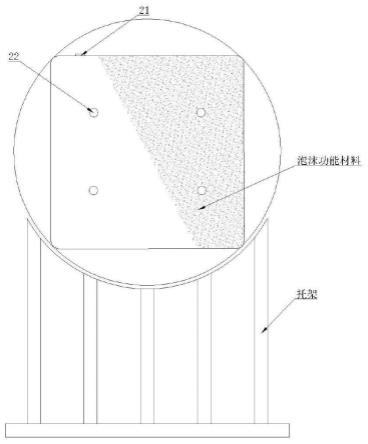
1.本发明属于复合材料技术领域,具体涉及二氧化铀芯块粉末运输装备用泡沫功能材料的制备方法。
背景技术:
2.转运二氧化铀芯块或粉末的运输装备外形接近正方体、内部设有4个分离式同尺寸结构单元,作为存放芯块或粉末罐的容置空间。该运输装备分为呈凹凸配合结构的盖体和本体两部分,盖体通过螺栓与本体锁紧,如图4和图5所示,装备长1020mm,宽1020mm,高1050mm。
3.该运输装备通常由薄壁金属外层(钢板厚度为2.5~3mm)和导热系数较低的非金属材料内层组成,金属外层通常具有空腔,金属外层上预留排气孔,以利于在严重的事故情况下(在装备外部温度900℃的真火火焰包裹下,持续35min,期间,内部温度不允许超过150℃)低导热系数非金属材料分解的小分子物质逃逸,避免因内压过大致使装备解体破裂。根据技术规范,运输装备内的非金属材料通常的密度要求为0.25
±
5%(g/cm3),盖体空腔内泡沫质量为21.88
±
1.1kg,本体空腔内泡沫质量为165.6
±ꢀ
8.3kg。
4.目前,常规的低导热系数非金属材料无法实现在焊装成整体的空腔金属壳体内部安装,如果先安装低导热系数非金属材料,后焊装金属壳体,一方面焊装时的高温损坏非金属材料,另一方面焊装后金属壳体如有漏点不能被及时检出,影响设备安全性和服役寿期。提供一种可在空腔内部均均匀分布且无缺料、空洞等缺陷的低导热系数非金属材料,是解决壳体内、外表面鼓胀、金属外层和非金属材料难以装配等问题的重要途径之一。
技术实现要素:
5.本发明所要解决的技术问题在于针对上述现有技术的不足,提供一种二氧化铀芯块粉末运输装备用泡沫功能材料的制备方法。本发明通过分别提供a料、b料和c料、将内支撑工装和外支撑工装安装于运输装备上、分三阶段向装备本体填充泡沫功能材料以及向装备盖体填充泡沫功能材料的方法,实现二氧化铀芯块粉末运输装备中填充泡沫功能材料,该泡沫功能材料在装备各腔体中分布均匀,满足材料密度指标和装备性能技术要求,该填充有泡沫功能材料的运输装备在严重事故测试中仍能满足二氧化铀芯块或粉末零外露的指标,满足40年服役期限安全性要求。
6.为解决上述技术问题,本发明采用的技术方案是:一种二氧化铀芯块粉末运输装备用泡沫功能材料的制备方法,其特征在于,所述二氧化铀芯块粉末运输装备包括装备本体和装备盖体,所述装备盖体可拆卸安装于装备本体上;
7.所述装备本体包括室腔以及合围形成所述室腔的侧壁面和底壁面,所述侧壁面和底壁面均为中空结构,所述侧壁面的中空腔体与底壁面的中空腔体连通;所述室腔包括四个腔室以及将所述室腔分隔成四个所述腔室的隔断件,所述隔断件为中空结构,所述隔断件的中空腔体与侧壁面的中空腔体和底壁面的中空腔体均连通;所述装备盖体内设置有盖
体空腔;
8.所述侧壁面上开设有第一排气孔,所述第一排气孔与侧壁面的中空腔体连通,所述底壁面上开设有第二排气孔,所述第二排气孔与底壁面的中空腔体连通,所述装备盖体上开设有第三排气孔,所述第三排气孔与盖体空腔连通;
9.所述制备方法包括:
10.步骤一、分别提供a料、b料和c料;
11.步骤二、将内支撑工装装入室腔,将所述装备盖体安装于装备本体上,将装有内支撑工装的二氧化铀芯块粉末运输装备装入外支撑工装,得到带工装的装备;
12.步骤三、将a料、b料和c料混合,得到混合液体料,分三个阶段向装备本体内导入混合液体料,生成泡沫功能材料,实现充填;
13.步骤四、向装备盖体内导入混合液体料,生成泡沫功能材料,完成充填。
14.上述的二氧化铀芯块粉末运输装备用泡沫功能材料的制备方法,其特征在于,步骤一中,所述a料为将a组原料经搅拌预混和强化分散后,得到的a料;所述搅拌预混的温度和强化分散的温度均为40℃~50℃;
15.所述a组原料包括:聚醚多元醇ⅱ、聚酯多元醇、阻燃剂、发泡剂、催化剂和氯离子固定浆剂;所述聚醚多元醇ⅱ的平均羟值为280 mgkoh/g~340mgkoh/g,黏度为900mpa.s/25℃~1700mpa.s/25℃;所述聚酯多元醇的平均羟值为390mgkoh/g~410mgkoh/g,黏度为1.3pa.s/25℃;所述阻燃剂为乙基膦酸二乙酯、三亚磷酸酯、三聚氰胺、聚磷酸铵、硫化钪和膨胀蛭石粉的组合物;所述发泡剂为去离子水;所述催化剂为二二丁基锡、二月桂酸二丁基锡、油酸钾、钛酸四丁酯和四丁基氯化铵的组合物;
16.所述聚醚多元醇ⅱ、聚酯多元醇、阻燃剂、发泡剂、催化剂和氯离子固定浆剂的质量比为(40~54):(10~20):(43~49):(0.2~0.4): (3.5~4.1):(2~3)。
17.上述的二氧化铀芯块粉末运输装备用泡沫功能材料的制备方法,其特征在于,步骤一中,所述b料为将b组原料经搅拌预混和强化分散后,得到的b料;所述b组原料包括聚醚多元醇ⅰ和环氧树脂;所述聚醚多元醇ⅰ的平均羟值为480mgkoh/g~500mgkoh/g,黏度为6500 mpa.s/25℃~9500mpa.s/25℃;所述搅拌预混的温度和强化分散的温度均为 60℃~70℃;所述环氧树脂为双酚a型环氧树脂,所述环氧树脂的黏度< 3000mpa
·
s/40℃;所述聚醚多元醇ⅱ的质量为聚醚多元醇ⅰ质量的2倍;所述聚醚多元醇ⅰ质量为环氧树脂质量的1倍~2.7倍。
18.上述的二氧化铀芯块粉末运输装备用泡沫功能材料的制备方法,其特征在于,步骤一中,所述c料为将c组原料经搅拌预混,得到的c料;所述搅拌预混的温度为40℃~50℃;所述c组原料包括聚合mdi和4,4'
‑ꢀ
二环己基甲烷二异氰酸酯,所述聚合mdi平均官能度为2.9~3.0,所述4, 4'-二环己基甲烷二异氰酸酯的官能度为2;所述聚合mdi质量为4,4'-二环己基甲烷二异氰酸酯质量的4倍;所述聚合mdi质量为聚酯多元醇质量的7倍~14倍。
19.上述的二氧化铀芯块粉末运输装备用泡沫功能材料的制备方法,其特征在于,步骤二中,所述内支撑工装包括内支撑工装第一本体和内支撑工装第二本体,所述内支撑工装第二本体的数量为多个,多个所述内支撑工装第二本体呈辐射状相邻排列于内支撑工装第一本体周围,多个所述内支撑工装第二本体形成的辐射中心与内支撑工装第一本体中心重合。
