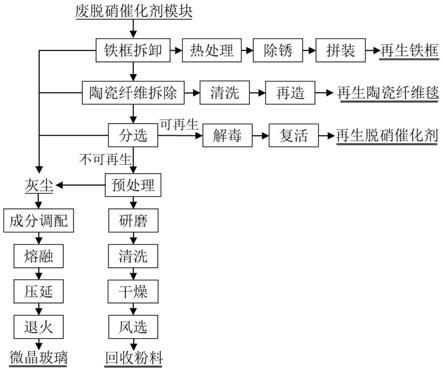
1.本发明涉及一种废脱硝催化剂模块全组分综合利用的方法,属于烟气脱硝及材料循环利用领域。
背景技术:
2.选择性催化还原(scr)技术是实现工业烟气no
x
超低排放的重要技术,其使用的脱硝催化剂易受烟气冲刷及有害组分毒化而失活,因而催化剂使用寿命较短。失活后的废脱硝催化剂是《国家危险废物名录》规定的危险废物,其环境风险极大,但循环再利用价值极高。2014年,生态环境部发布《关于加强废烟气脱硝催化剂监管工作的通知》,要求提高废烟气脱硝催化剂的再生和利用处置能力,鼓励优先进行再生,对不能再生的废脱硝催化剂实施安全处理。
3.现有废脱硝催化剂再生及资源回收再用技术仅能再生机械强度良好、失活不严重的脱硝催化剂,而资源回收技术也仅回收处理钒、钨、钛组分,对于铁框、陶瓷纤维纸等部分未能进行回收再用。具体针对废脱硝催化剂的资源回收,通常采用复杂的碱熔工艺将钒、钨、钛氧化物转化为盐,再溶于溶液中分步分离出钒、钨、钛组分,制备成偏钒酸铵、钨酸钠及二氧化钛产品,或采用简单的水洗、打浆、干燥或者粉料直接回用。采用碱熔的工艺复杂、能耗高,而简单水洗回用则产品质量差。
4.专利cn109536721a公开了一种废弃scr脱硝催化剂资源化综合利用的方法,包括预处理、破碎、磨制、超声波强化碱浸、液固分离、离子交换、解吸并化学沉淀、清洗洪干,可有选择的回收钒、钨、钛作为相关产业的原料,但回收钒、钨过程十分复杂,且回收产品主要为钙盐、镁盐,不能保级回用于脱硝催化剂的制备。专利cn108687105a公开了一种对废弃scr脱硝催化剂的综合利用方法,包括预处理、粉碎、提钒、提钨及不溶渣烘干,回收后的原料可以直接用于新催化剂的生产,但该工艺回收钒、钨过程复杂、耗水量大。
技术实现要素:
5.针对上述问题,本发明提供一种废脱硝催化剂模块全组分综合利用的方法,将废脱硝催化剂模块拆解,分别资源化利用铁框、陶瓷纤维、脱硝催化剂及灰尘。其中铁框材料通过调质处理恢复力学性能,并重新拼装成再生铁框,陶瓷纤维再造回用;催化剂通过分选分别进行再生和资源回收。机械强度良好的催化剂再生为再生催化剂,破损严重的催化剂通过酸浸湿磨去除有害组分,同时提高比表面积,并通过风选将回收粉料分成低密度和高密度两个品质等级;灰尘资源化利用制备微晶玻璃,最终实现了废脱硝催化剂模块的全组分综合利用。
6.本发明是通过以下技术方案实现的:
7.一种废脱硝催化剂模块全组分综合利用的方法,分为铁框再生、陶瓷纤维回用、可再生催化剂的再生、不可再生催化剂的回收及灰尘制备微晶玻璃5条资源化路线,实现废脱硝催化剂模块全组分的综合回收利用。
8.所述铁框再生是将拆卸后的铁框经热处理、除锈、拼装获得再生铁框,所述陶瓷纤维回用是将陶瓷纤维拆除后经清洗、再造获得再生陶瓷纤维毯。所述可再生催化剂的再生是将分选后的机械性能良好的催化剂经解毒、复活得到再生脱硝催化剂;分选标准是根据脱硝催化剂破损情况分选为可再生与不可再生催化剂;分选条件为蜂窝式催化剂迎风端磨损平均深度≤30mm,且贯穿性孔数≤5个则为可再生催化剂,否则为不可再生催化剂;平板式催化剂迎风端膏料磨损长度≤50mm,单板磨损面积小于整个单板面积的10%则为可再生催化剂,否则为不可再生催化剂。所述灰尘制备微晶玻璃是将废脱硝催化剂模块的灰尘收集,经成分调配、熔融、压延、退火制备获得微晶玻璃板材。
9.进一步地,铁框拆卸为首先将废脱硝催化剂模块的铁框迎风面与背风面钢板条拆除,然后将四周钢板沿焊缝切割;拆除迎风面或背风面一侧的钢板条后即可取出脱硝催化剂,当铁框整体保存良好时可修复后直接再用。
10.所述再生铁框的热处理为对拆卸后铁框材料进行淬火和回火处理,所述淬火为将铁框材料加热至820-960℃,保温15-60min,然后进行水淬;所述回火处理为将淬火后的铁框材料加热至450-550℃,保温15-60min,然后空冷至室温;
11.所述除锈为首先对热处理后的铁框材料进行质量检测,确保达到脱硝催化剂铁框强度要求,经检测合格的铁框材料进行表面除锈,除锈方法采用喷射、抛丸、化学除锈法中的一种;
12.所述拼装为将除锈后的铁框材料重新焊接、组装形成再生铁框。
13.进一步地,陶瓷纤维拆除为铁框拆卸后取出脱硝催化剂,并将催化剂外包堵风与抗震的陶瓷纤维毯拆除。所述陶瓷纤维的清洗步骤为对拆除后的陶瓷纤维进行水洗以去除部分杂质;
14.所述陶瓷纤维的再造步骤为将清洗后的陶瓷纤维作为原料经打浆、除渣、成型、干燥制备成再生陶瓷纤维毯,实现陶瓷纤维的回用。
15.进一步地,催化剂再生的解毒是将催化剂单元条置于2-10wt.%的naoh溶液,溶液温度40-90℃,清洗20-60min,沿催化剂单元条轴向45
°
角方向增加25-35khz的超声波,然后置于0.5-2wt.%的稀硫酸溶液中清洗5-15min,然后烘干。
