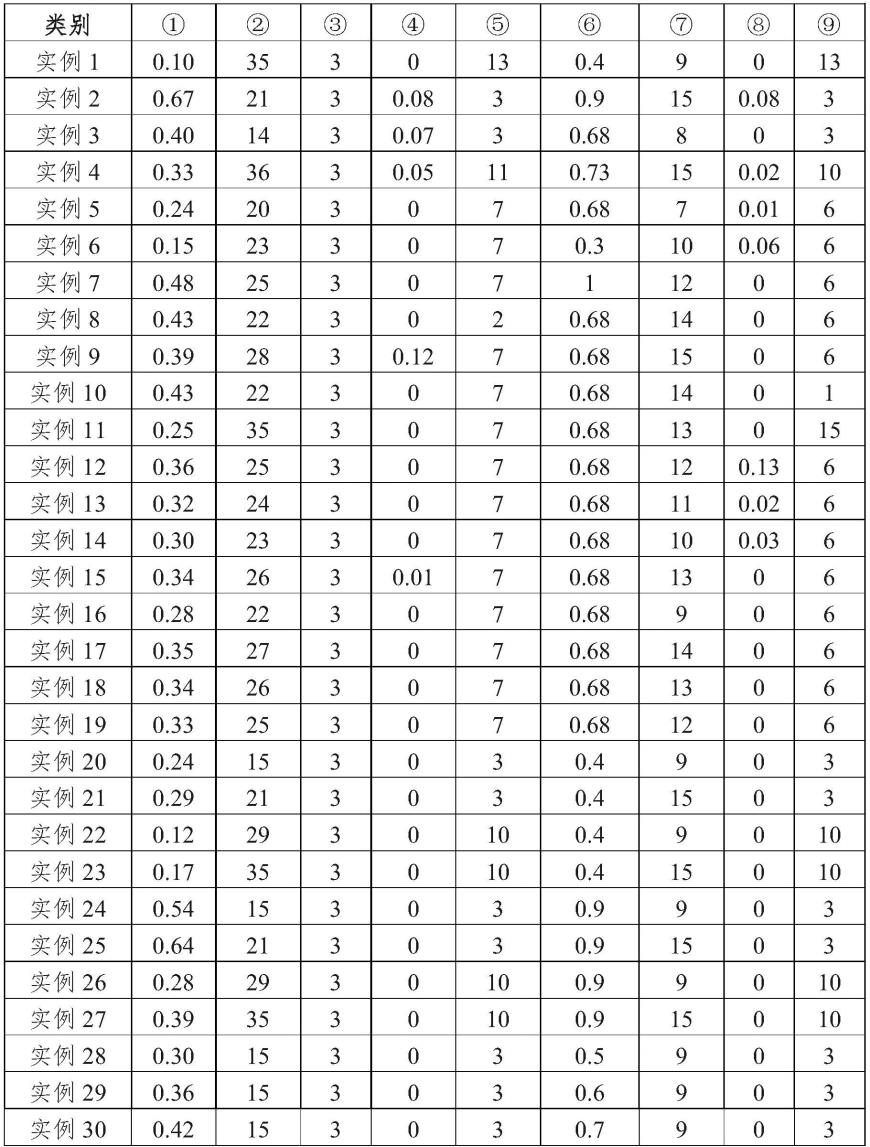
1.本发明涉及一种耐蚀性和点焊性优异的镀锌系钢材,更具体地,涉及一种镀覆有包括两个以上的层的多层锌合金且具有优异的耐蚀性和点焊性的镀锌系钢材。
背景技术:
2.通过阴极防蚀抑制铁的腐蚀的镀锌法具有优异的防腐蚀性能和经济性,因此广泛用于制造具有高耐腐蚀特性的钢材,并且汽车、家电产品及建筑材料等的全部产业对镀锌的镀锌钢材的需求正在增加。
3.这种镀锌钢材具有暴露在腐蚀环境中时氧化还原电位低于铁的锌先被腐蚀而抑制钢材的腐蚀的牺牲防蚀(sacrificial corrosion protection)的特性,而且镀层的锌被氧化,在钢材表面形成致密的腐蚀产物,将钢材与氧化气氛隔断,从而提高钢材的耐腐蚀性。
4.但是,随着产业的进步,大气污染日益增加,腐蚀环境日益恶化,并且对资源和节能的管制日益严格,因此开发具有比现有的镀锌钢材更优异的耐蚀性的钢材的需求日益增加。作为其中的一部分,正在进行通过在镀层中添加镁(mg)等元素来提高钢材的耐蚀性的镀锌系钢材的制造技术相关的各种研究。
5.另外,通常,镀锌钢材或者镀锌合金钢材(以下,称为“镀锌系钢材”)通过加工等被加工成部件,然后通过点焊等被焊接而用作产品,在微细组织包含奥氏体或者残余奥氏体的高强度钢材、添加高p的高强度无间隙原子(interstitial free,if)钢材等作为基材的镀锌系钢材的情况下,存在点焊时熔融状态的锌沿基材铁晶界渗透而诱发脆性裂纹的称为液态金属致脆(liquid metal embrittlement,lme)的问题。
6.图1是将由于点焊而产生lme裂纹的焊接部件的焊接部进行放大观察的照片。图1中,将在熔核(nugget)上部和下部产生的裂纹称为a型(type a)裂纹,将在焊接肩部产生的裂纹称为b型(type b)裂纹,将焊接时由于电极未对准(misalignment)而在钢板的内部产生的裂纹称为c型(type c)裂纹。其中,b型裂纹和c型裂纹对材料的刚性产生大的影响,因此焊接时防止产生裂纹是本技术领域的核心要求事项。
7.此外,在某些情况下,镀锌系钢材可以通过包括真空沉积等在内的物理气相(蒸汽)沉积(physical vapor deposition,pvd)方法进行镀覆。但是,通过所述物理气相沉积方法形成的锌镀层生长为柱形状的柱状(columnar)组织,因此在生长的柱和柱之间可能会产生空隙,这会引起镀层的密度降低的问题。如上所述低密度的锌镀层的硬度低,并且存在抗拉毛性降低的问题。
8.此外,在镀锌系钢材的情况下,根据镀层的组成,与基材铁的粘附性降低,因此加工时可能会发生镀层从基材铁脱落的问题。
技术实现要素:
本发明要解决的技术问题
9.根据本发明的一个方面,可以提供一种点焊性优异的镀锌系钢材。
10.根据本发明的另一个方面,可以提供一种抗拉毛性优异的镀锌系钢材。
11.根据本发明的另一个方面,可以提供一种镀层和基材铁的粘附性优异的镀锌系钢材。
12.本发明的技术问题并不限定于上述内容。本发明所属技术领域中的技术人员从本公开内容中记载的内容理解本发明的附加的技术问题是没有任何困难的。解决技术问题的技术手段
