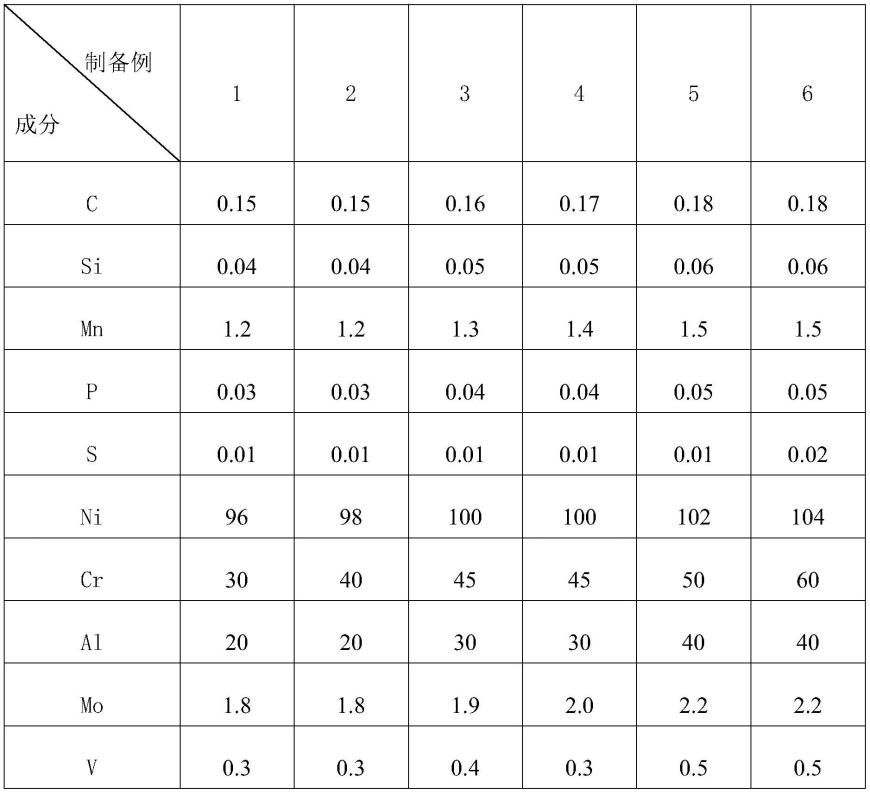
1.本技术涉及精密不锈钢带生产技术领域,更具体地说,它涉及一种短拉丝高光表面精密不锈钢带及其生产方法。
背景技术:
2.精密不锈钢带由于其优良的冲压性能和表面质量,被广泛应用于信息技术、计算机、汽车零部件、医疗、金属软管、半导体等有特殊需求的行业,是一种高附加值的产品,具有非常广阔的市场。因此,如何制得良好性能的精密不锈钢带就成为了行业现阶段主要研究的问题。
3.相关技术中及其生产方法,包括s1、表面抛光;s2、轧制成型;s3、脱脂清洗; s4、拉弯矫处理;s5、检验复卷,且已改善板形的成品卷,可按客户要求的卷重以恒张力进行分小卷,整体操作较为便捷。
4.经上述生产方法制得的精密不锈钢带,其经检测后的机械性能和表面粗糙度均合格,均能满足人们的常规应用,但光泽度普遍较差,x方向仅为180-200gu、y方向仅为 160-180gu,因此,迫切需要提供一种电子行业专用短拉丝高光、表面精密不锈钢带。
技术实现要素:
5.为保障精密不锈钢带力学性能和表面粗糙度的同时,赋予其优良的光泽度,本技术提供一种短拉丝高光表面精密不锈钢带及其生产方法。
6.一种短拉丝高光表面精密不锈钢带,其钢水由如下重量百分比的组分组成:c:0.015-0.018wt.%;si:0.004-0.006wt.%;mn:0.12-0.15wt.%;p:0.003-0.005wt.%;s:0.001-0.002wt.%;ni:9.6-10.4wt.%;cr:3.0-6.0wt.%;al:2.0-4.0wt.%;mo:0.18-0.22wt.%;v:0.03-0.05wt.%;ti:0.02-0.03wt.%;余量为fe和不可避免的杂质。
7.通过采用上述技术方案,由上述组分钢水制得的短拉丝高光表面精密不锈钢带,具有优良的力学性能和表面光泽度,其屈服强度为280-320mpa、粗糙度ra为0.06-0.12um;且光泽度较强,其x方向高达320-380gu、y方向高达280-350gu;分析其原因可能是由于上述组分所构成的奥氏体较为稳固,且适量添加的ni、cr、
al、 mo、v、ti元素,可在钢带表面经钝化/氧化形成嵌合的复合钝化层,其电子海的质量和密度较高,且电子可以较为活跃、高效的发生移动或震荡,从而可以将钢带表面的光线较为完整的反射出去,赋予了钢带表面优异的光泽度效果。
8.优选的,所述钢水中ni、cr、al、mo、v、ti的用量关系满足下式:0.8*ni含量=cr含量 0.5*al含量 10*(mo含量 ti含量 v含量)。
9.通过采用上述技术方案,上述用量关系的ni、cr、al、mo、v、ti元素,其复配效果较优,该结论由连续点的测量结果分布情况总结而来,具体原理未知,颠覆了原有合金类各元素含量不可预估的固有思维;分析其原因可能是由于上述组分元素形成的膜层,其电子更为活跃,能够在光线照入时,高效的发生移动或震荡,从而赋予了钢带表面优异的光泽度效果。
