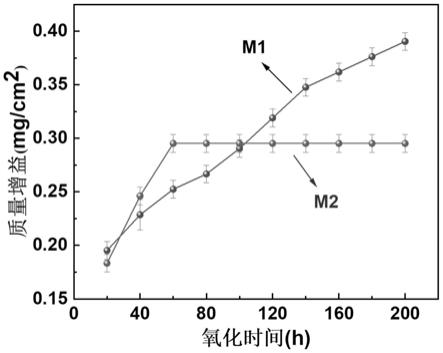
一种cocrnialy多层高温防护涂层及其增重控制方法、制备方法
技术领域
1.本发明属于热障涂层技术领域,具体涉及一种cocrnialy多层高温防护涂层及其在高温环境中的增重控制方法、制备方法。
背景技术:
2.mcraly涂层来源于第三代高温防护涂层,其中m代表ni基或co基三元ni-cr-al或co-cr-al合金体系,同时以ni和co为基的四元ni-co-cr-al合金体系构成的涂层(如cocrnialy涂层),具有更突出抗腐蚀能力及优异的力学性能。mcraly涂层一般用作热障涂层的粘结层,其与表面陶瓷层来一起构成热障涂层。
3.然而,以cocrnialy涂层为代表的热障涂层体系在高温环境中长时间服役时,由于高温合金基底与cocrnialy涂层在成分、元素浓度方面存在较大差异,以及热生长氧化物(tgo)的形成与生长,cocrnialy涂层与基底、陶瓷层的界面将发生元素互扩散行为,特别是在高温和基底合金添加更多难熔金属元素时,其互扩散速率显著增大,影响其性能,降低涂层体系抗蠕变强度及服役寿命。更关键地是,沉积在高温合金基底上的cocrnialy涂层在高温(>700℃)环境下使用时存在线性增重现象,如何防止其增重是需要解决的技术难题。
技术实现要素:
4.本发明目的在于提供一种cocrnialy多层高温防护涂层及其在高温环境中的增重控制方法、制备方法,至少解决涂层在高温(>700℃)环境下使用时存在线性增重的技术问题。
5.为了实现上述目的,本发明采用如下所述技术方案。
6.一种cocrnialy多层高温防护涂层,其特征在于:它包括在基体表面交替沉积多层cocrnialy层和多层al层,首层cocrnialy层沉积在基体表面,最外层为al层,涂层的总厚度为10.1~11μm。
7.作为本发明的优选方案,每层al层厚度为0.01~0.03μm,每层cocrnialy层厚度为0.01~0.03μm。
8.一种前述cocrnialy多层高温防护涂层在高温环境中的增重控制方法,其特征在于:将所述cocrnialy多层高温防护涂层置于750℃的干燥环境中放置60小时,该过程中每隔20小时将涂层取至常温环境中放置1-2分钟,该干燥环境中的氧含量为21
±
1%,该干燥环境中其余成分为氮气或惰性气体。
9.一种前述cocrnialy多层高温防护涂层的制备方法,其特征在于,步骤包括:步骤1,预处理:先对基材表面进行喷砂处理,然后进行超声清洗;步骤2,离子清洗:将真空室内真空度控制为1
×
10-3
pa~2
×
10-2
pa时,向真空室通入氩气,气压控制在0.1~4.0pa,将基体加脉冲负偏压在-40~-500v,采用电弧增强气体辉光放电,对基材表面进行辉光放电离子清洗10~120分钟;
步骤3,沉积cocrnialy/al多层涂层:调整ar气流量,将真空室内气压控制在0.1~4.0pa,基体加脉冲负偏压控制在-40~-500v,同时开启cocraly靶和al靶,控制cocraly靶弧流为60-150a,控制al靶弧流为50-120a,控制样品台转架转速为2-3转/分钟,控制沉积温度为200~400℃,在基材表面沉积厚度为10.1~11μm的cocrnialy/al多层涂层;步骤4,步骤3结束后,停弧、停基体脉冲负偏压、停止通入气体、停止样品台转架,继续抽真空,待工件随炉冷却至80℃以下后打开真空室,取出工件。
10.进一步地:步骤4结束后,将所得工件置于750℃的干燥环境中放置60小时,该过程中每隔20小时将涂层取至常温环境中放置1-2分钟,该干燥环境中的氧含量为21
±
1%,该干燥环境中其余成分为氮气或惰性气体。
11.有益效果:采用本发明的方案,不仅能够精准控制涂层在高温环境下使用时的增重情况,而且能够将其在高温(750℃)环境下使用时的增重控制在接近0mg/cm2,还能够大幅提高涂层的抗高温氧化能力、抗热腐蚀性能,延长涂层使用寿命,同时能够防止产生大量的铬酸盐尖晶石相。
附图说明