13.本发明的一个方面的镀锌系钢材可以包括:基材铁;以及多层锌系镀层,其由两个以上的有区别的镀层组成,其中,所述多层锌系镀层可以包含0.16-0.78重量%的mg。
14.本发明的另一个方面的制造镀锌系钢材的方法可以包括以下步骤:准备基材铁;在所述基材铁上依次形成由两个以上的有区别的镀层组成的多层锌系镀层,其中,所述多层锌系镀层可以包含0.12-0.64重量%的mg。发明效果
15.根据本发明的一个方面,通过形成多层锌镀层,并根据本发明的特别的条件控制各层的特征,可以提供一种具有优异的耐蚀性和点焊性的镀锌系钢材。此外,根据本发明的另一个方面,通过形成包括含有微量mg的锌合金镀层的多层锌系镀层并控制其中一部分层的刚性,可以提高抗拉毛性。此外,本发明的另一个方面可以提供一种镀锌钢材,其中,通过控制镀层的层组成,即使包括刚性的层,镀层与基材铁的粘附性也优异。
附图说明
16.图1是将由于点焊而产生lme裂纹的焊接部件的焊接部截面进行放大观察的照片。
17.图2是示出锌-镁二元系相图的一部分的图。
18.图3是示出根据本发明的一个具体实施方案获得的镀锌系钢材的多层锌系镀层的层结构的示意图。
19.图4是用于电磁加热物理气相沉积的装置的示意图。最佳实施方式
20.以下,对本发明的点焊性和耐蚀性优异的镀锌系钢材进行详细的说明。需要注意的是,本发明中钢板的上下可以根据堆叠状态随时改变,因此记载为“上(on)”,例如记载为“基材铁上”仅表示与基材铁接触,并不表示在高度方面位于上部。此外,需要注意的是,除非另有特别说明,否则本发明中元素的含量以重量为基准。
21.本发明的镀锌系钢材包括基材铁和形成在所述基材铁上的多层镀层。本发明中对所述基材铁的形式不作特别限定,例如,所述基材铁可以是钢板或者钢线材。本发明中描述的多层是指存在组成或组织方面有区别的多个层。根据本发明的一个具体实施方案,组成多层的各层可以通过物理气相沉积(pvd)等方法形成,由于如上所述的工艺的特性,同一层的组成的变化非常小,因此容易与其它层区分开。但是,在形成层的过程或层的形成前/后,由于向镀层施加热,两层之间发生扩散,可能存在两层的边界略微模糊的情况,本发明中还可以包括这种情况。在如上所述的情况下,可以将由于扩散而模糊的区域的中间位置处作为两层的边界。但是,即使并不一定是物理气相沉积,只要在上述范围内可以明确地区分各层,则不从本发明的范围内排除。
22.此外,本发明中对基材铁(钢材)的条件也不作特别限制。但是,点焊时lme裂纹引起的问题通常在强度为980mpa以上的高强度钢材中发生,因此本发明的一个具体实施方案可以更有利地应用于强度为1200mpa以上的高强度钢材。无需特别设定作为对象的高强度钢材的强度的上限,但将通常市售的钢材作为对象时,可以设定为1800mpa以下。
23.此外,高强度钢材的基材铁的微细组织可以包含选自奥氏体、残余奥氏体和马氏体中的一种以上,但并不必须限定于此。
24.并且,虽然并不必须限定于此,但可以应用于本发明的一个具体实施方案的基材铁可以列举具有以重量%计包含c:0.10-1.0%、si:0.5-3%、mn:1.0-25%、al:0.01-10%、p:0.1%以下、s:0.01%以下、余量的fe和不可避免的杂质的组成的基材铁。此外,在这种情况下,所述c、si、mn、p和s的含量可以满足以下关系式1。
