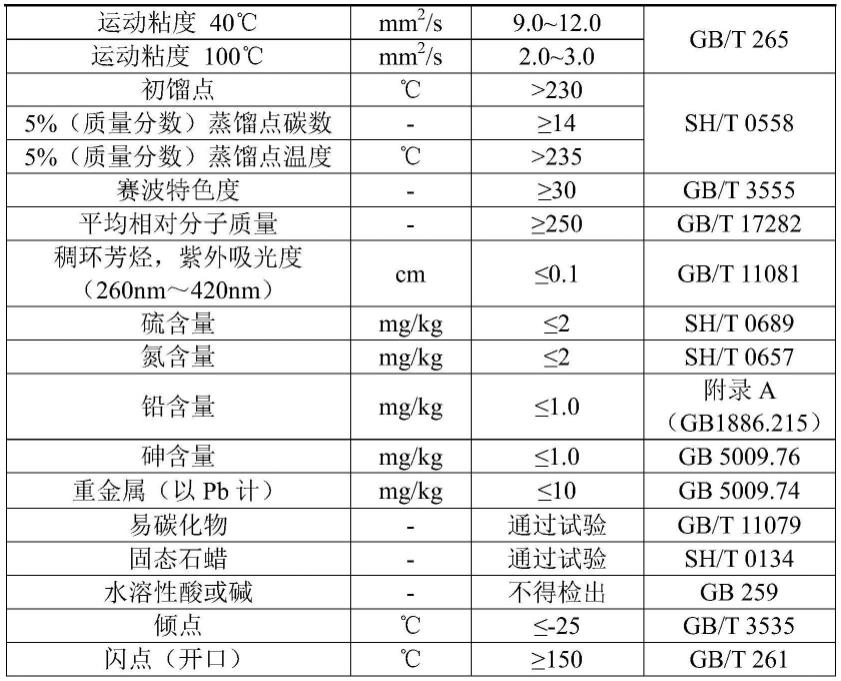
一种人造纤维用60n白油油剂及其制备方法
技术领域
1.本发明涉及白油制备技术领域,特别涉及一种人造纤维用60n白油油剂及其制备方法。
背景技术:
2.化纤油剂主要由平滑剂、乳化剂和抗静电剂等组成。白油作为开发较早而且廉价易得的一种原料,在化纤油剂中主要用做平滑剂。因不同纤维加工过程中对油剂要求不同,其相应的油剂所需的平滑剂也不相同。白油在涤纶dty油剂、涤纶fdy油剂、丙纶油剂、锦纶油剂、人造纤维油剂等中属于基础油,用量较大,其用量占油剂组成的30%~90%,甚至更高。华东和华南地区是国内化纤和纺织行业用油集中地,国内对白油的需求量有所增加,相应地,对白油性能提出了高要求。
3.白油经过二次加氢,通常芳烃含量较少,但易在后续切割过程中带入微量芳烃,或是常压蒸馏过程易引入杂质,杂质有效去除率降低,进而影响白油产品的品质,不能很好地达到作为人造纤维油剂的标准要求。
技术实现要素:
4.鉴于此,本发明的目的在于提出一种人造纤维用60n白油油剂及其制备方法,解决上述问题。
5.本发明的技术方案是这样实现的:
6.一种人造纤维用60n白油油剂的制备方法,包括以下步骤:
7.s1缓冲过滤:取原料油进行过滤,得除杂原料油;
8.s2预处理:通入氢气,将除杂原料油进行换热,换热温度为120~140℃,沉积20~30min后,得预处理原料油;
9.s3异构脱蜡反应:调节压力至18~19.5mpa,在预处理原料油中通入氢气,混合,加热至325~335℃,进行异构脱蜡反应,反应压力为14.5~15.5mpa,得异构脱蜡产物;
10.s4补充精制反应:通入氢气,将异构脱蜡产物进行补充精制反应,反应压力为14.5~15.5mpa,反应温度为250~280℃,得低芳烃产物;
11.s5冷高压分离:将低芳烃产物通过冷高压分离,分别获得气体和冷高压分离产物;
12.s6冷低压分离:将冷高压产物通过冷低压分离,获得冷低压分离产物;
13.s7常压回炼:将冷低压产物加热至285~290℃,得预热产物,进行常压蒸馏,得分馏产物;取分馏产物加入至预热产物混合,加入回炼助剂,进行常压蒸馏,得精产物;
14.s8成品:将精产物依次进行减压加热和减压蒸馏,得人造纤维用60n白油油剂。
15.进一步说明,步骤s7中,所述回炼助剂为质量比2~4:0.8~1.2:1~1.5的油酸镍、磺化树脂和二硫化碳组成;回炼助剂的加入量为120~160g/t。
16.进一步说明,所述加入回炼助剂,进行改性陶粒梯度过滤后,进行常压蒸馏。
17.进一步说明,所述梯度过滤为第一梯度过滤的改性陶粒孔径为65~85μm,第二梯
度过滤的改性陶粒孔径为50~60μm。
18.进一步说明,步骤s3中,所述在预处理原料油中通入氢气,混合,进行二次换热,二次换热温度为200~220℃,沉积15~25min后,加热至325~335℃。
19.进一步说明,步骤s7中,所述将冷低压产物加热至300~320℃前,还进行三次换热,三次换热温度为140~160℃,沉积15~25min。
20.进一步说明,所述三次换热温度为150℃,沉积20min。
21.进一步说明,步骤s5中,所述获得气体进行脱硫、压缩后,与原料氢混合,用于步骤s2除杂原料油的预处理;步骤s5中,所述获得气体进行脱硫、压缩后,分别用于步骤s3异构脱蜡反应和步骤s4精制反应。
22.与现有技术相比,本发明的有益效果为:
23.(1)本发明采用缓冲过滤、预处理、异构脱蜡反应、补充精制反应、冷高压分离、冷低压分离、常压回炼和成品的制备步骤,并严格控制反应条件,使获得的人造纤维用60n白油油剂运动粘度指标理想,稠环芳烃含量低,杂质(硫、氮、铅、砷等)含量低,倾点低、闪点(闭口)高,易碳化物和固态石蜡分析易通过,人造纤维用60n白油油剂符合人造纤维油剂的标准要求,该人造纤维用60n白油油剂可以作为人造纤维新型油剂,且人造纤维用60n白油油剂不再是单一的基础油,该产品可以充当环保的化工和机械的各个领域,真正达到了低芳烃溶剂油的标准,操作简单,适合工业化的大批量生产。
24.(2)此外,本发明通过增设常压回炼工艺,结合回炼助剂和梯度过滤方式,一方面可重新调节分馏进料组分,有利于调整分馏塔的部分汽液相平衡,并有助于控制后续减压部分的气液相负荷,调整减压塔内拔出速率从而达到精准控制产品的指标数值,另一方面可活化进料组分,进一步提高产品的品质,达到有效去除杂质的目的,极大地降低产品的重金属含量,符合国家标准要求,使产品收率高,成本较低。
25.(3)本发明还通过采用三次换热与沉积方式,有利于提高原料组分的热稳定性,避免因受空间位阻等效应,导致不能充分地进行原料油裂化、脱硫、除杂等反应,进而降低产品性质。
26.(4)本发明获得的人造纤维用60n白油油剂,用于人造纤维油剂的使用,能够改善产品的拉伸性能和耐磨性能,尤其是耐磨性能更加优异,有利于延长产品的使用寿命。
具体实施方式
27.为了更好理解本发明技术内容,下面提供具体实施例,对本发明做进一步的说明。
28.本发明实施例所用的实验方法如无特殊说明,均为常规方法。
29.本发明实施例所用的材料、试剂等,如无特殊说明,均可从商业途径得到。
30.本发明的改性陶粒经硝酸铁改性而得。
31.实施例1
32.一种人造纤维用60n白油油剂的制备方法,包括以下步骤:
33.s1缓冲过滤:取原料油进行过滤,得除杂原料油;
34.s2预处理:通入氢气,将除杂原料油进行换热,换热温度为130℃,沉积25min后,得预处理原料油;
35.s3异构脱蜡反应:调节压力至18.2mpa,在预处理原料油中通入氢气,混合,进行二
次换热,二次换热温度为220℃,沉积20min后,加热至330℃,进行异构脱蜡反应,反应压力为15.0mpa,得异构脱蜡产物;
36.s4补充精制反应:通入氢气,将异构脱蜡产物进行补充精制反应,反应压力为15.0mpa,反应温度为260℃,得低芳烃产物;
37.s5冷高压分离:将低芳烃产物通过冷高压分离,分别获得气体和冷高压分离产物;
38.所述获得气体进行脱硫、压缩后,与原料氢混合,用于步骤s2除杂原料油的预处理;所述获得气体进行脱硫、压缩后,分别用于步骤s3异构脱蜡反应和步骤s4精制反应;
39.s6冷低压分离:将冷高压产物通过冷低压分离,获得冷低压分离产物;
40.s7常压回炼:将冷低压产物进行三次换热,三次换热温度为150℃,沉积20min后,加热至285℃,得预热产物,进行常压蒸馏,得分馏产物;取分馏产物加入至预热产物混合,加入145g/t回炼助剂,进行常压蒸馏,得精产物;
41.所述回炼助剂为质量比3:1.0:1.2的油酸镍、磺化树脂和二硫化碳组成;
42.s8成品:将精产物依次进行减压加热和减压蒸馏,得人造纤维用60n白油油剂。
43.实施例2
44.一种人造纤维用60n白油油剂的制备方法,包括以下步骤:
45.s1缓冲过滤:取原料油进行过滤,得除杂原料油;
46.s2预处理:通入氢气,将除杂原料油进行换热,换热温度为120℃,沉积20min后,得预处理原料油;
47.s3异构脱蜡反应:调节压力至18mpa,在预处理原料油中通入氢气,混合,进行二次换热,二次换热温度为200℃,沉积15min后,加热至325℃,进行异构脱蜡反应,反应压力为14.5mpa,得异构脱蜡产物;
