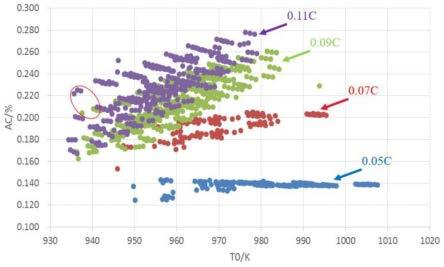
1.本发明涉及一种新型高强高韧抗氢脆钢板及其成分优选和制备方法,属于高强度钢板技术领域。
背景技术:
2.随着工程设备逐渐向大型化、轻量化发展,所采用钢的强度级别相应提升。采用屈服强度1000mpa级的超高强度钢制造工程机械的梁结构、汽车车体、海洋工程等设备构件,除了能满足其对强度的要求外,还能减轻设备自重,减少燃料消耗,提高工作效率。同时钢材的壁厚减小,既有利于降低焊接难度和提高焊接效率,又可以使钢结构的重心下移,安全性得到提高。而韧性作为强度和塑性的综合表现,体现了材料在变形过程吸收变形的能力,其中冲击韧性更是反映了其对外来冲击负荷的抵抗能力,高的冲击韧性可以延长钢结构在低温环境中的服役寿命。
3.目前,国内生产屈服强度1000mpa级的高强度钢板的企业逐渐增多,所采用的成分、工艺各不相同。但是通常是在碳素钢基础上通过添加少量微合金nb、v和ti等元素,结合优化的控轧控冷工艺(tmcp技术)和淬火 回火工艺,可生产出满足需求的超高强度钢板。公开号为cn104561827a和cn102560274a的专利文献公开了一种屈服强度1000mpa级高强度钢板及其制造方法,采用的是再加热淬火 回火工艺,但是钢板韧性较低,强韧性匹配不佳。公开号为cn106086657a和cn104532156a的专利文献公开了屈服强度大于1300mpa的超高强钢,其碳含量分别达到0.18~0.23%和0.21~0.26%,高的碳含量会使超高强钢的焊接裂纹敏感性增加,焊接冷裂纹倾向大,增加焊接难度。
4.由于超高强钢苛刻的使用环境和受力条件,除高强度、高韧性外、良好的抗氢脆性也是影响高强钢广泛应用的重要因素,尤其是屈服强度1000mpa级的高强钢,即使在较低的氢含量下也极易发生氢致延迟断裂,对工程结构的安全性和可靠性造成严重威胁。从生产制造到服役,氢原子无处不在,为此对高强钢进行严格的氢脆敏感性评估至关重要。检索强度级别相近钢种的相关技术文献发现,目前报道的高强钢均局限于强塑性,并未进行相应的氢脆敏感性评估,无法准确保证服役安全性。因此,加速开发兼具高强度、高低温韧性及良好抗氢脆性能的新型钢铁材料对于工程建设具有重大意义,成为急需解决的技术问题。
技术实现要素:
5.为了解决现有技术问题,本发明的目的在于克服已有技术存在的不足,提供一种高强高韧抗氢脆钢板及其成分优选和制备方法,解决了在控制成本和保证焊接性的前提下,如何选取恰当的目标成分,使其能够在淬火和高温回火工艺条件下,实现兼具屈服强度不低于1000mpa的高强度、在-40℃下冲击功不低于69j的高的低温韧性及氢脆敏感性不高于20%的问题。本发明提高了高强高韧抗氢脆钢板的综合性能,实现了新型高强高韧抗氢脆钢板材料的短周期研发。
6.为达到上述发明创造目的,本发明采用如下技术方案:
7.一种高强高韧抗氢脆钢板,按照质量百分比计算,其主要的各组分化学成分及比例如下:
8.c:0.089-0.110%,si:0.06-0.08%,mn:0.80-1.10%,cr:0.35-0.60%,ni:2.0-2.50%,cu:0.85-1.10%,mo:0.50-0.60%,nb:0.04-0.06%,余量为fe和不可避免的杂质;采用冶炼工艺制备铸锭,然后进行热轧、淬火和高温回火热处理;在进行热轧时,通过多道热轧将其轧至厚度不大于14mm,控制初轧温度为1150~1200℃,终轧温度为950~1000℃;在进行热处理时,控制淬火温度为850-870℃,淬火后降温至室温,然后控制回火温度为500-580℃,进行回火热处理,再空冷至室温,得到所述高强高韧抗氢脆钢板。
9.优选地,所述高强高韧抗氢脆钢板,按照质量百分比计,其主要的各组分化学成分如下:
10.c:0.089-0.108%,si:0.067-0.080%,mn:0.84-1.05%,cr:0.37-0.57%,ni:2.10-2.42%,cu:0.87-1.09%,mo:0.52-0.60%,nb:0.043-0.056%,余量为fe和不可避免的杂质。
11.优选地,所述高强高韧抗氢脆钢板的屈服强度不低于1000mpa,抗拉强度不低于1000mpa,延伸率不低于15%,在-40℃下的冲击韧性不低于69j,氢脆敏感性指数hei不高于20%。
12.进一步优选地,所述高强高韧抗氢脆钢板的屈服强度不低于1042mpa,抗拉强度不低于1079mpa,延伸率不低于15.8%,在-40℃下的冲击韧性不低于82j,氢脆敏感性指数hei不高于15.4%。
13.一种本发明所述高强高韧抗氢脆钢板的制备方法,采用冶炼工艺制备铸锭,然后进行热轧、淬火和高温回火热处理;在进行热轧时,通过多道热轧将其轧至厚度不大于14mm,控制初轧温度为1150~1200℃,终轧温度为950~1000℃;在进行热处理时,控制淬火温度为850-870℃,淬火后降温至室温,然后控制回火温度为500-580℃,进行回火热处理,再空冷至室温,得到所述高强高韧抗氢脆钢板;
14.所述制备的目标高强高韧抗氢脆钢板的主要的各组分化学成分及比例如下:
15.c:0.089-0.110%,si:0.06-0.08%,mn:0.80-1.10%,cr:0.35-0.60%,ni:2.0-2.50%,cu:0.85-1.10%,mo:0.50-0.60%,nb:0.04-0.06%,余量为fe和不可避免的杂质。
16.优选地,冶炼工艺过程采用真空感应熔炼炉进行熔炼,然后制备铸锭,再将铸锭切成厚度不低于40mm的钢块,将钢块作为热轧的钢材。
17.优选地,热处理过程是将热轧钢板加热至850~870℃单相区进行保温至少25min后,然后进行水淬在降温至室温,再加热至500~580℃保温至少35min后,再空冷至室温。
18.一种本发明所述高强高韧抗氢脆钢板的成分筛选方法,在控制成本和保证焊接性的前提下,选取目标成分,包括如下步骤:
19.a.拟定目标钢板的基体化学成分范围:
20.按照质量百分比计算,初步拟定主要的各组分化学成分及比例如下:
21.c:0.05-0.11%,si:0.05-0.09%,mn:0.50-1.10%,cr:0.30-0.60%,ni:1.0-2.50%,cu:0.70-1.10%,mo:0.50-0.60%,余量为fe和不可避免的杂质;
22.b.确定特征参量并编写开展集成批量计算的程序文件:
23.利用thermo-calc计算软件包,采用其tc-python接口使用python语言编写可开展
在不同成分和温度条件下,计算特征参量的程序文件,其中,特征参量1为t0温度,代表奥氏体与铁素体吉布斯自由能相等时的温度,特征参量2为ac,代表t0温度下奥氏体中的含碳量;程序文件中的关键指令包括,读取热力学数据,完成不同合金体系特征参量1和特征参量2的热力学计算;采用循环语句实现合金成分和温度的自动赋值,完成批量计算;限定计算误差范围以获得有效数据,完成计算结果的输出;
24.c.确定计算条件,运行计算程序进行成分筛选:
25.基于步骤a确定的成分范围,设置各个合金元素的计算步长,采用步骤b中计算特征参量1和特征参量2的程序文件ⅰ,获得t0和ac的计算结果,在保持低t0温度基础上,选取具有高ac值的点作为目标成分;
26.d.运用第一性原理计算氢原子的偏聚能,确定微合金元素:
27.采用第一性原理计算氢原子在碳化物/基体界面的偏聚能(e
mc
),计算和比较待选的nb,v和ti微合金元素对应的碳化物nbc、tic、vc/基体界面的偏聚能,选择偏聚能最小的碳化物中的微合金元素作为合金添加元素,来优化在所述步骤a中拟定目标钢板的基体化学成分;
28.e.筛选出钢板基体和微合金成分:
29.根据所述步骤d确定微合金元素,将确定微合金元素添加到拟定目标钢板的基体化学成分,重新确定目标钢板的基体化学组分和成分比例范围,用于制备目标高强高韧抗氢脆钢板。
