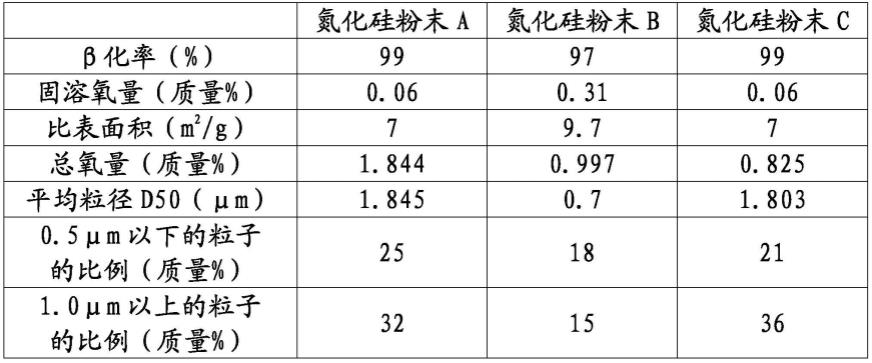
1.本发明涉及具有高热导率(导热系数)的氮化硅烧结体的制造方法。
背景技术:
2.在氮化硅粉末中添加各种烧结助剂在高温下烧结而成的氮化硅烧结体在各种陶瓷烧结体中具有轻、机械强度强、耐化学药品性高、电绝缘性高等特征,被用作滚珠轴承等耐磨损用部件、高温构造用部件。另外,由于还可以通过设计助剂的种类、烧结条件来提高导热性,因此它也被用作薄而强度高的散热用基板材料。
3.作为氮化硅粉末的合成法,已知有以二氧化硅粉末为原料,在碳粉末存在下使氮气流通而生成氮化硅的还原氮化法(例如专利文献1)、使金属硅(硅粉末)与氮在高温下反应的直接氮化法(例如专利文献2)、使卤化硅与氨反应的酰亚胺分解法等。进而,还已知有通过利用自燃烧法(self-propagating high temperature synthesis,shs法)的直接氮化法来合成金属氮化物的方法。自燃烧法又称燃烧合成法,是将含有硅粉的原料粉末导入反应容器内,在氮气气氛下灼热引燃原料粉末的一部分而产生氮化反应,使由该氮化反应产生的氮化燃烧的热传递到周围而使整体发生反应的合成法,作为比较廉价的合成方法而广为人知。
4.作为氮化硅粉末的晶体形态,已知有α型和β型。例如如非专利文献1所示,α型氮化硅粉末在烧结过程中溶解在烧结助剂中而作为β型再析出,其结果,能够得到致密且热导率高的烧结体,因此目前被广泛使用。
5.然而,在制造α型氮化硅粉末的情况下,其制造工艺容易变得复杂。例如在直接氮化法中,为了不生成β型,需要在低温下长时间氮化,因此制造成本变高(非专利文献2)。
6.从这样的背景出发,期望使用以较低成本制造的β型氮化硅粉末来制造致密且热导率高的烧结体的技术。专利文献3中记载了涉及高导热性氮化硅陶瓷及其制造方法的发明,在该实施例中,示出了通过将含有平均粒径0.5μm的β型氮化硅粉末和由氧化镱和氮化硅镁粉末构成的烧结助剂的成型体在10个大气压的加压氮气中在1900℃下烧结2~24小时,能够得到致密且热导率高的烧结体。现有技术文献
7.专利文献专利文献1:日本特开2009-161376号公报专利文献2:日本特开平10-218612号公报专利文献3:日本特开2002-128569号公报
8.非专利文献非专利文献1:日本舶用机关学会志,1993年9月,第28卷,第9号,p548-556非专利文献2:journal of the ceramic society of japan,100[11],1366-1370(1992)
技术实现要素:
发明要解决的课题
[0009]
专利文献3中公开的β型氮化硅粉末的烧结体如上所述在10个大气压的加压氮气中制造。一般在加压下烧成时,容易抑制原料的氮化硅的分解,因此能够在超过1800℃的高温下烧成。已知在这样的高温高压下烧成时,所生成的烧结体容易致密化,而且可降低导致热导率降低的主要原因之一的在氮化硅粒子内部固溶的杂质氧量,容易得到热导率高的烧结体。然而,在如专利文献3那样在加压下烧成时,在制造时需要使用耐压容器。因此,具有在制造上存在设备的限制,且制造成本升高的问题。另外,专利文献3完全没有公开或启示关于使用β型氮化硅粉末且在无需使用耐压容器的常压(大气压)或大致常压(大气压附近的压力)的条件下得到热导率高的烧结体的方法。
[0010]
本发明正是鉴于上述以往的课题而完成的,其课题在于提供一种在一般被认为难以得到高热导率的烧结体的条件下制造高热导率的烧结体的方法,所述条件是指使用β化率高的氮化硅粉末为原料,并且将其在常压或大致常压下烧结。解决课题的手段
