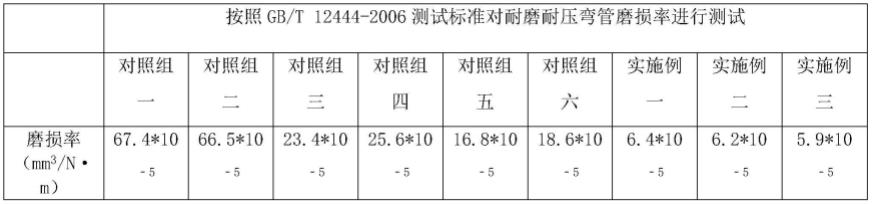
1.本发明涉及金属弯管技术领域,更具体地说,本发明涉及一种耐磨耐压弯管的制备工艺。
背景技术:
2.弯管是采用成套弯曲设备进行弯曲的,可分为冷煨与热推两种工艺,煨制弯管具有较好的伸缩性、耐压高、阻力小等优点,冷煨弯管是一种在室温下不加热或不改变材料结构的弯曲方式,热推弯管又称中频热推弯管,切割材料后,直管放置在钢管弯曲部分的感应环上,管头被机械旋转臂卡住,中频电流用来加热感应环中的钢管;当钢管温度上升到塑性状态时,钢管在钢管后端的机械推力推动弯曲,弯管部分用冷却剂快速冷却,使弯管在加热、推挤、弯曲和冷却的同时不断弯曲。弯管主要用以输油、输气、输液,工程桥梁建设等。弯管的材料有铸铁、可锻铸铁、不锈钢、合金钢、碳钢、有色金属及塑料等材质。
3.现在的弯管在输送物料过程中,物料补充冲击到弯管内壁,可对弯管进行磨损,长期输送过程中,弯管内壁磨损腐蚀严重,容易发生损伤,且不便于维修。
技术实现要素:
4.为了克服现有技术的上述缺陷,本发明的实施例提供一种耐磨耐压弯管的制备工艺。
5.一种耐磨耐压弯管的制备工艺,具体制备步骤如下:
6.步骤一:以不锈钢管为内衬层,以直缝焊管为外基层采用液压成型法,制成双金属复合管;
7.步骤二:采用双金属复合管进行热推加工,制成耐压弯管;
8.步骤三:采用聚四氟乙烯复合材料喷涂到弯管内壁和外壁,得到半成品耐磨耐压弯管;
9.步骤四:对半成品耐磨耐压弯管进行等离子体增强化学气相沉积法处理,得到耐磨耐压弯管。
10.进一步的,在步骤三中的所述聚四氟乙烯复合材料按照重量百分比计算包括:3.6~4.6%的聚氧化乙烯、9.6~10.6%的硅灰石、15.6~16.6%的聚乙烯吡咯烷酮、8.6~9.6%的碳纤维、6.6~7.6%的补充剂,其余为聚四氟乙烯树脂;补充剂按照重量百分比计算包括:40.6~42.6%的聚酰胺酸、12.6~13.6%的水性聚氨酯,其余为聚酰胺酰亚胺;
11.所述聚四氟乙烯复合材料的制备工艺,具体制备步骤如下:
12.s1:称取上述原料中的聚氧化乙烯、硅灰石、聚乙烯吡咯烷酮、碳纤维、聚四氟乙烯树脂、补充剂中的聚酰胺酸、水性聚氨酯和聚酰胺酰亚胺;
13.s2:将步骤s1中的聚酰胺酸、水性聚氨酯和聚酰胺酰亚胺进行水浴超声处理20~30min,得到混合料a;
14.s3:将步骤s2中的混合料进行静电纺丝,得到纳米纤维结构的补充剂;
15.s4:将步骤s1中的二分之一重量份的聚氧化乙烯、硅灰石、聚乙烯吡咯烷酮、碳纤维进行水浴超声处理20~30min,得到混合料b;
16.s5:将步骤s1中的剩余的聚氧化乙烯、硅灰石、聚乙烯吡咯烷酮、碳纤维和二分之一重量份的聚四氟乙烯树脂进行水浴超声处理10~20min,得到混合料c;
17.s6:将步骤s1中剩余的聚四氟乙烯树脂、步骤s3中制得的补充剂、步骤s4中制得的混合料b加入到步骤s5中制得的混合料c中进行共混超声处理10~20min,得到聚四氟乙烯复合材料;
18.进一步的,所述聚四氟乙烯复合材料按照重量百分比计算包括:3.6%的聚氧化乙烯、9.6%的硅灰石、15.6%的聚乙烯吡咯烷酮、8.6%的碳纤维、6.6%的补充剂,其余为聚四氟乙烯树脂;补充剂按照重量百分比计算包括:40.6%的聚酰胺酸、12.6%的水性聚氨酯,其余为聚酰胺酰亚胺;
