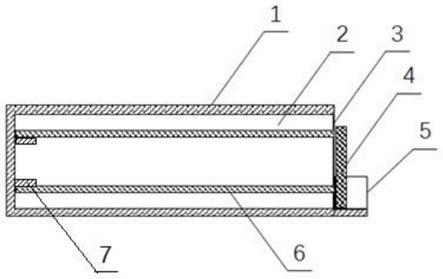
1.本发明涉及粉末冶金的生产技术领域,具体而言是涉及一种超细碳化物的生产方法及生产装置。
背景技术:
2.随着亚微细、超细碳化钨硬质合金的需求量及性能要求不断提高,市场对碳化钨、碳化钽、碳化铌、碳化铬等碳化物原料需求量及粒度要求也在不断提升。目前较理想的原料颗粒尺寸一般应是亚微细范围以下(《1μm)以保证其使用效果。
3.专利cn100457612c公开了一种细颗粒tac粉末的方法,该专利使用真空炉生产碳化钽,设备复杂、工序复杂,碳化温度高,耗时长,不利于连续生产。且产物粒度≤1.5μm,无法达到小于1μm。
4.专利cn202089772u公开了一种中频高温碳化炉用石墨舟皿,包括上、下垫板和舟皿体,所述上垫板至少一面设有环形凹槽,下垫板至少一面设有环形凹槽,所述舟皿体由至少两个弧形板对合而成,舟皿体的两端分别容置于上、下垫板的环形凹槽中。该舟皿类似拼接版石墨全圆舟皿,但其中部为完全导通的石墨管道,且料层两端完全密封。这样会导致碳化过程产生的废气无法及时排出,阻碍反应的进行,对产品质量不利。
5.专利cn109319785a公开了一种机械力化学法制备超细碳化钨粉末的方法,该方法耗时过长,碳化时长达到70h,且无法连续生产,无法很好地适应工业生产。
6.同样的,专利cn103408015b公开的一种超细碳化钨制备方法存在产能浪费(需要事先加入大量反应产物碳化钨),耗时长达3h等缺陷。
7.专利cn101723368a公开的一种超细碳化钨制备方法存在生产步骤繁琐、耗时长的缺陷,需要事先钝化钨粉,且配碳混合及冷却时长总计达到13-19h,破碎时长超过2h。
8.专利cn110510614a公开的一种超细碳化钨制备方法同样存在生产步骤繁琐、耗时长、碳化温度高的缺陷,其在钨粉使用前需进行超声波分散及分级过筛,随后再进行钨粉钝化,碳化温度需要1350℃~1550℃。
9.专利cn1789122a公开了一种能满足超细硬质合金生产用费氏粒度fsss≤2μm的cr3c2粉末的制备方法,该方法使用真空炉生产,设备复杂、工序复杂,产出碳化铬fsss粒度《2μm,同时仅生产碳化铬。
10.目前没有利用全圆舟生产超细碳化物的报道。碳化物传统生产所用舟皿为半圆舟,该舟皿生产碳化物所用生产工艺温度需要达到1200℃~1500℃。常规半圆舟皿结构包括半圆舟舟皿主体9及端盖8。半圆舟舟皿主体9为弦型柱体中空石墨舟,一侧密封,另一侧有开口;端盖8为弦型端盖,设于半圆舟舟皿主体9开口的一侧,物料装于半圆舟舟皿主体9内部中空位置,结构示意图如图3和4所示。
11.现有常规半圆舟皿封闭性较差,物料堆积形态为弦型柱体,且开口面积较大,碳化过程中物料温场不均匀,易造成物料碳化完成后粗细不均。例如生产超细物料易产生大量超过1μm的大颗粒。
技术实现要素:
12.现有方法及舟皿基本存在温度高、温场不均匀、耗时长、操作繁琐等缺陷。针对现有技术的不足,本发明的目的在于提供一种能够满足碳化物颗粒尺寸要求的超细碳化物的生产方法及生产装置,在较低的温度下生产超细碳化物(碳化钨、碳化钽、碳化铌、碳化铬等)粉末的方法。
