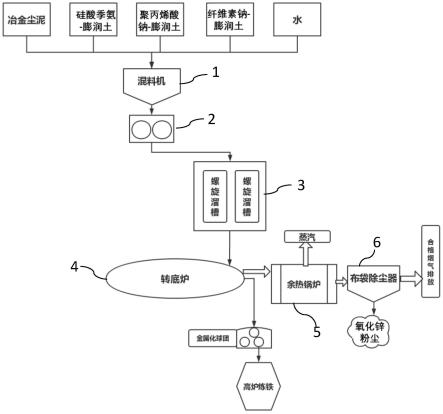
1.本发明属于冶金与能源领域,尤其涉及一种基于转底炉法处理钢铁冶金尘泥的方法及生产线。
背景技术:
2.钢铁冶炼要经过烧结、炼铁、炼钢三大工序,除尘灰产生的总量为钢产量的8%~15%,每年环保除尘回收的粉尘总量大约在10000万吨—16000万吨左右。其种类繁多、性质各异,成分复杂,利用难度大。对于很多没有环保意识的钢厂,都会选择填埋露天堆放的形式进行处理,而这些除尘灰中含有很多有害元素,对土壤、水质、大气环境等危害巨大。
3.现阶段转底炉法处置钢铁厂含锌粉尘已被较广泛的应用,含锌除尘灰在投入转底炉之前,需要通过粘结剂增加粘结力使其成型。转底炉工艺目前存在一些突出问题亟待解决:
①
本身球团(或团块)强度低、粉化率高达~30%,大量粉尘加速了耐材腐蚀和炉底板结,特别是含锌、铅和碱金属烟尘极易粘结,严重影响工艺顺行和产品质量;
②
压团工艺的粘结剂成本高,普遍使用淀粉类粘结剂,性质不稳定,每吨金属化球团用量高达6~8%;如果球团落下强度和抗压强度不足,在生产、转运、装卸过程中易破碎;没有足够热强度时,在转底炉高温下易粉化,所以粘合剂需要增加湿、冷强度和热强度。
4.目前,转底炉法处置钢铁厂含锌粉尘所采用的粘结剂主要是传统的红薯、木薯、玉米淀粉等粘结剂,虽有助于球团的成型,但还会有添加量大、成球率低、强度差、灰分大、引入的有害杂质多等缺点,会使除尘灰中的有害元素增加,且脱锌率和金属化率差,因此粘结剂对转底炉生产线生产顺行、生产成本、产品质量等具有重要影响,开发低成本新型高效粘结剂是未来转底炉发展趋势。
5.申请号cn201710306333.0公开了一种用于铜尾渣生产含碳球团的新型粘结剂、含碳球团及制造方法,其中,以重量份数计,用于铜尾渣生产的含碳球团包括铜尾渣100份、还原煤18~22份、石灰石8~12份、第一粘结剂2.5~3.5份、第二粘结剂0.3~0.5份和第三粘结剂0.03~0.05份,该技术对铜尾渣没有特定要求、3种粘结剂来源广泛且成本低廉、工艺操作简单、设备需求简单成本低,实现全自动化,生产能力大,节省成本;成型的含碳球团品质均匀性好、抗压强度大;成型的含碳球团适用于转底炉直接还原—磨矿磁选工艺生产铁精粉;但是该技术中粘结剂的添加方法复杂,添加量大,且是能适用于铜渣单一原料成型工艺。
6.申请号cn202110757761.1公开了一种转底炉专用的水性粘结剂及其生产方法,属于粘结剂技术领域;该技术采用淀粉残渣、聚乙烯醇、过硫酸铵、聚丙烯酰胺、氢氧化钠和水制备成适用于转底炉的水性粘结剂;但是该技术中的水性粘结剂制备工艺较复杂,需要增加专用的设备和管道,淀粉残渣在容易变质腐坏降低粘结剂粘结性,且水性粘结剂在转底炉产线生不利于连续添加生产。
7.申请号cn202110859890.1公开了一种转底炉含锌除尘灰球团用粘合剂及制备方法,包括按照一定的比例混合的原料,按照各组分的质量百分比,所述原料包括:酰胺0~