16.复活是将解毒后的催化剂在钛酸丁酯溶液中浸渍1-5min,然后在恒温恒湿房中放置30-120min,烘干后浸渍于偏钒酸铵溶液中负载活性组分,焙烧后即获得再生脱硝催化剂。放入恒温恒湿房可促进钛酸丁酯水解形成tio2,既可增强催化剂机械强度,又能增大催化剂表面材料的比表面积,使活性组分负载量增大。
17.进一步地,不可再生催化剂的回收步骤包括预处理、研磨、清洗、干燥、风选得到回收粉料。
18.所述预处理包括破碎、筛分、水洗步骤,是将不可再生催化剂破碎至2-150mm,进一步筛分去除碎料中的灰尘,筛网孔径控制为1-10mm,筛分后进行水洗以去除碎料表面灰尘。破碎过程控制碎料尺寸为2-150mm,可保证筛分过程较好地去除催化剂中的灰尘、砂粒等,且破碎过程简单,筛分后清洗可洗去催化剂碎料表面的灰尘,且清洗废水可循环利用。
19.进一步地,对废脱硝催化剂破碎料添加酸液进行湿磨,所述酸液中硫酸、硝酸和水的质量份数之比为(5-40):(1-20):100,酸液与催化剂物料的质量份数之比为(65-135):100,研磨控制物料粒度达到d90≤15um。添加酸液进行研磨可溶解废催化剂中的na、k、ca、
mg、al、as、hg等有害金属离子,研磨过程造成升温将促进溶解有害组分反应的进行。钒、钨、钛氧化物被酸溶解难度大于上述有害金属离子,因此可保证先发生除杂反应,随着酸浓度的增加可依次逐步溶解部分钒、钨氧化物及tio2进行表面侵蚀,提高tio2载体的比表面积、孔容和孔径。
20.进一步地,对研磨后浆料进行清洗,在研磨后的浆液中加入1-3倍质量的水并充分搅拌,然后进行过滤,如此反复1-3次,最终过滤后物料含水率≤80%;所述干燥为将清洗、过滤后物料进行干燥,干燥后粉料含水率≤5%。
21.进一步地,对粉料进行风选,将干燥后物料输送至风选系统,设置风速为0.5-5m/s,根据沉降末速的差异设置第一出料口和第二出料口,所述第一出料口获得密度较大、颗粒较大的重质粉料,所述第二出料口获得密度较小、颗粒较小的轻质粉料。第一出料口粉料主要用于25
×
25孔数以下的催化剂或板式催化剂的制备,第二出料口粉料主要用于25
×
25孔数以上的催化剂的制备。
22.进一步地,灰尘制备微晶玻璃的成分调配是将废催化剂孔道、表面富含si、na、ca的灰尘与铁框除锈产生的富含fe的组分混合,形成易熔融玻璃组分与易形核析晶的微晶组分;所述熔融是将灰尘体系加热至1000-1400℃熔融,获得熔融体系;所述压延是将熔融体系冷却至600-1000℃通过压延辊筒进行压制,获得玻璃板材胚料;所述退火为将板材胚料在400-600℃保温1-4小时,空冷至室温获得微晶玻璃板材。废脱硝催化剂中的灰尘主要成分为si、na等组分,能形成良好的玻璃网络体系,而铁框除锈过程的铁锈废料是良好的形核剂,将两种废料结合进行调配,形成制备微晶玻璃的良好原料。
23.以上工艺回收的粉料未采用复杂的工艺分离钒、钨、钛,而是通过调节酸的用量有效去除杂质,保留有价组分实现循环利用。
24.本发明的有益技术效果是:
25.(1)将废脱硝催化剂模块的有价组分全部实现循环利用,结合综合利用过程筛分、清洗出的灰尘、污泥高值化利用即可实现全组分综合利用;
26.(2)粉料回收采用酸浸研磨工艺可有效去除杂质,并保留钒、钨、钛有价组分,同时提高回收粉料的比表面积;
27.(3)铁框材料回收再用采用淬火 回火工艺调质,恢复材料力学性能,保障再生铁框使用安全;
28.(4)对废催化剂模块中的催化剂进行分选,可再生的单元优先进行再生,避免不加区分地进行破碎、回收。
附图说明
29.图1为本发明方法工艺流程图。
具体实施方式
30.为了使本发明的目的、技术方案及优点更加清楚明白,以下结合具体实施例,对本发明进行进一步详细描述。应当理解,此处所描述的具体实施例仅用于解释本发明,并不用于限定本发明,对本领域技术人员来说没有这些细节部分的描述也可以完全理解本发明。本发明涵盖任何由权利要求定义的在本发明的精髓和范围上做的替代、修改、等效方法以
及方案。
31.实施案例1
32.一种废脱硝催化剂模块全组分综合利用的方法,分为铁框再生、陶瓷纤维回用、可再生催化剂的再生、不可再生催化剂的回收及灰尘制备微晶玻璃5条资源化路线,实现废脱硝催化剂模块全组分的综合回收利用。铁框再生的淬火为将铁框材料加热至820℃,保温60min,然后进行水淬,回火为将淬火后的铁框材料加热至450℃,保温60min,然后空冷至室温,除锈采用喷射除锈法中的一种,除锈后的铁框材料重新焊接、组装形成再生铁框。陶瓷纤维清洗后经打浆、除渣、成型、干燥制备成再生陶瓷纤维毯,实现陶瓷纤维的回用。
33.将可再生催化剂单元条置于2wt.%的naoh溶液,溶液温度90℃,清洗40min,沿催化剂单元条轴向45
°
