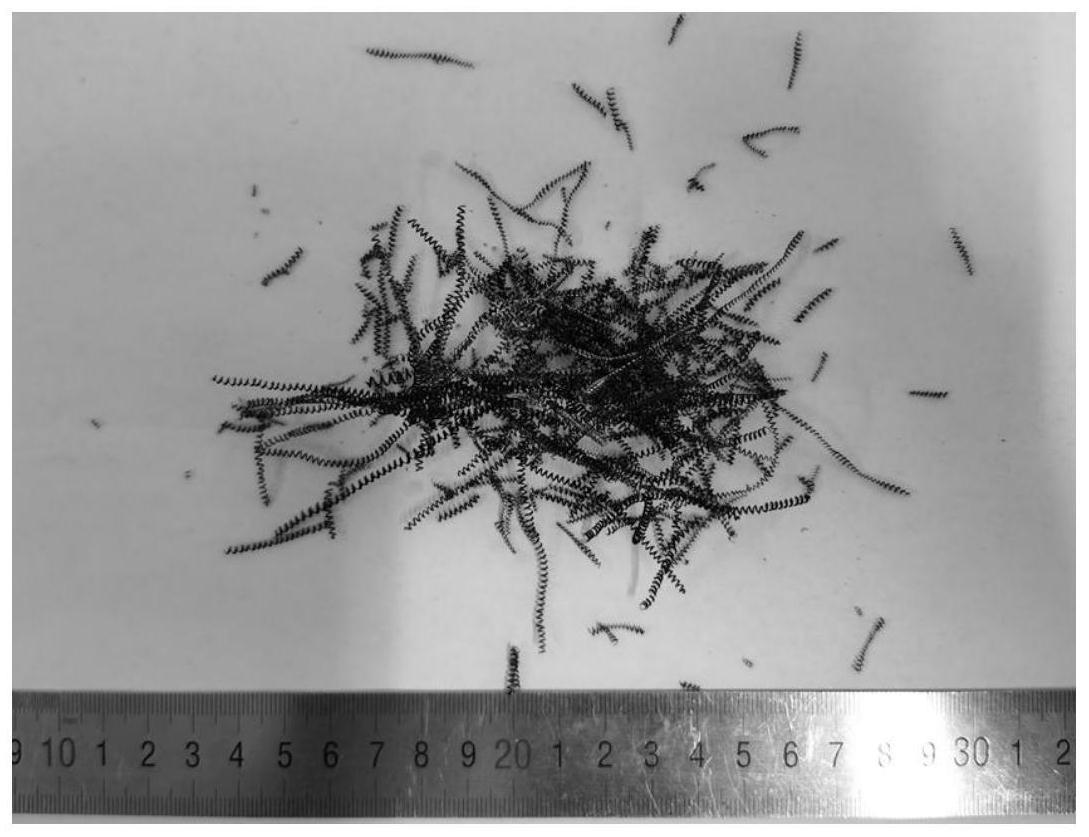
1.本技术属于钢铁冶金领域,具体涉及一种含碲易切削模具钢及其制备方法。
背景技术:
2.模具是工业产品批量生产中最为有效的工具,是工业生产中的重要工艺装备,在电子、汽车、电机、电器、仪器、仪表、家电和通信等产品中,60%~80%的零部件都要依靠模具成形。用模具生产制件所具备的高精度、高复杂程度、高一致性、高生产率和低消耗,是其他加工制造方法所不能替代的。
3.为了满足高精且复杂的产品需求,模具往往需具备复杂的型腔,模具用钢在车、铣及钻等机加工时,需开大量的孔、洞和槽等,这就使得所需材料具备一定的切削性能和加工性能。
4.模具用钢中含有大量的c、cr、mo及v等合金元素,其硬度值非常高,经过预硬处理以后,硬度可达38~40hrc。为改善钢铁材料的切削加工性能,传统工艺通常采用加入硫等易切削元素来提高材料的切削性能和表面加工质量,硫可与钢中的锰结合形成硫化锰,纯mns的熔点为1610℃,具有良好的高温塑性,在钢中起到中断基体连续性和应力集中的作用,在切削加工过程中,当刀刃碰到硫化锰夹杂时很容易产生显微裂纹,使切屑易于折断,此外,还起到润滑刀具的作用。但钢中的mns相具有热脆性,会降低材料的热塑性。在模具钢领域,硫化锰引起的热脆性尤为显著,严重降低材料的服役寿命。因此,模具钢中的硫含量应尽可能低,但模具钢的加工性能又是其重要性能之一,这成为了模具钢应用中的一对矛盾,如何保证模具钢在具备高温强度、良好塑韧性的同时,还具备良好的加工性能,是目前企业所面临的难题。
5.碲位于元素周期表中第六主族硒和钋之间,熔点为452℃,沸点为1390℃,被誉为“现代工业、国防与尖端技术的维生素”,它的金属性比氧、硫和硒要强,微量碲中可固溶于硫化物当中,提高硫化物的硬度,当碲含量高时,可形成mn(s,te)或mnte。mnte是本发明中高硬度易切削模具钢的主要易切削相,钢中均匀分布的mnte相能够显著降低切削过程中的切削力,降低被加工件表面粗糙度,延长刀具寿命等。
6.公开号为cn101429625a的中国专利公开了一种高性能热作易切削模具钢,其成分质量百分比为:c:0.33~0.42,mn:0.55~0.75,si:0.80~1.20,mo:1.20~1.60,v:0.80~1.20,cr:4.80~5.50,s、p、pb、se、ca、te或bi的一种或多种0.10~0.15,余铁和不可避免杂质。该高性能热作易切削模具钢具有较好的切削加工性,降低刀具消耗和机加工费用,满足人们对高精度的要求。但此发明中添加一种或多种0.10~0.15%的易切削元素,并未给出具体元素的含量,各元素的相互作用机理不清,且未给出力学性能与切削性能的匹配性,不利于钢性能的综合调控,且多种元素复合添加,增大生产成本和冶炼难度。
7.公开号为cn112760576a的中国专利公开了一种含碲的y1cr13易切削不锈钢及其制造方法,其中mn、s、te质量百分比满足如下关系式:mn/te》40,te/s:0.015~0.15。所述钢种采用电炉
→
aod
→
lf
→
连铸
→
轧制的生产工艺进行生产。此发明生产的不锈钢可有效避
免轧制过程中的劈头开裂现象,产品综合成材率达90%~95%。相比于原工艺下y1cr13易切削不锈钢,所生产的轧材中夹杂物大小和分布更加均匀,钢切削后断屑形貌良好,工件表面粗糙度降低,钢的切削性能也显著提高。但此发明中的钢种对疲劳寿命要求不高,其强度级别明显低于模具钢,仅对切削性能有明显要求,硫含量远高于模具钢所要求的成分范围,进而有关易切削钢中的碲硫比等成分的控制技术,对模具钢中碲含量的控制不具指导意义。
