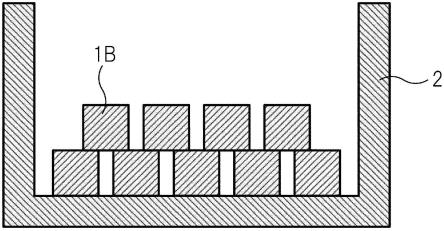
1.本发明涉及金属氮化物的制造方法。
背景技术:
2.氮化硅、氮化铝和氮化硼等金属氮化物由于其烧结体通常具有高导热性、高绝缘性、高强度等优异的特性,因此作为各种工业材料的陶瓷原料备受瞩目。在氮化硅粉末中添加各种烧结助剂在高温下烧结而成的氮化硅烧结体在各种陶瓷烧结体中具有轻、机械强度强、耐化学药品性高、电绝缘性高等特征,被用作滚珠轴承等耐磨损用部件、高温构造用部件。另外,由于还可以通过设计助剂的种类、烧结条件来提高导热性,因此它也被用作薄而强度高的散热用基板材料。
3.作为氮化硅粉末的制造方法,作为现有技术,已知有通过利用自燃烧法(self-propagating high temperature synthesis,shs法)的直接氮化法来合成氮化硅的方法(例如参照专利文献1,实施例3和4)。自燃烧法是将硅粉末用作原料,在氮气气氛下灼热引燃原料粉末的一部分,通过原料化合物的自发热进行合成反应的方法。在该专利文献1的实施例3中,虽然没有记载起始原料的纯度和详细的制造条件,但记载了将填充有平均粒径20μm的硅粉末的碳制坩埚放置在反应容器内,在5个大气压的氮气气氛中,以20w的输出功率向硅粉末照射yag激光而将其引燃后,停止激光照射,然后通过自放热进行燃烧合成反应,得到微细粉末的产物。另外,在专利文献1的实施例4中,虽然仍然没有记载起始原料的纯度和详细的制造条件,但记载了将填充有平均粒径5μm的硅粉末的碳制坩埚放置在反应容器内,在30个大气压的氮气气氛中,以100w的的输出功率向硅粉末照射yag激光而将其引燃后,停止激光照射,然后通过自放热进行燃烧合成反应,得到微细粉末的产物。
4.上述的通过利用自发热的直接氮化法制造氮化硅的方法虽然在热能方面极为有利,但在专利文献1的方法中,氮化反应的压力过高,暴发性地连锁发生氮化反应,生成的氮化硅的微粒热粘,结果,得到致密烧结体所需的微小粒子的生成减少。因此,对于通过该方法得到的氮化硅粉末来说,难以得到致密的烧结体,而且烧结时的收缩率大的问题也没有得到改善。
5.另外,在如上所述通过引燃硅粉末的自发热来实施燃烧合成反应的情况下,原料的硅粉末一下子被加热而进行反应,因此在反应时可能发生硅的熔化、热粘。因此,在专利文献2中提出了如下方案:在原料的硅粉末中以10质量%以上的量混合作为稀释剂的氮化硅粉末,将由该硅粉末和稀释剂的混合物构成的粉体层(原料粉末层)的体积密度调整为0.3~0.65g/cm3来进行燃烧合成。通过使用这样的稀释剂,燃烧反应温和地进行,防止硅的熔化、热粘,进而通过将原料粉末层的体积密度调整为一定的低水平,防止得到的块状氮化硅变硬和凝聚,容易粉碎。现有技术文献
6.专利文献
专利文献1:日本特开2000-264608号公报专利文献2:wo2018/110565号公报
技术实现要素:
发明要解决的课题
7.然而,在以往的氮化硅粉末的制造方法中,在向反应容器中填充原料粉末时,有时产生粉尘飞扬而使作业环境变差。另外,在将反应容器设置在反应装置中后,在将反应装置内从空气置换为氮气时,通过反应装置内的压力变化而促进原料粉末的填充,随之相伴地有时会在所填充的原料粉末中发生龟裂。当所填充的原料粉末发生龟裂时,氮化燃烧热的传递变得不稳定,在该龟裂部位有可能残留未反应的原料。当在龟裂部位残留未反应的原料时,在通过刷洗等除去该未反应的原料时,生成的金属氮化物也被大量地除去,结果,金属氮化物的回收率降低。
8.因此,本发明的目的在于制造一种金属氮化物,其能够抑制粉尘(粉尘飞扬)发生,并改善金属氮化物的回收率。解决课题的手段
9.本发明人对通过利用自燃烧的直接氮化法(以下,也称为燃烧合成法)制造氮化硅粉末的方法进行了大量实验和研究,结果发现了以下新见解:通过使用将原料粉末成型而得到的成型体来制造金属氮化物,能够抑制粉尘(即粉尘飞扬)的发生,同时能够抑制原料粉末的龟裂并改善金属氮化物的回收率,从而完成了本发明。予以说明,如上述专利文献2等记载的那样,通常是将原料粉末的体积密度减小到一定程度来进行燃烧合成。根据这样的技术常识可知,如果将原料粉末成型来提高体积密度,则存在以下担忧:燃烧合成法产生的燃烧热难以传递,所生成的块状氮化硅无法粉碎等。但出乎预料的是,通过使用由本发明原料粉末构成的特定成型体,能够通过燃烧合成法来制造金属氮化物,并且由于使用了该成型体,因此能够抑制粉尘(粉尘飞扬)的产生。