12.图1为实施例中涂层在750℃下处理200h的动力学曲线,m1表示对比实施例1中的cocrnialy涂层,m2表示实施例1中的cocrnialy-al涂层;图2是实施例中涂层的xrd谱图,图中位于下方的曲线对应对比实施例1中的cocrnialy涂层,位于上方的曲线对应实施例1中的cocrnialy-al涂层;图3是实施例中涂层表面sem图{(a)、(e)}和局部放大图{(b)、(f)},以及对应的eds能谱{(c)、(d)、(g)},(a)、(b)、(c)、(d)对应实施例1中的cocrnialy-al涂层,(e)、(f)、(g)对应对比实施例1中的cocrnialy涂层;图4是实施例中涂层的sem截面图和元素映射图,(a)、(b)对应对比实施例1中的cocrnialy涂层,(c)、(d)对应实施例1中的cocrnialy-al涂层;图5是实施例中涂层在750℃下处理100h、200h后的xrd谱图,(a)对应处理时间100h,(b)对应处理时间200h;两幅图中,位于下方的曲线对应对比实施例1中的cocrnialy涂层,位于上方的曲线对应实施例1中的cocrnialy-al涂层;图6是对比实施例1中cocrnialy涂层在750℃处理100h、200h后的表面sem图像和相应的eds能谱局部放大图,(a)、(b)、(c)、(d)对应100h,(e)、(f)、(g)对应200h;图7是实施例1中cocrnialy-al涂层在750℃处理100h、200h后的表面sem图像和相应的eds能谱局部放大图,(a)、(b)、(c)、(d)对应100h,(e)、(f)、(g)对应200h;图8是实施例中涂层在750℃下处理100h后沉积涂层的sem剖面图及对应元素映射,(a)、(b)对应实施例1中的cocrnialy-al涂层,(c)、(d)对应对比实施例1中的cocrnialy涂层;图9是实施例中涂层在750℃下处理200h后沉积涂层的sem剖面图及对应元素映射,(a)、(b)对应实施例1中的cocrnialy-al涂层,(c)、(d)对应对比实施例1中的cocrnialy涂层。
具体实施方式
13.结合附图和具体实施例对本发明作进一步说明,但以下实施例的说明只是用于帮助理解本发明的原理及其核心思想,并非对本发明保护范围的限定。应当指出,对于本技术领域普通技术人员来说,在不脱离本发明原理的前提下,针对本发明进行的改进也落入本发明权利要求的保护范围内。实施例1
14.基材采用高温合金gh4169,试样尺寸为15mm
×
15mm
×
5mm,镀膜面(涂层区域)尺寸为15mm
×
15mm。镀膜前试样表面先经过打磨、清洗、喷砂,然后再进行超声清洗;然后将处理后的试样基材放入电弧离子镀设备真空室内转架台上,开始抽真空,当真空室内真空度达到6
×
10-3
pa时,向真空室通入氩气,气压控制在0.6pa;基体加脉冲负偏压控制为为-120v,通过电弧增强气体辉光放电,对基材表面进行辉光放电离子清洗60分钟;然后开始沉积cocrnialy-al多层涂层(首先调整ar气流量,将真空室内气压控制在1.2pa;基体加脉冲负偏压控制为-80v,同时开启cocrnialy靶和al靶,cocrnialy靶弧流控制为90a,al靶弧流控制为60a,并将试样台转架转速调整为2转/分钟,沉积温度控制为230℃,沉积时间控制为240分钟);沉积结束后,停弧、停基体脉冲负偏压、停止通入气体、停止试样台转架转动,继续抽真空,试样随炉冷却至80℃以下后打开真空室,取出试样。本实施例中,每分钟可以沉积4层涂层,沉积240分钟总共约960层,所得cocrnialy-al多层涂层厚度为11μm,其单层涂层厚度仅约0.011μm。实施例2
15.基材采用钛合金(牌号为ti6al4v),试样尺寸为20mm
×
20mm
×
5mm,镀膜面(涂层区域)尺寸为20mm
×
20mm。镀膜前试样表面经过打磨、清洗、喷砂,然后再进行超声清洗;然后将处理后的试样基材放入电弧离子镀设备真空室内转架台上,开始抽真空,当真空室内真空度达到5.6
×
10-3
