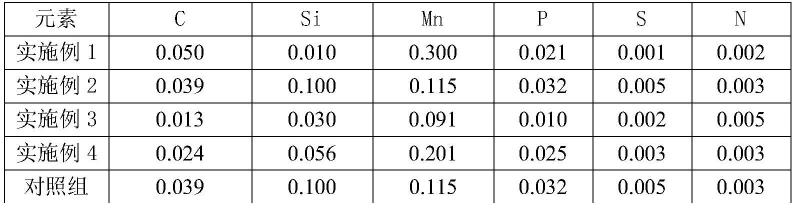
1.本发明涉及低碳钢花纹钢板生产技术领域,特别是一种基于薄板坯连铸连轧流程采用铁素体轧制工艺生产薄规格花纹钢板的方法。
背景技术:
2.近年来,钢铁行情持续走低,钢铁行业内竞争激烈,国内对环保问题也加强关注,因此探讨降本又环保的生产工艺对钢铁行业来讲是必要之举。因此,充分利用薄板坯连铸连轧流程开发应用新产品符合国家总体规划和行业需求。
3.目前基于薄板坯连铸连轧流程生产薄规格花纹钢板的方法研究比较多,例如《一种用csp流程生产厚度为1.4mm花纹板的方法》(公开号cn107716552b),以及本公司的《基于esp薄板坯连铸连轧流程生产薄规格花纹钢板的方法》(公开号cn106077090b),二者均采用全程奥氏体区轧制工艺。当变形抗力大时,薄规格花纹板轧制十分困难,因此现有技术铸坯经粗轧后需要在感应式加热炉进行加热至1120~1180℃,精轧出口温度≥850℃,方能使钢材部分或大部分在变形抗力较小的高温奥氏体区发生形变,但这种轧制方式能耗较大。精轧出口温度850℃时,钢材为低温奥氏体和部分铁素体,钢材强度大,需要较大的轧制力和压下率(20%~25%),进一步增加能耗成本且因增大工作辊的磨损而缩短了在线使用时间。
4.铁素体轧制工艺是一种针对低碳系列钢种的控制轧制技术,通过控制温度,带钢在全奥氏体状态下进行粗轧,在完全铁素体或部分铁素体状态下进行精轧。该工艺具有加热温度低、轧制温度低、温度损失小等优点,可生产薄规格热轧低碳钢,是降低生产成本提高产品利润的最佳选择。但是将铁素体轧制工艺引入本公司现有薄板坯连铸连轧流程生产薄规格花纹钢板工艺(cn106077090b)时,则会由于精轧机组部分或大全部在钢材变形抗力较小的低温铁素体温度区间轧制,带钢表面和边部温度低,摩擦力大,导致中间坯到成品带钢变形量小,组织不均;出现豆高偏小,豆形不饱满,且强度偏高,延伸率较低的缺陷;且带钢边部温度低,对工作辊磨损大,无法长时间批量生产。以上缺陷,限制了薄规格花纹钢板生产中进一步的节能减排降本增效。
技术实现要素:
5.本发明的技术任务是针对以上现有技术的不足,提供一种薄板坯连铸连轧工艺生产薄规格花纹钢板的方法,可实现0.9~1.5mm薄规格花纹钢板的生产,缩短生产周期,采用低温铁素体工艺可有效实降低生产成本,节能环保。
6.本发明解决其技术问题的技术方案是:一种薄板坯连铸连轧工艺生产薄规格花纹钢板的方法,包括冶炼、连铸、连轧、卷取后制成不同厚度的花纹钢板,所述的连轧包括粗轧、感应加热和精轧;其特征在于:所述的连铸工序铸坯厚度采用90~110mm,扇形段采用前段高压水快速冷却,后段应用气雾冷却;所述的连轧工序中粗轧出口温度950~1100℃;精轧出口温度为740~810℃;精轧末机架出口获得花纹钢板厚度范围是0.8~6.0mm;卷取温
度600~700℃。
7.进一步的,上述冶炼工序中,c含量控制在0.01~0.05%。
8.进一步的,上述连铸工序中,扇形段的前段高压水快速冷却,水压10~20bar,水量占总冷却水量75~85%。
9.进一步的,上述精轧入口温度870~1000℃。
10.进一步的,上述精轧末机架上工作辊采用花纹辊,花纹辊通过平辊刻辊形成,下工作辊采用普通凹辊,凸度为-30~-70μm。
11.进一步的,上述精轧末机架应用动态窜辊。
12.进一步的,上述精轧末机架应用润滑轧制。
13.进一步的,上述润滑轧制使用的有机润滑液油水比为1:50。
14.进一步的,上述精轧末机架压下率采用14~20%。
15.进一步的,上述精轧末机架出口获得花纹钢板厚度范围为0.9~1.5mm。
16.与现有技术相比较,本发明具有以下突出的有益效果:
17.1、本发明基于薄板坯连铸连轧技术,省去板坯运输和再加热、多道次反复轧制等过程,生产流程比传统热连轧短,同时比薄带连铸连轧单轧程产量大,生产效率高;
18.2、本发明可实现更薄厚度花纹钢板的生产,0.9~1.5mm厚度花纹钢板,其中≤1.2mm厚度规格比例达50%以上,可直接供市场应用,缩短产品周期;
19.3、本发明采用较低的精轧出口温度(740~810℃),实现精轧机组部分或大全部在钢材变形抗力较小的低温铁素体温度区间轧制;同时精轧入口温度由奥氏体轧制生产需求的1100~1200℃降低至870~1000℃,大幅降低了加热成本,节省电耗,是一种节能环保的生产工艺;