2%、cmc 0~8%、预糊化淀粉40~50%、纯碱0~5%、小苏打0~5%、氧化铝粉20~30%、膨润土15~25%;原料混合:将酰胺0~2%、cmc 0~8%、预糊化淀粉40~50%、纯碱0~5%、小苏打0~5%、氧化铝粉20~30%、膨润土15~25%的重量百分比配制混拌均匀;该技术中所用的配方过于复杂,加工制造成本较高,生产线上应用性不大。
8.鉴于上述情况,亟待研发一种新的转底炉法处置钢铁冶金尘泥的方法,能够有提高球团的成球率和强度,降低粘结剂的用量,同时能够有效减少球团在转底炉还原过程中的粉化现象。
技术实现要素:
9.针对现有技术中存在的上述缺陷,本发明的目的是提供一种基于转底炉法处理钢铁冶金尘泥的方法及生产线,采用硅酸季氨、聚丙烯酸钠、纤维素钠以及膨润土作为粘结剂,并将粘结剂通过强混机的加料口加入,确保粘结剂均匀分散在混合料中,从而减少粘结剂得用量,提高球团的成球率和强度,同时有效减少球团在转底炉还原过程中的粉化现象。
10.为实现上述目的,本发明采用如下技术方案:
11.本发明的第一方面提供了一种基于转底炉法处理钢铁冶金尘泥的生产线,包括:
12.强力混料机,用于钢铁冶金尘泥、粘结剂和水混合均匀,该混料机上设有冶金尘泥加料口、第一粘结剂加料口、第二粘结剂加料口、第三粘结剂加料口;
13.压球机,用于将所述强力混料机混合后的物料压制成球;该压球机与所述强力混料机的出料口之间通过皮带连接;
14.转底炉,该转底炉的转动炉底依次分为预热区、高温区和出料区,所述预热区、高温区和出料区之间均设有隔墙;所述高温区设有多个空气烧嘴和燃气烧嘴;该转底炉的进料口通过螺旋溜槽与所述压球机连通;
15.余热锅炉,用于回收所述转底炉内出来的含锌烟气内的热量;所述余热锅炉的烟气进口与所述转底炉的烟气出口连通;
16.除尘装置,用于将余热锅炉烟气出口出来的含锌烟气进行除尘处理;该除尘装置的烟气进口与所述余热锅炉的烟气出口连通。
17.优选地,所述强力混料机上还设有驱动机构和混料机构;所述混料机构包括设于所述混料机顶部的转轴以及设于所述转轴上的多个耙齿;所述驱动机构的输出端与所述混料机构的转轴连接,带动所述转轴混料机构转动。
18.优选地,所述螺旋溜槽包括固定支架以及设于所述固定支架上的溜槽本体;所述溜槽本体顶部设有加料口,底部设置有球团出料口和粉末出料口;所述溜槽本体的出料口与所述转底炉的进料口连通;和/或
19.所述转底炉的进料口设有振动布料器。
20.本发明的第二方面提供了一种基于转底炉法处理钢铁冶金尘泥的方法,采用本发明第一方面所述的基于转底炉法处理钢铁冶金尘泥的生产线,所述基于转底炉法处理钢铁冶金尘泥的方法包括以下步骤:
21.s1,将钢铁冶金尘泥、粘结剂和水加入到强力混料机中混合均匀后,并压制成球,得到冶金尘泥球团;所述粘结剂包括硅酸季氨、聚丙烯酸钠、纤维素钠以及膨润土;
22.s2,所述冶金尘泥球团进入到螺旋溜槽内,在转底炉进料口出来的烟气的作用下
脱除部分水分,再经振动布料器进入转底炉中进行还原,得到金属化球团和含锌烟气;
23.s3,所述含锌烟气经换热、除尘后得到含锌粉尘。
24.优选地,所述步骤s1中:
25.所述钢铁冶金尘泥包括高炉除尘灰、转炉og泥、电炉除尘灰、瓦斯泥以及焦化cdq粉中的一种或多种;和/或
