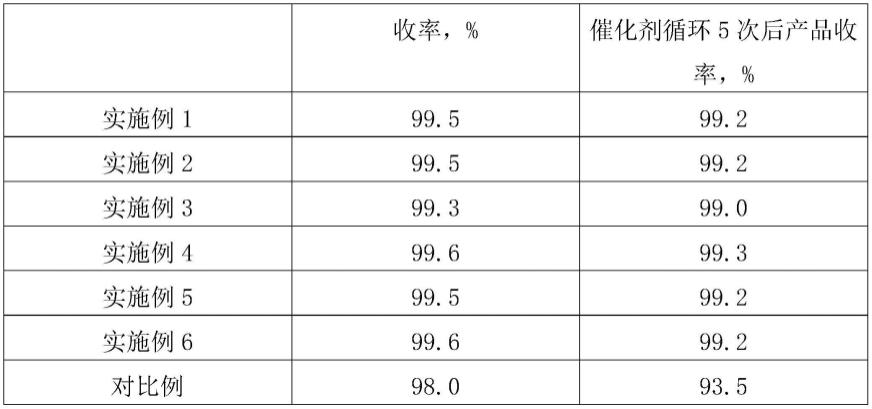
1.本发明涉及有机合成技术领域,具体涉及一种2,4-二氟硝基苯催化加氢制备2,4-二氟苯胺的方法。
背景技术:
2.2,4-二氟苯胺是有机合成中常见的中间体,其可以用于合成氟苯水杨酸,同时还可以用于合成用于医药领域的中间体1,2,3-三氟苯。目前2,4-二氟苯胺的制备工艺有以下几种方法:一是以间硝基苯胺、氟硼酸和亚硝酸钠为原料反应,反应后对产物进行热分解处理制得间硝基氟苯,再用硫氢化合物进行还原,制得。该方法合成路线较长,且合成过程中会产生大量含盐废水,不利于经济环保。二是以2,4-二氟硝基苯为原料,在催化剂的作用下加氢还原来制备2,4-二氟苯胺,该方法操作简单,制得的产品收率高,对环境无污染,得到了广泛的应用。对于该方法中如何制得一种催化活性高、经济实惠的催化剂成为关键。
技术实现要素:
3.本发明所要解决的技术问题是:针对现有技术存在的不足,提供一种2,4-二氟硝基苯催化加氢制备2,4-二氟苯胺的方法,本发明采用的催化剂是以珍珠岩与zr-mof作为复合载体,并采用pt与ni作为复合催化活性组分,采用2,4-二氟硝基苯为原料,制得的产品收率高,纯度高,而且催化剂用量少,没有采用有机溶剂,有利于环境保护。
4.为解决上述技术问题,本发明的技术方案是:
5.一种2,4-二氟硝基苯催化加氢制备2,4-二氟苯胺的方法,包括以下步骤:
6.(1)将珍珠岩和无水乙醇混合超声处理,之后研磨处理,然后过滤收集固体,将固体干燥后制得预处理珍珠岩;将预处理珍珠岩分散在dmf中,制得混合液a,将氯化锆和对苯二甲酸溶解在dmf中,制得混合液b,将混合液a和混合液b混合搅拌处理,之后将得到的反应液转移至高压釜内,升温反应,反应结束后冷却至室温并将反应液进行离心处理,离心得到的沉淀干燥后制得zr-mof/珍珠岩复合材料;
7.(2)将氯化钯和氯化镍溶于去离子水中制得混合溶液,然后加入上述制得的zr-mof/珍珠岩复合材料,超声处理,然后烘干,最后置于马弗炉内还原处理,制得催化剂;
8.(3)将2,4-二氟硝基苯加入到装有催化剂的反应器中,采用氢气置换出反应器中的空气,升温后通入氢气反应,反应结束后,将反应液过滤除去催化剂,滤液除去溶剂后进行减压蒸馏,制得目标产品。
9.作为上述技术方案的优选,步骤(1)中,所述预处理珍珠岩、氯化锆、对苯二甲酸的质量比为(1-3):0.65:0.33。
10.作为上述技术方案的优选,步骤(1)中,所述搅拌处理的温度为常温,时间为2-4h。
11.作为上述技术方案的优选,步骤(1)中,所述升温反应的温度为120℃,反应时间为14-17h。
12.作为上述技术方案的优选,步骤(2)中,所述氯化钯、氯化镍、zr-mof/珍珠岩复合
材料的质量比为(0.08-0.1):(0.08-0.1):5。
13.作为上述技术方案的优选,步骤(2)中,所述超声处理的时间为2-3h,功率为100-300w。
14.作为上述技术方案的优选,步骤(2)中,还原处理的气氛为氢气和氮气以体积比为1:9的混合气,温度为300℃,升温速率为1-1.5℃/min,处理时间为1-2h。
15.作为上述技术方案的优选,步骤(3)中,所述2,4-二氟硝基苯、催化剂的用量比为1mol(1-2)g。
16.作为上述技术方案的优选,步骤(3)中,所述反应的温度为45-55℃,反应压力为0.1mpa,反应时间为1-2h。