10.第二方面,本技术提供一种短拉丝高光表面精密不锈钢带的生产方法,采用如下的技术方案:一种短拉丝高光表面精密不锈钢带的生产方法,包括如下步骤:s1、毛坯钢卷制备:将钢水经脱硫处理、转炉吹炼、吹氩除杂、板坯连铸、热轧制后,即可制成毛坯钢卷;s2、轧辊表面打磨:选用砂轮磨料打磨轧辊,使其满足毛坯钢卷的压延压制条件后,再对轧辊进行使用,多组轧辊的表面粗糙度不同;s3、精压延轧制钢带:所得的毛坯钢卷经多道连续次轧制,即可制得精轧制钢带;s4、钢带酸洗:选择酸洗剂,将精轧制钢带浸入酸洗剂中5-20min进行酸洗钝化,然后烘干,即得酸洗后的精轧制钢带;s5、拉弯矫直:选用拉弯矫直机组对酸洗后的精轧制钢带进行处理拉弯、矫直处理,消除板形缺陷,即得短拉丝高光表面精密不锈钢带。
11.通过采用上述技术方案,由上述步骤制得的短拉丝高光表面精密不锈钢带,其性能相对稳定均一,在钢水各组分及用量一定的情况下,其屈服强度偏差为
±
5mpa、粗糙度ra 偏差为
±
0.02um;且所得的短拉丝高光表面精密不锈钢带经多组表面粗糙度不同的轧辊依次打磨、酸洗液酸洗后,均具有优良的光泽度,其x方向不低于360gu、y方向不低于300gu。
12.优选的,所述s1毛坯钢卷制备的具体步骤如下:1)脱硫处理:按钢水总重量的0.03-0.05%加入脱硫剂进行脱硫,直至钢水中s含量低于 0.002wt.%;2)转炉吹炼:将脱硫后的钢水转入吹炼炉中进行吹炼,氧气压强为0.9-1.2mpa,吹炼时间为45-60s;3)吹氩除杂:将吹炼后的钢水以100-200r/min搅拌10-25min,搅拌过程中持续通入氩气,氩气的通入量按每吨钢水计算,为15-25l/min;4)板坯连铸:板坯装炉温度为600-800℃,板坯再加热温度为1120-1280℃,入炉加热的板坯宽度为1500-1800mm,且长宽比为3.50-5.0;5)热轧制:经两次加热轧制工艺处理后,即可制得毛坯钢卷;其中第一次终轧温度为900-1000℃,第一次轧制过程累计压下率为50-80%;第二次终轧温度为760-820℃,第二次轧制过程累计压下率50-80%;最终收卷温度为250-400
℃。
13.通过采用上述技术方案,经上述工艺制得的毛坯钢卷,其内杂质较少的同时,所形成的奥氏体较为稳固,且上述多段温度的板坯连铸工艺和热轧制工艺有效降低了毛坯钢卷成型时的内应力,继而保障了毛坯钢卷的成型质量。
14.优选的,所述s2中砂轮磨料的粒径为100-200目,打磨时间为30-60min,磨削速度呈匀速增长,其范围为2000-3000r/min。
15.通过采用上述技术方案,经上述粒径的砂轮磨料、变速磨削的轧辊,其粗糙度更为均匀,继而打磨后的轧辊在投入s3精压延轧制钢带的过程中时,可有效保障钢带表面的粗糙度和光泽度。
16.优选的,所述砂轮磨料为碳化硅、氧化镁、氧化铬、氧化铝中的一种或多种。
17.优选的,所述砂轮磨料的平均粒径为200目,由碳化硅、氧化镁和氧化铝按重量比 1:(0.3-0.5):(0.1-0.2)组成。
18.通过采用上述技术方案,上述组分和用量的砂轮磨料其对轧辊的打磨效果最好,所得轧辊的粗糙度能满足毛坯钢卷的压延压制条件外,其粗糙度较为均一,便于制得光泽度稳定的短拉丝高光表面精密不锈钢带。
19.优选的,所述s3精压延轧制钢带的具体步骤如下:将所得的的毛坯钢卷经三道次轧制,使其压下率为25-30%,即可制得精轧制钢带,其中,其中,第一道次所选用轧辊的粗糙度为ra 0.15-0.20um,第二道次所选用轧辊的粗糙度为 ra 0.10-0.15um,第三道次所选用轧辊的粗糙度为ra 0.05-0.10um。
