现性能目标的途径均不相同,在生产管理过程中,每增加一个部件,工作的复杂程度就增加一倍。
4.影响鞋用胶料耐磨性能、拉伸性能、粘合性能的主要原因,包括胶料配方设计、胶料加工工艺和鞋底硫化工艺三种因素。
5.在胶料配方设计方面,在胶料中掺用塑料成份,可以降低产品与地面的摩擦阻力,增加耐磨性能,但掺用塑料成分会使橡胶产品的内在均匀性降低,产品拉伸性能能力降低,因此,在胶料中掺用塑料成分来提高橡胶的耐磨性能会导致拉伸强力及伸长率下降,综合性能偏低。还可以在胶料配方中加大合成橡胶的用量,随着合成橡胶的用量增加,橡胶的耐磨性能会有所提升,但由于合成橡胶的分子量分布较窄、分子较大的均匀性较强,而且合成橡胶有一定的半塑料性质,当其用量超过一定比例时,橡胶制品的抗湿滑能力降低,降低了胶鞋使用安全性。同时,胶料的表面粘性大幅度降低,引起胶鞋鞋边橡胶粘合效果差,使用价值降低。
6.随着生产效率提升需求增高。迫切需要简化模压鞋的制作难度,减少影响胶鞋外层胶料性能的因素,实现高效率生产高品质制作胶鞋目标。
技术实现要素:
7.本发明提供了一种模压鞋底边共用黑色橡胶及其制备方法与应用,它能解决现有模压鞋胶种共性差的问题,提高了胶料对鞋底的耐磨性能、拉伸性能、围条的粘合性能以及胶料耐折性能。
8.为了解决上述技术问题,本发明采用如下的技术方案:
9.一种模压鞋底边共用黑色橡胶,按照重量份计算,它包括下列原料制备而成:天然橡胶90~110份、硫化剂1.8~2.2份、硫化促进剂2.5~3.0份、硫化活性剂9.5~10份、固体软化剂7~9份、液体软化剂13~18份和炭黑48~52份及填充剂30~40份。
10.按照重量份计算,它包括下列原料制备而成:天然橡胶100份、硫化剂2份、硫化促进剂2.8份、硫化活性剂9.8份、固体软化剂8份、液体软化剂15份、炭黑50份及填充剂35份。
11.在所述原料中还加入防老剂1.5~2.5份、光亮剂0.3-0.7份及匀化撕裂剂5-7份。
12.优化地,按照重量份计算,它包括下列原料制备而成:天然橡胶100份、硫化剂2份、硫化促进剂2.8份、硫化活性剂9.8份、固体软化剂8份、液体软化剂15份、炭黑50份及填充剂
35份、防老剂2.0份、光亮剂0.5份、匀化撕裂剂6.0份。
13.所述的硫化促进剂是每2.8份硫化促进剂包括0.5份促进剂dm、1.5份促进剂cz和0.8份促进剂ds;所述的硫化活性剂是每9.8份硫化活性剂包括0.2份氧化镁、3.1份硬脂酸、5.5份纳米氧化锌和1.0份聚乙二醇4000#;所述的防老剂是每2份防老剂包括1.0份防老剂ky-405l和1份防老剂sp-c;所述固体软化剂是环保无味增粘树脂dt-100;所述液体软化剂是5%锭子油;所述填充剂是每35份填充剂包括10份白炭黑和25份陶土。
14.模压鞋底边共用黑色橡胶的制备方法,包括如下步骤:按上述质量份数取各组分;
15.(1)塑炼:取天然橡胶炼制至威氏可塑度为为0.50~0.60,制得塑炼胶;
16.(2)母炼:将炭黑与塑炼胶、固体软化剂及65~70%的液体软化剂加入到密炼机中母炼得a品;
17.(3)混炼:将a品投入炼胶机中在温度60~140℃、压力0.39~0.40mpa的条件下炼制0.5~1分钟后加入硫化促进剂、硫化活性剂及填充剂、继续炼制3’50”~4’20”,然后加入剩余的液体软化剂炼制均匀,排料到平机,降温,加入炼胶机补充翻炼、出片、水冷却、风干,停放,得硫化起点2’00
“‑2’
10”的得混炼胶,将混炼胶划片后冷却得b品;
18.(4)热炼及出型:将b品在40~60℃条件下热炼,加入硫磺再翻炼均匀后,裁切成鞋底和模压鞋围条胶料胚片;其中,鞋底胶片厚度7-8mm,围条胶片4.5-5mm。