[0011]
本发明人等为了实现上述目的反复进行了深入研究。结果发现,使用包含“β化率、固溶氧量和比表面积在特定范围内的氮化硅粉末”和“含有不具有氧键的化合物的烧结助剂”、且总氧量和铝元素总含量在特定范围内的成型体,将其在常压或大致常压下在特定温度范围内烧成,由此能够得到热导率高的烧结体,从而完成了本发明。
[0012]
本发明的主旨为以下的[1]~[10]。[1]氮化硅烧结体的制造方法,其特征在于,将成型体在非活性气体气氛和0mpa
·
g以上且低于0.1mpa
·
g的压力下加热至1200~1800℃的温度来烧结氮化硅,所述成型体包含:β化率为80%以上、固溶氧量为0.2质量%以下、比表面积为5~20m2/g的氮化硅粉末,和含有不具有氧键的化合物的烧结助剂,且所述成型体的总氧量被调节为1~15质量%,铝元素的总含量被调节为800ppm以下。[2]如上述[1]所述的氮化硅烧结体的制造方法,其中,所述氮化硅粉末的总氧量为1质量%以上。[3]如上述[1]或[2]所述的氮化硅烧结体的制造方法,其中,所述成型体是将含有氮化硅粉末、烧结助剂和水的成型用组合物成型而得到的成型体。[4]如上述[1]~[3]任一项所述的氮化硅烧结体的制造方法,其中,所述氮化硅粉末的平均粒径d
50
为0.5~1.2μm,粒径0.5μm以下的粒子所占的比例为20~50质量%,且粒径1.0μm以上的粒子所占的比例为20~50质量%。[5]如上述[1]~[4]任一项所述的氮化硅烧结体的制造方法,其中,所述烧结助剂含有金属氧化物。[6]如上述[1]~[5]任一项所述的氮化硅烧结体的制造方法,其中,所述烧结助剂中含有的不具有氧键的化合物为含有稀土类元素或镁元素的碳氮化物系化合物。
[7]如上述[1]~[6]任一项所述的氮化硅烧结体的制造方法,其中,所述成型体的密度为1.95g/cm3以上。[8]如上述[1]~[7]任一项所述的氮化硅烧结体的制造方法,其中,所得氮化硅烧结体的通过激光闪光法测定的热导率为80w/mk以上。[9]如上述[1]~[8]任一项所述的氮化硅烧结体的制造方法,其中,所得氮化硅烧结体的绝缘击穿电压为11kv以上。[10]如上述[1]~[9]任一项所述的氮化硅烧结体的制造方法,其中,所得氮化硅烧结体的ra为0.6μm以下。发明效果
[0013]
根据本发明,能够提供一种氮化硅烧结体的制造方法,其即使在使用β化率高的氮化硅粉末且在常压或大致常压下烧成时,也能够得到热导率高的氮化硅烧结体。
具体实施方式
[0014]
[氮化硅烧结体的制造方法]本发明的氮化硅烧结体的制造方法的特征在于,将成型体在非活性气体气氛和0mpa
·
g以上且低于0.1mpa
·
g的压力下加热至1200~1800℃的温度来烧结氮化硅,所述成型体包含:β化率为80%以上、固溶氧量为0.2质量%以下、比表面积为5~20m2/g的氮化硅粉末,和含有不具有氧键的化合物的烧结助剂,且所述成型体的总氧量被调节为1~15质量%、铝元素的总含量被调节为800ppm以下。
[0015]
[成型体]说明本发明的氮化硅烧结体的制造方法中使用的成型体。该成型体含有以下说明的特定的氮化硅粉末和烧结助剂。
[0016]
《氮化硅粉末》(β化率)成型体中含有的氮化硅粉末的β化率为80%以上。由于β化率为80%以上的氮化硅粉末即使不设定严密的制造条件也能够获得,因此能够以较低成本制造。因此,通过使用β化率高的氮化硅粉末,能够抑制氮化硅烧结体的整体制造成本。另外,通过将β化率设定得较高,能够进一步抑制烧成时α-氮化硅粒子相变为β-氮化硅粒子时的摄氧量。在此,氮化硅粉末的β化率优选为85%以上,更优选为90%以上。