pa时,向真空室通入氩气,气压控制为0.8pa;基体加脉冲负偏压控制为-160v,通过电弧增强气体辉光放电对试样进行辉光放电离子清洗60分钟;然后开始沉积cocrnialy-al多层涂层(首先调整ar气流量,将真空室内气压控制在1.1pa;基体加脉冲负偏压调整为-100v,同时开启cocrnialy靶和al靶,cocrnialy靶弧流控制为85a,al靶弧流控制为65a,并将试样台转架转速调整为2转/分钟,沉积温度控制为250℃,沉积时间控制为200分钟);沉积结束后,停弧、停基体脉冲负偏压、停止通入气体、停止试样台转架转动,继续抽真空,试样随炉冷却至80℃以下后打开真空室,取出试样。实施例3
16.基材采用不锈钢(牌号为1cr18ni9ti),试样尺寸为20mm
×
10mm
×
10mm,镀膜面(涂层区域)尺寸为20mm
×
10mm。镀膜前试样表面经过打磨、清洗、喷砂,然后再进行超声清洗;然后将处理后的试样基材放入电弧离子镀设备真空室内转架台上,开始抽真空,当真空室内真空度达到4.6
×
10-3
pa时,向真空室通入氩气,气压控制在0.4pa;基体加脉冲负偏压在-180v,通过电弧增强气体辉光放电,对试样进行辉光放电离子清洗55分钟;然后开始沉积cocrnialy-al多层涂层(首先调整ar气流量,将真空室内气压控制在1.0pa;基体加脉冲负偏压为-70v,同时开启cocrnialy靶和al靶,cocrnialy靶弧流控制为95a,al靶弧流控制为70a,并将试样台转架转速调整为3转/分钟,沉积温度控制为210℃,沉积时间控制为210分钟);沉积结束后,停弧、停基体脉冲负偏压、停止通入气体、停止试样台转架转动,继续抽真
空,试样随炉冷却至80℃以下后打开真空室,取出试样。实施例4
17.基材采用ta17钛合金(牌号为ti-4al-2v),试样尺寸为20mm
×
10mm
×
10mm,镀膜面尺寸为20mm
×
10mm。镀膜前试样表面经过打磨、清洗、喷砂,然后再进行超声清洗;然后将处理后的试样基材放入电弧离子镀设备真空室内转架台上,开始抽真空,当真空室内真空度达到5.3
×
10-3
pa时,向真空室通入氩气,气压控制在0.4pa;基体加脉冲负偏压在-150v,通过电弧增强气体辉光放电,对试样进行辉光放电离子清洗60分钟;然后开始沉积cocrnialy-al多层涂层(首先调整ar气流量,将真空室内气压控制在0.9pa;基体加脉冲负偏压控制为-100v,cocrnialy靶弧流控制为85a,al靶弧流控制为60a,并将试样台转架转速调整为2.5转/分钟,沉积温度控制为220℃,沉积时间控制为220分钟);沉积结束后,停弧、停基体脉冲负偏压、停止通入气体、停止试样台转架转动,继续抽真空,试样随炉冷却至80℃以下,打开真空室,取出试样。对比实施例
18.基材采用高温合金gh4169,试样尺寸为15mm
×
15mm
×
5mm,镀膜面尺寸为15mm
×
15mm,镀膜前试样表面经过打磨、清洗、喷砂,然后再进行超声清洗;然后将处理后的试样基材放入电弧离子镀设备真空室内转架台上,开始抽真空,当真空室内真空度达到6
×
10-3
pa时,向真空室通入氩气,气压控制在0.6pa;基体加脉冲负偏压为-120v,通过电弧增强气体辉光放电,对试样进行辉光放电离子清洗60分钟;然后开始沉积cocrnialy涂层(首先调整ar气流量,将真空室内气压控制在1.2pa;基体加脉冲负偏压为-80v,同时开启cocrnialy靶,cocrnialy靶弧流控制为90a,并将试样台转架转速调整为2转/分钟,沉积温度为230℃,沉积240分钟);沉积结束后,停弧、停基体脉冲负偏压、停止通入气体、停止试样台转架转动,继续抽真空,试样随炉冷却至80℃以下后打开真空室,取出试样。
19.对各实施例中试样的涂层总厚度进行检测,结果见表1;对各实施例中试样进行恒温氧化实验,实验方法采用重量增加法,在实验结束后统计氧化增重值,实验温度设定750℃,实验总时间设定为200小时,氧含量为21
±
1%(其与成分为氮气),前100h每隔20小时取出试样称量一次,后100h每隔20h取出试样称量一次,测试结果见表1。表1各实施例中涂层总厚度及增重值
20.对各实施例中试样进行恒温氧化实验,实验方法采用重量增加法,在实验结束后统计氧化增重值,实验温度设定850℃,实验总时间设定为200小时,氧含量为21