10.即,根据本发明,提供:一种金属氮化物的制造方法,其是在氮气气氛下,引燃反应容器中收容的含有金属粉末的原料粉末,使所述金属粉末的氮化燃烧热传递到所述收容的原料粉末整体,由此合成所述金属的氮化物的方法,其特征在于,将所述原料粉末制成空隙率为40~70%的成型体而收容在所述反应容器中。
11.在本发明的制造方法中,可适宜采用以下方式。(1)上述原料粉末相对于上述金属粉末100质量份,含有0~80质量份的金属氮化物粉末。(2)使多个上述原料粉末的成型体相互接触并收容在上述反应容器中。(3)在上述反应容器中收容的上述原料粉末的成型体的上表面上紧贴隔热层,上述隔热层具有氮透过性且由对氮化反应惰性的材质构成。(4)上述金属为硅。发明效果
12.根据本发明,可提供一种金属氮化物的制造方法,其能够抑制粉尘飞扬的发生,且
改善金属氮化物的回收率。
附图说明
13.[图1]图1是表示反应容器内的成型体的配置的一例的示意图。[图2]图2是表示反应容器内的成型体的配置的一例的示意图。[图3]图3(a)~(c)是分别表示反应容器内的成型体的配置的一例的示意图。[图4]图4是表示反应容器内的成型体的配置的一例的示意图。[图5]图5是表示在成型体的上方形成的隔热层的一例的示意图。[图6]图6是表示在成型体的上方、下方和侧方形成的隔热层的一例的示意图。
具体实施方式
[0014]
本发明的金属氮化物的制造方法是如下所述的金属氮化物的制造方法:在氮气气氛下,引燃反应容器中收容的含有金属粉末的原料粉末,使所述金属粉末的氮化燃烧热传递到所述收容的原料粉末整体,由此合成所述金属的氮化物。并且,本发明的金属氮化物的制造方法的特征在于,将原料粉末制成空隙率为40~70%的成型体而收容在反应容器中。由此,能够抑制粉尘飞扬的发生,并改善金属氮化物的回收率。以下,详细说明该制造方法。
[0015]
(原料粉末)本发明中,原料粉末含有金属粉末。作为金属粉末,例如可举出硅粉末、铝粉末、硼粉末等。予以说明,硅和硼为非金属元素,但有时将硅单质称为金属硅,将硼单质称为金属硼,因此在本说明书中,硅粉末和硼粉末也包含在金属粉末中。本发明中特别优选硅粉末。
[0016]
另外,从得到空隙率为40~70%的成型体的方面考虑,原料粉末中含有的上述金属粉末的平均粒径d
50
优选在1~10μm的范围内。予以说明,平均粒子d
50
是指通过激光衍射散射法测定的粒度分布中的累积体积为50%时的粒径。
[0017]
另外,与上述相关地,用作原料粉末的金属粉末优选为高纯度的金属粉末。例如,当金属粉末为硅粉末时,al、fe的含量分别优选为200ppm以下。另外,当金属粉末为铝粉末时,si、fe的含量分别优选为200ppm以下。进而,当金属粉末为硼粉末时,fe的含量优选为200ppm以下。当存在这样的金属元素时,可能存在以下情况:得到的金属氮化物的烧结性降低,而且得到的烧结体的强度等特性降低。基于同样的理由,w、mo等高熔点金属的含量也适宜为200ppm以下。
[0018]
金属粉末优选预先将其粉末表面适度氧化。即,这是因为金属粉末表面形成的氧化膜是适当控制燃烧合成反应进行的重要因素。作为适度氧化表面的方法,可简单地采用在空气中粉碎至上述粒径范围的方法。例如,适宜采用使用空气的气流粉碎机等。上述金属粉末的氧化程度可以在不阻碍本发明燃烧合成反应的范围内适当确定,但相对于金属粉末的重量,优选以0.1~1质量%左右的量含有氧。当金属粉末中的氧量低于上述范围时,氮化反应时燃烧温度有过度升高的倾向,另外,当氧量超过该范围时,存在氮化反应被抑制的倾向,有时发生引燃不良或未反应金属残留等的问题。
[0019]
本发明中,用作原料粉末的上述那样的金属粉末可以是以何任意方法得到的金属粉末,但优选将纯度和粒径调整在上述规定的范围内。例如,当金属粉末为硅粉末时,一般来说,将半导体多晶硅棒破碎制造金属块(nugget)的过程中产生的微粉回收利用是经济
的。另外,也可以将市售的工业用原料粉碎后使用。
[0020]
原料粉末可以含有稀释剂。金属粉末与氮的反应为放热反应,表面反应为限速(rate-determining)反应,因此金属粉末的量越多,越难以控制原料粉末的温度。但是,通过使原料粉末含有稀释剂,原料粉末中的金属粉末的含量减少,原料粉末的放热也减少。而且,原料粉末的温度控制变得容易。作为上述稀释剂,优选为金属氮化物粉末,其中,在金属粉末反应而生成金属氮化物后,为了不从生成的金属氮化物中除去原料粉末中含有的稀释剂,用作稀释剂的金属氮化物粉末优选为与原料的金属粉末相同的金属元素的氮化物粉末。例如,当金属粉末为硅粉末时,用作稀释剂的金属氮化物粉末优选为氮化硅,当金属粉末为铝粉末时,用作稀释剂的金属氮化物粉末优选为氮化铝,当金属粉末为硼粉末时,用作稀释剂的金属氮化物粉末优选为氮化硼。作为这些稀释剂,例如可以使用通过本发明的金属氮化物的制造方法制造的金属氮化物。