20.上述的二氧化铀芯块粉末运输装备用泡沫功能材料的制备方法,其特征在于,步骤二中,所述外支撑工装包括可套设于二氧化铀芯块粉末运输装备上的外支撑工装本体,所述外支撑工装本体外套设有可供固定外支撑工装本体和二氧化铀芯块粉末运输装备的钢索锁紧系统。
21.上述的二氧化铀芯块粉末运输装备用泡沫功能材料的制备方法,其特征在于,步骤三中分三个阶段向装备本体内导入混合液体料,生成泡沫功能材料,实现充填,具体包括:
22.步骤301、调整至二氧化铀芯块粉末运输装备底壁面竖直向上,将混合料液导入混合料液导入口,静置至混合料液填满侧壁面中空腔室和隔断件的中空腔体,完成第一阶段充填;
23.步骤302、调整使所述带工装的装备的底壁面垂直于地面,旋转调整带工装的装备,向底壁面的中空腔体中充填所述混合料液,至半满,静置;
24.步骤303、将带工装的装备逆时针旋转120
°
,向底壁面的中空腔体中继续充填所述混合料液,静置,完成装置本体的充填。
25.上述的二氧化铀芯块粉末运输装备用泡沫功能材料的制备方法,其特征在于,步骤301中,混合料液导入口为侧壁面上靠近底壁面的第一排气孔。
26.上述的二氧化铀芯块粉末运输装备用泡沫功能材料的制备方法,其特征在于,步骤302中,旋转调整带工装的装备后,底壁面靠近地面的底角的对角线与地面夹角为30~40
°
。
27.上述的二氧化铀芯块粉末运输装备用泡沫功能材料的制备方法,其特征在于,步骤303中向底壁面的中空腔体中继续充填所述混合料液为经底壁面上未填充区域且距离地面最远的第二排气孔进行充填。
28.所述份可以为克、两、斤、公斤、吨等重量计量单位。
29.本发明与现有技术相比具有以下优点:
30.1、本发明通过分别提供a料、b料和c料、将内支撑工装和外支撑工装安装于运输装备上、分三阶段向装备本体填充泡沫功能材料以及向装备盖体填充泡沫功能材料的方法,实现二氧化铀芯块粉末运输装备中填充泡沫功能材料,该泡沫功能材料在装备各腔体中分布均匀,满足材料密度指标和装备性能技术要求,该填充有泡沫功能材料的运输装备在严重事故测试中仍能满足二氧化铀芯块或粉末零外露的指标,满足40年服役期限安全性要求。
31.2、在内、外支撑工装作用下,既实现了泡沫材料的均匀布置,又有效解决了薄壁、大面积鼓胀问题,使二氧化铀芯块粉末运输装备内部尺寸合理,不影响元件或粉末桶的存储出入,使二氧化铀芯块粉末运输装备外部规整、美观,便于批量运输时整齐码放。
32.3、本发明原理可靠,利于推广应用。
33.下面结合附图和实施例,对本发明的技术方案做进一步的详细描述。
附图说明
[0034][0035]
图1为二氧化铀芯块粉末运输装备的结构示意图。
[0036]
图2为室腔结构示意图。
[0037]
图3为第一侧壁面结构示意图。
[0038]
图4为第二侧壁面结构示意图。
[0039]
图5为內支撑工装与室腔配合示意图。
[0040]
图6为內支撑工装结构示意图。
[0041]
图7为内支撑工装第一本体结构示意图。
[0042]
图8为内支撑工装第一本体与内支撑工装第二本体配合关系示意图。
[0043]
图9为二氧化铀芯块粉末运输装备和外支撑工装的装配示意图。
[0044]
图10为步骤二中所述装备的形态示意图。
[0045]
图11为步骤303中带工装的装备在托架上的位置关系示意图。
[0046]
图12为步骤304带工装的装备在托架上的位置关系示意图。
[0047]
图13为步骤四中带工装的装备在托架上的位置关系示意图。
具体实施方式
[0048]
实施例1
[0049]
本实施例提供一种二氧化铀芯块粉末运输装备用泡沫功能材料的制备方法,所述二氧化铀芯块粉末运输装备包括装备本体和装备盖体5,所述装备盖体5可拆卸安装于装备本体上;
[0050]
如图1~4所示,所述装备本体包括室腔1以及合围形成所述室腔1的侧壁面2和底壁面3,所述侧壁面2和底壁面3均为中空结构,所述侧壁面2的中空腔体与底壁面3的中空腔体连通;所述室腔1包括四个腔室以及将所述室腔1分隔成四个所述腔室的隔断件4,所述隔断件4为中空结构,所述隔断件4的中空腔体与侧壁面2的中空腔体和底壁面3的中空腔体均连通;所述隔断件的截面形状为十字型;所述装备盖体5内设置有盖体空腔;
[0051]
所述侧壁面2上开设有第一排气孔21,所述第一排气孔21与侧壁面 2的中空腔体连通,所述底壁面3上开设有第二排气孔22,所述第二排气孔22与底壁面3的中空腔体连通,所述装备盖体5上开设有第三排气孔 23,所述第三排气孔23与盖体空腔连通;
[0052]
所述侧壁面2包括合围形成室腔1且依次连接的第一侧壁面24、第二侧壁面25、第三侧壁面和第四侧壁面,所述第一侧壁面24和第三侧壁面上的第一排气孔21数量均为5个,所述第二侧壁面25和第四侧壁面上的第一排气孔21数量均为3个,3个所述第一排气孔21中,2个间隔设置于相应侧壁面的中部,另外1个设置于相应侧壁面的下部且位于2个间隔设置的第一排气孔21中间,位于相应侧壁面的下部的所述1个第一排气孔21正对隔断件4与相应侧壁面的连通处,5个所述第一排气孔21分为两组,第一组中的第一排气孔21数量为3个,第二组中的第一排气孔21 数量为2个,第一组中的3个所述第一排气孔21中,2个间隔设置于相应侧壁面的中部,另外1个设置于相应侧壁面的下部且位于2个间隔设置的第一排气孔21中间,位于相应侧壁面的下部的所述1个第一排气孔21正对隔断件4与相应侧壁面的连通处,第二组中的2个第一排气孔21间隔且位于第一组的3个第一排气孔21的下方;位于相应侧壁面的下部的1 个第一排气孔21临近底壁面3,处于侧壁面2、底壁面3和隔断件4的交汇处;
[0053]
所述第二排气孔22的数量为4个,4个所述第二排气孔22沿底壁面 3中心均匀分布
于底壁面3上;所述第三排气孔23的数量为4个,4个所述第三排气孔23沿装备盖体5中心均匀分布于装备盖体5上;向所述二氧化铀芯块粉末运输装备提供的泡沫功能材料密度为0.26g/cm3;
[0054]
所述制备方法包括:
[0055]
步骤一、分别提供a料、b料和c料,具体包括:
[0056]
步骤101、43℃~48℃温度条件下,将a组原料搅拌预混后强化分散 0.5h,得到a料;所述强化分散为经超精细研磨泵进行强化分散,所述43℃~48℃温度条件为搅拌预混和强化分散过程中保持的物料温度;所述a组原料包括a组原料i和a组原料ii,所述搅拌预混为在搅拌器转速为 1800r/min条件下将a组原料i搅拌105min~110min后加入a组原料ii继续搅拌10min~15min;
[0057]
所述a组原料i包括:质量比为46.7:20:20:6:5:5:3:2.5:0.5: 0.3:0.1:0.2:2的聚醚多元醇ⅱ、聚酯多元醇、乙基膦酸二乙酯、三聚氰胺、聚磷酸铵、硫化钪、膨胀蛭石粉、二十二烷基硫二丁基锡、二月桂酸二丁基锡、油酸钾、钛酸四丁酯、去离子水和氯离子固定浆剂;
[0058]
所述a组原料ii包括:质量比为10:0.1的三一缩二丙二醇亚磷酸酯和四丁基氯化铵,所述三一缩二丙二醇亚磷酸酯与聚醚多元醇ⅱ的质量比为10:46.7;
[0059]
所述氯离子固定浆剂为由硝酸银粉末、粘合剂、溶剂和助剂组成的浆液,其中硝酸银过筛3000目,所述氯离子固定浆剂中硝酸银含量为 60%~70%;所述粘合剂为环氧树脂,所述溶剂为异佛尔酮,所述助剂为 peg-200;所述聚醚多元醇ⅱ的平均羟值为280mgkoh/g~340mgkoh/g,黏度为900mpa.s/25℃~1700mpa.s/25℃,所述聚醚多元醇ⅱ为grw-310,产自上海高桥石化;所述聚酯多元醇的平均羟值为 390mgkoh/g~410mgkoh/g,黏度为1.3pa.s/25℃,所述聚酯多元醇为 ps-4002,产自南京金陵斯泰潘;所述聚磷酸铵聚合度为n>1000,产自山东世安化工有限公司;所述膨胀蛭石粉产自灵寿县瑞达矿业有限公司;所述三一缩二丙二醇亚磷酸酯产自沧州威化化工公司;
[0060]
所述聚磷酸铵、硫化钪、膨胀蛭石粉均经2000目筛预处理;
[0061]
所述超精细研磨泵的转速为2935r/min,磨盘间距为0.08mm;
[0062]
步骤102、65℃~70℃温度条件下,将b组原料搅拌预混1h后强化分散0.5h,得到b料;所述强化分散为经超精细研磨泵进行强化分散,所述 65℃~70℃温度条件为搅拌预混和强化分散过程中保持的物料温度;所述b 组原料包括:质量比为23.3:10的聚醚多元醇ⅰ和环氧树脂,所述聚醚多元醇ⅰ的质量为聚醚多元醇ⅱ质量的0.5倍;所述预混时搅拌器转速为 5000r/min;所述超精细研磨泵的转速为2935r/min,磨盘间距为0.06mm;所述聚醚多元醇ⅰ的平均羟值为480mgkoh/g~500mgkoh/g,黏度为6500 mpa.s/25℃~9500mpa.s/25℃,所述聚醚多元醇ⅰ的平均羟值为 480mgkoh/g~500mgkoh/g,黏度为6500mpa.s/25℃~9500mpa.s/25℃,所述聚醚多元醇ⅰ的平均羟值为480mgkoh/g~500mgkoh/g,黏度为6500 mpa.s/25℃~9500mpa.s/25℃,所述聚醚多元醇ⅰ为gr8349,产自上海高桥石化;所述环氧树脂为双酚a型环氧树脂,所述环氧树脂的黏度< 3000mpa
·
s/40℃,所述环氧树脂为e51,产自上海树脂厂;
[0063]
步骤103、42℃~47℃温度条件下,将c组原料搅拌预混3h,得到c 料;所述42℃~47℃温度条件为搅拌预混中保持的物料温度;所述c组原料包括质量比为4:1的聚合mdi和
4,4'-二环己基甲烷二异氰酸酯,所述聚合mdi的质量为聚酯多元醇质量的7.2倍;所述预混时搅拌器转速为 600r/min;所述聚合mdi平均官能度为2.9~3.0,4,4'-二环己基甲烷二异氰酸酯官能度为2;所述聚合mdi可以为烟台万华的pm-400,所述hmdi 可以为烟台万华氢化mdi;
[0064]
步骤二、将所述二氧化铀芯块粉末运输装备在70~80℃烘房中保温处理4h,将四个内支撑工装分别装入保温处理后二氧化铀芯块粉末运输装备的所述腔室中,如图5所示,将所述装备盖体安装于装备本体上,将二氧化铀芯块粉末运输装备装入外支撑工装中,得到带工装的装备;烘房处理的作用是提前预热,为化学反应提供热量,保证化学反应顺利起步;
[0065]
其中,所述内支撑工装包括内支撑工装第一本体71和内支撑工装第二本体72,所述内支撑工装第二本体72的数量为多个,多个所述内支撑工装第二本体72呈辐射状相邻排列于内支撑工装第一本体71周围,多个所述内支撑工装第二本体72形成的辐射中心与内支撑工装第一本体71中心重合;所述内支撑工装第一本体71形状为多棱椎台,所述多棱锥台的上表面面积大于下表面面积,所述多棱锥台的上表面中部设置有把手73;所述内支撑工装第二本体72均为多面体,所述多面体均具有与所述多棱椎台的一个棱面匹配的斜面;所述内支撑工装第一本体71与内支撑工装第二本体72上均设置有可供将内支撑工装第一本体71与内支撑工装第二本体72固定连接的螺钉螺孔组件;
[0066]
将内支撑工装置于所述腔室中时,内支撑工装第一本体71置于所述腔室中心处,多个内支撑工装第二本体72合围内支撑工装第一本体71且与所述多棱椎台的一个棱面匹配的斜面均贴近内支撑工装第一本体71,多个内支撑工装第二本体72的除斜面以外的其他侧平面与所述腔室的侧壁平面匹配;
[0067]
将所述内支撑工装装入所述腔室的方法包括:先装入第二本体72,在第二本体72合围中心区域装入第一本体71,压紧,将第二本体72斜面上的所述螺钉与第一本体71限位固定,使得贴近棱面的内支撑工装第二本体72同时贴紧棱面和腔室侧壁平面,实现对腔室的内支撑;
[0068]
比如当所述腔室形状为正四面体形时,如图5~8所示,其四个侧壁平面依次相接且垂直形成所述腔室的四面体形腔体,对应的内支撑工装第一本体71棱面数量为4,内支撑工装第二本体72的侧平面数量为5,5个所述侧平面中其中一个为与棱面形状匹配的斜面,另外4个侧平面依次相接且垂直与且与所述腔室侧壁平面匹配,比如所述内支撑工装第二本体72 可以为可放进所述腔室且与所述腔室匹配的正四面体结构,按照内支撑工装第一本体71的位置和形状;
