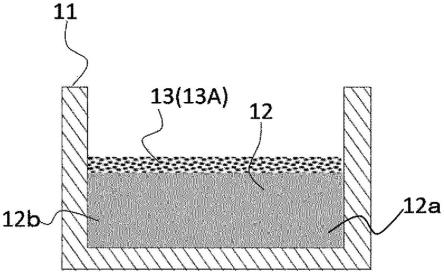
1.本发明涉及金属氮化物的制造方法。
背景技术:
2.氮化硅、氮化铝和氮化硼等金属氮化物由于其烧结体通常具有高导热性、高绝缘性、高强度等优异的特性,因此作为各种工业材料的陶瓷原料备受瞩目。作为金属氮化物的制造方法,已知有直接氮化法、还原氮化法等各种方法。例如,在氮化硅的情况下,已知有如下方法:以二氧化硅粉末为原料,在碳粉末存在下使氮气流通而生成氮化硅的还原氮化法(例如专利文献1)、使金属硅(硅粉末)与氮在高温下反应的直接氮化法(例如专利文献2)、使卤化硅与氨反应的酰亚胺分解法等。
3.另外,还已知有通过利用自燃烧法(self-propagating high temperature synthesis,shs法,以下也称为燃烧合成法)的直接氮化法来合成金属氮化物的方法。其是将含有硅粉末、铝粉末、硼粉末等金属粉末的原料粉末导入反应容器内,在氮气气氛下灼热引燃原料粉末的一部分而产生氮化反应,使由该氮化反应产生的氮化燃烧热传递到周围而使整体发生反应的合成法。例如,在专利文献3中记载了将填充有金属粉末的碳制坩埚置于反应容器内,在加压氮气气氛中,通过向金属粉末表面照射yag激光而将其引燃,然后通过自放热进行燃烧合成反应,得到微细粉末的产物。
4.由于燃烧合成法不需要点火以外的外部加热手段来启动反应,因此能够简化设备并削减投入能量。另外,由于反应本身是与直接氮化法相同的放热反应,因此反应温度容易变高,因此生成的金属氮化物热粘,以块状物的形态得到。以块状物得到的金属氮化物需要另行粉碎或解碎。如此一来,在燃烧合成法中,反应急剧进行,反应温度容易变高,因此,有时金属氮化物的热粘过度进行,难以形成致密的烧结体,或者由于作为原料的金属粉末熔化和热粘,有时会残留大量的未反应物。因此,还公开了使用稀释剂使燃烧反应温和进行的技术(专利文献4)。现有技术文献
5.专利文献专利文献1:日本特开2009-161376号公报专利文献2:日本特开平10-218612号公报专利文献3:日本特开2000-264608号公报专利文献4:wo2018/110565号公报
技术实现要素:
发明要解决的课题
6.然而,在上述燃烧合成法中,无论是否使用稀释剂,都会残留一定量的作为原料的未反应金属粉末。因此,金属氮化物的收率降低,并且纯度降低,进而,由于含有大量未反应
的金属粉末,因此还担心金属氮化物的烧结体的性能降低。在金属氮化物中,特别是在制造氮化硅的情况下,由于硅与氮气的反应性低,因此未反应的金属粉末残留的问题显著。解决问题的手段
7.本发明人等针对这样的未反应金属粉末残留的问题进行了研究,结果发现,在反应容器内生成的金属氮化物的块状物中,特别是在最上部形成的块状物的表面残留特异性未反应的金属粉末。而且,反应容器内的含有金属粉末的原料粉末层的表面温度与气氛温度之差较大,原料粉末的表面温度上升不充分,氮化反应难以进行,结果,预测在块状物的表面残留未反应的金属粉末。本发明人等基于上述见解和预测进行了进一步的研究,结果发现,通过在原料粉末层的表面上形成隔热层,以防止反应容器内的原料粉末层表面的温度降低,能够减少上述未反应物的量,从而完成了本发明。
8.本发明的主旨为以下的[1]~[7]。[1]金属氮化物的制造方法,其是在氮气气氛下,引燃反应容器中填充的含有金属粉末的原料粉末,使通过所述金属的氮化反应产生的氮化燃烧热传递到所述原料粉末整体,由此制造所述金属的氮化物的方法,其特征在于,在由所述原料粉末构成的层的上表面上形成隔热层,所述隔热层具有氮透过性且由对氮化反应惰性的材质构成。[2]如上述[1]所述的金属氮化物的制造方法,其中,所述隔热层由与所述金属粉末相同的金属元素的氮化物粉末形成。[3]如上述[1]或[2]所述的金属氮化物的制造方法,其中,所述原料粉末含有稀释剂,所述稀释剂由与所述金属粉末相同的金属元素的氮化物粉末构成。[4]如上述[1]~[3]任一项所述的金属氮化物的制造方法,其中,所述金属粉末为硅粉末。[5]如上述[1]~[4]任一项所述的金属氮化物的制造方法,其中,进一步在构成所述反应容器的内壁的至少一个表面上形成保护层,所述保护层由对氮化反应惰性的材质构成。[6]如上述[5]所述的金属氮化物的制造方法,其中,所述保护层形成于所述反应容器的底面。[7]如上述[5]或[6]所述的金属氮化物的制造方法,其中,所述保护层形成于所述反应容器的侧面。发明效果
