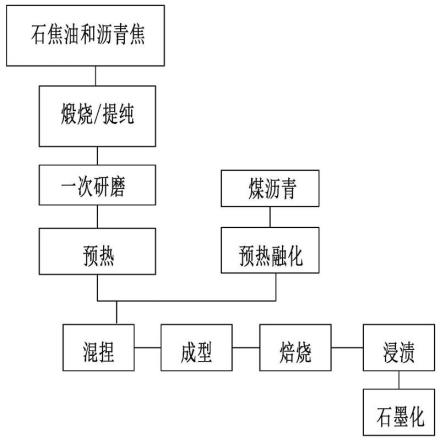
1.本发明涉及石墨材料制备技术领域,具体为一种用于电火花石墨加工的方法。
背景技术:
2.高纯石墨是指含碳量大于99.99%的石墨。高纯石墨具有耐高温、耐腐蚀、抗热震、热膨胀系数小、自润滑、电阻系数小及易于机械加工优点,被广泛应用于冶金、机械、环保、化工、电子、医药、军工和航空航天领域,在国民经济中的地位越来越重要,特别是在太阳能光伏产业。全球太阳能光伏产业平均年增长率为40%,中国作为全球最大的太阳能光伏生产国, 其份额达到全球的70%,行业在2011 年消耗的高档石墨材料达到2.3 万t 以上,预计今后光伏产业的单晶硅和多晶硅对高纯石墨材料的需求将以每年20%~25%的速度增长。目前我国石墨工业技术还处于世界中低水平,产品多以原料和初加工产品为主,产品中的高杂质使其应用范围受限。因此,一方面国产石墨产品在国际市场价格低廉,导致大量石墨资源外流;另一方面本国市场需要的高纯超细石墨制品则多依赖进口。综上所述,开展高纯石墨生产工艺研究,提高产品质量,对我国高纯石墨产业的发展意义深远。
3.电火花加工用石墨材料的原料粒度小,制品尺寸大,产品性能要求高,生产过程中 应力大,生产工艺复杂,技术难度极高。目前,只有为数不多的国外企业掌握了生产工艺,垄 断市场。国内企业对该石墨电极的制备方法的研究处于探索阶段,产品还远远不能满足用户的需求,本发明制备工艺操作简单,成品率高,充分利用资源,节约成本,同时还保持了较 高的体积密度和机械强度,实用性强。
技术实现要素:
4.本发明的目的在于提供一种用于电火花石墨加工的方法,以解决上述背景技术中提出的问题。
5.为解决上述问题,本发明所采取的技术方案是:一种用于电火花石墨加工的方法,包括:步骤一:选取原料,原料包括有骨料、粘结剂和浸渍剂,骨料选用针状石油焦和沥青焦,粘结剂和浸渍剂使用煤沥青;步骤二:煅烧/提纯,将骨料内的各种固体炭素原料与氢氧化钠按照1:1的比例在隔离空气的条件下进行高温加热处理,然后进行低温烘干,将骨料浸在水中一段时间,洗涤至中性,然后浸在盐酸中一段时间,洗涤至中性后进行烘干;步骤三:研磨,将骨料粒度粉碎到配料要求,通过立式辊磨机将骨料粒度磨制平均粒度为20μm完成一次磨粉,对骨料粉末和煤沥青进行预热;步骤四:混捏,将磨制好的骨料粉末和融化后的煤沥青黏结剂按一定的比例配好后投入加热式混捏机中进行混捏,冷却后再次进行破碎后二次磨粉,进行振动真空装料,使物料分布均匀;步骤五:成型,采用静压成型的方式,将混捏后的骨料粉末和煤沥青黏结剂置于软
模具内,密实、密封后进行抽真空,放入静压机缸内进行压制;步骤六:焙烧,将压制成型后的生坯在隔离空气条件下通过热处理,温度为1000 ℃,使黏结剂炭化为黏结剂焦;步骤七:浸渍,将熔融沥青浸渍剂,充填到焙烧过程中的制品内部形成的微小气孔以及骨料焦炭颗粒中原来存在的开口气孔里;步骤八:石墨化,将焙烧品经2000~2800 ℃的高温进行石墨化处理。
6.进一步地,所述步骤五中具体采用热静压的方式,介质的温度为1000℃。
7.进一步地,所述步骤6中的焙烧温度为1000℃,焙烧时间在20min,焙烧过程要求缓慢且始终保持温度稳定。
8.进一步地,所述步骤7中浸渍的方式采用加压浸渍的方式,将煤沥青浸渍到制品内部。
9.本发明结构新颖,构思巧妙,操作简单方便,和现有技术相比具有以下优点:工艺操作简单,成品率高,充分利用资源,节约成本,同时还保持了较高的体积密度和机械强度,实用性强,通过设定焙烧的温度和时间有效提高石墨提纯的效果,且得到的石墨具有较高的体积密度和机械强度,通过采用热静压的方式,介质的温度为1000℃,热静压的介质温度为1000℃,而步骤六中焙烧的温度大约为1000℃,温度相差小,便于后续的加热过程,有效的节约资源和成本。