26.所述粘结剂中,所述硅酸季氨与所述膨润土按照0.5:1的重量比混合作为第一粘结剂,所述聚丙烯酸钠与所述膨润土按照0.5:1的重量比混合作为第二粘结剂,所述纤维素钠与所述膨润土按照0.5:1的重量比混合作为第三粘结剂;和/或
27.所述粘结剂通过气力输送至所述强力混合机中。
28.优选地,所述钢铁冶金尘泥、第一粘结剂、第二粘结剂、第三粘结剂和水的重量分数比为100:0.4~0.7:0.1~0.3:0.2~0.3:8~10。
29.优选地,所述步骤s1中:
30.所述压制成球过程中,压球机的线压力为4t/cm~7t/cm,转速为7~11转/min;和/或
31.所述冶金尘泥球团的落下强度为18~25次/1m,抗压强度为100~140n,水分含量为8.5~10wt%,返料比≤25%。
32.优选地,所述步骤s2中:
33.所述冶金尘泥球团在所述螺旋溜槽上的流动时间为5~8min;和/或
34.所述冶金尘泥球团在进入所述转底炉前,水分含量降低至5%以下;和/或
35.所述还原过程中,所述冶金尘泥球团依次经过所述转底炉的预热区、高温区和出料区;所述转底炉的高温区内设有多个空气烧嘴和燃气烧嘴。
36.优选地,所述转底炉的预热区温度为1150~1220℃,所述高温区的温度为1260~1280℃,所述出料区的温度为900~1000℃。
37.优选地,所述步骤s2中获得的金属化球团的金属化率>75%,脱锌率>85%,抗压强度为1500~2000n。
38.本发明所提供的一种基于转底炉法处理钢铁冶金尘泥的方法及生产线,还具有以下几点有益效果:
39.1、本发明的基于转底炉法处理钢铁冶金尘泥的方法及生产线,采用硅酸季氨、聚丙烯酸钠、纤维素钠以及膨润土作为粘结剂,并将粘结剂通过强力混料机的加料口加入,确保粘结剂均匀分散在混合料中,从而减少粘结剂得用量,提高球团的成球率和强度,同时有效减少球团在转底炉还原过程中的粉化现象;
40.2、本发明采用采用硅酸季氨、聚丙烯酸钠、纤维素钠以及膨润土作为粘结剂,将转底炉处置钢铁冶金尘泥粘结剂的添加量由6~8%降低至1.5%以内,且粘结剂原料都是无毒无害的,最终的得到的球团具有强度高,返料少的优点;
41.3、本发明基于转底炉法处理钢铁冶金尘泥的方法及生产线,通过在强力混料机上部设置3个粘结剂加料口,气力输送的粘结剂通过粘结剂加料口加入到强力混料机内,确保粘结剂能均匀分散到混合料中,发挥最大的粘结剂作用,减少水的加入量(仅需要8~10.5%);
42.4、本发明基于转底炉法处理钢铁冶金尘泥的方法及生产线,在转底炉的料口设置
螺旋溜槽用于将压球机压制的球团送入转底炉中,一方面利用螺旋溜槽延长球团进入转底炉的时间,另一方面利用转底炉进料口的热烟气烘干球团中的一部分水分,避免球团在在转底炉内爆裂的弊端,同时可省去转底炉烘干系统,螺旋溜槽可以将冶金尘泥球团整球和粉末分开,提升入炉冶金尘泥球团质量,减少粉末入炉量可以有效的控制降低粉化率减轻炉底板结等不利的生产因素;
43.5、本发明基于转底炉法处理钢铁冶金尘泥的方法及生产线,所采用的粘结剂中的硅酸根和氧化钙成分可以起到高温固结球团的作用,将转底炉内的粉化率降由30%降低到10%以内。
附图说明
44.通过阅读参照以下附图对非限制性实施例所作的详细描述,本发明的其它特征、目的和优点将会变得更明显:
45.图1为本发明基于转底炉法处理钢铁冶金尘泥的生产线的结构示意图;
46.图2为本发明的转底炉的结构示意图;
47.图3为本发明的强混机的结构示意图;
48.图4是本发明的螺旋溜槽的结构示意图。
具体实施方式
49.为了能更好地理解本发明的上述技术方案,下面结合实施例进一步说明本发明的技术方案。
50.结合图1所示,本发明所提供的一种基于转底炉法处理钢铁冶金尘泥的生产线,包括强力混料机1、压球机2、转底炉4、余热锅炉5、除尘装置6;结合图3所示,强力混料机1用于钢铁冶金尘泥、粘结剂和水混合均匀,该强力混料机1上设有冶金尘泥加料口15、第一粘结剂加料口11、第二粘结剂加料口12、第三粘结剂加料口13。压球机2用于将强力混料机1混合后的物料压制成球;该压球机2与强力混料机1的出料口之间通过皮带连接。结合图2所示,转底炉4用于将压球机2制备的冶金尘泥球团进行还原,该转底炉4的转动炉底依次分为预热区a、高温区b和出料区c,预热区a、高温区b和出料区c之间均设有隔墙;高温区b设有多个空气烧嘴41和燃气烧嘴42;该转底炉4的进料口通过螺旋溜槽3(参见图4所示)与压球机2连通。余热锅炉5用于回收转底炉4内出来的含锌烟气内的热量;余热锅炉5的烟气进口与转底炉4的烟气出口连通。除尘装置6用于将余热锅炉5烟气出口出来的含锌烟气进行除尘处理;该除尘装置6的烟气进口与余热锅炉5的烟气出口连通。
51.结合图3所示,强力混料机1上还设有驱动机构14和可转动的混料机构;其中混料机构包括设于混料机1顶部的转轴以及设于转轴上的多个耙齿;转轴上的多个耙齿用于将冶金尘泥、粘结剂与水打散,充分混合;驱动机构14的输出端与混料机构的转轴连接,带动混料机构转动;在具体的实施例中,驱动机构14可采用电机等。该强力混料机1为连续进料和出料的装置。
52.结合图4所示,螺旋溜槽3包括固定支架31以及设于固定支架31上的溜槽本体32;溜槽本体32顶部设有加料口33,底部设有球团出料口34和粉末出料口35;溜槽本体32的出料口34与转底炉4的进料口连通。溜槽本体32由多个螺旋结构通过螺栓连接到一起,可通过
调整单个螺旋结构的角度控制进料速度和进料量,每个螺旋结构角度的调整范围在30~45
°
之间,冶金尘泥球团从进入螺旋溜槽3加料口33自然从高往下旋流,在螺旋溜槽3的斜面流速中产生一种惯性的离心力,通过旋流的重力和离心力的作用,将球团中的整球和球团粉末分开,球团由于比重较大通过球团出料口34进入转底炉,球团粉末比重轻,从粉末出料口35出去返回强力混料机1内重新混合;通过上述过程可控制冶金尘泥球团在螺旋溜槽3内的流动速度,进而使得冶金尘泥球团在转底炉4进料口上来的烟气的作用下,在进入转底炉4前将水分降低至5wt%以下。在具体的实施例中,转底炉4的进料口设有振动布料器,用于将螺旋溜槽本体32出料口34出来的冶金尘泥球团均匀地布在转底炉4转动炉底的预热区内。
53.采用上述的基于转底炉法处理钢铁冶金尘泥的生产线对冶金尘泥进行处理,包括以下步骤:
54.s1,将钢铁冶金尘泥、粘结剂和水加入到强力混料机中混合均匀后,并压制成球,得到冶金尘泥球团;粘结剂包括硅酸季氨、聚丙烯酸钠、纤维素钠以及膨润土;