[0017]
予以说明,氮化硅粉末的β化率是指氮化硅粉末中的β相的峰强度相对于α相和β相合计的峰强度的比例[100
×
(β相的峰强度)/(α相的峰强度 β相的峰强度)],通过使用cukα射线的粉末x射线衍射(xrd)测定而求出。更详细地,通过c.p.gazzara and d.r.messier:ceram.bull.,56(1977),777-780中记载的方法,计算出氮化硅粉末的α相与β相的重量比例而求出。
[0018]
(固溶氧量)氮化硅粉末的固溶氧量为0.2质量%以下。当固溶氧量超过0.2质量%时,在本发
明特征的烧成条件下烧成得到的氮化硅烧结体的热导率变低。从得到高热导率的氮化硅烧结体的观点考虑,氮化硅粉末的固溶氧量优选为0.1质量%以下。在此,固溶氧量是指在氮化硅粉末的粒子内部固溶的氧(以下,也称为内部氧),不含不可避免地存在于粒子表面的来自sio2等氧化物的氧(以下,也称为外部氧)。予以说明,固溶氧量可以通过实施例中记载的方法测定。
[0019]
氮化硅粉末的固溶氧量的调整方法没有特别限定,例如,可以在制造氮化硅粉末时使用高纯度的原料。例如,在通过直接氮化法制造氮化硅粉末的情况下,作为所使用的原料,优选使用内部没有氧固溶的主要原因的硅粉末,具体而言,优选使用源自半导体级的硅,例如以切割上述硅等加工时产生的切削粉为代表的硅粉末。上述半导体级的硅代表性的是通过在钟罩式反应容器内使高纯度的三氯硅烷与氢反应的所谓“西门子法”得到的多晶硅。
[0020]
(比表面积)氮化硅粉末的比表面积为5~20m2/g。当氮化硅粉末的比表面积超过20m2/g时,难以降低固溶氧量,当比表面积小于5m2/g时,难以得到高密度且高强度的氮化硅烧结体。氮化硅粉末的比表面积优选为7~20m2/g,更优选为12~15m2/g。予以说明,本发明中,比表面积是指使用基于氮气吸附的单点bet法测定的bet比表面积。
[0021]
(平均粒径)氮化硅粉末的平均粒径d
50
优选为0.5~3μm,更优选为0.7~1.7μm。当使用这样的平均粒径的氮化硅粉末,烧结变得更容易进行。平均粒径d
50
是通过激光衍射散射法测定的基于50%体积的值。氮化硅粉末中的粒径0.5μm以下的粒子的比例优选为20~50质量%,更优选为20~40质量%。另外,氮化硅粉末中的粒径为1.0μm以上的粒子的比例优选为20~50质量%,更优选为20~40质量%。当使用具有这样的粒度分布的氮化硅粉末时,容易得到致密且热导率高的氮化硅烧结体。其原因尚不清楚,但认为β-氮化硅粒子与α-氮化硅粒子不同,烧成时不易引起溶解再析出,通过预先在烧成初期阶段将微细粒子和粗大粒子调整至一定的平衡,能够得到更致密的烧结体。
[0022]
(总氧量)氮化硅粉末的总氧量没有特别限定,优选为1质量%以上。总氧量是指上述的固溶氧(内部氧)量与外部氧量的合计。当总氧量为这些下限值以上时,例如发挥粒子表面的氧化硅等容易促进烧结的效果。另外,氮化硅粉末的总氧量优选为10质量%以下。予以说明,即使氮化硅粉末的总氧量为1质量%以上,只要固溶氧量如上所述为一定值以下,就能够提高烧结体的导热性。氮化硅粉末的总氧量可通过实施例中记载的方法测定。
[0023]
成型体中的氮化硅粉末的量以成型体总量为基准,优选为80质量%以上,更优选为90质量%以上。
[0024]
《氮化硅粉末的制造》氮化硅粉末的制造方法只要是能够得到具有上述特性的氮化硅粉末的方法,就没