[0021]
原料粉末优选含有相对于金属粉末100质量份为0~80质量份的金属氮化物。即,原料粉末可以含有金属氮化物,也可以不含金属氮化物。而且,当原料粉末含有金属氮化物时,金属氮化物的含量相对于金属粉末100质量份,优选为80质量份以下。当金属氮化物的含量相对于金属粉末100质量份为80质量份以下时,能够容易地在氮气气氛下引燃成型体,并且能够容易地使金属的氮化燃烧热传递到反应容器中收容的成型体整体。从这样的观点考虑,相对于金属粉末100质量份,金属氮化物的含量更优选为50质量份以下,进一步优选为30质量份以下。另外,从原料粉末的温度控制的观点考虑,相对于金属粉末100质量份,金属氮化物的含量更优选为1质量份以上,进一步优选为5质量份以上。
[0022]
在不阻碍本发明效果的范围内,原料粉末中可以含有金属粉末以及根据需要使用的稀释剂以外的其他成分。作为其他成分,例如可举出:氯化钠、氯化铵等氯化物,氧化钙、氧化钇、氧化镁等氧化物等。以原料粉末的总量为基准,其他成分优选为10质量%以下,更优选为5质量%以下,进一步优选为1质量%以下,更进一步优选为0质量%。
[0023]
(成型体)成型体的空隙率为40~70%。当成型体的空隙率小于40%时,有时氮气不能充分地透过成型体中。在这种情况下,燃烧反应不能充分进行,在反应过程中熄火等而导致未反应物变多,收率降低。另外,当成型体的空隙率大于70%时,有时无法确保在操作成型体时所需的成型体的强度。从这些观点考虑,成型体的空隙率优选为48~68%,更优选为50~65%。予以说明,以往认为当将原料粉末成型而制成成型体时,燃烧反应不能充分进行。但是,本发明人等深入研究的结果发现,通过将成型体的空隙率设为40%以上,即使在成型体的情况下,燃烧反应也能充分进行。予以说明,成型体的空隙率可以通过调节原料粉末的平均粒径、成型时的成型压力等来控制。
[0024]
另外,当在反应容器内收容多个成型体时,将该多个成型体的空隙率的平均值作为本发明的成型体的空隙率。在此,多个成型体的空隙率的平均值是指由各成型体的空隙率和各成型体的重量计算出的加权平均值。因此,当使用多个成型体时,一部分成型体的空隙率可以小于40%或大于70%,但优选多个成型体中的每个成型体的空隙率均为40~70%,更优选为48~68%,进一步优选为50~65%。
[0025]
成型体的空隙率可以由不存在空隙时的成型体的密度(成型体的理论密度:d2)和成型体的密度的实测值(成型体的密度:d1)如下算出,详细而言,通过实施例中记载的方法进行测定。成型体的理论密度可以由构成成型体的各原料的密度和成分比求出。空隙率(%)=(1-d1/d2)
×
100
[0026]
成型体的体积密度优选为0.85~1.30g/cm3。另外,当成型体的体积密度为0.85g/cm3以上时,能够确保在操作成型体时所需的成型体的强度。另外,当成型体的体积密度为1.30g/cm3以下时,能够使氮气充分地透过成型体中。由此能够使氮化燃烧反应充分地进行。从这样的观点考虑,成型体的体积密度更优选为0.90~1.20g/cm3,进一步优选为0.95~1.15g/cm3。
[0027]
成型体的形状没有特别限定。成型体的形状例如可举出:板状、长方体、立方体、圆柱形、棱柱形、球形、椭圆球形等。反应容器中收容的成型体可以是单个成型体,也可以是多个成型体。当反应容器中收容多个成型体时,成型体的形状优选为成型体彼此能够接触的形状,优选为成型体彼此能够面接触的形状。由此,能够在成型体之间容易地传递氮化燃烧热。从这样的观点考虑,成型体的形状优选为圆柱形、棱柱形等,其中,考虑到成型的容易性等,更优选圆柱形。
[0028]
原料粉末的成型方法只要是能够制作原料粉末的成型体,就没有特别限定。但是,为了抑制氧杂质混入原料粉末中,优选通过干式成型将原料粉末成型。例如,可以通过单轴压制成型法将原料粉末成型。在这种情况下,例如可以使用自动干式压制成型机将原料粉末成型。另外,可以通过压块、压片等压缩造粒将原料粉末成型。
[0029]