13.本发明解决技术问题所采用的技术方案是:一种超细碳化物的生产方法,所述生产方法为,将原料、炭黑按相应比例使用混合设备混合均匀,后将混合料加入全圆舟中送入碳化炉,在一定气氛下,在1000℃~1400℃条件下,进行碳化;碳化后冷却至50℃左右,得到块状碳化物,块状碳化物球磨破碎后得到fsss《1μm的碳化物粉末。
14.进一步地,所述碳化时间为50~70min。
15.进一步地,所述原料包括但不限于钨粉、氧化钨、氧化钽、氧化铌、氧化铬。
16.本发明所述的生产装置为全圆舟皿,所述全圆舟皿包括舟皿主体、通管及盖板;所述舟皿主体为一内部中空的圆柱形套筒,其一侧密封,另一侧有开口;所述通管为一内部打通的环形通管;所述盖板为一弦型盖板;所述通管套设于所述舟皿主体内部,所述通管外壁与所述舟皿主体内壁之间形成用于装填物料的装料区域;所述盖板设于所述舟皿主体开口的一侧。
17.进一步地,所述舟皿主体、通管及盖板均为石墨材质;石墨材质对碳化物生产的碳化反应而言有一定促进作用且基本不会引入杂质。
18.进一步地,所述舟皿主体中封闭一侧的圆心处设有环形卡槽,所述通管套设于所述舟皿主体内部后,通过所述环形卡槽固定,放置于与所述舟皿主体同圆心位置;所述舟皿主体与所述通管之间形成环形的装料区域。
19.进一步地,所述舟皿主体的开口侧不在同一平面上,所述开口侧上的部分筒壁长于所述开口侧的其余筒壁。
20.进一步地,所述弦型盖板部分覆盖所述舟皿主体的开口侧,使所述装料区域不完全被所述盖板密封,有利于反应废气的排出,使其反应更容易进行,可以有效降低反应温度。
21.如前文所述,现有常规半圆舟皿封闭性较差,物料堆积形态为弦型柱体,且开口面积较大,碳化过程中物料温场不均匀,易造成物料碳化完成后粗细不均。而本发明专利所述的,制备超细碳化物的方法是通过降低反应温度实现的,使物料碳化完全的同时,粒度涨幅不明显。本发明中使用的全圆舟通过环形装料区使得物料堆积形态成为薄厚相同、分布较均匀的环形柱体,有效的改善了物料薄厚不均的分布情况,进而改善了因物料厚度不同而造成的温度场分布不均这一缺陷。同时其仅有单侧开口,并且开口处有端盖进行密封,有效地减少了温度的散失,可以有效地降低反应温度。
22.本发明的有益效果是:针对现有技术中碳化温度较高、温场不均匀、耗时长、操作繁琐的不足,提供一种能够满足碳化物颗粒尺寸要求的超细碳化物的生产方法及装置;将现有的超细碳化物生产中采用的常规半圆舟皿替换为石墨全圆舟皿,石墨舟皿对碳化物生产的碳化反应而言有一定促进作用且基本不会引入杂质;单侧开口有利于反应废气的排出,使其反应更容易进行;其环形装料层可以有效改善料层厚度和物料、温场的均匀性,可以有效降低反应温度。
附图说明
23.图1为本发明提供的全圆舟的剖面结构示意图。
24.图2为本发明提供的全圆舟的侧面结构示意图。
25.图3为现有技术中半圆舟的剖面结构示意图。
26.图4为图3中截面a-a’的结构示意图。
27.其中,1-舟皿主体;2-装料区域;3-开口侧;4-盖板;5-长筒壁部分;6-通管;7-环形卡槽;8-端盖;9-半圆舟舟皿主体。
具体实施方式
28.下面通过具体实施例来进一步说明本发明。但这些实例仅用于说明本发明而不用于限制本发明的范围。
29.实施例1
30.将原料粒度约为0.5微米的钨粉(w)约1000kg及炭黑(c)约60kg进行混合约2h,混合均匀后卸出。