30.优选地,在所述步骤d中,nb、v和ti微合金元素的添加可以产生析出强化和细晶强化的效果,不过,ti容易和氮结合,形成方形tin或ti(c,n)颗粒,影响塑韧性。此外,由于nbc、vc和tic均对氢原子有较强的吸附能力,可作为氢陷阱捕获氢原子,抑制氢的扩散偏聚,提高钢的抗氢脆性。本发明采用第一性原理计算氢原子在碳化物/基体界面的偏聚能。从半共格失配位错界面确定的偏聚能可发现:e
nbc
(-0.99ev)<e
tic
(-0.52ev)<e
vc
(-0.31ev),即nbc/fe界面吸氢所需要的能量最小,即吸氢能力最强,能有效抑制钢中氢原子的扩散。此外,本发明创新性地采用第一性原理计算了nb-v和nb-ti复合添加时偏聚能的变化,即,氢原子在半共格(nb,v)c/fe界面和(nb,ti)c/fe界面的偏聚能,计算得其偏聚能为-0.42ev和-0.34ev,由此可见,nbc比(nb,v)和(nb,ti)c对氢原子的吸附力更强,更有利于提高钢的抗氢脆性。因此添加nb微合金以改善钢的综合性能。
31.在完成本发明高强高韧抗氢脆钢板的成分优选后,根据优选出的基体和微合金成分,制备目标实验钢。经过冶炼、热轧、淬火 高温回火热处理,淬火温度为850~870℃,回火温度为500~580℃可获得屈服强度在1000mpa以上,在-40℃冲击功在69j以上,氢脆敏感性小于20%的新型高强高韧抗氢脆钢板。
32.本发明的原理:
33.一种高强高韧抗氢脆钢板的成分筛选方法,在保证焊接性以及降低成本的前提下,通过对特征参量的热力学计算和第一性原理计算,筛选基体成分和微合金成分,从而获得屈服强度达到1000mpa以上,-40℃冲击功在69j以上,氢脆敏感性小于20%的新型高强高韧抗氢脆钢板。
34.高强高韧钢由普通碳素钢发展而来,通常添加ni、cr、mo、si、mn、cu等合金元素达到预期性能。其中,碳含量增加可以显著提高强度,但会造成焊接性等服役性能下降,镍含
量增加,有利于改善其强塑性,但会增加成本。此外,c、ni、mn、cu为奥氏体形成元素,而si、cr、mo为铁素体形成元素,t0温度标志着铁素体和奥氏体自由能相等时的温度,奥氏体形成元素会导致该温度下降,意味着淬火后获得马氏体的强度提升,而铁素体形成元素会则会起到相反的作用;不过,t0温度时奥氏体中碳元素的含量(ac)则会由于铁素体形成元素的存在而增加,该影响会造成奥氏体稳定性提高,有利于保证塑韧性。可以看出,采用t0温度和ac可以作为特征参量以综合评估不同合金成分对实验钢强韧性可能造成的影响。
35.前已提及,nb、v和ti微合金元素的添加除了可产生析出强化和细晶强化的效果外,还可以作为氢陷阱抑制氢的扩散,提高钢的抗氢脆性。因此,以氢原子在碳化物/基体界面的偏聚能作为另一特征参量,采用第一性原理开展对nb、v和ti以及复合碳化物的计算,可以评估不同微合金元素对实验钢抗氢脆能力可能造成的影响。
36.基于此,本发明采用thermo-calc计算软件包开展对不同成分合金t0温度以及t0温度时奥氏体中碳含量ac的批量计算,以t0温度较低和ac较高为目标,进行基体成分优选,同时,采用第一性原理计算,以偏聚能最低为目标,确定理想微合金元素。
37.钢铁材料传统的研发模式秉承“试错法”的思路开展成分优选,以获得所期望的性能,这种方法耗时长、成本高、效率低,严重制约了新钢种的研发进度。本发明可应用相图热力学计算和第一性原理计算实现了新型高强高韧抗氢脆钢板目标成分的科学设计和验证,完成短周期制备,是本发明的独创性工作。
38.本发明与现有技术相比较,具有如下显而易见的突出实质性特点和显著优点:
39.1.本发明设计的新型高强高韧抗氢脆钢板成分合理,具备高强度、高韧性、良好的抗氢脆性,能应用于苛刻的使用环境和受力条件中,准确保证服役安全性,开拓新型高强高韧抗氢脆钢板的应用领域;
40.2.本发明能加速开发兼具高强度、高低温韧性及良好抗氢脆性能的新型钢铁材料,对于工程建设具有重大意义;
