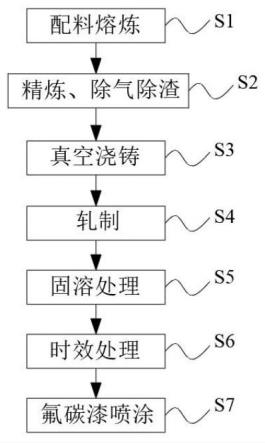
1.本发明涉及铝合金技术领域,具体涉及一种高韧性耐蚀铝合金型材及其制备工艺。
背景技术:
2.通过长期的生产实践和科学实验,人们逐渐以加入合金元素及运用热处理等方法来强化铝,这就得到了一系列的铝合金,添加一定元素形成的合金在保持纯铝质轻等优点的同时还能具有较高的强度;申请号2017102961492的专利公开了一种高韧性耐蚀铝合金型材及其制备工艺,以铝合金型材的总量为基准,按重量百分比计,高韧性耐蚀铝合金型材含有以下元素:zn1.17~3.48%,zr 0.008~0.21%,b 0.89~1.75%,mg 1.25~3.71%,ni 1.21~3.81%,cu0.08~0.36%,ti 0.26~0.84%,ta 0.005~0.12%,微量元素0.01~0.03%,其余为al和不可避免的杂质,该发明提供的高韧性耐蚀铝合金型材中形成了铝化物弥散相,并产生协同作用,起到细化铸态晶粒,强化钉扎位错的作用,从而显著提高了铝合金型材的再结晶温度,改善了铝合金型材的强度、断裂韧性和抗应力腐蚀性;在制备时进行超声处理,不仅可以提高合金熔液中各物质的均匀度,还可以使杂质从熔液中分离出来,从而达到提高铝合金强度的作用;但研究发现还存在以下的技术问题:铝合金型材的强度、韧性和耐腐蚀性有待提高,制备时缺乏配套设备进行高效的除气、除渣滓,针对此方面的技术缺陷,现提出一种解决方案。
技术实现要素:
3.本发明的目的在于提供一种高韧性耐蚀铝合金型材及其制备工艺,用于解决现有技术中铝合金型材的强度、韧性和耐腐蚀性有待提高,制备时缺乏配套设备进行高效的除气、除渣滓的技术问题。
4.本发明的目的可以通过以下技术方案实现:一种高韧性耐蚀铝合金型材,按照如下重量百分比的元素配制铝合金型材的原料:si 0.03~0.12wt%、fe 0.13~0.35wt%、cu 0.05~0.08wt%、mn 0.06~0.15wt%、ni 0.1~0.3wt%、zr 0.025~0.046wt%、cr 0.03~0.08wt%、nd 0.016~0.045wt%、yb 0.02~0.06wt%、y 0.035~0.062wt%,余量为al和不可避免的杂质;其中,元素nd、yb、y的加和含量为0.085~0.155wt%;该铝合金型材按照配料熔炼、精炼、除气除渣、真空浇铸、轧制、固溶处理、时效处理、氟碳漆喷涂制备得到。
5.一种高韧性耐蚀铝合金型材的制备工艺,包括以下步骤:s1、配料熔炼:按照如下重量百分比的元素,si 0.03~0.12wt%、fe 0.13~0.35wt%、cu 0.05~0.08wt%、mn 0.06~0.15wt%、ni 0.1~0.3wt%、zr 0.025~0.046wt%、cr 0.03~0.08wt%、nd 0.016~0.045wt%、yb 0.02~0.06wt%、y 0.035~0.062wt%,余量为al和不可避免
的杂质,元素nd、yb、y的加和含量为0.085~0.155wt%;选择铝锭、铝硅合金、铝铁合金、铝铜合金、铝锰合金、铝镍合金、铝锆合金、铝铬合金,加入熔炼除渣浇铸设备的熔炼炉内,升温至740~760℃,保温熔炼30~50min后,加入铝稀土合金,升温至980~1000℃,保温搅拌熔炼得到熔炼液;s2、精炼、除气除渣:待熔炼液温度降低至760~780℃后,向熔炼炉20内加入熔炼液质量0.16~0.22%的精炼剂,排出熔炼液内的氧气,并通过电动排渣机构排出氧化铝渣滓,得到精炼熔液;s3、真空浇铸:精炼熔液进入浇铸炉30内,水冷降温至680~700℃后进行真空连续浇铸,得到铸坯;s4、