有特别限定。作为氮化硅粉末的制造方法,例如可应用:以二氧化硅粉末为原料,在碳粉末存在下使氮气流通而生成氮化硅的还原氮化法;使硅粉末与氮在高温下反应的直接氮化法;使卤化硅与氨反应的酰亚胺分解法等,但从容易制造具有上述特性的氮化硅粉末的观点考虑,优选直接氮化法,其中,更优选利用自燃烧法的直接氮化法(燃烧合成法)。燃烧合成法是使用硅粉末作为原料,在氮气气氛下强制引燃原料粉末的一部分,通过原料化合物的自发热来合成氮化硅的方法。燃烧合成法是公知的方法,例如可以参照日本特开2000-264608号公报、国际公开第2019/167879号等。
[0025]
《烧结助剂》本发明的成型体包含含有“不具有氧键的化合物”的烧结助剂。通过使用这样的烧结助剂,能够防止得到的氮化硅烧结体的热导率降低。作为上述不具有氧键的化合物,优选含有稀土类元素或镁元素的碳氮化物系化合物(以下,也称为特定的碳氮化物系化合物)。通过使用这种特定的碳氮化物系化合物,更有效地容易地获得热导率高的氮化硅烧结体。其原因尚不清楚,但推测上述特定的碳氮化物系化合物起吸附氮化硅粉末中含有的氧的吸气剂的作用,结果可得到热导率高的氮化硅烧结体。
[0026]
在含有稀土类元素的碳氮化物系化合物中,作为稀土类元素,优选y(钇)、la(镧)、sm(钐)、ce(铈)等。
[0027]
作为含有稀土类元素的碳氮化物系化合物,例如可举出y2si4n6c、yb2si4n6c、ce2si4n6c等,其中,从容易得到热导率高的氮化硅烧结体的观点考虑,优选y2si4n6c、yb2si4n6c。作为含有镁元素的碳氮化物系化合物,例如可举出mgsi4n6c等。这些特定的碳氮化物系化合物可以单独使用1种,也可以并用2种以上。
[0028]
上述含有稀土类元素或镁元素的碳氮化物系化合物中,特别优选的化合物为y2si4n6c、mgsi4n6c。
[0029]
另外,烧结助剂除了含有不具有上述氧键的化合物以外,还可以含有金属氧化物。通过使烧结助剂含有金属氧化物,氮化硅粉末的烧结变得容易进行,容易得到更致密且高强度的烧结体。作为金属氧化物,例如可举出氧化钇(y2o3)、氧化镁(mgo)、氧化铈(ceo)等。其中,优选氧化钇。金属氧化物可以单独使用1种,也可以并用2种以上。
[0030]
烧结助剂中含有的以上述特定的碳氮化物系化合物为代表的不具有氧的化合物与金属氧化物的质量比(不具有氧的化合物/金属氧化物)优选为0.2~4,更优选为0.6~2。当为这样的范围时,容易得到致密且热导率高的氮化硅烧结体。
[0031]
另外,成型体中的烧结助剂的含量相对于氮化硅粉末100质量份,优选为5~20质量份,更优选为7~10质量份。
[0032]
《粘合剂》成型体可以使用粘合剂来成型。在这种情况下,成型体可以通过将后述的成型用组合物成型,根据需要进行干燥,脱脂,以除去粘合剂而获得。作为粘合剂,没有特别限定,可举出聚乙烯醇、聚乙烯醇缩丁醛、甲基纤维素、海藻酸、聚乙二醇、羧甲基纤维素、乙基纤维素、丙烯酸系树脂等。
[0033]
用于制造成型体的成型用组合物中的粘合剂的含量相对于氮化硅粉末100质量份,优选为1~30质量份,根据成型方法适当确定其比例即可。
[0034]
《总氧量》本发明中,成型体的总氧量(总氧含量)为1~15质量%。在此,从上述说明可以理解,上述成型体是指供于烧结的状态的成型体,是指不含用于制造成型体的粘合剂、溶剂等在供于烧结之前通过干燥、脱脂等处理而被除去的物质的状态。当总氧量超过15质量%时,由于氧的影响,所得氮化硅烧结体的热导率降低。另外,当总氧量小于1质量%时,烧结难以进行,得不到致密的氮化硅烧结体,热导率和强度降低。成型体的总氧量优选为2~10质量%,更优选为3~5质量%。总氧量可通过适当调节所使用的氮化硅的总氧量、烧结助剂的种类以及成型方法等而成为期望的范围。