20.通过采用上述技术方案,经上述三道次轧制后的毛坯钢卷,其力学性能得以保障的同时,还可赋予短拉丝高光表面精密不锈钢带稳定、优异的光泽度。
21.优选的,所述s4中的酸洗剂为ajc-3005、sr-600和avesta中的一种或多种。
22.通过采用上述技术方案,上述组分的酸洗剂均有利于复合钝化层的形成,且形成膜层的电子海的质量和密度较高,电子可以较为活跃、高效的发生移动或震荡,可赋予钢带表面优异的光泽度。
23.优选的,所述s5拉弯矫直的具体步骤如下:选用23辊拉弯矫直机,采用恒延伸、恒张力模式对其进行板形改善,其中拉矫张力控制在8-12kn,提升延伸率控制在0.3
‑ꢀ
0.5%。
24.通过采用上述技术方案,经上述拉弯矫直工艺处理后的钢带,其表面的缺陷均可被有效的消除,从而保障了短拉丝高光表面精密不锈钢带的表面性能和力学性能。
25.综上所述,本技术具有以下有益效果:1、本技术通过上述组分的钢水,赋予了短拉丝高光表面精密不锈钢带优良的力学性能和表面光泽度,其屈服强度为280-320mpa、粗糙度ra为0.06-0.12um;且在ni、cr、al、mo、 v、ti元素的作用下,光泽度显著增强,其x方向高达320-380gu、y方向高达280-350 gu;2、本技术的制备步骤较为简易、易于操作的同时,所得短拉丝高光表面精密不锈钢带的性能相对稳定均一,其屈服强度偏差为
±
5mpa、粗糙度ra偏差为
±
0.02um;还具有优良的光泽度,其x方向不低于360gu、y方向不低于300gu;3、本技术通过砂轮磨料的优选配比、多组轧辊的切换使用以及酸洗液的优选,共同赋予了短拉丝高光表面精密不锈钢带优良的光泽度。
具体实施方式
26.以下结合实施例对本技术作进一步详细说明。
27.制备例制备例1一种毛坯钢卷,其1t钢水中各组分及用量经测定如表1所示,具体制备步骤如下:1)脱硫处理:按钢水总重量的0.03%加入脱硫剂进行脱硫,直至钢水中s含量低于0.002 wt.%,脱硫剂为cao;2)转炉吹炼:将脱硫后的钢水转入吹炼炉中进行吹炼,氧气压强为0.9mpa,吹炼时间为 60s;3)吹氩除杂:将吹炼后的钢水以100r/min搅拌25min,搅拌过程中持续通入氩气,氩气的通入量按每吨钢水计算,为15l/min;4)板坯连铸:板坯装炉温度为600℃,板坯再加热温度为1120℃,入炉加热的板坯宽度为 1600mm,且长宽比为4.0;5)热轧制:经两次加热轧制工艺处理后,即可制得毛坯钢卷;其中第一次终轧温度为900℃,第一次轧制过程累计压下率为80%;第二次终轧温度为 760℃,第二次轧制过程累计压下率60%;最终收卷温度为250℃。
28.制备例2-6一种毛坯钢卷,与制备例1的不同之处在于,其钢水各组分及其相应的重量如表1所示。
29.表1制备例1-6中钢水各组分及其重量(kg)
制备例7一种毛坯钢卷,与制备例1的不同之处在于,具体制备步骤如下:1)脱硫处理:按钢水总重量的0.03%加入脱硫剂进行脱硫,直至钢水中s含量低于0.002 wt.%,脱硫剂为cao;2)转炉吹炼:将脱硫后的钢水转入吹炼炉中进行吹炼,氧气压强为1.0mpa,吹炼时间为 50s;3)吹氩除杂:将吹炼后的钢水以150r/min搅拌210min,搅拌过程中持续通入氩气,氩气的通入量按每吨钢水计算,为20l/min;4)板坯连铸:板坯装炉温度为700℃,板坯再加热温度为1200℃,入炉加热的板坯宽度为1600mm,且长宽比为4.0;5)热轧制:经两次加热轧制工艺处理后,即可制得毛坯钢卷;