8.公开号为cn102851625a的中国专利公开了一种含碲高性能不锈钢研磨材料,该材料按质量百分比包括下列组分:mn:13.00,cr:11.00~12.00,ni:5.00~6.00,te:0.035~0.08,cu:2.50~3.0,其余为fe及不可避免的微量杂质。此发明材料降低稀缺金属的使用量,使成本进一步降低。另外,te的加入增加钢的延展性,提高加工后的钢的表面亮泽度,不易产生裂痕和裂纹,同时还易于切削和加工,抛光性好,精度高。而且,碲的加入还使得材料具有良好的导热、导电、耐腐蚀、抗高低温、无磁性能。但此发明所述含碲高性能不锈钢,为hafield钢改进钢种,其基体组织仍然主要为面心立方奥氏体,与四方结构马氏体为基体组织的模具钢完全不同,基体组织的不同,对碲含量的控制机理不同,且该钢种为高锰钢,甚至无需考虑mn/te比。
技术实现要素:
9.为了解决现有技术问题,本发明的目的在于克服已有技术存在的模具钢可加工性能不足,提供一种含碲易切削模具钢及其制备方法,兼具良好的高温强度、塑韧性和切削性能,进而满足人们对易切削模具钢的需求。
10.为达到上述目的,本发明采用如下技术方案:
11.一种含碲易切削模具钢,其化学成分及质量百分比为:c:0.37~0.44%,si≤0.60%,mn:0.30~0.78%,cr:12.00~14.00%,p≤0.035%,ni≤0.60%,s:0.001~0.005%,te:0.0005~0.0100%,余量为铁及不可避免的杂质,并且满足:te/s为0.2~3.0;mn/te》50;(cr-16c)
×
te《0.05。
12.优选地,本发明含碲易切削模具钢化学成分及质量百分比为:c:0.38~0.43%,si≤0.50%,mn:0.35~0.78%,cr:12.20~14.00%,p≤0.030%,ni≤0.60%,s:0.001~0.0043%,te:0.0007~0.0100%,余量为铁及不可避免的杂质,并且满足:te/s为0.2~3.0;mn/te》50;(cr-16c)
×
te《0.05。
13.进一步优选地,本发明含碲易切削模具钢化学成分及质量百分比为:c:0.38~0.42%,si:0.35~0.40%,mn:0.37~0.64%,cr:12.35~13.92%,p:0.008~0.012%,ni:0.22~0.55%,s:0.0018~0.0043%,te:0.0007~0.0086%,余量为铁及不可避免的杂质,并且满足:te/s为0.24~2.46;mn/te为74~529;(cr-16c)
×
te为0.005~0.048。
14.更进一步优选地,本发明含碲易切削模具钢化学成分及质量百分比为:c:0.38~0.42%,si:0.38~0.40%,mn:0.42~0.64%,cr:12.35~13.92%,p:0.009~0.012%,ni:0.22~0.38%,s:0.0018~0.0043%,te:0.0025~0.0086%,余量为铁及不可避免的杂质,并且满足:te/s为1.26~2.46;mn/te为74~168;(cr-16c)
×
te为0.017~0.048。
15.优选地,本发明含碲易切削模具钢在钢基体上弥散分布着六方结构的尺寸为1~3μm的易切削相mnte。为保证钢在凝固过程中生成更多的1~3μm,均匀分布的易切削相mnte,