轧制:铸坯进行连续轧制,控制入轧的温度为520~540℃,终轧温度为260~280℃,得到轧制型材;其中,轧制的速度为4.2~4.8m/min,水冷降温至35~45℃;s5、固溶处理:将轧制型材按照5~10℃/min的速度升温至480~500℃,保温30~50min,再以3~6℃/min的速度升温至520~535℃,保温15~25min,高压水喷淋淬火降温至30~40℃,得到固溶处理型材;s6、时效处理:固溶处理型材升温至105~115℃时效处理10~12小时,得到时效处理型材;s7、氟碳漆喷涂:时效处理型材的外表面喷涂氟碳漆得到铝合金型材。
6.进一步的,步骤s1升温、保温熔炼的具体过程为:液压油缸通过其活塞杆驱动控制箱沿限位板上下滑动,调节石墨加热棒伸入熔炼炉内的位置;启动驱动电机,驱动电机驱动石墨加热棒转动,石墨加热棒升温后对原料进行保温熔炼。
7.进一步的,步骤s2排出熔炼液内的氧气的具体过程为:开启氮气钢瓶,氮气钢瓶内的氮气经过气体增压泵增压后,由进气管进入石墨加热棒内腔,从多个出气口喷出至熔液内,排出熔液内的氧气。
8.进一步的,步骤s2电动排渣机构排出氧化铝渣滓的具体过程为:伺服电机驱动转动轴转动,转动轴带动转动筒转动,转动筒外围的棘爪也随之转动,对内啮合棘轮施力,使得内啮合棘轮带动扒渣板转动,将漂浮在熔液表面的氧化铝等渣滓排入排渣腔内,在排渣腔内冷凝收集。
9.进一步的,所述精炼剂由na3alf6、mgcl2、naf、na2sif6、alf3、nacl按照质量比1:2:1:1:2:3混合粉碎而成。
10.进一步的,所述氟碳漆的制备方法如下:按照重量份,将45~65份氟碳树脂、10~20份乙烯基酯树脂、6~12份乙酸乙酯、5~10份环己酮添加至反应釜中,搅拌30~50min,加入3~8份滑石粉、1~3份二硫化钼、2~6份羧甲基纤维素钠后,混合均匀,过滤即可。
11.进一步的,所述熔炼除渣浇铸设备包括机架、熔炼炉、浇铸炉和可调加热除气机构,可调加热除气机构包括控制箱、液压油缸和石墨加热棒,液压油缸的活塞杆贯穿固定板设置,固定板的两侧设有限位板,限位板向下延伸与第一安装板固定连接,活塞杆的底端与控制箱的顶部连接,液压油缸通过其活塞杆驱动控制箱沿限位板上下滑动;控制箱的内腔通过卡槽安装有若干个石墨加热棒,石墨加热棒朝熔炼炉内腔延伸;卡槽的上方安装有驱动电机,石墨加热棒的外周向外延伸设置有多个出气口,石墨加热棒的内腔延伸设置有进气管,进气管随着石墨加热棒的转动位置不发生变化;进气管延伸出控制箱外与气体增压
泵的出气端连接,气体增压泵的进气端通过出气管与氮气钢瓶连接。
12.进一步的,熔炼炉的顶部一侧设有排渣腔,熔炼炉上靠近排渣腔处设有电动排渣机构;电动排渣机构包括伺服电机、转动筒和内啮合棘轮,转动筒的轴心设有转动轴,转动轴贯穿熔炼炉设置,转动筒的外围转动连接有若干个棘爪,棘爪与内啮合棘轮的内围接触;伺服电机从熔炼炉的外部伸入后与转动轴连接,内啮合棘轮的外围环形阵列分布多个弯折状的扒渣板,扒渣板的外缘靠近排渣腔。
13.本发明具备下述有益效果:1、本发明的高韧性耐蚀铝合金型材,铝通过其他金属元素和稀土元素形成了铝化物弥散相,产生协同作用,提高了铝合金型材的强度、断裂韧性和耐腐蚀性,稀土元素nd、yb、y加入熔液后明显细化了合金组织,生成al2y、al2nd、al3yb等新的稀土相,有效提高了铝合金型材的力学性能,进一步提高铝合金型材的强度、断裂韧性和耐腐蚀性。
14.2、制备工艺中熔炼、精炼、除气、除渣步骤均通过熔炼除渣浇铸设备完成,提高了精炼熔液的纯度和各元素的分散均匀度;氟碳漆由氟碳树脂、乙烯基酯树脂作为主要成分,添加溶剂乙酸乙酯、环己酮,填料滑石粉、羧甲基纤维素钠,润滑剂二硫化钼制备得到,在铝合金型材表面喷涂成膜后,含氟侧链和乙烯基集中在涂膜表面,形成疏水疏油的基团,起到良好的防水、防油、耐腐蚀的效果。