41.3.本发明方法简单易行,成本低,适合推广使用。
附图说明
42.图1为本发明中基体成分筛选过程中的数据点计算结果。
43.图2dft计算中关于(001)
α-fe
/(001)
mc
界面的三种高度对称的典型原子结构图。
具体实施方式
44.本发明一种高强高韧抗氢脆钢板,按照质量百分比计,其主要组分的化学成分及比例如下:
45.c:0.089-0.110%,si:0.06-0.08%,mn:0.80-1.10%,cr:0.35-0.60%,ni:2.0-2.50%,cu:0.85-1.10%,mo:0.50-0.60%,nb:0.04-0.06%,余量为fe和不可避免的杂质;
46.采用冶炼工艺制备铸锭,然后进行热轧、淬火和高温回火热处理;在进行热轧时,通过多道热轧将其轧至厚度不大于14mm,控制初轧温度为1150~1200℃,终轧温度为950~1000℃;在进行热处理时,控制淬火温度为850-870℃,淬火后降温至室温,然后控制回火温度为500-580℃,进行回火热处理,再空冷至室温,得到所述高强高韧抗氢脆钢板。
47.在以下实施例中,所述高强高韧抗氢脆钢板,按照质量百分比计,其主要的各组分
化学成分如下:
48.c:0.089-0.108%,si:0.067-0.080%,mn:0.84-1.05%,cr:0.37-0.57%,ni:2.10-2.42%,cu:0.87-1.09%,mo:0.52-0.60%,nb:0.043-0.056%,余量为fe和不可避免的杂质。
49.以下结合具体的实施例子对上述方案做进一步说明,本发明的优选实施例详述如下:
50.在本实施例中,一种高强高韧抗氢脆钢板成分优选及制备方法,具体如下:
51.本实施例基于集成计算材料工程技术开展了新型高强高韧抗氢脆钢板的研发工作,创新性地选取t0温度为特征参量1,t0温度下奥氏体中碳元素含量ac为特征参量2,采用商用计算软件thermo-calc及接口程序,利用相图热力学计算进行基体合金成分的优选,并结合第一性原理计算氢原子与微合金碳化物的相互作用,确定理想微合金元素,具体包括以下步骤:
52.a、拟定实验钢板的基体化学成分范围:
53.按照质量百分比计,钢板的化学成分包括:c:0.05-0.11%,si:0.05-0.09%,mn:0.50-1.10%,cr:0.30-0.60%,ni:1.0-2.50%,cu:0.70-1.10%,mo:0.50-0.60%,余量为fe和不可避免的杂质;
54.其中,ni含量较低,有利于降低生产成本;碳含量小于0.11%,0.11%为gravile图中易焊接区碳含量上限。采用公式(1)对该成分范围碳当量进行了计算,发现成分范围内的碳当量在0.18到0.33之间,该成分范围正好处于gravile图中的易焊接区,便于大型结构的焊接;
55.c
eq
=c si/30 (cu mn cr)/20 ni/60 mo/15 v/10 5b
ꢀꢀꢀꢀꢀꢀ
(1)
56.b、确定特征参量并编写开展集成批量计算的程序文件:
57.利用thermo-calc计算软件包,采用其tc-python接口使用python语言编写可开展不同成分和温度条件下,计算特征参量的程序文件,其中,特征参量1为t0,代表奥氏体与铁素体吉布斯自由能相等时的温度,特征参量2为ac,代表t0温度下奥氏体中的含碳量;编写的程序文件可读取tc软件中的热力学数据,即tcfe10数据库,完成不同合金体系特征参量1和特征参量2的热力学计算,获得t0和ac随成分的变化规律;
58.采用python程序中的循环语句实现合金成分和温度的自动赋值,即按照下面表1中的计算步长、逐次对合金元素含量以及温度进行赋值,完成批量计算,限定计算误差范围以获得有效数据,完成计算结果的输出;
59.c、确定计算条件,运行计算程序进行成分筛选:
60.基于步骤a确定的成分范围,以一定步长将各合金元素范围进行划分,如表1所示,计算成分点共4
×3×4×3×4×2×
3=3456个,采用步骤b中集成计算特征参量1和特征参量2的程序文件,输入成分范围和步长,最终获得3456组t0和ac的计算结果,得到特征参量的计算值集合,计算结果如图1所示;
61.在保持低t0温度基础上,选取具有高ac值的点作为目标成分,如图1中圈中所示;
62.表1.各个合金元素的计算步长表
63.csimncunicrmo0.050.050.50.710.40.5
0.070.070.70.91.50.60.550.090.090.91.12 0.60.11 1.1 2.5
ꢀꢀ
64.d、运用第一性原理计算氢原子的偏聚能,确定微合金元素:
65.基于密度泛函理论(dft),采用第一性原理计算了(001)
α-fe
/(001)
mc
界面与氢的相互作用,以深入了解氢的捕获行为,m代表nb,v和ti微合金元素;
66.本实施例通过关注baker-nutting(n-b)取向关系((001)
fe
||(001)
mc and100.fe
||110.mc
)来计算α-fe和mc碳化物之间的相干和半相干界面对氢原子的捕获作用;
67.图2显示了dft计算中关于(001)
α-fe
/(001)
mc
界面的三种高度对称的典型原子结构:
68.(i)fe-on-c构型,其中fe原子位于c原子之上;
69.(ii)fe-on-m构型,其中fe原子位于nb原子之上;
70.(iii)桥接构型,其中fe原子有两个c原子和两个nb原子作为最近邻;
71.通过dft计算确定了三种构型下,氢在α-fe和vc,tic,nbc界面上的偏聚能,结果如表2所示;可见氢在(001)
α-fe
/(001)
nbc
界面的桥接构型中偏聚能最低,即nbc捕获氢原子的效果最为明显;
72.此外,本发明选取偏聚能最低的桥接构型,计算了nb-v复合碳化物(nb,v)c和nb-ti复合碳化物(nb,ti)c与氢的相互作用,计算结果在表2中所示,可以看出,氢原子在(001)
α-fe
/(001)
nbc
界面的偏聚能最低,说明nbc对氢原子的捕获作用最强,为此拟添加0.04-0.06%nb来提高钢的抗氢脆能力;
73.表2.氢原子在(001)α-fe/(001)mc界面的偏聚能表
74.捕氢界面构型氢原子偏聚能(ev)(001)fe/(001)ticfe-on-c-0.29 fe-on-ti-0.48 bridge-0.52(001)fe/(001)vcfe-on-c-0.12 fe-on-v-0.39 bridge-0.31(001)fe/(001)nbcfe-on-c-0.18 fe-on-nb-0.58 bridge-0.99(001)fe/(001)(nb,v)cbridge-0.42(001)fe/(001)(nb,ti)cbridge-0.34
75.本实施例采用第一性原理计算氢原子在碳化物/基体界面的偏聚能(e
mc
),结果表明,e
nbc
(-0.99ev)<e
tic
(-0.52ev)<e
vc
(-0.31ev),即nbc/fe界面吸氢所需要的能量最小,即吸氢能力最强,可以有效抑制钢中氢原子向晶界的偏聚;
76.进而,本实施例计算了氢原子在半共格(nb,v)c/fe界面和(nb,ti)c/fe界面的偏聚能分别为-0.42ev和-0.34ev,由此可见,nbc比(nb,v)c和(nb,ti)c对氢原子的吸附力更强,更有利于提高钢的抗氢脆性,因此添加nb微合金来改善钢的综合性能;
77.e、根据筛选出的基体和微合金成分,制备实验钢:
78.采用20kg真空感应熔炼炉制备铸锭而后切出厚度为40mm的钢块用于热轧;通过多道热轧将其轧至14mm,初轧温度为1150~1200℃,终轧温度在950~1000℃;目标成分和实测成分如表3所示;
79.表3.本实施例实验钢板成分(wt.%)和碳当量表