19.胶料硫化起点使用硫化起点板在平板硫化机上测量,平板硫化机硫化温度为143℃、工作压力20mpa。
20.在步骤(3)的混炼过程中,将防老剂、光亮剂及匀化撕裂剂与硫化促进剂、硫化活性剂一同作为中料加入。
21.模压鞋底边共用黑色橡胶的应用,将胶料胚片贴合在刷浆已烘干的套帮模压鞋铁脚上在底模温度、边模温度145~155℃、铁脚楦温度140~145℃、工作压力20mpa的条件下硫化5.5~6分钟,制成橡胶模压鞋。
22.胶鞋部件性能检测方法执行国家或行业标准。
23.为了进一步验证本发明的效果,进行了如下实验:
24.实验例一、模压鞋底边共用黑色橡胶配方的研究
25.1、方法
26.1)配方:天然橡胶100份、硫化剂2.0份、硫化促进剂2.8份、硫化活性剂9.8份、固体软化剂8份、液体软化剂15份和炭黑50份、填充剂35份、防老剂2.0份、光亮剂0.5份、匀化撕裂剂6份。
27.试验号中进行变量。
28.2)模压鞋底边共用黑色橡胶的制备方法如下:
29.(1)塑炼:取天然橡胶炼制至威氏可塑度为为0.50~0.60,制得塑炼胶;
30.(2)母炼:将炭黑与塑炼胶、固体软化剂及65~70%的液体软化剂加入到密炼机中母炼得a品;
31.(3)混炼:将a品投入炼胶机中在温度60~140℃、压力0.39~0.40mpa的条件下炼制0.5~1分钟后加入中料(中料包括硫化促进剂、硫化活性剂、防老剂、光亮剂、匀化撕裂剂)、填充剂,继续炼制3’50”~4’20”,然后加入剩余的液体软化剂炼制均匀,排料到平机,降温,加入炼胶机补充翻炼、出片、水冷却、风干,停放,得硫化起点2
‘
00
“‑2’
10”的得混炼
胶,将混炼胶划片后冷却得b品;
32.(4)热炼及出型:将b品在40~60℃条件下热炼,加入硫磺、再翻炼均匀后,裁切成鞋底和模压鞋围条胶料胚片;其中,鞋底胶片厚度7-8mm,围条胶片4.5-5mm。
33.(5)硫化制作模压鞋:将胶料胚片贴合在刷浆已烘干的套帮模压鞋铁脚上在底模温度、边模温度145~155℃、铁脚楦温度140~145℃、工作压力20mpa的条件下硫化5.5~6分钟,制成橡胶模压鞋。
34.(6)按国标或行标检验胶鞋的鞋底性能和围条粘性能。
35.2、原料及设备
36.1)原料:天然橡胶、硫化剂、硫化促进剂、硫化活性剂、固体软化剂、液体软化剂、炭黑、防老剂和填充剂。
37.2)主要设备:75立升密炼机、模压机
38.3、实验数据
39.试验数据见表1和表2
40.表1
[0041][0042][0043]
表2
[0044][0045]
4、结论
[0046]
通过表1和表2得出,配方“天然橡胶100份、硫化剂2.0份、硫化促进剂2.8份、硫化活性剂9.8份、固体软化剂8份、液体软化剂15份和炭黑50份、填充剂35份、防老剂2.0份、光亮剂0.5份、匀化撕裂剂6份”物理性能最好。
[0047]
实验例二、制备方法的研究
[0048]
1、方法
[0049]
橡胶鞋底的制备一般分五个步骤:塑炼、母炼、混炼、裁切、硫化制作模压鞋,在此工艺中,母炼时间及模压条件是影响各种性能的主要参数。
[0050]
(1)天然橡胶塑炼可塑度研究:
[0051]
表3
[0052][0053]
通过表3试验数据得出,塑炼胶可塑度范围处于0.50~0.60之间,鞋底性能最好,围条粘合强度最佳。
[0054]
(2)母炼工艺研究
[0055]
表4
[0056]
混炼方式一段式混炼母炼(两段)式混炼炭黑分散效果差好鞋底磨耗cm3/1.61km0.750.55
[0057]
注:母炼式混炼即先将炭黑与塑炼胶、固体软化剂及65~70%的液体软化剂加入到密炼机中炼制得母炼胶,再将母炼胶与塑炼胶及其它材料混炼得混炼胶。
[0058]
通过表4得出,母炼胶制造工艺比一段式混炼工艺优越。
[0059]