角方向增加25khz的超声波,然后置于0.5wt.%的稀硫酸溶液中清洗15min,然后烘干;进一步将催化剂在钛酸丁酯溶液中浸渍1min,然后在恒温恒湿房中放置30min,烘干后浸渍于偏钒酸铵溶液中负载活性组分,焙烧后即获得再生脱硝催化剂。将不可再生催化剂破碎至2-10mm,进一步筛分去除碎料中的灰尘,筛网孔径控制为1mm,筛分后进行水洗以去除碎料表面灰尘,进一步添加酸液进行湿磨。酸液中硫酸、硝酸和水的质量份数之比为5:1:100,酸液与催化剂物料的质量份数之比为65:100,研磨控制物料粒度达到d90≤15um。进一步在研磨后的浆液中加入1倍质量的水并充分搅拌,然后进行过滤,如此反复3次,最终过滤后物料含水率≤80%,进一步干燥后粉料含水率≤5%。进一步进行风选,设置风速为5m/s,第一出料口获得密度较大、颗粒较大的重质粉料,第二出料口获得密度较小、颗粒较小的轻质粉料。
34.灰尘制备微晶玻璃将废脱硝催化剂模块中的灰尘收集与除锈产生的锈渣进行混合,加热至1000℃熔融,冷却至600℃通过压延辊筒进行压制,获得玻璃板材胚料,进一步在400℃保温4小时,空冷至室温获得微晶玻璃板材。
35.实施案例2
36.一种废脱硝催化剂模块全组分综合利用的方法,分为铁框再生、陶瓷纤维回用、可再生催化剂的再生、不可再生催化剂的回收及灰尘制备微晶玻璃5条资源化路线,实现废脱硝催化剂模块全组分的综合回收利用。铁框再生的淬火为将铁框材料加热至830℃,保温55min,然后进行水淬,回火为将淬火后的铁框材料加热至460℃,保温55min,然后空冷至室温,除锈采用抛丸除锈法中的一种,除锈后的铁框材料重新焊接、组装形成再生铁框。陶瓷纤维清洗后经打浆、除渣、成型、干燥制备成再生陶瓷纤维毯,实现陶瓷纤维的回用。
37.将可再生催化剂单元条置于3wt.%的naoh溶液,溶液温度85℃,清洗45min,沿催化剂单元条轴向45
°
角方向增加26khz的超声波,然后置于0.6wt.%的稀硫酸溶液中清洗14min,然后烘干;进一步将催化剂在钛酸丁酯溶液中浸渍2min,然后在恒温恒湿房中放置50min,烘干后浸渍于偏钒酸铵溶液中负载活性组分,焙烧后即获得再生脱硝催化剂。将不可再生催化剂破碎至2-50mm,进一步筛分去除碎料中的灰尘,筛网孔径控制为1mm,筛分后进行水洗以去除碎料表面灰尘,进一步添加酸液进行湿磨。酸液中硫酸、硝酸和水的质量份数之比为10:2:100,酸液与催化剂物料的质量份数之比为70:100,研磨控制物料粒度达到d90≤14um。进一步在研磨后的浆液中加入1倍质量的水并充分搅拌,然后进行过滤,如此反复3次,最终过滤后物料含水率≤80%,进一步干燥后粉料含水率≤5%。进一步进行风选,设置风速为4.5m/s,第一出料口获得密度较大、颗粒较大的重质粉料,第二出料口获得密度
较小、颗粒较小的轻质粉料。
38.灰尘制备微晶玻璃将废脱硝催化剂模块中的灰尘收集与除锈产生的锈渣进行混合,加热至1000℃熔融,冷却至800℃通过压延辊筒进行压制,获得玻璃板材胚料,进一步在450℃保温3小时,空冷至室温获得微晶玻璃板材。
39.实施案例3
40.一种废脱硝催化剂模块全组分综合利用的方法,分为铁框再生、陶瓷纤维回用、可再生催化剂的再生、不可再生催化剂的回收及灰尘制备微晶玻璃5条资源化路线,实现废脱硝催化剂模块全组分的综合回收利用。铁框再生的淬火为将铁框材料加热至840℃,保温50min,然后进行水淬,回火为将淬火后的铁框材料加热至470℃,保温50min,然后空冷至室温,除锈采用化学除锈法中的一种,除锈后的铁框材料重新焊接、组装形成再生铁框。陶瓷纤维清洗后经打浆、除渣、成型、干燥制备成再生陶瓷纤维毯,实现陶瓷纤维的回用。
41.将可再生催化剂单元条置于4wt.%的naoh溶液,溶液温度80℃,清洗50min,沿催化剂单元条轴向45
°
角方向增加27khz的超声波,然后置于0.8wt.%的稀硫酸溶液中清洗13min,然后烘干;进一步将催化剂在钛酸丁酯溶液中浸渍3min,然后在恒温恒湿房中放置70min,烘干后浸渍于偏钒酸铵溶液中负载活性组分,焙烧后即获得再生脱硝催化剂。将不可再生催化剂破碎至2-100mm,进一步筛分去除碎料中的灰尘,筛网孔径控制为2mm,筛分后进行水洗以去除碎料表面灰尘,进一步添加酸液进行湿磨。酸液中硫酸、硝酸和水的质量份数之比为10:5:100,酸液与催化剂物料的质量份数之比为75:100,研磨控制物料粒度达到d90≤13um。进一步在研磨后的浆液中加入1.5倍质量的水并充分搅拌,然后进行过滤,如此反复2次,最终过滤后物料含水率≤80%,进一步干燥后粉料含水率≤5%。进一步进行风选,设置风速为4m/s,第一出料口获得密度较大、颗粒较大的重质粉料,第二出料口获得密度较小、颗粒较小的轻质粉料。
42.灰尘制备微晶玻璃将废脱硝催化剂模块中的灰尘收集与除锈产生的锈渣进行混合,加热至1000℃熔融,冷却至1000℃通过压延辊筒进行压制,获得玻璃板材胚料,进一步在500℃保温2小时,空冷至室温获得微晶玻璃板材。
43.实施案例4