所述元素质量分数比值te/s为0.2~3.0;te/s《0.2时,平均易切削相mnte尺寸小于1μm,切削性能改善不明显;te/s》3.0时,大于3μm大尺寸的易切削相mnte,不利于钢的疲劳强度、韧塑性、耐蚀性等性能。
16.为保证钢在全流程生产及服役过程中,te元素不与fe生成热脆的铁碲化合物,所述mn/te》50。
17.一种本发明含碲易切削模具钢的制备方法,进行电炉冶炼
→
aod精炼
→
lf精炼
→
碲合金化
→
连铸/模铸
→
轧制
→
热处理,包括如下步骤:
18.(1)电炉冶炼:采用废钢或所述含碲易切削模具钢进行机械加工后的返回料作为原料,确保残余元素符合钢中标准要求,将原料进行脱磷预处理,升温达到不低于1550℃时,加造渣剂石灰及发泡剂萤石,吹氧去磷,当温度高于1600℃,磷含量小于0.02%时,采用偏心底方式出钢;
19.(2)aod精炼:将冶炼后得到钢液进行精炼,采用aod精炼分为氧化期和还原期,在氧化期阶段主要向钢液中添加铬铁,并进行不同比例的氩氧混吹脱碳;在还原期阶段,先将氧化性强的渣扒除,再加入铝铁、硅铁进行沉淀脱氧,后期再加入石灰、萤石、硅石造新渣,使渣系碱度保持在2.0~2.5,在整个aod精炼过程中温度需控制在1650~1690℃;
20.(3)lf精炼:在aod精炼结束后,钢包吊至lf工位进行精炼,造碱性白渣,待渣壳熔化后加入发泡剂,渣层用铝粉进行扩散脱氧及扩散脱硫,随后加入碳粉、硅铁、锰铁、铬铁等合金进行成分微调,使钢液达满足成分要求;
21.(4)碲合金化:取样检测达到成分要求后,喂入铁皮包裹的含碲包芯线,包芯线成分fe:80~90%;te:10~20%,并加入硫作为缓释剂,包芯线外径12~14mm,外包裹铁皮厚度0.4~0.6mm,喂线速度120~180m/min,喂线结束后,钢液表面施加碳化稻壳覆盖剂,软吹氩10~15min后,成分温度合格后,吊包上回转台浇注;
22.(5)连铸/模铸:采用连铸或模铸;
23.当采用连铸过程时,采用大方坯连铸;
24.当采用连铸过程时,采用保护渣进行保护浇注,中间包温度控制在1525~1545℃,确保过热度不超过50℃,连铸时,铸坯的方形断面尺寸为150
×
150mm~200
×
200mm,拉速控制在1.2~1.5m/min,稳拉速操作,二冷采用弱冷水,比水量为:0.25~0.40;模铸过程中,保证全程在氩气保护下进行钢液浇注,钢锭模内表面清理干净,坐模时,尾砖眼与模底水扣眼对齐,绝热板装配与帽口下沿平齐,缝隙塞严,等待浇注时钢锭模帽口上用铁板盖严,防止粉尘进入钢锭模,浇注过程保证钢液平稳上升并控制帽口补缩时间,浇注温度控制在1535~1555℃,保证过热度不超过60℃,模铸后进行缓冷,冷却时间不小于12h,模铸开模后,加热至不低于1250℃,然后,开坯得到铸坯方形断面尺寸为150
×
150mm~200
×
200mm的方坯;
25.(6)铸坯/模铸开坯料进行加热及轧制:将方坯在步进式加热炉中在1200~1250℃加热2~3小时,开轧温度为1150~1200℃,终轧温度为850~950℃,单道次压下量≤15%,轧后以1~3℃/s的平均冷却速率缓冷至480~530℃;
26.(7)热处理:将轧制后得到的轧材加热至920~990℃,淬火保温0.5~1.5h,油冷淬火;然后在200~300℃下进行回火处理,回火保温2~5h,然后空冷,获得回火马氏体组织。
27.优选地,在所述步骤(4)中,在lf精炼末期,将铁皮包裹的含碲包芯线喂入钢液中,进行碲合金化。
