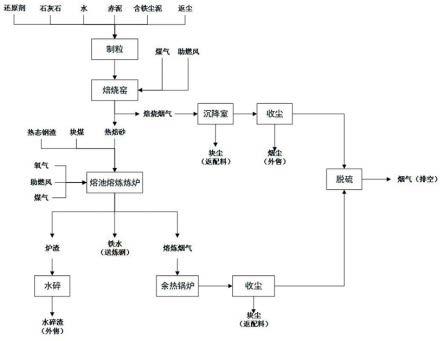
1.本发明属于固废利用技术领域,具体涉及的是一种高铁赤泥和熔融钢渣协同利用方法。
背景技术:
2.赤泥是氧化铝生产过程中产生的固体废弃物,我国每年产生赤泥1亿吨以上,历史堆存量在10亿吨以上,一直未能得到很好的利用。高铁赤泥是一种潜在的铁源,相比铁精矿,高铁赤泥的品位低,且含有钠元素,无法以原料的方式直接进入炼铁工序。目前大多通过磁选提铁或者还原焙烧 磁选提铁的预处理方式进行利用,其中磁选提铁工艺存在回收率低、产品铁品位低、尾渣依然需要填埋处理等问题,还原焙烧 磁选提铁工艺存在成本高、磁选尾渣难以利用等问题。
3.近年来,熔池熔炼,尤其是侧吹富氧熔池熔炼技术在有色冶炼、固废处理领域得到广泛应用,取得了很好的效果,将富氧侧吹熔池熔炼工艺应用于赤泥处理,可充分发挥该工艺反应效率高、烟气量小、自动化程度高、环保效果好等优势,同时也需要解决以下问题:1)、若将赤泥直接用于富氧侧吹熔池熔炼,因其含钠高,还原熔炼过程中钠大多数挥发至烟气中,粘接在余热锅炉或者收尘器上,影响正常生产;2)、相比铜、镍等有色金属的还原,铁的还原对气氛要求更高,冶炼温度更高,因此在工艺参数上需要有很大的调整;3)、高铁赤泥铁高、铝高,造渣需要选择富含硅、钙的辅料,使用天然辅料成本高、能耗高,寻求一种低廉的辅料非常有必要。
4.钢渣是炼钢过程中产生的固体废弃物,占钢产量的12-15%之间。钢渣碱度高,含铁高,常规处理工艺是“热焖/热泼 磁选”,铁类物料返回钢铁系统,但钢渣尾渣因游离氧化钙过高,影响了其正常使用,目前利用率不到三分之一。
5.专利“cn112981028a”公开了一种通过侧吹熔炼从赤泥中提取铁元素的方法。赤泥中含有大量的碱,直接采用侧吹还原熔炼将大量被还原挥发进入烟气中,粘接在余热锅炉、收尘器上,影响正常生产;另外,该专利照搬了有色冶炼侧吹熔炼工艺,未考虑铁还原的特点,生产时难以达到预期还原效果。
6.专利“cn101456573a”公开了一种拜耳法赤泥熔融还原的方法,通过在赤泥中配入硅石、还原剂和助溶剂,利用1600-1900℃的高温还原熔炼,获得硅铁和刚玉熔体。该专利利用赤泥生产硅铁,需要配入硅石和助熔剂,生产成本高;静态还原效率低,回收率低;赤泥中含有的碱金属(na的复合氧化物),在还原过程中挥发,影响熔炉和烟气净化系统的正常作业。
7.专利“cn103866128b”公布一种碳热法还原赤泥生产铝铁合金的方法。该方法需要湿法脱碱、酸浸的预处理工序获得氧化铝作为原料,浸出渣依然是难以利用的固体废弃物(由于赤泥中氧化铝含量并不高,浸出渣量与赤泥量相当);碳热还原过程中需要加入铁矿石,增加了处理成本。
8.专利“cn104988321a”公开了一种“还原焙烧 熔分”的工艺处理赤泥得到氧化纳、铁水和水碎渣的方法,该专利可实现对赤泥的综合利用。该专利需要3个工序(焙烧、熔分和调质)实现对赤泥的利用,流程长;焙烧还原脱碱仅配碳,脱碱效果差;熔分为静态过程,效率低;造渣剂为石灰石,采用天然原料成本高。以上不足导致其处理成本高,限制其推广应用。