25.[关系式1][c] [mn]/20 [si]/30 2[p] 4[s]≥0.3
[0026]
(其中,[c]、[mn]、[si]、[p]和[s]分别表示相应元素的含量(重量%)。)
[0027]
具有如上所述的合金组成和微细组织时,点焊时液态金属致脆(lme)可能会成为主要问题,其原因如下。即,与其它组织相比,奥氏体组织或者残余奥氏体组织的晶界脆弱,由于点焊而施加应力时,液态的熔融锌渗透到焊接部上的奥氏体组织或者残余奥氏体组织的晶界而产生裂纹,因此引发作为脆性断裂的液态金属致脆。
[0028]
但是,在本发明中,如下所述,使液态的熔融锌残留的时间最小化,因此即使将具有如上所述的合金组成和微细组织的钢材作为基材制造镀锌系钢材,也会有效地抑制液态金属致脆的发生。然而,基材铁的合金组成不满足上述范围时,也可以应用本发明。
[0029]
本发明中,为了进一步提高镀锌系钢材的耐蚀性,将锌系镀层中添加mg的镀锌系钢材作为对象。将mg添加到锌镀层中时,可以进一步提高镀层的耐蚀性。但是,如图2所示,将mg添加到锌镀层中时,镀层的熔点降低,由于低熔点,焊接时镀层的流动性增加,因此容易沿着晶界渗透。
[0030]
本发明的发明人为了解决这种问题而进行深入研究的结果,确认了在基材铁上形成由两个以上的有区别的镀层组成的锌系镀层时,确保耐蚀性,并且焊接时不引起液态金属致脆等的问题,从而完成了本发明。
[0031]
本发明涉及一种基材铁的表面形成有锌系镀层的镀锌系钢材,所述锌系镀层包括两个以上的锌层或含有微量的mg的锌合金层,将镀层的结构设计为通过降低所述锌系镀层中的mg含量,但仅在一部分层中添加适量的mg,从而可以确保耐蚀性。在如上所述的情况下,本发明的锌系镀层中,相对于整个多层镀层的重量,包含0.12-0.64%的mg,并且包括至少一个包含0.4-0.9重量%的mg的层。相对于整个多层镀层的重量,当mg含量不足时,可能无法充分确保耐蚀性。另一方面,当mg含量过高时,点焊性可能不良,因此相对于整个多层镀层的重量,可以将mg含量设为上述范围。
[0032]
即,从图2中可以确认,当从锌含量为100%的位置处开始增加整个镀层的mg含量以提高耐蚀性时,存在熔点大幅降低的区域,因此非常容易发生lme。本发明中,为了解决如上所述的问题,仅在一部分层中添加相对高含量的mg以有助于确保耐蚀性,其余层中不添加mg或添加微量mg,以使整个合金镀层的mg含量不会升高。即使一部分镀层中的mg含量略微高,由于焊接时镀层熔融并混合,因此在熔融的镀液中mg被稀释为整个镀层中的含量或者由于fe的扩散而被稀释为低于其的含量,其结果熔融的镀液的熔点不会大幅降低。因此,
根据本发明的一个具体实施方案控制锌系镀层的层结构时,可以同时实现耐蚀性和点焊性。
[0033]
根据本发明的一个具体实施方案,所述锌系镀层可以以每一面35g/m2以下的少量附着在基材铁上(表示以整个层的总附着量为基准,基材铁的每单位面积附着的镀层的量)。这种附着量是远小于热浸镀锌钢板(gi钢板)的常规的锌镀覆附着量60g/m2的值,通过这样减少附着量,可以进一步降低点焊时发生lme的可能性。因此,本发明的一个具体实施方案中,锌系镀层的附着量可以为35g/m2以下。但是,当附着量过小时,可能无法充分确保耐蚀性,因此所述附着量可以为15g/m2以上。