(3)混炼工艺研究:
[0060]
表5混炼时间对性能的影响
[0061][0062]
[0063]
通过表5,可以得出,在混炼工艺中,加中料之前的母炼胶的合炼时间以0.5~1分钟为宜,而中料与补强剂的净压合时间处于3’50”~4’20”之间时,模压鞋的性能最好
[0064]
4、结论
[0065]
(1)模压鞋底边共用黑色橡胶的塑炼胶可塑度范围为0.50~0.60。
[0066]
(2)模压鞋底边共用黑色橡胶采用炭黑母炼胶工艺,才能保障耐磨性能。
[0067]
(3)混炼关键时间控制为加粗料及中料之前的母炼胶的合炼时间以0.5~1分钟为宜,而加粗料后的最佳净压合时间处于3’50”~4’20”。
[0068]
实验例三、硫化工艺的研究
[0069]
一、硫化工艺
[0070]
1、方法
[0071]
将模压鞋底边共用黑色橡胶,使用处于硫化温度下的模压鞋模具套帮硫化。研究硫化温度和硫化时间对鞋底性能及鞋边粘合强度的贡献。
[0072]
2.试验结果见表6。
[0073]
表6模压机硫化条件实验数据
[0074]
[0075][0076]
3、结论
[0077]
根据上表模压鞋硫化条件试验结果,模压鞋的硫化温度及时间对鞋底及鞋边性能有很大的影响,当底模具的硫化温度低于150℃或高于155℃时,胶鞋性能差,不能满足胶鞋外底的最佳性能要求。而鞋边模具温度处于145~150℃之间时,鞋边的粘合强度处于最好水平。因此,规定模压机的模具硫化温度最佳区域为:模压底模具温度150~155℃、模压鞋铁脚楦温度140-145℃、模压鞋边模模具温度为145-150℃,减少模具硫化温度对硫化鞋胶各项性能的影响,确保胶料的性能稳定、波动性较小。
[0078]
与现有技术相比,本发明提出了模压鞋底边共用黑色橡胶的胶料配方和制备方法,增强了橡胶自身的抗外力能力并提高了橡胶的拉伸强度、伸长率,确保了耐磨性能,该发明中的混炼胶在制造鞋底过程中具有硫化快速、工艺性能优良、操作简单等加工优点。本发明的模压鞋底边共用黑色橡胶的胶料中不掺用塑料成份,很好的保证了橡胶鞋底的穿着舒适性能。
具体实施方式
[0079]
模压鞋底边共用黑色橡胶配方实例及制备方法:
[0080]
1)配方:天然橡胶100份、硫化剂2.0份、硫化促进剂2.8份、硫化活性剂9.8份、固体软化剂8份、液体软化剂15份和炭黑50份、填充剂35份、防老剂2.0份、光亮剂0.5份、匀化撕裂剂6份。
[0081]
2)模压鞋底边共用黑色橡胶的制备方法如下:
[0082]
(1)塑炼:取天然橡胶炼制至威氏可塑度为为0.50~0.60,制得塑炼胶;
[0083]
(2)母炼:将炭黑与塑炼胶、固体软化剂及65~70%的液体软化剂加入到密炼机中母炼得a品;
[0084]
(3)混炼:将a品投入炼胶机中在温度60~140℃、压力0.39~0.40mpa的条件下炼制0.5~1分钟后加入中料(中料包括硫化促进剂、硫化活性剂、防老剂、光亮剂、匀化撕裂剂),填充剂、继续炼制3’50”~4’20”,然后加入剩余的液体软化剂炼制均匀,排料到平机,降温,加入炼胶机补充翻炼、出片、水冷却、风干,停放,得硫化起点2
‘
00
“‑2’
10”的得混炼胶,将混炼胶划片后冷却得b品;
[0085]
(4)热炼及出型:将b品在40~60℃条件下热炼,加入硫磺、再翻炼均匀后,裁切成鞋底和模压鞋围条胶料胚片;其中,鞋底胶片厚度7-8mm,围条胶片4.5-5mm。
[0086]
(5)硫化制作模压鞋:将胶料胚片贴合在刷浆已烘干的套帮模压鞋铁脚上在底模温度、边模温度145~155℃、铁脚楦温度140~145℃、工作压力20mpa的条件下硫化5.5~6分钟,制成橡胶模压鞋。
再多了解一些
本文用于企业家、创业者技术爱好者查询,结果仅供参考。