[0009]
根据本发明,能够提供一种在通过燃烧合成法制造金属氮化物时,能够减少未反应的金属粉末的量的方法。
附图说明
[0010]
[图1]是说明本发明的金属氮化物的制造方法的一实施方式的截面图。[图2]是说明本发明的金属氮化物的制造方法的另一实施方式的截面图。[图3]是说明本发明的金属氮化物的制造方法的另一实施方式的截面图。[图4]是说明本发明的金属氮化物的制造方法的另一实施方式的截面图。
[图5]是说明本发明的金属氮化物的制造方法的另一实施方式的截面图。[图6]是说明本发明的金属氮化物的制造方法的另一实施方式的截面图。[图7]是说明本发明的金属氮化物的制造方法的另一实施方式的截面图。[图8]是说明本发明的金属氮化物的制造方法的另一实施方式的截面图。
具体实施方式
[0011]
《金属氮化物的制造方法》本发明是一种金属氮化物的制造方法,其是在氮气气氛下,引燃反应容器中填充的含有金属粉末的原料粉末,使通过所述金属的氮化反应产生的氮化燃烧热传递到所述原料粉末整体,由此制造所述金属的氮化物的方法,其特征在于,在由所述原料粉末构成的层的上表面上形成隔热层,所述隔热层由具有氮透过性且对氮化反应惰性的材质构成。在形成所述隔热层后,引燃原料粉末,通过燃烧合成法制造金属氮化物时,能够减少未反应的金属粉末的量。作为本发明中用作原料的金属粉末,例如可举出:硅粉末、铝粉末、硼粉末等。另外,根据该金属粉末的种类而得到金属氮化物,若金属粉末为硅粉末,则得到氮化硅(si3n4);若金属粉末为铝粉末,则得到氮化铝(aln);若金属粉末为硼粉末,则得到氮化硼(bn)。予以说明,详情如后所述,通过燃烧合成法得到的金属氮化物通常以块状物得到,将该块状物粉碎成粉末状的金属氮化物,将其烧成而得到烧结体。
[0012]
图1是示意性地表示本发明的金属氮化物的制造方法的一实施方式的截面图。具体而言,是表示使含有金属粉末的原料粉末在反应容器中反应的一实施方式的截面图。予以说明,本发明不限定于附图的内容。在反应容器11的内部填充含有金属粉末的原料粉末,形成由原料粉末构成的层12(以下也称为原料粉末层12)。
[0013]
反应容器11设置在未图示的密闭式的反应器内,在进行燃烧合成时,将反应器内调节为氮气气氛。反应容器11是耐热性容器,例如可适宜使用碳制容器等。通过点燃填充在反应容器11内部的原料粉末层12的一端12a,原料粉末中含有的金属粉末的氮化反应开始,通过该氮化反应产生的氮化燃烧热朝着另一端12b传递到原料粉末整体,生成金属氮化物。在此,作为金属粉末,优选可举出硅粉末、铝粉末、硼粉末等,作为金属氮化物,可举出:作为上述金属粉末的氮化反应产物的氮化硅、氮化铝、氮化硼等。予以说明,为了使氮化反应更温和地进行,如后所述,在原料粉末中除了金属粉末以外还可以含有稀释剂。
[0014]
(隔热层)本发明中,在原料粉末层12的上表面上形成有隔热层13。通过在原料粉末层12的上表面上形成隔热层13,能够防止原料粉末层12的表面的温度降低,促进氮化反应,并减少金属粉末的未反应物的量。特别是在使用硅作为金属粉末来制造氮化硅的情况下,反应温度变高(1500~2500℃左右),因此原料粉末层12的表面与层内部的温差变大,存在表面出现更多金属粉末的未反应物的倾向。因此,在利用燃烧合成法,使用硅作为金属粉末生成氮化硅的情况下,更能显著发挥本发明的效果。
[0015]
隔热层13只要形成在原料粉末层12的上表面上即可,既可以紧贴地形成在原料粉
末层12上,也可以与原料粉末层12之间留有间隙地形成。从有效抑制表面温度降低的观点考虑,隔热层13优选与原料粉末层12紧贴地形成。予以说明,当原料粉末层12与隔热层13之间留有间隙时,该间隙优选为10mm以下,更优选为5mm以下。
[0016]
在此,隔热层13具有氮透过性且由对氮化反应惰性的材质构成。通过具有氮透过性,氮气不会被隔热层13阻断,因此不会阻碍存在于隔热层13下部的原料粉末的氮化反应。具有氮透过性是指以至少不阻碍原料粉末的氮化反应的程度让氮透过。例如,如后所述,当隔热层由粉末形成时、当隔热层为多孔板时、当隔热层使用毛毡或布时等的情况下,隔热层具有氮透过性。另外,由于隔热层13是对氮化反应为惰性的材质,因此能够防止隔热层13的劣化,并且能够防止来自隔热层13的反应物的杂质混入制造对象物的金属氮化物中。
[0017]