44.一种废脱硝催化剂模块全组分综合利用的方法,分为铁框再生、陶瓷纤维回用、可再生催化剂的再生、不可再生催化剂的回收及灰尘制备微晶玻璃5条资源化路线,实现废脱硝催化剂模块全组分的综合回收利用。铁框再生的淬火为将铁框材料加热至850℃,保温45min,然后进行水淬,回火为将淬火后的铁框材料加热至480℃,保温45min,然后空冷至室温,除锈采用喷射除锈法中的一种,除锈后的铁框材料重新焊接、组装形成再生铁框。陶瓷纤维清洗后经打浆、除渣、成型、干燥制备成再生陶瓷纤维毯,实现陶瓷纤维的回用。
45.将可再生催化剂单元条置于5wt.%的naoh溶液,溶液温度75℃,清洗55min,沿催化剂单元条轴向45
°
角方向增加28khz的超声波,然后置于1wt.%的稀硫酸溶液中清洗12min,然后烘干;进一步将催化剂在钛酸丁酯溶液中浸渍4min,然后在恒温恒湿房中放置90min,烘干后浸渍于偏钒酸铵溶液中负载活性组分,焙烧后即获得再生脱硝催化剂。将不可再生催化剂破碎至2-150mm,进一步筛分去除碎料中的灰尘,筛网孔径控制为2mm,筛分后进行水洗以去除碎料表面灰尘,进一步添加酸液进行湿磨。酸液中硫酸、硝酸和水的质量份数之比为15:5:100,酸液与催化剂物料的质量份数之比为80:100,研磨控制物料粒度达到
d90≤12um。进一步在研磨后的浆液中加入1.5倍质量的水并充分搅拌,然后进行过滤,如此反复2次,最终过滤后物料含水率≤75%,进一步干燥后粉料含水率≤5%。进一步进行风选,设置风速为3.5m/s,第一出料口获得密度较大、颗粒较大的重质粉料,第二出料口获得密度较小、颗粒较小的轻质粉料。
46.灰尘制备微晶玻璃将废脱硝催化剂模块中的灰尘收集与除锈产生的锈渣进行混合,加热至1100℃熔融,冷却至700℃通过压延辊筒进行压制,获得玻璃板材胚料,进一步在500℃保温2小时,空冷至室温获得微晶玻璃板材。
47.实施案例5
48.一种废脱硝催化剂模块全组分综合利用的方法,分为铁框再生、陶瓷纤维回用、可再生催化剂的再生、不可再生催化剂的回收及灰尘制备微晶玻璃5条资源化路线,实现废脱硝催化剂模块全组分的综合回收利用。铁框再生的淬火为将铁框材料加热至860℃,保温40min,然后进行水淬,回火为将淬火后的铁框材料加热至490℃,保温40min,然后空冷至室温,除锈采用抛丸除锈法中的一种,除锈后的铁框材料重新焊接、组装形成再生铁框。陶瓷纤维清洗后经打浆、除渣、成型、干燥制备成再生陶瓷纤维毯,实现陶瓷纤维的回用。
49.将可再生催化剂单元条置于6wt.%的naoh溶液,溶液温度70℃,清洗60min,沿催化剂单元条轴向45
°
角方向增加29khz的超声波,然后置于1.2wt.%的稀硫酸溶液中清洗11min,然后烘干;进一步将催化剂在钛酸丁酯溶液中浸渍5min,然后在恒温恒湿房中放置120min,烘干后浸渍于偏钒酸铵溶液中负载活性组分,焙烧后即获得再生脱硝催化剂。将不可再生催化剂破碎至5-50mm,进一步筛分去除碎料中的灰尘,筛网孔径控制为3mm,筛分后进行水洗以去除碎料表面灰尘,进一步添加酸液进行湿磨。酸液中硫酸、硝酸和水的质量份数之比为20:1:100,酸液与催化剂物料的质量份数之比为85:100,研磨控制物料粒度达到d90≤11um。进一步在研磨后的浆液中加入1.5倍质量的水并充分搅拌,然后进行过滤,如此反复2次,最终过滤后物料含水率≤75%,进一步干燥后粉料含水率≤5%。进一步进行风选,设置风速为3m/s,第一出料口获得密度较大、颗粒较大的重质粉料,第二出料口获得密度较小、颗粒较小的轻质粉料。
50.灰尘制备微晶玻璃将废脱硝催化剂模块中的灰尘收集与除锈产生的锈渣进行混合,加热至1100℃熔融,冷却至900℃通过压延辊筒进行压制,获得玻璃板材胚料,进一步在550℃保温1小时,空冷至室温获得微晶玻璃板材。
51.实施案例6
52.一种废脱硝催化剂模块全组分综合利用的方法,分为铁框再生、陶瓷纤维回用、可再生催化剂的再生、不可再生催化剂的回收及灰尘制备微晶玻璃5条资源化路线,实现废脱硝催化剂模块全组分的综合回收利用。铁框再生的淬火为将铁框材料加热至870℃,保温35min,然后进行水淬,回火为将淬火后的铁框材料加热至500℃,保温35min,然后空冷至室温,除锈采用化学除锈法中的一种,除锈后的铁框材料重新焊接、组装形成再生铁框。陶瓷纤维清洗后经打浆、除渣、成型、干燥制备成再生陶瓷纤维毯,实现陶瓷纤维的回用。
53.将可再生催化剂单元条置于7wt.%的naoh溶液,溶液温度65℃,清洗20min,沿催化剂单元条轴向45
°
角方向增加30khz的超声波,然后置于1.4wt.%的稀硫酸溶液中清洗10min,然后烘干;进一步将催化剂在钛酸丁酯溶液中浸渍1min,然后在恒温恒湿房中放置40min,烘干后浸渍于偏钒酸铵溶液中负载活性组分,焙烧后即获得再生脱硝催化剂。将不
可再生催化剂破碎至5-100mm,进一步筛分去除碎料中的灰尘,筛网孔径控制为4mm,筛分后进行水洗以去除碎料表面灰尘,进一步添加酸液进行湿磨。酸液中硫酸、硝酸和水的质量份数之比为25:10:100,酸液与催化剂物料的质量份数之比为90:100,研磨控制物料粒度达到d90≤10um。进一步在研磨后的浆液中加入2倍质量的水并充分搅拌,然后进行过滤,如此反复2次,最终过滤后物料含水率≤75%,进一步干燥后粉料含水率≤4%。进一步进行风选,设置风速为2.5m/s,第一出料口获得密度较大、颗粒较大的重质粉料,第二出料口获得密度较小、颗粒较小的轻质粉料。