19.进一步的,所述聚四氟乙烯复合材料按照重量百分比计算包括:4.6%的聚氧化乙烯、10.6%的硅灰石、16.6%的聚乙烯吡咯烷酮、9.6%的碳纤维、7.6%的补充剂,其余为聚四氟乙烯树脂;补充剂按照重量百分比计算包括:42.6%的聚酰胺酸、13.6%的水性聚氨酯,其余为聚酰胺酰亚胺;
20.进一步的,所述聚四氟乙烯复合材料按照重量百分比计算包括:4.1%的聚氧化乙烯、10.1%的硅灰石、16.1%的聚乙烯吡咯烷酮、9.1%的碳纤维、7.1%的补充剂,其余为聚四氟乙烯树脂;补充剂按照重量百分比计算包括:41.6%的聚酰胺酸、13.1%的水性聚氨酯,其余为聚酰胺酰亚胺;
21.进一步的,在步骤一中,液压成型法中,胀形压力160~180mpa、初始间隙1.5~2.5mm、衬管壁厚2~4mm;在步骤二中,热推加工过程中,加热温度为950~980℃、保温时间为2~3min;喷水冷却速度为9~15℃/s;回火温度为480~510℃、保温时间为45~51min;在步骤三中,采用静电喷涂加工处理,静电高压为70~80kv,静电电流为10~20μa,流速压力为0.35~0.45mpa,雾化压力为0.36~0.40mpa,喷枪口与管壁距离为230~260mm;在步骤四中,等离子体增强化学气相沉积处理过程中,将半成品耐磨耐压弯管放入到等离子体增强化学气相沉积设备中的沉积室内部,抽真空,然后通入氮气进行预处理,同时通入甲烷进行沉积处理;氮气通入流量为75~85sccm,甲烷通入流量为6~8sccm,射频功率为160~180w,生长70~80min,反应温度为350~370℃。
22.进一步的,在步骤一中,液压成型法中,胀形压力180mpa、初始间隙2.5mm、衬管壁厚4mm;在步骤二中,热推加工过程中,加热温度为980℃、保温时间为3min;喷水冷却速度为15℃/s;回火温度为510℃、保温时间为51min;在步骤三中,采用静电喷涂加工处理,静电高压为80kv,静电电流为20μa,流速压力为0.45mpa,雾化压力为0.40mpa,喷枪口与管壁距离为260mm;在步骤四中,等离子体增强化学气相沉积处理过程中,将半成品耐磨耐压弯管放入到等离子体增强化学气相沉积设备中的沉积室内部,抽真空,然后通入氮气进行预处理,同时通入甲烷进行沉积处理;氮气通入流量为85sccm,甲烷通入流量为8sccm,射频功率为180w,生长80min,反应温度为370℃。
23.进一步的,在步骤一中,液压成型法中,胀形压力170mpa、初始间隙2.0mm、衬管壁厚3mm;在步骤二中,热推加工过程中,加热温度为965℃、保温时间为2.5min;喷水冷却速度为12℃/s;回火温度为495℃、保温时间为48min;在步骤三中,采用静电喷涂加工处理,静电
高压为75kv,静电电流为15μa,流速压力为0.40mpa,雾化压力为0.38mpa,喷枪口与管壁距离为245mm;在步骤四中,等离子体增强化学气相沉积处理过程中,将半成品耐磨耐压弯管放入到等离子体增强化学气相沉积设备中的沉积室内部,抽真空,然后通入氮气进行预处理,同时通入甲烷进行沉积处理;氮气通入流量为80sccm,甲烷通入流量为7sccm,射频功率为170w,生长75min,反应温度为360℃。