(成型体在反应容器中的收容)代替将原料粉末直接填充到耐热性容器中的方式,通过将原料粉末制成成型体而收容在反应容器中,能够抑制原料粉末的飞散。由此,能够抑制产生粉尘飞扬而使作业环境变差。作为反应容器,例如可举出石墨制的反应容器。另外,由于成型体的密度几乎不会因将反应装置内从空气置换为氮气时的反应装置内的压力的变化而改变,因此能够抑制原料粉末的龟裂的产生。将成型体收容在反应容器内的方法只要是能够将成型体以一定程度的密度收容在反应容器内,就没有特别限定。例如,如图1所示,可以将一片板状的成型体1a收容在反应容器2中。另外,如图2所示,可以以将多个圆柱形成型体1b与左右方向相邻的成型体1b不接触而堆积的状态将成型体1b收容在反应容器2中。进而,如图3(a)所示,收容在反应容器中的成型体1b可以是左右方向相邻的成型体1b相互接触状态下的平装(平放)。另外,多个圆柱形的成型体1b的堆积方式如图3(b)所示,可以是使成型体1b在与左右方向相邻的成型体1b接触的同时以仅与1个成型体1b重叠的方式堆积在成型体1b的上方。进而,如图3(c)所示,也可以是使成型体1b在与左右方向相邻的成型体1b接触的同时以与2个成型体1b重叠的方式堆积在成型体1b的上方。另外,如图4所示,也可以以填充多个球形成型体1c的状态将成型体1c收容在反应容器2中。
[0030]
在将多个原料粉末的成型体收容于耐热性容器中时,对于各个成型体,该成型体与最旁边位置的另一成型体之间的距离优选为10mm以内,更优选为5mm以内,进一步优选使多个成型体相互接触地收容在反应容器中。由此,氮化燃烧热能够容易地在相邻的成型体之间传递。当相邻的2个成型体接触时,从更可靠地在成型体之间传递氮化燃烧热的观点考
虑,相邻的2个成型体优选点接触,更优选线接触,进一步优选面接触。另外,成型体可以在与相邻的成型体面接触的同时,与相邻的另一成型体面接触。进而,当相邻的2个成型体面接触时,相邻的2个成型体之间的接触面积(成型体间的接触面积)优选为1cm2以上,更优选为2cm2以上。予以说明,上述相邻的2个成型体间的接触面积为平均值,可以由成型体与成型体接触的部位总量以及成型体与成型体接触的总面积来计算。
[0031]
如图5所示,在收容于反应容器2的原料粉末的成型体1b的上表面上紧贴地形成隔热层3,所述隔热层3具有氮透过性且由对氮化反应惰性的材质构成。由此,能够抑制氮化燃烧热从成型体上方扩散,并且能够抑制在收容于反应容器的成型体中的上方的成型体的温度降低至成型体与氮气发生不能充分反应的温度。而且,能够抑制未反应物的残留。
[0032]
隔热层3例如可以由与成型体中的金属粉末相同的金属元素的氮化物的粉末形成。例如,当成型体中的金属粉末为硅粉末时,隔热层优选为氮化硅的粉末。由氮化硅的粉末形成的隔热层具有氮透过性,且对于氮化反应为惰性的。另外,作为隔热层,可以使用石墨制纤维、多孔质陶瓷板等。予以说明,当隔热层为金属氮化物的粉末时,虽然产生一些粉尘飞扬,但与不将原料粉末成型而填充到反应容器中的情况相比,能够抑制粉尘(粉尘飞扬)的产生。另外,如图6所示,具有氮透过性且由对氮化反应惰性的材质构成的隔热层3不仅可以形成在成型体1b的上方,也可以形成在成型体1b的下方和侧方。由此,能够防止反应容器的劣化,进而能够抑制成型体与反应容器之间的反应。例如,当成型体与反应容器接触时,在反应容器为石墨制反应容器的情况下,有时会在反应容器与成型体的接触面上形成金属碳化物,但当为如上述图6那样的方式时,能够防止金属碳化物的形成。
[0033]
(金属氮化物的合成)在本发明的氮化物的制造方法中,在氮气气氛下,引燃反应容器中收容的含有金属粉末的原料粉末,使金属粉末的氮化燃烧热传递到所收容的原料粉末整体,由此合成金属的氮化物。在燃烧合成反应时,可以向成为引燃点的部分预先配置含有ti、al等粉末的引燃剂。例如,挖出成型体的一部分而制作凹陷。在该凹陷中可以配置引燃剂。配置于成型体中的引燃剂的量应该是不会影响所得金属氮化物的烧结性的程度的少量。在配置引燃剂时,可以配置在成型体的端部、中央部或任意位置,可以配置在单个或多个部位上。
[0034]
将成型体收容于反应容器中后,对反应容器内进行氮气置换,在氮气气氛下引燃成型体。一般来说,反应容器设置在具有点火装置和气体供给/排出机构的耐压性密闭式反应器内,在对耐热性反应器内减压而除去空气后,供给氮气进行氮气置换。
[0035]
本发明中,反应既可以在常压下进行,也可以在加压下进行,优选在加压下进行。特别是在进行作为金属氮化物得到氮化硅的反应时,从容易进行氮化反应的观点考虑,优选在加压下进行。具体地,优选在常压~1mpa的压力下进行,该压力通过供给到所述密闭式反应器的氮气压力来实现。当密闭式反应器的压力小于上述范围时,存在在反应过程中熄火等而导致未反应物变多、收率下降的倾向。另外,当密闭式反应器的压力大于上述范围时,存在以下倾向:反应温度过度上升而导致生成粗大的硅的块状物,使最终得到的氮化硅粉末含有大量难以粉碎的粗大颗粒,难以确保适当的粒度分布。
[0036]