17.由于采用了上述技术方案,本发明的有益效果是:
18.对于负载型加氢催化剂,载体是催化剂的重要组成部分,将催化活性组分稳定在载体上,可有效提高催化剂的回收和再循环能力,而且载体的正确选择还能在一定程度上促进加氢还原反应的进行。本发明选择价格低廉的珍珠岩作为载体材料,其具有一定的吸附有机化合物的能力,从而使得溶剂中的反应原料与催化活性组分充分接触,从而提高催化活性。金属有机框架材料具有多孔结构,比表面积大,环境稳定性好,本发明将珍珠岩和zr-mof材料复合作为载体例负载镍和钯,制得的催化剂分散性好,在反应时可很好的将反应原料吸附于其孔内,并与催化剂充分接触反应,制得的产品收率和纯度都较高,且该负载型催化剂稳定性好,使用多次后依然具有良好的催化性能,而且本发明加氢还原过程中无需添加溶剂,有效节约了成本。本发明提供的方法可以实现产品的连续化生产,生产效率高。
具体实施方式
19.下面结合实施例进一步阐述本发明。应理解,这些实施例仅用于说明本发明而不用于限制本发明的范围。
20.实施例1
21.(1)将3g珍珠岩和100ml无水乙醇混合超声处理30min,之后研磨处理30min,然后过滤收集固体,将固体干燥后制得预处理珍珠岩;将3g预处理珍珠岩分散在40mldmf中,制得混合液a,将1.3g氯化锆和0.66g对苯二甲酸溶解在40mldmf中,制得混合液b,将混合液a和混合液b混合常温下搅拌处理2h,之后将得到的反应液转移至高压釜内,升温至120℃反应14h,反应结束后冷却至室温并将反应液进行离心处理,离心得到的沉淀干燥后制得zr-mof/珍珠岩复合材料;
22.(2)将0.16g氯化钯和0.16g氯化镍溶于去离子水中制得混合溶液,然后加入10g上述制得的zr-mof/珍珠岩复合材料,100w下超声处理3h,然后烘干,最后置于马弗炉内,处理气氛为氢气和氮气体积比为1:9的混合气,以1℃/min的升温速率升温至300℃,处理时间为1h,制得催化剂;
23.(3)将2,4-二氟硝基苯加入到装有催化剂的反应器中,2,4-二氟硝基苯、催化剂的用量比控制在1mol:1g,采用氢气置换出反应器中的空气,升温至50℃后通入氢气反应,反应压力控制为0.1mpa,反应时间控制为1h,反应结束后,将反应液过滤除去催化剂,滤液除去溶剂后进行减压蒸馏,制得目标产品。
24.实施例2
25.(1)将4g珍珠岩和100ml无水乙醇混合超声处理30min,之后研磨处理30min,然后过滤收集固体,将固体干燥后制得预处理珍珠岩;将4g预处理珍珠岩分散在40mldmf中,制得混合液a,将1.3g氯化锆和0.66g对苯二甲酸溶解在40mldmf中,制得混合液b,将混合液a和混合液b混合常温下搅拌处理3h,之后将得到的反应液转移至高压釜内,升温至120℃反应15h,反应结束后冷却至室温并将反应液进行离心处理,离心得到的沉淀干燥后制得zr-mof/珍珠岩复合材料;
26.(2)将0.17g氯化钯和0.17g氯化镍溶于去离子水中制得混合溶液,然后加入10g上述制得的zr-mof/珍珠岩复合材料,200w下超声处理2h,然后烘干,最后置于马弗炉内,处理气氛为氢气和氮气体积比为1:9的混合气,以1.5℃/min的升温速率升温至300℃,处理时间为2h,制得催化剂;
27.(3)将2,4-二氟硝基苯加入到装有催化剂的反应器中,2,4-二氟硝基苯、催化剂的用量比控制在1mol:2g,采用氢气置换出反应器中的空气,升温至50℃后通入氢气反应,反应压力控制为0.1mpa,反应时间控制为2h,反应结束后,将反应液过滤除去催化剂,滤液除去溶剂后进行减压蒸馏,制得目标产品。