24.进一步的,在步骤s2中,水浴温度为70~80℃,超声处理频率为25~27khz,功率为1000~1100w;在步骤s3中,静电纺丝过程中,电压13~15kv,接收距离14~16cm,纺丝液流速0.9~1.3ml/h;在步骤s4中,水浴温度为50~60℃,超声处理频率为23~25khz,功率为1100~1200w;在步骤s5中,水浴温度为60~70℃,超声处理频率为28~30khz,功率为900~1000w;在步骤s6中,超声处理频率为1.5~1.7mhz,功率为400~500w。
25.进一步的,在步骤s2中,水浴温度为75℃,超声处理频率为26khz,功率为1050w;在步骤s3中,静电纺丝过程中,电压14kv,接收距离15cm,纺丝液流速1.1ml/h;在步骤s4中,水浴温度为55℃,超声处理频率为24khz,功率为1150w;在步骤s5中,水浴温度为65℃,超声处理频率为29khz,功率为950w;在步骤s6中,超声处理频率为1.6mhz,功率为450w。
26.本发明的技术效果和优点:
27.1、采用本发明的制备方法制备的耐磨耐压弯管,在步骤一中,以不锈钢管为内衬层、直缝焊管为外基层制成双金属复合管,保证弯管的耐压、耐磨、耐腐蚀性能;在步骤二中,对双金属复合管进行热推处理,可有效保证弯管热推处理效果,弯管质量更佳;在步骤三中,在弯管内壁外壁静电喷涂形成聚四氟乙烯复合材料涂层,可有效加强弯管内壁和外壁耐磨和防腐蚀性能;在步骤四中,进行等离子体增强化学气相沉积处理,氮气对聚四氟乙烯表面进行更改性处理,通过pecvd技术在聚四氟乙烯复合材料涂层上制备了类金刚石薄膜,在聚四氟乙烯复合材料涂层表面沉积了氢化非晶碳薄膜,可有效降低弯管内壁和外壁表面磨损率,且碳薄膜与聚四氟乙烯复合材料涂层的结合力更大,保证氢化非晶碳薄膜与聚四氟乙烯复合材料涂层之间连接的稳定性;在步骤s6中进行高频超声处理,可有效加强聚四氟乙烯复合材料中原料的共混复合效果,同时原料在超声低频和高频配合处理下,可有效加强聚四氟乙烯复合材料中原料的结合效果和分布均匀效果;
28.2、本发明中聚四氟乙烯为基材,保证聚四氟乙烯复合材料的安全性和稳定性;可在聚四氟乙烯复合材料涂层中形成聚四氟乙烯微纳米纤维膜,可有效加强聚四氟乙烯复合材料涂层的耐用性、耐磨稳定性、耐酸碱稳定性和耐热稳定性;可对聚四氟乙烯复合材料涂层进行改性处理,可有效加强聚四氟乙烯复合材料涂层的耐磨损性能和稳定性;静电纺丝形成纳米纤维结构的补充剂,聚乙烯吡咯烷酮、水性聚氨酯进行复合,可有效加强补充剂的耐水性能和力学性能;补充剂共混合聚四氟乙烯复合材料中,聚酰胺酸、聚酰胺酰亚胺以纳米纤维形式加入到聚四氟乙烯复合材料涂层中,可有效加强聚四氟乙烯复合材料涂层的热稳定性能。
具体实施方式
29.下面将结合本发明实施例中的技术方案进行清楚、完整地描述,显然,所描述的实施例仅仅是本发明一部分实施例,而不是全部的实施例。基于本发明中的实施例,本领域普通技术人员在没有做出创造性劳动前提下所获得的所有其他实施例,都属于本发明保护的
范围。
30.实施例1:
31.本发明提供了一种耐磨耐压弯管的制备工艺,具体制备步骤如下:
32.步骤一:以不锈钢管为内衬层,以直缝焊管为外基层采用液压成型法,制成双金属复合管;
33.步骤二:采用双金属复合管进行热推加工,制成耐压弯管;
34.步骤三:采用聚四氟乙烯复合材料喷涂到弯管内壁和外壁,得到半成品耐磨耐压弯管;
35.步骤四:对半成品耐磨耐压弯管进行等离子体增强化学气相沉积法处理,得到耐磨耐压弯管;
36.所述聚四氟乙烯复合材料按照重量百分比计算包括:3.6%的聚氧化乙烯、9.6%的硅灰石、15.6%的聚乙烯吡咯烷酮、8.6%的碳纤维、6.6%的补充剂,其余为聚四氟乙烯树脂;补充剂按照重量百分比计算包括:40.6%的聚酰胺酸、12.6%的水性聚氨酯,其余为聚酰胺酰亚胺;
37.所述聚四氟乙烯复合材料的制备工艺,具体制备步骤如下:
38.s1:称取上述原料中的聚氧化乙烯、硅灰石、聚乙烯吡咯烷酮、碳纤维、聚四氟乙烯树脂、补充剂中的聚酰胺酸、水性聚氨酯和聚酰胺酰亚胺;
39.s2:将步骤s1中的聚酰胺酸、水性聚氨酯和聚酰胺酰亚胺进行水浴超声处理20~30min,得到混合料a;
40.s3:将步骤s2中的混合料进行静电纺丝,得到纳米纤维结构的补充剂;
41.s4:将步骤s1中的二分之一重量份的聚氧化乙烯、硅灰石、聚乙烯吡咯烷酮、碳纤维进行水浴超声处理20~30min,得到混合料b;
42.s5:将步骤s1中的剩余的聚氧化乙烯、硅灰石、聚乙烯吡咯烷酮、碳纤维和二分之一重量份的聚四氟乙烯树脂进行水浴超声处理10~20min,得到混合料c;
43.s6:将步骤s1中剩余的聚四氟乙烯树脂、步骤s3中制得的补充剂、步骤s4中制得的混合料b加入到步骤s5中制得的混合料c中进行共混超声处理10~20min,得到聚四氟乙烯复合材料。
44.在步骤一中,液压成型法中,胀形压力160mpa、初始间隙1.5mm、衬管壁厚2mm;在步骤二中,热推加工过程中,加热温度为950℃、保温时间为2min;喷水冷却速度为9℃/s;回火温度为480℃、保温时间为45min;在步骤三中,采用静电喷涂加工处理,静电高压为70kv,静电电流为10μa,流速压力为0.35mpa,雾化压力为0.36mpa,喷枪口与管壁距离为230mm;在步骤四中,等离子体增强化学气相沉积处理过程中,将半成品耐磨耐压弯管放入到等离子体增强化学气相沉积设备中的沉积室内部,抽真空,然后通入氮气进行预处理,同时通入甲烷进行沉积处理;氮气通入流量为75sccm,甲烷通入流量为6sccm,射频功率为160w,生长70min,反应温度为350℃;在步骤s2中,水浴温度为70℃,超声处理频率为25khz,功率为1000w;在步骤s3中,静电纺丝过程中,电压13kv,接收距离14cm,纺丝液流速0.9ml/h;在步骤s4中,水浴温度为50℃,超声处理频率为23khz,功率为1100w;在步骤s5中,水浴温度为60℃,超声处理频率为28khz,功率为900w;在步骤s6中,超声处理频率为1.5mhz,功率为400w。
45.实施例2:
46.与实施例1不同的是,在步骤一中,液压成型法中,胀形压力180mpa、初始间隙2.5mm、衬管壁厚4mm;在步骤二中,热推加工过程中,加热温度为980℃、保温时间为3min;喷水冷却速度为15℃/s;回火温度为510℃、保温时间为51min;在步骤三中,采用静电喷涂加工处理,静电高压为80kv,静电电流为20μa,流速压力为0.45mpa,雾化压力为0.40mpa,喷枪口与管壁距离为260mm;在步骤四中,等离子体增强化学气相沉积处理过程中,将半成品耐磨耐压弯管放入到等离子体增强化学气相沉积设备中的沉积室内部,抽真空,然后通入氮气进行预处理,同时通入甲烷进行沉积处理;氮气通入流量为85sccm,甲烷通入流量为8sccm,射频功率为180w,生长80min,反应温度为370℃。
47.实施例3:
48.与实施例1-2均不同的是,在步骤一中,液压成型法中,胀形压力170mpa、初始间隙2.0mm、衬管壁厚3mm;在步骤二中,热推加工过程中,加热温度为965℃、保温时间为2.5min;喷水冷却速度为12℃/s;回火温度为495℃、保温时间为48min;在步骤三中,采用静电喷涂加工处理,静电高压为75kv,静电电流为15μa,流速压力为0.40mpa,雾化压力为0.38mpa,喷枪口与管壁距离为245mm;在步骤四中,等离子体增强化学气相沉积处理过程中,将半成品耐磨耐压弯管放入到等离子体增强化学气相沉积设备中的沉积室内部,抽真空,然后通入氮气进行预处理,同时通入甲烷进行沉积处理;氮气通入流量为80sccm,甲烷通入流量为7sccm,射频功率为170w,生长75min,反应温度为360℃。
49.分别取上述实施例1-3中的耐磨耐压弯管的制备工艺与对照组一的耐磨耐压弯管的制备工艺、对照组二的耐磨耐压弯管的制备工艺、对照组三的耐磨耐压弯管的制备工艺、对照组四的耐磨耐压弯管的制备工艺、对照组五的耐磨耐压弯管的制备工艺和对照组六的耐磨耐压弯管的制备工艺,对照组一的耐磨耐压弯管的制备工艺与实施例三相比在步骤三中直接对弯管内壁贴附聚四氟乙烯膜;对照组二的耐磨耐压弯管的制备工艺与实施例三相比没有步骤四中的加工处理;对照组三的耐磨耐压弯管的制备工艺与实施例三相比在步骤四中采用化学气相沉积处理;对照组四的耐磨耐压弯管的制备工艺与实施例三相比直接将聚四氟乙烯复合材料的全部原料进行混合;对照组五的耐磨耐压弯管的制备工艺与实施例三相比在步骤s3中没有进行静电纺丝;对照组六的耐磨耐压弯管的制备工艺与实施例三相比在步骤s4和步骤s5中没有进行超声处理;分九组分别测试三个实施例中加工制得的耐磨耐压弯管以及六个对照组的耐磨耐压弯管的制备工艺处理后的耐磨耐压弯管,不锈钢钢管材质为304l不锈钢,直缝焊管材质为q235b,聚酰胺酸(常州市润川塑胶材料有限公司)、聚酰胺酰亚胺(南通博联材料科技有限公司)、水性聚氨酯(浙江罗星实业有限公司)、硅灰石(山东多聚化学有限公司cas 13983-17-0,塑料橡胶级硅灰石)、碳纤维(吉林市晟鑫碳纤维有限公司水溶性碳纤维短纤2mm)、聚四氟乙烯(四氟新材料(苏州)有限公司)、聚氧化乙烯(南通润丰石油化工有限公司68441-17-8)、聚乙烯吡咯烷酮(山东昌耀新材料有限公司9003-39-8),进行测试,测试结果如表一所示:
50.表一:
[0051][0052]