[0035]
《铝元素的总含量》成型体的铝元素的总含量(质量)为800ppm以下。即,本发明中使用的成型体的铝元素的量非常少,由此能够得到具有高热导率的氮化硅烧结体。成型体的铝元素的总含量优选为500ppm以下,更优选为200ppm以下。
[0036]
《成型体密度》成型体的密度没有特别限定,优选为1.95g/cm3以上,更优选为1.98g/cm3以上。当成型体的密度为这些下限值以上时,容易得到热导率优异的氮化硅烧结体。
[0037]
[成型体的制造]本发明中使用的成型体的制造方法没有特别限定,例如可举出将至少含有氮化硅粉末和烧结助剂的成型用组合物通过公知的成型手段成型的方法。作为公知的成型手段,例如可举出:压制成型法、挤出成型法、注塑成型法、片材成型法(刮刀法)等。
[0038]
从容易成型的观点考虑,可以在成型用组合物中进一步配合粘合剂。予以说明,粘合剂的种类如上所述。予以说明,关于成型用组合物中的相对于氮化硅粉末100质量份的烧结助剂的量和粘合剂的量,与在成型体中说明的量相同。
[0039]
另外,从操作容易性和成型容易性等的观点考虑,成型用组合物中可以含有溶剂。作为溶剂,没有特别限定,可举出醇类、烃类等有机溶剂、水等,本发明中,优选使用水。即,优选将含有氮化硅粉末、烧结助剂和水的成型用组合物成型,得到成型体。使用水作为溶剂的情况与使用有机溶剂的情况相比,降低了环境负荷,因而是优选的。
[0040]
通常,当使用水作为成型用组合物中含有的溶剂时,将成型体烧成得到的氮化硅烧结体的内部容易残留源自水的氧,因此,热导率容易降低。与此相比,本发明中,通过使用所述固溶氧量为一定值以下的氮化硅粉末等,即使使用水作为溶剂来增加总氧量,通过控制所述总氧量也能够得到热导率高的烧结体。
[0041]
[烧结方法]在本发明的氮化硅烧结体的制造方法中,将上述成型体在一定条件下烧成,使氮化硅烧结。以下,说明烧成时的条件。烧成在非活性气体气氛下进行。非活性气体气氛下是指例如氮气气氛下或氩气气氛下等。
[0042]
另外,在这样的非活性气体气氛下,在0mpa
·
g以上且小于0.1mpa
·
g的压力下进
行烧成。压力优选为0mpa
·
g以上且0.05mpa
·
g以下,更优选为0mpa
·
g(即常压(大气压))。在此,压力单位的mpa
·
g的末尾的g是指表压。通常,当为这样的常压或大致常压区域的压力时,氮化硅容易分解,因此无法将温度调整为例如超过1800℃,因此,难以得到致密化和热导率高的氮化硅烧结体。与此相比,在本发明的制造方法中,由于如上所述使用特定的成型体,因此即使在上述压力范围内,也能够得到热导率高的氮化硅烧结体。
[0043]
另外,由于能够在常压或大致常压的条件下烧结氮化硅,因此无需在压力容器(耐压容器)内制造。因此,能够简化制造设备,能够降低制造成本。具体而言,烧成可以在马弗炉、管式炉等间歇式炉中进行,也可以在推送式炉等连续炉中进行,因此可适用多种制造方法,生产率提高。
[0044]
将成型体加热至1200~1800℃的温度来烧制。当温度低于1200℃时,氮化硅的烧结难以进行,当超过1800℃时,氮化硅容易分解。从这样的观点考虑,烧成时的加热温度优选为1600~1800℃。另外,烧成时间没有特别限定,优选为3~20小时左右。
[0045]
予以说明,在上述成型体的形成中使用粘合剂时,粘合剂等有机成分的除去优选设置脱脂工序来进行。上述脱脂条件没有特别限定,例如可以通过将成型体在空气中或氮气、氩气等非活性气氛下加热至450~650℃来进行。