其中第一次终轧温度为950℃,第一次轧制过程累计压下率为80%;第二次终轧温度为 800℃,第二次轧制过程累计压下率60%;最终收卷温度为300℃。
30.制备例8一种毛坯钢卷,与制备例1的不同之处在于,具体制备步骤如下:1)脱硫处理:按钢水总重量的0.03%加入脱硫剂进行脱硫,直至钢水中s含量低于0.002 wt.%,脱硫剂为cao;2)转炉吹炼:将脱硫后的钢水转入吹炼炉中进行吹炼,氧气压强为1.2mpa,吹炼时间为 45s;3)吹氩除杂:将吹炼后的钢水以200r/min搅拌10min,搅拌过程中持续通入氩气,氩气的通入量按每吨钢水计算,为15l/min;4)板坯连铸:板坯装炉温度为800℃,板坯再加热温度为1280℃,入炉加热的板坯宽度为 1600mm,且长宽比为4.0;5)热轧制:经两次加热轧制工艺处理后,即可制得毛坯钢卷;其中第一次终轧温度为1000℃,第一次轧制过程累计压下率为80%;第二次终轧温度为 820℃,第二次轧制过程累计压下率60%;最终收卷温度为400℃。
31.制备例9一种毛坯钢卷,与制备例1的不同之处在于,具体制备步骤如下:1)脱硫处理:按钢水总重量的0.03%加入脱硫剂进行脱硫,直至钢水中s含量低于0.002 wt.%,脱硫剂为cao;2)转炉吹炼:将脱硫后的钢水转入吹炼炉中进行吹炼,氧气压强为1.5mpa,吹炼时间为 30s;3)吹氩除杂:将吹炼后的钢水以400r/min搅拌5min,搅拌过程中持续通入氩气,氩气的通入量按每吨钢水计算,为30l/min;4)板坯连铸:板坯装炉温度为1000℃,板坯再加热温度为1280℃,入炉加热的板坯宽度为 1600mm,且长宽比为4.0;5)热轧制:经两次加热轧制工艺处理后,即可制得毛坯钢卷;其中第一次终轧温度为1120℃,第一次轧制过程累计压下率为80%;第二次终轧温度为 860℃,第二次轧制过程累计压下率60%;最终收卷温度为460℃。
32.性能检测试验选取各实施例和对比例中制得的不锈钢带作为检测对象,钢带厚度为0.15
±
0.005mm,分别测试其屈服强度、粗糙度和光泽度;其中屈服强度和粗糙度的具体检测步骤和标准可参照gb/t 5213-2008《冷轧低碳钢板及钢带》,光泽度为光泽度测量仪ls192在60
°
的测量值。实施例
33.实施例1一种短拉丝高光表面精密不锈钢带的生产方法,包括如下步骤:s1、毛坯钢卷制备:其毛坯钢卷由制备例1制得,具体步骤和各组分含量同制备例1:s2、轧辊表面打磨:选用砂轮磨料打磨轧辊,使其满足毛坯钢卷的压延压制条件后,再对轧辊进行使用,三组轧辊的表面粗糙度不同,三组轧辊的粗糙度ra分别为0.05um、
0.10um、 0.15um;其中砂轮磨料为平均粒径200目的碳化硅,打磨时间为60min,磨削速度呈匀速增长,每 15min增长250r/min的转速,其转速范围为2000-3000r/min。
34.s3、精压延轧制钢带:将所得的的毛坯钢卷经三道次轧制,使其压下率为30%,即可制得精轧制钢带,其中,第一道次所选用轧辊的粗糙度ra为0.15um,第二道次所选用轧辊的粗糙度ra为0.10um,第三道次所选用轧辊的粗糙度ra为0.05um。