9.专利“cn110484734a”公开了一种高铁赤泥“强磁预选 深度还原熔炼”的方法,通过磁选获得铁精矿,然后精矿、煤和石灰在回转窑内还原焙烧,焙砂在还原炉内还原得到铁水和高铝渣,通过浸出回收铝。该工艺本质上属于还原焙烧 熔分的路线,提铁效率低,成本高。
10.专利“cn104988322a”公开了一种赤泥和钢渣协同处理的方法,通过将赤泥、钢渣和还原剂混合后还原焙烧、磁选得到含铁产品和尾料。该专利主要利用冷态钢渣尾渣,焙烧磁选工艺成本高、收益低。
11.专利“cn111850214a”公开了钢渣和赤泥协同利用的工艺,通过将赤泥、还原剂加入到钢渣中,还原得到铁和无害渣。该专利试图利用固体还原剂在静态环境下获得铁水,还原效率低,还原剂消耗量大,生产成本高。
12.专利“cn112939489a“公开了协同利用赤泥、转炉熔融钢渣生产铁水和无害渣的方法。该专利以赤泥作为钢渣的调质剂,且采用电炉作为熔融炉。
13.专利“cn101054628a”公开了一种从赤泥中提取钛渣的工艺,通过配料熔融除铁后对水碎渣进行酸性浸,除掉na、ca、mg、al、fe等杂质,获得富钛渣,该专利侧重点在提钛,熔融和酸浸都是为了除掉钛以外的杂质,适合含钛很高的赤泥。且赤泥中ti基本上以钛酸钙形式存在,通过熔融很难分离除理想的tio2。
14.专利“cn106148699a”公开了一种协同利用赤泥和红土镍矿制备镍铁合金的方法,通过将赤泥、红土镍矿、焦粉和石灰配料,利用矿热炉还原熔炼得到镍铁合金和无害渣。
15.若能以熔融钢渣作为赤泥还原熔炼的熔剂,依托钢铁厂处理赤泥,既可以充分发挥钢铁厂的煤气、蒸汽等能源介质优势,同时也可以协同处理钢厂的钢渣,达到以废治废的目的,从而实现降低赤泥处理成本,解决钢渣的出路,回收铁资源等目的。
16.针对现有技术的不足,本发明引入有色冶炼领域的富氧熔池熔炼技术,通过采用“干燥 还原挥发焙烧 富氧侧吹熔池熔炼”的方式,协同处理赤泥和熔融钢渣,产出铁水和无害渣。既解决了赤泥和钢渣的利用难题,同时通过钢厂和铝厂的介质协同,大幅度降低了处理成本。
技术实现要素:
17.本发明的目的在于克服背景技术中的不足,以处理高铁赤泥、熔融钢渣并回收铁水为主要目的,本发明提供一种高铁赤泥和熔融钢渣协同利用的方法。
18.本发明为解决背景技术中存在的技术问题而采取的技术方案是:一种高铁赤泥和熔融钢渣协同利用方法,本发明的主要原料是高铁赤泥和钢厂熔融钢渣,以协同处理高铁赤泥和熔融钢渣并回收铁元素为目的,除此之外还可以协同处理钢厂的含铁尘泥(如烧结灰、高炉瓦斯灰、转炉灰等),本发明的主要工艺路线为“干燥脱水 还原挥发焙烧 富氧侧吹熔池熔炼”,包括以下步骤:
s1、高铁赤泥干燥脱水:高铁赤泥中铁元素(以fe2o3计,干基)含量≥25wt%,tio2的含量≤10wt%,高铁赤泥干燥至含水量为8~10%;高铁赤泥中铁元素的含量过低,提铁性价比低,经济效益差;钛元素的含量过高,在还原过程中容易产生tin(c)等难熔物质,增加熔渣粘度,不利于铁的分离和渣排放;s2、高铁赤泥还原焙烧:s2-1、将步骤s1干燥脱水后的高铁赤泥与还原剂、含铁尘泥、返尘和粘结剂混合造粒,并且当高铁赤泥中na2o的含量>3%时还需在混合物料中配入石灰石,其中:还原剂为焦粒、块煤或者兰碳中的一种或多种,还原剂中固定碳与(fe na)的摩尔比为0.6~0.8,还原剂的粒径为1-5mm;石灰石中的ca和赤泥中的游离ca之和(即混合料中的有效ca)与na的摩尔比为1~2,还原焙烧时配入石灰石粉通过利用cao从复合氧化物中置换na2o,以促进钾、钠的挥发;s2-2、步骤s2-1制得的粒状混合物料连续加入回转式焙烧炉或者转底炉中焙烧,粒状混合物料与窑内烟气逆流换热(即烟气流动方向与物料运动方向相反),经干燥、分解、还原、挥发等过程逐步脱除其中的自由水、结晶水、以及钠、钾、氯、锌等,脱除易挥发组份的同时进行还原反应(直接还原和间接还原),制得热焙砂;其中,还原焙烧温度为以下两种情形中的任一种:1)、当高铁赤泥中na2o的含量≤3%时,还原焙烧温度为600-800℃,此时无脱钠任务,所以粒状混合物料中无需配入石灰石;2)、当高铁赤泥中na2o的含量>3%时,还原焙烧温度为1000-1200℃,优选1150℃。温度过低钠的挥发效果差,温度过高易粘接,影响生产;s3、富氧侧吹熔池熔炼:s3-1、将步骤s2制得的热焙砂转运至熔炼炉炉前料仓内,缓存时间1-2h;热焙砂转运过程中温度控制在600-800℃,转运全过程密闭,防止热焙砂降温和氧化;高温熔融钢渣通过渣包和返渣流槽加入熔炼炉内,渣流槽材质优选铸铁。熔融钢渣与热焙砂的质量比为0.3~0.5;熔炼炉内二次加入还原剂,二次加入还原剂的添加量为热焙砂总重量的20-40%;s3-2、采用富氧侧吹熔池熔炼炉进行熔炼,熔炼过程鼓入一次风、二次风和三次风:一次风富氧浓度≥50%,一次风喷入熔池内部用于熔池内co的燃烧,并且在一次风的搅拌作用下,焙砂发生熔化、还原、造渣反应,熔炼温度为1500℃,因密度不同分离得到铁水、熔渣和一次烟气:铁水经渗碳后通过铁排放口放出后送往炼钢车间,铁水温度1400-1450℃;熔渣经澄清分离后通过渣排放口排出,排放温度≤1550℃,采用cao-sio
2-mgo-al2o
3-tio2五元渣系,通过配料控制渣cao/sio2=1.0-1.3,sio2/al2o3=1.5-2.0,熔点≤1500℃,1500℃时粘度≤1pa
•
s,然后熔渣进行水碎,水碎渣作为建材原料;二次风从炉膛空间鼓入,一次烟气从熔池中排出后与二次风发生燃烧反应,二次风富氧浓度≤35%,控制二次燃烧的温度为1550-1650℃;三次风从余热锅炉的膜式壁侧墙鼓入,二次燃烧后的烟气与三次风进行充分燃烧并通过锅炉换热至300℃以下,二次燃烧后的烟气与三次风充分燃烧以实现烟气中co的彻
底燃烧完全,降温后的烟气经收尘、脱硫后排放;本发明熔炼过程产生的烟气全部采用余热锅炉降温和回收热量,余热锅炉采用膜式壁结构,锅炉出口烟气温度≤200℃;s4、焙砂收尘和熔炼收尘得到的低钠尘返回步骤s2-1中用于配料,高钠尘送往铝冶炼厂作为钠源使用。
19.本发明的工艺原理(主要反应):s1、高铁赤泥干燥脱水:h2o