附图说明
10.图1为本发明的一种用于电火花石墨加工的方法的过程图;图2为本发明的一种用于电火花石墨加工的方法的焙烧时间对石墨提纯效果的影响图;图3为本发明的一种用于电火花石墨加工的方法的焙烧温度对石墨提纯效果的影响图。
具体实施方式
11.以下是本发明的具体实施例,并结合附图对本发明技术方案作进一步的描述,但本发明并不限于这些实施例。
12.一种用于电火花石墨加工的方法,包括:步骤一:选取原料,原料包括有骨料、粘结剂和浸渍剂,骨料选用针状石油焦和沥青焦,粘结剂和浸渍剂都使用煤沥青,针状石油焦具有灰分低,含量小于1%,在高温下容易石墨化,导电与导热性能好,线膨胀系数小特性; 用沥青焦在同样的石墨化温度下得到的石墨,其电阻率较大,但机械强度较高,所以一般生产石墨化产品时, 除石油焦外还采用一定比例的沥青焦,以便提高产品的机械强度,浸渍剂与黏结剂大体上相同,它是为了提高制品的体积密度、不透性、润滑性、强度及其他特殊性能,要求制品在焙烧或石墨化及机械加工后,加入浸渍剂。
13.步骤二:煅烧/提纯,将骨料内的各种固体炭素原料与氢氧化钠按照1:1的比例在隔离空气的条件下进行高温加热处理,然后进行低温烘干,将骨料浸在水中一段时间,洗涤至中性,然后浸在盐酸中一段时间,洗涤至中性后进行烘干,选好后的骨料,由于它们的成
焦温度或成煤的地质年代不同,在内部结构中不同程度地含有水分、杂质或挥发物,这些物质如果不预先排除,直接用它们生产石墨材料,势必会影响产品质量和使用性能,应对选好的骨料进行煅烧或提纯。
14.步骤三:研磨,将骨料粒度粉碎到配料要求,通过立式辊磨机将骨料粒度磨制平均粒度为20μm完成一次磨粉,对骨料粉末和煤沥青进行预热,用于石墨生产的固体材料,虽经煅烧或提纯的块度有所减小,但粒度仍比较大,且波动较大,组成不均匀,需要将骨料粒度粉碎到配料要求。
15.步骤四:混捏,将磨制好的骨料粉末和融化后的煤沥青黏结剂按一定的比例配好后投入加热式混捏机中进行混捏,冷却后再次进行破碎后二次磨粉,进行振动真空装料,使物料分布均匀,磨制好的粉末,它是分散的,且不均匀。它需与煤沥青黏结剂按一定比例配好后投入到加热式混捏机中进行混捏,使物料分布均匀,并且使黏结剂薄薄地均匀地包裹在粉粒的表面,及渗透浸润到粉粒表面的微孔中。
16.步骤五:成型,采用静压成型的方式,将混捏后的骨料粉末和煤沥青黏结剂置于软模具内,密实、密封后进行抽真空,放入静压机缸内进行压制,通过静压成型的方式获得的产品在结构和性能上具有各向同性。
17.步骤六:焙烧,将压制成型后的生坯在隔离空气条件下通过热处理,温度1000 ℃,使黏结剂炭化为黏结剂焦。
18.步骤七:浸渍,将熔融沥青浸渍剂,充填到焙烧过程中的制品内部形成的微小气孔以及骨料焦炭颗粒中原来存在的开口气孔里,可有效的提高制品的体积密度、导电率、机械强度、抗化学腐蚀性。
19.步骤八:石墨化,将焙烧品经2000~2800 ℃的高温进行石墨化处理。
20.所述步骤五中具体采用热静压的方式,介质的温度为1000℃,热静压的介质温度为1000℃,而步骤六中焙烧的温度大约为1000℃,温度相差小,便于后续的加热过程。
21.如图2和3所示,所述步骤6中的焙烧温度为1000℃,焙烧时间在20min,焙烧过程要求缓慢且始终保持温度稳定,焙烧温度为1000℃,焙烧时间在20min,石墨提纯的效果最佳。
22.本文中所描述的具体实施例仅仅是对本发明精神作举例说明。本发明所属技术领域的技术人员可以对所描述的具体实施例做各种各样的修改或补充或采用类似的方式代替,但并不会偏离本发明的精神或者超越所附权利要求书所定义的范围。
再多了解一些
本文用于企业家、创业者技术爱好者查询,结果仅供参考。