54.灰尘制备微晶玻璃将废脱硝催化剂模块中的灰尘收集与除锈产生的锈渣进行混合,加热至1100℃熔融,冷却至1000℃通过压延辊筒进行压制,获得玻璃板材胚料,进一步在600℃保温1小时,空冷至室温获得微晶玻璃板材。
55.实施案例7
56.一种废脱硝催化剂模块全组分综合利用的方法,分为铁框再生、陶瓷纤维回用、可再生催化剂的再生、不可再生催化剂的回收及灰尘制备微晶玻璃5条资源化路线,实现废脱硝催化剂模块全组分的综合回收利用。铁框再生的淬火为将铁框材料加热至880℃,保温30min,然后进行水淬,回火为将淬火后的铁框材料加热至510℃,保温30min,然后空冷至室温,除锈采用喷射除锈法中的一种,除锈后的铁框材料重新焊接、组装形成再生铁框。陶瓷纤维清洗后经打浆、除渣、成型、干燥制备成再生陶瓷纤维毯,实现陶瓷纤维的回用。
57.将可再生催化剂单元条置于8wt.%的naoh溶液,溶液温度60℃,清洗25min,沿催化剂单元条轴向45
°
角方向增加31khz的超声波,然后置于1.6wt.%的稀硫酸溶液中清洗9min,然后烘干;进一步将催化剂在钛酸丁酯溶液中浸渍2min,然后在恒温恒湿房中放置60min,烘干后浸渍于偏钒酸铵溶液中负载活性组分,焙烧后即获得再生脱硝催化剂。将不可再生催化剂破碎至5-150mm,进一步筛分去除碎料中的灰尘,筛网孔径控制为5mm,筛分后进行水洗以去除碎料表面灰尘,进一步添加酸液进行湿磨。酸液中硫酸、硝酸和水的质量份数之比为25:15:100,酸液与催化剂物料的质量份数之比为95:100,研磨控制物料粒度达到d90≤9um。进一步在研磨后的浆液中加入2倍质量的水并充分搅拌,然后进行过滤,如此反复2次,最终过滤后物料含水率≤70%,进一步干燥后粉料含水率≤4%。进一步进行风选,设置风速为2m/s,第一出料口获得密度较大、颗粒较大的重质粉料,第二出料口获得密度较小、颗粒较小的轻质粉料。
58.灰尘制备微晶玻璃将废脱硝催化剂模块中的灰尘收集与除锈产生的锈渣进行混合,加热至1200℃熔融,冷却至650℃通过压延辊筒进行压制,获得玻璃板材胚料,进一步在600℃保温1小时,空冷至室温获得微晶玻璃板材。
59.实施案例8
60.一种废脱硝催化剂模块全组分综合利用的方法,分为铁框再生、陶瓷纤维回用、可再生催化剂的再生、不可再生催化剂的回收及灰尘制备微晶玻璃5条资源化路线,实现废脱硝催化剂模块全组分的综合回收利用。铁框再生的淬火为将铁框材料加热至890℃,保温25min,然后进行水淬,回火为将淬火后的铁框材料加热至520℃,保温25min,然后空冷至室温,除锈采用喷射除锈法中的一种,除锈后的铁框材料重新焊接、组装形成再生铁框。陶瓷纤维清洗后经打浆、除渣、成型、干燥制备成再生陶瓷纤维毯,实现陶瓷纤维的回用。
61.将可再生催化剂单元条置于9wt.%的naoh溶液,溶液温度55℃,清洗30min,沿催
化剂单元条轴向45
°
角方向增加32khz的超声波,然后置于1.8wt.%的稀硫酸溶液中清洗8min,然后烘干;进一步将催化剂在钛酸丁酯溶液中浸渍3min,然后在恒温恒湿房中放置80min,烘干后浸渍于偏钒酸铵溶液中负载活性组分,焙烧后即获得再生脱硝催化剂。将不可再生催化剂破碎至10-50mm,进一步筛分去除碎料中的灰尘,筛网孔径控制为5mm,筛分后进行水洗以去除碎料表面灰尘,进一步添加酸液进行湿磨。酸液中硫酸、硝酸和水的质量份数之比为25:20:100,酸液与催化剂物料的质量份数之比为100:100,研磨控制物料粒度达到d90≤8um。进一步在研磨后的浆液中加入2倍质量的水并充分搅拌,然后进行过滤,如此反复2次,最终过滤后物料含水率≤70%,进一步干燥后粉料含水率≤4%。进一步进行风选,设置风速为1.5m/s,第一出料口获得密度较大、颗粒较大的重质粉料,第二出料口获得密度较小、颗粒较小的轻质粉料。
62.灰尘制备微晶玻璃将废脱硝催化剂模块中的灰尘收集与除锈产生的锈渣进行混合,加热至1200℃熔融,冷却至750℃通过压延辊筒进行压制,获得玻璃板材胚料,进一步在500℃保温3小时,空冷至室温获得微晶玻璃板材。
63.实施案例9
64.一种废脱硝催化剂模块全组分综合利用的方法,分为铁框再生、陶瓷纤维回用、可再生催化剂的再生、不可再生催化剂的回收及灰尘制备微晶玻璃5条资源化路线,实现废脱硝催化剂模块全组分的综合回收利用。铁框再生的淬火为将铁框材料加热至900℃,保温20min,然后进行水淬,回火为将淬火后的铁框材料加热至530℃,保温20min,然后空冷至室温,除锈采用抛丸除锈法中的一种,除锈后的铁框材料重新焊接、组装形成再生铁框。陶瓷纤维清洗后经打浆、除渣、成型、干燥制备成再生陶瓷纤维毯,实现陶瓷纤维的回用。