28.实施例3
29.(1)将5g珍珠岩和100ml无水乙醇混合超声处理30min,之后研磨处理30min,然后过滤收集固体,将固体干燥后制得预处理珍珠岩;将5g预处理珍珠岩分散在40mldmf中,制得混合液a,将1.3g氯化锆和0.66g对苯二甲酸溶解在40mldmf中,制得混合液b,将混合液a和混合液b混合常温下搅拌处理2h,之后将得到的反应液转移至高压釜内,升温至120℃反应16h,反应结束后冷却至室温并将反应液进行离心处理,离心得到的沉淀干燥后制得zr-mof/珍珠岩复合材料;
30.(2)将0.18g氯化钯和0.18g氯化镍溶于去离子水中制得混合溶液,然后加入10g上述制得的zr-mof/珍珠岩复合材料,300w下超声处理2h,然后烘干,最后置于马弗炉内,处理气氛为氢气和氮气体积比为1:9的混合气,以1.5℃/min的升温速率升温至300℃,处理时间为2h,制得催化剂;
31.(3)将2,4-二氟硝基苯加入到装有催化剂的反应器中,2,4-二氟硝基苯、催化剂的用量比控制在1mol:1g,采用氢气置换出反应器中的空气,升温至50℃后通入氢气反应,反应压力控制为0.1mpa,反应时间控制为2h,反应结束后,将反应液过滤除去催化剂,滤液除去溶剂后进行减压蒸馏,制得目标产品。
32.实施例4
33.(1)将5g珍珠岩和100ml无水乙醇混合超声处理30min,之后研磨处理30min,然后过滤收集固体,将固体干燥后制得预处理珍珠岩;将5g预处理珍珠岩分散在40mldmf中,制得混合液a,将1.3g氯化锆和0.66g对苯二甲酸溶解在40mldmf中,制得混合液b,将混合液a和混合液b混合常温下搅拌处理4h,之后将得到的反应液转移至高压釜内,升温至120℃反应16h,反应结束后冷却至室温并将反应液进行离心处理,离心得到的沉淀干燥后制得zr-mof/珍珠岩复合材料;
34.(2)将0.19g氯化钯和0.19g氯化镍溶于去离子水中制得混合溶液,然后加入10g上述制得的zr-mof/珍珠岩复合材料,200w下超声处理2h,然后烘干,最后置于马弗炉内,处理
气氛为氢气和氮气体积比为1:9的混合气,以1℃/min的升温速率升温至300℃,处理时间为1h,制得催化剂;
35.(3)将2,4-二氟硝基苯加入到装有催化剂的反应器中,2,4-二氟硝基苯、催化剂的用量比控制在1mol:1.5g,采用氢气置换出反应器中的空气,升温至50℃后通入氢气反应,反应压力控制为0.1mpa,反应时间控制为1h,反应结束后,将反应液过滤除去催化剂,滤液除去溶剂后进行减压蒸馏,制得目标产品。
36.实施例5
37.(1)将5g珍珠岩和100ml无水乙醇混合超声处理30min,之后研磨处理30min,然后过滤收集固体,将固体干燥后制得预处理珍珠岩;将5g预处理珍珠岩分散在40mldmf中,制得混合液a,将1.3g氯化锆和0.66g对苯二甲酸溶解在40mldmf中,制得混合液b,将混合液a和混合液b混合常温下搅拌处理4h,之后将得到的反应液转移至高压釜内,升温至120℃反应17h,反应结束后冷却至室温并将反应液进行离心处理,离心得到的沉淀干燥后制得zr-mof/珍珠岩复合材料;
