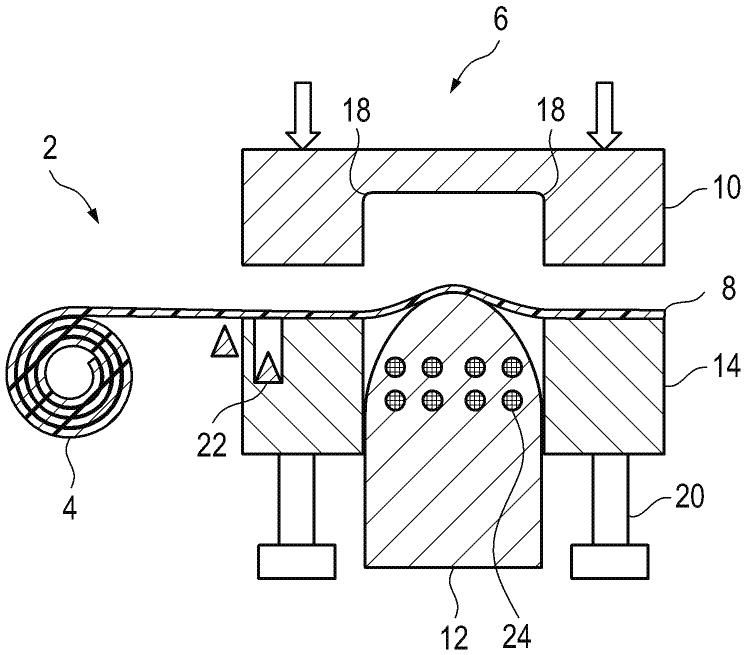
1.本发明涉及一种用于将软包膜深拉成型为软包袋的袋半部的成型工具,具有作为袋半部的阴模的凹模和用于将软包膜成型为凹模的成型压模。本发明还涉及一种用于制造软包袋的方法和一种用于实施该方法的装置。
背景技术:
2.电地或电动地驱动或可驱动的机动车辆,例如电动或混合动力车辆,通常包括电动机,利用该电动机可驱动一个或两个车轴。为了供应电能,电动机通常连接到车辆内部的(高压)电池作为电的能量存储器。
3.特别是电化学的电池在此和在下文中应特别是理解为机动车辆的所谓的二次的电池(二次电池)。在这种(二次)车辆电池的情况下,用过的化学能可通过电的(充电)过程恢复。这种车辆电池例如设计为电化学蓄电池,特别是锂离子蓄电池。为了产生或提供足够高的工作电压,这种车辆电池通常具有至少一个电池单体模块,其中,多个单独的电池单体模块化地连接。
4.电池单体例如设计为电化学的(薄)膜单电池。薄膜单电池具有分层结构,该分层结构带有阴极层(阴极)和阳极层(阳极)以及引入它们之间的隔离层(隔离器)。这些组成部分例如被液态电解质(液体电解质)渗透,该电解质会使得这些组成部分产生能传导离子的连接或产生电荷均衡。通常,在此多个膜单电池作为单电池堆垛上下堆叠地布置。
5.为了保护单电池堆垛免受湿气和/或灰尘的进入,以及另一方面,为了防止化学物质或液体电解质在电池单体损坏的情况下逸出,通常设置单电池壳体作为包壳或包套。单电池外壳例如设计为铝复合膜或铝层压膜,其中,这种柔性的或薄膜状的单电池壳体也称为软包袋或软包膜护套,且具有这种单电池壳体的电池单体也称为软包单电池或软包单体电池。
6.这种软包袋通常由两个沿圆周接合的袋半部制成。袋半部在此通常设计为深拉软包膜,这些深拉软包膜例如采用热封工艺,材料配合地接合成密封的软包袋。
[0007]“深拉工艺”或“深拉”在此并且在下文中尤其应理解为软包膜的拉伸压力成型。深拉例如可以利用成型工具(拉环、压模)、作用介质(气体、液体)或作用能量(磁成型、高速成型)进行。袋半部通常通过借助成型工具的深拉进行制造,其中,利用压制压模或成型压模将软包膜压入凹模中。
[0008]
为了生产尽可能高容量的电池单体或软包单电池,需要在电池堆垛中有尽可能多的电极或膜单电池。因此,有必要尽可能深地成型软包膜或袋半部,以及保持模腔或凹模的半径尽可能小,以便尽可能少地损失单电池中的容量。
[0009]
在拉深时,软包膜发生位移,这会导致强度发生变化。尤其是由铝层压紧器制成的软包膜在此具有较差的深拉能力。在此,随着成型深度的增加,软包膜变薄,即在受力区域中材料厚度减小,这些区域因此更容易产生裂纹。此外,在袋半部的凸缘区域(拐角区域)中形成褶皱。这种裂纹和褶皱降低了电池单体的操作可靠性。
[0010]
为了避免裂纹的形成,压制压模和凹模因此通常具有大半径的圆角区域,以实现必要的深拉深度。这意味着,凹模通常只有大于90
°
的拐角角度。这不利地导致软包袋中可用的结构空间减小,结果是容量损失和/或必须使用更厚或更大的软包单电池。
[0011]
为了避免或减少裂纹的形成,例如可以减小深拉深度,然而,这对于尽可能高容量的软包单电池来说是不期望的。替代地,例如可以对板片保持器或箔保持器进行有针对性的刮削,但这牵涉到耗费大量时间。还可想到,例如在成型时提高软包膜的温度,但其中这会增加工艺成本,并降低层压质量。此外,可以增加软包膜中的铝含量,但其中不利地增加了软包袋的材料成本以及结构重量。