[0034]
图3中示出的本发明的一个具体实施方案中,锌系镀层100可以具有从与基材铁的界面依次由第一镀层110至第三镀层130组成的三层结构,其中,第二镀层120的mg含量可以为0.4-0.9重量%。通过将第二镀层120的mg含量控制在0.4重量%以上,可以确保整个锌系镀层的耐蚀性。此外,通过将第二镀层120的mg含量控制在0.9重量%以下,可以提高锌镀层的点焊性。
[0035]
为了可以发挥后述各层的功能,第一镀层110和第三镀层130的mg含量优选为0.1重量%以下,实质上可以是不包含mg的纯zn层。但是,需要注意的是,即使是纯zn层,也并不意味着排除杂质水平的其它元素(其它元素中也可能包含mg)。
[0036]
通过在与基材铁的界面形成第一镀层110,可以提高镀覆粘附性。即,包含0.4-0.9重量%的mg的第二镀层120是较硬的层,与基材铁的粘附可能不顺利,当在第二镀层120和基材铁之间形成mg含量低或纯zn的第一镀层110时,可以提高镀层的粘附性。此外,第三镀层130可以抑制钢板表面发生黑变。mg是强氧化性元素,具有容易形成氧化物或氢氧化物的倾向,因此可能会改变表面的粗糙度,并且可能会发生黑变现象。通过将mg含量低的第三镀层作为最表面,可以防止黑变。此外,将第三镀层130的附着量控制在一定水平以上时,可以在镀覆钢板表面形成均匀的磷酸盐薄膜,因此用于汽车用途时可以期待优异的磷酸盐处理性和密封剂(sealer)粘附性。
[0037]
根据本发明的一个具体实施方案,获得所述第二镀层120所带来的提高耐蚀性的效果的第二镀层120的附着量可以为8g/m2以上。但是,当第二镀层的附着量过大时,其它镀层的附着量相对减少,不仅难以获得由此带来的有利的效果,而且焊接时熔融的镀液的熔点降低,可能容易受到lme的影响,因此所述第二镀层120的附着量可以限制为16g/m2以下。根据本发明的另一个具体实施方案,所述第二镀层120的附着量可以为9-15g/m2,在又一个具体实施方案中,所述第二镀层120的附着量可以为11-13g/m2。
[0038]
此外,为了期待第一镀层110和第三镀层130的作用,这些镀层的附着量可以分别为3g/m2以上。但是,当这些镀层的附着量过度增加时,第二镀层120的附着量可能会受到限制,因此这些镀层的附着量的上限可以分别设定为14g/m2,在一个具体实施方案中,这些镀层的附着量的上限也可以设定为10g/m2。本发明的另一个具体实施方案中,所述第一镀层110和所述第三镀层130中的一个或全部的附着量可以分别为3-10g/m2,在又一个具体实施方案中,所述第一镀层110和所述第三镀层130中的一个或全部的附着量可以分别为6-8g/m2。
[0039]
在组成方面,与常规的热浸镀锌(gi)钢板相比,本发明的所述锌系镀层可以有效地防止焊接时的lme。原因在于,常规的热浸镀锌钢板包含少量的铝,由于所述铝而形成阻
碍镀层和基材铁之间的合金化的抑制层(inhibition layer)。在这种抑制层的存在下进行点焊时,与铁的合金化延迟,因此形成低熔点的熔融镀液,可能容易渗透到晶界,但如本发明所示存在包含mg的合金层时,不形成抑制层,促进与铁的合金化,从而镀层(熔融镀液)的熔点升高,因此可以有效地防止lme。
[0040]