20.4、本发明采用直弧式高拉速连铸机,连铸机扇形段应用前段快速冷却、后段应用气雾冷却,充分利用铸坯芯部温度高的逆向温度场,降低粗轧机组轧制过程中钢材的变形抗力;为后续精轧机组低温铁素体温度区间轧制奠定了基础;
21.5、本发明采用末机架轧制润滑以及动态窜辊,提高薄规格带钢在变形后的组织均匀性和豆高豆形,获得性能均匀的花纹钢板,克服了低温轧制下末机架出口带钢变形迅速冷却导致晶粒过小不均匀,以及残余应力引发的板形不良,以获取更优良的板形和成形性。
具体实施方式
22.下面结合具体实施方式对本发明进一步说明。
23.出于以下详细描述的目的,应该理解的是,除非明确相反地指出,否则本发明可以采取各种替代变型和步骤次序。此外,除了在任何操作实例中或在另外指示的地方以外,所有表示例如说明书和权利要求中使用的成分的量的数字在所有情况下均应理解为由术语“约”修饰。至少,并且不企图限制对权利要求书的范围的相等物的原理的应用,每个数字参数应至少按照报告的有效数字的数量并通过应用普通的舍入技术来理解。
24.尽管阐述本发明的广泛范围的数值范围和参数是近似值,但具体实例中阐述的数值尽可能精确地报告。然而,任何数值固有地含有某些由其相应测试测量值中所发现的标准差必然造成的误差。
25.还应理解的是,本文陈述的任何数值范围旨在包含所有其中纳入的子范围。例如,“1到10”的范围旨在包含所有介于(及包含)所陈述的最小值1及所陈述的最大值10之间的子范围,也就是说,具有等于或大于1的最小值及等于或小于10的最大值。
26.在本技术中,除非另外特别说明,否则单数的使用包含复数并且复数涵盖单数。另外,在本技术中,除非另有明确说明,否则“或”的使用意指“和/或”,即使在某些情况下可以明确地使用“和/或”。进一步地,在本技术中,除非另外特别说明,否则“一个”或“一种”的使用意指“至少一个/种”。例如,“一种”第一材料、“一种”涂料组合物等是指这些项目中的任何项目中的一个或多个项目。
27.本发明花纹钢板化学成分及质量百分比含量为:c:0.01~0.05%、si:0.01~0.1%、mn:0.06~0.3%、p<0.035%、s<0.006%、n<0.006%,其余为fe和不可避免的不纯物。
28.本发明关键成分控制说明:
29.c:c对钢的相变点影响明显,是决定铁素体轧制工艺窗口的关键元素之一,一般随c含量的增加,铁素体温度区间减小,奥氏体向铁素体相变温度降低。如将c元素含量控制过低会使冶炼成本大幅增加。研究表明,低碳钢的平均变形抗力,在奥氏体温度范围内(900~1010℃)和铁素体温度范围(750~840℃)的轧制变形抗力几乎相等,而c含量大于0.05%的低碳钢采用铁素体轧制时,变形抗力偏大,成品组织不均匀,延伸率偏低。c含量在0.06%~0.15%范围内,钢水凝固过程受包晶反应影响使铸坯表面容易发生裂纹,严重时引发漏钢事故,并且过高的c含量对焊接性能不利,因此本发明将c含量控制在0.01~0.05%。
30.n:n原子拥有两种存在形式,一种是处于固溶状态,另一种处于析出状态。固溶n严重影响钢材的成形性能,并且n原子与位错发生交互作用形成柯氏气团后,影响钢材的应变时效。因此本发明将n含量控制在<0.006%。
31.mn:mn具有固溶强化作用,可扩大γ区,降低γ
→
α相变温度,细化晶粒,mn还可推迟珠光体转变,有利于贝氏体形成。因此本发明将mn含量控制在0.06~0.3%。
32.p和s:p和s为铁水中残余的有害元素,因此本发明为保障钢的生产稳定和成形性能,p<0.035%、s<0.006%。
33.本发明工艺流程路线为:冶炼、连铸、连轧、卷取后制成不同厚度的花纹钢板。具体方法如下:
34.s1:冶炼
35.将原材料进行转炉冶炼及lf炉冶炼得到钢水;钢水化学成分及质量百分比含量为:c:0.01~0.05%、si:0.01~0.1%、mn:0.06~0.3%、p<0.035%、s<0.006%、n<0.006%,其余为fe和不可避免的不纯物。
36.s2:连铸
37.采用直弧式高拉速连铸机,冶炼所得钢水进入连铸机获得铸坯;铸坯厚度采用90~110mm,拉速与铸坯厚度有关系,薄的铸坯拉速可以高,厚铸坯拉速就要低,本实施例为110mm铸坯,拉速在3.8~5.8m/min范围。