隔热层13只要具有上述性质,可以是纤维状、粉体状、板状等的任意形态,另外,其材质也没有特别限定,可以是金属制,也可以是陶瓷制。其中,隔热层13优选由与原料粉末中含有的金属粉末相同的金属元素的氮化物粉末形成。具体而言,若作为原料的金属粉末为硅粉末,则隔热层13优选由氮化硅形成,若金属粉末为铝粉末,则隔热层13优选由氮化铝形成,若金属粉末为硼粉末,则隔热层13优选由氮化硼形成。由此,能够在使原料粉末发生氮化反应而生成金属氮化物后,无需除去隔热层而与隔热层一起进行粉碎、烧结等后续工序。另外,当然,由与金属粉末相同的金属元素的氮化物粉末形成的隔热层相当于由对氮化反应为惰性的材质构成的隔热层。因此,能够防止隔热层的劣化,同时防止在生成的金属氮化物中混入来自隔热层的杂质。
[0018]
隔热层13只要形成于原料粉末层12的上表面的至少一部分上即可,但从提高隔热(绝热)效果的观点考虑,隔热层13优选以覆盖原料粉末层12的表面积的90%以上、更优选95%以上的方式形成,特别优选以覆盖原料粉末层12的整个表面的方式形成。
[0019]
隔热层13的厚度优选按照隔热层13由粉末形成或者为板状等隔热层的形态来适当调整,例如为5~30mm,优选为10~30mm。当为上述下限值以上时,隔热效果提高,当为上述上限值以下,氮透过性良好。
[0020]
隔热层13例如可举出由粉末形成的隔热层13a、板状隔热层13b、由多孔板制成的隔热层13c等。以下,分别对它们进行说明。
[0021]
如图1所示,隔热层13优选为由粉末形成的隔热层13a。通过由粉末形成隔热层,能够容易地具有氮透过性,能够使存在于隔热层下部的原料粉末的氮化反应容易地进行。形成隔热层13a的粉末可以为粉体状,也可以为颗粒状。该粉末的平均粒径没有特别限定,优选为0.1~100μm,更优选为0.5~20μm。予以说明,平均粒径是指通过激光衍射/散射法粒度分布测定装置进行的粒径分布测定所测得的粒径分布的累积曲线为50%的粒径(平均粒径d50)。从隔热性和氮透过性这两者均良好的观点考虑,由粉末形成的绝热层13a的体积密度优选为0.3~1.5g/cm3,更优选为0.3~1g/cm3。另外,由粉末形成的隔热层13的氮透过性高,因此能够形成得比较厚,相应地隔热效果也得以提高。从这样的观点考虑,由粉末形成的隔热层13的厚度例如为5~30mm,优选为10~30mm。
[0022]
如图2所示,隔热层也可以是板状的隔热层13b。将板状的隔热层13b设置于原料粉
末层12的上表面上或者在氮化反应后除去的操作容易,处理性优异。作为板状的隔热层13b,例如可以使用将金属氮化物的粉体烧成而形成的烧结体等。予以说明,在图2中,板状的隔热层13b由一块板状的成型体形成,但不限定于此,例如,可以准备多个尺寸更小的板状成型体,将它们并排而形成板状的隔热层13b。
[0023]
如图3所示,隔热层也可以是由多孔板构成的隔热层13c。在图3所示的多孔板上设置有多个从板的一面贯通至另一面的孔15,因此氮透过性优异。孔15的形状没有特别限定,作为孔15的截面形状,例如可举出:圆形、椭圆形、四边形等多边形等。另外,由于只要具有氮透过性就可以用作隔热层,因此可以将多孔质烧结体用作多孔板。多孔质烧结体具有多个气孔,可根据气孔率来调节氮透过性。多孔板的表观气孔率优选为50~80%,更优选为60~75%。当多孔板的表观气孔率为这些下限值以上时,氮透过性提高,当为这些上限值以下时,则隔热层的隔热性可确保为一定以上。表观气孔率可通过使用水的阿基米德法测定,当将多孔板的干燥重量设为w1、将多孔板在水中的重量设为w2、将使多孔板含有水并除去了表面的过剩水分后的多孔板在空气中的重量设为w3时,可通过下式求出。表观气孔率(%)=100
×
(w3-w1)/(w3-w2)
[0024]
(保护层)本发明中,优选在构成反应容器的内壁的至少一面上形成保护层。由此,能够抑制反应容器的劣化,还能够防止构成反应容器的材料与原料粉末的副反应。除此以外,通过形成保护层,能够进一步减少金属粉末的未反应物。保护层16由对氮化反应惰性的材质形成。保护层16只要具有这样的性质,就可以是纤维状、粉体状、板状等任意形态,另外,其材质也没有特别限定,可以是金属制,也可以是陶瓷制。其中,保护层16优选由与原料粉末中含有的金属粉末相同的元素的氮化物粉末形成。由此,在氮化反应结束后,作为产物的金属氮化物和保护层16可以不分离而直接一起粉碎,得到烧结体等的原料。作为在原料粉末层12和反应容器的内壁的至少一个表面上形成保护层的方式,例如可举出:如图4所示在反应容器的底面形成保护层16的方式、如图5所示在反应容器的侧面形成保护层16的方式等。另外,从更有效地防止反应容器的劣化的观点考虑,如图6所示,优选在反应容器的底面与反应容器的侧面两面这两者上均设置保护层16。予以说明,在将保护层16设置于反应容器的侧面时,既可以设置于反应容器的一部分侧面,也可以设置于反应容器的全部侧面,但从防止反应容器的劣化的观点考虑,优选设置于反应容器的全部侧面。