[0012]
从de 10 2013 019 634 a1已知一种用于制造板片成型件的方法,其中,板片材料成型为板片预成型件,并且其中,板片预成型件的板片成型件边缘通过局部的电磁的后成型而形成。在此,板片成型件的预成型和后成型在此在单独的且空间上分开的成型工具中进行。
技术实现要素:
[0013]
本发明的目的是,提出一种特别合适的成型工具,用于将软包膜深拉成型为袋半部。本发明的目的还在于,提出一种特别合适的用于制造软包袋的方法。在此尤其是要实现软包袋的尽可能大的安装空间。本发明的目的还在于,提出一种特别合适的装置以及一种特别合适的软包单电池。
[0014]
根据本发明,关于成型工具的目的通过权利要求1的特征来实现,且关于方法的目的通过权利要求5的特征来实现,以及,关于装置的目的通过权利要求10的特征来实现。有利的设计和改进是从属权利要求的主题。
[0015]
根据本发明的成型工具被设置用于以及适合于并且被设计用于将软包膜深拉成型为软包袋的袋半部。在此,成型工具具有凹模或模腔作为袋半部的阴模,且具有用于将软包膜成型或拉深到凹模中的成型压模或压制压模。可移动的成型压模(深拉压模)因此被设置和设计用于通过压力将软包膜压入或顶压到凹模中,以使软包膜变形或成型。
[0016]
根据本发明,用于磁成型(电磁成型),特别是用于借助于电磁脉冲技术(empt)的成型,即用于电磁脉冲成型(empu)的线圈总成被集成到成型压模中。线圈总成在此特别是集成在成型压模的头部区域或压制区域中。集成在此特别是指,线圈总成布置在成型压模内部,即线圈总成被成型压模包围或包纳。
[0017]
根据本发明,因而将用于制造袋半部的传统的深拉压力机扩展,以包括磁成型的功能。由此可以使用唯一的成型工具,既利用成型工具又利用作用能量,对软包膜进行深拉。
[0018]
由此实现了一种特别合适的成型工具。特别地,由此可以实现借助成型工具且借助作用能量,对软包膜进行组合深拉。优选地,作为工件的软包膜在此首先借助成型压模和凹模进行预成型,然后借助线圈总成,通过磁成型而最终成型为袋半部。换句话说,可以借助于成型压模使得软包膜预成型,并在(唯一的)成型工具中利用empt进行最终成型。由此可实现对软包膜的特别大的深拉深。
[0019]“预成型”或“预变形”在此且在下文中尤其应理解为,将工件或软包膜成型为一种设计(形状、基本形状),然后将其进一步改变或成型为中间产品(预制件)。中间产品在此是
预成型的袋半部。在此和下文中,“最终成型”或“最终变形”尤其应理解为,将中间产品进一步改变为最终产品,也就是说,将预成型的袋半部成型为最终的袋半部。
[0020]
在至少两个相互连接的部分之间的“材料配合”或“材料配合的连接”在此并且在下文中特别是指,相互连接的部分在它们的接触面上通过材料结合或交联(例如由于原子或分子的键合力),必要时在添加剂的作用下而保持在一起。
[0021]
在有利的设计中,凹模具有直角的拐角区域。这意味着,凹模或模腔的拐角区域具有90
°
的(拐角)角度。凹模的拐角区域因此具有小半径,从而可以实现具有用于容纳单电池堆垛的特别大的安装空间的袋半部。换句话说,凹模的矩形拐角区域可以实现成品袋半部的更陡峭的或更小的半径,结果,可实现在软包袋中的更大的安装空间,进而可实现配备它的软包单电池的更高的单电池容量。
[0022]