如上所述,本发明的一个具体实施方案的镀锌系钢材具有高的抗lme裂纹性,因此可以具有优异的点焊性,例如,根据sep 1220-2标准进行点焊时,b型裂纹的平均长度可以控制在基材铁厚度的0.1倍以下。
[0041]
本发明的一个具体实施方案的镀锌系钢材可以通过包括真空沉积(vacuum deposition)等的物理气相沉积(pvd)等方法对钢板表面进行沉积镀覆来制造,但并不必须限定于此。真空沉积法是指在真空室内加热涂覆物质而形成蒸汽,将所述蒸汽喷射到基材铁的表面以实现沉积的方法,下面进行更详细的说明。利用物理气相沉积的情况下,可以减少或防止在热浸镀过程中发生的抑制层的形成。所述抑制层起到在焊接等加热过程中抑制基材铁和镀层之间的合金化的作用,从而起到增加镀层保持低熔点的状态的时间的作用,因此不利于确保焊接性。但是,如上所述,真空沉积等物理气相沉积法减少或防止抑制层,从而容易形成熔点比锌熔点(419℃)高的fe
11
zn
40
等fe-zn合金相,因此通过物理气相沉积法形成的镀层可以更有利于确保点焊性。
[0042]
通过如上所述的真空沉积制造镀锌系钢材时,由于沉积工艺的特性,在镀层的表面方向上颗粒形成为柱状,形成所谓的柱状颗粒,在这种情况下,颗粒和颗粒之间不致密,因此冲压成型等成型时可能会发生拉毛(galling)现象。但是,根据本发明的一个具体实施方案,当包括包含0.4-0.9重量%的mg的镀层作为多层镀层中的一层时,可以显著改善拉毛现象。即,当镀层中包含少量mg时,镀层的硬度上升,从而可以防止发生拉毛。
[0043]
根据本发明的具体实施方案的镀锌系钢材可以通过各种方法制造,对其制造方法不作特别限制。但是,根据一个具体实施方案,组成所述多层锌系镀层的有区别的镀层中的至少一个层可以通过物理气相沉积(pvd)法形成,优选可以通过真空沉积法形成。在这种情况下,通过所述物理气相沉积法形成的镀层可以是包含0.4重量%以上的mg的层(根据一个具体实施方案,该层是第二镀层)。此外,根据本发明的一个具体实施方案,组成所述多层锌系镀层的有区别的镀层全部可以通过物理气相沉积形成,优选可以通过真空沉积法形成。具体地,根据一个具体实施方案,本发明的锌系镀层可以通过如下的方法制造。
[0044]
首先,准备基材铁,利用14重量%以上的hcl水溶液进行酸洗,并进行冲洗及干燥,然后利用等离子体和离子束等去除表面的异物和天然氧化膜,然后依次形成多层镀层,从而可以制造本发明的镀锌系钢材。
[0045]
此时,多层镀层的各层可以通过电镀法或常规的真空沉积法,例如电子束法、溅射法、热蒸发法、感应加热蒸发法、离子镀法等形成,但是其中的mg镀层或zn-mg合金镀层的情况下,也可以通过具有电磁搅拌(electromagnetic stirring)效果的电磁加热物理气相沉积法形成。
[0046]
其中,电磁加热物理气相沉积法(electro-magnetic heating physical vapor deposition)利用如下现象:将高频电源施加到产生交流电磁场的一对电磁线圈而产生电磁力时,涂覆物质(本发明中为zn、mg或者zn-mg合金)在由交流电磁场包围的空间中被加热,被加热的涂覆物质产生大量的沉积蒸气(金属蒸气),图4中示出用于这种电磁加热物理