[0069]
所述外支撑工装包括可套设于二氧化铀芯块粉末运输装备上的外支撑工装本体81,所述外支撑工装本体81外套设有可供固定外支撑工装本体81和二氧化铀芯块粉末运输装备的钢索锁紧系统82;所述外支撑工装本体81形状为空心圆柱体,所述外支撑工装本体81空心形状与二氧化铀芯块粉末运输装备侧壁轮廓相同;
[0070]
所述外支撑工装本体81包括多个外支撑工装本体块,多个所述外支撑工装本体块可合围并套设于所述二氧化铀芯块粉末运输装备上,将二氧化铀芯块粉末运输装备外形截面补足成圆形;图9所示为二氧化铀芯块粉末运输装备和外支撑工装的装配示意图;
[0071]
所述钢索锁紧系统82可供套设于合围后的外支撑工装本体块上,实现固定;所述
钢索锁紧系统82可以包括收紧用钢索、收紧机钳、u型卡扣;通过对外支撑工装本体81圆周周向预紧力作用,实现对二氧化铀芯块粉末运输装备均匀作用力,限制大面积平面向外的鼓胀程度,保证在泡沫生长过程中产生的内压力不致二氧化铀芯块粉末运输装备薄壁发生显著鼓出,保障合格率;
[0072]
步骤三、调整所述带工装的装备,使二氧化铀芯块粉末运输装备底壁面3竖直向上,如图10所示,将a料、b料和c料混合,得到混合液体料,分三个阶段向装备本体内导入混合液体料,生成泡沫功能材料,实现充填,具体包括:
[0073]
步骤301、将a料、b料和c料同时加入到高压混合釜中,以5800r/min 的转速搅拌20s,得到混合料液;所述混合料液中a料质量为40.62kg,b 料质量为11.14kg,c料质量为60.24kg;
[0074]
步骤302、如图10所示,将第一侧壁面24上靠近底壁面3的第一排气孔21作为混合料液导入口,将底壁面3上的2个第二排气孔22作为工艺排气孔,将其余排气孔封堵,利用耐高压软管将高压混合釜的出料口与作为混合料液导入口的第一排气孔21连通,向高压混合釜充气至釜内压力为3mpa,釜压作用下混合料液流入混合料液导入口,静置10h以上至混合料液填满侧壁面2中空腔室和隔断件4的中空腔体,完成第一阶段充填;预留工艺排气孔可以有效避免填充过程物料溢出;
[0075]
步骤303、将所述带工装的装备置于托架上,使带工装的装备的底壁面3垂直于地面,旋转调整带工装的装备,使底壁面3靠近地面的底角的对角线与地面夹角a为30~40
°
,如图11所示,向底壁面3的中空腔体中充填所述混合料液,至半满,静置4h;所述托架上部设置有与外支撑工装本体81形状匹配的支撑部,所述支撑部呈环面状;充填至底壁面3的中空腔体的混合料液中的a料质量为10.92kg,b料质量为3.0kg,c料质量为16.2kg;确定填充至半满效果可以通过用手掌在容器外壁寻找冷热分界线,或将内窥镜通过未封堵的孔观测确定;本步骤中继续以第一侧壁面24 上靠近底壁面3的第一排气孔21作为混合料液导入口,以距离α角最远处的第二排气孔作为工艺排气孔,即图11中标识22;
[0076]
步骤304、将带工装的装备逆时针旋转120
°
,以底壁面3上的一个第二排气孔22作为混合料液导入口,以第一侧壁面24上靠近底壁面3的第一排气孔21为工艺排气孔,如图12所示,向底壁面3的中空腔体中继续充填所述混合料液,观察工艺排气孔,泡沫即将流出时迅速封堵所述混合料液导入口和工艺排气孔,静置4h,完成装置本体的充填;继续充填的所述混合料液中a料质量为10.92kg,b料质量为3.0kg,c料质量为16.2kg;所述混合料液导入口为底壁面3上未填充区域且距离地面最远的第二排气孔22,所述工艺排气孔为第一侧壁面24上靠近底壁面3且距离地面最远的第一排气孔21;
[0077]
步骤四、以距离地面最远处的第三排气孔23作为混合料液导入口,以混合料液导入口下方的第三排气孔23作为工艺排气孔,工艺排气孔如图13中标识23所示,向盖体空腔中充入步骤301中的混合料液,利用工艺排气孔,观察泡沫即将流出时,迅速封堵所述混合料液导入口和工艺排气孔,静置2h,完成盖体空腔充填;其中,a料质量为8.25kg,b料质量为2.26kg,c料质量为12.24kg;向盖体空腔中充入步骤301中的混合料液时带工装的装备状态如图13所示;
[0078]
步骤五、将步骤四完成盖体空腔充填的运输装备置于140℃烘房中保持20h以使功能材料熟化,待所述运输装备外壁温度低于50℃后转出烘房,冷却,完成。
[0079]
实施例2
[0080]
本实施例提供一种二氧化铀芯块粉末运输装备用泡沫功能材料的制备方法,所述二氧化铀芯块粉末运输装备包括装备本体和装备盖体5,所述装备盖体5可拆卸安装于装备本体上;
[0081]
如图1~4所示,所述装备本体包括室腔1以及合围形成所述室腔1的侧壁面2和底壁面3,所述侧壁面2和底壁面3均为中空结构,所述侧壁面2的中空腔体与底壁面3的中空腔体连通;所述室腔1包括四个腔室以及将所述室腔1分隔成四个所述腔室的隔断件4,所述隔断件4为中空结构,所述隔断件4的中空腔体与侧壁面2的中空腔体和底壁面3的中空腔体均连通;所述隔断件的截面形状为十字型;所述装备盖体5内设置有盖体空腔;
[0082]
所述侧壁面2上开设有第一排气孔21,所述第一排气孔21与侧壁面 2的中空腔体连通,所述底壁面3上开设有第二排气孔22,所述第二排气孔22与底壁面3的中空腔体连通,所述装备盖体5上开设有第三排气孔 23,所述第三排气孔23与盖体空腔连通;
[0083]
所述侧壁面2包括合围形成室腔1且依次连接的第一侧壁面24、第二侧壁面25、第三侧壁面和第四侧壁面,所述第一侧壁面24和第三侧壁面上的第一排气孔21数量均为5个,所述第二侧壁面25和第四侧壁面上的第一排气孔21数量均为3个,3个所述第一排气孔21中,2个间隔设置于相应侧壁面的中部,另外1个设置于相应侧壁面的下部且位于2个间隔设置的第一排气孔21中间,位于相应侧壁面的下部的所述1个第一排气孔21正对隔断件4与相应侧壁面的连通处,5个所述第一排气孔21分为两组,第一组中的第一排气孔21数量为3个,第二组中的第一排气孔21 数量为2个,第一组中的3个所述第一排气孔21中,2个间隔设置于相应侧壁面的中部,另外1个设置于相应侧壁面的下部且位于2个间隔设置的第一排气孔21中间,位于相应侧壁面的下部的所述1个第一排气孔21正对隔断件4与相应侧壁面的连通处,第二组中的2个第一排气孔21间隔且位于第一组的3个第一排气孔21的下方;位于相应侧壁面的下部的1 个第一排气孔21临近底壁面3,处于侧壁面2、底壁面3和隔断件4的交汇处;