31.将混合均匀的钨粉及炭黑加入全圆舟中,送入中频炉进行碳化,在氮气气氛中碳化,碳化温度1150℃,装舟量约2kg/舟,碳化55min后,在炉内冷却后,得到wc块状物,块状物经球磨破碎1.5h后得到wc粉末,其fsss粒度为0.65μm。
32.实施例2
33.将细粒度的的氧化钨粉(wo3)约1000kg及炭黑(c)约140kg加入混合设备进行约3h混合后,停止混合,冷却完成后将其卸出。
34.将混合均匀的物料加入全圆舟中,送入碳管炉进行碳化,在氢气气氛下,温度1350℃,装舟量约1.5kg/舟,碳化70min后,在炉内冷却,得到wc块状物,块状物经球磨破碎2h后得到wc粉末,其fsss粒度为0.5μm。
35.将上述实施例1和2中得到的超细碳化钨进行化学成分分析,具体如下表1所示。
36.实施例por.1fsss(μ)o/%ct/%cf/%bets/%ife/%ni/%co/%ca/%10.6290.650.1706.140.042.000.00050.00100.00050.00210.000520.6650.500.2906.150.062.650.00050.00180.00050.00180.0005
37.上述各实施例中的所述的生产装置为全圆舟皿,所述全圆舟皿包括舟皿主体1、通管6及盖板4;所述舟皿主体1为一内部中空的圆柱形套筒,其一侧密封,另一侧有开口;所述通管6为一内部打通的环形通管6;所述盖板4为一弦型盖板4;所述通管6套设于所述舟皿主体1内部,所述通管6外壁与所述舟皿主体1内壁之间形成用于装填物料的装料区域2;所述盖板4设于所述舟皿主体1开口的一侧。所述舟皿主体1、通管6及盖板4均为石墨材质;石墨材质对碳化物生产的碳化反应而言有一定促进作用且基本不会引入杂质。所述舟皿主体1中封闭一侧的圆心处设有环形卡槽7,所述通管6套设于所述舟皿主体1内部后,通过所述环形卡槽7固定,放置于与所述舟皿主体1同圆心位置;所述舟皿主体1与所述通管6之间形成环形的装料区域2。所述舟皿主体1的开口侧3不在同一平面上,所述开口侧3上的部分筒壁长于所述开口侧3的其余筒壁,为图1中图示5所示的长筒壁部分5。所述弦型盖板4部分覆盖所述舟皿主体1的开口侧3,使所述装料区域2不完全被所述盖板4密封,有利于反应废气的排出,使其反应更容易进行,可以有效降低反应温度。
38.使用时,将混合好的物料填充至环形装料区域2内,送入碳化炉中在特定气氛下进行碳化,由于料层厚度降低,物料及温场分布更加均匀。而更加良好的密封性使得其保温效果提升(因其单侧开口处有弦型盖板4进行密封,仅会留下很小的开口以供反应气体产物排出,有利于反应正向进行),同时端面的不完全密封有利于反应废气的排出,使其反应更容易进行,可以有效降低反应温度。在1000-1400℃条件下,装舟量约2kg/舟,碳化50-70min后,在炉内冷却至50℃左右卸出,得到wc块状物,块状物经球磨破碎1-2h后得到wc粉末。
39.以上实施方式仅用于说明本发明,而并非对本发明的限制,有关技术领域的普通技术人员,在不脱离本发明的精神和范围的情况下,还可以做出各种变化和变型,因此所有等同的技术方案也属于本发明的范畴,本发明的专利保护范围应由权利要求限定。
再多了解一些
本文用于企业家、创业者技术爱好者查询,结果仅供参考。