在此,成型压模优选地在其头部区域上具有相对大的半径,由此避免在借助成型工具进行深拉过程中形成裂纹。这意味着,头部区域的半径被设计得大于凹模的半径。通过成型压模,因而在预成型期间虽然将软包膜压入凹模中,但不将其拐角区域压入凹模中。软包膜在拐角区域中的成型,优选地在随后的最终成型时通过磁成型来进行。
[0023]
为了避免或减少在袋半部的凸缘区域中形成褶皱,在一种可想到的改进中,成型工具具有用于固定软包膜的压紧器,当成型工具关闭或成型压模被压入凹模时,该压紧器将软包膜夹紧地固定在凹模边缘上。
[0024]
在优选的设计中,在压紧器中集成了用于分离或分开软包膜的分离刀。由此可将软包膜切割成或分离成所希望的最终尺寸。特别地,由此可以实现在深拉过程期间或过程中切割软包膜。
[0025]
针对成型工具所述的优点和设计也可有益地转用于该方法,且反之亦然。如果在下面描述方法步骤,则用于装置或成型工具的有利设计尤其是通过将它们设置和设计用于执行这些方法步骤中的一个或多个而产生。
[0026]
根据本发明的方法被规定用于以及适合于和被设计用于制造用于软包单电池的软包袋。为此设置了上述的成型工具,其中,在深拉过程中通过成型压模将软包膜转变为预成型的袋半部(中间产品、预成型部),并且在随后的磁成型过程中借助线圈总成把预成型的袋半部最终成型为袋半部。拉深工艺在此尤其应理解为利用成型工具(成形压模)进行的深拉,其中,磁成型工艺是利用作用能量的深拉。例如,为了制造软包袋,在此把两个如此制造的袋半部沿圆周材料配合地接合成软包袋。材料配合在此例如采用热封工艺来实现。
[0027]
根据该方法,因而采用传统的深拉工艺作为预成型步骤,并辅以磁成型工艺作为最终成型步骤,该最终成型步骤将预成型的软包膜或袋半部,尤其是在凹模的拐角区域和边缘区域中,附加地成型为所希望的最终形状。
[0028]
为了磁成型或empu,线圈总成适当地与脉冲发生器耦合或可耦合,借助脉冲发生器将电流脉冲馈送到线圈总成中。通过脉冲式通电,线圈总成产生脉冲磁场。软包膜在此设计为铝复合膜或铝层压膜,其中,通过脉冲磁场又会感应出电流。因此,流经线圈总成的短暂而高的电流脉冲会在线圈总成的磁场与预成型的软包膜或袋半部的感应电流之间产生洛伦兹力,该洛伦兹力无接触地将预成型件或中间产品成型为袋半部。这意味着,软包膜首先以接触方式借助成型压模成型为预成型的袋半部,然后无接触地借助线圈总成最终成型为袋半部。
[0029]
当借助成型压模进行预成型时,在模腔的拐角区域中利用成型压模的大半径,以便在软包膜不明显减薄的情况下首先在拐角区域中深拉该软包膜。之后,或经过短暂的时间延迟,在拐角区域中借助empu最终成型为最终的、清晰的几何形状。由此可以在模腔或凹模中将软包膜或预成型的袋半部成型为具有90
°
斜角或直角的拐角区域。
[0030]
对于该方法,将线圈总成集成到成型压模中是特别有利的,因为线圈总成因此在预成型之后已经定位在预成型的袋半部的附近。因此,材料(软包膜)在最终成型时被压制成最终形状,而非拉制。
[0031]
通过根据本发明的方法,可实现软包膜的改进的深拉能力,即更大的深拉深度。尤其是,在此减少了袋半部中褶皱的形成,并且最小化了回弹效应,这提高了袋半部的质量,从而提高了软包袋的质量。通过两阶段的成型或深拉工艺,改善了软包袋的工作可靠性和密封性,因为在受力的或关键的(拐角)区域中实现了软包膜的更均匀的材料分布或层厚分布。尤其是,采用该方法可以省去用于减小成型的袋半部的固有应力的预热或后加热,因为这种固有应力通过磁成型或empu被减小或被完全防止。
[0032]