[0084]
所述第二排气孔22的数量为4个,4个所述第二排气孔22沿底壁面 3中心均匀分布于底壁面3上;所述第三排气孔23的数量为4个,4个所述第三排气孔23沿装备盖体5中心均匀分布于装备盖体5上;向所述二氧化铀芯块粉末运输装备提供的泡沫功能材料密度为0.25g/cm3;
[0085]
所述制备方法包括:
[0086]
步骤一、分别提供a料、b料和c料,具体包括:
[0087]
步骤101、45℃~50℃温度条件下,将a组原料搅拌预混后强化分散 0.5h,得到a料;所述强化分散为经超精细研磨泵进行强化分散,所述45℃~50℃温度条件为搅拌预混和强化分散过程中保持的物料温度;所述a组原料包括a组原料i和a组原料ii,所述搅拌预混为在搅拌器转速为 1800r/min条件下将a组原料i搅拌105min~110min后加入a组原料ii继续搅拌10min~15min;
[0088]
所述a组原料i包括:质量比为53.4:10:19:9:3:3:1:3.2:0.5: 0.1:0.1:0.3:2.5的聚醚多元醇ⅱ、聚酯多元醇、乙基膦酸二乙酯、三聚氰胺、聚磷酸铵、硫化钪、膨胀蛭石粉、二十二烷基硫二丁基锡、二月桂酸二丁基锡、油酸钾、钛酸四丁酯、去离子水和氯离子固定浆剂;
[0089]
所述a组原料ii包括:质量比为8:0.1的三一缩二丙二醇亚磷酸酯和四丁基氯化铵,所述三一缩二丙二醇亚磷酸酯与聚醚多元醇ⅱ的质量比为8:53.4;
[0090]
所述氯离子固定浆剂为由硝酸银粉末、粘合剂、溶剂和助剂组成的浆液,其中硝酸银过筛3000目,所述氯离子固定浆剂中硝酸银含量为 60%~70%;所述粘合剂为环氧树脂,所述溶剂为异佛尔酮,所述助剂为 peg-200;所述聚醚多元醇ⅱ的平均羟值为280mgkoh/g~340mgkoh/g,黏度为900mpa.s/25℃~1700mpa.s/25℃,所述聚醚多元醇ⅱ为grw-310,产自上海高桥石化;所述聚酯多元醇的平均羟值为 390mgkoh/g~410mgkoh/g,黏度为1.3pa.s/25℃,所述聚酯多元醇为 ps-4002,产自南京金陵斯泰潘;所述聚磷酸铵聚合度为n>1000,产自山东世安化工有限公司;所述膨胀蛭石粉产自灵寿县瑞达矿业有限公司;所述三一缩二丙二醇亚磷酸酯产自沧州威化化工公司;
[0091]
所述聚磷酸铵、硫化钪、膨胀蛭石粉均经2000目筛预处理;
[0092]
所述超精细研磨泵的转速为2935r/min,磨盘间距为0.06mm;
[0093]
步骤102、65℃~70℃温度条件下,将b组原料搅拌预混1h后强化分散0.5h,得到b料;所述强化分散为经超精细研磨泵进行强化分散,所述 65℃~70℃温度条件为搅拌预混和强化分散过程中保持的物料温度;所述b 组原料包括:质量比为26.6:10的聚醚多元醇ⅰ和环氧树脂,所述聚醚多元醇ⅰ的质量为聚醚多元醇ⅱ质量的0.5倍;所述预混时搅拌器转速为 5000r/min;所述超精细研磨泵的转速为2935r/min,磨盘间距为0.06mm;所述聚醚多元醇ⅰ为gr8349,产自上海高桥石化;所述环氧树脂为双酚 a型环氧树脂,所述环氧树脂的黏度<3000mpa
·
s/40℃,所述环氧树脂为 e51,产自上海树脂厂;
[0094]
步骤103、45℃~50℃温度条件下,将c组原料搅拌预混3h,得到c 料;所述45℃~50℃温度条件为搅拌预混中保持的物料温度;所述c组原料包括质量比为4:1的聚合mdi和4,4'-二环己基甲烷二异氰酸酯,所述聚合mdi的质量为聚酯多元醇质量的14倍;所述预混时搅拌器转速为 300r/min;所述聚合mdi平均官能度为2.9~3.0,4,4'-二环己基甲烷二异氰酸酯官能度为2;所述聚合mdi可以为烟台万华的pm-400,所述hmdi 可以为烟台万华氢化mdi;
[0095]
步骤二、将所述二氧化铀芯块粉末运输装备在70~80℃烘房中保温处理4h,将四个内支撑工装分别装入保温处理后二氧化铀芯块粉末运输装备的所述腔室中,如图5所示,将所述装备盖体安装于装备本体上,将二氧化铀芯块粉末运输装备装入外支撑工装中,得到带工装的装备;烘房处理的作用是提前预热,为化学反应提供热量,保证化学反应顺利起步;
[0096]
其中,所述内支撑工装包括内支撑工装第一本体71和内支撑工装第二本体72,所述内支撑工装第二本体72的数量为多个,多个所述内支撑工装第二本体72呈辐射状相邻排列于内支撑工装第一本体71周围,多个所述内支撑工装第二本体72形成的辐射中心与内支撑工装第一本体71中心重合;所述内支撑工装第一本体71形状为多棱椎台,所述多棱锥台的上表面面积大于下表面面积,所述多棱锥台的上表面中部设置有把手73;所述内支撑工装第二本体72均为多面体,所述多面体均具有与所述多棱椎台的一个棱面匹配的斜面;所述内支撑工装第一本体71与内支撑工装第二本体72上均设置有可供将内支撑工装第一本体71与内支撑工装第二本体72固定连接的螺钉螺孔组件;
[0097]
将内支撑工装置于所述腔室中时,内支撑工装第一本体71置于所述腔室中心处,
多个内支撑工装第二本体72合围内支撑工装第一本体71且与所述多棱椎台的一个棱面匹配的斜面均贴近内支撑工装第一本体71,多个内支撑工装第二本体72的除斜面以外的其他侧平面与所述腔室的侧壁平面匹配;
[0098]
将所述内支撑工装装入所述腔室的方法包括:先装入第二本体72,在第二本体72合围中心区域装入第一本体71,压紧,将第二本体72斜面上的所述螺钉与第一本体71限位固定,使得贴近棱面的内支撑工装第二本体72同时贴紧棱面和腔室侧壁平面,实现对腔室的内支撑;
