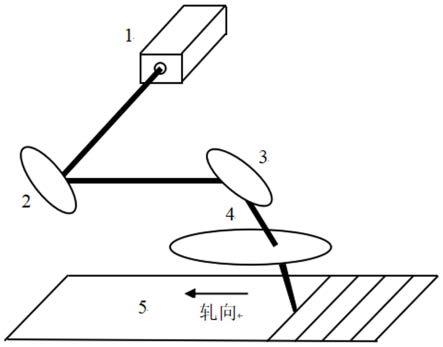
1.本发明属于取向硅钢制造技术领域,本发明涉及一种激光刻痕高磁感取向硅钢及其制造方法。
背景技术:
2.取向硅钢是用于制造变压器设备的基本材料,变压器因铁损而大量消耗电能,因此降低铁损是生产取向硅钢不懈追求的目标。硅钢片的铁损可分为磁滞损耗和涡流损耗,涡流损耗还可进一步分为经典涡流损耗(因涡流引起的)和异常涡流损耗(因磁壁运动引起的,正比于磁畴宽)。在工频条件下,异常涡流损耗约占铁损的一半左右。随着冶金工艺的发展,(110)[001]织构不断完善,在二次再结晶中势必引起晶粒生长过快,形成大晶粒,导致磁畴宽度增大,异常涡流损耗比例增加。在这种条件下,继续采用传统的冶金方法来进一步降低铁损,将是愈来愈困难。
[0003]
为了进一步细化磁畴来降低取向硅钢铁损,国内外很多钢铁企业或科研院所对细化磁畴技术展开了研究,先后开发了机械加工法、激光照射法、放电处理法、等离子流照射法、局部加热法、超声波振动和喷射流体法等表面处理技术,通过细化180
°
磁畴壁间距来细化磁畴,从而达到降低铁损的目的,其中以激光刻痕法最为突出。
[0004]
激光照射法是利用激光束的热量在钢板的表面之下产生一个弹性-塑性形变区域,通过在弹塑性形变区产生的压应力和刻痕间的张应力来减小取向硅钢主畴宽度,从而达到降低其涡流损耗的目的。这种方法由于大大降低了铁损,而且是非接触加工,具有非常高的可靠性和可控制性。为了保证铁损改善率,必须提供足够的照射能以保证合适的变形量,然而过高的照射能量密度又会损伤硅钢的表面涂层,甚至使钢板的平整面发生物理变形。能量密度很大程度上由激光功率和照射时间决定,通过降低能量密度能有效控制照射损伤,然而,必须保证最小的总热输入以产生足够的热变形。
[0005]
现有文献已提到的激光刻痕技术可以分为脉冲激光技术和连续波激光技术。脉冲激光方法能有效地得到钢板表面上的玻璃膜蒸发抗力,但由于表面绝缘涂层易遭到破坏而造成激光照射损伤,刻痕后需重新提供绝缘涂层,从而很不方便。传统脉冲式激光刻痕工艺主要通过减小激光功率来降低照射损伤,激光功率减小势必会伴随着入射热量的减小,导致变形不充分,进一步导致不好的铁损性能,从而铁损改善效果不明显。这种情况下,通常采用低扫描速度来延长激光束的照射时间以保证热输入,而降低扫描速度势必会牺牲机组的加工速度,不利于高速激光刻痕生产。
[0006]
专利文献cn1216072a公开了一种具有优良磁性能的晶粒取向性电工钢薄板及其生产工艺,采用长轴为钢板横向的椭圆形光斑照射,在钢板表面重叠形成连续脉冲光束,用脉冲激光照射减小180
°
磁畴壁间距提高磁性能;激光照射产生的周期闭合磁畴在轧制方向上的宽度≤150μm,在钢板厚度方向上的深度≥30μm,宽度和深度的乘积≥4500μm2,0.23mm板材的磁致收缩(λ19p-p压缩)≤0.9
×
10-6
,0.27mm板材的磁致收缩≤1.3
×
10-6
。该方法解决了传统脉冲激光法易对钢板表面薄膜造成照射损伤的问题;但是为了保证足够的能量积
累,扫描速度不能太快,从而限制了机组的激光刻痕速度,不能满足高速激光刻痕的要求。
[0007]
传统连续型激光技术采用瞬时功率较低的连续激光器,由于能量密度低,能有效控制激光照射损伤。但因其快速加热和快速冷却的能力与高峰值功率脉冲激光相比较小,从而造成变形的效率也低。因此,为了得到与通过脉冲激光方法相同的变形效率,必须提高照射面的能量;而提高照射面的能量密度又会出现钢板的平整面发生物理变形的新问题。这些物理变形表现为钢板上的翘曲或形成表面上的条纹,这种条纹对于铁磁性能和叠装性能都是不利的。另外,取向钢板的磁致伸缩在其用作变压器时与产生的噪声成正比,已经发现磁致伸缩与全部照射能有正向关系,提高照射能必然产生磁变形大的问题。
[0008]