由表一可知,实施例3为本发明的较佳实施方式;在步骤一中,以不锈钢管为内衬层、直缝焊管为外基层,在胀形压力170mpa、初始间隙2.0mm、衬管壁厚3mm条件下制成双金属复合管,不锈钢管在双金属复合管内部进行防腐蚀耐磨处理,直缝焊管在双金属复合管外部进行耐压支撑,保证弯管的耐压、耐磨、耐腐蚀性能;在步骤二中,对双金属复合管进行加热温度为965℃、保温时间为2.5min;喷水冷却速度为12℃/s;回火温度为495℃、保温时间为48min热推处理,可有效保证弯管热推处理效果,弯管质量更佳;在步骤三中,将聚四氟乙烯复合材料,采用静电高压为75kv,静电电流为15μa,流速压力为0.40mpa,雾化压力为0.38mpa,喷枪口与管壁距离为245mm静电喷涂到弯管内壁和外壁,在弯管内壁外壁形成聚四氟乙烯复合材料涂层,可有效加强弯管内壁和外壁耐磨和防腐蚀性能;在步骤四中,采用氮气通入流量为80sccm预处理,甲烷通入流量为7sccm沉积处理,射频功率为170w,生长75min,反应温度为360℃,进行等离子体增强化学气相沉积处理,氮气对聚四氟乙烯表面进行更改性处理,通过pecvd技术在聚四氟乙烯复合材料涂层上制备了类金刚石薄膜,在聚四氟乙烯复合材料涂层表面沉积了氢化非晶碳薄膜,可有效降低弯管内壁和外壁表面磨损率,且碳薄膜与聚四氟乙烯复合材料涂层的结合力更大,保证氢化非晶碳薄膜与聚四氟乙烯复合材料涂层之间连接的稳定性;在步骤s3中,静电纺丝制得的纳米纤维结构的补充剂,使得补充剂在后续聚四氟乙烯复合材料中的分布更加均匀,涂层稳定性更佳;在步骤s4和步骤s5中分别对混合料b和混合料c进行低频超声处理,对混合料b和混合料c进行空化超声处理,可有效加强混合料b和混合料c中的物质进行分别加速结合反应处理;在步骤s6中进行高频超声处理,可有效加强聚四氟乙烯复合材料中原料的共混复合效果,同时原料在超声低频和高频配合处理下,可有效加强聚四氟乙烯复合材料中原料的结合效果和分布均匀效果。
[0053]
实施例4:
[0054]
本发明提供了一种耐磨耐压弯管的制备工艺,具体制备步骤如下:
[0055]
步骤一:以不锈钢管为内衬层,以直缝焊管为外基层采用液压成型法,制成双金属复合管;
[0056]
步骤二:采用双金属复合管进行热推加工,制成耐压弯管;
[0057]
步骤三:采用聚四氟乙烯复合材料喷涂到弯管内壁和外壁,得到半成品耐磨耐压弯管;
[0058]
步骤四:对半成品耐磨耐压弯管进行等离子体增强化学气相沉积法处理,得到耐磨耐压弯管;
[0059]
所述聚四氟乙烯复合材料按照重量百分比计算包括:3.6%的聚氧化乙烯、9.6%的硅灰石、15.6%的聚乙烯吡咯烷酮、8.6%的碳纤维、6.6%的补充剂,其余为聚四氟乙烯树脂;补充剂按照重量百分比计算包括:40.6%的聚酰胺酸、12.6%的水性聚氨酯,其余为
聚酰胺酰亚胺;
[0060]
所述聚四氟乙烯复合材料的制备工艺,具体制备步骤如下:
[0061]
s1:称取上述原料中的聚氧化乙烯、硅灰石、聚乙烯吡咯烷酮、碳纤维、聚四氟乙烯树脂、补充剂中的聚酰胺酸、水性聚氨酯和聚酰胺酰亚胺;
[0062]
s2:将步骤s1中的聚酰胺酸、水性聚氨酯和聚酰胺酰亚胺进行水浴超声处理20~30min,得到混合料a;
[0063]
s3:将步骤s2中的混合料进行静电纺丝,得到纳米纤维结构的补充剂;
[0064]