→
h2o
↑
;s2、高铁赤泥还原焙烧:a、干燥、分解:h2o
→
h2o
↑
;caco3→
cao co2↑
;b、还原:fe(oh)3→
fe2o3 h2o
↑
;fe2o3 c
→
fe3o4 co
↑
;fe3o4 c
→
feo co
↑
;feo c
→
fe co
↑
;feo co
→
fe co2↑
;c、交互反应:c co2→
co
↑
;d、脱杂:naalo2 c
→
2na
↑
co
↑
al2o3;na2o
•
al2o3•
2sio2 c cao
→
na
↑
co
↑
2cao
•
sio2 al2o3;zno c
→
zn
↑
co
↑
;nacl
→
nacl
↑
;kcl
→
kcl
↑
;s3、富氧侧吹熔池熔炼:a、还原:feo c
→
fe co
↑
;fe3o4 c
→
fe co
↑
;b、燃烧:c o2→
co
↑
;co o2→
co
↑
;c、造渣:cao sio2→
2cao
•
sio2。
20.进一步的,在所述步骤s1中,高铁赤泥通过汽车、袋装或者管道输送至钢厂,或者当氧化铝厂位于钢厂附近时,将脱水前的赤泥浆液用管道泵送至干燥车间,在干燥车间压滤得到高铁赤泥,滤液重新返回氧化铝厂,既可以降低污泥运输过程中的成本,而且可以改善环境。
21.进一步的,在所述步骤s1中,高铁赤泥干燥采用蒸汽干燥或者回转窑干燥。采用蒸汽干燥可以充分利用熔炼时烟气余热回收产生的蒸汽,降低能耗和生产成本;若采用回转窑干燥,燃料优选钢厂低热值的煤气。
22.进一步的,在所述步骤s2-2中,还原焙烧的燃料为钢厂煤气,以降低焙烧成本,煤气热值不够时采用富氧助燃,以提高火焰温度。
23.进一步的,在所述步骤s2-2中,热焙砂与还原焙烧过程中产生的还原焙烧烟气(温度约300℃)经重力收尘、布袋收尘或者电收尘后送入脱硫系统,其中重力尘返回步骤s2-1作为造粒的原料,布袋尘或者电尘因为钠含量高,反馈至铝厂作为钠源。
24.进一步的,在所述步骤s3-1中,热焙砂通过溜槽、热料转运料斗或者埋刮板输送机进行转运。
25.进一步的,在所述步骤s3-1中,炉前料仓内部设有隔热材料,控制仓壁温度≤50℃,防止热损失过大导致焙砂大幅降温;料仓设有秤重料位计量系统和排料系统,可实现连续定量下料。
26.进一步的,在所述步骤s3-2中,富氧熔池熔炼炉上设置用于补充热量的燃料烧嘴,燃料采用煤粉或者天然气,燃料烧嘴采用欠氧燃烧以维持强还原性气氛,供氧量为完全燃烧需要量的50%,高温高压燃烧气直接从渣层鼓入并穿透铁水层,起到搅拌铁水、补热和渗碳的作用。
27.进一步的,在所述步骤s3-2中,降温后的烟气采用布袋收尘器或者电收尘器收尘,收集的烟尘返回铝厂作为碱源。
28.与现有技术相比本发明的有益效果为:本发明依托钢铁厂处理赤泥,既可以充分发挥钢铁厂的煤气、蒸汽等能源介质优势,同时也可以协同处理钢厂的钢渣,达到以废治废的目的。