气相沉积的装置的示意图。参照图4,通过如上所述的方法形成的大量的沉积蒸气通过蒸气分配箱(vapor distribution box)的多个喷嘴高速喷射到基材铁的表面而形成镀层。
[0047]
在常规的真空沉积装置中,坩埚内部具备涂覆物质,通过加热这种具备涂覆物质的坩埚来实现涂覆物质的汽化,在这种情况下,由于坩埚的熔融、坩埚引起的热损失等,难以向涂覆物质本身供应充足的热能。因此,不仅沉积速度慢,而且在使组成镀层的晶粒尺寸微细化方面也存在一定的局限性。此外,如本发明所示想要沉积zn-mg合金蒸气时,在确保镀层的均质性方面也存在一定的局限性。
[0048]
但是,与此不同,通过电磁加热物理气相沉积法进行沉积时,与常规的真空沉积法不同,由于没有温度的约束条件,可以将涂覆物质暴露在更高的温度下,因此可以进行高速沉积,而且具有可以实现组成最终形成的镀层的晶粒尺寸的微细化和镀层内合金元素分布的均质化的优点。
[0049]
沉积工艺时,真空沉积室内部的真空度优选调节为1.0
×
10-3
毫巴(mbar)至1.0
×
10-5
毫巴的条件,在这种情况下,可以有效地防止在镀层形成过程中形成氧化物而导致的脆性增加和物理性能降低。
[0050]
沉积工艺时,加热的涂覆物质的温度优选调节为700℃以上,更优选调节为800℃以上,进一步优选调节为1000℃以上。当加热的涂覆物质的温度低于700℃时,可能难以充分确保晶粒微细化和镀层均质化效果。另外,加热的涂覆物质的温度越高,越有利于实现所期望的技术效果,本发明中对该温度的上限不作特别限定,但该温度为一定水平以上时,不仅其效果饱和,而且工艺成本过高,考虑到这些情况,可以将该温度的上限限定为1500℃。
[0051]
沉积前后的基材铁的温度优选调节为100℃以下,当该温度超过100℃时,由于钢板宽度方向的温度的不均匀性,宽度方向上发生弯曲,从而通过出口侧多级分级减压系统时可能阻碍真空度的保持。
具体实施方式
[0052]
以下,通过实施例对本发明进行更具体的说明。但是,需要注意的是,下述实施例并不限制本发明的权利范围。这是因为本发明的权利范围由权利要求书中记载的内容和由此合理推导的内容所确定。
[0053]
(实施例)
[0054]
准备厚度为1.4mm的汽车用高强度冷轧钢板,以重量%计,所述冷轧钢板包含:c:0.18%、si:1.5mn:3.5%、al:0.01p:0.006%、s:0.003%、余量的fe和不可避免的杂质,并且利用图4的装置(真空度为3.2
×
10-3
毫巴)制造具有下表1中所示的条件的多层镀层的多层镀锌系钢材。在所有实例中,在单独的真空室中通过单独的工艺获得各层的镀层,在形成各层的镀层时,施加到一对电磁线圈的电流为1.2ka,以2kg的沉积物质为基准,施加到一对电磁线圈的频率为60khz,加热的涂覆物质的温度为1000℃,蒸气分配箱的温度恒定为900℃。此外,各层的镀层沉积前后的基材铁的温度恒定为60℃。
[0055]
接着,通过电感耦合等离子体(inductively coupled plasma,icp)法测量制得的多层镀锌系钢材的附着量和mg重量比。更具体地,切割成尺寸为80mm
×
80mm的试片,对表面进行脱脂,然后利用高精度秤进行一次称重(w1:0.0000g)。之后,利用夹具将直径(dia)为54.5mm的o形圈(o-ring)专用柱附着在前面,并使其紧密粘附,以防止溶液泄露。之后,加入