55.具体过程为:将钢铁冶金尘泥、粘结剂和水充分混合后得到混合料,混合料中铁含量为40~45wt%,锌含量为1.5~3wt%;然后将混合料转移至压球机中压制成球,得到冶金尘泥球团。粘结剂包括硅酸季氨、聚丙烯酸钠、纤维素钠以及膨润土,其中膨润土既可以在压球工艺中起到粘结作用,同时是其他3种原料的输送载体,因此在混合前需要将膨润土分别与其他3种原料提前混合,即先制备第一粘结剂(硅酸季氨-膨润土)、第二粘结剂(聚丙烯酸钠-膨润土)、第三粘结剂(纤维素钠-膨润土),然后分别加入到强力混合机的第一粘结剂料仓、第二粘结剂料仓、第三粘结剂料仓内;其中第一粘结剂由硅酸季氨与膨润土按照0.5:1的重量比混合而成,第二粘结剂由聚丙烯酸钠与膨润土按照0.5:1的重量比混合而成,第三粘结剂由纤维素钠与膨润土按照0.5:1的重量比混合而成;为确保每种粘结剂的原料充分分散在混合料中,将第一粘结剂、第二粘结剂、第三粘结剂分别通过强力混料机顶部设置的第一粘结剂加料口、第二粘结剂加料口、第三粘结剂加料口;再采用气力输送至强力混合机中,其中钢铁冶金尘泥包括高炉除尘灰、转炉og泥、电炉除尘灰、瓦斯泥以及焦化cdq粉中的一种或多种。钢铁冶金尘泥、第一粘结剂、第二粘结剂、第三粘结剂和水的重量分数比为100:0.4~0.7:0.1~0.3:0.2~0.3:8~10;由于强力混料机内有可以旋转的混料机构,该混料机构的转轴上带有打散混匀耙齿,通过驱动机构驱动旋转,且该强力混料机为连续进料和出料的装置,其混合时间设置为2~5min。从强力混料机中出来的混合料通过压球机进行压球,其中压球机的线压力可设置为4t/cm~7t/cm,压球机的转速为7~11转/min。由压球机制得的冶金尘泥球团,其湿球的落下强度为18~24次/1m,冶金尘泥球团的抗压强度为100~140n,水分含量为8.5~10wt%,返料比≤25%。
56.在上述的粘结剂原料中,硅酸季氨、聚丙烯酸钠、纤维素钠都是具有较强粘性的物料,可以起到将冶金尘泥颗粒粘结到一起的作用,膨润土具有提高成球率和抗压强度以及烧结固化作用;粘结剂原料硅酸季氨、聚丙烯酸钠、纤维素钠粘度较高,如果直接添加到强力混料机里会造成粘堵,采用和膨润土混合后气力输送的方式既实现了膨润土的协同添加,又避免了管道堵塞。
57.s2,冶金尘泥球团进入到螺旋溜槽内,在转底炉进料口出来的烟气的作用下脱除部分水分,再经振动布料器进入转底炉中进行还原,得到金属化球团和含锌烟气;
58.具体过程为:步骤s1中制备的冶金尘泥球团经皮带运输至螺旋溜槽,从螺旋溜槽顶部的进料口进入到螺旋溜槽内,转底炉进料口出来的烟气经螺旋溜槽的出料口进入到螺旋溜槽内,冶金尘泥球团在烟气的作用下部分水分蒸发,在进入转底炉前冶金尘泥球团的水分含量降低至5wt%以下,冶金尘泥球团经螺旋溜槽出料口进入到转底炉内,然后经振动布料器均匀布料至转底炉上进行还原,在转底炉内,冶金尘泥球团依次经转底炉的预热区、高温区和出料区,最终获得金属化球团和含锌烟气,其中出料区排除的金属化球团的粉化率<10%,且该方法不影响转底炉的金属化率和脱锌率,球团金属化率>75%,脱锌率>85%,抗压强度1500n~2000n,可以作为炼铁或者炼钢的优质原料;含锌烟气则从转底炉的烟气出口排出。
