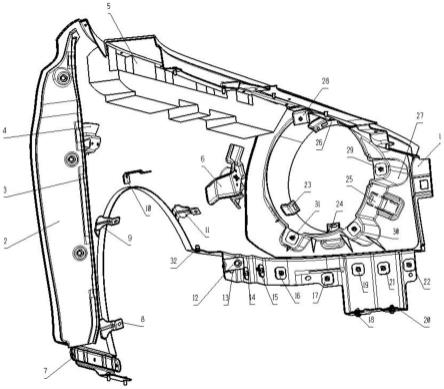
1.本发明属于前端覆盖件翼子板技术领域,具体涉及一种新型碳纤维复合材料翼子板。
背景技术:
2.现有技术中,如翼子板所属车型系国内自主具有重要历史意义车型时,造型师需要延续车身前部覆盖件的家族脸谱特征,此造型创意传统成型工艺无法满足零件质量要求,因此翼子板产品需要特殊的材质和工艺才能满足车身制件质量标准。
3.目前,金属钣金材质翼子板在中低端乘用车中被广泛应用,其成型工艺较为成熟,工艺缺陷控制手段多样,但钣金材质翼子板对造型自由度限制较大。此外,由于目前翼子板造型影响,前大灯安装极其困难,灯光调整空间不足,更无法保证与周边零件的间隙配合。
4.碳纤维材质翼子板属于复合材料产品,不同的结构胶牌号和不同碳纤维铺层(或碳纤维片材)都会实现不同的结构性能,刚度和强度都存有差异。此外,虽然碳纤维的抗拉强度和轻量化等方面性能优势明显,但由于目前碳纤维零件的成本较高,只有少数车型中采用,无法量产普及。国外少数豪华车在此类制品的应用多数应用于前后盖覆盖件中,翼子板多采用镁铝合金材质,而国内少数应用的车型尚属课题性研究或者展车、试制车状态,另外不同主机厂对表面强度以及局部固定点强度的要求不同,表面涂装质量的标准存在差异,因此造成碳纤维复合材料制品的结构胶牌号选取和碳纤维铺层(或碳纤维片材)方案选择,各有不同,成品零件的质量也存在较大的差异化。
5.现有技术公开了一种碳纤维翼子板,所述碳纤维翼子板为弧形板且自上向下逐渐向外延伸,所述碳纤维翼子板的前边沿自上向下逐渐向后延伸,所述碳纤维翼子板的后边沿自上向下逐渐向前延伸,所述碳纤维翼子板的下边沿自前向后逐渐向下延伸,所述碳纤维翼子板的上边沿自前向后逐渐向上延伸;所述碳纤维翼子板采用碳纤维增强环氧树脂复合材料,所述碳纤维翼子板包括依次层叠的四层结构,所述碳纤维翼子板的第一层和第四层采用第一种碳纤维预浸料织布,所述碳纤维翼子板的第二层和第三层采用第二种碳纤维预浸料织布,其中,所述第二种碳纤维预浸料织布的强度高于所述第一种碳纤维预浸料织布的强度。
6.现有技术还公开了一种碳纤维复合材料翼子板,包括翼子板本体,所述翼子板本体由碳纤维复合材料制成的一体化结构,所述翼子板本体前端表壁上设置有与汽车前保险杆连接的第一连接块,所述翼子板本体的底部设置有第二连接块,所述翼子板本体后端顶部设置有第三连接块,且第三连接块上开设有第二圆形孔洞。
7.但是,目前的机舱布置导致车灯无法固定在车身上,现有碳纤维复合材料翼子板并不能解决前灯和翼子板的安装问题。
技术实现要素:
8.本发明的目的就在于,提供一种新型碳纤维复合材料翼子板,以解决现有碳纤维
复合材料翼子板并不能解决前灯和翼子板的安装问题。
9.本发明的目的是通过以下技术方案实现的:
10.一种新型碳纤维复合材料翼子板,包括左前翼子板1,还包括与左前翼子板1固定的左前翼子板后部加强板2、用于安装左转向灯的左转向灯安装支架4、左前翼子板密封块5、用于安装旗杆总成的左前翼子板旗杆安装支架6、侧裙装饰板安装支架7、多个轮罩固定支架、多个前保险杠螺母板总成、用于安装左前大灯的左前大灯安装板27、多个用于固定左前大灯安装板27的左大灯面罩固定支架、与左前大灯安装板27固定的左前大灯支架总成28和多个前保险杠螺母板总成以及拉铆螺母32;所述左前翼子板1采用7层cfrp进行铺覆,左前翼子板1上旗杆固定点进行局部加厚增强,采用11层cfrp进行铺覆。