本发明中,优选如下方法:引燃上述成型体,在用氮气加压的状态下,即在常压~
1mpa的氮气气氛下,通过自燃烧扩散,使金属粉末直接反应。点火(点燃,引燃)可以通过以往公知的方法进行,例如可以采用以下方法:通过使用安装在密闭式反应器中的一对电极的电弧放电来点火,通过对碳制或金属制的加热器进行通电加热来点火,通过激光照射来点火等。
[0037]
当如上所述点火时,成型体通过自燃在短时间内燃烧而扩散,例如被加热到1500~2000℃的反应温度,通过金属粉末与氮的直接反应来进行燃烧合成反应,由此得到金属氮化物。得到的金属氮化物通常为块状产物(即,金属氮化物的块状物)。
[0038]
(金属氮化物的粉碎)在本发明的金属氮化物的制造方法中,优选将金属氮化物在干式下进行机械粉碎。本发明中,通过如上所述实施燃烧合成反应,得到金属氮化物。如上所述,这样得到的金属氮化物通常为块状。通过对该块状金属氮化物进行后述的机械粉碎,能够得到粉末粒径小且具有适当粒度分布的金属氮化物粒子。予以说明,块状金属氮化物由于是由空隙率为40%以上的成型体得到的,因此能够容易地粉碎。
[0039]
(机械粉碎)本发明中,通过对通过上述燃烧合成反应得到的块状金属氮化物进行机械粉碎,能够得到具有适当粒度分布的金属氮化物粉末。该机械粉碎优选通过干式粉碎进行。对于使用水等液体介质的湿式粉碎来说,由于均匀地施加粉碎压力,因此在得到微细的粉末方面是有利的。但是,湿式粉碎存在生产率低的问题。另外,存在金属氮化物与液体介质反应而产生杂质的可能性,在粉碎后需要通过酸处理等的精制来除去杂质。而且,为了不增加环境负荷,需要对酸处理废液进行处理,导致粉碎的成本变高。因此,通过本发明的上述反应得到的块状金属氮化物优选通过干式粉碎进行粉碎。
[0040]
可以将块状金属氮化物以不同的粉碎条件进行多次粉碎,准备粒度分布不同的多种粉碎物,将它们适当混合,也能够得到具有适当粒度分布的金属氮化物的粉末。另外,通过导入筛分等分级工序,也能够得到具有适当粒度分布的金属氮化物的粉末。
[0041]
这样的干式粉碎使用振动粉碎机、珠磨机、使破碎对象物相互碰撞的气流粉碎机(喷射磨机)等粉碎机来进行。作为抑制粉碎时的重金属类污染的不言而喻的对策,是将金属氮化物的共用材料作为粉碎介质的方法。例如,使用气流粉碎机的气流粉碎由于能够通过粉末相互之间的碰撞来粉碎,因此从防止污染的观点考虑是最佳的。另外,即使是使用振动粉碎机或珠磨机的方法,只要使用作为共用材料的金属氮化物制的球作为粉碎介质,就没有污染问题。此时,由于粉碎介质也会有磨损,即使是微量的,因此很明显应该利用污染物少的介质。
[0042]
关于用作粉碎介质的金属氮化物球的制作,单独使用金属氮化物获得耐磨烧结体的方法的成本高,因此为了以低成本制作介质,可以采用混合氧化钇、氧化镁、氧化铝等烧结助剂来烧结的方法。对于这些烧结助剂的选择,只要选择目标的金属氮化物粉末所允许的成分,则作为制作烧结体用的金属氮化物粉末的方法就没有问题。予以说明,在以干式使用振动粉碎机或珠磨机粉碎金属氮化物粉末时,适宜采用添加微量的乙醇、异丙醇等醇类或水等来进行粉碎的方法。这些成分起促进粉碎的粉碎助剂的作用,因此能够缩短粉碎时间。关于粉碎助剂的添加量,以使粉碎物能够维持干燥状态的范围的量来添加。其量根据粉碎助剂的成分而不同,但相对于粉碎的金属氮化物粉末,适宜为0.1~2质量%的范围。
[0043]
(金属氮化物烧结体的制造)使用如上所述得到的金属氮化物的粉末,可以通过公知的方法制造金属氮化物烧结体。例如,当金属氮化物粉末为氮化硅粉末时,在氮化硅粉末中混合氧化钇、氧化镁、氧化锆、氧化铝等烧结助剂,通过压制成型,制作体积密度为1.7g/cm3以上、特别优选1.85g/cm3以上、更优选1.95g/cm3以上的成型体,接着通过进行烧成,能够得到烧结体。
[0044]
上述压制成型代表性的是单轴压制成型,优选采用在单轴压制成型后进行cip(cold isostatic pressing,冷等静压)成型的方法。
[0045]
另外,烧成在氮气气氛中在1700~2000℃下进行。烧结体的密度取决于烧成温度和烧成时间这两者。例如在1700℃烧成时,烧成时间为3~20小时左右。另外,在1850℃以上的温度烧成时,烧成时间过长时,有时由于氮化硅本身的分解而导致烧结体的密度下降。在这种情况下,通过在用氮气加压的气氛下烧结,能够抑制氮化硅烧结体的分解。该氮气压力越高,越能抑制氮化硅的分解,但从装置的耐压性能等经济上的理由考虑,适宜采用小于1mpa的压力。为了得到相对密度为99%以上的高密度的烧结体,适宜在1800℃以上的加压氮气气氛下进行烧成。以如上所述那样得到的金属氮化物烧结体可适用于散热用基板材料等。实施例