15.3、熔炼除渣浇铸设备中,可调加热除气机构进行石墨加热棒的位置调节,对熔液进行加热搅拌,并进行氧气的迅速排出,保障了熔液的纯度和精炼质量;棘爪棘轮的配合方式保持氧化铝渣滓的自动化规律排出,提高了氧化铝渣滓的去除效率。
附图说明
16.为了更清楚地说明本发明实施例或现有技术中的技术方案,下面将对实施例或现有技术描述中所需要使用的附图作简单地介绍,显而易见地,下面描述中的附图仅仅是本发明的一些实施例,对于本领域普通技术人员来讲,在不付出创造性劳动的前提下,还可以根据这些附图获得其他的附图。
17.图1为本发明实施例中高韧性耐蚀铝合金型材的制备工艺流程图;图2为本发明实施例中熔炼除渣浇铸设备的结构示意图;图3为本发明实施例中可调加热除气机构的三维图;图4为本发明实施例中控制箱与石墨加热棒的装配结构剖面图;图5为本发明实施例中熔炼炉与浇铸炉的剖面图。
18.附图标记:10、机架;11、底板;12、支撑板;13、第一安装板;14、第二安装板;15、加强板;20、熔炼炉;21、排渣腔;22、伺服电机;23、转动筒;24、内啮合棘轮;25、转动轴;26、棘爪;27、扒渣板;30、浇铸炉;31、水冷腔;32、出水管;33、进水管;34、水泵;35、排料阀;40、可调加热除气机构;41、控制箱;42、液压油缸;43、石墨加热棒;44、固定板;45、限位板;46、卡槽;47、驱动电机;48、出气口;49、进气管;50、气体增压泵;51、出气管;52、氮气钢瓶。
具体实施方式
19.下面将结合实施例对本发明的技术方案进行清楚、完整地描述,显然,所描述的实施例仅仅是本发明一部分实施例,而不是全部的实施例。基于本发明中的实施例,本领域普
通技术人员在没有作出创造性劳动前提下所获得的所有其它实施例,都属于本发明保护的范围。
20.实施例1如图2所示,本实施例提供一种熔炼除渣浇铸设备,用于高韧性耐蚀铝合金型材制备过程中的熔炼、除气除渣、浇铸工序,包括机架10、熔炼炉20、浇铸炉30和可调加热除气机构40,机架10设于熔炼炉20的两侧,浇铸炉30设于熔炼炉20的下方,可调加热除气机构40设于机架10的内部及熔炼炉20的顶部。熔炼炉20用于熔炼、精炼高韧性耐蚀铝合金型材的原料得到精炼熔液并扒渣除去氧化铝渣滓,浇铸炉30用于对精炼熔液进行冷却浇铸,可调加热除气机构40用于对熔液进行可调节的加热、去除氧气。
21.具体地,机架10包括底板11、支撑板12、第一安装板13和第二安装板14,底板11对称设置在熔炼炉20的底部两侧,支撑板12设于底板11的上方,第一安装板13套设在熔炼炉20的顶部外围且外周与支撑板12连接,第二安装板14设于第一安装板13的上方。第一安装板13与第二安装板14之间连接有加强板15。机架10中通过支撑板12和第一安装板13对熔炼炉20进行支撑,通过支撑板12和第二安装板14对可调加热除气机构40进行支撑,使得熔炼炉20和可调加热除气机构40保持稳定的运行。
22.如图2-4所示,可调加热除气机构40包括控制箱41、液压油缸42和石墨加热棒43,液压油缸42的活塞杆贯穿固定板44设置,固定板44的两侧设有限位板45,限位板45向下延伸与第一安装板13固定连接,活塞杆的底端与控制箱41的顶部连接,液压油缸42通过其活塞杆驱动控制箱41沿限位板45上下滑动。控制箱41的内腔通过卡槽46安装有若干个石墨加热棒43,石墨加热棒43朝熔炼炉20内腔延伸。卡槽46的上方安装有驱动电机47,石墨加热棒43的外周向外延伸设置有多个出气口48,石墨加热棒43的内腔延伸设置有进气管49,进气管49随着石墨加热棒43的转动位置不发生变化。进气管49延伸出控制箱41外与气体增压泵50的出气端连接,气体增压泵50的进气端通过出气管51与氮气钢瓶52连接。