65.将可再生催化剂单元条置于10wt.%的naoh溶液,溶液温度50℃,清洗35min,沿催化剂单元条轴向45
°
角方向增加33khz的超声波,然后置于2wt.%的稀硫酸溶液中清洗7min,然后烘干;进一步将催化剂在钛酸丁酯溶液中浸渍4min,然后在恒温恒湿房中放置100min,烘干后浸渍于偏钒酸铵溶液中负载活性组分,焙烧后即获得再生脱硝催化剂。将不可再生催化剂破碎至10-100mm,进一步筛分去除碎料中的灰尘,筛网孔径控制为6mm,筛分后进行水洗以去除碎料表面灰尘,进一步添加酸液进行湿磨。酸液中硫酸、硝酸和水的质量份数之比为30:1:100,酸液与催化剂物料的质量份数之比为105:100,研磨控制物料粒度达到d90≤7um。进一步在研磨后的浆液中加入2.5倍质量的水并充分搅拌,然后进行过滤,如此反复1次,最终过滤后物料含水率≤70%,进一步干燥后粉料含水率≤4%。进一步进行风选,设置风速为1m/s,第一出料口获得密度较大、颗粒较大的重质粉料,第二出料口获得密度较小、颗粒较小的轻质粉料。
66.灰尘制备微晶玻璃将废脱硝催化剂模块中的灰尘收集与除锈产生的锈渣进行混合,加热至1200℃熔融,冷却至850℃通过压延辊筒进行压制,获得玻璃板材胚料,进一步在520℃保温4小时,空冷至室温获得微晶玻璃板材。
67.实施案例10
68.一种废脱硝催化剂模块全组分综合利用的方法,分为铁框再生、陶瓷纤维回用、可再生催化剂的再生、不可再生催化剂的回收及灰尘制备微晶玻璃5条资源化路线,实现废脱硝催化剂模块全组分的综合回收利用。铁框再生的淬火为将铁框材料加热至910℃,保温15min,然后进行水淬,回火为将淬火后的铁框材料加热至540℃,保温15min,然后空冷至室
温,除锈采用化学除锈法中的一种,除锈后的铁框材料重新焊接、组装形成再生铁框。陶瓷纤维清洗后经打浆、除渣、成型、干燥制备成再生陶瓷纤维毯,实现陶瓷纤维的回用。
69.将可再生催化剂单元条置于2.5wt.%的naoh溶液,溶液温度45℃,清洗40min,沿催化剂单元条轴向45
°
角方向增加34khz的超声波,然后置于0.5wt.%的稀硫酸溶液中清洗6min,然后烘干;进一步将催化剂在钛酸丁酯溶液中浸渍5min,然后在恒温恒湿房中放置110min,烘干后浸渍于偏钒酸铵溶液中负载活性组分,焙烧后即获得再生脱硝催化剂。将不可再生催化剂破碎至10-150mm,进一步筛分去除碎料中的灰尘,筛网孔径控制为6mm,筛分后进行水洗以去除碎料表面灰尘,进一步添加酸液进行湿磨。酸液中硫酸、硝酸和水的质量份数之比为30:15:100,酸液与催化剂物料的质量份数之比为110:100,研磨控制物料粒度达到d90≤6um。进一步在研磨后的浆液中加入2.5倍质量的水并充分搅拌,然后进行过滤,如此反复1次,最终过滤后物料含水率≤65%,进一步干燥后粉料含水率≤4%。进一步进行风选,设置风速为0.5m/s,第一出料口获得密度较大、颗粒较大的重质粉料,第二出料口获得密度较小、颗粒较小的轻质粉料。
70.灰尘制备微晶玻璃将废脱硝催化剂模块中的灰尘收集与除锈产生的锈渣进行混合,加热至1300℃熔融,冷却至950℃通过压延辊筒进行压制,获得玻璃板材胚料,进一步在540℃保温2小时,空冷至室温获得微晶玻璃板材。
71.实施案例11
72.一种废脱硝催化剂模块全组分综合利用的方法,分为铁框再生、陶瓷纤维回用、可再生催化剂的再生、不可再生催化剂的回收及灰尘制备微晶玻璃5条资源化路线,实现废脱硝催化剂模块全组分的综合回收利用。铁框再生的淬火为将铁框材料加热至920℃,保温15min,然后进行水淬,回火为将淬火后的铁框材料加热至550℃,保温15min,然后空冷至室温,除锈采用喷射除锈法中的一种,除锈后的铁框材料重新焊接、组装形成再生铁框。陶瓷纤维清洗后经打浆、除渣、成型、干燥制备成再生陶瓷纤维毯,实现陶瓷纤维的回用。
73.将可再生催化剂单元条置于3.5wt.%的naoh溶液,溶液温度40℃,清洗45min,沿催化剂单元条轴向45
°
角方向增加35khz的超声波,然后置于0.7wt.%的稀硫酸溶液中清洗5min,然后烘干;进一步将催化剂在钛酸丁酯溶液中浸渍1min,然后在恒温恒湿房中放置35min,烘干后浸渍于偏钒酸铵溶液中负载活性组分,焙烧后即获得再生脱硝催化剂。将不可再生催化剂破碎至20-100mm,进一步筛分去除碎料中的灰尘,筛网孔径控制为7mm,筛分后进行水洗以去除碎料表面灰尘,进一步添加酸液进行湿磨。酸液中硫酸、硝酸和水的质量份数之比为30:20:100,酸液与催化剂物料的质量份数之比为115:100,研磨控制物料粒度达到d90≤5um。进一步在研磨后的浆液中加入2.5倍质量的水并充分搅拌,然后进行过滤,如此反复1次,最终过滤后物料含水率≤65%,进一步干燥后粉料含水率≤3%。进一步进行风选,设置风速为1m/s,第一出料口获得密度较大、颗粒较大的重质粉料,第二出料口获得密度较小、颗粒较小的轻质粉料。
