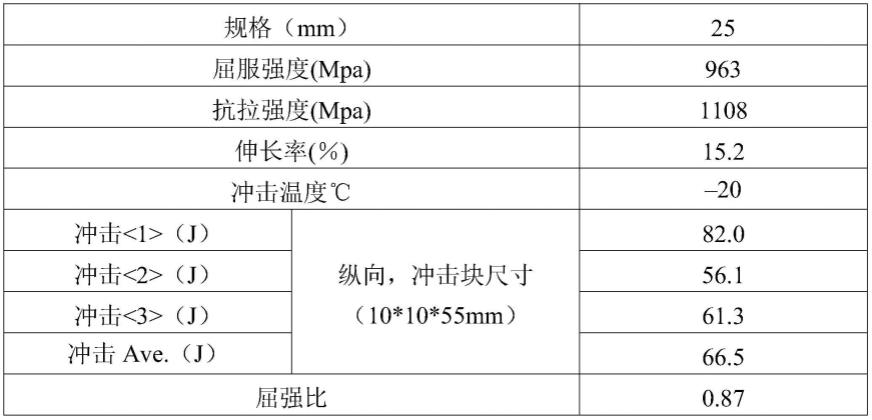
1.本发明涉及钢铁加工技术领域,尤其涉及一种耐磨耐蚀复合钢板的轧制工艺。
背景技术:
2.金属基复合板材的出现和发展,大大地改善及拓展了传统单一金属材料的性能及使用范围。金属基复合板材比传统的单一金属材料有更高的比张度、比刚度和比强度等;其是以一种金属作为基材,以另一种不同物理、化学性能的材料作为复材,并利用复合技术将其进行结合的一种新型复合板材。这对于我国缺乏镍、铬资源的国家来说有着重大意义和社会效益,随着冶金、化工等经济支柱性产业的迅速发展,如矿山机械、煤炭采运、石油化工、建材装饰、船舶工程等对耐磨材料复合板的需求倍增,如矿山机械用轨道、煤炭采用选煤机械、石油天然气输送管道及船体、结构件等,在复合耐磨钢板的生产过程中,钢板轧制是一项必不可少的工序。
3.针对现有技术存在以下问题:
4.1、双相复合板因形变速率不一样,轧制过程中中间坯复合厚度分配不合理,压下率分配不科学,导致界面之间很容易出现轧制过程中出现分层;
5.2、轧制完成后直接空冷,会造成应力释放不完全,钢板出现瓢曲;
6.3、淬火过程中由于耐磨钢是马氏体钢,冷却时相变带来剧烈的应变很容易出现瓢曲和复合板在界面处开裂;
7.4、淬火后到回火时间生产组织不及时,容易造成应力开裂以及瓢曲。
技术实现要素:
8.有鉴于此,本发明提供了一种耐磨耐蚀复合钢板的轧制工艺,能够解决现有技术中出现的分层、瓢曲以及开裂等问题。
9.本发明提供的耐磨耐蚀复合钢板的轧制工艺,包括以下步骤,
10.步骤一:将耐磨钢和耐蚀钢分别进行粗轧开坯,得到耐磨钢中间坯和耐蚀钢中间坯,所述耐磨钢中间坯和耐蚀钢中间坯的厚度比为1.7~1.9;
11.步骤二:将步骤一制备的耐磨钢中间坯和耐蚀钢中间坯在钢制保温罩中堆垛缓冷到室温,然后将冷却后的耐磨钢中间坯和耐蚀钢中间坯放置在垛板台上,采用霞普气火焰切割成相同尺寸;
12.步骤三:对步骤二中火切后的耐磨钢中间坯和耐蚀钢中间坯进行表面抛丸处理;
13.步骤四:将步骤三中抛丸处理后的耐磨钢中间坯和耐蚀钢中间坯在压平机的挤压下进行复合焊接,得到复合钢板;
14.步骤五:对步骤四的复合钢板进行加热处理;
15.步骤六:将步骤五加热处理后的复合钢板进行轧制;
16.步骤七:将步骤六轧制后的复合钢板进行缓冷,然后进行超声波探伤;
17.步骤八:探伤合格的钢板进入淬火炉加热后淬火,淬火后的钢板进行回火处理,对
回火后的钢板进行超声波探伤。
18.优选的,所述耐磨钢中的的化学成分质量百分比为c 0.20~0.25%,si 0.10~0.60%,mn 1.00~1.55%,p≤0.020%,s≤0.010%,als 0.010~0.030%,nb 0.010~0.045%,ti 0.010~0.020%,cr 0.5~0.8%,余量为fe和不可避免的杂质。
19.所述耐蚀钢中的元素成分为耐蚀钢的化学成分质量百分比为c 0.08~0.12%%,si 0.20~0.50%,mn 0.75~1.00%,p 0.07~0.15%,s≤0.015%,als 0.010~0.030%,nb 0.015~0.025%,ti 0.020~0.035%,cr 0.3~0.6%,cu 0.25~0.5%,ni 0.2~0.4%,余量为fe和不可避免的杂质。