s4:将步骤s1中的二分之一重量份的聚氧化乙烯、硅灰石、聚乙烯吡咯烷酮、碳纤维进行水浴超声处理20~30min,得到混合料b;
[0065]
s5:将步骤s1中的剩余的聚氧化乙烯、硅灰石、聚乙烯吡咯烷酮、碳纤维和二分之一重量份的聚四氟乙烯树脂进行水浴超声处理10~20min,得到混合料c;
[0066]
s6:将步骤s1中剩余的聚四氟乙烯树脂、步骤s3中制得的补充剂、步骤s4中制得的混合料b加入到步骤s5中制得的混合料c中进行共混超声处理10~20min,得到聚四氟乙烯复合材料。
[0067]
在步骤一中,液压成型法中,胀形压力170mpa、初始间隙2.0mm、衬管壁厚3mm;在步骤二中,热推加工过程中,加热温度为965℃、保温时间为2.5min;喷水冷却速度为12℃/s;回火温度为495℃、保温时间为48min;在步骤三中,采用静电喷涂加工处理,静电高压为75kv,静电电流为15μa,流速压力为0.40mpa,雾化压力为0.38mpa,喷枪口与管壁距离为245mm;在步骤四中,等离子体增强化学气相沉积处理过程中,将半成品耐磨耐压弯管放入到等离子体增强化学气相沉积设备中的沉积室内部,抽真空,然后通入氮气进行预处理,同时通入甲烷进行沉积处理;氮气通入流量为80sccm,甲烷通入流量为7sccm,射频功率为170w,生长75min,反应温度为360℃;在步骤s2中,水浴温度为70℃,超声处理频率为25khz,功率为1000w;在步骤s3中,静电纺丝过程中,电压13kv,接收距离14cm,纺丝液流速0.9ml/h;在步骤s4中,水浴温度为50℃,超声处理频率为23khz,功率为1100w;在步骤s5中,水浴温度为60℃,超声处理频率为28khz,功率为900w;在步骤s6中,超声处理频率为1.5mhz,功率为400w。
[0068]
实施例5:
[0069]
与实施例4不同的是,所述聚四氟乙烯复合材料按照重量百分比计算包括:4.6%的聚氧化乙烯、10.6%的硅灰石、16.6%的聚乙烯吡咯烷酮、9.6%的碳纤维、7.6%的补充剂,其余为聚四氟乙烯树脂;补充剂按照重量百分比计算包括:42.6%的聚酰胺酸、13.6%的水性聚氨酯,其余为聚酰胺酰亚胺;在步骤s2中,水浴温度为70~80℃,超声处理频率为25~27khz,功率为1000~1100w;在步骤s3中,静电纺丝过程中,电压15kv,接收距离16cm,纺丝液流速1.3ml/h;在步骤s4中,水浴温度为60℃,超声处理频率为25khz,功率为1200w;在步骤s5中,水浴温度为70℃,超声处理频率为30khz,功率为1000w;在步骤s6中,超声处理频率为1.7mhz,功率为500w。
[0070]
实施例6:
[0071]
与实施例4-5均不同的是,所述聚四氟乙烯复合材料按照重量百分比计算包括:4.1%的聚氧化乙烯、10.1%的硅灰石、16.1%的聚乙烯吡咯烷酮、9.1%的碳纤维、7.1%的补充剂,其余为聚四氟乙烯树脂;补充剂按照重量百分比计算包括:41.6%的聚酰胺酸、