在一种有利的设计中,采用磁成型工艺的最终成型基本上无中断地在采用成型压模的预成型之后进行。这意味着,这些成型工艺直接前后相继地进行,特别是,成型工艺是在不打开成型工具的同时进行的。因此,在预成型件保持于成型压模和凹模之间期间,进行磁成型,使得预成型件离开成型压模而被压入凹模的拐角区域中。这确保了特别减少耗费地且简化地制造袋半部或软包袋。
[0033]
该方法的附加的或另一个方面规定,当软包膜向成型工具进给时,成型压模从成型工具的压紧器突出,从而在软包膜预成型之前,软包膜至少部分地拱起。换句话说,成型工具最初被移动到一个位置,在该位置,它至少部分地从压紧器突出或伸出。因此,成型压模具有比压紧器或反保持器更高的高度。在软包膜进给期间,压模不会移动,因此软包膜在成型工具中定位期间,已经略微预成型,这有助于后续的成型。
[0034]
根据可想到的设计,通过从膜卷上退绕软包膜来进给或定位软包膜。在此,软包膜沿着进给方向从膜卷自动引导至成型工具。在此,软包膜设置在凹模和成型压模之间,并在成型工具中固定和分离。在该方法的有益设计中,成型压模在深拉工艺的过程中被转移或移动到止点位置,其中,特别是当成型压模到达止点位置时,软包膜被分离。
[0035]
因此,软包膜优选不设计为各个膜片的形式,而是设计为环形材料,即看起来或在一定程度上连续的膜带。在此,环形材料尤其是指一种材料带,其宽度尺寸和高度尺寸明显小于其长度尺寸。因此,冲压膜逐个地作为膜带在一定程度上连续地从膜卷上退绕,并且保持不间断,直至其向成型工具进给。在此,“分离”或“分开”尤其是指,从连续材料分离或切断或裁剪膜片。这意味着,分离或裁剪切割在成型工具中进行。换言之,实现了分离和成型的功能集成,由此有利地减少了在软包袋制造中的工艺步骤数量。
[0036]
针对成型工具和/或方法所述的优点和设计也可有益地转用于下面描述的装置,且反之亦然。
[0037]
根据本发明的装置被设置用于以及适合于并且被设计用于制造软包单电池的软包袋。在此,该装置具有如上所述的成型工具,用于分两阶段地将软包膜深拉成袋半部。该装置还具有膜卷,用于为成型工具提供软包膜。成型工具和/或膜卷在此与控制器(即控制单元)连接。以这种方式,实现了一种特别合适的用于制造软包袋的装置。
[0038]
在此,该装置优选地具有处于成型工具下游的接合机构,该接合机构将两个袋半部接合成软包袋。接合机构例如设计为热封机构,其实现在袋半部之间的在边缘侧沿圆周的材料配合的接合连接。
[0039]
在此,控制器通常—采用编程技术和/或电路技术—被设计用于执行上述根据本发明的方法。控制器因此具体地被设计用于从膜卷上退绕软包膜,并将其向成型工具进给,以及控制成型工具的预成型步骤和最终成型步骤。
[0040]
在优选的设计方式中,控制器至少在核心中由具有处理器和数据存储器的微控制器构成,在该微控制器中,以运行软件(固件)的形式采用编程技术实施用于执行根据本发明的方法的功能,从而该方法—必要时与装置用户交互地—当在微控制器中执行运行软件时自动实施。然而,在本发明的范围内,控制器替代地也可以由不可编程的电子器件例如专用集成电路(asic)形成,在该器件中采用电路技术手段实施用于执行根据本发明的方法的功能。
附图说明
[0041]
下面参照附图更详细地解释本发明的实施例。在附图中,以简化的且示意性的图示出了一种用于制造软包袋的方法,该方法采用了具有膜卷和成型工具的装置。其中:图1示出了在成型工具中对软包膜的进给和定位;图2示出了在成型工具中对软包膜的夹紧固定;图3示出了软包膜的分离和预成型;图4示出了软包膜的最终成型;和图5示出了移除袋半部。