74.灰尘制备微晶玻璃将废脱硝催化剂模块中的灰尘收集与除锈产生的锈渣进行混合,加热至1300℃熔融,冷却至1000℃通过压延辊筒进行压制,获得玻璃板材胚料,进一步在560℃保温1小时,空冷至室温获得微晶玻璃板材。
75.实施案例12
76.一种废脱硝催化剂模块全组分综合利用的方法,分为铁框再生、陶瓷纤维回用、可
再生催化剂的再生、不可再生催化剂的回收及灰尘制备微晶玻璃5条资源化路线,实现废脱硝催化剂模块全组分的综合回收利用。铁框再生的淬火为将铁框材料加热至930℃,保温35min,然后进行水淬,回火为将淬火后的铁框材料加热至485℃,保温35min,然后空冷至室温,除锈采用抛丸除锈法中的一种,除锈后的铁框材料重新焊接、组装形成再生铁框。陶瓷纤维清洗后经打浆、除渣、成型、干燥制备成再生陶瓷纤维毯,实现陶瓷纤维的回用。
77.将可再生催化剂单元条置于4.5wt.%的naoh溶液,溶液温度50℃,清洗50min,沿催化剂单元条轴向45
°
角方向增加26khz的超声波,然后置于0.9wt.%的稀硫酸溶液中清洗12min,然后烘干;进一步将催化剂在钛酸丁酯溶液中浸渍2min,然后在恒温恒湿房中放置55min,烘干后浸渍于偏钒酸铵溶液中负载活性组分,焙烧后即获得再生脱硝催化剂。将不可再生催化剂破碎至30-80mm,进一步筛分去除碎料中的灰尘,筛网孔径控制为8mm,筛分后进行水洗以去除碎料表面灰尘,进一步添加酸液进行湿磨。酸液中硫酸、硝酸和水的质量份数之比为35:5:100,酸液与催化剂物料的质量份数之比为120:100,研磨控制物料粒度达到d90≤15um。进一步在研磨后的浆液中加入2.5倍质量的水并充分搅拌,然后进行过滤,如此反复1次,最终过滤后物料含水率≤65%,进一步干燥后粉料含水率≤3%。进一步进行风选,设置风速为1.5m/s,第一出料口获得密度较大、颗粒较大的重质粉料,第二出料口获得密度较小、颗粒较小的轻质粉料。
78.灰尘制备微晶玻璃将废脱硝催化剂模块中的灰尘收集与除锈产生的锈渣进行混合,加热至1300℃熔融,冷却至800℃通过压延辊筒进行压制,获得玻璃板材胚料,进一步在550℃保温1小时,空冷至室温获得微晶玻璃板材。
79.实施案例13
80.一种废脱硝催化剂模块全组分综合利用的方法,分为铁框再生、陶瓷纤维回用、可再生催化剂的再生、不可再生催化剂的回收及灰尘制备微晶玻璃5条资源化路线,实现废脱硝催化剂模块全组分的综合回收利用。铁框再生的淬火为将铁框材料加热至940℃,保温30min,然后进行水淬,回火为将淬火后的铁框材料加热至495℃,保温30min,然后空冷至室温,除锈采用化学除锈法中的一种,除锈后的铁框材料重新焊接、组装形成再生铁框。陶瓷纤维清洗后经打浆、除渣、成型、干燥制备成再生陶瓷纤维毯,实现陶瓷纤维的回用。
81.将可再生催化剂单元条置于5.5wt.%的naoh溶液,溶液温度60℃,清洗55min,沿催化剂单元条轴向45
°
角方向增加27khz的超声波,然后置于1.1wt.%的稀硫酸溶液中清洗13min,然后烘干;进一步将催化剂在钛酸丁酯溶液中浸渍3min,然后在恒温恒湿房中放置75min,烘干后浸渍于偏钒酸铵溶液中负载活性组分,焙烧后即获得再生脱硝催化剂。将不可再生催化剂破碎至40-120mm,进一步筛分去除碎料中的灰尘,筛网孔径控制为9mm,筛分后进行水洗以去除碎料表面灰尘,进一步添加酸液进行湿磨。酸液中硫酸、硝酸和水的质量份数之比为35:15:100,酸液与催化剂物料的质量份数之比为125:100,研磨控制物料粒度达到d90≤12um。进一步在研磨后的浆液中加入3倍质量的水并充分搅拌,然后进行过滤,如此反复1次,最终过滤后物料含水率≤60%,进一步干燥后粉料含水率≤3%。进一步进行风选,设置风速为2m/s,第一出料口获得密度较大、颗粒较大的重质粉料,第二出料口获得密度较小、颗粒较小的轻质粉料。
82.灰尘制备微晶玻璃将废脱硝催化剂模块中的灰尘收集与除锈产生的锈渣进行混合,加热至1400℃熔融,冷却至600℃通过压延辊筒进行压制,获得玻璃板材胚料,进一步在
530℃保温2小时,空冷至室温获得微晶玻璃板材。
83.实施案例14
84.一种废脱硝催化剂模块全组分综合利用的方法,分为铁框再生、陶瓷纤维回用、可再生催化剂的再生、不可再生催化剂的回收及灰尘制备微晶玻璃5条资源化路线,实现废脱硝催化剂模块全组分的综合回收利用。铁框再生的淬火为将铁框材料加热至950℃,保温25min,然后进行水淬,回火为将淬火后的铁框材料加热至505℃,保温25min,然后空冷至室温,除锈采用喷射除锈法中的一种,除锈后的铁框材料重新焊接、组装形成再生铁框。陶瓷纤维清洗后经打浆、除渣、成型、干燥制备成再生陶瓷纤维毯,实现陶瓷纤维的回用。
85.将可再生催化剂单元条置于6.5wt.%的naoh溶液,溶液温度70℃,清洗60min,沿催化剂单元条轴向45
°