专利文献cn1761764a公开了一种磁特性良好的方向性电磁钢板及其制造方法,通过被高度聚光的激光束的扫描照射来降低取向硅钢的铁损:将tem00模式的、振荡波长λ为1.07≤λ≤2.10μm的连续振荡光纤维激光,相对于钢板的轧制方向大致垂直、并且以大致一定的间隔扫描照射;照射光束的轧制方向聚光直径d(mm)、激光束的扫描线速度v(mm/s)、激光器的平均输出p(w)、形成的照射痕迹宽度或闭合磁畴宽度w1(mm)、照射痕迹的轧制方向间隔p1(mm)在以下的范围内:0<d≤0.20;0.001≤p/v≤0.012;0<w1≤0.20;1.5≤p1≤11.0。该方法由于采用振荡波长λ为1.07≤λ≤2.10μm的连续振荡光纤维激光,相比波长为10.6μm的co2连续激光来讲,激光能量向钢板的吸收量相对较低,不利于磁畴的有效控制,同时,该方法的激光照射法与通常相比中心附近的光束强度较高,根据情况不同有可能在激光照射后的表面产生凹凸,如果通过降低平均输出功率p来解决这一问题,相应的扫描速度v必须同步降低,势必会牺牲机组的加工速度。
[0009]
此外,专利文献cn1076492a公开了一种降低硅钢片铁损的激光处理方法及装置,该专利描述的装置较简单,且未涉及具体的实施工艺,铁损改善率仅在5%左右。专利文献cn1244597a公开了一种耐热型激光处理取向硅钢表面的方法,通过激光局域合金化处理优化磁畴分布降低铁损,然而该工艺需要先剥离绝缘涂层,刻痕处理后又需重新涂层,工艺复杂且不易实现,不适合于大生产生产。专利文献cn101348853公开了一种降低普通取向电工钢铁损的方法,但该方法严重破坏钢板表面涂层,刻痕后需重新涂层,操作很不方便。专利文献cn101209514公开了一种基于振镜阵列的激光在线高速刻痕装置,着眼点在激光刻痕的装置,未涉及刻痕工艺和产品。
技术实现要素:
[0010]
本发明的目的在于,提供一种激光刻痕高磁感取向硅钢及其制造方法,可以减小传统连续激光磁致伸缩增加的问题,且不会产生弯曲变形,刻痕后涂层不破坏,无需重新涂层,适用于高速、连续加工的激光加工步骤,可以保证产品优良的综合性能。
[0011]
本发明通过以下技术方案来实现:
[0012]
本发明的一种激光刻痕高磁感取向硅钢的制造方法,在取向硅钢表面进行激光刻痕,照射激光束为椭圆形光束,其长轴大致垂直于钢板的轧制方向,以大致相等的间距在钢板表面形成连续重叠照射,从而改善所述取向硅钢的铁损特性;其特征在于,所述照射激光束的激光源为co2气体连续波激光源,激光输出功率≤3000w,激光扫描速度≥150m/min,扫描间距为3~7mm;
[0013]
试验表明,在本发明的激光刻痕参数下,可以既能保证铁损改善率稳定在7%~
14%,又不牺牲硅钢的表面质量和磁致伸缩性能,刻痕产品表面照射能量密度不会超过钢板表面绝缘涂薄膜的损伤阀值,产品表面不会产生照射损伤;而扫描间距3~7mm可以获得铁损降低最大值,太小会导致刻痕应力对磁性的劣化,抵消了磁畴宽度变小的改善效果,太大则磁畴宽度变小的程度对磁性改善效果不明显。
[0014]
优选地,所述照射激光束的长轴平行于板宽方向,影响照射能量密度,从防止激光照射损伤和降低铁损的角度上讲,其长度为6.0~10.0mm;短轴平行于轧制方向,影响铁损改善率和磁致伸缩性能,其宽度为0.20~0.30mm。
[0015]
优选地,所述co2气体连续波激光源的波长为10.6μm,
[0016]
优选地,所述激光输出功率为1000~3000w;加热功率太大,会损坏绝缘涂层,甚至使带钢弯曲变形;加热功率太小,产生的残余应力不够起到细化磁筹的作用。
[0017]
优选地,所述激光扫描速度为150~350m/min,可以达到与机组的生产速度的最佳匹配,符合高速激光刻痕生产的要求;而同时,在不影响刻痕效果的前提下,为了提高产能,机组的生产速度越大越好,但要和扫描速度相匹配,优选为30~120m/min。
[0018]
采用本发明的方法制备的激光刻痕高磁感取向硅钢,通过连续激光照射减小180
°
磁畴壁间距提高磁性能,其特征在于,激光照射产生的周期闭合磁畴在轧制方向上的宽度为200~400μm,在钢板厚度方向上的深度为150~200μm,宽度和深度的乘积30000~80000μm2;刻痕产品表面无照射损伤,铁损改善率为7%~14%,磁致伸缩性能优异,其中板厚0.23mm材料的磁致伸缩≤0.85