13.1%的水性聚氨酯,其余为聚酰胺酰亚胺;在步骤s2中,水浴温度为75℃,超声处理频率为26khz,功率为1050w;在步骤s3中,静电纺丝过程中,电压14kv,接收距离15cm,纺丝液流速1.1ml/h;在步骤s4中,水浴温度为55℃,超声处理频率为24khz,功率为1150w;在步骤s5中,水浴温度为65℃,超声处理频率为29khz,功率为950w;在步骤s6中,超声处理频率为1.6mhz,功率为450w。
[0072]
分别取上述实施例4-6所制得的耐磨耐压弯管的制备工艺对照组七的耐磨耐压弯管的制备工艺、对照组八的耐磨耐压弯管的制备工艺、对照组九的耐磨耐压弯管的制备工艺、对照组十的耐磨耐压弯管的制备工艺、对照组十一的耐磨耐压弯管的制备工艺、对照组十二的耐磨耐压弯管的制备工艺,对照组七的耐磨耐压弯管的制备工艺与实施例六相比没有聚氧化乙烯,对照组八的耐磨耐压弯管的制备工艺与实施例六相比没有硅灰石,对照组九的耐磨耐压弯管的制备工艺与实施例六相比没有聚乙烯吡咯烷酮,对照组十的耐磨耐压弯管的制备工艺与实施例六相比没有碳纤维,对照组十一的耐磨耐压弯管的制备工艺与实施例六相比没有聚酰胺酸,对照组十二的耐磨耐压弯管的制备工艺与实施例六相比没有聚酰胺酰亚胺;分九组分别测试三个实施例中加工制得的耐磨耐压弯管以及六个对照组的耐磨耐压弯管的制备工艺处理后的耐磨耐压弯管,聚酰胺酸(常州市润川塑胶材料有限公司)、聚酰胺酰亚胺(南通博联材料科技有限公司)、水性聚氨酯(浙江罗星实业有限公司)、硅灰石(山东多聚化学有限公司cas 13983-17-0,塑料橡胶级硅灰石)、碳纤维(吉林市晟鑫碳纤维有限公司水溶性碳纤维短纤2mm)、聚四氟乙烯(四氟新材料(苏州)有限公司)、聚氧化乙烯(南通润丰石油化工有限公司68441-17-8)、聚乙烯吡咯烷酮(山东昌耀新材料有限公司9003-39-8),进行测试,测试结果如表二所示:
[0073]
表二:
[0074][0075][0076]
由表二可知,实施例6为本发明的较佳实施方式;聚四氟乙烯复合材料中的聚四氟乙烯树脂作为基材,保证聚四氟乙烯复合材料的安全性和稳定性;聚氧化乙烯和聚乙烯吡咯烷酮作为聚四氟乙烯的复合载体,在聚四氟乙烯复合材料涂层中形成聚四氟乙烯微纳米纤维膜,可有效加强聚四氟乙烯复合材料涂层的耐用性、耐磨稳定性、耐酸碱稳定性和耐热稳定性;硅灰石和碳纤维对聚四氟乙烯进行协同改性,进而实现对聚四氟乙烯复合材料涂层进行改性处理,可有效加强聚四氟乙烯复合材料涂层的耐磨损性能和稳定性;聚酰胺酸、聚酰胺酰亚胺与水性聚氨酯在超声共混处理后静电纺丝,形成纳米纤维结构的补充剂,聚乙烯吡咯烷酮、水性聚氨酯进行复合,可有效加强补充剂的耐水性能和力学性能;碳纤维和聚酰胺酸进行复合,保证聚四氟乙烯复合材料涂层的热稳定性性能和耐磨性能;补充剂共混合聚四氟乙烯复合材料中,聚酰胺酸、聚酰胺酰亚胺以纳米纤维形式加入到聚四氟乙烯
复合材料涂层中,可有效加强聚四氟乙烯复合材料涂层的热稳定性能。
[0077]
最后应说明的是:以上所述仅为本发明的优选实施例而已,并不用于限制本发明,尽管参照前述实施例对本发明进行了详细的说明,对于本领域的技术人员来说,其依然可以对前述各实施例所记载的技术方案进行修改,或者对其中部分技术特征进行等同替换。凡在本发明的精神和原则之内,所作的任何修改、等同替换、改进等,均应包含在本发明的保护范围之内。
再多了解一些
本文用于企业家、创业者技术爱好者查询,结果仅供参考。