11.进一步地,所述左前翼子板后部加强板2粘接固定于左前翼子板1后部,左前翼子板后部加强板2的边缘处粘接前翼子板密封条3。
12.进一步地,所述左前翼子板密封块5粘接固定于左前翼子板1顶部。
13.进一步地,所述左前翼子板1靠近左前翼子板后部加强板2的位置粘接有左转向灯安装支架4。
14.进一步地,所述左前翼子板1中部装有左前翼子板旗杆安装支架6,所述旗杆固定座通过定位销插入左前翼子板旗杆安装支架6,此处翼子板局部铺层增厚,左前翼子板旗杆安装支架6通过结构胶与左前翼子板1粘接,旗杆固定座通过两个十字槽盘头螺钉固定在左前翼子板旗杆安装支架6上。
15.进一步地,所述左前翼子板1的左转向灯安装支架4一侧底部粘接固定侧裙装饰板安装支架7。
16.进一步地,所述左前翼子板1底部弧形边缘处还粘接轮罩固定支架
ⅰꢀ
8、轮罩固定支架
ⅱꢀ
9、轮罩固定支架
ⅲꢀ
10和轮罩固定支架
ⅳꢀ
11。
17.进一步地,所述左前翼子板1底部通过结构胶粘接固定前翼子板支架12、保险杠螺母板总成
ⅰꢀ
13、前保险杠螺母板总成
ⅱꢀ
14、前保险杠螺母板总成
ⅲꢀ
15、前保险杠螺母板总成
ⅳꢀ
16、前保险杠螺母板总成v 17、前保险杠螺母板总成vi 18、前保险杠螺母板总成vii 19、前保险杠螺母板总成viii 20、前保险杠螺母板总成ix 21和前保险杠螺母板总成
ⅹꢀ
22。
18.进一步地,所述左前翼子板1上还粘接固定有用于固定左前大灯安装板27的左大灯面罩固定支架i 23、左大灯面罩固定支架ii 24、左大灯面罩固定支架iii 25以及左大灯面罩定位支架26,左大灯面罩固定支架i 23、左大灯面罩固定支架ii 24、左大灯面罩固定支架iii 25以及左大灯面罩定位支架26与左前大灯安装板27卡接,左前大灯安装板27上通过螺栓连接左前大灯支架总成28。
19.进一步地,前大灯通过定位销插入左前大灯支架总成28,然后通过四个组合螺栓固定在左前大灯支架总成28上,左前大灯支架总成28通过结构胶与左前翼子板1粘接。所述左前大灯安装板27上通过螺栓连接前保险杠螺母板总成
ⅺꢀ
29、前保险杠螺母板总成
ⅻꢀ
30以及前保险杠螺母板总成xiii 31。
20.与现有技术相比,本发明的有益效果是:
21.本发明新型碳纤维复合材料翼子板,主体铺层结构基于各项同性的前提下进行设计,采用7层cfrp进行铺覆,旗杆固定点进行局部加厚增强,采用11层cfrp进行铺覆,前大灯
固定板采用专用框架与翼子板本体粘接,此外粘接若干固定支架对其他分装零件进行固定;在满足翼子板工艺成型和局部固定点强度的同时,解决前大灯及nvh隔热材料无法安装的难题,可以最大程度的满足造型自由度,实现翼子板降重45%左右,同时极大提升高端乘用车翼子板系统的装配难度和精度。
附图说明
22.为了更清楚地说明本发明实施例的技术方案,下面将对实施例中所需要使用的附图作简单地介绍,应当理解,以下附图仅示出了本发明的某些实施例,因此不应被看作是对范围的限定,对于本领域普通技术人员来讲,在不付出创造性劳动的前提下,还可以根据这些附图获得其他相关的附图。
23.图1是本发明翼子板结构示意图;
24.图2是本发明翼子板分解图;
25.表1是本发明翼子板整体碳纤维铺层方案;
26.表2是本发明翼子板旗杆固定结构铺层方案;
27.图3是本发明翼子板附件结构示意图;
28.图4是本发明旗杆装配结构示意图;
29.图5是本发明旗杆固定结构示意图;
30.图6是本发明前大灯固定结构示意图。