±
1%(其与成分为氮气),前100h每隔20小时取出试样称量一次,后100h每隔20h取出试样称量一次,测试结果见表2。表2各实施例中涂层总厚度及增重值
21.由表1和表2可知,实施例1-4中所得cocrnialy-al多层涂层在经750℃、850℃及氧含量为21
±
1%的高温环境处理60小时后,涂层不再增重(而在实施例1-4中所得cocrnialy-al多层涂层在经500℃、1000℃,氧含量为21
±
1%的高温环境处理60小时后,涂层在第60-200小时却呈现不规律的明显增重),据表1得到的动力学曲线如图1所示,m1表示对比实施例1中的cocrnialy涂层,m2表示实施例1中的cocrnialy-al涂层。
22.基于此,实施例5提供一种前述cocrnialy-al多层高温防护涂层在高温环境中的增重控制方法:将cocrnialy-al多层高温防护涂层置于750℃的干燥环境中放置60小时,该过程中每隔20小时将涂层取至常温环境中放置1-2分钟,该干燥环境中的氧含量为21
±
1%。采用该方案,不仅能够精准控制涂层在高温环境下使用时的增重情况,而且能够将其
在高温(750℃)环境下使用140小时的增重控制在0mg/cm2。能够在750℃的干燥环境中防止cocrnialy-al多层高温防护涂层增重,即将其增重
23.进一步地,还提供一种前述cocrnialy-al多层高温防护涂层的制备方法,步骤包括:步骤1,预处理:先对基材表面进行喷砂处理,然后进行超声清洗;步骤2,离子清洗:将真空室内真空度控制为1
×
10-3
pa~2
×
10-2
pa时,向真空室通入氩气,气压控制在0.1~4.0pa,将基体加脉冲负偏压在-40~-500v,采用电弧增强气体辉光放电,对基材表面进行辉光放电离子清洗10~120分钟;步骤3,沉积cocrnialy-al多层涂层:调整ar气流量,将真空室内气压控制在0.1~4.0pa,基体加脉冲负偏压控制在-40~-500v,同时开启cocraly靶和al靶,控制cocraly靶弧流为60-150a,控制al靶弧流为50-120a,控制样品台转架转速为2-3转/分钟,控制沉积温度为200~400℃,在基材表面沉积厚度为10.1~11μm的cocrnialy/al多层涂层;步骤4,步骤3结束后,停弧、停基体脉冲负偏压、停止通入气体、停止样品台转架,继续抽真空,待工件随炉冷却至80℃以下后打开真空室,取出工件。步骤5,将所得工件置于750℃的干燥环境中放置60小时,该过程中每隔20小时将工件取至常温环境中放置1-2分钟,该干燥环境中的氧含量为21
±
1%。
24.采用该方法制得的cocrnialy-al涂层,在高温环境下的性能非常稳定,至少能够在750℃的环境下使用140小时,大幅提高了涂层的抗高温氧化能力、抗热腐蚀性能,延长了涂层使用寿命。
25.对实施例1中试样进行检测,结果如下。
26.实施例1和对比实施例1中涂层的xrd谱图如图2所示,图中位于下方的曲线对应对比实施例1中的cocrnialy涂层,位于上方的曲线对应实施例1中的cocrnialy-al涂层,两种涂层均以alni3相为主,这是因为制备涂层所用的原料是cocrnialy,其中al和ni元素含量较高,在制备条件下容易形成alni相化合物。
27.实施例1和对比实施例1中涂层表面sem图和局部放大图,以及对应的eds能谱如图3所示,(a)、(b)、(c)、(d)对应实施例1中的cocrnialy-al涂层,(e)、(f)、(g)对应对比实施例1中的cocrnialy涂层。两种涂层的表面形貌致密,如图3的(a)部分和(e)部分所示,表面呈现出明显的颗粒分布特征;如图3的(b)部分和(f)部分所示,图像的eds映射显示,白色小颗粒位于富y区,表面为al、cr和ni的混合氧化物。
28.实施例1和对比实施例1中涂层的sem截面图、元素映射图如图4所示,(a)、(b)对应对比实施例1中的cocrnialy涂层,(c)、(d)对应实施例1中的cocrnialy-al涂层,图中可见两种涂层与相邻的基体层都形成了满意的结合界面,在sem截面图中可以清楚地观察到al元素发生了的不同程度的扩散,在eds能谱中下的图中al元素分布图颜色较亮,证明al含量较多。