×
10-6
,板厚0.27mm材料的磁致伸缩≤1.1
×
10-6
,板厚0.30mm材料的磁致伸缩≤1.3
×
10-6
。
[0019]
所述的磁致伸缩是指在1.9t的磁场中0.3kg/mm2压应力下所述取向硅钢的延伸率。
[0020]
本发明具有以下有益效果:
[0021]
本发明采用波长为10.6μm的co2气体连续波激光源进行激光刻痕,通过激光功率和扫描速度等关键工艺参数的合理匹配,来控制合理的照射能量密度,达到既保证铁损改善率稳定达到7%~14%之间,又不会产生表面照射损伤,避免硅钢表面不会产生物理变形和激光照射损伤,且磁致伸缩性能优良,磁感强度b8与原材料相当,低磁场条件下磁性能b1、b0.5高,产品的磁致伸缩性能明显优于脉冲激光法和传统连续波法,可以大幅提高变压器综合性能通过控制合理的变形量来防止不好的磁滞收缩性能。本发明采用高速扫描速度,适合于高速、大规模连续加工,可以降低生产成本。
附图说明
[0022]
图1为本发明激光照射光路示意图。
[0023]
图2为本发明钢板表面的光斑形状。
[0024]
图3为本发明的产品刻痕前后表面质量情况。
具体实施方式
[0025]
以下结合具体实施例,对本发明作进一步说明。应理解,以下实施例仅用于说明本发明而非用于限定本发明的范围。
[0026]
下列实施例中未注明具体条件的实验方法,通常按照常规条件,或厂商提供的条
件进行。
[0027]
本实施例的激光照射光路图见图1,其中部件1为激光发射器,部件2为反射镜,部件3为振镜,部件4为聚焦镜,部件5为运行的带钢。激光束经激光发射器1激发后,通过反射镜2到达振镜3,再经振镜3反射后到达聚焦镜4,通过聚焦镜聚焦到运行中的带钢5表面,其中振镜3沿带钢横向摆动,通过振镜的摆动角度和摆动速度来控制激光的反射角度和扫描速度。
[0028]
实施例1~9
[0029]
实施例1~9采用co2气体连续波激光源在取向硅钢表面进行激光刻痕,照射激光束为椭圆形光束,直径为8mm
×
0.2mm,光斑形状见图2;其长轴大致垂直于钢板的轧制方向,可以在扫描方向形成叠加的照射效果;以大致相等的间距在钢板表面形成连续重叠照射,保证在瞬时能量一定的前提下提高照射面的能量照射密度,从而改善所述取向硅钢的铁损特性;激光输出功率、扫描速度和机组速度见表1,扫描间距为5mm,最终获得表面质量优良的“no-show”型激光刻痕高磁感取向硅钢产品。
[0030]
表1实施例1~9的工艺参数和测试结果
[0031][0032]
由表1可见,实施例1~9的铁损(p17/50)改善率稳定在7%~14%之间,表面涂层不被破坏,励磁功率s17在2.00va/kg以下,磁致伸缩性能优异。实施例2、实施例5和实施例8的激光刻痕产品的电磁性能典型值见表2。
[0033]
表2磁性能典型值
[0034][0035]
由表2可知,本发明产品的磁感强度b8与原材料相当,低磁场条件下的磁感强度b1、b0.5劣化程度轻,1.7t磁场条件下的励磁功率s17控制在1.85va/kg以下。本发明电磁性能数据均采用尺寸为500
×
500(mm)的单片在德国brauckhause公司制造的磁测仪上测量。
[0036]
表3为实施例2、实施例5和实施例8的激光刻痕产品与脉冲激光方法、传统连续波激光方法生产的产品的磁致伸缩性能对比情况。
[0037]
表3磁致伸缩性能
[0038][0039]
由表3可见,本发明产品具有明显优于脉冲激光方法和传统连续波方法的磁致伸缩性能。
[0040]
图3给出了实施例5的产品刻痕前后表面质量情况,刻痕后绝缘涂层未遭到破坏,表面刻痕线不可见或“隐约”可见;通过酸洗去除带钢表面除绝缘涂层和底层后,带钢基板上刻痕线清晰可见。由此可见,由于绝缘涂层未遭到破坏,刻痕后无需重新涂绝缘涂层,产品的叠装系数和层间电阻不会受到影响,即使长时间存放也不易生锈。
再多了解一些
本文用于企业家、创业者技术爱好者查询,结果仅供参考。