[0099]
比如当所述腔室形状为正四面体形时,如图5~8所示,其四个侧壁平面依次相接且垂直形成所述腔室的四面体形腔体,对应的内支撑工装第一本体71棱面数量为4,内支撑工装第二本体72的侧平面数量为5,5个所述侧平面中其中一个为与棱面形状匹配的斜面,另外4个侧平面依次相接且垂直与且与所述腔室侧壁平面匹配,比如所述内支撑工装第二本体72 可以为可放进所述腔室且与所述腔室匹配的正四面体结构,按照内支撑工装第一本体71的位置和形状;
[0100]
所述外支撑工装包括可套设于二氧化铀芯块粉末运输装备上的外支撑工装本体81,所述外支撑工装本体81外套设有可供固定外支撑工装本体81和二氧化铀芯块粉末运输装备的钢索锁紧系统82;所述外支撑工装本体81形状为空心圆柱体,所述外支撑工装本体81空心形状与二氧化铀芯块粉末运输装备侧壁轮廓相同;
[0101]
所述外支撑工装本体81包括多个外支撑工装本体块,多个所述外支撑工装本体块可合围并套设于所述二氧化铀芯块粉末运输装备上,将二氧化铀芯块粉末运输装备外形截面补足成圆形;图9所示为二氧化铀芯块粉末运输装备和外支撑工装的装配示意图;
[0102]
所述钢索锁紧系统82可供套设于合围后的外支撑工装本体块上,实现固定;所述钢索锁紧系统82可以包括收紧用钢索、收紧机钳、u型卡扣;通过对外支撑工装本体81圆周周向预紧力作用,实现对二氧化铀芯块粉末运输装备均匀作用力,限制大面积平面向外的鼓胀程度,保证在泡沫生长过程中产生的内压力不致二氧化铀芯块粉末运输装备薄壁发生显著鼓出,保障合格率;
[0103]
步骤三、调整所述带工装的装备,使二氧化铀芯块粉末运输装备底壁面3竖直向上,如图10所示,将a料、b料和c料混合,得到混合液体料,分三个阶段向装备本体内导入混合液体料,生成泡沫功能材料,实现充填,具体包括:
[0104]
步骤301、将a料、b料和c料同时加入到高压混合釜中,以5800r/min 的转速搅拌20s,得到混合料液;所述混合料液中a料质量为38.09kg,b 料质量为12.31kg,c料质量为56.6kg;
[0105]
步骤302、如图10所示,将第一侧壁面24上靠近底壁面3的第一排气孔21作为混合料液导入口,将底壁面3上的2个第二排气孔22作为工艺排气孔,将其余排气孔封堵,利用耐高压软管将高压混合釜的出料口与作为混合料液导入口的第一排气孔21连通,向高压混合釜充气至釜内压力为4mpa,釜压作用下混合料液流入混合料液导入口,静置10h以上至混合料液填满侧壁面2中空腔室和隔断件4的中空腔体,完成第一阶段充填;预留工艺排气孔可以有效避免填充过程物料溢出;
[0106]
步骤303、将所述带工装的装备置于托架上,使带工装的装备的底壁面3垂直于地面,旋转调整带工装的装备,使底壁面3靠近地面的底角的对角线与地面夹角a为30~40
°
,
如图11所示,向底壁面3的中空腔体中充填所述混合料液,至半满,静置4h;所述托架上部设置有与外支撑工装本体81形状匹配的支撑部,所述支撑部呈环面状;充填至底壁面3的中空腔体的混合料液中的a料质量为10.27kg,b料质量为3.32kg,c料质量为15.41kg;确定填充至半满效果可以通过用手掌在容器外壁寻找冷热分界线,或将内窥镜通过未封堵的孔观测确定;本步骤中继续以第一侧壁面24上靠近底壁面3的第一排气孔21作为混合料液导入口,以距离α角最远处的第二排气孔作为工艺排气孔,即图11中标识22;
[0107]
步骤304、将带工装的装备逆时针旋转120
°
,以底壁面3上的一个第二排气孔22作为混合料液导入口,以第一侧壁面24上靠近底壁面3的第一排气孔21为工艺排气孔,如图12所示,向底壁面3的中空腔体中继续充填所述混合料液,观察工艺排气孔,泡沫即将流出时迅速封堵所述混合料液导入口和工艺排气孔,静置4h,完成装置本体的充填;继续充填的所述混合料液中a料质量为10.27kg,b料转入质量为3.32kg,c料转入质量为15.41kg;所述混合料液导入口为底壁面3上未填充区域且距离地面最远的第二排气孔22,所述工艺排气孔为第一侧壁面24上靠近底壁面 3且距离地面最远的第一排气孔21;
[0108]
步骤四、以距离地面最远处的第三排气孔23作为混合料液导入口,以混合料液导入口下方的第三排气孔23作为工艺排气孔,工艺排气孔如图13中标识23所示,向盖体空腔中充入步骤301中的混合料液,利用工艺排气孔,观察泡沫即将流出时,迅速封堵所述混合料液导入口和工艺排气孔,静置2h,完成盖体空腔充填;其中,a料质量为7.75kg,b料质量为2.5kg,c料质量为11.63kg;向盖体空腔中充入步骤301中的混合料液时带工装的装备状态如图13所示;
[0109]
步骤五、将步骤四完成盖体空腔充填的运输装备置于140℃烘房中保持12h以使功能材料熟化,待所述运输装备外壁温度低于50℃后转出烘房,冷却,完成。
[0110]
实施例3
[0111]
本实施例提供一种二氧化铀芯块粉末运输装备用泡沫功能材料的制备方法,所述二氧化铀芯块粉末运输装备包括装备本体和装备盖体5,所述装备盖体5可拆卸安装于装备本体上;
[0112]
如图1~4所示,所述装备本体包括室腔1以及合围形成所述室腔1的侧壁面2和底壁面3,所述侧壁面2和底壁面3均为中空结构,所述侧壁面2的中空腔体与底壁面3的中空腔体连通;所述室腔1包括四个腔室以及将所述室腔1分隔成四个所述腔室的隔断件4,所述隔断件4为中空结构,所述隔断件4的中空腔体与侧壁面2的中空腔体和底壁面3的中空腔体均连通;所述隔断件的截面形状为十字型;所述装备盖体5内设置有盖体空腔;
[0113]
所述侧壁面2上开设有第一排气孔21,所述第一排气孔21与侧壁面 2的中空腔体连通,所述底壁面3上开设有第二排气孔22,所述第二排气孔22与底壁面3的中空腔体连通,所述装备盖体5上开设有第三排气孔 23,所述第三排气孔23与盖体空腔连通;
[0114]