[0046]
以下,为了更具体地说明本发明示出了实施例,但本发明并不限定于这些实施例。予以说明,在实施例中,各种物性的测定通过如下方法进行。
[0047]
(1)有无粉尘飞扬确认将各实施例的由原料粉末构成的成型体以及各比较例的原料粉末填充于反应容器时是否产生粉尘(粉尘飞扬)。a
··
没有观察到粉尘飞扬。b
··
观察到粉尘飞扬。
[0048]
(2)氮化物回收率将刷洗前的氮化硅块的质量设为w1,将刷洗去除了未反应硅之后的氮化硅块的质量设为w2,由下式计算出氮化物回收率。然后,根据以下基准评价氮化物回收率。予以说明,进行刷洗直至通过目测在氮化硅块表面上看不到黑色部分(未反应硅)为止。氮化物回收率(%)=w2/w1
×
100a
··
氮化物回收率为95%以上b
··
氮化物回收率小于95%
[0049]
(3)氮化硅粉末的粒径(i)样品的前处理作为样品氮化硅粉末的前处理,将氮化硅粉末在空气中在约500℃的温度下进行2小时的烧成处理。在上述烧成处理中,对于粒径测定而言,存在以下情况:氮化硅粉末的表面氧量少,或者由于粉碎时的粉碎助剂等而导致粒子表面被疏水性物质覆盖,粒子本身呈疏水性,在这种情况下,存在在水中的分散不充分,再现性的粒径测定变得困难的情况。因此,通过将样品氮化硅粉末在空气中在200℃~500℃左右的温度下进行数小时的烧成处
理,向氮化硅粉末赋予亲水性,使之容易分散在水溶剂中,能够进行再现性高的粒径测定。此时确认,即使在空气中烧成(烧制),也几乎不影响测定的粒径。
[0049]
(ii)粒径的测定在最大100ml的具有标线的烧杯(内径60mmφ,高70mm)中加入90ml水和浓度5质量%的焦磷酸钠5ml,充分搅拌后,投入约一耳勺的样品氮化硅粉末,通过超声波均质器((株)日本精机制作所制us-300e,芯片直径26mm)以振幅(amplitude)50%(约2安培)使氮化硅粉末分散2分钟。予以说明,将上述芯片的前端插入至烧杯的20ml标线的位置进行分散。接着,对得到的氮化硅粉末的分散液,使用激光衍射/散射法粒度分布测定装置(microtrac-bel公司制的microtrac mt3300exii)测定粒度分布。测定条件如下:溶剂选择水(折射率1.33),粒子特性选择折射率为2.01,粒子透过性选择透过,粒子形状选择非球形。将通过上述粒径分布测定所测得的粒径分布的累积曲线为50%的粒径作为平均粒径。
[0051]
(4)成型体的空隙率使用自动比重计(新光电子(株)制,dma-220h型)对各个成型体测定密度,将15个成型体的密度的平均值表示为成型体的密度(d1)。由硅的密度、氮化硅的密度、以及原料粉末中的硅和氮化硅的比例,计算出成型体的理论密度(d2)。然后根据下式计算空隙率。空隙率(r)(%)=(1-d1/d2)
×
100
[0052]
(5)体积密度将上述成型体的密度(d1)作为成型体的体积密度。
[0053]
(6)β化率进行使用cukα射线的粉末x射线衍射(xrd)测定,通过“c.p.gazzara and d.r.messier:ceram.bull.,56(1977),777-780”中记载的方法,计算氮化硅粉末的α相与β相的重量比例。
[0054]
(7)bet比表面积制造好的氮化硅粉末的比表面积使用mountech公司制的bet法比表面积测定装置(macsorb hm型号-1201),使用基于氮气吸附的单点bet法测定。予以说明,在进行上述的比表面积测定之前,预先将待测定的氮化硅粉末在空气中在600℃下热处理30分钟,以除去吸附于粉末表面的有机物。
[0055]
(8)铝元素和铁元素的含量硅粉末中的杂质浓度按如下所述测定。将供于燃烧合成反应的硅粉末称量到树脂制容器中,添加70%浓度的高纯度浓硝酸。一边滴加50%浓度的高纯度氢氟酸,一边注意不要使硅的分解反应过于剧烈,当硅粉末完全溶解后,使树脂制容器中残留的硝酸和氢氟酸的混合酸在加热板上完全蒸发,将吸附于树脂制容器内表面的重金属成分用1%稀硝酸回收得到的溶液通过电感耦合等离子体-原子发射光谱仪(icp-aes)定量重金属成分。在此,使用“赛默飞世尔科技公司制的icap 6500duo”。氮化硅粉末中的杂质浓度使用jis r 1603:2007中规定的方法测定。
[0056]
(9)烧结体的制作相对于样品氮化硅粉末100质量份,添加作为主烧结助剂的氧化钇粉末5质量份、