48.s4补充精制反应:通入氢气,将异构脱蜡产物进行补充精制反应,反应压力为14.5mpa,反应温度为250℃,得低芳烃产物;
49.s5冷高压分离:将低芳烃产物通过冷高压分离,分别获得气体和冷高压分离产物;
50.所述获得气体进行脱硫、压缩后,与原料氢混合,用于步骤s2除杂原料油的预处理;所述获得气体进行脱硫、压缩后,分别用于步骤s3异构脱蜡反应和步骤s4精制反应;
51.s6冷低压分离:将冷高压产物通过冷低压分离,获得冷低压分离产物;
52.s7常压回炼:将冷低压产物进行三次换热,三次换热温度为140℃,沉积15min后,加热至285℃,得预热产物,进行常压蒸馏,得分馏产物;取分馏产物加入至预热产物混合,加入120g/t回炼助剂,进行常压蒸馏,得精产物;
53.所述回炼助剂为质量比2:0.8:1的油酸镍、磺化树脂和二硫化碳组成;
54.s8成品:将精产物依次进行减压加热和减压蒸馏,得人造纤维用60n白油油剂。
55.实施例3
56.一种人造纤维用60n白油油剂的制备方法,包括以下步骤:
57.s1缓冲过滤:取原料油进行过滤,得除杂原料油;
58.s2预处理:通入氢气,将除杂原料油进行换热,换热温度为140℃,沉积30min后,得预处理原料油;
59.s3异构脱蜡反应:调节压力至19.5mpa,在预处理原料油中通入氢气,混合,进行二次换热,二次换热温度为210℃,沉积25min后,加热至335℃,进行异构脱蜡反应,反应压力
为15.5mpa,得异构脱蜡产物;
60.s4补充精制反应:通入氢气,将异构脱蜡产物进行补充精制反应,反应压力为15.5mpa,反应温度为280℃,得低芳烃产物;
61.s5冷高压分离:将低芳烃产物通过冷高压分离,分别获得气体和冷高压分离产物;
62.所述获得气体进行脱硫、压缩后,与原料氢混合,用于步骤s2除杂原料油的预处理;所述获得气体进行脱硫、压缩后,分别用于步骤s3异构脱蜡反应和步骤s4精制反应;
63.s6冷低压分离:将冷高压产物通过冷低压分离,获得冷低压分离产物;
64.s7常压回炼:将冷低压产物进行三次换热,三次换热温度为160℃,沉积25min后,加热至290℃,得预热产物,进行常压蒸馏,得分馏产物;取分馏产物加入至预热产物混合,加入160g/t回炼助剂,进行常压蒸馏,得精产物;
65.所述回炼助剂为质量比4:1.2:1.5的油酸镍、磺化树脂和二硫化碳组成;
66.s8成品:将精产物依次进行减压加热和减压蒸馏,得人造纤维用60n白油油剂。
67.实施例4
68.本实施例与实施例1的区别在于,步骤s7不同,具体步骤为:
69.s1缓冲过滤:取原料油进行过滤,得除杂原料油;
70.s2预处理:通入氢气,将除杂原料油进行换热,换热温度为140℃,沉积30min后,得预处理原料油;
71.s3异构脱蜡反应:调节压力至19.5mpa,在预处理原料油中通入氢气,混合,进行二次换热,二次换热温度为210℃,沉积25min后,加热至335℃,进行异构脱蜡反应,反应压力为15.5mpa,得异构脱蜡产物;
72.s4补充精制反应:通入氢气,将异构脱蜡产物进行补充精制反应,反应压力为15.5mpa,反应温度为280℃,得低芳烃产物;
73.s5冷高压分离:将低芳烃产物通过冷高压分离,分别获得气体和冷高压分离产物;
74.所述获得气体进行脱硫、压缩后,与原料氢混合,用于步骤s2除杂原料油的预处理;所述获得气体进行脱硫、压缩后,分别用于步骤s3异构脱蜡反应和步骤s4精制反应;
75.s6冷低压分离:将冷高压产物通过冷低压分离,获得冷低压分离产物;