20.优选的,步骤一所述粗轧开坯,得到厚度为180mm的耐磨钢中间坯和厚度为100mm的耐蚀钢中间坯。
21.优选的,步骤四所述压平机的压力大于1吨,进行复合焊接时钢板四个角要保留50mm不进行焊接。
22.优选的,步骤五所述加热的温度为1150-1200℃。
23.优选的,步骤六所述轧制包括粗轧和精轧;所述粗轧的开轧温度为1060-1120℃,轧制道次为9-12道次,单道次压下率≤20%;所述精轧的开轧温度在900-950℃,轧机轧辊冷却水流量设置为最大流量的1/2,终轧温度在820-850℃。
24.优选的,步骤七所述缓冷采用蒸汽保温箱进行缓冷,复合钢板进入蒸汽保温箱的温度≥350℃,蒸汽保温箱恒温100~150℃,缓冷时间12h-48h。以保证轧后钢板内应力能得到充分释放。缓冷温度和时间根据钢板厚度规格进行调整。其中厚度规格在14-16mm范围内,下线温度350℃,缓冷时间12小时;厚度规格在16mm~25mm范围内下线温度380℃,缓冷时间20小时;厚度规格在25mm~40mm范围内下线温度400℃,缓冷时间30小时;厚度规格在40mm~60mm范围,下线温度450℃,缓冷时间48小时。
25.优选的,步骤八所述淬火炉中的加热温度为900℃,加热时间为1.6mm*min,然后快速淬火至室温;淬火时耐磨钢在上表面,采用缝隙喷嘴冷却,冷却速度为43~50℃/s;耐蚀钢在下表面,采用高密喷嘴冷却,冷却速度为17~25℃/s。
26.优选的,步骤八所述回火的温度为300℃,加热时间为45min;所述回火与淬火的时间间隔≤2小时。
27.与现有技术相比,本发明具有以下有益效果:
28.本发明通过调整耐磨耐蚀复合钢板轧制工艺的步骤及参数,能够防止轧制过程中由于厚度分配不合理,压下率分配不科学导致的分层,以及轧后冷却过程中由于应变速率不匹配导致的复合板间开裂;同时能够解决钢板淬火过程中复合板界面处开裂,和淬火后放置时间较长,无法快速释放应力造成钢板瓢曲问题。
具体实施方式
29.下面结合实施例对本发明作进一步说明。
30.实施例1
31.一种耐磨耐蚀复合钢板的轧制工艺,步骤如下:
32.步骤一:将耐磨钢和耐蚀钢分别进行粗轧开坯,得到厚度为180mm的耐磨钢中间坯和厚度为100mm的耐蚀钢中间坯;
33.所述耐磨钢中的的化学成分质量百分比为c 0.23%,si 0.25%,mn 1.45%,p 0.008%,s 0.003%,als 0.027%,nb 0.035%,ti 0.016%,cr 0.68%,余量为fe和不可避免的杂质。
34.所述耐蚀钢中的元素成分为耐蚀钢的化学成分质量百分比为c 0.11,si 0.23%,mn 0.92%,p 0.09%,s 0.005%,als 0.025%,nb 0.020%,ti 0.029%,cr 0.53%,cu 0.41%,ni 0.35%,余量为fe和不可避免的杂质;
35.步骤二:将步骤一制备的耐磨钢中间坯和耐蚀钢中间坯在钢制保温罩中堆垛缓冷到室温,然后将冷却后的耐磨钢中间坯和耐蚀钢中间坯放置在垛板台上,采用霞普气火焰切割成相同尺寸;