35.s4、钢带酸洗:选择酸洗剂ajc-3005,将精轧制钢带浸入酸洗剂中10min进行酸洗钝化,然后烘干,即得酸洗后的精轧制钢带;s5、拉弯矫直:选用23辊拉弯矫直机,采用恒延伸、恒张力模式对其进行板形改善,其中拉矫张力控制在10kn,提升延伸率控制在0.3%。
36.实施例2-6一种短拉丝高光表面精密不锈钢带及其生产方法,与实施例1的不同之处在于,所用毛坯钢卷的使用情况不同,具体对应关系下表所示。
37.表:实施例2-6中毛坯钢卷使用情况对照表组别毛坯钢卷实施例2由制备例2制得实施例3由制备例3制得实施例4由制备例4制得实施例5由制备例5制得实施例6由制备例6制得对比例1一种短拉丝高光表面精密不锈钢带及其生产方法,与实施例1的不同之处在于,所用毛坯钢卷为316l/astm。
38.抽取上述实施例1-6和对比例1中制得的短拉丝高光表面精密不锈钢带,分别测试其屈服强度、粗糙度和光泽度,测试结果取平均值记入下表。
39.从上表中可以看出,由实施例1-6中制备方法制得的短拉丝高光表面精密不锈钢带,均具有优良的力学性能和表面光泽度,其屈服强度为280-320mpa、粗糙度ra为0.010um;且光泽度较强,其x方向高达320-362gu、y方向高达280-336gu;可见由制备例1-6中各组分及用量所制得的毛坯钢卷,其构成的奥氏体较为稳固、力学性能较优,且适量的ni、cr、al、mo、v、ti元素,可进一步提升钢带的光泽度,具体可参见实施例3-4,满足0.8*ni含量=cr含量 0.5*al含量 10*(mo含量 ti含量 v含量)时,其x 方向高达360-362gu、y方向高达335-336gu;分析其原因肯能是由于由上述组分元素经钝化/氧化形成嵌合的复合膜层,其电子海的质量和密度较高,且电子可以较为活跃,能够在光线照入时,高效的发生移动或震荡,从而可以将钢带表面的光线较为完整的反射出去,赋予了钢带表面优异的光泽度效果。
40.而缺少上述组分配比制得的不锈钢带,参见对比例1,其各项性能均有不同程度下降,其屈服强度仅为305mpa、粗糙度ra为0.010um;且光泽度较强,其x方向高达200 gu、y方向高达180gu,可见组分的优选和复配有利于进一步保障不锈钢带的成品性能。
41.实施例7-9一种短拉丝高光表面精密不锈钢带及其生产方法,与实施例1的不同之处在于,所用毛坯钢卷的使用情况不同,具体对应关系下表所示。
42.表:实施例7-9中毛坯钢卷使用情况对照表组别毛坯钢卷实施例7由制备例7制得实施例8由制备例8制得实施例9由制备例9制得抽取上述实施例7-9中制得的短拉丝高光表面精密不锈钢带,分别测试其屈服强度、粗糙度和光泽度,测试结果取平均值记入下表。
43.从上表中可以看出,由实施例7-8中制备方法制得的短拉丝高光表面精密不锈钢带,均具有优良的力学性能和表面光泽度,其屈服强度为280-312mpa、粗糙度ra为0.010um;且光泽度较强,其x方向高达320-322gu、y方向高达280-281gu;可见由制备例7-8中工艺条件所制得的毛坯钢卷,其内杂质较少的同时,所形成的奥氏体较为稳固,从而赋予了不锈钢带优良的力学性能,当各项工艺条件超出特定条件后,其屈服强度小幅度下降,参见实施例9,仅为262mpa,分析其原因可能是由于生产过程中钢带的内应力较大,影响到了最终的成品质量。