[0042]
彼此相应的零件和尺寸在下面总是标有相同的附图标记。
具体实施方式
[0043]
图1至5中所示的装置2具有膜卷4以及成型工具6和未详细示出的用于控制膜卷4和成型工具6的控制器。装置2被设置用于以及适合于并且被设计用于制造软包单电池的软包袋。在膜卷4上缠绕了软包膜8作为环形材料。软包膜8在此设计为铝复合膜或铝层压膜。
[0044]
成型工具6具有凹模或模腔10和可移动的成型压模12以及压紧器或反夹持器14。凹模10被设计为用于未详细示出的软包袋的袋半部16(图5)的阴模。凹模10在此具有基本上直角的拐角区域18。压紧器14与气压弹簧20连接,并具有集成的切割刀或分离刀22。
[0045]
成型压模12具有与凹模10的凹面形状适配的压模头,但在此具有比拐角区域18更大的半径。在压模头中集成了线圈总成24。线圈总成24在此尤其是empt或empu线圈总成。线圈总成24例如与未更详细地示出的脉冲发生器耦合,该脉冲发生器例如由控制器控制。
[0046]
成型工具6可在打开位置(图1)和关闭位置(图2)之间移调。在打开位置,凹模10与压紧器14间隔开,从而软包膜8可以布置在凹模10和压紧器14之间。在关闭位置,凹模10被压到压紧器14上,使得软包膜8被夹紧并固定在工具部件10、14之间的凸缘区域中。
[0047]
在图1所示的方法步骤中,软包膜8从膜卷4上退绕,并沿着未详细标明的进给方向自动地向成型工具6进给。成型压模12在此移动到下压模位置,其中,压模头至少部分地从压紧器14突出。结果,软包膜8在插入成型工具6中时已经具有一定的(预)拱曲。
[0048]
图2示出了随后的方法步骤,其中,成型工具6关闭,即移动到关闭位置。结果,软包膜8被压紧器14和凹模10夹紧地固定。
[0049]
在图3的后续的方法步骤中,通过在凹模10的方向上移动成型压模12来使得软包膜8预成型为预成型的袋半部16'。图3在此示出成型压模12的上止点位置,在该上止点位置,软包膜8或预成型的袋半部16'至少部分地贴靠在凹模10上。在到达该止点位置时,优选同时对袋半部16进行分离切割至目标尺寸的步骤。为此,利用分离刀22使得预成型的袋半部16'与软包膜8的材料带分离。袋半部16'是预成型件,其特别是在拐角区域18中尚未完全成型到凹模10的阴模处。
[0050]
在成型压模12的止点位置,线圈总成24被激活,并且袋半部16'被压入凹模10的拐角区域18中,并且因此通过磁成型在图4所示的方法步骤中最终成型为袋半部16。通过磁成型工艺的最终成型,在此基本上不间断地在利用成型压模12的预成型之后进行,而不必打开成型工具6。
[0051]
最后,在图5所示的方法步骤中,打开成型工具6,并移除成型的软包膜或袋半部16。袋半部16例如被引导至处于成型工具6的下游的接合机构,该接合机构将两个袋半部16接合成软包袋。
[0052]
要求保护的本发明不限于上述实施例。确切地说,本领域技术人员也可以在所公开的权利要求书的范围内,在不脱离所要求保护的本发明的主题的情况下,从中推导出本发明的其他变体。特别地,在不脱离所要求保护的本发明的主题的情况下,还可在所公开的权利要求书的范围内,以其他方式将结合各种不同的实施例描述的所有具体特征组合。
[0053] 附图标记清单2装置4膜卷6成型工具8软包膜10凹模12成型压模14压紧器16、16'袋半部18拐角区域20气压弹簧22分离刀24线圈总成
再多了解一些
本文用于企业家、创业者技术爱好者查询,结果仅供参考。