28.优选地,在所述步骤(7)中,热处理的淬火温度为(920 6500te)~990℃。
29.进一步优选地,在所述步骤(7)中,淬火温度为925~976℃,淬火保温1.0~1.5h;回火温度为255~282℃,回火保温2.5~4.5h。
30.更进一步优选地,在所述步骤(7)中,淬火温度为936~976℃,淬火保温1.0~1.5h;回火温度为255~270℃,回火保温2.5~4.5h。
31.本发明为保证钢热处理时,在淬火前的保温过程中,不形成大尺寸的铬碲化合物》1μm,大尺寸的铬碲化合物会导致局部区域耐腐蚀性能的下降,易发生点蚀,所述(cr-16c)
×
te《0.05。
32.本发明与现有技术相比较,具有如下显而易见的突出实质性特点和显著优点:
33.1.本发明含碲易切削模具钢,基体上弥散分布着易切削相mnte,在车、铣、钻、磨等机加工过程中,切削力明显减小、切削温度下降、断屑性及切屑清理效率提高、表面粗糙度降低、表面质量及抛光性能改善,减小刀具消耗及机加工成本;
34.2.本发明通过添加适量质量分数的碲元素,将钢中的mns夹杂改质为近球形且在钢基体中均匀分布的mn(s,te)和mnte,提高模具材料的强度、韧塑性,获得力学性能与切削性能的良好配合,并且模具的表面光洁度有所提高;
35.3.本发明含碲易切削模具钢喂碲线工艺稳定,喂线过程无剧烈喷溅,碲元素收得率高且稳定。
附图说明
36.图1为本发明实施例1中夹杂物金相照片。
37.图2为本发明对比例1中夹杂物金相照片。
38.图3为本发明实施例2中电解腐刻后基体sem照片。
39.图4为本发明实施例3中电解腐刻后碲化锰立体形貌。
40.图5为本发明实施例4中电解腐刻后碲化锰立体形貌。
41.图6为本发明对比例3中电解腐刻后碲化锰立体形貌。
42.图7为本发明实施例1中车削断屑形貌。
43.图8为本发明实施例2中车削断屑形貌。
44.图9为本发明实施例3中车削断屑形貌。
45.图10为本发明实施例4中车削断屑形貌。
46.图11为本发明对比例1中车削断屑形貌。
47.图12为本发明对比例2中车削断屑形貌。
48.图13为本发明实施例3中钻削钻屑形貌。
49.图14为本发明实施例4中钻削钻屑形貌。
50.图15为本发明对比例1中钻削钻屑形貌。
具体实施方式
51.本发明公开了一种含碲易切削模具钢及其制备方法。本领域技术人员可以借鉴本文内容,适当改进工艺参数实现。特别需要指出的是,所有类似的替换和改动对本领域技术人员来说是显而易见的,它们都被视为包括在本发明。本发明的方法及应用已经通过较佳
实施例进行了描述,相关人员明显能在不脱离本发明内容、精神和范围内对本文所述的方法和应用进行改动或适当变更与组合,来实现和应用本发明技术。
52.下面结合具体实施例,对本发明的实施方式进行进一步说明:
53.一种含碲易切削模具钢化学成分及质量百分比为:c:0.38~0.42%,si:0.35~0.40%,mn:0.37~0.64%,cr:12.35~13.92%,p:0.008~0.012%,ni:0.22~0.55%,s:0.0018~0.0043%,te:0.0007~0.0086%,余量为铁及不可避免的杂质,并且满足:te/s为0.24~2.46;mn/te为74~529;(cr-16c)
×
te为0.005~0.048。
54.一种本实施例含碲易切削模具钢的制备方法,进行电炉冶炼
→
aod精炼
→
lf精炼
→
碲合金化
→
连铸/模铸
→
轧制
→
热处理,包括如下步骤:
55.(1)电炉冶炼:采用废钢或所述含碲易切削模具钢进行机械加工后的返回料作为原料,确保残余元素符合钢中标准要求,将原料进行脱磷预处理,升温达到1550℃时,加造渣剂石灰及发泡剂萤石,吹氧去磷,当温度高于1600℃,磷含量小于0.02%时,采用偏心底方式出钢;
56.(2)aod精炼:将冶炼后得到钢液进行精炼,采用aod精炼分为氧化期和还原期,在氧化期阶段主要向钢液中添加铬铁,并进行不同比例的氩氧混吹脱碳;在还原期阶段,先将氧化性强的渣扒除,再加入铝铁、硅铁进行沉淀脱氧,后期再加入石灰、萤石、硅石造新渣,使渣系碱度保持在2.0~2.5,在整个aod精炼过程中温度需控制在1650~1690℃;
57.(3)lf精炼:在aod精炼结束后,钢包吊至lf工位进行精炼,造碱性白渣,待渣壳熔化后加入发泡剂,渣层用铝粉进行扩散脱氧及扩散脱硫,随后加入碳粉、硅铁、锰铁、铬铁等合金进行成分微调,使钢液达满足成分要求;
58.(4)碲合金化:取样检测达到成分要求后,喂入铁皮包裹的含碲包芯线,包芯线成分fe:80%;te:20%,并加入硫作为缓释剂,包芯线外径13mm,外包裹铁皮厚度0.5mm,喂线速度150m/min,喂线结束后,钢液表面施加碳化稻壳覆盖剂,软吹氩15min后,成分温度合格后,吊包上回转台浇注;
59.(5)连铸/模铸:采用大方坯连铸;
60.进行连铸过程时,采用保护渣进行保护浇注,中间包温度控制在1525~1545℃,确保过热度不超过50℃,连铸时,铸坯的方形断面尺寸为150
×
150mm~200
×
200mm,拉速控制在1.2~1.5m/min,稳拉速操作,二冷采用弱冷水,比水量为:0.25~0.40;模铸过程中,保证全程在氩气保护下进行钢液浇注,钢锭模内表面清理干净,坐模时,尾砖眼与模底水扣眼对齐,绝热板装配与帽口下沿平齐,缝隙塞严,等待浇注时钢锭模帽口上用铁板盖严,防止粉尘进入钢锭模,浇注过程保证钢液平稳上升并控制帽口补缩时间,浇注温度控制在1535~1555℃,保证过热度不超过60℃,模铸后进行缓冷,冷却时间不小于12h,模铸开模后,加热至1250℃,然后,开坯得到铸坯方形断面尺寸为150
×
150mm~200
×
200mm的方坯;
61.(6)铸坯/模铸开坯料进行加热及轧制:将方坯在步进式加热炉中在1200℃加热2.5小时,开轧温度为1170℃,终轧温度为900℃,单道次压下量8~15%,轧后以2℃/s的平均冷却速率缓冷至500℃;
62.(7)热处理:将轧制后得到的轧材加热至925~976℃,淬火保温1.0h,油冷淬火;然后在255~282℃下进行回火处理,回火保温2.5~4.5h,然后空冷,获得回火马氏体组织。
63.为保证mnte以六方结构析出,热处理温度需低于991℃,为保证碲化锰中mn/(fe
cr)》5,淬火温度优选为(920 6500te)℃。
64.以下结合具体的实施例子对上述方案做进一步说明,本发明的优选实施例详述如下:
65.实施例1~实施例4和对比例1~对比例2:
66.本发明相应实施例钢及对比例钢的化学成分见表1:
67.表1.本发明各实施例钢及对比例钢化学成分wt%表
68.元素csimncrpnistete/smn/te(cr-16c)
×
te实施例10.410.350.3713.420.0080.550.00290.00070.245290.005实施例20.380.400.4212.850.0120.380.00180.00251.391680.017实施例30.400.380.5913.920.0090.220.00430.00541.261090.041实施例40.420.390.6412.350.0100.350.00350.00862.46740.048对比例10.400.360.3812.600.0150.240.0032