76.s7常压回炼:将冷低压产物进行三次换热,三次换热温度为150℃,沉积20min后,加热至285℃,得预热产物,进行常压蒸馏,得分馏产物;取分馏产物加入至预热产物混合,加入145g/t回炼助剂,进行改性陶粒梯度过滤,第一梯度过滤的改性陶粒孔径为75μm,第二梯度过滤的改性陶粒孔径为55μm,过滤后,进行常压蒸馏,得精产物;
77.所述回炼助剂为质量比4:1.2:1.5的油酸镍、磺化树脂和二硫化碳组成;
78.s8成品:将精产物依次进行减压加热和减压蒸馏,得人造纤维用60n白油油剂。
79.实施例5
80.本实施例与实施例4的区别在于,步骤s3和步骤s7未进行换热处理,包括以下步骤:
81.s1缓冲过滤:取原料油进行过滤,得除杂原料油;
82.s2预处理:通入氢气,将除杂原料油进行换热,换热温度为130℃,沉积25min后,得预处理原料油;
83.s3异构脱蜡反应:调节压力至18.2mpa,在预处理原料油中通入氢气,混合,加热至
330℃,进行异构脱蜡反应,反应压力为15.0mpa,得异构脱蜡产物;
84.s4补充精制反应:通入氢气,将异构脱蜡产物进行补充精制反应,反应压力为15.0mpa,反应温度为260℃,得低芳烃产物;
85.s5冷高压分离:将低芳烃产物通过冷高压分离,分别获得气体和冷高压分离产物;
86.所述获得气体进行脱硫、压缩后,与原料氢混合,用于步骤s2除杂原料油的预处理;所述获得气体进行脱硫、压缩后,分别用于步骤s3异构脱蜡反应和步骤s4精制反应;
87.s6冷低压分离:将冷高压产物通过冷低压分离,获得冷低压分离产物;
88.s7常压回炼:将冷低压产物加热至285℃,得预热产物,进行常压蒸馏,得分馏产物;取分馏产物加入至预热产物混合,加入145g/t回炼助剂,进行改性陶粒梯度过滤,第一梯度过滤的改性陶粒孔径为75μm,第二梯度过滤的改性陶粒孔径为55μm,过滤后,进行常压蒸馏,得精产物;
89.所述回炼助剂为质量比3:1.0:1.2的油酸镍、磺化树脂和二硫化碳组成;
90.s8成品:将精产物依次进行减压加热和减压蒸馏,得人造纤维用60n白油油剂。
91.对比例1
92.本对比例与实施例4的区别在于,步骤s7不同,未设置回炼工艺,具体步骤为:
93.s1缓冲过滤:取原料油进行过滤,得除杂原料油;
94.s2预处理:通入氢气,将除杂原料油进行换热,换热温度为140℃,沉积30min后,得预处理原料油;
95.s3异构脱蜡反应:调节压力至19.5mpa,在预处理原料油中通入氢气,混合,进行二次换热,二次换热温度为210℃,沉积25min后,加热至335℃,进行异构脱蜡反应,反应压力为15.5mpa,得异构脱蜡产物;
96.s4补充精制反应:通入氢气,将异构脱蜡产物进行补充精制反应,反应压力为15.5mpa,反应温度为280℃,得低芳烃产物;
97.s5冷高压分离:将低芳烃产物通过冷高压分离,分别获得气体和冷高压分离产物;
98.所述获得气体进行脱硫、压缩后,与原料氢混合,用于步骤s2除杂原料油的预处理;所述获得气体进行脱硫、压缩后,分别用于步骤s3异构脱蜡反应和步骤s4精制反应;
99.s6冷低压分离:将冷高压产物通过冷低压分离,获得冷低压分离产物;
100.s7常压回炼:将冷低压产物进行三次换热,三次换热温度为150℃,沉积20min后,加热至285℃,加入145g/t回炼助剂,进行改性陶粒梯度过滤,第一梯度过滤的改性陶粒孔径为75μm,第二梯度过滤的改性陶粒孔径为55μm,过滤后,进行常压蒸馏,得精产物;
101.所述回炼助剂为质量比4:1.2:1.5的油酸镍、磺化树脂和二硫化碳组成;
102.s8成品:将精产物依次进行减压加热和减压蒸馏,得人造纤维用60n白油油剂。
103.对比例2