30毫升(cc)的1:3hcl溶液,然后加入2-3滴抑制剂(inhibiter)。在表面产生h2气体的过程结束后,将溶液收集在100毫升量瓶中。此时,利用洗涤瓶收集表面的所有余量,收集100毫升以下。之后,将试片完全干燥,然后进行二次称重(w2),将一次称重值与二次称重值之差除以单位面积的值作为总附着量。另外,将收集的溶液作为对象,通过icp法测量mg含量,并将其作为mg重量比,将该结果一同示于表1中。如表1所示,第一镀层和第三镀层是纯zn镀层,具有实质上不包含除zn以外的其它元素的组成,第二镀层具有进一步包含mg的zn-mg合金组成。
[0056]
接着,对制得的多层镀锌系钢材的焊接性、耐蚀性、密封剂粘合性、磷酸盐处理性和耐黑变性进行评价,并将该结果示于下表2中。
[0057]
更具体地,对于耐蚀性,将各多层镀锌系钢材切割成尺寸为75mm
×
150mm的试片,然后根据jis z2371进行盐雾试验来测量初期红锈产生时间,并按照下述的基准进行评价。
[0058]
1.优异:与单面附着量为60g/m2的镀锌钢板(gi钢板)相比,红锈产生时间为2倍以上的情况
[0059]
2.普通:与单面附着量为60g/m2的镀锌钢板(gi钢板)相比,红锈产生时间为同等水平或小于2倍的情况
[0060]
3.不良:与单面附着量为60g/m2的镀锌钢板(gi钢板)相比,红锈产生时间更短的情况
[0061]
对于焊接性,根据sep 1220-2标准,切割成尺寸为40mm
×
120mm的试片,对各试片进行总共100次点焊,然后测量b型裂纹的有无及其尺寸,并按照下述的基准进行评价。
[0062]
1.非常优异:所有试片中没有产生b型裂纹的情况
[0063]
2.优异:一部分或者所有试片中产生b型裂纹,并且b型裂纹的平均长度为基材铁(冷轧钢板)厚度的0.1倍以下的情况
[0064]
3.普通:一部分或者所有试片中产生b型裂纹,并且b型裂纹的平均长度超过基材铁(冷轧钢板)厚度的0.1倍且0.2倍以下的情况
[0065]
4.不良:一部分或者所有试片中产生b型裂纹,并且b型裂纹的平均长度超过基材铁(冷轧钢板)厚度的0.2倍的情况
[0066]
另外,对于抗拉毛性,通过在涂油的状态下使镀铬的冷加工用模具钢材质的钢球以5mpa的载荷和200mm/秒的速度在试片上旋转的同时测量直到摩擦系数超过0.3时的摩擦旋转数来进行确认。
[0067]
1.优异:直到摩擦系数超过0.3时的摩擦旋转数为80次以上
[0068]
2.普通:直到摩擦系数超过0.3时的摩擦旋转数为60次以上且小于80次
[0069]
3.不良:直到摩擦系数超过0.3时的摩擦旋转数小于60次
[0070]
为了确认镀覆粘附性,将多层镀锌系钢材切割成尺寸为40mm
×
80mm的试片,然后将试片安装在冲压试验机并进行60
°
弯曲试验,然后将试片从试验机取下,在弯曲的部分贴上玻璃纸胶带并取下胶带,然后将取下的胶带贴在白纸上并测量剥离宽度,并且按照下述的基准进行评价。
[0071]
1.优异:剥离宽度为6.0mm以下的情况
[0072]
2.普通:剥离宽度为超过6.0mm且8.0mm以下的情况
[0073]
