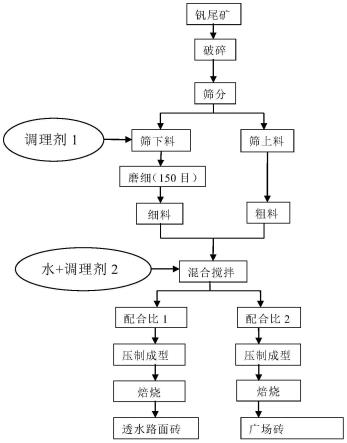
1.本发明属于尾矿综合利用技术领域,具体涉及一种利用钒尾矿制备烧结路面砖的方法。
背景技术:
2.目前,钒矿的钠化焙烧是提钒的主流工艺,该工艺以纯碱、食盐等为添加剂,通过高温氧化钠化,将钒矿中低价态的钒转化为水溶性五价钒酸钠盐,经后续产品转化生产钒氧化物、钒合金等钒化工产品。然而长期以来,传统的钒化工冶金流程伴生产出大量固体废物,主要为提钒后的钒矿尾渣。每年仅钒矿尾渣就高达近百万吨,并逐年上升。由于缺乏有效的处理利用技术,对产业的可持续发展形成日益严重的负面效应,需要对钒尾矿进行充分利用,以避免固废污染和资源的浪费。
3.现有研究采用钒尾矿为原料制备墙体材料,主要分为两类:(1)在普通烧结砖的制备过程中利用钒尾矿的残余热量,以节省一部分燃料;(2)利用钒尾矿作为细沙插入制备非烧结砖。但因为钒尾矿的塑形指数和含碳量严重影响了制品普通烧结砖或非烧结砖的质量,上述研究方法对钒尾矿的利用率均不到20%,难以从根源上解决钒尾矿的消纳问题。
4.因此,需要寻找一种更好地利用钒尾矿的方法。
技术实现要素:
5.本发明所要解决的技术问题在于针对上述现有技术的不足,提供一种利用钒尾矿制备烧结路面砖的方法。该方法以钒尾矿为主要原料,同时加入调理剂1和调理剂2作为辅助原料,从钒尾矿中筛选具有一定强度的粗料作为目的产物的骨架,并添加调理剂1球磨制备细料在高温下熔融充当粘结剂,在保证目的产物烧结路面砖具有强度的同时,其内部还能粘接形成孔隙用于排水,满足了烧结路面砖的使用要求,提高了原料中钒尾矿的掺量,大大提高了钒尾矿的利用率,降低了原料成本。
6.为解决上述技术问题,本发明采用的技术方案为:一种利用钒尾矿制备烧结路面砖的方法,其特征在于,该方法依次经粗料与细料制备、配料搅拌、静压成型和烧结,得到烧结路面砖;所述路面砖的制备原料包括钒尾矿和调理剂1和调理剂2。
7.本发明以钒尾矿为主要原料,同时加入调理剂1和调理剂2作为辅助原料,经原料处理后进行均化,并依次经成型、干燥和焙烧,得到烧结路面砖,提高了原料中钒尾矿的掺量,实现了对钒尾矿的利用率。
8.上述的一种利用钒尾矿制备烧结路面砖的方法,其特征在于,按质量计所述制备原料中钒尾矿的掺量为88%以上,调理剂1的掺量为1.5%~9%,调理剂2的掺量为2%~3%。相对于传统的最高仅达40%的掺量,本发明原料中钒尾矿的掺量达88%以上,且仅需要添加少量的调理剂1和调理剂2,大大提高了钒尾矿的利用率,且原料中调理剂1和调理剂2的加入量较低,降低了原料成本。
9.上述的一种利用钒尾矿制备烧结路面砖的方法,其特征在于,所述钒尾矿中二氧
化硅的质量含量不低于70%,钙元素的质量含量不高于5%,含水量小于4%。该组成的钒尾矿覆盖了大部分钒尾矿的成分范围,提高了本发明方法的实用性。
10.上述的一种利用钒尾矿制备烧结路面砖的方法,其特征在于,所述调理剂1为碎玻璃、风积沙和碳酸钠中的一种或两种。本发明采用上述成分的调理剂1,实现了对路面材料或路面砖的强度和烧结温度的调节。
11.上述的一种利用钒尾矿制备烧结路面砖的方法,其特征在于,所述调理剂2为水玻璃或/和羧甲基纤维素钠。本发明采用上述成分的调理剂2,实现了对路面材料或路面砖的坯体的塑性和强度的调节。
12.上述的一种利用钒尾矿制备烧结路面砖的方法,其特征在于,该方法包括以下步骤:
13.步骤一、粗料制备:将钒尾矿破碎后进行筛分,得到筛下料和筛上料即粗料;所述粗料的粒径大于0.75mm;
14.步骤二、细料制备:将步骤一中得到的筛下料和调理剂1混合后干法球磨至150目,得到细料;所述筛下料和调理剂1中调理剂1的质量含量为8%~12%;