38.扇形段采用前段高压水快速冷却,水压10~20bar,水量占总冷却水量75~85%;
39.后段应用气雾冷却,充分利用铸坯芯部温度高的逆向温度场提高铸坯组织的均匀性;并且铸坯芯部热量扩散至表面,减少在铸坯生产过程中的温度损失。
40.s3:连轧
41.具体包括:粗轧
→
感应加热
→
高压除鳞
→
精轧。
42.粗轧:粗轧出口温度950~1100℃;中间坯厚度为9~18mm。较高的粗轧出口温度设定,充分利用铸坯芯部扩散至表面的热量,连铸工序中铸坯芯部较高的热量储存得以利用,铸坯温度分布呈现芯部温度高的逆向温度场,降低粗轧机组轧制过程中钢材的变形抗力,提高变形后的组织均匀性,为后续精轧机组低温铁素体温度区间轧制奠定了基础。
43.精轧:
44.(1)精轧入口温度870~1000℃,出口温度控制范围为740~810℃,通过调整感应式加热炉出口温度设定达到控制精轧出口温度的目的。实现精轧机组部分或大全部在钢材变形抗力较小的低温铁素体温度区间轧制,大幅降低了加热成本,节省电耗,是一种节能环保的生产工艺;
45.(2)精轧末机架上工作辊采用花纹辊,花纹辊通过平辊刻辊形成,下工作辊采用普通凹辊,凸度为-30~-70μm,实施例中辊形长度约1330mm,用于生产1250mm宽度的花纹钢板;
46.(3)精轧末机架(f5)应用动态窜辊以弥补工作辊在使用过程中的局部磨损不均带来的不良影响,有利于保持工作辊原始辊形,改善带钢板形;
47.(4)末机架(f5)应用100:5000(ml,油水比,有机润滑液)的轧制润滑液进行润滑轧制,减少花纹板表面豆形脱模过程中对轧辊豆形的损坏,降低轧制负荷,减小带钢与工作辊之间的摩擦力,延长工作辊使用寿命,可有效提高薄规格花纹板产量。并且有助于改善带钢表面质量、降低轧机电耗,同时提高薄规格带钢在变形后的组织均匀性,获得性能均匀的花纹钢板;
48.(5)精轧末机架(f5)压下率采用14~20%,f5出口可获得花纹钢板厚度范围是0.8~6.0mm。优选厚度为0.9~1.5mm。
49.s4:卷取
50.卷取温度600~700℃。
51.本发明采用较高的卷取温度设定配合较低的精轧出口温度设定,达到层流冷却不投用水冷的效果,也可通过关闭层流冷却禁用设备功能的方式进行实施,目的是避免花纹钢板上表面由于豆高阻碍而残留冷却水导致带钢冷却不均匀、残余应力过大引发板形不良。在末机架出口带钢变形后,完全靠带钢与空气和接触设备间传热缓慢冷却,避免末机架出口带钢变形迅速冷却导致晶粒过小且不均匀,促进铁素体晶粒的长大。同时较高的卷取温度有利于带钢卷取后的内应力的释放,以获取更优良的板形和成形性。
52.最终获得0.9~1.5mm薄规格花纹钢板。
53.为了更好地比较本技术和现有技术,进行了对比试验。
54.实施例1~4为本技术成分设计和生产工艺。
55.对照组采用实施例1的成分设计,结合本公司专利《基于esp薄板坯连铸连轧流程生产薄规格花纹钢板的方法》(公开号cn106077090b)中的工艺方案,连铸机需在后段气雾冷却基础上加强冷却水,或延长扇形段方式以获得较低的粗轧出口温度(800~860℃)。卷取冷却方式为依次通过层冷系统底部冷却和层冷系统上部冷却,但精轧部分采用低温铁素体温度区间轧制。
56.1.各组成分设计:
[0057][0058]
2.各组生产参数控制参见下表:
[0059][0060]
对比结果见下表:
[0061][0062][0063]
由上述结果可以看出,使用本发明的各个实施例组,最薄可生产0.9mm厚度花纹钢板。1.2mm厚度花纹钢板实测基板厚度1.199mm,豆高0.220mm,满足薄规格花纹钢板的市场客户需求。连浇炉数为8炉(约2300t钢水)的轧程产出1.2mm规格花纹钢板1300吨以上,满足工业化连续生产。而对照组中采用传统连铸、粗轧,仅仅是在精轧部分改良应用低温铁素体轧制,且不配合末机架(f5)调整,其结果钢板表面豆形呈现明显粗糙、豆高偏小、豆形不饱满,且强度偏高,延伸率较低,不能满足性能需求。
[0064]
需要说明的是,本发明的特定实施方案已经对本发明进行了详细描述,对于本领域的技术人员来说,在不背离本发明的精神和范围的情况下对它进行的各种显而易见的改变都在本发明的保护范围之内。
再多了解一些
本文用于企业家、创业者技术爱好者查询,结果仅供参考。