角方向增加28khz的超声波,然后置于1.3wt.%的稀硫酸溶液中清洗14min,然后烘干;进一步将催化剂在钛酸丁酯溶液中浸渍4min,然后在恒温恒湿房中放置95min,烘干后浸渍于偏钒酸铵溶液中负载活性组分,焙烧后即获得再生脱硝催化剂。将不可再生催化剂破碎至50-100mm,进一步筛分去除碎料中的灰尘,筛网孔径控制为9mm,筛分后进行水洗以去除碎料表面灰尘,进一步添加酸液进行湿磨。酸液中硫酸、硝酸和水的质量份数之比为40:5:100,酸液与催化剂物料的质量份数之比为130:100,研磨控制物料粒度达到d90≤9um。进一步在研磨后的浆液中加入3倍质量的水并充分搅拌,然后进行过滤,如此反复1次,最终过滤后物料含水率≤60%,进一步干燥后粉料含水率≤3%。进一步进行风选,设置风速为1.5m/s,第一出料口获得密度较大、颗粒较大的重质粉料,第二出料口获得密度较小、颗粒较小的轻质粉料。
86.灰尘制备微晶玻璃将废脱硝催化剂模块中的灰尘收集与除锈产生的锈渣进行混合,加热至1400℃熔融,冷却至1000℃通过压延辊筒进行压制,获得玻璃板材胚料,进一步在520℃保温3小时,空冷至室温获得微晶玻璃板材。
87.实施案例15
88.一种废脱硝催化剂模块全组分综合利用的方法,分为铁框再生、陶瓷纤维回用、可再生催化剂的再生、不可再生催化剂的回收及灰尘制备微晶玻璃5条资源化路线,实现废脱硝催化剂模块全组分的综合回收利用。铁框再生的淬火为将铁框材料加热至960℃,保温20min,然后进行水淬,回火为将淬火后的铁框材料加热至515℃,保温20min,然后空冷至室温,除锈采用喷射除锈法中的一种,除锈后的铁框材料重新焊接、组装形成再生铁框。陶瓷纤维清洗后经打浆、除渣、成型、干燥制备成再生陶瓷纤维毯,实现陶瓷纤维的回用。
89.将可再生催化剂单元条置于7.5wt.%的naoh溶液,溶液温度80℃,清洗20min,沿催化剂单元条轴向45
°
角方向增加29khz的超声波,然后置于1.5wt.%的稀硫酸溶液中清洗15min,然后烘干;进一步将催化剂在钛酸丁酯溶液中浸渍5min,然后在恒温恒湿房中放置115min,烘干后浸渍于偏钒酸铵溶液中负载活性组分,焙烧后即获得再生脱硝催化剂。将不可再生催化剂破碎至50-150mm,进一步筛分去除碎料中的灰尘,筛网孔径控制为10mm,筛分后进行水洗以去除碎料表面灰尘,进一步添加酸液进行湿磨。酸液中硫酸、硝酸和水的质量份数之比为40:10:100,酸液与催化剂物料的质量份数之比为135:100,研磨控制物料粒度达到d90≤6um。进一步在研磨后的浆液中加入3倍质量的水并充分搅拌,然后进行过滤,如此反复2次,最终过滤后物料含水率≤60%,进一步干燥后粉料含水率≤3%。进一步进行风选,设置风速为3m/s,第一出料口获得密度较大、颗粒较大的重质粉料,第二出料口获得密
度较小、颗粒较小的轻质粉料。
90.灰尘制备微晶玻璃将废脱硝催化剂模块中的灰尘收集与除锈产生的锈渣进行混合,加热至1400℃熔融,冷却至750℃通过压延辊筒进行压制,获得玻璃板材胚料,进一步在510℃保温4小时,空冷至室温获得微晶玻璃板材。
91.实施案例16
92.一种废脱硝催化剂模块全组分综合利用的方法,分为铁框再生、陶瓷纤维回用、可再生催化剂的再生、不可再生催化剂的回收及灰尘制备微晶玻璃5条资源化路线,实现废脱硝催化剂模块全组分的综合回收利用。铁框再生的淬火为将铁框材料加热至915℃,保温15min,然后进行水淬,回火为将淬火后的铁框材料加热至525℃,保温15min,然后空冷至室温,除锈采用抛丸除锈法中的一种,除锈后的铁框材料重新焊接、组装形成再生铁框。陶瓷纤维清洗后经打浆、除渣、成型、干燥制备成再生陶瓷纤维毯,实现陶瓷纤维的回用。
93.将可再生催化剂单元条置于8.5wt.%的naoh溶液,溶液温度90℃,清洗20min,沿催化剂单元条轴向45
°
角方向增加35khz的超声波,然后置于1.7wt.%的稀硫酸溶液中清洗10min,然后烘干;进一步将催化剂在钛酸丁酯溶液中浸渍3min,然后在恒温恒湿房中放置60min,烘干后浸渍于偏钒酸铵溶液中负载活性组分,焙烧后即获得再生脱硝催化剂。将不可再生催化剂破碎至100-150mm,进一步筛分去除碎料中的灰尘,筛网孔径控制为10mm,筛分后进行水洗以去除碎料表面灰尘,进一步添加酸液进行湿磨。酸液中硫酸、硝酸和水的质量份数之比为40:20:100,酸液与催化剂物料的质量份数之比为135:100,研磨控制物料粒度达到d90≤15um。进一步在研磨后的浆液中加入3倍质量的水并充分搅拌,然后进行过滤,如此反复3次,最终过滤后物料含水率≤80%,进一步干燥后粉料含水率≤3%。进一步进行风选,设置风速为3m/s,第一出料口获得密度较大、颗粒较大的重质粉料,第二出料口获得密度较小、颗粒较小的轻质粉料。
94.灰尘制备微晶玻璃将废脱硝催化剂模块中的灰尘收集与除锈产生的锈渣进行混合,加热至1000℃熔融,冷却至650℃通过压延辊筒进行压制,获得玻璃板材胚料,进一步在490℃保温4小时,空冷至室温获得微晶玻璃板材。
再多了解一些
本文用于企业家、创业者技术爱好者查询,结果仅供参考。