3.不良:剥离宽度超过8.0mm的情况
[0074]
对于磷酸盐处理性,将多层镀锌系钢材切割成尺寸为75mm
×
150mm的试片,然后根据常规的汽车公司标准进行表面调整和磷酸盐处理,然后评价磷酸盐均匀度。
[0075]
1.良好:形成均匀的磷酸盐薄膜
[0076]
2.不良:形成不均匀的磷酸盐薄膜
[0077]
对于耐黑变性,将多层镀锌系钢材切割成尺寸为75mm
×
150mm的试片,然后在保持50℃和95%的相对湿度(rh)的恒温恒湿器中以10-20kgf/cm的压力加压粘附的试片放置120小时,测量实验前后的颜色变化(
△
e),并按照下述的基准进行评价。
[0078]
1.良好:
△
e≤3
[0079]
2.普通:3《
△
e≤5
[0080]
3.不良:
△
e》5
[0081]
[表1]
[0082]
其中,
①
:整个镀层中的mg含量,
②
:整个镀层的附着量,
③
:镀层的层数量,
④
:第一镀层的mg含量,
⑤
:第一镀层的附着量,
⑥
:第二镀层的mg含量,
⑦
:第二镀层的附着量,
⑧
:第三镀层的mg含量,
⑨
:第三镀层的附着量。此外,含量是以重量%为基准,附着量是以g/m2为基准。
[0083]
[表2]
[0084]
从所述表1的条件和表2的结果可以确认,实例1是整个镀层中的mg含量小于本发明的一个具体实施方案的范围的情况,可以确认耐蚀性不足。此外,实例2是整个镀层中的mg含量过多的情况,虽然耐蚀性充分,但容易发生lme,因此显示出差的点焊性。
[0085]
实例3是整个镀层的附着量小的情况,无法显示出充分的耐蚀性,而且实例4的整个镀层的附着量过多,因此点焊性不良。实例8和实例44是第一镀层的镀覆附着量小的情况,其结果,镀覆粘附性为2级或3级。
[0086]
实例9是第一镀层的mg含量过多的情况,这也导致镀覆粘附性差的结果。
[0087]
实例45是第一镀层和第三镀层的附着量小的情况,显示出镀覆粘附性和耐黑变性不足的结果。实例46是第一镀层和第三镀层的附着量不足且第二镀层的mg含量也低的情况,显示出磷酸盐处理性、耐黑变性和耐蚀性不足的结果。此外,实例47和实例50是第三镀层的附着量不足的情况,显示出耐黑变性和耐蚀性不足的结果。实例51是整个镀层中的mg含量过多且第三镀层的附着量不足的情况,显示出点焊性略微不足的结果。
[0088]
实例12是第三镀层的mg含量高的情况,显示出耐黑变性不优异的结果。
[0089]
此外,实例5是第二镀层的附着量小于本发明中规定的值的情况,其结果,与满足规定值的情况相比,显示出耐蚀性略微不足的结果(2级)。实例6是第二镀层的mg含量不足的情况,可以确认在这种情况下,与满足规定值的情况相比,耐蚀性也略微不足(2级)。另一方面,实例7是第二镀层的mg含量过多的情况,虽然耐蚀性优异,但点焊性为2级。
[0090]
实例10是第三镀层的镀覆附着量不足的情况,显示出耐黑变性为2级。实例11是第三镀层的附着量过多的情况,显示出镀覆的抗拉毛性为2级的结果。
[0091]
另一方面,在满足本发明中规定的所有条件的其余实例中,可以获得耐蚀性、点焊性、磷酸盐处理性、抗拉毛性、镀覆粘附性和耐黑变性均为最佳的结果。因此,可以确认本发明的有利的效果。
再多了解一些
本文用于企业家、创业者技术爱好者查询,结果仅供参考。