104.本对比例与实施例4的区别在于,步骤s7不同,采用油酸镍替换回炼助剂,具体步骤为:
105.s1缓冲过滤:取原料油进行过滤,得除杂原料油;
106.s2预处理:通入氢气,将除杂原料油进行换热,换热温度为140℃,沉积30min后,得预处理原料油;
107.s3异构脱蜡反应:调节压力至19.5mpa,在预处理原料油中通入氢气,混合,进行二
次换热,二次换热温度为210℃,沉积25min后,加热至335℃,进行异构脱蜡反应,反应压力为15.5mpa,得异构脱蜡产物;
108.s4补充精制反应:通入氢气,将异构脱蜡产物进行补充精制反应,反应压力为15.5mpa,反应温度为280℃,得低芳烃产物;
109.s5冷高压分离:将低芳烃产物通过冷高压分离,分别获得气体和冷高压分离产物;
110.所述获得气体进行脱硫、压缩后,与原料氢混合,用于步骤s2除杂原料油的预处理;所述获得气体进行脱硫、压缩后,分别用于步骤s3异构脱蜡反应和步骤s4精制反应;
111.s6冷低压分离:将冷高压产物通过冷低压分离,获得冷低压分离产物;
112.s7常压回炼:将冷低压产物进行三次换热,三次换热温度为150℃,沉积20min后,加热至285℃,加入145g/t油酸镍,进行改性陶粒梯度过滤,第一梯度过滤的改性陶粒孔径为75μm,第二梯度过滤的改性陶粒孔径为55μm,过滤后,进行常压蒸馏,得精产物;
113.s8成品:将精产物依次进行减压加热和减压蒸馏,得人造纤维用60n白油油剂。
114.一、品质检测
115.分别将获得的人造纤维用60n白油油剂进行品质检测,检测方法如下:
[0116][0117][0118]
结果如下表:
[0119][0120]
通过上表可知,本发明实施例1和实施例4获得的人造纤维用60n白油油剂,运动黏度、初馏点、5%蒸馏点碳数、稠环芳烃含量,以及硫、氮、铅、砷等含量、倾点和闪点(开口)的检测指标均符合人造纤维油剂的标准要求,该产品运动粘度指标理想,稠环芳烃含量低,杂质(硫、氮、铅、砷等)含量低,倾点低、闪点(闭口)高,该产品不再是单一的基础油,可充当环保的化工和机械的各个领域,真正达到了低芳烃溶剂油的标准,操作简单,适合工业化的大批量生产。
[0121]
实施例4与实施例1相比,通过常压回炼工艺中增设改性陶粒梯度过滤,可进一步降低稠环芳烃和重金属含量;实施例4与实施例5相比,采用三次换热与沉积方式,有利于避免空间位阻等效应,降低产品的稠环芳烃和硫含量,进一步提高产品品质。
[0122]
实施例4与对比例1和2相比,通过增设常压回炼工艺,结合回炼助剂和梯度过滤方式,有利于调整减压塔内拔出速率从而达到精准控制产品的指标数值,使运动粘度和闪点指标稳定,并有助于活化进料组分,达到有效去除杂质的目的,符合国家标准要求。
[0123]
二、性能测试
[0124]
采用本发明获得的人造纤维用60n白油油剂制备涤纶织物,依据《特种工业用绳带物理机械性能试验方法》(fz65002-1995)测试拉伸性能;依据《纺织品马丁代尔耐磨性的测定》(gb/t21196-1-2007)测试耐磨性能,采用市售白油作为对照品,结果如下表:
[0125]
项目断裂强力/n耐磨次数/104次实施例427843对照品26730
[0126]
由上表可知,本发明获得的人造纤维用60n白油油剂,用于人造纤维油剂的使用,能够改善产品的拉伸性能和耐磨性能,尤其是耐磨性能更加优异,有利于延长产品的使用寿命。
[0127]
以上所述仅为本发明的较佳实施例而已,并不用以限制本发明,凡在本发明的精神和原则之内,所作的任何修改、等同替换、改进等,均应包含在本发明的保护范围之内。
再多了解一些
本文用于企业家、创业者技术爱好者查询,结果仅供参考。