[0046]
[氮化硅烧结体的物性]通过本发明制造方法得到的氮化硅烧结体显示出高的热导率。所得氮化硅烧结体的热导率优选为80w/mk以上,更优选为100w/mk以上。热导率可以通过激光闪光法测定。
[0047]
通过本发明制造方法得到的氮化硅烧结体的绝缘击穿电压优选为11kv以上,更优选为13kv以上。具备这样的绝缘击穿电压的氮化硅烧结体不易发生绝缘击穿,作为产品的可靠性优异。
[0048]
通过本发明制造方法得到的氮化硅烧结体由于在温和的条件(在常压或大致常压下、且温度比通常低的条件)下烧成,因此表面的凹凸少。具体而言,得到的氮化硅烧结体的ra(算术平均粗糙度)优选为0.6μm以下,更优选为0.55μm以下。具有这样的ra的氮化硅烧结体例如对金属等使用对象物的贴附性良好。进而,能够缩短将氮化硅烧结体根据需要进行镜面抛光时的作业时间。ra可以通过表面粗糙度计测定。另外,上述热导率、绝缘击穿电压、ra的测定是在对氮化硅烧结体的表面进行喷砂处理以除去烧结时附着在烧结体上的脱模剂等附着物之后进行。实施例
[0049]
以下,为了更具体地说明本发明,示出了实施例,但本发明并不限定于这些实施例。予以说明,在实施例中,各种物性的测定通过以下方法进行。
[0050]
(1)氮化硅粉末的β化率氮化硅粉末的β化率通过使用cukα射线的粉末x射线衍射(xrd)测定而求出。具体而言,通过c.p.gazzara and d.r.messier:ceram.bull.,56(1977),777-780中记载的方
法,计算出氮化硅粉末的α相和β相的重量比例,求出β化率。
[0051]
(2)氮化硅粉末的比表面积氮化硅粉末的比表面积使用mountech公司制的bet法比表面积测定装置(macsorb hm型号-1201),使用基于氮气吸附的单点bet法测定。予以说明,在进行上述的比表面积测定之前,预先将待测定的氮化硅粉末在空气中在600℃下热处理30分钟,以除去吸附于粉末表面的有机物。
[0052]
(3)氮化硅粉末的固溶氧量和总氧量氮化硅粉末的固溶氧量通过非活性气体熔融-红外线吸收法测定。测定通过氧/氮分析装置(horiba公司制的“emga-920”)进行。作为样品,将各实施例、比较例中使用的氮化硅粉末25mg封入锡囊(锡囊使用leco公司制的锡囊),导入石墨坩埚中,以5.5kw加热20秒,进行吸附气体的脱气,然后以0.8kw升温10秒、再以0.8kw至4kw升温350秒,测定其间产生的二氧化碳的量,换算为氧含量。在350秒的升温中,初期产生的氧是存在于氮化硅粒子表面的源自氧化物的氧(外部氧),之后产生的氧相当于固溶在氮化硅晶体中的固溶氧(内部氧),因此从与减去预先测定的背景而得到的这2个测定峰的谷相当的部分引一条垂线,将2个峰分开。通过按比例分配各自的峰面积,计算出固溶氧(内部氧)量和外部氧量。
[0053]
(4)氮化硅粉末的粒径(i)样品的前处理作为样品氮化硅粉末的前处理,将氮化硅粉末在空气中在约500℃的温度下进行2小时的烧成处理。在上述烧成处理中,对于粒径测定而言,存在以下情况:氮化硅粉末的表面氧量少,或者由于粉碎时的粉碎助剂等而导致粒子表面被疏水性物质覆盖,粒子本身呈疏水性,在这种情况下,存在在水中的分散不充分,再现性的粒径测定变得困难的情况。因此,通过将样品氮化硅粉末在空气中在200℃~500℃左右的温度下进行数小时的烧成处理,向氮化硅粉末赋予亲水性,使之容易分散在水溶剂中,能够进行再现性高的粒径测定。此时确认,即使在空气中烧成(烧制),也几乎不影响测定的粒径。