36.步骤三:对步骤二中火切后的耐磨钢中间坯和耐蚀钢中间坯进行表面抛丸处理;
37.步骤四:将步骤三中抛丸处理后的耐磨钢中间坯和耐蚀钢中间坯放置在压平机上,调整压平机的压力为1吨,挤压进行复合焊接,复合焊接时钢板四个角要保留50mm不进行焊接,得到复合钢板;
38.步骤五:对步骤四的复合钢板进行加热处理,加热温度为1180℃;
39.步骤六:将步骤五加热处理后的复合钢板进行轧制;所述轧制包括粗轧和精轧;所述粗轧的开轧温度为1095℃,轧制道次为12道次;所述精轧的开轧温度在930℃,轧机轧辊冷却水流量设置为最大流量的1/2,终轧温度在825℃;得到的钢板厚度为25mm;
40.步骤七:将步骤六轧制后的复合钢板采用蒸汽保温箱进行缓冷,复合钢板进入蒸汽保温箱的温度为390℃,蒸汽保温箱恒温120℃,缓冷时间20h,然后进行超声波探伤;
41.步骤八:探伤合格的钢板进入淬火炉900℃加热1.6mm*min,然后快速淬火至室温,淬火时耐磨钢在上表面,采用缝隙喷嘴冷却,冷却速度为46℃/s;耐蚀钢在下表面,采用高密喷嘴冷却,冷却速度为22℃/s;淬火后的钢板进行回火处理,回火的温度为300℃,加热时间为45min;所述回火与淬火的时间间隔1小时,最后对回火后的钢板进行超声波探伤。
42.实施例2
43.一种耐磨耐蚀复合钢板的轧制工艺,步骤如下:
44.步骤一:将耐磨钢和耐蚀钢分别进行粗轧开坯,得到厚度为180mm的耐磨钢中间坯和厚度为100mm的耐蚀钢中间坯;
45.所述耐磨钢中的化学成分质量百分比为c 0.24%,si 0.15%,mn 1.20%,p 0.010%,s 0.002%,als 0.020%,nb 0.030%,ti 0.012%,cr 0.59%,余量为fe和不可避免的杂质。
46.所述耐蚀钢中的元素成分为耐蚀钢的化学成分质量百分比为c 0.09,si 0.26%,mn 0.86%,p 0.085%,s 0.005%,als 0.013%,nb 0.021%,ti 0.030%,cr 0.45%,cu 0.42%,ni 0.32%,余量为fe和不可避免的杂质;
47.步骤二:将步骤一制备的耐磨钢中间坯和耐蚀钢中间坯在钢制保温罩中堆垛缓冷到室温,然后将冷却后的耐磨钢中间坯和耐蚀钢中间坯放置在垛板台上,采用霞普气火焰切割成相同尺寸;
48.步骤三:对步骤二中火切后的耐磨钢中间坯和耐蚀钢中间坯进行表面抛丸处理;
49.步骤四:将步骤三中抛丸处理后的耐磨钢中间坯和耐蚀钢中间坯放置在压平机上,调整压平机的压力为1.2吨,挤压进行复合焊接,复合焊接时钢板四个角要保留50mm不
进行焊接,得到复合钢板;
50.步骤五:对步骤四的复合钢板进行加热处理,加热温度为1160℃;
51.步骤六:将步骤五加热处理后的复合钢板进行轧制;所述轧制包括粗轧和精轧;所述粗轧的开轧温度为1080℃,轧制道次为10道次;所述精轧的开轧温度在910℃,轧机轧辊冷却水流量设置为最大流量的1/2,终轧温度在820℃;得到的钢板厚度为35mm;
52.步骤七:将步骤六轧制后的复合钢板采用蒸汽保温箱进行缓冷,复合钢板进入蒸汽保温箱的温度为400℃,蒸汽保温箱恒温150℃,缓冷时间30h,然后进行超声波探伤;