15.步骤三、配料搅拌:将步骤一中得到的粗料和步骤二中得到的细料按照设计配合比混合制成混合料,将混合料送入搅拌机中,在转速80r/min的条件下干法慢速搅拌5min以上,然后喷洒调理剂2的水溶液,在转速120r/min的条件下混合搅拌5min以上,再密封均化24h;所述调理剂2的水溶液的质量浓度为40%~60%,且以密封均化后的混合料的干料质量为基准计算所述调理剂2的加入质量为2%~3%,所述密封均化后的混合料的质量含水率不大于10%;
16.步骤四、静压成型:将步骤三中经密封均化后的混合料在转速80r/min的条件下搅拌5min以上,然后布料入模并在压力40mpa以上的条件下静压成型,得到坯体;
17.步骤五、烧结:将步骤四中得到的坯体进行烧结,得到烧结路面砖。
18.本发明先对钒尾矿进行破碎筛分,得到粗料和筛下料,即从钒尾矿中筛选具有一定强度的粗料作为目的产物的骨架,并将粗料与筛下物包括细粉结块物充分分离,然后将筛下料添加调理剂1通过球磨制备细料,保证后续工艺中两者的熔融粘接作用,再将粗料和细料搅拌并添加调理剂2搅匀,后续的烧结过程中细料在高温下熔融充当粘结剂,在保证目的产物路面材料或路面砖具有强度的同时,其内部还能粘接形成孔隙用于排水,满足了路面材料或路面砖的使用要求,实现了钒尾矿的有效利用。
19.上述的方法,其特征在于,步骤一中将钒尾矿送入对辊破碎机中进行破碎,然后经过滚筒筛进行筛分;所述对辊破碎机的辊距为1mm,滚筒筛的筛网孔径为0.75mm。本发明采用对辊破碎有效降低了钒尾矿中大块硬骨料和细粉结块物的尺寸,同时减少了对细粉结块物的破碎效果,有利于实现了粗料和筛下物的充分分离,保证了粗料和细料的作用效果。
20.上述的方法,其特征在于,步骤三中所述设计配合比为混合料中粗料的质量含量为40%~50%,对应步骤五所述烧结的制度为:先以1℃/min的升温速度加热至200℃,然后以3℃/min的升温速度加热至500℃,继续以5℃/min的升温速度加热至700℃并保温120min,再以5℃/min的升温速度加热至1150℃~1250℃并保温180min,自然冷却至室温得到透水路面砖。
21.上述的方法,其特征在于,步骤三中所述设计配合比为混合料中粗料的质量含量
不超过30%,对应步骤五所述烧结的制度为:先以2℃/min的升温速度加热至500℃并保温120min,然后以5℃/min的升温速度加热至700℃并保温180min,继续以5℃/min的升温速度加热至1150℃~1250℃并保温200min,自然冷却至室温得到广场砖。
22.本发明通过控制设计配合比即混合料中粗料的质量含量,并选择对应的烧结方式,分别得到不同的烧结路面砖。具体地,本发明先确定粗料的粒径大于0.75μm,细料的粒径为150目即0.60μm,利用粒径较大的粗料充当骨架,利用粒径较小的细料及调理剂在后续烧结时熔融充当粘结剂,保证目的产物的成型,然后控制粗料与细料的质量含量即比例以及对应的烧结的制度,通过采用质量含量高达40%~50%的粗料制备透水路面砖,满足了透水路面砖对较好透水性能和一般强度和耐久性的需求,通过采用质量含量不超过30%的粗料制备广场砖,满足了广场砖对较高强度和一般透水性的需求,实现了对钒尾矿的充分分类利用,增加了目的产物的种类和应用范围。
23.本发明与现有技术相比具有以下优点:
24.1、本发明以钒尾矿为主要原料,同时加入调理剂1和调理剂2作为辅助原料,经粗料与细料制备、配料搅拌、静压成型和烧结,得到烧结路面砖,提高了原料中钒尾矿的掺量,大大提高了钒尾矿的利用率,降低了原料成本。
25.2、本发明先对钒尾矿进行破碎筛分,从钒尾矿中筛选具有一定强度的粗料作为目的产物的骨架,并添加调理剂1球磨制备细料在高温下熔融充当粘结剂,在保证目的产物烧结路面砖具有强度的同时,其内部还能粘接形成孔隙用于排水,满足了烧结路面砖的使用要求,实现了钒尾矿的有效利用。