[0054]
(ii)粒径的测定在最大100ml的具有标线的烧杯(内径60mmφ,高70mm)中加入90ml水和浓度5质量%的焦磷酸钠5ml,充分搅拌后,投入约一耳勺的样品氮化硅粉末,通过超声波均质器((株)日本精机制作所制us-300e,芯片直径26mm)以振幅(amplitude)50%(约2安培)使氮化硅粉末分散2分钟。予以说明,将上述芯片的前端插入至烧杯的20ml标线的位置进行分散。接着,对得到的氮化硅粉末的分散液,使用激光衍射/散射法粒度分布测定装置(microtrac-bel公司制的microtrac mt3300exii)测定粒度分布。测定条件如下:溶剂选择水(折射率1.33),粒子特性选择折射率为2.01,粒子透过性选择透过,粒子形状选择非球形。将通过上述粒径分布测定所测得的粒径分布的累积曲线为50%的粒径作为平均粒径(平均粒径d50)。
[0055]
(5)成型体的总氧量成型体的总氧量通过非活性气体熔融-红外线吸收法测定。测定通过氧/氮分析装置(horiba公司制的“emga-920”)进行。
将作为样品的成型体15mg封入锡囊(锡囊使用leco制的锡囊),导入石墨坩埚中,以5.5kw加热20秒,再以5.0kw加热20秒,进行吸附气体的脱气,然后以5.0kw加热75秒,测定其间产生的二氧化碳的量,换算为氧含量。
[0056]
(6)成型体的密度使用自动比重计(新光电子(株)制:dma-220h型)测定每个成型体的密度,将15件成型体的密度的平均值作为成型体的密度。
[0057]
(7)成型体的铝元素的总含量成型体中的铝元素的总含量使用电感耦合等离子体发光分光分析装置(thermo fisher scientific公司制“icap 6500duo”)测定。
[0058]
(8)氮化硅烧结体的热导率氮化硅烧结体的热导率使用京都电子工业制的lfa-502通过激光闪光法测定。热导率是通过将热扩散率、烧结体密度和烧结体比热相乘而求出。予以说明,氮化硅烧结体的比热采用0.68(j/g
·
k)的值。烧结体的密度使用自动比重计(新光电子(株)制:dma-220h型)测定。予以说明,热导率的测定在对氮化硅烧结体的表面进行喷砂处理后,在表面涂敷au和涂敷碳后进行。
[0059]
(9)氮化硅烧结体的绝缘击穿电压根据jis c2110测定绝缘击穿电压。具体而言,使用绝缘耐压测定装置(计测技术研究所社制“tk-o-20k”)向氮化硅烧结体施加电压,测定发生绝缘击穿时的电压。
[0060]
(10)氮化硅烧结体的ra(算术平均粗糙度)氮化硅烧结体的ra使用表面粗糙度测定器(东京精密株式会社制,
“サーフコム
480a”),以评价长度2.5mm、测定速度0.3mm/s的针扫描,测定ra。予以说明,氮化硅烧结体使用对表面进行喷砂处理而除去了脱模剂等的烧结体。
[0061]
在各实施例和比较例中,使用以下的各原料。《氮化硅粉末》准备表1所示的氮化硅粉末a、b、c。它们通过以下方法制造。
[0062]
(氮化硅粉末a的制造)将硅粉末(半导体级,平均粒径5μm)和作为稀释剂的氮化硅粉末(平均粒径1.5μm)混合,得到原料粉末(si:80质量%,si3n4:20质量%)。将该原料粉末填充到反应容器中形成原料粉末层。接着,将该反应容器设置在具有点火装置和气体供给/排出机构的耐压性密闭式反应器内,将反应器内减压而脱气后,供给氮气进行氮气置换。然后,逐渐供给氮气使其上升至0.7mpa为止。达到规定压力的时间点(引燃时)的原料粉末的体积密度为0.5g/cm3。然后,引燃反应容器内的原料粉末的端部,进行燃烧合成反应,得到含有氮化硅的块状产物。将得到的块状产物相互摩擦而解碎后,适量投入到振动粉碎机中进行6小时的微粉碎。予以说明,微粉碎机和微粉碎方法使用常规的装置和方法,但作为防止重金属污染的措施,在粉碎机的内部衬有氨基甲酸酯,粉碎介质使用以氮化硅为主要成分的球。另外,在临开始微粉碎之前,添加1质量%的乙醇作为粉碎助剂,将粉碎机设为密闭状态进行微粉碎,接着,在空气中加热以进行氧化处理,调整总氧浓度,得到氮化硅粉末a。所得氮化硅粉末a的测定结果示于表1。