29.采用本发明高铁赤泥和熔融钢渣协同利用方法,以年处理50万吨(干基)赤泥为例,可协同处置约25万吨熔融钢渣(相当于200万吨钢厂的渣量),年回收铁水约21万吨,铁回收率超过90%,单位铁水处理成本约2100元,每年产生净利润约1.5亿元,所有二次固废都得到了有效利用,经济效益和环保效益均很明显。
附图说明
30.图1为本发明流程图。
具体实施方式
31.下面结合附图和实施例对本发明作进一步的详细描述。
32.实施例1如图1所示的一种高铁赤泥和熔融钢渣协同利用方法,包括以下步骤:s1、高铁赤泥干燥脱水:高铁赤泥通过袋装送至试验车间,含水32%,干基成分为:fe:31%、ca:8%、si:4.7%、na:5%、al:10%;高铁赤泥用量200kg/h(干基),采用蒸汽干燥机干燥至含水量为8%,蒸汽用量55kg/h;s2、高铁赤泥还原焙烧:将步骤s1干燥脱水后的高铁赤泥与焦粉25kg/h、石灰石粉50kg/h、膨润土6kg/h混合造粒,混合粒料在回转窑内还原焙烧,还原焙烧温度为1150℃,物料停留时间2h,还原焙烧的燃料为钢厂转炉煤气,用量15nm3/h,得到热焙砂230kg/h;还原焙烧烟气经重力收尘、布袋收尘或者电收尘后送入脱硫系统,其中重力尘返回步骤s2作为
造粒的原料,布袋尘或者电尘因为钠含量高,反馈至铝厂作为钠源;s3、富氧侧吹熔池熔炼:s3-1、将步骤s2制得的热焙砂通过热料转运料斗转运至熔炼炉炉前料仓内,缓存时间1h,炉前料仓内部设有隔热材料,控制仓壁温度≤50℃,料仓设有秤重料位计量系统和排料系统;热焙砂转运过程中温度控制在600℃,转运全过程密闭,防止热焙砂降温和氧化;高温熔融钢渣通过渣包和返渣流槽加入熔炼炉内,熔融钢渣110kg/h,熔融钢渣的干基成分为:fe:23.5%、cao:46.5%、sio2:13.5%;熔炼炉内二次加入还原剂:还原煤40kg/h,煤粉30kg/h,氧气70nm3/h;s3-2、采用富氧侧吹熔池熔炼炉进行熔炼,富氧熔池熔炼炉上设置用于补充热量的燃料烧嘴,燃料采用煤粉,燃料烧嘴采用欠氧燃烧以维持强还原性气氛,供氧量为完全燃烧需要量的50%,熔炼过程鼓入一次风、二次风和三次风:一次风富氧浓度65%,一次风喷入熔池内部用于熔池内co的燃烧,并且在一次风的搅拌作用下,焙砂发生熔化、还原、造渣反应,熔炼温度为1500℃,因密度不同,分离得到铁水85kg/h(fe93.8%)、熔渣263kg/h,铁回收率91.5%,钢渣消纳率55%,煤比1117kg/t(铁水);铁水经渗碳后通过铁排放口放出后送往炼钢车间,铁水温度1400℃;熔渣经澄清分离后通过渣排放口排出,排放温度≤1550℃,采用cao-sio
2-mgo-al2o
3-tio2五元渣系,通过配料控制渣cao/sio2=1.0,sio2/al2o3=1.5,熔点≤1500℃,1500℃时粘度≤1pa
•
s,然后熔渣进行水碎,水碎渣作为建材原料;二次风从炉膛空间鼓入,一次烟气从熔池中排出后与二次风发生燃烧反应,二次风富氧浓度30%,控制二次燃烧的温度为1550℃;三次风从余热锅炉的膜式壁侧墙鼓入,二次燃烧后的烟气与三次风进行充分燃烧并通过锅炉换热至300℃以下,降温后的烟气经收尘、脱硫后排放,降温后的烟气采用布袋收尘器或者电收尘器收尘,收集的烟尘返回铝厂作为碱源;s4、焙砂收尘和熔炼收尘得到的低钠尘返回步骤s2-1中用于配料,高钠尘送往铝冶炼厂作为钠源使用。