31.图中,1.左前翼子板 2.左前翼子板后部加强板 3.前翼子板密封条 4.左转向灯安装支架 5.左前翼子板密封块 6.左前翼子板旗杆安装支架 7.侧裙装饰板安装支架 8.轮罩固定支架
ⅰꢀ
9.轮罩固定支架
ⅱꢀ
10.轮罩固定支架
ⅲꢀ
11.轮罩固定支架
ⅳꢀ
12.前翼子板支架 13.前保险杠螺母板总成
ⅰꢀ
14.前保险杠螺母板总成
ⅱꢀ
15.前保险杠螺母板总成
ⅲꢀ
16.前保险杠螺母板总成
ⅳꢀ
17.前保险杠螺母板总成v 18.前保险杠螺母板总成vi 19.前保险杠螺母板总成vii 20.前保险杠螺母板总成viii 21.前保险杠螺母板总成ix 22.前保险杠螺母板总成
ⅹꢀ
23.左大灯面罩固定支架i 24.左大灯面罩固定支架ii 25.左大灯面罩固定支架iii 26.左大灯面罩定位支架 27.左前大灯安装板 28.左前大灯支架总成 29.前保险杠螺母板总成
ⅺꢀ
30.前保险杠螺母板总成
ⅻꢀ
31.前保险杠螺母板总成xiii 32.拉铆螺母。
具体实施方式
32.下面结合实施例对本发明作进一步说明:
33.下面结合附图和实施例对本发明作进一步的详细说明。可以理解的是,此处所描述的具体实施例仅仅用于解释本发明,而非对本发明的限定。另外还需要说明的是,为了便于描述,附图中仅示出了与本发明相关的部分而非全部结构。
34.应注意到:相似的标号和字母在下面的附图中表示类似项,因此,一旦某一项在一个附图中被定义,则在随后的附图中不需要对其进行进一步定义和解释。同时,在本发明的描述中,术语“第一”、“第二”等仅用于区分描述,而不能理解为指示或暗示相对重要性。
35.本发明新型碳纤维复合材料翼子板的主体铺层结构基于各项同性的前提下进行设计,采用7层cfrp进行铺覆,旗杆固定点进行局部加厚增强,采用11层cfrp进行铺覆,前大
灯固定板采用专用框架与左前翼子板1粘接,此外粘接若干固定支架对其他分装零件进行固定。
36.如图1所示,本发明新型碳纤维复合材料翼子板由左前翼子板1、左前翼子板后部加强板2、前翼子板密封条3、左转向灯安装支架4、左前翼子板密封块5、左前翼子板旗杆安装支架6、侧裙装饰板安装支架7、轮罩固定支架
ⅰꢀ
8、轮罩固定支架
ⅱꢀ
9、轮罩固定支架
ⅲꢀ
10、轮罩固定支架
ⅳꢀ
11、前翼子板支架12、前保险杠螺母板总成
ⅰꢀ
13、前保险杠螺母板总成
ⅱꢀ
14、前保险杠螺母板总成
ⅲꢀ
15、前保险杠螺母板总成
ⅳꢀ
16、前保险杠螺母板总成v 17、前保险杠螺母板总成vi 18、前保险杠螺母板总成vii 19、前保险杠螺母板总成viii 20、前保险杠螺母板总成ix 21、前保险杠螺母板总成
ⅹꢀ
22、左大灯面罩固定支架i 23、左大灯面罩固定支架ii 24、左大灯面罩固定支架iii 25、左大灯面罩定位支架 26、左前大灯安装板27、左前大灯支架总成28、前保险杠螺母板总成
ⅺꢀ
29、前保险杠螺母板总成
ⅻꢀ
30、前保险杠螺母板总成xiii 31以及拉铆螺母32构成。
37.所述左前翼子板后部加强板2粘接固定于左前翼子板1后部,左前翼子板后部加强板2的边缘处粘接前翼子板密封条3。
38.所述左前翼子板密封块5粘接固定于左前翼子板1顶部。
39.所述左前翼子板1靠近左前翼子板后部加强板2的位置粘接有左转向灯安装支架4,用于安装左转向灯。
40.如图4所示,所述左前翼子板1中部装有左前翼子板旗杆安装支架6。所述旗杆固定座通过定位销插入左前翼子板旗杆安装支架6,此处翼子板局部铺层增厚。如图5所示,左前翼子板旗杆安装支架6通过结构胶与左前翼子板1粘接,共同加强旗杆固定座固定点强度。旗杆固定座通过两个十字槽盘头螺钉固定在左前翼子板旗杆安装支架6上。