[0025]
保护层可以如图4~6所示由粉末形成,也可以如图7所示由板状的成型体形成。另外,保护层不一定都采用相同的形态,例如,如图8所示,设置于反应容器的底面的保护层可以由粉末形成,设置于反应容器的侧面的保护层可以由板状的成型体形成,反之亦可。
[0026]
保护层的厚度优选为5~30mm,更优选为10~30mm。当保护层的厚度为这些下限值以上时,容易防止反应容器的劣化,当为这些上限值以下时,可增加反应容器内的原料粉末的体积,使得到的金属氮化物的量增多。
[0027]
(原料粉末)
本发明中,原料粉末含有金属粉末。作为金属粉末,可举出:硅粉末、铝粉末、硼粉末等。本发明中,特别优选硅粉末。
[0028]
另外,用作原料粉末的上述金属粉末的平均粒径没有特别限定,平均粒径d50优选在1~100μm的范围。当原料粉末为硅粉末时,平均粒径d50优选为1~10μm,当原料粉末为铝粉末时,平均粒径d50优选为5~100μm,当原料粉末为硼粉末时,平均粒径d50优选为5~50μm。
[0029]
另外,用作原料粉末的金属粉末优选为高纯度的金属粉末。例如,当金属粉末为硅粉末时,al、fe的含量分别优选为200ppm以下。另外,当金属粉末为铝粉末时,si、fe的含量分别优选为200ppm以下。进而,当金属粉末为硼粉末时,fe的含量优选为200ppm以下。当存在这样的金属元素时,可能存在以下情况:得到的金属氮化物的烧结性降低,而且得到的烧结体的强度等特性降低。基于同样的理由,w、mo等高熔点金属的含量也适宜为200ppm以下。
[0030]
金属粉末优选预先将其粉末表面适度氧化。即,这是因为金属粉末表面形成的氧化膜是适当控制燃烧合成反应进行的重要因素。作为适度氧化表面的方法,可简单地采用在空气中粉碎至上述粒径范围的方法。例如,适宜采用使用空气的气流粉碎机等。上述金属粉末的氧化程度可以在不阻碍本发明燃烧合成反应的范围内适当确定,但相对于金属粉末的重量,优选以0.1~1质量%左右的量含有氧。当金属粉末中的氧量低于上述范围时,氮化反应时燃烧温度有过度升高的倾向,另外,当氧量超过该范围时,存在氮化反应被抑制的倾向,有时发生引燃不良或未反应金属残留等的问题。
[0031]
本发明中,用作原料粉末的上述那样的金属粉末可以是以何任意方法得到的金属粉末,但优选将纯度和粒径调整在上述规定的范围内。例如,当金属粉末为硅粉末时,一般来说,将半导体多晶硅棒破碎制造金属块(nugget)的过程中产生的微粉回收利用是经济的。
[0032]
原料粉末可以含有稀释剂。金属粉末与氮的反应为放热反应,表面反应为限速(rate-determining)反应,因此金属粉末的量越多,越难以控制原料粉末的温度。但是,通过使原料粉末含有稀释剂,原料粉末中的金属粉末的含量减少,原料粉末的放热也减少。而且,原料粉末的温度控制变得容易。在金属粉末反应而生成金属氮化物后,为了不从生成的金属氮化物中除去原料粉末中含有的稀释剂,稀释剂优选为与金属粉末相同的金属元素的氮化物粉末。例如,当金属粉末为硅粉末时,原料粉末中含有的稀释剂优选为氮化硅,当金属粉末为铝粉末时,原料粉末中含有的稀释剂优选为氮化铝,当金属粉末为硼粉末时,原料粉末中含有的稀释剂优选为氮化硼。作为这些稀释剂,例如可以使用通过本发明的金属氮化物的制造方法制造的金属氮化物。
[0033]
当原料粉末中含有稀释剂时,稀释剂的含量相对于原料粉末的总量基准,例如可以为5~80质量%左右。稀释剂的含量优选根据原料粉末的种类而适当调整,例如当原料粉末为硅粉末时,稀释剂的含量相对于原料粉末的总量基准,优选为5~50质量%,更优选为10~30质量%。当原料粉末为铝粉末或硼粉末时,稀释剂的含量相对于原料粉末的总量基准,优选为10~80质量%,更优选为30~80质量%。当稀释剂的含量为这些下限值以上时,原料粉末的
放热降低,温度的控制变得容易。当稀释剂的含量为这些上限值以下时,能够使金属的氮化燃烧热量容易地传递到反应容器内填充的原料粉末整体中。