所述侧壁面2包括合围形成室腔1且依次连接的第一侧壁面24、第二侧壁面25、第三侧壁面和第四侧壁面,所述第一侧壁面24和第三侧壁面上的第一排气孔21数量均为5个,所述第二侧壁面25和第四侧壁面上的第一排气孔21数量均为3个,3个所述第一排气孔21中,2个间隔设置于相应侧壁面的中部,另外1个设置于相应侧壁面的下部且位于2个间隔设置的第一排气孔21中间,位于相应侧壁面的下部的所述1个第一排气孔21正对隔断件4与相应侧壁面的连通处,5个所述第一排气孔21分为两组,第一组中的第一排气孔21数量为3个,
第二组中的第一排气孔21 数量为2个,第一组中的3个所述第一排气孔21中,2个间隔设置于相应侧壁面的中部,另外1个设置于相应侧壁面的下部且位于2个间隔设置的第一排气孔21中间,位于相应侧壁面的下部的所述1个第一排气孔21正对隔断件4与相应侧壁面的连通处,第二组中的2个第一排气孔21间隔且位于第一组的3个第一排气孔21的下方;位于相应侧壁面的下部的1 个第一排气孔21临近底壁面3,处于侧壁面2、底壁面3和隔断件4的交汇处;
[0115]
所述第二排气孔22的数量为4个,4个所述第二排气孔22沿底壁面 3中心均匀分布于底壁面3上;所述第三排气孔23的数量为4个,4个所述第三排气孔23沿装备盖体5中心均匀分布于装备盖体5上;向所述二氧化铀芯块粉末运输装备提供的泡沫功能材料密度为0.24g/cm3;
[0116]
所述制备方法包括:
[0117]
步骤一、分别提供a料、b料和c料,具体包括:
[0118]
步骤101、43℃~48℃温度条件下,将a组原料搅拌预混后强化分散 0.5h,得到a料;所述强化分散为经超精细研磨泵进行强化分散,所述43℃~48℃温度条件为搅拌预混和强化分散过程中保持的物料温度;所述a组原料包括a组原料i和a组原料ii,所述搅拌预混为在搅拌器转速为 1800r/min条件下将a组原料i搅拌105min~110min后加入a组原料ii继续搅拌10min~15min;
[0119]
所述a组原料i包括:质量比为40:20:22:5:3:5:2:2.8:0.5: 0.1:0.1:0.4:3的聚醚多元醇ⅱ、聚酯多元醇、乙基膦酸二乙酯、三聚氰胺、聚磷酸铵、硫化钪、膨胀蛭石粉、二十二烷基硫二丁基锡、二月桂酸二丁基锡、油酸钾、钛酸四丁酯、去离子水和氯离子固定浆剂;
[0120]
所述a组原料ii包括:质量比为10:0.1的三一缩二丙二醇亚磷酸酯和四丁基氯化铵,所述三一缩二丙二醇亚磷酸酯与聚醚多元醇ⅱ的质量比为9:0.3;
[0121]
所述氯离子固定浆剂为由硝酸银粉末、粘合剂、溶剂和助剂组成的浆液,其中硝酸银过筛3000目,所述氯离子固定浆剂中硝酸银含量为 60%~70%;所述粘合剂为环氧树脂,所述溶剂为异佛尔酮,所述助剂为 peg-200;所述聚醚多元醇ⅱ的平均羟值为280mgkoh/g~340mgkoh/g,黏度为900mpa.s/25℃~1700mpa.s/25℃,所述聚醚多元醇ⅱ为grw-310,产自上海高桥石化;所述聚酯多元醇的平均羟值为 390mgkoh/g~410mgkoh/g,黏度为1.3pa.s/25℃,所述聚酯多元醇为 ps-4002,产自南京金陵斯泰潘;所述聚磷酸铵聚合度为n>1000,产自山东世安化工有限公司;所述膨胀蛭石粉产自灵寿县瑞达矿业有限公司;所述三一缩二丙二醇亚磷酸酯产自沧州威化化工公司;
[0122]
所述聚磷酸铵、硫化钪、膨胀蛭石粉均经2000目筛预处理;
[0123]
所述超精细研磨泵的转速为2935r/min,磨盘间距为0.08mm;
[0124]
步骤102、65℃~70℃温度条件下,将b组原料搅拌预混1h后强化分散1h,得到b料;所述强化分散为经超精细研磨泵进行强化分散,所述65℃~70℃温度条件为搅拌预混和强化分散过程中保持的物料温度;所述b 组原料包括:质量比为1:1的聚醚多元醇ⅰ和环氧树脂,所述聚醚多元醇ⅰ的质量为聚醚多元醇ⅱ质量的0.5倍;所述预混时搅拌器转速为 5000r/min;所述超精细研磨泵的转速为2935r/min,磨盘间距为0.06mm;所述聚醚多元醇ⅰ为gr8349,产自上海高桥石化;所述环氧树脂为双酚 a型环氧树脂,所述环氧树脂的黏度<3000mpa
·
s/40℃,所述环氧树脂为 e51,产自上海树脂厂;
[0125]
步骤103、45℃~50℃温度条件下,将c组原料搅拌预混3h,得到c 料;所述45℃~50℃温度条件为搅拌预混中保持的物料温度;所述c组原料包括质量比为4:1的聚合mdi和4,4'-二环己基甲烷二异氰酸酯,所述聚合mdi的质量为聚酯多元醇质量的7.6倍;所述预混时搅拌器转速为 500r/min;所述聚合mdi平均官能度为2.9~3.0,4,4'-二环己基甲烷二异氰酸酯官能度为2;所述聚合mdi可以为烟台万华的pm-400,所述hmdi 可以为烟台万华氢化mdi;
[0126]
步骤二、将所述二氧化铀芯块粉末运输装备在70~80℃烘房中保温处理4h,将四个内支撑工装分别装入保温处理后二氧化铀芯块粉末运输装备的所述腔室中,如图5所示,将所述装备盖体安装于装备本体上,将二氧化铀芯块粉末运输装备装入外支撑工装中,得到带工装的装备;烘房处理的作用是提前预热,为化学反应提供热量,保证化学反应顺利起步;
[0127]
其中,所述内支撑工装包括内支撑工装第一本体71和内支撑工装第二本体72,所述内支撑工装第二本体72的数量为多个,多个所述内支撑工装第二本体72呈辐射状相邻排列于内支撑工装第一本体71周围,多个所述内支撑工装第二本体72形成的辐射中心与内支撑工装第一本体71中心重合;所述内支撑工装第一本体71形状为多棱椎台,所述多棱锥台的上表面面积大于下表面面积,所述多棱锥台的上表面中部设置有把手73;所述内支撑工装第二本体72均为多面体,所述多面体均具有与所述多棱椎台的一个棱面匹配的斜面;所述内支撑工装第一本体71与内支撑工装第二本体72上均设置有可供将内支撑工装第一本体71与内支撑工装第二本体72固定连接的螺钉螺孔组件;
[0128]
将内支撑工装置于所述腔室中时,内支撑工装第一本体71置于所述腔室中心处,多个内支撑工装第二本体72合围内支撑工装第一本体71且与所述多棱椎台的一个棱面匹配的斜面均贴近内支撑工装第一本体71,多个内支撑工装第二本体72的除斜面以外的其他侧平面与所述腔室的侧壁平面匹配;