29.实施例1和对比实施例1中涂层在750℃下处理100h、200h后的xrd谱图如图5所示,(a)对应处理时间100h,(b)对应处理时间200h;两幅图中,位于下方的曲线对应对比实施例1中的cocrnialy涂层,位于上方的曲线对应实施例1中的cocrnialy-al涂层。图5中(a)部分所示,两种涂层的相组成主要为al
0.9
ni
4.22
;如图5中(b)部分所示,随着处理时间的延长,两
种涂层的表面元素分布没有明显变化,由于大量的al元素和氧向下扩散,在涂层与基体的界面处形成了al2o3保护层,因此涂层表面不能检测到al2o3相,与图2中原始样品表面的xrd相比,衍射峰的宽度明显变窄。
30.对比实施例1中cocrnialy涂层在750℃下处理100h、200h后的表面sem图像和相应的eds能谱局部放大图见图6所示,(a)、(b)、(c)、(d)对应100h,(e)、(f)、(g)对应200h。试样经100h高温环境处理后的表面形貌如图6中(a)、(b)部分所示,表面出现细小的裂纹和气孔,且表面分布有大小不一的白色颗粒;如图6中(c)、(d)部分所示,白色颗粒为铬酸盐尖晶石相,片状、带状结构为al、cr和ni的混合氧化物;随着处理时间延长至200小时后,如图中6(e)、(f)部分所示,表面白色颗粒明显增多,片状和条状组织明显减少,此时,镀层表面分布了大量的铬酸盐尖晶石相,如图6中(g)部分所示。
31.实施例1中cocrnialy-al涂层在750℃下处理100h、200h后的表面sem图像和相应的eds能谱局部放大图见图7所示,(a)、(b)、(c)、(d)对应100h,(e)、(f)、(g)对应200h。试样经100h高温环境处理后的表面形貌如图7中(a)、(b)部分所示,涂层表面分布有条状和多边形块状结构材料,与cocrnialy涂层不同,没有发现明显的白色颗粒,eds mapping显示cocrnialy涂层中的条状、多边形块状结构物质主要为铝和镍的混合氧化物,以不同的形式分布在样品表面,如图7中(c)、(d)部分所示;如图7中(e)、(f)部分所示,随着处理时间的延长至200小时后,涂层表面暴露出一些疏松的块状结构,但仍有一些条状、多边形块状结构物质,eds谱图显示此时表面存在大量的al氧化物,如图7中(g)部分所示。
32.实施例1和对比实施例1中涂层在750℃下处理100h后沉积涂层的sem剖面图及对应元素映射如图8所示,(a)、(b)对应实施例1中的cocrnialy-al涂层,(c)、(d)对应对比实施例1中的cocrnialy涂层。如图8中(a)部分所示,涂层与基体之间存在一层连续的al2o3保护层,涂层中的al元素不断向下扩散,为基体提供连续致密的al2o3保护层;eds能谱清楚地表明,连续和致密氧化铝阻挡层有效地阻碍了元素的相互扩散,如图8中(b)部分所示;如图8中(c)部分所示,对比实施例1中cocrnialy涂层的铝元素的消耗更严重,与原试样相比,al2o3变得更薄,不能对涂层和基体产生良好的保护效果,严重降低了此时涂层的保护效果,且涂层中al元素含量较低,不能及时向al2o3阻挡层提供al元素,因此不能抑制氧元素的侵入和基体元素的扩散,如图8中(d)部分所示。
33.实施例1和对比实施例1中涂层在750℃下处理200h后沉积涂层的sem剖面图及对应元素映射如图9所示,(a)、(b)对应实施例1中的cocrnialy-al涂层,(c)、(d)对应对比实施例1中的cocrnialy涂层。如图9中(a)、(b)部分所示,实施例1的涂层中有充足的al元素供给,上层的al元素向下层扩散,氧化铝的密实度保护层较好;如图9中(c)、(d)部分所示,对比实施例1中cocrnialy涂层的铝元素被大大消耗,和氧化铝保护层变得松散,进一步削弱涂层的保护作用,抑制作用较弱,元素间相互扩散严重。
再多了解一些
本文用于企业家、创业者技术爱好者查询,结果仅供参考。