26.3、本发明通过控制设计配合比即混合料中粗料的质量含量,并选择对应的烧结的制度,分别得到具有不同性能的烧结路面砖即透水路面砖和广场砖,实现了对钒尾矿的充分分类利用,增加了目的产物的种类和应用范围。
27.4、本发明在同一批钒尾矿的利用过程中,通过采用钒尾矿分别制备透水路面砖和广场砖,实现了对多余细料的充分利用,进一步提高了对钒尾矿的利用效率,避免了资源的浪费,节约了生产能耗。
28.5、本发明通过在原料中采用少量的调理剂1,实现了对烧结路面砖的强度和烧结温度的调节,通过采用少量的调理剂2,实现了对烧结路面砖的坯体的塑性调节,原料成本低,且调节效果优异。
29.下面通过附图和实施例对本发明的技术方案作进一步的详细描述。
附图说明
30.图1为本发明利用钒尾矿制备烧结路面砖的工艺流程图。
具体实施方式
31.本发明实施例1~实施例4采用的钒尾矿为陕西商洛山阳县的钒矿提取后的尾渣,其sio2的质量含量为79.13%,cao的质量含量为0.82%,含水量为2%,符合本发明对原料钒尾矿的一般要求,原料钒尾矿中的化学成分如下表1所示。
32.表1钒矿尾渣的化学成分表
[0033][0034]
实施例1
[0035]
如图1所示,本实施例包括以下步骤:
[0036]
步骤一、粗料制备:采用装载机将钒尾矿送入2pg-610x400型对辊破碎机中进行破碎,然后经转运皮带机送入滚筒筛进行筛分,得到筛下料和筛上料即粗料,粗料依次经皮带机、斗式提升机送入粗料仓中备用;所述对辊破碎机的辊距为1mm,滚筒筛的筛网孔径为0.75mm;所述粗料的粒径大于0.75mm,且筛下料和粗料中粗料的质量含量为30%;
[0037]
步骤二、细料制备:将步骤一中得到的筛下料依次经转运皮带机、皮带秤送入球磨机中,和调理剂1混合后干法球磨至150目,得到细料,将细料依次经皮带机、斗式提升机转运至细料仓中备用,其中,由细料仓自带的配料系统根据皮带秤称量的筛下料的质量计算调理剂1的掺量并送入球磨机中;所述调理剂1为碎玻璃和碳酸钠质量比为1:1的混合物,且筛下料和调理剂1中调理剂1的质量含量为12%;
[0038]
步骤三、配料搅拌:将步骤一中得到的粗料和步骤二中得到的细料经对应粗料仓和细料仓的底部的皮带秤称量后,经输送管送入配料机中按照设计配合比混合制成混合料,将混合料经皮带机送入搅拌机中,在转速80r/min的条件下干法慢速搅拌10min,然后喷洒质量浓度为60%的调理剂2的水溶液,边喷洒边搅拌,在转速120r/min的条件下混合搅拌10min,将完成混合搅拌的物料经皮带机、斗式提升机送入均化仓中密封均化24h;所述设计配合比为混合料中粗料的质量含量为50%,所述调理剂2为水玻璃和羧甲基纤维素钠质量比为1:1的混合物,且以密封均化后的混合料的干料质量为基准计算所述调理剂2的加入质量为2%,所述密封均化后的混合料的质量含水率为5%;
[0039]
步骤四、静压成型:将步骤三中经密封均化后的混合料经转运皮带机送入静压制砖机中,在转速80r/min的条件下搅拌10min,然后布料放入长度
×
宽度
×
高度为150mm
×
300mm
×
60mm的模具中,并在压力40mpa的条件下静压成型,得到坯体;
[0040]
步骤五、烧结:将步骤四中得到的坯体经跺码机器人转运至焙烧窑中进行烧结,先以1℃/min的升温速度加热至200℃,然后以3℃/min的升温速度加热至500℃,继续以5℃/min的升温速度加热至700℃并保温120min,再以5℃/min的升温速度加热至1150℃~1250℃并保温180min,自然冷却至室温得到透水路面砖,经自动打包系统打包后存入成品堆放区。
[0041]
本实施例中的调理剂1还可替换为除了碎玻璃和碳酸钠混合物以外的碎玻璃、风积沙和碳酸钠中的一种或两种。