[0034]
在不阻碍本发明效果的范围内,原料粉末中可以含有金属粉末以及根据需要使用的稀释剂以外的其他成分。作为其他成分,例如可举出:氯化钠、氯化铵等氯化物,氧化钙、氧化钇、氧化镁等氧化物等。以原料粉末的总量为基准,其他成分优选为10质量%以下,更优选为5质量%以下,进一步优选为1质量%以下,更进一步优选为0质量%。
[0035]
(引燃(点火)及燃烧合成法的条件)上述的原料粉末填充在反应容器(setter)中。反应容器优选为陶瓷制、石墨制等耐热性的反应容器。反应容器内的原料粉末层的体积密度优选设定在0.3~1.0g/cm3的范围。通过调整至这样的体积密度进行点火而使燃烧反应进行,抑制未反应物的残留,使整个原料粉末容易反应。原料粉末层的体积密度可以通过原料粉末的平均粒径和在氮气置换中供给的氮气压力等来调节。
[0036]
另外,在燃烧合成法时,可以向成为引燃点的部分预先添加含有ti、al等粉末的引燃剂。当然,这种引燃剂的量应该是不影响所得金属氮化物的烧结性程度的少量。在配置引燃剂时,可以配置在原料粉末层的端部、中央部或任意位置,可以配置在单个或多个部位上。如上所述,将原料粉末填充于反应容器后,对反应容器内进行氮气置换,在氮气气氛下引燃原料粉末。一般来说,上述反应容器设置在具有点火装置和气体供给/排出机构的耐压性密闭式反应器内,在对反应器内减压而除去空气后,供给氮气进行氮气置换。
[0037]
本发明中,反应既可以在常压下进行,也可以在加压下进行,优选在加压下进行。特别是在进行作为金属氮化物得到氮化硅的反应时,从容易进行氮化反应的观点考虑,优选在加压下进行。具体地,优选在常压~1mpa的压力下进行,该压力通过供给到所述密闭式反应器的氮气压力来实现。当密闭式反应器的压力小于上述范围时,存在在反应过程中熄火等而导致未反应物变多、收率下降的倾向。另外,当密闭式反应器的压力大于上述范围时,存在以下倾向:反应温度过度上升而导致生成粗大的硅的块状物,使最终得到的氮化硅粉末含有大量难以粉碎的粗大颗粒,难以确保适当的粒度分布。
[0038]
本发明中,优选如下方法:将填充在反应容器中的原料粉末点燃(点火,引燃),在用氮气加压的状态下,即100kpag~1mpag的氮气气氛下,通过自燃烧扩散,使金属粉末直接反应。点火(点燃,引燃)可以通过以往公知的方法进行,例如可以采用以下方法:通过使用安装在密闭式反应器中的一对电极的电弧放电来点火,通过对碳制或金属制的加热器进行通电加热来点火,通过激光照射来点火等。
[0039]
(粉碎)本发明中,通过如上述那样实施燃烧合成反应,得到由金属氮化物构成的块状产物。该块状产物可通过后述的机械粉碎而制成具有适当粒度分布的金属氮化物粒子。
[0040]
本发明中,通过对通过上述燃烧合成反应得到的块状产物进行机械粉碎,能够得到具有适当粒度分布的金属氮化物粉末。该机械粉碎优选通过干式粉碎进行。对于使用水
等液体介质的湿式粉碎来说,由于均匀地施加粉碎压力,因此在得到微细的粉末方面是有利的。但是,湿式粉碎的生产率低。另外,存在金属氮化物与液体介质反应而产生杂质的可能性,在粉碎后需要通过酸处理等的精制来除去杂质。而且,为了不增加环境负荷,需要对酸处理废液进行处理,导致粉碎的成本进一步提高。因此,通过本发明的上述反应得到的块状产物优选通过干式粉碎进行粉碎。可以将块状产物以不同的粉碎条件进行多次粉碎,准备粒度分布不同的多种粉碎物,将它们适当混合,也能够得到具有适当粒度分布的金属氮化物的粉末。另外,通过导入筛分等分级工序,也能够得到具有适当粒度分布的金属氮化物的粉末。
[0041]
这样的干式粉碎使用振动粉碎机、珠磨机、使破碎对象物相互碰撞的气流粉碎机(喷射磨机)等粉碎机来进行。作为抑制粉碎时的重金属类污染的不言而喻的对策,是将金属氮化物的共用材料作为粉碎介质的方法。例如,使用气流粉碎机的气流粉碎由于能够通过粉末相互之间的碰撞来粉碎,因此从防止污染的观点考虑是最佳的。另外,即使是使用振动粉碎机或珠磨机的方法,只要使用作为共用材料的金属氮化物制的球作为粉碎介质,就没有污染问题。此时,由于粉碎介质也会有磨损,即使是微量的,因此很明显应该利用污染物少的介质。
[0042]