33.实施例2一种高铁赤泥和熔融钢渣协同利用方法,包括以下步骤:s1、高铁赤泥干燥脱水:原始赤泥同实施例1,采用蒸汽干燥机干燥至含水9%,蒸汽用量52kg/h;s2、高铁赤泥还原焙烧:将步骤s1干燥脱水后的高铁赤泥与焦粉26.3kg/h、石灰石粉46.5kg/h、膨润土5.6kg/h混合造粒,混合粒料在回转窑内还原焙烧,还原焙烧温度为1100℃,物料停留时间2h,还原焙烧的燃料为钢厂转炉煤气,用量11nm3/h,得到热焙砂227kg/h;s3、富氧侧吹熔池熔炼:s3-1、将步骤s2制得的热焙砂通过热料转运料斗转运至熔炼炉炉前料仓内,料仓同实施例1;高温熔融钢渣通过渣包和返渣流槽加入熔炼炉内,熔融钢渣122.6kg/h,熔融钢渣成分同实施例1;熔炼炉内二次加入还原剂(还原煤)41.3kg/h,煤粉25.2kg/h,氧气65.5nm3/h;
s3-2、侧吹熔炼炉及熔炼过程同实施例1:一次风富氧浓度65%,熔炼温度为1500℃,得到铁水88.5kg/h(fe93.8%)、熔渣272kg/h铁回收率91.2%,钢渣消纳率61.3%,煤比1050kg/t(铁水);炉渣排放温度1550℃,cao/sio2=1.2,sio2/al2o3=1.8,熔点≤1500℃,1500℃时粘度≤1pa
•
s;二次风富氧浓度35%,二次燃烧的温度1600℃。
34.实施例3一种高铁赤泥和熔融钢渣协同利用方法,试验过程同实施例1,赤泥、钢渣成分同实施例1,包括以下步骤:s1、高铁赤泥干燥脱水:高铁赤泥200kg/h,采用蒸汽干燥干燥至含水量为10%,蒸汽用量50.8kg/h;s2、高铁赤泥还原焙烧:含水10%的高铁赤泥与焦粉23.4kg/h、石灰石粉53.8kg/h、膨润土5.7kg/h混合造粒后送回转窑还原焙烧,还原焙烧温度为1200℃,焙烧时间2h,采用钢厂转炉煤气nm3/h,得到热焙砂229.3kg/h;s3、富氧侧吹熔池熔炼:熔融钢渣170.9kg/h,二次加入还原剂(还原煤)49.8kg/h,煤粉30kg/h,氧气77nm3/h;一次风富氧浓度70%,一次风量59nm3/h,熔炼温度1550℃;二次风富氧浓度35%,二次燃烧的温度为1650℃,二次风量89nm3/h。
35.炉渣排放温度1550℃,cao/sio2=1.3,sio2/al2o3=2.0,熔点≤1500℃,1500℃时粘度≤1pa
•
s;获得铁水99.4kg/h(fe93.7%)、熔渣319.3,铁回收率91.1%,钢渣消纳率85.5%,煤比1037kg/t(铁水)。
36.以上所述,仅为本发明的具体实施方式,但本发明的保护范围并不局限于此,任何熟悉技术领域的技术人员在本发明揭露的技术范围内,可轻易想到的变化或替换,都应涵盖在本发明的保护范围之内。因此,本发明的保护范围应以所述权利要求的保护范围为准。
再多了解一些
本文用于企业家、创业者技术爱好者查询,结果仅供参考。