[0063]
(氮化硅粉末b的制造)作为氮化硅粉末b,将市售的氮化硅粉末在氮气气氛中加热,准备表1所示的氮化硅粉末。
[0064]
(氮化硅粉末c的制造)在上述氮化硅粉末a的制造方法中,不进行氧化处理,除此以外,同样操作,得到氮化硅粉末c。所得氮化硅粉末c的测定结果示于表1。[表1]
[0065]
《烧结助剂》1、不具有氧键的化合物关于y2si4n6c粉末,将氧化钇(信越化学工业株式会社制)、氮化硅粉末(上述记载的本公司制粉末)和碳粉末(三菱化学制)使用下述反应式进行加热合成来制作。8si3n4 6y2o3 15c 2n2→
6y2si4n6c 9co2对于mgsi4n6c粉末,同样地使用下述反应式进行加热合成来制作。si3n4 mgsin2 c
→
mgsi4n6c2、金属氧化物氧化钇(y2o3)
·····
信越化学工业株式会社制
[0066]
《粘合剂》作为粘合剂,使用作为水系树脂粘合剂的聚乙烯醇树脂(日本vam&poval公司制)。
[0067]
[实施例1]称量氮化硅粉末a 100质量份、不具有氧键的化合物y2si4n6c 2质量份、mgsi4n6c 5质量份、氧化钇3质量份,以水为分散介质,使用树脂罐和氮化硅球,用球磨机粉碎混合24小时。予以说明,按照使浆料的浓度为60wt%的方式预先称量水,投入到树脂罐内。粉碎混合后,添加22质量份的水系树脂粘合剂,进一步混合12小时,得到浆料状的成型用组合物。接着,使用真空脱泡机(
サヤマ
理研制)调整该成型用组合物的粘度,制作涂布用浆料。然后,通过刮刀法将该调整了粘度的成型用组合物进行片材成型,得到宽75cm、厚0.42mmt的片材成型体。将如上所述得到的片材成型体在干燥空气中在550℃的温度下进行脱脂处理,得到脱脂了的成型体。所得成型体的物性示于表2。然后,将该脱脂后的成型体放入烧制容器中,在氮气气氛和0.02mpa
·
g的压力下,
在1780℃下烧成(烧制)9小时,得到氮化硅烧结体。烧结体的物性示于表2。
[0068]
[比较例1]将实施例1中使用的氮化硅粉末a变更为氮化硅粉末b,除此以外,与实施例1同样操作,得到氮化硅烧结体。烧结体的物性示于表2。
[0069]
[实施例2]在上述实施例1中,如表2所示那样变更烧结助剂的量,设为表2所示的总氧量、成型体密度,另外,将烧成温度设为1740℃,除此以外,与实施例1同样操作,得到氮化硅烧结体。烧结体的物性示于表2。
[0070]
[实施例3]在上述实施例1中,作为氮化硅粉末,使用氮化硅粉末c,调整烧结助剂的量,如表2所示那样变更总氧量和成型体密度,除此以外,与实施例1同样操作,得到氮化硅烧结体。烧结体的物性示于表2。
[0071]
[表2]
[0072]
由各实施例的结果可知,在采用特定成型体的情况下,即使用作原料的氮化硅粉末的β化率高、且烧成时的压力低时,也能够获得热导率高的烧结体。与此相比,在使用不满足本发明要件的成型体的情况下,在烧成时的压力低时,无法得到热导率高的烧结体。
再多了解一些
本文用于企业家、创业者技术爱好者查询,结果仅供参考。