[0080][0081]
将热轧实验钢板加热至850-870℃单相区保温25min后水淬至室温,之后加热至500-580℃保温35min后空冷至室温,最终实验钢板可获得屈服强度1000mpa以上,-40℃冲击韧性69j以上,氢脆敏感性小于20%的优异性能,实验钢板热处理工艺及性能如表4所示:
[0082]
表4.本实施例实验钢板热处理工艺及力学性能表
[0083]
[0084]
由表4中的数据可知,采用本实施例中优选的成分所制备的实验钢屈服强度达到1000mpa以上,-40℃冲击韧性69j以上。
[0085]
结合阴极充氢,电解液:0.2mol/lh2so4 0.5g/l硫脲;充氢时间:24h;电流密度:2ma/cm2。和慢拉伸(应变率:1
×
10-5
/s)实验对经过860℃淬火 500℃回火的实验钢进行氢脆敏感性评估,充氢前后性能对比如表5所示:
[0086]
由表5中数据可知,实验钢的氢脆敏感性指数均小于20%。
[0087]
表5.本实施例钢板在500℃回火后充氢前后慢拉伸性能对比表
[0088][0089]
选取相似化学成分的钢种作为对比例,化学成分和碳当量如表6所示:与对比例相比,本发明所设计钢种的碳当量与其相当,甚者更低。
[0090]
表6.对比例成分及碳当量表
[0091][0092]
表7是本发明实施例与对比例1~5的力学性能对比。可以看出,对比例1的碳含量较低,因此屈服强度不理想。对比例2在对比例1的基础上通过nb-ti复合添加使其屈服强度有所改善,但韧性明显降低。对比例3和4同样是低碳的成分,但是增加了6-7%的ni来弥补强度损失,增加了生产成本。其中对比例3采用了nb-v复合添加,增加了钢的屈服强度,但韧性极低。对比例4屈服强度不理想,但韧性较好。对比例5增加了碳含量,并采用了v-ti复合添加,其屈服强度和韧性较好,但较高的碳含量可能导致焊接性降低。采用本发明设计的较低碳与镍含量的钢种,获得了理想的强度和低温韧性。
[0093]
表7.力学性能对比表
[0094]
[0095][0096]
此外,比较了实施例与同强度级别高强钢对比例5~8的抗氢脆性,如表8所示。
[0097]
表8.抗氢脆性能对比表
[0098][0099]
由上述结果可见,本实施例的氢脆敏感性均低于20%,具有良好的抗氢脆能力。而具有相同强度级别的四种对比例,经过电化学预充氢后,以低应变率进行慢拉伸表现出高达35~60%塑性损失,表现出的抗氢脆能力较低。对比例8采用nb-v复合添加,并且微合金元素含量大于本发明实施例中nb微合金元素含量,但其氢脆敏感性指数为37.0%,抗氢脆性比本专利钢种低。上述实施例解决了在控制成本和保证焊接性的前提下,如何选取恰当的目标成分,使其在淬火和高温回火工艺条件下实现兼具屈服强度》1000mpa的高强度、-40℃下冲击功》69j的高的低温韧性及氢脆敏感性小于20%的优异性能。上述实施例设计的钢材成分合理,本发明新型高强高韧抗氢脆钢板高强度、高韧性、良好的抗氢脆性,能应用于
苛刻的使用环境和受力条件中,准确保证服役安全性,开拓新型高强高韧抗氢脆钢板的应用领域;本发明上述实施例方法加速开发兼具高强度、高低温韧性及良好抗氢脆性能的新型钢铁材料对于工程建设具有重大意义。
[0100]
综上所述:上述实施例创新性地提出一种新型高强高韧抗氢脆钢板的成分优选及制备方法,在控制成本和保证焊接性的同时,具有高强度、高韧性和优良抗氢脆性的综合性能,在材料设计研究以及工程建设领域具有明显的应用参考价值。
[0101]
上面对本发明实施例结合附图进行了说明,但本发明不限于上述实施例,还可以根据本发明的发明创造的目的做出多种变化,凡依据本发明技术方案的精神实质和原理下做的改变、修饰、替代、组合或简化,均应为等效的置换方式,只要符合本发明的发明目的,只要不背离本发明的技术原理和发明构思,都属于本发明的保护范围。
再多了解一些
本文用于企业家、创业者技术爱好者查询,结果仅供参考。