作为副烧结助剂的氧化铝粉末或氧化镁粉末2质量份,在乙醇中使通过行星式球磨机充分混合。将如上所述混合有烧结助剂的氮化硅粉末充分干燥后,将约20g的氮化硅粉末以约0.2吨/cm2的压力进行单轴压制成型,由此制作50mmφ的圆板状成型体15片,然后将每片密封在软橡胶袋中并投入水中,进行向成型体表面施加2吨/cm2的压力的cip处理。在进行了cip处理的圆板状成型体的表面上涂布防粘附用的氮化硼粉末。将成型体以5片堆叠的方式放置在密闭性高的氮化硼制的箱型装置(setter)内,在0.8mpa的氮气气氛下,在1900℃下烧成5小时,得到烧结体。
[0057]
(10)烧结体密度使用自动比重计(新光电子(株)制,dma-220h型)对各个烧结体测定密度,将15个烧结体的密度的平均值表示为烧结体的密度。
[0058]
(11)烧结体的热导率(w/m
·
k)使用激光闪光法热物性测定装置(京都电子工业(株)制,lfa-502型),对各个烧结体测定热扩散率。通过将热扩散率、烧结体密度和烧结体比热相乘而求出热导率。予以说明,氮化硅烧结体的比热采用0.68(j/g
·
k)的值。从上述(9)的方法中制作的15个烧结体中任意取出3个,切出激光闪光法热物性测定用的试验片。由3个试验片各自的密度、热扩散率计算热导率,将该3个试验片的热导率的平均值表示为烧结体的热导率。
[0059]
(12)烧结体的三点弯曲强度(mpa)从上述(9)的方法中制作的除了用于测定热导率的3个以外的剩余12个烧结体中任意取出10个,切出用于测定三点弯曲强度的试验片。对10个试验片的每一个,通过根据jis r 1601:2008的方法测定三点弯曲强度。此时,使用支点间距离为30mm的试验夹具。将10个试验片的三点弯曲强度的平均值表示为烧结体的三点弯曲强度。
[0060]
在以下的实验中,使用以下的原料粉末。
·
硅粉末使用施加了氮化硅内衬的气流粉碎装置(气流粉碎机),将太阳能电池应用级别的高纯度多晶硅粉碎至平均粒径约5μm而得到的硅粉末100质量%用作原料粉末a。予以说明,在此得到的硅粉末的氧含量为约0.3质量%。另外,作为杂质的量,fe为10ppm,al为5ppm。
·
氮化硅粉末(稀释剂)使用平均粒径1μm的氮化硅粉末
[0061]
《实施例1》将8kg硅粉末和2kg氮化硅粉末混合而制成原料粉末。使用市售的粉末成型模具,对制成的原料粉末进行加压成型,制作成型体。具体地,使用内部尺寸为50mmφ的粉末成型模具,将约30g的原料粉末填充到上述粉末成型模具中,然后从上方以约60kg/cm2的压力压缩,然后从筒状容器中取出内部尺寸为50mmφ、高度约为15mm的圆柱形成型体。通过同样的方法制作多个成型体。然后,如图3(a)所示,以平放的方式将成型体排列在反应容器中。予以说明,在反应容器内,由氮化硅粉末形成隔热层,以将氮化硅粉末填埋入排列的成型体的间隙的方式,并且,以将氮化硅粉末以30mm的厚度覆盖成型体的上表面的方式。如上所述,将成型体收容在反应容器中后,将该反应容器设置在具有点火装置和气体供给/排出机构的耐压性密闭式反应器内,将反应器内减压脱气后,供给氮气进行氮气
置换。然后,逐渐供给氮气,使压力上升至0.7mpa。然后,引燃反应容器内的成型体中的一个成型体的端部,进行燃烧合成反应,得到块状氮化硅。然后,刷洗块状氮化硅的表面以削掉黑色的未反应硅,由此从块状氮化硅中除去未反应硅。然后,将块状氮化硅通过相互摩擦而解碎至大约5~20μm后,适量投入到振动粉碎机中进行7小时的微粉碎。微粉碎机和微粉碎方法使用常规的装置和方法,但作为防止重金属污染的措施,在粉碎机的内部衬有氨基甲酸酯,粉碎介质使用以氮化硅为主要成分的球。另外,在临开始微粉碎之前,添加1质量%的乙醇作为粉碎助剂,将粉碎机设为密闭状态进行微粉碎。结果,得到具有平均粒径0.7μm、比表面积16m2/g的特性的、基本上β型的100%的氮化硅粉末。反应条件、得到的氮化硅粉末的物性等示于表1。
[0062]
[烧结体1]在通过上述方法得到的氮化硅粉末100质量份中添加作为主烧结助剂的氧化钇5质量份、作为副烧结助剂的氧化镁2质量份,通过行星式球磨机混合后,经过上述的单轴压制成型和cip成型,在0.8mpa的氮气气氛下在1900℃下进行5小时的烧成。得到的烧结体的密度为3.25g/cm3,热导率为90w/m
·
k,三点弯曲强度为750mpa。该氮化硅粉末的烧结体具有高密度并且非常致密。并且热导率和弯曲强度的特性也优异。
[0063]
《实施例2》在实施例1的氮化硅粉末的制造方法中,将成型体的空隙率设为表1所示那样的低值,进行燃烧合成反应,得到块状氮化硅。得到的氮化硅团聚块的解碎和微粉碎在与实施例1同样的条件下进行。结果,得到具有表1所示特性的基本上β型的100%的氮化硅粉末。