44.实施例10一种短拉丝高光表面精密不锈钢带及其生产方法,与实施例1的不同之处在于,s4中砂轮磨料为平均粒径200目的碳化硅,打磨时间为30min,磨削速度呈匀速增长,每15min增长 500r/min的转速,其转速范围为2000-3000r/min。
45.实施例11一种短拉丝高光表面精密不锈钢带及其生产方法,与实施例1的不同之处在于,s4中砂轮磨料为平均粒径200目的碳化硅,打磨时间为45min,磨削速度呈匀速增长,每15min增长250r/min的转速,其转速范围为2000-3000r/min。
46.实施例12一种短拉丝高光表面精密不锈钢带及其生产方法,与实施例1的不同之处在于,s4中砂轮磨料为平均粒径200目的碳化硅,打磨时间为75min,磨削速度呈匀速增长,每15min增长 150r/min的转速,其转速范围为2000-3000r/min。
47.对比例2一种短拉丝高光表面精密不锈钢带及其生产方法,与实施例1的不同之处在于,s4中砂轮磨料为平均粒径200目的碳化硅,打磨时间为60min,磨削速度为2500r/min。
48.抽取上述实施例10-12和对比例2中制得的短拉丝高光表面精密不锈钢带,分别测试其屈服强度、粗糙度和光泽度,测试结果取平均值记入下表。
49.从上表中可以看出,由实施例10-12中制备方法制得的短拉丝高光表面精密不锈钢带,均具有较为平整、优良的表面光泽度,其粗糙度ra为0.010-0.14um,其x方向高达 312-320gu、y方向高达276-280gu;可见经上述粒径的砂轮磨料、变速磨削的轧辊,其粗糙度更为均匀,继而打磨后的轧辊在投入s3精压延轧制钢带的过程中时,可有效保障钢带表面的粗糙度和光泽度,且轧辊打磨时间超过60min后,其不利于钢带的轧制,参见实施例12。
50.从表中还可以看出,轧辊未采用变速打磨,相同打磨条件下,其对钢带的轧制效果显著降低,其粗糙度ra为0.018um,其x方向高达302gu、y方向高达268gu;分析其原因可能是由于变速打磨后的轧辊,其粗糙度较为均匀,有利于轧制作业的进行。
51.实施例13一种短拉丝高光表面精密不锈钢带及其生产方法,与实施例1的不同之处在于,s2中的砂轮磨料由碳化硅和氧化镁按重量比1:0.8组成。
52.实施例14一种短拉丝高光表面精密不锈钢带及其生产方法,与实施例1的不同之处在于,s2中的砂轮磨料由碳化硅、氧化镁和氧化铝按重量比1:0.3:0.1组成。
53.实施例15一种短拉丝高光表面精密不锈钢带及其生产方法,与实施例1的不同之处在于,s4中的砂轮磨料由碳化硅、氧化镁和氧化铝按重量比1:0.4:0.15组成。
54.实施例16一种短拉丝高光表面精密不锈钢带及其生产方法,与实施例1的不同之处在于,s2中的砂轮磨料由碳化硅、氧化镁和氧化铝按重量比1:0.5:0.2组成。
55.实施例17一种短拉丝高光表面精密不锈钢带及其生产方法,与实施例1的不同之处在于,s2中的砂轮磨料由碳化硅、氧化镁和氧化铝按重量比1:0.8:0.5组成。
56.实施例18一种短拉丝高光表面精密不锈钢带及其生产方法,与实施例1的不同之处在于,s2中的砂轮磨料由碳化硅、氧化镁和氧化铝按重量比1:0.1:0.05组成。
57.抽取上述实施例13-18中制得的短拉丝高光表面精密不锈钢带,分别测试其屈服