23.可调加热除气机构40中,液压油缸42通过其活塞杆驱动控制箱41沿限位板45上下滑动,便于调节石墨加热棒43伸入熔炼炉20内的位置;当调节好石墨加热棒43的位置后,启动驱动电机47,驱动电机47驱动石墨加热棒43转动,石墨加热棒43升温后对原料进行熔化搅拌;开启氮气钢瓶52后,氮气钢瓶52内的氮气经过气体增压泵50增压后,由进气管49进入石墨加热棒43内腔,从多个出气口48喷出至熔液内,排出熔液内的氧气。可调加热除气机构40能够进行石墨加热棒43的位置调节,对熔液进行加热搅拌,并进行氧气的迅速排出,保障了熔液的纯度和精炼质量。
24.如图5所示,熔炼炉20的顶部一侧设有排渣腔21,熔炼炉20上靠近排渣腔21处设有电动排渣机构。电动排渣机构包括伺服电机22、转动筒23和内啮合棘轮24,转动筒23的轴心设有转动轴25,转动轴25贯穿熔炼炉20设置,转动筒23的外围转动连接有若干个棘爪26,棘爪26与内啮合棘轮24的内围接触。伺服电机22从熔炼炉20的外部伸入后与转动轴25连接,内啮合棘轮24的外围环形阵列分布多个弯折状的扒渣板27,扒渣板27的外缘靠近排渣腔21。电动排渣机构中,当伺服电机22驱动转动轴25转动后,转动轴25带动转动筒23转动,转动筒23外围的棘爪26也随之转动,对内啮合棘轮24施力,使得内啮合棘轮24带动扒渣板27规律的顺时针或逆时针转动,将漂浮在熔液表面的氧化铝等渣滓排入排渣腔21内,在排渣腔21内冷凝收集。棘爪棘轮的配合方式保持氧化铝渣滓的自动化规律排出,提高了氧化铝
渣滓的去除效率。
25.浇铸炉30内设有水冷腔31,水冷腔31的一侧设有出水管32,水冷腔31的一侧通过进水管33连接有水泵34,浇铸炉30的底部设有排料阀35。熔炼炉20内精炼得到的精炼熔液进入浇铸炉30内后,水泵34将冷却水经进水管33输送入水冷腔31内,换热后从出水管32排出,冷却水循环提高了对精炼熔液的降温速率,减少浇铸所需时间。
26.实施例2如图1-5所示,本实施例提供一种高韧性耐蚀铝合金型材的制备工艺,包括以下步骤:s1、配料熔炼:按照如下重量百分比的元素,si 0.08wt%、fe 0.25wt%、cu 0.07wt%、mn 0.09wt%、ni 0.15wt%、zr 0.033wt%、cr 0.06wt%、nd 0.028wt%、yb 0.04wt%、y 0.053wt%,余量为al和不可避免的杂质;选择铝锭、铝硅合金、铝铁合金、铝铜合金、铝锰合金、铝镍合金、铝锆合金、铝铬合金,加入熔炼除渣浇铸设备的熔炼炉20内,升温至755℃,保温熔炼45min后,加入铝稀土合金,升温至995℃,保温搅拌熔炼得到熔炼液;升温、保温熔炼的具体过程为:液压油缸42通过其活塞杆驱动控制箱41沿限位板45上下滑动,调节石墨加热棒43伸入熔炼炉20内的位置;启动驱动电机47,驱动电机47驱动石墨加热棒43转动,石墨加热棒43升温后对原料进行保温熔炼。
27.s2、精炼、除气除渣:待熔炼液温度降低至772℃后,向熔炼炉20内加入熔炼液质量0.18%的精炼剂,排出熔炼液内的氧气,并通过电动排渣机构排出氧化铝渣滓,得到精炼熔液;排出熔炼液内的氧气的具体过程为:开启氮气钢瓶52,氮气钢瓶52内的氮气经过气体增压泵50增压后,由进气管49进入石墨加热棒43内腔,从多个出气口48喷出至熔液内,排出熔液内的氧气;电动排渣机构排出氧化铝渣滓的具体过程为:伺服电机22驱动转动轴25转动,转动轴25带动转动筒23转动,转动筒23外围的棘爪26也随之转动,对内啮合棘轮24施力,使得内啮合棘轮24带动扒渣板27转动,将漂浮在熔液表面的氧化铝等渣滓排入排渣腔21内,在排渣腔21内冷凝收集;精炼剂由na3alf6、mgcl2、naf、na2sif6、alf3、nacl按照质量比1:2:1:1:2:3混合粉碎而成。