41.所述左前翼子板1的左转向灯安装支架4一侧底部粘接侧裙装饰板安装支架7。
42.所述左前翼子板1底部弧形边缘处还粘接轮罩固定支架
ⅰꢀ
8、轮罩固定支架
ⅱꢀ
9、轮罩固定支架
ⅲꢀ
10和轮罩固定支架
ⅳꢀ
11。
43.所述左前翼子板1底部还装有前翼子板支架12、保险杠螺母板总成
ⅰꢀ
13、前保险杠螺母板总成
ⅱꢀ
14、前保险杠螺母板总成
ⅲꢀ
15、前保险杠螺母板总成
ⅳꢀ
16、前保险杠螺母板总成v 17、前保险杠螺母板总成vi 18、前保险杠螺母板总成vii 19、前保险杠螺母板总成viii 20、前保险杠螺母板总成ix 21和前保险杠螺母板总成
ⅹꢀ
22,其均通过结构胶与左前翼子板1固定。
44.所述左前翼子板1上还通过粘接固定有用于固定左前大灯安装板27的左大灯面罩固定支架i 23、左大灯面罩固定支架ii 24、左大灯面罩固定支架iii 25以及左大灯面罩定位支架26,左大灯面罩固定支架i 23、左大灯面罩固定支架ii 24、左大灯面罩固定支架iii 25以及左大灯面罩定位支架26与左前大灯安装板27卡接,左前大灯安装板27上通过螺栓连接左前大灯支架总成28。如图6所示,前大灯通过定位销插入左前大灯支架总成28,然后通过四个组合螺栓固定在左前大灯支架总成28上,左前大灯支架总成28通过结构胶与左前翼子板1粘接。所述左前大灯安装板27上通过螺栓连接前保险杠螺母板总成
ⅺꢀ
29、前保险杠螺母板总成
ⅻꢀ
30以及前保险杠螺母板总成xiii 31。
45.所述左前翼子板1底部靠近前翼子板支架12的位置还通过拉铆连接拉铆螺母32。
46.本发明翼子板附件的分装顺序依次为前大灯、旗杆总成及左转向灯。
47.本发明新型碳纤维复合材料翼子板的整体碳纤维铺层方案,如表1所示。新型碳纤维复合材料翼子板的旗杆固定结构铺层方案,如表2所示。
48.翼子板附件的分装顺序依次为左前大灯,旗杆总成,左转向灯。
49.表1
[0050][0051][0052]
表2
[0053]
铺层材料材料类型厚度(mm)纤维方向密度(g/cm3)备注p001cfrp200gsm织物0.22 45/-451.5整铺层p002cfrp400gsm织物0.480/901.5整铺层p003cfrp300gsm织物0.30/901.5整铺层p004cfrp600gsm织物0.60/901.5局部铺层p005cfrp300gsm织物0.30/901.5局部铺层p006cfrp200gsm织物0.22 45/-451.5整铺层p007cfrp300gsm织物0.30/901.5局部铺层p008cfrp600gsm织物0.60/901.5局部铺层p009cfrp300gsm织物0.30/901.5整铺层p010cfrp400gsm织物0.480/901.5整铺层p011cfrp200gsm织物0.22 45/-451.5整铺层
[0054]
注意,上述仅为本发明的较佳实施例及所运用技术原理。本领域技术人员会理解,本发明不限于这里所述的特定实施例,对本领域技术人员来说能够进行各种明显的变化、重新调整和替代而不会脱离本发明的保护范围。因此,虽然通过以上实施例对本发明进行了较为详细的说明,但是本发明不仅仅限于以上实施例,在不脱离本发明构思的情况下,还可以包括更多其他等效实施例,而本发明的范围由所附的权利要求范围决定。
再多了解一些
本文用于企业家、创业者技术爱好者查询,结果仅供参考。