[0064]
[烧结体2]使用上述氮化硅粉末,在与实施例1的烧结体1同样的条件下制作烧结体。烧结体的特性与上述烧结体1同样优异。
[0065]
《实施例3》在实施例1的氮化硅粉末的制作方法中,将成型体的空隙率设为表1所示那样的高值,进行燃烧合成反应,同时降低反应时的压力,通过与实施例1同样的方法合成氮化硅粉末。结果,得到的氮化硅粉末为含有约5%α型的β型氮化硅。得到的氮化硅粉末的特性示于表1。
[0066]
[烧结体3]使用上述含有α型的氮化硅粉末,在与实施例1的烧结体1同样的条件下制作烧结体。烧结体的特性与上述烧结体1同样优异。
[0067]
《实施例4》在实施例1所示的氮化硅粉末的制造方法中,仅将微粉碎时间缩短为5小时,除此以外,与实施例1同样操作,得到氮化硅粉末。得到的氮化硅粉末的特性示于表1。
[0068]
[烧结体4]使用通过上述方法得到的氮化硅粉末,在与实施例1的烧结体1同样的条件下制造烧结体。烧结体的特性与上述烧结体1同样优异。
[0069]
《实施例5》
在实施例1所示的氮化硅粉末的制造方法中,将微粉碎时间延长至10小时,除此以外,与实施例1同样操作,得到氮化硅粉末。得到的氮化硅粉末的特性示于表1。
[0070]
[烧结体5]使用通过上述方法得到的氮化硅粉末,在与实施例1的烧结体1同样的条件下制造烧结体。烧结体的特性与上述烧结体1同样优异。
[0071]
《实施例6》改变原料粉末中的硅粉末和氮化硅粉末的比例,除此以外,进行与实施例1同样的燃烧合成反应和粉碎方法。得到的氮化硅粉末的特性示于表1。
[0072]
[烧结体6]使用通过上述方法得到的氮化硅粉末,在与实施例1的烧结体1同样的条件下制造烧结体。烧结体的特性与上述烧结体1同样优异。
[0073]
《比较例1》不将原料粉末成型而直接填充到反应容器中,除此以外,进行与实施例1同样的燃烧合成反应和粉碎方法。得到的氮化硅粉末的特性示于表1。
[0074]
[烧结体7]使用上述氮化硅粉末,在与实施例1的烧结体1同样的条件下制作烧结体。烧结体的特性与上述烧结体1同样优异。
[0075]
《比较例2》不将原料粉末成型而直接填充到反应容器中,除此以外,进行与实施例4同样的燃烧合成反应和粉碎方法。得到的氮化硅粉末的特性示于表1。
[0076]
[烧结体8]使用上述氮化硅粉末,在与实施例4的烧结体4同样的条件下制作烧结体。烧结体的特性与上述烧结体1同样优异。
[0077]
《比较例3》不将原料粉末成型而直接填充到反应容器中,除此以外,进行与实施例5同样的燃烧合成反应和粉碎方法。得到的氮化硅粉末的特性示于表1。
[0078]
[烧结体9]使用上述氮化硅粉末,在与实施例5的烧结体5同样的条件下制作烧结体。烧结体的特性与上述烧结体1同样优异。
[0079]
《比较例4》不将原料粉末成型而直接填充到反应容器中,除此以外,进行与实施例6同样的燃烧合成反应和粉碎方法。得到的氮化硅粉末的特性示于表1。
[0080]
[烧结体10]使用上述氮化硅粉末,在与实施例6的烧结体6同样的条件下制作烧结体。烧结体的特性与上述烧结体1相同。
[0082]
〈比较例5〉在实施例1的氮化硅粉末的制造方法中,将成型体的空隙率设为30%的值,进行燃
烧合成反应。此时,燃烧反应不能充分进行,反应过程中熄火,未反应物增多。
[0083]
〈比较例6〉在实施例1的氮化硅粉末的制造方法中,将成型体的空隙率设为80%的值。此时,成型体变脆,处理性变差,难以设置在反应容器内。
[0084]
由此可知,通过使用将粉末原料成型为具有规定空隙率而获得的原料,能够抑制粉尘飞扬,并且能够提高氮化物的回收率。另外可知,使用成型的原料也与使用未成型的原料的情况同样地得到了优异的烧结体。予以说明,在使用未成型的原料制作的氮化硅块的表面,主要残留条纹状的黑色的未反应硅。由该条纹状的形状来看,认为未反应的硅残留的原因是由于在填充的原料粉末中产生了龟裂(裂纹)。由于龟裂(裂纹)从原料粉末的表面直达深处,因此认为在使用未成型原料制作出的氮化硅块中,未反应的硅残留在氮化硅块的表面直到深处。而且,未反应的硅不能从氮化硅块中除去,除非用刷子将氮化硅块的表面刷洗刮掉很多时,因此认为,对于使用未成型原料制作出的氮化硅块来说,氮化物的回收率低。另外,通过在上述成型的原料的周围形成隔热层,能够将未反应物的量降低至10%以下,根据情况能够降低至5%以下。
[0085]
符号说明1a~1c
ꢀꢀꢀꢀ
成型体2
ꢀꢀꢀꢀꢀꢀꢀꢀꢀ
耐热性容器3
ꢀꢀꢀꢀꢀꢀꢀꢀꢀ
隔热层
再多了解一些
本文用于企业家、创业者技术爱好者查询,结果仅供参考。