‑‑‑‑‑‑‑‑
对比例20.430.420.3113.520.0110.410.00650.00120.182580.008对比例30.390.380.5513.180.0090.260.00210.01225.81450.085
69.本发明相应实施例钢及对比例钢的热处理制度见表2:
70.表2.本发明各实施例钢及对比例钢的热处理制度表
71.热处理制度淬火温度/℃保温时间/h回火温度/℃回火时间/h实施例192512822.5实施例293612683实施例395512702.5实施例497612554.5对比例195012902对比例292812852对比例399912722.5
72.力学性能测试采用拉伸试验机,测定每个试样的抗拉强度rm、屈服强度r
p0.2
、断后伸长率a和断面收缩率z。结果如表3所示:
73.表3.本发明各实施例钢及对比例钢力学性能
74.力学性能抗拉强度rm/mpa屈服强度r
p0.2
/mpa断后伸长率a/%断面收缩率z/%实施例1168212808.530实施例2169012908.529实施例3169512849.530实施例4168812859.032对比例1167612818.028对比例2168512908.529对比例3165012617.527
75.采用车床、铣床和钻床三种机床对试样进行
76.在相同机加工参数下,对各组试样测试,测量了车削和铣削后试样的粗糙度,车削力,统计了车屑和钻屑的主要类型,结果如表4所示:
77.表4本发明各实施例钢及对比例钢切削性能
78.机加工车削粗糙度/μm车削力/n主要车屑类型铣削粗糙度ra/μm主要钻屑类型实施例10.783723.7超长螺旋 长螺旋0.673长锥形 短锥形实施例20.625694.1长螺旋0.488短锥形实施例30.588650.4长螺旋 短螺旋0.414锥形实施例40.504605.3短螺旋0.348半锥形对比例10.958758.2超长螺旋0.954长锥形对比例20.822735.5超长螺旋 长螺旋0.658长锥形 短锥形对比例30.498595.8短螺旋0.336半锥形
79.通过上述各实施例和对比例可知,上述实施例含碲易切削模具钢及其制备方法,具体包括:电炉冶炼
→
aod精炼
→
lf精炼
→
碲合金化
→
连铸/模铸
→
轧制
→
热处理。实施例一~实施例四的含碲易切削模具钢力学性能、切削性能明显优于对比例1和对比例2,其中实施例二~实施例四的含碲易切削模具钢力学性能、切削性能更是优于实施例一。上述实施例的含碲易切削模具钢不仅具备良好的力学性能,还具备优异的切削性能和高的表面加工质量。能够降低机加工过程中的切削力及切削温度,提高断屑性及切削加工效率,减少刀具消耗和机加工成本等,满足对高硬度易切削模具钢的加工需求。
80.上面结合附图对本发明实施例进行了说明,但本发明不限于上述实施例,还可以根据本发明的发明创造的目的做出多种变化,凡依据本发明技术方案的精神实质和原理下做的改变、修饰、替代、组合或简化,均应为等效的置换方式,只要符合本发明的发明目的,只要不背离本发明的技术原理和发明构思,都属于本发明的保护范围。
再多了解一些
本文用于企业家、创业者技术爱好者查询,结果仅供参考。