强度、粗糙度和光泽度,测试结果取平均值记入下表。
58.从上表中可以看出,由实施例13-18中制备方法制得的短拉丝高光表面精密不锈钢带,均具有较为平整、优良的表面光泽度,其粗糙度ra为0.06-0.10um,其x方向高达 318-346gu、y方向高达292-322gu;进一步,实施例14-16为优选实施例,可见s4中的砂轮磨料由碳化硅、氧化镁和氧化铝按重量比1:(0.3-0.5):(0.1-0.2)组成时,其对轧辊的打磨效果最好,便于制得光泽度稳定的短拉丝高光表面精密不锈钢带。
59.实施例19一种短拉丝高光表面精密不锈钢带及其生产方法,与实施例1的不同之处在于,s3中第一道次所选用轧辊的粗糙度ra为0.05um,第二道次所选用轧辊的粗糙度ra为0.10um,第三道次所选用轧辊的粗糙度ra为0.15um。
60.实施例20一种短拉丝高光表面精密不锈钢带及其生产方法,与实施例1的不同之处在于,s3中第一道次所选用轧辊的粗糙度ra为0.10um,第二道次所选用轧辊的粗糙度ra为0.05um,第三道次所选用轧辊的粗糙度ra为0.15um。
61.对比例3一种短拉丝高光表面精密不锈钢带及其生产方法,与实施例1的不同之处在于,所得的的毛坯钢卷经两道次轧制,其中第一道次所选用轧辊的粗糙度ra为0.15um,第二道次所选用轧辊的粗糙度ra为0.10um。
62.抽取上述实施例19-20和对比例3中制得的短拉丝高光表面精密不锈钢带,分别测试其屈服强度、粗糙度和光泽度,测试结果取平均值记入下表。
63.从上表中可以看出,由实施例19-20中制备方法制得的短拉丝高光表面精密不锈钢带,均具有较为平整、优良的表面光泽度,其粗糙度ra为0.06-0.12um,其x方向高达 312-320gu、y方向高达276-280gu;从表中还可以看出,由于对比例3未采用三道轧制工艺,钢带表面的平整度和光泽度均有不同程度下降,其粗糙度ra高达0.016um,其x方向高达296gu、y方向高达258gu。
64.实施例21一种短拉丝高光表面精密不锈钢带及其生产方法,与实施例1的不同之处在于,s4中酸洗剂为sr-600。
65.实施例22一种短拉丝高光表面精密不锈钢带及其生产方法,与实施例1的不同之处在于,s4中酸洗剂由ajc-3005和sr-600按重量比3:1组成。
66.抽取上述实施例21-22中制得的短拉丝高光表面精密不锈钢带,分别测试其屈服强度、粗糙度和光泽度,测试结果取平均值记入下表。
67.从上表中可以看出,由实施例21-22中制备方法制得的短拉丝高光表面精密不锈钢带,均具有较为平整、优良的表面光泽度,其粗糙度ra为0.10-0.12um,其x方向高达 310-332gu、y方向高达272-286gu;可见上述组分的酸洗剂均有利于复合钝化层的形成,且ajc-3005与sr-600具有复配效果,所形成膜层的电子海的质量和密度较高,电子可以较为活跃、高效的发生移动或震荡,赋予了钢带表面优异的光泽度。
68.本具体实施例仅仅是对本技术的解释,其并不是对本技术的限制,本领域技术人员在阅读完本说明书后可以根据需要对本实施例做出没有创造性贡献的修改,但只要在本
申请的权利要求范围内都受到专利法的保护。
再多了解一些
本文用于企业家、创业者技术爱好者查询,结果仅供参考。