38.(2)将0.2g氯化钯和0.2g氯化镍溶于去离子水中制得混合溶液,然后加入10g上述制得的zr-mof/珍珠岩复合材料,300w下超声处理2h,然后烘干,最后置于马弗炉内,处理气氛为氢气和氮气体积比为1:9的混合气,以1.5℃/min的升温速率升温至300℃,处理时间为1h,制得催化剂;
39.(3)将2,4-二氟硝基苯加入到装有催化剂的反应器中,2,4-二氟硝基苯、催化剂的用量比控制在1mol:1g,采用氢气置换出反应器中的空气,升温至50℃后通入氢气反应,反应压力控制为0.1mpa,反应时间控制为1.5h,反应结束后,将反应液过滤除去催化剂,滤液除去溶剂后进行减压蒸馏,制得目标产品。
40.实施例6
41.(1)将4g珍珠岩和100ml无水乙醇混合超声处理30min,之后研磨处理30min,然后过滤收集固体,将固体干燥后制得预处理珍珠岩;将4g预处理珍珠岩分散在40mldmf中,制得混合液a,将1.3g氯化锆和0.66g对苯二甲酸溶解在40mldmf中,制得混合液b,将混合液a和混合液b混合常温下搅拌处理3h,之后将得到的反应液转移至高压釜内,升温至120℃反应15h,反应结束后冷却至室温并将反应液进行离心处理,离心得到的沉淀干燥后制得zr-mof/珍珠岩复合材料;
42.(2)将0.16g氯化钯和0.16g氯化镍溶于去离子水中制得混合溶液,然后加入10g上述制得的zr-mof/珍珠岩复合材料,300w下超声处理2h,然后烘干,最后置于马弗炉内,处理气氛为氢气和氮气体积比为1:9的混合气,以1℃/min的升温速率升温至300℃,处理时间为1h,制得催化剂;
43.(3)将2,4-二氟硝基苯加入到装有催化剂的反应器中,2,4-二氟硝基苯、催化剂的用量比控制在1mol:2g,采用氢气置换出反应器中的空气,升温至50℃后通入氢气反应,反应压力控制为0.1mpa,反应时间控制为1h,反应结束后,将反应液过滤除去催化剂,滤液除去溶剂后进行减压蒸馏,制得目标产品。
44.对比例
45.(1)将1.3g氯化锆和0.66g对苯二甲酸溶解在40mldmf中,制得混合液将得到的混合液转移至高压釜内,升温至120℃反应15h,反应结束后冷却至室温并将反应液进行离心
处理,离心得到的沉淀干燥后制得zr-mof材料;
46.(2)将0.16g氯化钯和0.16g氯化镍溶于去离子水中制得混合溶液,然后加入10g上述制得的zr-mof材料,300w下超声处理2h,然后烘干,最后置于马弗炉内,处理气氛为氢气和氮气体积比为1:9的混合气,以1℃/min的升温速率升温至300℃,处理时间为1h,制得催化剂;
47.(3)将2,4-二氟硝基苯加入到装有催化剂的反应器中,2,4-二氟硝基苯、催化剂的用量比控制在1mol:2g,采用氢气置换出反应器中的空气,升温至50℃后通入氢气反应,反应压力控制为0.1mpa,反应时间控制为1h,反应结束后,将反应液过滤除去催化剂,滤液除去溶剂后进行减压蒸馏,制得目标产品。
48.上述实施例中目标产品的收率如表1所示。
49.表1
[0050][0051]
由上述测试结果可以看出,采用zr-mof/珍珠岩复合材料作为载体制得的催化剂不仅催化活性高,且循环使用多次后催化活性均没有明显的降低,这主要是由于二者相互协同能很好的保护钯、镍活性组分在反应过程中浸出或溶解。
[0052]
此外应理解,在阅读了本发明讲授的内容之后,本领域技术人员可以对本发明作各种改动或修改,这些等价形式同样落于本技术所附权利要求书所限定的范围。
再多了解一些
本文用于企业家、创业者技术爱好者查询,结果仅供参考。