28.s3、真空浇铸:精炼熔液进入浇铸炉30内,水冷降温至688℃后进行真空连续浇铸,得到铸坯;s4、轧制:铸坯进行连续轧制,控制入轧的温度为525℃,终轧温度为272℃,得到轧制型材;其中,轧制的速度为4.6m/min,水冷降温至38℃;s5、固溶处理:将轧制型材按照8℃/min的速度升温至492℃,保温36min,再以5℃/min的速度升温至530℃,保温22min,高压水喷淋淬火降温至35℃,得到固溶处理型材;s6、时效处理:固溶处理型材升温至108℃时效处理11小时,得到时效处理型材;s7、氟碳漆喷涂:时效处理型材的外表面喷涂氟碳漆得到铝合金型材。其中,氟碳漆的制备方法如下:按照重量份,将53份氟碳树脂、16份乙烯基酯树脂、10份乙酸乙酯、7份环己酮添加至反应釜中,搅拌45min,加入6份滑石粉、1.5份二硫化钼、4.5份羧甲基纤维素钠后,混合均匀,过滤即可。
29.实施例3如图1-5所示,本实施例提供一种高韧性耐蚀铝合金型材的制备工艺,包括以下步骤:s1、配料熔炼:按照如下重量百分比的元素,si 0.11wt%、fe 0.28wt%、cu 0.06wt%、mn 0.13wt%、ni 0.18wt%、zr 0.035wt%、cr 0.07wt%、nd 0.034wt%、yb 0.05wt%、y 0.052wt%,余量为al和不可避免的杂质;选择铝锭、铝硅合金、铝铁合金、铝铜合金、铝锰合金、铝镍合金、铝锆合金、铝铬合金,加入熔炼除渣浇铸设备的熔炼炉20内,升温至752℃,保温熔炼45min后,加入铝稀土合金,升温至992℃,保温搅拌熔炼得到熔炼液;s2、精炼、除气除渣:待熔炼液温度降低至775℃后,向熔炼炉20内加入熔炼液质量0.19%的精炼剂,排出熔炼液内的氧气,并通过电动排渣机构排出氧化铝渣滓,得到精炼熔液;精炼剂由na3alf6、mgcl2、naf、na2sif6、alf3、nacl按照质量比1:2:1:1:2:3混合粉碎而成。
30.s3、真空浇铸:精炼熔液进入浇铸炉30内,水冷降温至695℃后进行真空连续浇铸,得到铸坯;s4、轧制:铸坯进行连续轧制,控制入轧的温度为535℃,终轧温度为275℃,得到轧制型材;其中,轧制的速度为4.3m/min,水冷降温至42℃;s5、固溶处理:将轧制型材按照8℃/min的速度升温至493℃,保温47min,再以5℃/min的速度升温至530℃,保温20min,高压水喷淋淬火降温至35℃,得到固溶处理型材;s6、时效处理:固溶处理型材升温至112℃时效处理10.5小时,得到时效处理型材;s7、氟碳漆喷涂:时效处理型材的外表面喷涂氟碳漆得到铝合金型材。其中,氟碳漆的制备方法如下:按照重量份,将60份氟碳树脂、18份乙烯基酯树脂、11份乙酸乙酯、9份环己酮添加至反应釜中,搅拌46min,加入7份滑石粉、2份二硫化钼、5份羧甲基纤维素钠后,混合均匀,过滤即可。