关于用作粉碎介质的金属氮化物球的制作,单独使用金属氮化物获得耐磨烧结体的方法的成本高,因此为了以低成本制作介质,可以采用混合氧化钇、氧化镁、氧化铝等烧结助剂来烧结的方法。对于这些烧结助剂的选择,只要选择目标的金属氮化物粉末所允许的成分,则作为制作烧结体用的金属氮化物粉末的方法就没有问题。予以说明,在以干式使用振动粉碎机或珠磨机粉碎金属氮化物粉末时,适宜采用添加微量的乙醇、异丙醇等醇类或水等来进行粉碎的方法。这些成分起促进粉碎的粉碎助剂的作用,因此能够缩短粉碎时间。关于粉碎助剂的添加量,以使粉碎物能够维持干燥状态的范围的量来添加。其量根据粉碎助剂的成分而不同,但相对于粉碎的金属氮化物粉末,适宜为0.1~2质量%的范围。
[0043]
(金属氮化物烧结体的制造)使用如上所述得到的金属氮化物的粉末,可以通过公知的方法制造金属氮化物烧结体。例如,当金属氮化物粉末为氮化硅粉末时,在氮化硅粉末中混合氧化钇、氧化镁、氧化锆、氧化铝等烧结助剂,通过压制成型,制作体积密度为1.7g/cm3以上、优选1.85g/cm3以上、更优选1.95g/cm3以上的成型体,接着通过进行烧成,能够得到烧结体。
[0044]
上述压制成型代表性的是单轴压制成型,优选采用在单轴压制成型后进行cip(cold isostatic pressing,冷等静压)成型的方法。
[0045]
另外,烧成在氮气气氛中在1700~2000℃下进行。烧结体的密度取决于烧成温度和烧成时间这两者。例如在1700℃烧成时,烧成时间为3~20小时左右。烧成温度和烧成时间可根据金属氮化物的种类等而适当设定。例如,在氮化硅的情况下,在1850℃以上的温度烧成时,烧成时间过长时,有时由于氮化硅本身的分解而导致烧结体的密度下降。在这种情况下,通过在用氮气加压的气氛下烧结,能够抑制氮化硅烧结体的分解。该氮气压力越高,越能抑制氮化硅的分解,但从装置的耐压性能等经济上的理由考虑,适宜采用小于1mpa的压力。为了得到相对密度为99%以上的高密度的烧结体,适宜在1800℃以上的加压氮气
气氛下进行烧成。以如上所述那样得到的金属氮化物烧结体可适用于散热用基板材料等。实施例
[0046]
以下,为了更具体地说明本发明示出了实施例,但本发明并不限定于这些实施例。予以说明,在实施例中,各种物性的测定通过如下方法进行。
[0047]
(1)未反应物的量的测定按如下所述测定将各实施例、比较例中制造的块状产物粉碎后的氮化硅粉末中的未反应物的量(未反应的硅量)。制作改变了氮化硅粉末和硅粉末的比例的氮化硅粉末和硅粉末的混合粉末,然后测定该混合粉末的x射线衍射图,根据测得的x射线衍射图中的氮化硅和硅的峰强度比制作校准曲线。然后,分别测定实施例和比较例的氮化硅粉末的x射线衍射图,根据测得的x射线衍射图中的氮化硅和硅的峰强度比,基于上述校准曲线,计算出未反应物的量(未反应硅的量)。(2)反应容器的劣化对各实施例、比较例中进行20次同样的燃烧合成反应后的反应容器的劣化,通过反应容器的底面和侧面的目测观察,按照以下基准进行评价。a:未观察到反应容器的劣化。b:在反应容器的侧面和底面的任一者上观察到劣化。c:在反应容器的侧面和底面均观察到劣化。
[0048]
(3)氮化硅粉末的粒径(i)样品的前处理作为样品氮化硅粉末的前处理,将氮化硅粉末在空气中在约500℃的温度下进行2小时的烧成处理。在上述烧成处理中,对于粒径测定而言,存在以下情况:氮化硅粉末的表面氧量少,或者由于粉碎时的粉碎助剂等而导致粒子表面被疏水性物质覆盖,粒子本身呈疏水性,在这种情况下,存在在水中的分散不充分,再现性的粒径测定变得困难的情况。因此,通过将样品氮化硅粉末在空气中在200℃~500℃左右的温度下进行数小时的烧成处理,向氮化硅粉末赋予亲水性,使之容易分散在水溶剂中,能够进行再现性高的粒径测定。此时确认,即使在空气中烧成(烧制),也几乎不影响测定的粒径。
[0049]
(ii)粒径的测定在最大100ml的具有标线的烧杯(内径60mmφ,高70mm)中加入90ml水和浓度5质量%的焦磷酸钠5ml,充分搅拌后,投入约一耳勺的样品氮化硅粉末,通过超声波均质器((株)日本精机制作所制us-300e,芯片直径26mm)以振幅(amplitude)50%(约2安培)使氮化硅粉末分散2分钟。予以说明,将上述芯片的前端插入至烧杯的20ml标线的位置进行分散。接着,对得到的氮化硅粉末的分散液,使用激光衍射/散射法粒度分布测定装置(microtrac-bel公司制的microtrac mt3300exii)测定粒度分布。测定条件如下:溶剂选择水(折射率1.33),粒子特性选择折射率为2.01,粒子透过性选择透过,粒子形状选择非球形。将通过上述粒径分布测定所测得的粒径分布的累积曲线为50%的粒径作为平均粒径(平均粒径d50)。