[0129]
将所述内支撑工装装入所述腔室的方法包括:先装入第二本体72,在第二本体72合围中心区域装入第一本体71,压紧,将第二本体72斜面上的所述螺钉与第一本体71限位固定,使得贴近棱面的内支撑工装第二本体72同时贴紧棱面和腔室侧壁平面,实现对腔室的内支撑;
[0130]
比如当所述腔室形状为正四面体形时,如图5~8所示,其四个侧壁平面依次相接且垂直形成所述腔室的四面体形腔体,对应的内支撑工装第一本体71棱面数量为4,内支撑工装第二本体72的侧平面数量为5,5个所述侧平面中其中一个为与棱面形状匹配的斜面,另外4个侧平面依次相接且垂直与且与所述腔室侧壁平面匹配,比如所述内支撑工装第二本体72 可以为可放进所述腔室且与所述腔室匹配的正四面体结构,按照内支撑工装第一本体71的位置和形状;
[0131]
所述外支撑工装包括可套设于二氧化铀芯块粉末运输装备上的外支撑工装本体81,所述外支撑工装本体81外套设有可供固定外支撑工装本体81和二氧化铀芯块粉末运输装备的钢索锁紧系统82;所述外支撑工装本体81形状为空心圆柱体,所述外支撑工装本体81空心形状与二氧化铀芯块粉末运输装备侧壁轮廓相同;
[0132]
所述外支撑工装本体81包括多个外支撑工装本体块,多个所述外支撑工装本体块可合围并套设于所述二氧化铀芯块粉末运输装备上,将二氧化铀芯块粉末运输装备外形截
面补足成圆形;图9所示为二氧化铀芯块粉末运输装备和外支撑工装的装配示意图;
[0133]
所述钢索锁紧系统82可供套设于合围后的外支撑工装本体块上,实现固定;所述钢索锁紧系统82可以包括收紧用钢索、收紧机钳、u型卡扣;通过对外支撑工装本体81圆周周向预紧力作用,实现对二氧化铀芯块粉末运输装备均匀作用力,限制大面积平面向外的鼓胀程度,保证在泡沫生长过程中产生的内压力不致二氧化铀芯块粉末运输装备薄壁发生显著鼓出,保障合格率;
[0134]
步骤三、调整所述带工装的装备,使二氧化铀芯块粉末运输装备底壁面3竖直向上,如图10所示,将a料、b料和c料混合,得到混合液体料,分三个阶段向装备本体内导入混合液体料,生成泡沫功能材料,实现充填,具体包括:
[0135]
步骤301、将a料、b料和c料同时加入到高压混合釜中,以5800r/min 的转速搅拌20s,得到混合料液;所述混合料液中a料质量为34.01kg,b 料质量为12.02kg,c料质量为57.32kg;
[0136]
步骤302、如图10所示,将第一侧壁面24上靠近底壁面3的第一排气孔21作为混合料液导入口,将底壁面3上的2个第二排气孔22作为工艺排气孔,将其余排气孔封堵,利用耐高压软管将高压混合釜的出料口与作为混合料液导入口的第一排气孔21连通,向高压混合釜充气至釜内压力为5mpa,釜压作用下混合料液流入混合料液导入口,静置10h以上至混合料液填满侧壁面2中空腔室和隔断件4的中空腔体,完成第一阶段充填;预留工艺排气孔可以有效避免填充过程物料溢出;
[0137]
步骤303、将所述带工装的装备置于托架上,使带工装的装备的底壁面3垂直于地面,旋转调整带工装的装备,使底壁面3靠近地面的底角的对角线与地面夹角a为30~40
°
,如图11所示,向底壁面3的中空腔体中充填所述混合料液,至半满,静置4h;所述托架上部设置有与外支撑工装本体81形状匹配的支撑部,所述支撑部呈环面状;充填至底壁面3的中空腔体的混合料液中的a料质量为9.16kg,b料质量为3.24kg,c料质量为15.43kg;确定填充至半满效果可以通过用手掌在容器外壁寻找冷热分界线,或将内窥镜通过未封堵的孔观测确定;本步骤中继续以第一侧壁面 24上靠近底壁面3的第一排气孔21作为混合料液导入口,以距离α角最远处的第二排气孔作为工艺排气孔,即图11中标识22;
[0138]
步骤304、将带工装的装备逆时针旋转120
°
,以底壁面3上的一个第二排气孔22作为混合料液导入口,以第一侧壁面24上靠近底壁面3的第一排气孔21为工艺排气孔,如图12所示,向底壁面3的中空腔体中继续充填所述混合料液,观察工艺排气孔,泡沫即将流出时迅速封堵所述混合料液导入口和工艺排气孔,静置4h,完成装置本体的充填;继续充填的所述混合料液中a料质量为9.16kg,b料质量为3.24kg,c料质量为 15.43kg;所述混合料液导入口为底壁面3上未填充区域且距离地面最远的第二排气孔22,所述工艺排气孔为第一侧壁面24上靠近底壁面3且距离地面最远的第一排气孔21;
[0139]
步骤四、以距离地面最远处的第三排气孔23作为混合料液导入口,以混合料液导入口下方的第三排气孔23作为工艺排气孔,工艺排气孔如图13中标识23所示,向盖体空腔中充入步骤301中的混合料液,利用工艺排气孔,观察泡沫即将流出时,迅速封堵所述混合料液导入口和工艺排气孔,静置2h,完成盖体空腔充填;其中,a料质量为6.91kg,b料转入质量为2.44kg,c料转入质量为11.65kg;向盖体空腔中充入步骤301中的混合料液时带工装的装备状态如图13所示;
[0140]
步骤五、将步骤四完成盖体空腔充填的运输装备置于140℃烘房中保持15h以使功能材料熟化,待所述运输装备外壁温度低于50℃后转出烘房,冷却,完成。
[0141]
性能评价:
[0142]
按照表1的方法对本发明实施例1~3中泡沫功能材料的性能进行检测,检测结果见表2。所述泡沫功能材料取材方法包括从所述装备中裁切取样。
[0143]
表1性能检测的方法及所依照的标准
[0144][0145]
表2泡沫功能材料的性能
[0146][0147]
注:*装备样机实测值
[0148]
表2中结果显示,在装备外壁温度>900℃下,持续35min过程中,装备内壁温度最高达到133.5℃,<150℃限值,表明泡沫功能材料达到核级装备要求。
[0149]
以上所述,仅是本发明的较佳实施例,并非对本发明做任何限制,凡是根据发明技术实质对以上实施例所作的任何简单修改、变更以及等效结构变化,均仍属于本发明技术方案的保护范围内。
再多了解一些
本文用于企业家、创业者技术爱好者查询,结果仅供参考。