[0042]
本实施例中的调理剂2还可替换为水玻璃或羧甲基纤维素钠。
[0043]
实施例2
[0044]
如图1所示,本实施例包括以下步骤:
[0045]
步骤一、粗料制备:采用装载机将钒尾矿送对辊破碎机中进行破碎,然后经转运皮带机送入滚筒筛进行筛分,得到筛下料和筛上料即粗料,粗料依次经皮带机、斗式提升机送入粗料仓中备用;所述对辊破碎机的辊距为1mm,滚筒筛的筛网孔径为0.75mm;所述粗料的
粒径大于0.75mm;
[0046]
步骤二、细料制备:将步骤一中得到的筛下料送入球磨机中,和调理剂1混合后干法球磨至150目,得到细料备用;所述调理剂1为碎玻璃和碳酸钠质量比为1:1的混合物,且筛下料和调理剂1中调理剂1的质量含量为8%;
[0047]
步骤三、配料搅拌:将步骤一中得到的粗料和步骤二中得到的细料经对应粗料仓和细料仓的底部的皮带秤称量后,经输送管送入配料机中按照设计配合比混合制成混合料,将混合料经皮带机送入搅拌机中,在转速80r/min的条件下干法慢速搅拌10min,然后喷洒质量浓度为60%的调理剂2的水溶液,边喷洒边搅拌,在转速120r/min的条件下混合搅拌10min,将完成混合搅拌的物料经皮带机、斗式提升机送入均化仓中密封均化24h;所述设计配合比为混合料中粗料的质量含量为40%,所述调理剂2为水玻璃和羧甲基纤维素钠质量比为1:1的混合物,且以密封均化后的混合料的干料质量为基准计算所述调理剂2的加入质量为3%,所述密封均化后的混合料的质量含水率为4%;
[0048]
步骤四、静压成型:将步骤三中经密封均化后的混合料经转运皮带机送入静压制砖机中,在转速80r/min的条件下搅拌10min,然后布料放入模具中,并在压力40mpa的条件下静压成型,得到坯体;
[0049]
步骤五、烧结:将步骤四中得到的坯体经跺码机器人转运至焙烧窑中进行烧结,先以1℃/min的升温速度加热至200℃,然后以3℃/min的升温速度加热至500℃,继续以5℃/min的升温速度加热至700℃并保温120min,再以5℃/min的升温速度加热至1150℃~1250℃并保温180min,自然冷却至室温得到透水路面砖。
[0050]
经检测,本实施例得到的透水路面砖的透水系数可达1.5
×
10-2
cm/s,抗压强度可达25mpa,符合b级透水砖指标要求。
[0051]
本实施例中的调理剂1还可替换为除了碎玻璃和碳酸钠混合物以外的碎玻璃、风积沙和碳酸钠中的一种或两种。
[0052]
本实施例中的调理剂2还可替换为水玻璃或羧甲基纤维素钠。
[0053]
实施例3
[0054]
如图1所示,本实施例包括以下步骤:
[0055]
步骤一、粗料制备:采用装载机将钒尾矿送对辊破碎机中进行破碎,然后经转运皮带机送入滚筒筛进行筛分,得到筛下料和筛上料即粗料;所述对辊破碎机的辊距为1mm,滚筒筛的筛网孔径为0.75mm;所述粗料的粒径大于0.75mm;
[0056]
步骤二、细料制备:将步骤一中得到的筛下料送入球磨机中,和调理剂1混合后干法球磨至150目,得到细料备用;所述调理剂1为碎玻璃和碳酸钠质量比为1:1的混合物,且筛下料和调理剂1中调理剂1的质量含量为12%;
[0057]
步骤三、配料搅拌:将步骤一中得到的粗料和步骤二中得到的细料经对应粗料仓和细料仓的底部的皮带秤称量后,经输送管送入配料机中按照设计配合比混合制成混合料,将混合料经皮带机送入搅拌机中,在转速80r/min的条件下干法慢速搅拌10min,然后喷洒质量浓度为50%的调理剂2的水溶液,边喷洒边搅拌,在转速120r/min的条件下混合搅拌10min,将完成混合搅拌的物料经皮带机、斗式提升机送入均化仓中密封均化24h;所述设计配合比为混合料中粗料的质量含量为30%,所述调理剂2为水玻璃和羧甲基纤维素钠质量比为1:1的混合物,且以密封均化后的混合料的干料质量为基准计算所述调理剂2的加入质