[0050]
(4)β化率进行使用cukα射线的粉末x射线衍射(xrd)测定,通过“c.p.gazzara and d.r.messier:ceram.bull.,56(1977),777-780”中记载的方法,计算氮化硅粉末的α相与β相的重量比例。
[0051]
(5)bet比表面积制造好的氮化硅粉末的比表面积使用mountech公司制的bet法比表面积测定装置(macsorb hm型号-1201),使用基于氮气吸附的单点bet法测定。予以说明,在进行上述的比表面积测定之前,预先将待测定的氮化硅粉末在空气中在600℃下热处理30分钟,以除去吸附于粉末表面的有机物。
[0052]
(6)铝元素和铁元素的含量硅粉末中的杂质浓度按如下所述测定。将供于燃烧合成反应的硅粉末称量到树脂制容器中,添加70%浓度的高纯度浓硝酸。一边滴加50%浓度的高纯度氢氟酸,一边注意不要使硅的分解反应过于剧烈,当硅粉末完全溶解后,使树脂制容器中残留的硝酸和氢氟酸的混合酸在加热板上完全蒸发,将吸附于树脂制容器内表面的重金属成分用1%稀硝酸回收得到的溶液通过电感耦合等离子体-原子发射光谱仪(icp-aes)定量重金属成分。在此,使用“赛默飞世尔科技公司制的icap 6500 duo”。氮化硅粉末中的杂质浓度使用jis r 1603:2007中规定的方法测定。
[0053]
在各实施例和比较例中,使用以下的原料粉末。《原料粉末》(硅粉末)使用施加了氮化硅内衬的气流粉碎装置(气流粉碎机),将太阳能电池应用级别的高纯度多晶硅粉碎至平均粒径约5μm而得到的硅粉末。予以说明,在此得到的硅粉末的氧含量为约0.3质量%。另外,作为杂质的量,fe为10ppm,al为5ppm。(稀释剂)使用平均粒径1μm的氮化硅粉末。
[0054]
《隔热层的材料》(i)使用平均粒径1μm的氮化硅粉末a形成粉体状的隔热层。(ii)使用平均粒径1μm的氮化硅粉末的烧结体b形成板状的隔热层。该烧结体b为厚度10mm的板状,每1cm2设置1个以上以可通气的表里连通的约1mm的孔,作为多孔板。(iii)作为多孔板c,使用以氮化硅为主成分的厚度10mm的多孔质烧结体。该多孔板c的表观气孔率为60%。
[0055]
《保护层的材料》(iv)使用与上述(i)相同的材料形成粉体状的保护层。(v)使用与上述(iii)相同的材料形成板状的保护层。
[0056]
[实施例1]将硅粉末和作为稀释剂的氮化硅粉末混合,得到原料粉末(si:80质量%,si3n4:20质量%)。将该原料粉末填充到反应容器中,形成厚度30mm的原料粉末层。接着,在该原料粉末层的整个表面上层叠上述氮化硅粉末a,形成由粉末构成的厚度10mm的隔热层。接着,将该反应容器设置在具有点火装置和气体供给/排出机构的耐压性密闭式反应器内,将反应
器内减压脱气后,供给氮气进行氮气置换。然后,逐渐供给氮气,使压力上升至0.7mpa。达到规定压力的时间点(引燃时)的原料粉末的体积密度为0.8g/cm3,隔热层的体积密度为0.8g/cm3。然后,引燃反应容器内的原料粉末的端部,进行燃烧合成反应,得到由氮化硅形成的块状产物。将得到的块状产物相互摩擦而解碎至大约5~20μm后,适量投入到振动粉碎机中进行6小时的微粉碎。予以说明,微粉碎机和微粉碎方法使用常规的装置和方法,但作为防止重金属污染的措施,在粉碎机的内部衬有氨基甲酸酯,粉碎介质使用以氮化硅为主要成分的球。另外,在临开始微粉碎之前,添加1质量%的乙醇作为粉碎助剂,将粉碎机设为密闭状态进行微粉碎,得到氮化硅粉末。关于未反应物的量、反应容器的劣化的评价示于表1。所得氮化硅粉末的测定结果示于表2。
[0057]
[实施例2]通过与实施例1同样的方法形成原料粉末层。接着,在该原料粉末层的整个表面上层叠上述的10mm厚的设有可通气的孔的板状氮化硅烧结体b作为隔热层。接着,将该反应容器设置在具有点火装置和气体供给/排出机构的耐压性密闭式反应器内,将反应器内减压脱气后,供给氮气进行氮气置换。然后,逐渐供给氮气,使压力上升至0.7mpa。达到规定压力的时间点(引燃时)的原料粉末的体积密度为0.8g/cm3。然后,引燃反应容器内的原料粉末的端部,进行燃烧合成反应,得到由氮化硅形成的块状产物。将得到的块状产物通过与实施例1同样的方法进行解碎和微粉碎,得到氮化硅粉末。关于未反应物的量、反应容器的劣化的评价示于表1。所得氮化硅粉末的测定结果示于表2。