59.在上述过程中,由于冶金尘泥球团中水分含量为8.5~10wt%,为了避免球团中的水分在转底炉内由于高温急剧挥发产生较大的蒸汽压造成球团爆裂,在湿球进入转底炉进料口的上方设置螺旋溜槽,以延长球团进入转底炉的时间,利用从转底炉进料口出来的热烟气将球团的水分烘干一部分,其中冶金尘泥球团由螺旋溜槽顶部的进料口到转底炉的进料口之间的流动时间控制在5~8min,螺旋溜槽可通过底部的控制装置调整溜槽的角度,控制球团的流动速度,使得最终冶金尘泥求软进入到转底炉前水分含量降低至5wt%以下。
60.冶金尘泥球团经振动布料器布入至转递路内进行还原时,将转递路的预热区温度设置为1150~1220℃,高温区的温度设置为1260~1280℃;出料区的温度设置为900~1000℃;在还原过程中,由于膨润土和硅酸季氨中含有氧化钙和硅酸根离子,在高温条件下,氧化钙在高温下与冶金尘氧化铝和氧化镁以及二氧化硅发生固结反应生成钙镁石榴石等复杂高分子物相,硅酸根离子和球团中没有还原的铁反应生成半液相的硅酸铁,起到粘连球团颗粒的作用,固化反应和硅酸铁的生产反应可极大降低了球团粉化率。
61.s3,含锌烟气经换热、除尘后得到含锌粉尘。
62.具体过程为:在步骤s2中,冶金尘泥球团的锌元素在转底炉中挥发进入收尘系统以含锌烟气的形式被收集,含锌烟气经余热锅炉换热、除尘装置除尘后烟气达标后排放,含锌粉尘中的锌主要以氧化锌的形式存在,可作为其他利用原料。
63.下面结合具体的例子对本发明的一种基于转底炉法处理钢铁冶金尘泥的方法及生产线进一步介绍;
64.实施例1
65.本实施例中钢铁冶金尘泥采用上述的基于转底炉法处理钢铁冶金尘泥的方法进行处理:
66.钢铁冶金尘泥混合料铁含量42wt%,锌含量2wt%,硅酸季氨、聚丙烯酸钠、纤维素钠分别与膨润土按照重量份0.5:1的比例提前混合均匀,钢铁冶金尘泥与硅酸季氨-膨润土、聚丙烯酸钠-膨润土、纤维素钠-膨润土以及水的重量份数比例为100:0.4:0.1:0.2:10的比例在强力混料机混合均匀,混料时间为5min,混合料送入压球机压球,压球机线压力设置为7t/cm,压球机转速为10.5转/min,压球机出来的冶金尘泥球团的落下强度为18次/1m,抗压强度为100n,水分含量为10wt%,返料比为25%,冶金尘泥球团通过皮带送到转底炉上的螺旋溜槽,从螺旋溜槽顶部流动到底部8min,冶金尘泥球团由溜槽进到振动布料器,冶金尘泥球团水分降低至4.7wt%,冶金尘泥球团通过振动布料器步入转底炉预热区,预热区温度设置为预热区(1180℃),高温区(1260℃),和出料区(900℃),转底炉转一圈25min,由转
底炉排出的金属化球团抗压强度为1600n,金属化率为76.5%,脱锌率为86.2%,粉化率为9.2%,球团作为原料送去转炉或者高炉进行冶炼。
67.实施例2
68.本实施例中钢铁冶金尘泥采用上述的基于转底炉法处理钢铁冶金尘泥的方法进行处理:
69.钢铁冶金尘泥混合料铁含量42wt%,锌含量2wt%,硅酸季氨、聚丙烯酸钠、纤维素钠分别与膨润土按照重量份0.5:1的比例提前混合均匀,钢铁冶金尘泥与硅酸季氨-膨润土、聚丙烯酸钠-膨润土、纤维素钠-膨润土以及水的重量份数比例为100:0.55:0.2:0.25:9.5的比例在强力混料机混合均匀,混料时间为3.5min,混合料送入压球机压球,压球机线压力设置为5.5t/cm,压球机转速为9转/min,压球机出来的冶金尘泥球团的落下强度为23次/1m,抗压强度为120n,水分含量为9.2wt%,返料比为24%,冶金尘泥球团通过皮带送到转底炉上的螺旋溜槽,从螺旋溜槽顶部流动到底部7min,冶金尘泥球团由溜槽进到振动布料器,冶金尘泥球团水分降低至4.8wt%,冶金尘泥球团通过振动布料器步入转底炉预热区,预热区温度设置为预热区(1200℃),高温区(1270℃),和出料区(950℃),转底炉转一圈25min,由转底炉排出的金属化球团抗压强度为1800n,金属化率为78%,脱锌率为89%,粉化率为8.5%,球团作为原料送去转炉或者高炉进行冶炼。
70.实施例3
71.本实施例中钢铁冶金尘泥采用上述的基于转底炉法处理钢铁冶金尘泥的方法进行处理:
72.钢铁冶金尘泥混合料铁含量43wt%,锌含量2wt%,硅酸季氨、聚丙烯酸钠、纤维素钠分别与膨润土按照重量份0.5:1的比例提前混合均匀,钢铁冶金尘泥与硅酸季氨-膨润土、聚丙烯酸钠-膨润土、纤维素钠-膨润土以及水的重量份数比例为100:0.7:0.3:0.3:8的比例在强力混料机混合均匀,混料时间为2.5min,混合料送入压球机压球,压球机线压力设置为4.5t/cm,压球机转速为7.5转/min,压球机出来的冶金尘泥球团的落下强度为25次/1m,抗压强度为140n,水分含量为8.1wt%,返料比为22.5%,冶金尘泥球团通过皮带送到转底炉上的螺旋溜槽,从螺旋溜槽顶部流动到底部5min,冶金尘泥球团由溜槽进到振动布料器,冶金尘泥球团水分降低至4.1wt%,冶金尘泥球团通过振动布料器步入转底炉预热区,预热区温度设置为预热区(1220℃),高温区(1280℃),和出料区(1000℃),转底炉转一圈25min,由转底炉排出的金属化球团抗压强度为2000n,金属化率为80%,脱锌率为90.2%,粉化率为7%,球团作为原料送去转炉或者高炉进行冶炼。
73.综上,本发明的基于转底炉法处理钢铁冶金尘泥的方法机生产线,将转底炉处置冶金尘泥粘结剂添加量由6~8%降低至1.3%以内,粘结剂原料都无毒无害,采用本发明的粘结剂压球得到球团具有强度高,返料少的优点。通过在强力混料机上部设置3个粘结剂加料口,气力输送的粘结剂通过该添加口加入均匀的添加到混料机内,确保粘结剂均匀的分散到混合料中,发挥最大的粘结剂作用,减少水加入量和进料口设置溜槽的方法和系统可以省去转底炉专用烘干系统,缩短流程和节约能耗。本发明所用的粘结剂中的硅酸根和氧化钙成分可以起到高温固结球团的作用,将炉子内的粉化率降由30%降低到10%以内。
74.本技术领域中的普通技术人员应当认识到,以上的实施例仅是用来说明本发明,而并非用作为对本发明的限定,只要在本发明的实质精神范围内,对以上所述实施例的变
化、变型都将落在本发明的权利要求书范围内。
再多了解一些
本文用于企业家、创业者技术爱好者查询,结果仅供参考。