53.步骤八:探伤合格的钢板进入淬火炉900℃加热1.6mm*min,然后快速淬火至室温,淬火时耐磨钢在上表面,采用缝隙喷嘴冷却,冷却速度为50℃/s;耐蚀钢在下表面,采用高密喷嘴冷却,冷却速度为25℃/s;淬火后的钢板进行回火处理,回火的温度为300℃,加热时间为45min;所述回火与淬火的时间间隔0.5小时,最后对回火后的钢板进行超声波探伤。
54.实施例3
55.一种耐磨耐蚀复合钢板的轧制工艺,步骤如下:
56.步骤一:将耐磨钢和耐蚀钢分别进行粗轧开坯,得到厚度为180mm的耐磨钢中间坯和厚度为100mm的耐蚀钢中间坯;
57.所述耐磨钢中的化学成分质量百分比为c 0.25%,si 0.26%,mn 1.50%,p 0.005%,s 0.003%,als 0.022%,nb 0.040%,ti 0.018%,cr 0.66%,余量为fe和不可避免的杂质。
58.所述耐蚀钢中的元素成分为耐蚀钢的化学成分质量百分比为c 0.10%,si 0.25%,mn 0.75%,p 0.07%,s 0.005%,als 0.023%,nb 0.018%,ti 0.025%,cr 0.36%,cu 0.29%,ni 0.32%,余量为fe和不可避免的杂质;
59.步骤二:将步骤一制备的耐磨钢中间坯和耐蚀钢中间坯在钢制保温罩中堆垛缓冷到室温,然后将冷却后的耐磨钢中间坯和耐蚀钢中间坯放置在垛板台上,采用霞普气火焰切割成相同尺寸;
60.步骤三:对步骤二中火切后的耐磨钢中间坯和耐蚀钢中间坯进行表面抛丸处理;
61.步骤四:将步骤三中抛丸处理后的耐磨钢中间坯和耐蚀钢中间坯放置在压平机上,调整压平机的压力为1.5吨,挤压进行复合焊接,复合焊接时钢板四个角要保留50mm不进行焊接,得到复合钢板;
62.步骤五:对步骤四的复合钢板进行加热处理,加热温度为1200℃;
63.步骤六:将步骤五加热处理后的复合钢板进行轧制;所述轧制包括粗轧和精轧;所述粗轧的开轧温度为1120℃,轧制道次为9道次,单道次压下率为20%;所述精轧的开轧温度在900℃,轧机轧辊冷却水流量设置为最大流量的1/2,终轧温度在835℃;得到的钢板厚度为45mm;
64.步骤七:将步骤六轧制后的复合钢板采用蒸汽保温箱进行缓冷,复合钢板进入蒸汽保温箱的温度为420℃,蒸汽保温箱恒温150℃,缓冷时间48h,然后进行超声波探伤;
65.步骤八:探伤合格的钢板进入淬火炉900℃加热1.6mm*min,然后快速淬火至室温,淬火时耐磨钢在上表面,采用缝隙喷嘴冷却,冷却速度为50℃/s;耐蚀钢在下表面,采用高密喷嘴冷却,冷却速度为25℃/s;淬火后的钢板进行回火处理,回火的温度为300℃,加热时间为45min;所述回火与淬火的时间间隔0.5小时,最后对回火后的钢板进行超声波探伤。
66.对本技术实施例1制备的复合钢板进行性能测试,结果为如表1:
67.表1
[0068][0069]
以上所述仅是本发明的优选实施方式,应当指出,对于本技术领域的普通技术人员来说,在不脱离本发明原理的前提下,还可以做出若干改进和润饰,这些改进和润饰也应视为本发明的保护范围。
再多了解一些
本文用于企业家、创业者技术爱好者查询,结果仅供参考。