量为2%,所述密封均化后的混合料的质量含水率为3%;
[0058]
步骤四、静压成型:将步骤三中经密封均化后的混合料经转运皮带机送入静压制砖机中,在转速80r/min的条件下搅拌10min,然后布料放入模具中,并在压力40mpa的条件下静压成型,得到坯体;
[0059]
步骤五、烧结:将步骤四中得到的坯体转运至焙烧窑中进行烧结,先以2℃/min的升温速度加热至500℃并保温120min,然后以5℃/min的升温速度加热至700℃并保温180min,继续以5℃/min的升温速度加热至1150℃~1250℃并保温200min,自然冷却至室温得到广场砖。
[0060]
经检测,本实施例制备的广场砖的抗压强度可达28mpa,符合nx类强度指标要求。
[0061]
本实施例中的调理剂1还可替换为除了碎玻璃和碳酸钠混合物以外的碎玻璃、风积沙和碳酸钠中的一种或两种。
[0062]
本实施例中的调理剂2还可替换为水玻璃或羧甲基纤维素钠。
[0063]
实施例4
[0064]
如图1所示,本实施例包括以下步骤:
[0065]
步骤一、粗料制备:采用装载机将钒尾矿送入对辊破碎机中进行破碎,然后经转运皮带机送入滚筒筛进行筛分,得到筛下料和筛上料即粗料备用;所述对辊破碎机的辊距为1mm,滚筒筛的筛网孔径为0.75mm;所述粗料的粒径大于0.75mm;
[0066]
步骤二、细料制备:将步骤一中得到的筛下料送入球磨机中,和调理剂1混合后干法球磨至150目,得到细料备用;所述调理剂1为碎玻璃和碳酸钠质量比为1:1的混合物,且筛下料和调理剂1中调理剂1的质量含量为10%;
[0067]
步骤三、配料搅拌:将步骤一中得到的粗料和步骤二中得到的细料经对应粗料仓和细料仓的底部的皮带秤称量后,经输送管送入配料机中按照设计配合比混合制成混合料,将混合料经皮带机送入搅拌机中,在转速80r/min的条件下干法慢速搅拌10min,然后喷洒质量浓度为40%的调理剂2的水溶液,边喷洒边搅拌,在转速120r/min的条件下混合搅拌10min,将完成混合搅拌的物料经皮带机、斗式提升机送入均化仓中密封均化24h;所述设计配合比为混合料中粗料的质量含量为10%,所述调理剂2为水玻璃和羧甲基纤维素钠质量比为1:1的混合物,且以密封均化后的混合料的干料质量为基准计算所述调理剂2的加入质量为3%,所述密封均化后的混合料的质量含水率为6.5%;
[0068]
步骤四、静压成型:将步骤三中经密封均化后的混合料经转运皮带机送入静压制砖机中,在转速80r/min的条件下搅拌10min,然后布料放入长度
×
宽度
×
高度为100cm
×
100cm
×
30cm的模具中,并在压力50mpa的条件下静压成型,得到坯体;
[0069]
步骤五、烧结:将步骤四中得到的坯体转运至焙烧窑中进行烧结,先以2℃/min的升温速度加热至500℃并保温120min,然后以5℃/min的升温速度加热至700℃并保温180min,继续以5℃/min的升温速度加热至1150℃~1250℃并保温200min,自然冷却至室温得到广场砖。
[0070]
经检测,本实施例制备的广场砖的抗压强度可达30mpa,符合nx类强度指标要求。
[0071]
本实施例中的调理剂1还可替换为除了碎玻璃和碳酸钠混合物以外的碎玻璃、风积沙和碳酸钠中的一种或两种。
[0072]
本实施例中的调理剂2还可替换为水玻璃或羧甲基纤维素钠。
[0073]
以上所述,仅是本发明的较佳实施例,并非对本发明作任何限制。凡是根据发明技术实质对以上实施例所作的任何简单修改、变更以及等效变化,均仍属于本发明技术方案的保护范围内。
再多了解一些
本文用于企业家、创业者技术爱好者查询,结果仅供参考。