[0058]
[实施例3]通过与实施例1同样的方法形成原料粉末层。接着,在该原料粉末层的整个表面上层叠由上述氮化硅粉末构成的厚度10mm的多孔板c作为隔热层。接着,将该反应容器设置在具有点火装置和气体供给/排出机构的耐压性密闭式反应器内,将反应器内减压脱气后,供给氮气进行氮气置换。然后,逐渐供给氮气,使压力上升至0.7mpa。达到规定压力的时间点(引燃时)的原料粉末的体积密度为0.8g/cm3。然后,引燃反应容器内的原料粉末的端部,进行燃烧合成反应,得到由氮化硅形成的块状产物。将得到的块状产物通过与实施例1同样的方法进行解碎和微粉碎,得到氮化硅粉末。关于未反应物的量、反应容器的劣化的评价示于表1。所得氮化硅粉末的测定结果示于表2。
[0059]
[实施例4]将硅粉末和作为稀释剂的氮化硅粉末混合,得到原料粉末(si:80质量%,si3n4:20质量%)。向反应容器的底面导入上述的氮化硅粉末a,在整个底面上形成厚度10mm的保护层,然后将上述的原料粉末填充到反应容器中,形成厚度30mm的原料粉末层。接着,在该原料粉末层的整个表面上层叠上述氮化硅粉末a,形成由粉末构成的厚度10mm的隔热层。接着,将该反应容器设置在具有点火装置和气体供给/排出机构的耐压性密闭式反应器内,将
反应器内减压脱气后,供给氮气进行氮气置换。然后,逐渐供给氮气,使压力上升至0.7mpa。达到规定压力的时间点(引燃时)的原料粉末的体积密度为0.8g/cm3,隔热层的体积密度为0.8g/cm3。然后,引燃反应容器内的原料粉末的端部,进行燃烧合成反应,得到由氮化硅形成的块状产物。将得到的块状产物通过与实施例1同样的方法进行解碎和微粉碎,得到氮化硅粉末。关于未反应物的量、反应容器的劣化的评价示于表1。所得氮化硅粉末的测定结果示于表2。
[0060]
[实施例5]将硅粉末和作为稀释剂的氮化硅粉末混合,得到原料粉末(si:80质量%,si3n4:20质量%)。用上述的板状多孔板c覆盖反应容器的整个侧面,从而在侧面形成保护层。进而,向反应容器的底面导入上述的氮化硅粉末a,在整个底面上形成厚度10mm的保护层。然后,将原料粉末填充到反应容器中,形成厚度30mm的原料粉末层。接着,在该原料粉末层的整个表面上层叠上述氮化硅粉末a,形成由粉末构成的厚度10mm的隔热层。将该反应容器设置在具有点火装置和气体供给/排出机构的耐压性密闭式反应器内,将反应器内减压脱气后,供给氮气进行氮气置换。然后,逐渐供给氮气,使压力上升至0.7mpa。达到规定压力的时间点(引燃时)的原料粉末的体积密度为0.8g/cm3,隔热层的体积密度为0.8g/cm3。然后,引燃反应容器内的原料粉末的端部,进行燃烧合成反应,得到由氮化硅形成的块状产物。将得到的块状产物通过与实施例1同样的方法进行解碎和微粉碎,得到氮化硅粉末。关于未反应物的量、反应容器的劣化的评价示于表1。所得氮化硅粉末的测定结果示于表2。
[0061]
[比较例1]将硅粉末和作为稀释剂的氮化硅粉末混合,得到原料粉末(si:80质量%,si3n4:20质量%)。将该原料粉末填充到反应容器中,形成厚度30mm的原料粉末层。接着,将该反应容器设置在具有点火装置和气体供给/排出机构的耐压性密闭式反应器内,将反应器内减压脱气后,供给氮气进行氮气置换。然后,逐渐供给氮气,使压力上升至0.7mpa。达到规定压力的时间点(引燃时)的原料粉末的体积密度为0.8g/cm3。然后,引燃反应容器内的原料粉末的端部,进行燃烧合成反应,得到由氮化硅形成的块状产物。将得到的块状产物通过与实施例1同样的方法进行解碎和微粉碎,得到氮化硅粉末。关于未反应物的量、反应容器的劣化的评价示于表1。
[0062]
[表1]
※
1:底面为粉末,侧面为多孔板
[0063]
[表2]
[0064]
在原料粉末层的表面上形成隔热层,通过燃烧合成反应得到氮化硅的各实施例所示的方法中,观察到未反应物减少。进而可知,通过在反应容器中设置保护层,能够防止反应容器的劣化。与此相比,由比较例1可知,当在不形成隔热层和保护层的情况下进行燃烧合成反应时,未反应物多,且反应容器也劣化。
[0065]
符号说明11
ꢀꢀꢀꢀ
反应容器12
ꢀꢀꢀꢀ
原料粉末层13
ꢀꢀꢀꢀ
隔热层15
ꢀꢀꢀꢀ
孔16
ꢀꢀꢀꢀ
保护层
再多了解一些
本文用于企业家、创业者技术爱好者查询,结果仅供参考。