31.实施例4如图1-5所示,本实施例提供一种高韧性耐蚀铝合金型材的制备工艺,包括以下步骤:s1、配料熔炼:按照如下重量百分比的元素,si 0.07wt%、fe 0.32wt%、cu 0.07wt%、mn 0.08wt%、ni 0.25wt%、zr 0.036wt%、cr 0.06wt%、nd 0.038wt%、yb 0.05wt%、y 0.057wt%,余量为al和不可避免的杂质;选择铝锭、铝硅合金、铝铁合金、铝铜合金、铝锰合金、铝镍合金、铝锆合金、铝铬合金,加入熔炼除渣浇铸设备的熔炼炉20内,升温至758℃,保温熔炼47min后,加入铝稀土合金,升温至993℃,保温搅拌熔炼得到熔炼液;s2、精炼、除气除渣:待熔炼液温度降低至772℃后,向熔炼炉20内加入熔炼液质量0.21%的精炼剂,排出熔炼液内的氧气,并通过电动排渣机构排出氧化铝渣滓,得到精炼熔液;精炼剂由na3alf6、mgcl2、naf、na2sif6、alf3、nacl按照质量比1:2:1:1:2:3混合粉碎而成。
32.s3、真空浇铸:精炼熔液进入浇铸炉30内,水冷降温至695℃后进行真空连续浇铸,得到铸坯;s4、轧制:铸坯进行连续轧制,控制入轧的温度为536℃,终轧温度为275℃,得到轧制型材;其中,轧制的速度为4.6m/min,水冷降温至42℃;
s5、固溶处理:将轧制型材按照9℃/min的速度升温至495℃,保温45min,再以4.5℃/min的速度升温至530℃,保温25min,高压水喷淋淬火降温至40℃,得到固溶处理型材;s6、时效处理:固溶处理型材升温至105~115℃时效处理10~12小时,得到时效处理型材;s7、氟碳漆喷涂:时效处理型材的外表面喷涂氟碳漆得到铝合金型材。其中,氟碳漆的制备方法如下:按照重量份,将63份氟碳树脂、18份乙烯基酯树脂、11份乙酸乙酯、9份环己酮添加至反应釜中,搅拌45min,加入7份滑石粉、2.5份二硫化钼、5份羧甲基纤维素钠后,混合均匀,过滤即可。
33.对比例1本对比例与实施例2的区别在于,未添加稀土元素yb。
34.对比例2本对比例与实施例2的区别在于,未添加精炼剂。
35.对比例3本对比例与实施例2的区别在于,未喷涂氟碳漆。
36.性能测试对实施例2-4、对比例1-3制备的铝合金型材进行了抗拉强度、屈服强度、伸长率、耐腐蚀性能的测试,其中耐腐蚀性能测试采用60wt%氢氧化钠溶液、40wt%盐酸溶液产生的循环雾气进行侵蚀,测试铝合金型材发生明显锈蚀所需的时间,具体结果见下表:由上表可以看出,本发明实施例制备的铝合金型材,抗拉强度、屈服强度、伸长率均优于对比例,且耐腐蚀性能优于对比例,具有良好的强度、韧性和耐腐蚀性能。对比例1由于未添加稀土元素yb,无法生成al3yb稀土相,力学性能显著降低;对比例2由于未添加精炼剂,铝合金熔液的纯度降低,力学性能和耐腐蚀性能降低;对比例3由于未喷涂氟碳漆,无法形成防水、防油、耐腐蚀的表面膜层,耐腐蚀性能显著降低。
37.以上内容仅仅是对本发明结构所作的举例和说明,所属本技术领域的技术人员对所描述的具体实施例做各种各样的修改或补充或采用类似的方式替代,只要不偏离发明的结构或者超越本权利要求书所定义的范围,均应属于本发明的保护范围。
38.在本说明书的描述中,参考术语“一个实施例”、“示例”、“具体示例”等的描述意指结合该实施例或示例描述的具体特征、结构、材料或者特点包含于本发明的至少一个实施例或示例中。在本说明书中,对上述术语的示意性表述不一定指的是相同的实施例或示例。而且,描述的具体特征、结构、材料或者特点可以在任何的一个或多个实施例或示例中以合适的方式结合。
39.以上公开的本发明优选实施例只是用于帮助阐述本发明。优选实施例并没有详尽
叙述所有的细节,也不限制该发明仅为的具体实施方式。显然,根据本说明书的内容,可作很多的修改和变化。本说明书选取并具体描述这些实施例,是为了更好地解释本发明的原理和实际应用,从而使所属技术领域技术人员能很好地理解和利用本发明。本发明仅受权利要求书及其全部范围和等效物的限制。
再多了解一些
本文用于企业家、创业者技术爱好者查询,结果仅供参考。